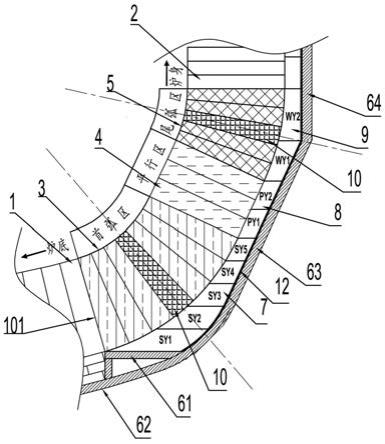
1.本发明涉及一种应力释放型炼钢转炉熔炼区耐火衬体及其砌筑方法,属于炼钢炉用耐火材料技术领域。
背景技术:
2.由于生产率高、冶炼质量好、建设费用低、节省劳动力、烟气除尘容易、耐材消耗低等优点,转炉炼钢已经发展成为当今的主流炼钢方法。尤其在我国,据相关部门统计,近几年转炉钢占全国总粗钢产量的80%以上。可见,发展转炉用耐火材料新技术、提高其炉衬使用寿命,对我国钢铁工业坚持走绿色、减排、低耗的健康发展之路具有重要的推动作用。目前,我国大中型转炉(公称容量大于100吨)炉衬中,炉底工作衬普遍采用球形镁碳砖环形法砌筑。
3.如图1所示,在传统转炉的熔炼区,大都采用纵向截面为直角梯形的翻身砖13来连接球形炉底末环砖1和熔池砖层14,该翻身砖层一般为3~5层不等。砌筑方法是,当球炉底末环砖1砌筑完成后,首先按设计图将永久层砖15紧贴炉壳6方向铺砌;然后按照标高h将最底层翻身砖砌筑面131找出,并用镁质捣打料16填充该砌筑面以下缝隙,且要求砌筑面131为水平面;再按照翻身砖层序依次从下往上砌筑,在保证砌筑面水平的情况下,每层翻身砖的斜角面紧贴炉底末环砖外侧面101,而翻身砖的炉外端与永久层砖15之间缝隙均采用镁质捣打料16捣实填充;最后,在最上层翻身砖132面上砌筑首层熔池砖14,并按设计图从下至上方向砌筑其他熔池砖层,从而完成整个熔炼区耐火炉衬的砌筑工作。
4.上述传统转炉熔炼区耐火炉衬结构,因其具有砖型设计相对简单、制作方便等优点而被广泛运用。但是,随着人们对高品质钢需求量不断增加,转炉炼钢正朝向炉壳大型化、钢水纯净化、冶金辅料低耗化、生产节奏快速化发展,一项项“低碳氧积冶炼技术”、“底吹强化搅拌技术”、“超低铁耗冶炼技术”等被逐步推广应用,这就对转炉炉衬提出了更高的质量要求。也正是在这种背景下,上述传统炉衬结构的缺点被逐渐暴露出来,成为了当前制约转炉炉衬寿命进一步提高的主要因素。概括起来有以下几点:(1)在砌筑最底层翻身砖前要标高,定位,找平,增加一定的砌筑难度,另外,一旦最底层翻身砖砌筑基准面找平操作不当,将直接影响整个转炉炉衬的砌筑质量;(2)提高了耐材制造商的生产成本。在传统熔炼区炉衬结构中,顶靠球形炉底末环砖层砌筑的翻身砖通常由3~5层构成,且正好位于转炉炉底炉壳和下锥段炉壳之间的三角转向区,可见,从下至上砖长逐步变长,另外,不同转炉间的翻身砖砖长相差较大,因此采用传统的翻身砖结构设计将大幅度降低了砖型通用率,给耐材制造商带来较大的模具管理及成本上的压力;(3)由于在砖型生产、砌筑过程中将不可避免地产生尺寸误差,在保证砌筑面水平度的前提下,常造成翻身砖的斜角面与炉底末环砖外侧面贴合不严,不仅影响了砌体的封闭性,存在着冶炼时“穿钢、漏钢”风险,还在两者之间形成了易热应力集中的“线面衔接”结构,导致熔炼区耐火衬体过快损毁,降低了炉衬的整体使用寿命;
(4)翻身砖被封闭在炉底砖、熔池砖、炉壳间的三角区域,各部分在升温过程中产生的膨胀效应不同步,且互相抵触与限制,从而造成了各部分接触处易形成热应力集中的问题。
