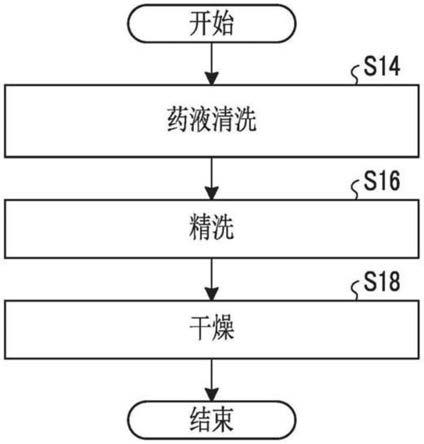
1.本发明涉及一种脱硝催化剂的再生方法及脱硝催化剂的再生系统,尤其涉及一种燃煤锅炉(coal
‑
fired boiler)用的已劣化脱硝催化剂的再生方法及再生系统。本技术主张基于2019年3月28日申请的日本专利申请案第2019
‑
063522号的优先权,并援用其所有的记载内容。
背景技术:
2.燃烧化石燃料、生物质燃料等燃料的设备,具备通过使燃料燃烧而去除产生废气中所含的氮氧化物的脱硝设备。这样的脱硝设备,具备促进氮氧化物的去除的脱硝催化剂。脱硝催化剂随着使用而性能劣化。因此,具备脱硝催化剂的脱硝设备,在维修时进行脱硝催化剂的更换或追加。并且,为了再利用脱硝催化剂,进行恢复催化剂性能的再生处理。
3.作为上述再生处理,已知有使用含有氢氟酸浓度0.3~3质量%,并将其温度维持在40~80℃的清洗液,清洗脱硝性能降低的催化剂的方法(专利文献1)。并且,已知还有用二氧化硅/氧化铝/硫酸钙系的中毒物质预先水洗活性降低的脱硝催化剂之后,使用有机酸与氟化物的混合液在常温下清洗之后,以水或稀薄的有机酸清洗,进一步以含有催化剂成分的水溶液清洗的方法(专利文献2)。
4.以往技术文献
5.专利文献
6.专利文献1:日本特开平10
‑
235209号公报
7.专利文献2:日本特开2011
‑
31237号公报
技术实现要素:
8.通过记载于上述文献的再生处理,可以在某种程度上恢复催化剂的脱硝性能。然而,通过这些再生处理,虽然可以恢复催化剂的脱硝性能,但是根据催化剂不同,存在因使用而上升的催化剂的so2氧化率仍然很高的问题。
9.鉴于上述情况,本发明的目的在于提供一种能够较高地恢复催化剂的脱硝性能,并且能够降低催化剂的so2氧化率的脱硝催化剂的再生方法及脱硝催化剂的再生系统。
10.为了实现上述目的,本发明的其一方式为脱硝催化剂的再生方法,所述再生方法包括:将脱硝催化剂浸渍于包含氟化合物与无机酸的药液的药液清洗步骤,从所述药液取出所述脱硝催化剂的步骤,及将从所述药液取出的所述脱硝催化剂,用包含有机酸的精洗液清洗的精洗步骤。
11.本发明的其一方式为脱硝催化剂的再生方法,所述再生方法包括:将脱硝催化剂浸渍于包含氟化合物与第1有机酸的药液的药液清洗步骤,从所述药液取出所述脱硝催化剂的步骤,及将从所述药液取出的所述脱硝催化剂,用包含第1无机酸的精洗液清洗的精洗步骤。
12.本发明的其一方式为脱硝催化剂的再生系统,所述再生系统具备:将脱硝催化剂
浸渍于包含氟化合物与无机酸的药液的药液清洗部;及将从所述药液取出的所述脱硝催化剂,用包含有机酸的精洗液精洗的精洗部。
13.本发明的其一方式为脱硝催化剂的再生系统,所述再生系统具备:将脱硝催化剂浸渍于包含氟化合物与第1有机酸的药液的药液清洗部;及将从所述药液取出的所述脱硝催化剂,用包含第1无机酸的精洗液精洗的精洗部。
14.根据本发明提供一种能够较高地恢复催化剂的脱硝性能,并且能够降低催化剂的so2氧化率的脱硝催化剂的再生方法及脱硝催化剂的再生系统。
附图说明
15.图1是表示第一~第三实施方式所涉及的脱硝催化剂的再生系统的概略结构的示意图。
16.图2是表示第一~第三实施方式所涉及的脱硝催化剂的再生方法的一例的流程图。
17.图3是表示第四实施方式所涉及的脱硝催化剂的再生系统的概略结构的示意图。
18.图4是表示第四实施方式所涉及的脱硝催化剂的再生方法的一例的流程图。
具体实施方式
19.以下,参考附图对优选的实施方式进行详细说明。本发明并不受实施方式的限定。在实施方式有多个的情况下,本发明也包含将各实施方式组合及置换各实施方式的一部分而构成的形态。
20.[1.第一实施方式]
[0021]
[1.1.再生系统]
[0022]
图1表示第一实施方式所涉及的脱硝催化剂的再生系统的概略结构。如图1所示,脱硝催化剂的再生系统100,至少具备药液清洗部104、精洗部106和干燥部108,以通过该结构执行用于恢复脱硝催化剂的催化剂性能的再生处理的方式构成。
