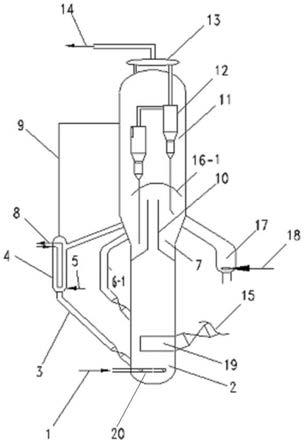
减少mto反应中二次反应的方法和设备
技术领域
1.本发明涉及一种减少mto反应中二次反应的方法和设备。
背景技术:
2.乙烯和丙烯是两种重要的基础化工原料,用作生产许多重要化学品和聚合物的原料,其需求量在不断增加。一般地,乙烯、丙烯是通过裂化石油原料来获得,但由于石油资源有限的供应量及较高的价格,由石油资源生产乙烯、丙烯的成本不断增加。近年来,人们开始致力于发展含氧化合物,特别是甲醇替代石油转化制乙烯、丙烯的技术。由于含氧化合物来源的广泛性,再加上转化生成低碳烯烃工艺的经济性,所以由含氧化合物转化制烯烃(oto)的工艺,特别是由甲醇转化制烯烃(mto)的工艺受到越来越多的重视。
3.用于促进含氧化合物转化为烯烃的催化剂是分子筛催化剂,特别是硅铝磷酸盐分子筛。硅铝磷酸盐(sapo)分子筛含有[sio2]、[alo2]和[po2]角共享四面体单元的三维微孔性晶体框架结构。文献us4440871公开了sapo的合成方法。文献cn1248993c公开了一种将氧化物原料转化为烯烃产品的方法。具体地,该方法包括在乙烯和丙烯的生产过程中应用硅铝磷酸盐分子筛催化剂。所述方法包括在流化床反应器设备中使含有氧化物的原料与硅铝磷酸盐分子筛催化剂接触从而形成含有烯烃的产品,其中所述流化床反应器设备至少包括反应区和循环区。
[0004]
文献us6166282公布了一种甲醇转化为低碳烯烃的技术和反应器,采用快速流化床反应器,气相在气速较低的密相反应区反应完成后,上升到内径急速变小的快分区后,采用特殊的气固分离设备初步分离出大部分的夹带催化剂。由于反应后产物气与催化剂快速分离,有效的防止了二次反应的发生。经模拟计算,与传统的鼓泡流化床反应器相比,该快速流化床反应器内径及催化剂所需藏量均大大减少。该方法中低碳烯烃碳基收率一般均在77%左右。
[0005]
文献us 20060025646公开了一种控制mto反应器反应区中催化剂积炭量的方法,将失活的催化剂一部分送入再生区烧炭,另一部分失活催化剂返回到反应区继续反应。
[0006]
然而,随着市场上对乙烯、丙烯需求量的不断增加,对低碳烯烃生产技术提出了更高的要求。
技术实现要素:
[0007]
本发明的发明人发现,用流化床反应器进行甲醇转化为低碳烯烃的过程中,反应速度很快,属于秒级反应,因此控制流化床反应区内气体与催化剂的接触时间至关重要,当反应结束后,应该尽量减少产物与催化剂的继续接触,减少二次反应的发生。本发明基于这些发现而完成。
[0008]
具体而言,本发明涉及以下方面的内容:
[0009]
1、一种减少mto反应中二次反应的方法,包括甲醇原料进入流化床反应器的反应区与催化剂接触生成包括乙烯、丙烯产品的步骤;其中,所述流化床反应器中,在包括甲醇
的气相物流的运动方向上,所述催化剂中至少50重量%(优选80重量%,优选90%,更优选100重量%)经历至少一次角度大于90
°
(优选大于120
°
,更优选大于180
°
)的运行轨迹转变。
[0010]
2、前述或后述任一方面所述减少mto反应中二次反应的方法,其特征在于,使所述催化剂与运行轨迹转变设备接触,从而使至少50重量%(优选80重量%,优选90%,更优选100重量%)的催化剂经历至少一次角度大于90
°
(优选大于120
°
,更优选大于180
°
)的运行轨迹转变。
[0011]
3、前述或后述任一方面所述减少mto反应中二次反应的方法,其中,所述催化剂通过加速管后与所述运行轨迹转变设备接触。
[0012]
4、前述或后述任一方面所述减少mto反应中二次反应的方法,其中,所述运行轨迹转变设备选自挡板、气固快速分离旋风分离器和倒l型弯管
[0013]
5、前述或后述任一方面所述减少mto反应中二次反应的方法,其中,所述挡板为弧形挡板,其弧度至少大于95
°
。
[0014]
6、前述或后述任一方面所述减少mto反应中二次反应的方法,其中,所述挡板中心最高点与所述加速管出口之间的距离为所述加速管长度的1/10~1/5。
[0015]