5.在不断苛刻的冶炼环境中,上述传统砌体结构缺点正在日益凸显,尤其像(3)、(4)阐述的那样,因热应力集中、“天然”存在砖缝等原因已经在实际应用中发生了“底角深坑”、“熔炼区侵蚀过快”等严重影响转炉安全生产和整体寿命的现象。为了适应“低碳氧积冶炼”、“底吹强化搅拌”、“超低铁耗冶炼”等转炉炼钢新技术的应用与发展,上述问题亟待解决。
技术实现要素:
6.本发明要解决的技术问题是提供一种应力释放型炼钢转炉熔炼区耐火衬体及其砌筑方法,该耐火衬体以双圆弧型砌体实现砌筑面转向且在两圆弧间以平行砌筑面过渡的创新型结构,分别将圆弧型砌体的中间层设置为应力吸收缓冲层,该结构可最大限度地将转炉整个炉衬的热膨胀无死角地引导至炉口封口料层上,最大程度地实现了转炉衬体热状态下的应力释放。
7.为解决以上问题,本发明的具体技术方案如下:一种应力释放型炼钢转炉熔炼区耐火衬体,包括炉壳内的炉衬工作层和炉衬永久层,炉衬工作层由首弧区砌体、平行区砌体和尾弧区砌体依次排列的环形结构组成,并位于炉底环砖层和炉身环砖层之间进行平滑弧面过渡连接;每个区域的砌体均由纵向截面完全相同的高温耐火砖以面
‑
面无缝贴合形式组成的,在首弧区砌体和尾弧区砌体的中间层设有应力吸收缓冲层。
8.所述的首弧区砌体位于下锥段炉壳与炉底炉壳交界处,首弧区砌体的应力吸收缓冲层的中心线经过下锥段炉壳与炉底炉壳拐角区的中心位置;尾弧区砌体位于炉身段炉壳与下锥段炉壳的交界处,尾弧区砌体的应力吸收缓冲层的中心线经过炉身段炉壳与下锥段炉壳拐角区的中心位置;平行区砌体位于下锥段炉壳的中心位置。
9.所述的应力吸收缓冲层为化学成分满足mgo≥40%, c≥40%的超高碳镁碳砖。
10.所述的炉衬永久层采用若干层砌筑面均为水平面的高温耐火砖砌筑而成;在炉底炉壳上焊接永久层支撑平台,永久层支撑平台为纵向截面为倒“l”型的环状高强钢结构;永久层支撑平台的竖直面位于首弧区砌体首层砖的正下方,永久层支撑平台的上表面为水平面,并为上部永久层高温耐火砖砌筑的基础。
11.所述的永久层分为首弧区永久层、平行区永久层和尾弧区永久层三个区域,且首弧区永久层的炉内端面与首弧区砌体炉外端面无缝贴合;平行区永久层的炉内端面与平行区砌体的炉外端面无缝贴合;尾弧区永久层的炉内端面与尾弧区砌体炉外端面无缝贴合。
12.所述的首弧区砌体和尾弧区砌体内的高温耐火砖是纵向截面为扇环形、横向截面为等腰梯形的弧型砖;首弧区永久层和尾弧区永久层的高温耐火砖形状为纵截面的炉内端呈非对称凹弧状、炉外端呈斜角状,且横截面为等腰梯形;平行区砌体内的高温耐火砖纵截面为矩形、横截面为等腰梯形;平行区永久层的高温耐火砖的纵截面为平行四边形、横截面为等腰梯形。
13.所述的首弧区永久层设置为4~6层;平行区永久层为2~6层;尾弧区永久层为2层。
14.所述的永久层与炉壳之间设有隔热层。
15.采用上述炼钢转炉熔炼区耐火衬体的砌筑方法,包括以下步骤:步骤1、永久层支撑平台的焊接:先按照设计图的要求,采用满焊方式将永久层支撑平台焊接在炉底炉壳上,并保证支撑平台的水平度达到设计要求;步骤2、隔热层的铺砌:从步骤1搭建的永久层支撑平台上表面开始,在下锥段炉壳和炉身段炉壳炉内表面依次从下至上方向铺砌隔热层,厚度为10~30mm;步骤3、熔炼区永久层砌筑:在步骤1搭建的永久层支撑平台上表面均匀涂抹一层薄薄的镁质火泥,火泥层厚度≤3mm;然后按照设计