[0023]
再生处理对象的脱硝催化剂,例如是使用于从燃煤锅炉所产生的包含二氧化硅(sio2)等硅(si)、铝(al)、钙(ca)、磷(p)、砷(as)、钠(na)、钾(k)等中毒物质的废气的脱硝而中毒,其催化剂性能降低的已使用的脱硝催化剂(以下,称为已使用脱硝催化剂)。这种脱硝催化剂具有格子状(蜂窝状)、板状、波浪(corrugate)状等形状,例如在二氧化钛(tio2)等载体上,负载着选自由钒(v)、钨(w)及钼(mo)构成的组中的至少1种活性成分而成。
[0024]
药液清洗部104至少具备用于用药液清洗脱硝催化剂的药洗槽,及对药洗槽内供给药液的供给机构。药液槽例如是比脱硝催化剂大,且能够储存液体的容器。药液清洗部104是以在药洗槽内将从脱硝设备取出的已使用脱硝催化剂浸渍于供给机构的药液,去除附着在脱硝催化剂的二氧化硅(sio2)等物质的方式构成。药液清洗部104可以是将脱硝催化剂投入于储存药液的水槽,使药液浸渍于脱硝催化剂的结构,也可以是通过淋浴喷嘴等对药洗槽内的脱硝催化剂淋上药液,而清洗脱硝催化剂的结构。
[0025]
精洗部106至少具备用于用精洗液(以下,称为清洗液)清洗脱硝催化剂的精洗槽、及对药洗槽内供给清洗液的供给机构。精洗槽例如是比脱硝催化剂大,且能够储存液体的容器。精洗部106是以将精洗槽内的脱硝催化剂用供给机构的清洗液精洗,去除或降低附着
在脱硝催化剂的药液的方式构成。精洗部106可以是将脱硝催化剂投入于储存精洗液的水槽,使清洗液浸渍于脱硝催化剂的结构,也可以是通过淋浴喷嘴等对精洗槽内的脱硝催化剂淋上清洗液,而清洗脱硝催化剂的结构。并且,精洗部106可以进一步具备用于将精洗过的脱硝催化剂进一步水洗,去除药液的精水洗部。
[0026]
干燥部108是以通过从精洗过的脱硝催化剂去除水分,而使脱硝催化剂干燥的方式构成。干燥部108至少具有加热机构,能够作成向脱硝催化剂通气加热至100℃以上的气体、例如130℃的气体,去除附着在脱硝催化剂的水分的结构。干燥部108能够从脱硝催化剂去除水分即可,可以是通过向脱硝催化剂输送干燥的空气而将水分从脱硝催化剂吹掉的结构,也可以是在被加热至100℃以上的空间使水分从脱硝催化剂蒸发的结构。
[0027]
并且,本实施方式所涉及的脱硝催化剂的再生系统100,可以任意选择地进一步具备未图示的预洗部。在这样的情况下,预洗部至少具备用于水洗脱硝催化剂的水槽,及对水槽内供给水的水供给机构。水槽例如是比脱硝催化剂大,且能够储存液体的容器。预洗部是以在水槽内将从脱硝设备取出的脱硝催化剂利用来自水供给机构的水进行水洗,去除附着在脱硝催化剂的表面及内部的异物、灰、可溶性的钙等中毒物质的方式构成。预洗部可以是将脱硝催化剂投入于储存水的水槽,使脱硝催化剂浸渍在水中的结构,也可以是通过淋浴喷嘴等对水槽内的脱硝催化剂淋上水,而清洗脱硝催化剂的结构。预洗部至少去除附着在脱硝催化剂的异物即可,也可以使用混合水与用于清洗脱硝催化剂的成分的液体。
[0028]
并且,预洗部可以任意选择地进一步具备未图示的抽真空槽和喷射水洗槽。抽真空槽至少具有用于清洗脱硝催化剂的水槽、盖子、及真空泵等抽吸机构,以将预洗后的脱硝催化剂投入于储存水的水槽,并浸渍在水中,将其内部作成密闭状态同时抽吸空气形成真空状态的方式构成。喷射水洗槽至少具备用于清洗脱硝催化剂的水槽和水供给装置,以通过将压缩空气辅助的高压水进行喷雾,而对脱硝催化剂的内部供给水的方式构成。本发明中,内部是由脱硝催化剂的形状而决定,包含废气流通的气体通气口。通过这样的处理,可以进一步去除主要堵塞于脱硝催化剂内部的异物。
[0029]
[1.2.再生方法]
[0030]
图2是表示第一实施方式所涉及的脱硝催化剂的再生方法的一例的流程图。图2所示的脱硝催化剂的再生方法,是可以通过在图1所示的脱硝催化剂的再生系统100的各部执行处理而实现。本实施方式所涉及的脱硝催化剂的再生方法,至少包括药液清洗步骤,取出脱硝催化剂的步骤,及精洗步骤。