7、前述或后述任一方面所述减少mto反应中二次反应的方法,其中,所述催化剂包含硅铝磷分子筛(优选sapo-18、sapo-34、sapo-5或其组合)。
[0016]
8、前述或后述任一方面所述减少mto反应中二次反应的方法,其中,所述流化床反应器的反应区为快速流态化反应区,所述快速流态化反应区内气固并流向上流动。
[0017]
9、前述或后述任一方面所述减少mto反应中二次反应的方法,其中,所述反应区反应条件包括:反应温度400~550℃,反应压力0~1mpa。
[0018]
10、一种流化床反应器,包括反应区、二密床、沉降区和加速管;所述反应区、所述二密床和所述沉降区以流体相通的方式相连;所述反应区出口与所述加速管入口相连,所述加速管伸入所述二密床中,所述加速管出口设置有运行轨迹转变设备。
[0019]
11、前述或后述任一方面所述流化床反应器,其中,所述运行轨迹转变设备选自挡板、气固快速分离旋风分离器和倒l型弯管。
[0020]
12、前述或后述任一方面所述流化床反应器,其中,所述挡板为弧形挡板,其弧度大于95
°
。
[0021]
13、前述或后述任一方面所述流化床反应器,其中,所述挡板中心最高点与所述加速管出口之间的距离为所述加速管长度的1/10~1/5。
[0022]
14、前述或后述任一方面所述流化床反应器,其中,所述反应区底部设置有气相进料分布设备(优选分布板和树枝形分布管)。
[0023]
15、前述或后述任一方面所述流化床反应器,其中,所述反应区出口与所述加速管相连之处设置有溢流管使所述二密床与所述反应区流体相通。
[0024]
16、前述或后述任一方面所述流化床反应器,其中,所述反应区下部设置有再生管路出口,所述再生管路出口设置有固相进料分布设备。
[0025]
17、前述或后述任一方面所述流化床反应器,其中,所述固相进料分布设备沿所述反应器径向基本水平布置。
[0026]
技术效果
[0027]
根据本发明,既能保证高的原料转化率,又能保证高的低碳烯烃选择性,低碳烯烃
选择性可达到85%以上。
附图说明
[0028]
图1为本发明的流化床反应器实施方式之一的示意图。
[0029]
图2为本发明的流化床反应器实施方式之二的示意图。
[0030]
图3为本发明的流化床反应器实施方式之三的示意图。
[0031]
图4为本发明的流化床反应器实施方式之四的示意图。
[0032]
图1-图4中,
[0033]
1为甲醇进料管线;
[0034]
2为反应区;
[0035]
3为外取热器下斜管;
[0036]
4为反应器外取热器;
[0037]
5为反应器外取热器流化介质;
[0038]
6-1为反应器循环斜管;
[0039]
6-2为溢流管;
[0040]
7为二密床;
[0041]
8为反应器外取热器冷却介质;
[0042]
9为反应器外取热器气相返回反应器沉降区管线;
[0043]
10为加速管;
[0044]
11为沉降区;
[0045]
12为旋风分离器;
[0046]
13为反应器集气室;
[0047]
14为产品气出口管线;
[0048]
15为再生管路;
[0049]
16-1为挡板;
[0050]
16-2气固快速分离旋风分离器;
[0051]
16-3为倒l型弯管;
[0052]
17为汽提器;
[0053]
18为汽提蒸汽;
[0054]
19为固相进料分布设备;
[0055]
20为气相进料分布设备。
具体实施方式
[0056]
下面对本发明的具体实施方式进行详细说明,但是需要指出的是,本发明的保护范围并不受这些具体实施方式的限制,而是由附录的权利要求书来确定。
[0057]
本说明书提到的所有出版物、专利申请、专利和其它参考文献全都引于此供参考。除非另有定义,本说明书所用的所有技术和科学术语都具有本领域技术人员常规理解的含义。在有冲突的情况下,以本说明书的定义为准。
[0058]
当本说明书以词头“本领域技术人员公知”、“现有技术”或其类似用语来导出材
料、物质、方法、步骤、装置或部件等时,该词头导出的对象涵盖本技术提出时本领域常规使用的那些,但也包括目前还不常用,却将变成本领域公认为适用于类似目的的那些。