要求依次铺设首弧区永久层、平行区永久层和尾弧区永久层,永久层炉外端面与隔热层顶紧;步骤4、首弧区砌体砖层砌筑:步骤4.1、用电动角磨机将炉底环砖层的外侧面进行打磨处理,保证平整度;步骤4.2、第1层首弧区砌体砖层的砌筑:用激光水平仪找出整个炉底环砖层的最低点,以最低点为起始点同时沿环形从顺、逆时针两个方向依次砌筑;砌筑时,每块高温耐火砖的砌筑始终以相邻砖间保持水平与平整为原则,要求炉外端面与永久层靠严顶实,而炉内端与其下层平齐,不得出现退台或凸起;步骤4.3、第2层~n
‑
1层的砌筑,其中n为首弧区砌体中间层数;从第二层开始,每层的砌筑起始位置仍是以其下层起始点位置沿环形顺时针或逆时针错开10~15
°
,其余方法与步骤4.2相同;步骤4.4、第n层的砌筑:首先测量第n层的中心线是否位于炉底炉壳与下锥段炉壳的拐角区中心位置,如果有偏差,偏差要求控制在
±
5mm内,如超出该范围,需要对n
‑
1层整个外侧面进行打磨处理;然后以n
‑
1层砌筑起始位置为基点,沿环形顺时针或逆时针旋转10~15
°
处为中间层的首块砖位置,同时沿环形从顺、逆时针两个方向依次砌筑,砌筑方法和要求与步骤4.3一致;步骤4.5、第n 1层~末层的砌筑,砌筑方法和要求与步骤4.3一致;步骤5、平行区砌体砖层砌筑:步骤5.1、用电动角磨机将首弧区砌体末环砖外侧面进行局部打磨处理,使该环形面0~360
°
范围内的平整度均满足设计要求;步骤5.2、以步骤5.1处理后的外侧面为砌筑面,从下至上逐层砌筑平行区各砖层;各层砌筑起始点位置仍然是以其下层起始点位置沿环形顺时针或逆时针错开10~15
°
获得,要求炉外端面与永久层靠严顶实,而炉内端与其下层平齐,不得出现退台或凸起;步骤6、尾弧区砌体砖层砌筑:步骤6.1、用电动角磨机将平行区砌体末环砖外侧面进行打磨处理,保证平整度;步骤6.2、第1层~n
‑
1层的砌筑,其中n为首弧区砌体中间层数;以步骤6.1处理后的环形侧面为砌筑面,以其下层起始点位置沿环形顺时针或逆时针错开10~15
°
进行砌筑;步骤6.3、第n层的砌筑:首先测量第n层的中心线是否位于下锥段炉壳与炉身段炉壳的拐角区中心位置,如果有偏差,偏差要求控制在
±
5mm内,如超出该范围,需要对n
‑
1层整个外侧面进行打磨处理;然后以n
‑
1层砌筑起始位置为基点,沿环形顺时针或逆时针旋转10~15
°
处为中间层的首块砖位置,同时沿环形从顺、逆时针两个方向依次砌筑,砌筑方法和要求与步骤6.2一致;步骤6.4、第n 1层~末层的砌筑,以n层外表面为基础进行砌筑,砌筑方法和要求与
步骤6.2一致;步骤7、尾弧区砌体末层砖上表面处理:利用激光水平仪和水平尺同时对环形面501进行水平度检测与校验,要求转炉径向上水平度≤2mm/m为合格,否则需要采用电动角磨机进行打磨处理;处理合格后的尾弧去砌体的端面作为炉身砖2的砌筑基础面,标志着整个熔炼区耐火炉衬的砌筑工作全部完成。
16.本技术采用上述技术方案具有以下技术效果:1、无论是在首弧区、平行区还是尾弧区,相同区域内的每层砖纵向剖面尺寸一致,且受炉壳尺寸变化影响小,提高了同一砖型在不同转炉上通用的程度,可为耐材制造商大大降低生产模具成本;2、从炉底末环砖到首弧区、平行区、尾弧区、最终到炉身砖层,无论砖型制造及砌筑误差如何变化,层与层之间的接触部分始终为“面