[0031]
如图2所示,在药液清洗步骤(步骤s14)中,使用药液,将从脱硝设备内取出的已使用的脱硝催化剂,浸渍于用药液填满的药液清洗部104内。药液清洗处理可以是执行将脱硝催化剂投入于预先储存药液的药液清洗部104,也可以是在药液清洗部104内对脱硝催化剂淋上药液来执行。处理时间可以在例如15~60分钟的范围,药液温度可以在例如1~40℃的范围。在药液清洗处理后,从药液取出脱硝催化剂。通过药液清洗,抑制从脱硝催化剂溶出钒等活性成分去除附着在脱硝催化剂的二氧化硅(sio2)等物质。另外,通过药液清洗使脱硝催化剂的表面容易接触精洗液等液体,并且使液体容易浸入脱硝催化剂的内部,且降低脱硝催化剂的so2氧化率。
[0032]
在本实施方式中,药液至少含有氟化合物和无机酸。作为氟化合物,例示出氟化氢铵(nh4hf2)、氟化铵(nh4f)等。氟化合物,优选为氟化氢铵。氟化氢铵的含量,例如相对于药
液整体可以在1~10质量%的范围,优选在1~5质量%的范围。
[0033]
作为无机酸,例示出氨基磺酸(h3nso3)、盐酸(hcl)、硫酸(h2so4)、硼酸(h3bo3)等。无机酸优选为盐酸或盐酸与硼酸。硼酸能够作为防锈剂发挥功能。硼酸的含量,例如相对于药液可以在0.001~10质量%的范围。并且,无机酸优选为氨基磺酸。无机酸的含量,例如优选以使药液的ph值在ph1~6的范围的方式添加,更优选在ph1~3的范围。若药液的ph值在所述范围内,则也能够添加上述以外的无机酸。
[0034]
并且,药液优选含有表面活性剂,更优选为无机酸、氟化合物和表面活性剂的混合液。作为表面活性剂,优选非离子系或阴离子系表面活性剂。作为药液的表面活性剂,优选非离子系表面活性剂或阴离子系表面活性剂。作为非离子系表面活性剂活性剂,优选以聚氧乙烯聚氧丙二醇、聚氧乙烯衍生物、聚亚烷基二醇衍生物为主要成分的非磷酸系表面活性剂。聚氧乙烯聚氧丙二醇的环氧乙烷(eo)含量例如可以为39质量%。作为以聚氧乙烯聚氧丙烯二醇为主要成分的非磷酸系表面活性剂,可以例示出blaunon p
‑
101m(aoki oil industrial co.,ltd.制造)、emulgen pp
‑
220(kao corporation制造)、newpol pe
‑
61、newpol pe
‑
62、newpol pe
‑
64、newpol pe
‑
68、newpol pe
‑
71、newpol pe
‑
74、newpol pe
‑
75、newpol pe
‑
78、newpol pe
‑
108等(sanyo chemical industries,ltd.制造)、epan 410、epan 420、epan 450、epan 485、epan 680、epan 710、epan 720、epan 740、epan 750、epan 785、epan u
‑
103、epan u
‑
105、epan u
‑
108等(dks co.,ltd.制造)、pronon(注册商标)#056、pronon#101p、pronon#105、pronon#124、pronon#124p、pronon#154、pronon#188p、pronon#201、pronon#202、pronon#204、pronon#208、pronon#235、pronon#235p、pronon#237p、pronon#238、pronon#407p、unilube(注册商标)70dp
‑
950b、unilube 75de
‑
2620r等(nof corporation制造)、prestall em
‑
440、prestall em
‑
640、prestall rm
‑