[0059]
在本说明书的上下文中,所谓“基本”指的是允许存在对于本领域技术人员而言可以接受或认为合理的偏差,比如偏差在
±
10
°
以内、
±5°
以内、
±1°
以内、
±
0.5
°
以内或者
±
0.1
°
以内。
[0060]
在本说明书的上下文中,甲醇转化反应发生的主要区域为反应区2和加速管10内,该主要区域内气固基本并流向上流动。
[0061]
在没有明确指明的情况下,本说明书内所提到的所有百分数、份数、比率等都是以重量为基准的,而且压力是表压。
[0062]
在本说明书的上下文中,本发明的任何两个或多个实施方式都可以任意组合,由此而形成的技术方案属于本说明书原始公开内容的一部分,同时也落入本发明的保护范围。
[0063]
根据本发明的一个实施方式,涉及一种减少mto反应中二次反应的方法。所述方法包括甲醇原料进入流化床反应器的反应区与催化剂接触生成包括乙烯、丙烯产品的步骤。其中所述流化床反应器中,在包括甲醇的气相物流的运动方向上,所述催化剂中至少50重量%经历至少一次角度大于90
°
的运行轨迹转变。
[0064]
根据本发明的一个实施方式,所述催化剂中优选80重量%,优选85重量%,优选90%,更优选100重量%经历至少一次角度大于90
°
的运行轨迹转变。
[0065]
根据本发明的一个实施方式,包含甲醇的原料进入反应区2,与催化剂接触,生成包括未反应的甲醇、低碳烯烃(比如乙烯、丙烯)、c4烃的气相物流。所述气相物流夹带着催化剂。在旋风分离器12的作用下,所述气相物流基本上是向上运动的。在该包括甲醇的气相物流的运动方向上,所述催化剂经历运行轨迹转变,从而保证在甲醇未转化完成的过程中,催化剂强制发生轨迹转变。如果催化剂不经历运行轨迹转变,那么大量催化剂会跟随气相物流一起运行至旋风分离器才分开,这样势必增加了二次反应的发生。所述催化剂运行轨迹转变的角度优选大于120
°
,更优选大于150
°
,最优选大于180
°
。
[0066]
根据本发明的一个实施方式,为实现所述催化剂运行轨迹转变,使所述催化剂与运行轨迹转变设备接触。
[0067]
根据本发明的一个实施方式,所述催化剂通过加速管后与所述运行轨迹转变设备接触。
[0068]
根据本发明的一个实施方式,所述催化剂包含硅铝磷分子筛,优选sapo-18、sapo-34、sapo-5或其组合,更优选为sapo-34。sapo分子筛或者sapo分子筛催化剂的制备方法是为本领域所熟知的。
[0069]
根据本发明的一个实施方式,所述流化床反应器为快速流态化型式,所述流化床反应器包括快速流态化反应区,所述快速流态化反应区内气固并流向上流动,从而避免流化床层内的返混导致的低碳烯烃的二次反应。
[0070]
根据本发明的一个实施方式,所述反应区反应条件包括:反应温度400~550℃,反应压力0~1mpa。
[0071]
根据本发明的一个实施方式,还涉及一种流化床反应器。所述流化床反应器包括反应区、二密床、沉降区和加速管;所述反应区、所述二密床和所述沉降区以流体相通的方
式相连;所述反应区出口与所述加速管入口相连,所述加速管伸入所述二密床中,所述加速管出口设置有运行轨迹转变设备。
[0072]
根据本发明的一个实施方式,所述运行轨迹转变设备选自挡板、气固快速分离旋风分离器和倒l型弯管。
[0073]
根据本发明的一个实施方式,所述运行轨迹转变设备为挡板,所述挡板设置于所述加速管出口,例如所述加速管出口的上方。所述挡板优选弧形挡板,弧度至少大于95
°
;沿包括甲醇的气相物流的运动方向,所述挡板为上凸型;挡板中心最高点与加速管出口之间的距离为加速管长度的1/10~1/5。
[0074]
根据本发明的一个实施方式,所述运行轨迹转变设备为气固快速分离旋风分离器。所述气固快速分离旋风分离器的入口与所述加速管出口相连。
[0075]
根据本发明的一个实施方式,所述运行轨迹转变设备为倒l型弯管。所述倒l型弯管的入口与所述加速管出口相连。
[0076]
根据本发明的一个实施方式,所述反应区底部设置有气相进料分布设备,优选分布板和树枝形分布管。
[0077]