‑
面”无缝结构,提高了转炉熔炼区高温冶炼条件下的封闭性与安全性;3、在转炉熔炼区的两个砌筑面转向区采用了圆弧结构实现逐步转向,并始终维持圆弧与永久层面相融合或相切,避免了热状态下衬体在砌筑方向上的膨胀受阻,使得整个炉衬产生的热膨胀被全部引导至炉口封口料层中吸收与释放,另外,在首弧区和尾弧区的中间层均设置了一层超高碳镁碳砖层,可有效吸收转向区不同方向上的热膨胀,从而解决了不同方向上热膨胀不同步、不协调问题。因此,相较于传统衬体结构,本发明具有很好的热应力传导和释放能力;4、由于本发明提供的耐火衬体结构和炉底砖层、熔池砖层一样,不存在封闭空间的问题,不用特意标高、找平,只需沿着原有砌筑面按规定一层一层往上叠砌即可,因此施工难度低,砌筑质量易控制;5、由于本发明在双弧转向区均采用了不对称弧形砖砌筑永久层,该弧形砖砌筑完成后,靠近炉内端呈现出与首弧区或尾弧区完美贴合的弧形面,无需在其间采用镁质捣打料捣实填充,属于无缝无料砌筑,彻底杜绝砌体下沉现象,进一步提高转炉熔炼区安全性;6、正是由于本发明技术方案实现了前文所述的砌筑面始终保持“面
‑
面”无缝衔接、具有很好的热应力释放能力等有益效果,使得本发明彻底解决了传统转炉熔炼区易发生“底角深坑”的问题,大幅度降低了炉役期修补频率,有效减少了转炉日常维护工作及吨钢耐火材料消耗;7、给转炉炉膛带来了圆滑过渡并逐步开放的熔炼区,十分有利于由底吹气体带来的钢液流翻滚,加大了钢水搅拌效能,促进了冶金反应,大幅度提高了转炉生产效率。
附图说明
17.图1为图1是传统转炉熔炼区“翻身砖”式炉衬砌筑结构示意图。
18.图2为应力释放型炼钢转炉熔炼区耐火衬体的结构示意图。
19.图3a为首弧区砌体和尾弧区砌体砖型主视图。
20.图3b为首弧区砌体和尾弧区砌体砖型俯视图。
21.图4a为平行区砌体砖型主视图。
22.图4b为平行区砌体砖型俯视图。
23.图5a为首弧永久层和尾弧永久层砖型主视图。
24.图5b为首弧永久层和尾弧永久层砖型俯视图。
25.图6a为平行永久层主视图。
26.图6b为平行永久层俯视图。
具体实施方式
27.如图2所示,一种应力释放型炼钢转炉熔炼区耐火衬体,包括炉壳内的炉衬工作层和炉衬永久层,永久层与炉壳之间设有隔热层12,炉衬工作层由首弧区砌体3、平行区砌体4和尾弧区砌体5依次排列的环形结构组成,并位于炉底环砖层1和炉身环砖层2之间进行平滑弧面过渡连接;每个区域的砌体均由纵向截面完全相同的高温耐火砖以面
‑
面无缝贴合形式组成的,无缝贴合提高了转炉熔炼区高温冶炼条件下的封闭性与安全性;在首弧区砌体3和尾弧区砌体5的中间层设有应力吸收缓冲层10。由于相同区域内的每层砖纵向剖面形状与尺寸完全一致,且受炉壳尺寸变化影响小,这就提高了同一砖型在不同转炉上通用的程度,可为耐火材制造商大大降低生产模具成本;另外,在砌筑面转向区,工作层炉外端始终以平滑圆弧面与永久层炉内端面相融合或相切,避免了热状态下衬体在砌筑方向上的膨胀受阻,使得整个炉衬产生的热膨胀被全部引导至炉口封口料层中吸收与释放。