183等(miyoshi oil&fat co.,ltd.制造)。并且,作为以聚亚烷基二醇衍生物为主要成分的非磷酸系表面活性剂,可以举出master air404(basf公司制造)、foam killer m
‑
14(aoki oil industrial co.,ltd.制造)、dispanol wi
‑
115(nof corporation制造)、unilube 50mb
‑
2、unilube 50mb
‑
5、unilube 50mb
‑
11、unilube 50mb
‑
26、unilube 50mb
‑
72、unilube 60mb
‑
2b、unilube 60mb
‑
16、unilube 60mb
‑
26、unilube 75de
‑
15、unilube 75de
‑
25、unilube 75de
‑
60、unilube 75de
‑
170、unilube 75de
‑
2620、unilube 75de
‑
3800、unilube 80de
‑
40u、unisafe ax
‑
22、unilube mb
‑
7、unilube mb
‑
19、unilube mb
‑
700、unilube mb
‑
7x、unilube mb
‑
11x、unilube 10ms
‑
250kb等(nof corporation制造)、trimin df
‑
300、trimin 610等(miyoshi oil&fat co.,ltd.制造)、rikei rk
‑
95(rikei chemicalindustry co.,ltd.制造)。并且,作为阴离子系表面活性剂,优选以聚氧化烯烷基醚磷酸酯等磷酸酯或其盐为主要成分的磷酸酯系表面活性剂。作为磷酸酯系表面活性剂,优选以聚氧乙烯烷基醚磷酸酯等磷酸酯为主要成分的表面活性剂,更优选以聚氧乙烯烷基(c8)醚磷酸酯
·
单乙醇胺盐为主要成分的表面活性剂。作为以磷酸酯或其盐为主要成分的磷酸酯系表面活性剂,可以举出antox ehd
‑
pna、newcol 100
‑
fcp、antox ehd
‑
400等(nippon nyukazai co.,ltd.制造)、plysurf a208f、plysurf a208n、plysurf a210d、plysurf m208f等(dks co.,ltd.制造)等。表面活性剂的量例如相对于药液整体可以为0.001~10质量%。
[0035]
在精洗步骤(步骤s16)中,使用精洗液使脱硝催化剂在精洗部106中进行精洗。精洗处理可以是通过将脱硝催化剂投入于预先储存清洗液的精洗部106来浸渍而执行,也可
以是在精洗部106内对脱硝催化剂淋上清洗液而执行。处理时间,例如可以在15~60分钟的范围,清洗液的温度,例如可以在1~40℃的范围。通过精洗去除或降低附着在脱硝催化剂的药液,并降低脱硝催化剂的so2氧化率。
[0036]
在本实施方式中,精洗液至少含有有机酸。作为有机酸,例示出水(h2o)、草酸(c2h2o4)、及这些的混合液。有机酸优选至少含有草酸。精洗液优选为水与1种以上的有机酸的混合液(以下,称为含有机酸水),更优选为水与草酸的混合液(以下,称为含草酸水)。有机酸的含量,例如相对于水可以在1~10重量%的范围。
[0037]
在干燥步骤(步骤s18)中,通过将脱硝催化剂移动到干燥部108,将水分从脱硝催化剂去除,而使脱硝催化剂干燥。在本步骤中,通过向脱硝催化剂通气加热至100℃以上的气体、例如130℃的气体,而去除附着在脱硝催化剂的水分。干燥方法可以将水分从脱硝催化剂去除的方法即可,可以是通过向脱硝催化剂输送干燥的空气而将水分从脱硝催化剂吹掉,也可以是在被加热至100℃以上的空间使水分从脱硝催化剂蒸发。
[0038]