根据本发明的一个实施方式,所述反应区出口与所述加速管相连之处设置有溢流管使所述二密床与所述反应区流体相通。运行轨迹发生转变后的催化剂通过循环斜管或溢流管返回所述反应区。
[0078]
根据本发明的一个实施方式,所述反应区内的催化剂失活后形成待生催化剂,所述待生催化剂通过待生管路进入再生器再生,形成再生催化剂,所述再生催化剂通过再生管路返回到流化床反应区。所述再生管路出口设置有固相进料分布设备。
[0079]
根据本发明的一个实施方式,所述固相进料分布设备沿所述反应器径向基本水平布置,使再生催化剂均匀分布于所述流化床反应器反应区的径向平面上。
[0080]
以下将通过实施例和比较例对本发明进行进一步的详细描述,但本发明不限于以下实施例。
[0081]
【实施例1】
[0082]
如图1所示,主要为甲醇的原料进入快速床反应区2,与包括硅铝磷分子筛的催化剂接触,生成包括低碳烯烃、c4烃的气相物流和待生催化剂,然后经过加速管10加速后与设置于加速管上方的弧形挡板16-1接触,弧形挡板的弧度为120
°
,上凸型,挡板中心最高点与加速管出口之间的距离为加速管高度的1/8。56%的固体催化剂运行轨迹发生120℃的转变,剩余的催化剂和气体经过旋风分离器12分离后,气相物流经管线14进入分离工段,待生催化剂至少分为三部分,第一部分经反应器外取热器4取热后返回快速床反应区2的底部,第二部分经反应器循环斜管6-1返回快速床反应区,第三部分进入汽提器17汽提后经待生斜管(图中未显示)进入再生器再生,形成再生催化剂,再生催化剂经脱气后经再生斜管15进入快速床反应区2,再生斜管15出口设有固相进料分布设备19,所述固相进料分布设备19沿流化床反应器径向水平布置,将再生催化剂均匀分布于流化床反应器反应区的径向平面上。
[0083]
发生运行轨迹改变的催化剂量计算方法如下:
[0084]
发生运行轨迹改变的催化剂量=反应区出口的催化剂总量-不发生运行轨迹转变的催化剂量。
[0085]
其中,反应区出口的催化剂总量是已测的;不发生运行轨迹转变的催化剂是跑到稀相空间(沉降区)的,通过稀相空间的密度(可实时检测)计算出来。甲醇原料(甲醇纯度95wt%)进入快速流化床反应区,与sapo-34分子筛催化剂接触,流化床反应区工艺条件为:反应温度480℃,反应表压为0.15mpa,取样分析结果表明,甲醇转化率为99.96%,乙烯 丙烯碳基选择性为84.54%。
[0086]
【实施例2】
[0087]
如图2所示,主要为甲醇的原料进入快速床反应区2,与包括硅铝磷分子筛的催化剂接触,生成包括低碳烯烃、c4烃的气相物流和待生催化剂,然后经过加速管10加速后进入气固快速分离旋风分离器16-2,85%的固体催化剂运行轨迹发生180℃的转变,剩余的催化剂和气体经过旋风分离器12分离后,气相物流经管线14进入分离工段,待生催化剂至少分为三部分,第一部分经反应器外取热器4取热后返回快速床反应区2的底部,第二部分经反应器循环斜管6-1返回快速床反应区,第三部分进入汽提器17汽提后经待生斜管进入再生器再生,形成再生催化剂,再生催化剂经脱气后经再生斜管15进入快速床反应区2,再生斜管15出口设有固相进料分布设备19,所述固相进料分布设备19沿流化床反应器径向水平布置,将再生催化剂均匀分布于流化床反应器反应区的径向平面上。
[0088]
甲醇原料(甲醇纯度95wt%)进入快速流化床反应区,与sapo-34分子筛催化剂接触,流化床反应区工艺条件为:反应温度480℃,反应表压为0.15mpa,取样分析结果表明,甲醇转化率为99.99%,乙烯 丙烯碳基选择性为85.04%。
[0089]
【实施例3】
[0090]
如图3所示,主要为甲醇的原料进入快速床反应区2,与包括硅铝磷分子筛的催化剂接触,生成包括低碳烯烃、c4烃的气相物流和待生催化剂,然后经过加速管10加速后进入气固快速分离旋风分离器16-2,85%的固体催化剂运行轨迹发生180℃的转变,剩余的催化剂和气体经过旋风分离器12分离后,气相物流经管线14进入分离工段,待生催化剂至少分为三部分,第一部分经反应器外取热器4取热后返回快速床反应区2的底部,第二部分经溢流管6-2返回快速床反应区,第三部分进入汽提器17汽提后经待生斜管进入再生器再生,形成再生催化剂,再生催化剂经脱气后经再生斜管15进入快速床反应区2,再生斜管15出口设有固相进料分布设备19,所述固相进料分布设备19沿流化床反应器径向水平布置,将再生催化剂均匀分布于流化床反应器反应区的径向平面上。