28.所述的首弧区砌体3位于下锥段炉壳63与炉底炉壳62交界处,首弧区砌体3的应力吸收缓冲层10的中心线经过下锥段炉壳63与炉底炉壳62拐角区的中心位置;尾弧区砌体5位于炉身段炉壳64与下锥段炉壳63的交界处,尾弧区砌体5的应力吸收缓冲层10的中心线经过炉身段炉壳64与下锥段炉壳63拐角区的中心位置;平行区砌体4位于下锥段炉壳63的中心位置。
29.所述的应力吸收缓冲层10为化学成分满足mgo≥40%, c≥40%的超高碳镁碳砖。所述的超高碳镁碳砖的制备技术已经在2020年11月25日申请、专利号为202011341444.3、发明名称为《一种碳含量大于40%的超高碳镁碳砖及其制备方法》的专利中获得公开,该超高碳镁碳砖具有足够小的热膨胀、足够强的导温能力、热应力吸收、传导、释放能力和足够大的韧性的特点,可有效吸收转向区不同方向上的热膨胀,从而解决了不同方向上热膨胀不同步、不协调问题。
30.所述的炉衬永久层采用若干层砌筑面均为水平面的高温耐火砖砌筑而成,在炉底炉壳62上焊接永久层支撑平台61,永久层支撑平台61为纵向截面为倒“l”型的环状高强钢结构;永久层支撑平台61的竖直面位于首弧区砌体3首层砖的正下方,永久层支撑平台61的上表面为水平面,并为上部永久层高温耐火砖砌筑的基础。这种高强钢支撑平台结构,可为永久层提供持续稳定的支撑作用,从而保证了工作层在整个炉役过程不下沉、不滑移,提高了转炉熔炼区的安全性能!所述的永久层分为首弧区永久层7、平行区永久层8和尾弧区永久层9三个区域,且首弧区永久层的炉内端面与首弧区砌体3炉外端面无缝贴合;平行区永久层8的炉内端面与平行区砌体4的炉外端面无缝贴合;尾弧区永久层9的炉内端面与尾弧区砌体5炉外端面无缝贴合。双弧转向区均采用了不对称弧形砖砌筑永久层,该弧形砖砌筑完成后,靠近炉内端呈现出与首弧区或尾弧区完美贴合的弧形面,无需在其间采用镁质捣打料捣实填充,属于无缝无料砌筑,彻底杜绝砌体下沉现象,进一步提高转炉熔炼区安全性。
31.如图3a和图3b所示,所述的首弧区砌体3和尾弧区砌体5内的高温耐火砖是纵向截
面为扇环形、横向截面为等腰梯形的弧型砖;如图5a和图5b所示,首弧区永久层7和尾弧区永久层9的高温耐火砖形状为纵截面的炉内端呈非对称凹弧状、炉外端呈斜角状,且横截面为等腰梯形;如图4a和图4b所示,平行区砌体4内的高温耐火砖的纵截面为矩形、横截面为等腰梯形;如图6a和图6b所示,平行区永久层8的高温耐火砖的纵截面为平行四边形、横截面为等腰梯形。
32.所述的首弧区永久层7设置为4~6层;平行区永久层8为2~6层;尾弧区永久层9为2层。
33.所述的永久层与炉壳之间设有隔热层12。
34.该耐火衬体以双圆弧型砌体(double circular
‑
arc masonry)实现砌筑面转向且在两圆弧间以平行砌筑面(parallel masonry)过渡的创新型结构,本发明为能清晰描述该结构的显著形貌特点,选择以“double、circular、parallel”的首字母来命名,即“dc
‑
p”结构。