并且,本实施方式所涉及的脱硝催化剂的再生方法,可以任意选择地进一步包含预洗处理。在这样的情况下,在预洗处理中,在药液清洗步骤之前,将从脱硝设备内取出的已使用的脱硝催化剂在预洗部进行水洗。处理时间,例如可以在3~30分钟的范围,水的温度,例如可以在1~40℃的范围。预洗处理可以是通过将脱硝催化剂投入于预先储存水的预洗部来浸渍而执行,也可以是在预洗部内对脱硝催化剂淋上水来执行。通过预洗脱硝催化剂,而将附着于脱硝催化剂的表面及内部的异物、灰、可溶性的钙等中毒物质去除,使脱硝催化剂的表面容易接触药液、精洗液等液体,并使液体容易浸入脱硝催化剂的内部。
[0039]
并且,预洗处理可以任意选择地进一步包含抽真空水洗处理和喷射水洗处理。抽真空水洗处理,例如可以通过将预洗处理后的脱硝催化剂浸渍于抽真空槽内的水同时抽吸槽内的空气而执行。并且,喷射水洗处理,例如可以通过将压缩空气辅助的高压水进行喷雾而执行。
[0040]
根据本实施方式,针对脱硝性能降低且so2氧化率增加的已使用的脱硝催化剂,可以恢复脱硝性能,而且大幅降低so2氧化率。其结果,在处理工厂的废气时,能够降低由废气中的so3所产生的硫酸铵((nh4)2so4)的量。另外,从防止大气污染的观点考虑,也是防止工厂废气中残留的so3所产生的紫烟排放到外部的对策。脱硝催化剂的so2氧化率,例如,与使用含有氨基磺酸的精洗液的情况比较,能够大幅降低10%左右。
[0041]
[2.第二实施方式]
[0042]
[2.1.再生方法]
[0043]
使用图2说明第二实施方式所涉及的脱硝催化剂的再生方法。本实施方式所涉及的脱硝催化剂的再生方法,主要在药液清洗步骤所使用的药液与精洗步骤所使用的精洗液的点上,与第一实施方式不同。省略与第一实施方式相同的结构的说明。
[0044]
在本实施方式中,在药液清洗步骤(步骤s14)中使用的药液至少含有氟化合物和第1有机酸。氟化合物可以优选采用前述的氟化合物。作为第1有机酸,例示出甲酸(ch2o2)、柠檬酸(c6h8o7)、草酸(c2h2o4)。第1有机酸优选为草酸。草酸的含量,例如相对于药液整体可以在1~20质量%的范围,优选在5~15质量%的范围。有机酸的含量,例如优选以使药液的ph值在ph1~6的范围的方式添加,更优选在ph1~3的范围。
[0045]
并且,药液优选含有表面活性剂,更优选为含有氟化合物、有机酸和表面活性剂。
表面活性剂,可以优选采用前述的表面活性剂。表面活性剂的含量,可以优选采用前述的量。
[0046]
在本实施方式中,在精洗步骤(步骤s16)中使用的精洗液至少含有第1无机酸。作为第1无机酸,例示出水(h2o)、氨基磺酸(h3nso3)、及这些的混合液。第1无机酸优选至少含有氨基磺酸。精洗液优选为水与1种以上的第1无机酸的混合液(以下,称为含无机酸水),更优选为水与氨基磺酸的混合液(以下,称为含氨基磺酸水)。第1无机酸的含量,例如相对于水可以在0.5~5mol/l的范围。
[0047]
根据本实施方式,针对脱硝性能降低且so2氧化率增加的已使用的脱硝催化剂,可以恢复脱硝性能,而且大幅降低so2氧化率。例如,与使用含有氨基磺酸的药液的情况比较,能够大幅降低20%左右的so2氧化率。
[0048]
[3.第三实施方式]
[0049]
[3.1.再生方法]
[0050]
使用图2说明第三实施方式所涉及的脱硝催化剂的再生方法。本实施方式所涉及的脱硝催化剂的再生方法,主要在药液清洗步骤所使用的药液的点上,与第二实施方式不同。省略与第二实施方式相同的结构的说明。
[0051]
在本实施方式中,在药液清洗步骤(步骤s14)中使用的药液至少含有氟化合物、第1有机酸和第2无机酸。氟化合物与第2无机酸可以优选采用第一实施方式的氟化合物及无机酸。另外,第1有机酸可以优选采用第二实施方式的第1有机酸。
[0052]
[4.第四实施方式]
[0053]
[4.1.再生系统]
[0054]
图3表示第四实施方式所涉及的脱硝催化剂的再生系统的概略结构。图3所示的脱硝催化剂的再生系统100a,可以与脱硝催化剂的再生系统100或本发明的其他实施方式进行组合。
[0055]