[0091]
甲醇原料(甲醇纯度95wt%)进入快速流化床反应区,与sapo-34分子筛催化剂接触,流化床反应区工艺条件为:反应温度480℃,反应表压为0.15mpa,取样分析结果表明,甲醇转化率为99.98%,乙烯 丙烯碳基选择性为84.95%。
[0092]
【实施例4】
[0093]
如图4所示,主要为甲醇的原料进入快速床反应区2,与包括硅铝磷分子筛的催化剂接触,生成包括低碳烯烃、c4烃的气相物流和待生催化剂,然后经过加速管10加速后进入倒l型弯管16-3,99.9%的固体催化剂运行轨迹发生180℃的转变,剩余的催化剂和气体经过旋风分离器12分离后,气相物流经管线14进入分离工段,待生催化剂至少分为三部分,第一部分经反应器外取热器4取热后返回快速床反应区2的底部,第二部分经溢流管6-2返回快速床反应区,第三部分进入汽提器17汽提后经待生斜管进入再生器再生,形成再生催化剂,再生催化剂经脱气后经再生斜管15进入快速床反应区2,再生斜管15出口设有固相进料
分布设备19,所述固相进料分布设备19沿流化床反应器径向水平布置,将再生催化剂均匀分布于流化床反应器反应区的径向平面上。
[0094]
甲醇原料(甲醇纯度95wt%)进入快速流化床反应区,与sapo-34分子筛催化剂接触,流化床反应区工艺条件为:反应温度480℃,反应表压为0.15mpa,取样分析结果表明,甲醇转化率为99.99%,乙烯 丙烯碳基选择性为85.32%。
[0095]
【实施例5】
[0096]
按照【实施例2】所述的条件和步骤,只是流化床反应区工艺条件为:反应温度400℃,反应表压为0.1mpa,取样分析结果表明,甲醇转化率为99.32%,乙烯 丙烯碳基选择性为83.06%。
[0097]
【实施例6】
[0098]
按照【实施例2】所述的条件和步骤,只是流化床反应区工艺条件为:反应温度480℃,反应表压为0.3mpa,取样分析结果表明,甲醇转化率为99.66%,乙烯 丙烯碳基选择性为83.78%。
[0099]
【实施例7】
[0100]
按照【实施例1】所述的条件和步骤,流化床反应区的气相物流和待生催化剂,然后经过加速管加速后与设置于加速管上方的弧形挡板接触,弧形挡板的弧度为150
°
,70%的固体催化剂运行轨迹发生150℃的转变,剩余的催化剂和气体经过旋风分离器12分离。取样分析结果表明,甲醇转化率为99.94%,乙烯 丙烯碳基选择性为85.09%。
[0101]
【比较例1】
[0102]
按照【实施例2】所述的条件和步骤,只是流化床反应器内不设置加速管和气固快速分离旋风分离器。反应器内催化剂不经历运行轨迹转变,催化剂跟随气体产物一起运行至沉降区的旋风分离器才分开,增加了二次反应。取样分析结果表明,甲醇转化率为99.99%,乙烯 丙烯碳基选择性为81.06%。
[0103]
【比较例2】
[0104]
按照【实施例1】所述的条件和步骤,流化床反应区的气相物流和待生催化剂,然后经过加速管加速后与设置于加速管上方的弧形挡板接触,弧形挡板的弧度为60
°
,30%的固体催化剂运行轨迹发生60℃的转变,剩余的催化剂和气体经过旋风分离器12分离。取样分析结果表明,甲醇转化率为99.91%,乙烯 丙烯碳基选择性为82.87%。
[0105]
【比较例3】
[0106]
按照【实施例2】所述的条件和步骤,只是流化床反应器为湍动流化床,气固在反应区内为返混状态,反应区出口不设置加速管和气固快速分离旋风分离器。取样分析结果表明,甲醇转化率为99.87%,乙烯 丙烯碳基选择性为80.45%。
[0107]
显然,采用本发明的方法,可以达到提高低碳烯烃收率的目的,具有较大的技术优势,可用于低碳烯烃的工业生产中。
再多了解一些
本文用于企业家、创业者技术爱好者查询,结果仅供参考。