35.采用上述炼钢转炉熔炼区耐火衬体的砌筑方法,包括以下步骤:步骤1、永久层支撑平台61的焊接:先按照设计图的要求,采用满焊方式将永久层支撑平台61焊接在炉底炉壳62上,并保证支撑平台61的水平度达到设计要求;步骤2、隔热层12的铺砌:从步骤1搭建的永久层支撑平台上表面开始,在下锥段炉壳63和炉身段炉壳64炉内表面依次从下至上方向铺砌隔热层12,厚度为10~30mm;步骤3、熔炼区永久层砌筑:在步骤1搭建的永久层支撑平台上表面均匀涂抹一层薄薄的镁质火泥,火泥层厚度≤3mm;然后按照设计要求依次铺设首弧区永久层、平行区永久层和尾弧区永久层,永久层炉外端面与隔热层12顶紧;步骤4、首弧区砌体砖层砌筑:步骤4.1、用电动角磨机将炉底环砖层1的外侧面进行打磨处理,保证平整度;步骤4.2、第1层首弧区砌体砖层的砌筑:用激光水平仪找出整个炉底环砖层1的最低点,以最低点为起始点同时沿环形从顺、逆时针两个方向依次砌筑;砌筑时,每块高温耐火砖的砌筑始终以相邻砖间保持水平与平整为原则,要求炉外端面与永久层靠严顶实,而炉内端与其下层平齐,不得出现退台或凸起;步骤4.3、第2层~n
‑
1层的砌筑,其中n为首弧区砌体中间层数;从第二层开始,每层的砌筑起始位置仍是以其下层起始点位置沿环形顺时针或逆时针错开10~15
°
,其余方法与步骤4.2相同;步骤4.4、第n层的砌筑:首先测量第n层的保温砖中心线是否位于炉底炉壳62与下锥段炉壳63的拐角区中心位置,如果有偏差,偏差要求控制在
±
5mm内,如超出该范围,需要对n
‑
1层整个外侧面进行打磨处理;然后以n
‑
1层砌筑起始位置为基点,沿环形顺时针或逆时针旋转10~15
°
处为中间层的首块砖位置,同时沿环形从顺、逆时针两个方向依次砌筑,砌筑方法和要求与步骤4.3一致;步骤4.5、第n 1层~末层的砌筑,砌筑方法和要求与步骤4.3一致;步骤5,平行区砌体砖层砌筑:步骤5.1、用电动角磨机将首弧区砌体末环砖外侧面进行局部打磨处理,使该环形面0~360
°
范围内的平整度均满足设计要求;步骤5.2、以步骤5.1处理后的外侧面为砌筑面,从下至上逐层砌筑平行区各砖层;
各层砌筑起始点位置仍然是以其下层起始点位置沿环形顺时针或逆时针错开10~15
°
获得,要求炉外端面与永久层靠严顶实,而炉内端与其下层平齐,不得出现退台或凸起;步骤6、尾弧区砌体砖层砌筑:步骤6.1、用电动角磨机将平行区砌体4末环砖外侧面进行打磨处理,保证平整度;步骤6.2、第1层~n
‑
1层的砌筑,其中n为首弧区砌体中间层数;以步骤6.1处理后的环形侧面为砌筑面,以其下层起始点位置沿环形顺时针或逆时针错开10~15
°
进行砌筑;步骤6.3、第n层的砌筑:首先测量第n层的中心线是否位于下锥段炉壳63与炉身段炉壳64的拐角区中心位置,如果有偏差,偏差要求控制在
±
5mm内,如超出该范围,需要对n
‑
1层整个外侧面进行打磨处理;然后以n
‑
1层砌筑起始位置为基点,沿环形顺时针或逆时针旋转10~15
°
处为中间层的首块砖位置,同时沿环形从顺、逆时针两个方向依次砌筑,砌筑方法和要求与步骤6.2一致;步骤6.4、第n 1层~末层的砌筑,以n层外表面为基础进行砌筑,砌筑方法和要求与步骤6.2一致;步骤7、尾弧区砌体末层砖上表面处理:利用激光水平仪和水平尺同时对环形面501进行水平度检测与校验,要求转炉径向上水平度≤2mm/m为合格,否则需要采用电动角磨机进行打磨处理。处理合格后的尾弧去砌体的端面作为炉身砖2的砌筑基础面,标志着整个熔炼区耐火炉衬的砌筑工作全部完成。