如图3所示,脱硝催化剂的再生系统100a具备预洗部102a、药液清洗部104a、精洗部106a、干燥部108、及催化剂输送装置112。催化剂输送装置112,从设置有脱硝催化剂的脱硝设备将脱硝催化剂取下,输送取下的脱硝催化剂的装置。催化剂输送装置112,可以包含输送催化剂的通过起重机、车辆、人力而移动的台车等。
[0056]
预洗部102a具备预水洗槽114、水供给装置116、废液罐117、抽真空槽118、废液罐119、及真空泵120。预水洗槽114是比再生处理对象的脱硝催化剂还大,且能够储存水的容器。水供给装置116具有储存水的罐及控制供水的阀等,以将预洗、抽真空所使用的水供给到各个预水洗槽114、抽真空槽118的方式构成。废液罐117是储存从预水洗槽114排出的水的容器。抽真空槽118是比再生处理对象的脱硝催化剂还大,且能够储存水的容器。抽真空槽118是以具有盖等,可以取出放入脱硝催化剂,且内部可以形成密闭状态的方式构成。废液罐119是储存从抽真空槽118排出的水的容器。真空泵120是以抽吸抽真空槽118内的空气的方式构成。预洗部102a可以是将预水洗槽114与抽真空槽118作成1个槽的结构,也可以是将废液罐117与废液罐119作成1个槽的结构。
[0057]
药液清洗部104a具备药洗槽122、药液供给装置123、及废液罐129。药洗槽122是比再生处理对象的脱硝催化剂还大,且能够储存药液的容器。药液供给装置123具有储存药液的罐及控制药液供给的阀等,以将药液清洗所使用的药液供给到药洗槽122的方式构成。废
液罐129是储存从药洗槽122排出的药液的容器。
[0058]
精洗部106a具备精洗槽130、供给装置132、及废液罐134。精洗槽130是比再生处理对象的脱硝催化剂还大,且能够储存精洗液的容器。供给装置132,具有储存本发明的精洗液的罐及控制精洗液供给的阀等,以对精洗槽130供给精洗液的方式构成。废液罐134是储存从精洗槽130排出的精洗液的容器。
[0059]
干燥部108可以优选采用与脱硝催化剂的再生系统100的干燥部108相同的结构。
[0060]
并且,预洗部可以任意选择地进一步具备用于进行喷射水洗的未图示的喷射水洗槽。喷射水洗槽,至少具备用于清洗脱硝催化剂的水槽和水供给装置,以通过将压缩空气辅助的高压水进行喷雾,而对脱硝催化剂的气体通气孔供给清洗水的方式构成。喷射水洗槽与预水洗槽及抽真空槽同样地,可以是共用水供给装置或废液罐的结构。
[0061]
[4.2.再生方法]
[0062]
图4是表示第四实施方式所涉及的脱硝催化剂的再生方法的一例的流程图。图4所示的脱硝催化剂的再生方法,可以通过在脱硝催化剂的再生系统100a的各部执行处理而实现。本实施方式所涉及的脱硝催化剂的再生方法,主要在进一步包含预洗步骤的点上,与第一~第三实施方式不同。
[0063]
如图4所示,在预洗步骤中,在脱硝催化剂的再生系统100a,通过催化剂输送装置112将脱硝催化剂从脱硝设备取出,且将取出的脱硝催化剂移动到预水洗槽114(步骤s22)。接着,在预水洗槽114内将脱硝催化剂进行水清洗(步骤s24)。在本处理中,可以是在将脱硝催化剂输送到空的预水洗槽114之后,通过水供给装置116对预水洗槽114供给水而执行,也可以是通过水供给装置116对预水洗槽114供给水,并将脱硝催化剂投入于已储存水的状态的预水洗槽114而执行。
[0064]
将水清洗后的脱硝催化剂通过催化剂输送装置112移动到抽真空槽118(步骤s26)。当将脱硝催化剂移动到抽真空槽118后,用真空泵120抽吸抽真空槽118内的空气而形成真空状态(步骤s28)。在本处理中,通过将抽真空槽118内形成真空状态,能够在异物堵塞于脱硝催化剂内部的情况下,抽吸异物。抽真空水洗可以通过使抽真空槽118内的气压降低到例如
‑
600mmhg以下而实施。当将抽真空槽118内为真空状态后,将抽真空槽118大气压开放,并通过催化剂输送装置112将脱硝催化剂从抽真空槽118移动到药洗槽122(步骤s30)。
[0065]
并且,预洗步骤进一步包括在抽真空水洗之后且药液清洗步骤之前进行喷射清洗。在喷射清洗中,在未图示的喷射水洗槽,通过将压缩空气辅助的高压水进行喷雾,而对气体通过孔供给清洗水。由此,能够可靠地去除主要残留于脱硝催化剂内部的异物。
[0066]
作为药液清洗步骤,将脱硝催化剂移动到药洗槽122(步骤s30)。将脱硝催化剂移动到药洗槽122之后,在药洗槽122内使脱硝催化剂浸渍于药液(步骤s32)。可以是将脱硝催化剂移动到药洗槽122之后,通过对药洗槽122内供给药液,而使配置于药洗槽122内的脱硝催化剂浸渍于药液,也可以是将脱硝催化剂移动到已储存药液的药洗槽122,而使配置于药洗槽122内的脱硝催化剂浸渍于药液。
[0067]
作为精洗步骤,在脱硝催化剂的再生系统100a中,当将脱硝催化剂浸渍于药液后,通过催化剂输送装置112将脱硝催化剂从药洗槽122移动到精洗槽130(步骤s34)。在脱硝催化剂的再生系统100a中,当将脱硝催化剂移动到精洗槽130后,在精洗槽130内将脱硝催化剂进行清洗(进行精洗)(步骤s36)。具体而言,从供给装置132对精洗槽130内供给精洗液,
用精洗液清洗脱硝催化剂。精洗处理可以是在排出精洗槽130内的精洗液的同时执行,也可以是在精洗槽130内储存精洗液而执行。
[0068]
接着,当进行脱硝催化剂的精洗后,移动到干燥部108,在干燥部108使脱硝催化剂干燥(步骤s38)。
[0069]
根据本实施方式,在脱硝催化剂的再生系统100a,通过反复使用药液和/或精洗液,能够有效率地使用药液和/或精洗液。利用药液和/或精洗液能够降低so2氧化率,因此即使多次使用这些也能够维持低的so2氧化率。在反复使用药液的情况下,在药洗槽122使脱硝催化剂浸渍于药液,之后从药洗槽122将脱硝催化剂取出之后,也不将浸渍脱硝催化剂的药液排出到废液罐129,而储存于药洗槽122。其后,使下一个脱硝催化剂移动到已储存药液的药洗槽122。由此,可以反复使用药液。并且,在第2次以后的药液的使用时,即使第2次以后的脱硝催化剂浸渍时,可以调整药液的成分。另外,作为代替的方法,可以在药洗槽122设置暂时储存药液的罐或使药液循环的循环机构,从药洗槽122将药液一度排出到罐,在使用时利用循环机构将药液从罐再度投入于药洗槽122内。并且,在该情况下,也可以作成在循环机构设置过滤器等,去除药液中的异物,也可以在循环机构设置浓度计和/或ph计,根据药液的浓度和/或ph值,来追加药液或药液的成分。并且,反复使用精洗液的情况下,通过采用与上述的药液的情况相同的结构及方法,可以反复使用精洗液。
[0070]
并且,根据本实施方式,精洗液为含有机酸水或含无机酸水、尤其是在含草酸水或含氨基磺酸水的情况下,可以更加提高再生处理时的催化剂性能恢复率。另外,精洗液为水的情况下,通过反复使用进行预洗或精洗时所使用的水,也可以有效率地使用水。通过有效率地利用水,可以减少废液的量。例如,可以作成将水洗后的脱硝催化剂从预水洗槽114、抽真空槽118、精洗槽130取出之后,均维持将水储存于预水洗槽114、抽真空槽118、精洗槽130的状态,使下一个脱硝催化剂移动,进行水洗。
[0071]
在前述的实施方式中例示出具备不同的槽作为进行预水洗、抽真空水洗、药液清洗、精洗、及任意选择的喷射水洗的处理的槽的结构的再生系统。本发明并不限定于此。也可以是设置1个能够实施脱硝催化剂的再生方法所相关联的各步骤的槽。例如,可以是将预水洗槽、抽真空槽、及精洗槽作成1个槽的结构,也可以是将这些的废液罐作成1个罐的结构。并且,例如,预洗部可以是将预水洗槽、抽真空槽、与喷射水洗槽作成1个槽的结构,也可以是将这些的废液罐作成1个罐的结构。
[0072]
并且,在前述的实施方式中例示出从脱硝设备取下脱硝催化剂而进行处理的再生系统及再生方法。本发明并不限定于此。将脱硝催化剂设置于脱硝设备的状态下,也可以直接进行脱硝催化剂的再生处理。在该情况下,对脱硝设备供给水、药液和/或精洗液,从脱硝设备回收废液。
[0073]
并且,前述的实施方式所涉及的脱硝催化剂的再生系统,也可以进一步具备用于调整药液和/或精洗液的温度的温度调整机构。通过设置这样的温度调整机构,能够控制药洗和/或精洗处理中的温度。可以将浸渍在脱硝催化剂时的处理温度,用温度调整机构维持在常温,或比常温还高。
[0074]
实施例
[0075]
以下,根据实施例更具体地说明本发明。本发明所涉及的脱硝催化剂的再生方法及脱硝催化剂的再生系统,并不限定于以下的实施例。
[0076]
1.催化剂再生的评价
[0077]
在实验室规模上,对脱硝催化剂用不同的药液和精洗液实施脱硝催化剂的再生方法,评价各个情况下的脱硝率、脱硝k值、脱硝恢复率(再生处理后的脱硝性能/新品时的脱硝性能:k/k0)及so2氧化率。作为脱硝性能的指标,采用催化剂的反应速度常数。作为脱硝催化剂,以在实机发电工厂进行50,000小时脱硝处理后的脱硝催化剂为供试试样。脱硝催化剂以二氧化钛(tio2)为主要成分,并在此负载五氧化钒(v2o5)与氧化钨(wo3)的蜂窝催化剂。并且,为了比较,也评价新品的脱硝催化剂。
[0078]
1.1.药液
[0079]
在实施例1中,使用氟化铵以氟化氢成分计算为1质量%,作为无机酸的氨基磺酸为0.33mol/l,作为表面活性剂聚氧乙烯聚氧丙二醇为0.05质量%的比例混合的药液。在实施例2中,使用氟化铵以氟化氢成分计算为1质量%,草酸为10.8质量%,作为表面活性剂聚氧乙烯聚氧丙二醇为0.05质量%的比例混合的药液。在比较例1中,使用与实施例1相同的药液。
[0080]
1.2.精洗液
[0081]
在实施例1中,使用了以氨基磺酸为1mol/l的方式制备的精洗液。在实施例2中,使用了以草酸为5.4质量%的方式制备的精洗液。并且,在比较例1中,使用与实施例1相同的精洗液。
[0082]
1.3.催化剂再生处理和催化剂性能的测量
[0083]
针对各实施例的催化剂,进行催化剂再生处理。并且,针对各催化剂的催化剂性能,使用管式流通反应试验装置以下述表1所示的评价条件进行了测量。
[0084]
[表1]
[0085]
评价条件
[0086][0087]
首先,针对上述催化剂,测量脱硝率与so2氧化率,求出反应速度常数k(脱硝k值)和脱硝性能恢复率(再生处理后的脱硝性能/新品时的脱硝性能:k/k0)。接着,针对因脱硝处理而造成催化剂性能降低的各催化剂,进行使用各例的药液及精洗液的清洗处理。清洗处理将各催化剂预洗3分钟之后,浸渍于药液60分钟进行药液清洗。针对药液清洗后的各催化剂,在常温下浸渍于精洗液30分钟进行精洗。精洗后,在110℃下干燥一晚。针对干燥后的再生处理后的各催化剂,再度测量脱硝率和so2氧化率,求出反应速度常数k(脱硝k值)和脱硝性能恢复率(再生处理后的脱硝性能/新品时的脱硝性能:k/k0)。将结果示于下述表2。
[0088]
[表2]
[0089]
清洗处理的结果
[0090][0091]
针对so2氧化率的降低,比起比较例1,实施例1的so2氧化率降低10%左右,实施例2的so2氧化率降低20%左右。并且,针对脱硝性能,实施例1及实施例2,均可在脱硝性能恢复
率为0.98~1.00的范围恢复脱硝性能。
[0092]
产业上的可利用性
[0093]
根据本发明所涉及的脱硝催化剂的再生方法及脱硝催化剂的再生系统,能够较高地恢复催化剂性能,并且能够降低催化剂的so2氧化率。
[0094]
符号说明
[0095]
100、100a
‑
脱硝催化剂的再生系统,104、104a
‑
药液清洗部,106、106a
‑
精洗部,108、108a
‑
干燥部,112
‑
催化剂输送装置,114
‑
预水洗槽,116
‑
水供给装置,118
‑
抽真空槽,120
‑
真空泵,122
‑
药洗槽,130
‑
精洗槽。
再多了解一些
本文用于企业家、创业者技术爱好者查询,结果仅供参考。