36.以下将结合具体实施例来进一步阐述本发明技术方案的具体实施方法和所能达到的有意效果。
37.实施例1将本发明用于国内某大型钢铁公司210吨转炉上国内某大型钢铁公司主要以saph400系列热轧薄板和40crh系列合金棒材为主打产品,为了降低钢中夹杂物含量,提高产品质量,该公司在其210吨转炉冶炼时通常采用远低于产品碳含量标准来进行终点拉碳,并要求全程炉役维持底吹高强度搅拌,最终创造了终点温度经常高于1700℃、钢水过氧化、熔炼区钢水对炉衬冲刷动能大、终渣氧化性强、炉衬渣层薄等严重影响炉衬寿命的恶劣条件。针对上述冶炼条件,本实施例将本发明技术方案用于在该转炉熔炼区耐火衬体的构建上。在本实施例中,首弧区、平行区、尾弧区的工作层与永久层的结构特点及各部位的连接方式、砌筑方法等与前文所描述的技术方案一致,此处不作赘述,但为了能更好地说明本发明在本实施例中所起到的有益效果,以下具体技术信息有必要列出:炉底工作层选用mt
‑
14b镁碳砖,砖长为1000mm;首弧区砌体3共7层,由砖长为1000mm、牌号为mt
‑
16a镁碳砖砌成,首弧区永久层共5层,经测量,其炉内端圆弧半径实际值为1522mm,而首弧区衬体炉外端半径为1520mm,通过塞尺测量,工作层与永久层之间缝隙小于1mm,圆弧贴合度符合设计要求;平行区砌体4共5层,每层层高150mm,由砖长为1000mm、牌号为mt
‑
16a镁碳砖砌成,平行区永久层共4层,经塞尺测量,工作层与永久层之间缝隙小于1mm,贴合度符合设计要求;尾弧区砌体5衬体共5层,由砖长为1000mm、牌号为mt
‑
16a镁碳砖砌成,尾弧区永久层共2层,经测量,其炉内端圆弧半径实际值为1579mm,而尾弧区衬体炉外端半径为1576mm,经塞尺测量,工作层与永久层之间缝隙小于1mm,圆弧贴合度符合设计要求;首弧区和尾弧区中间热应力吸收缓冲层由长度为1000mm的超高碳镁碳砖砌筑而成,该超高碳镁碳砖是以53%的电熔黑瓦片、43.5%的v96高碳混合目鳞片状石墨、2%的(al mg
tib2)复合抗氧化剂、1.5%的碳化硅晶须(增韧剂)为原料,外加3%热固性酚醛数值为结合剂,经1300吨摩擦压砖机生产而成,经检测,其化学成分为mgo=51.20wt%、c=42.15wt%。
38.对比例1:在采用本发明前,该转炉熔炼区采用了如附图1所示的传统的“翻身砖”式炉衬结构设计,为对比例1。在对比例1中,熔炼区工作层的长度和镁碳砖的材质和配方和实施例1完全一致,即:炉底镁碳砖长度为1000mm,牌号为mt
‑
14b,熔池镁碳砖长度也为1000mm,牌号为mt
‑
16a。
39.实施例1和对比例1的使用效果见下表:从表中可见,采用本发明后,该转炉寿命大幅度提高,增幅约46.3%,而补炉料用量和耐材单耗却大幅下降,降幅分别高达24.6%、36.1%,相对于对比例1,由于实施例1设计的熔炼区衬体砌筑面始终保持“面
‑
面”无缝衔接、且具有很好的热应力释放能力,整个炉役过程中,始终维持圆滑过渡的底角形貌,彻底解决了对比例1所出现的“深坑”问题。
40.实施例2将本发明用于国内某钢铁公司150吨转炉上该钢铁公司主要以q235、q195系列优质碳素结构钢等为主要生产钢种,属于低碳钢门类,产品形式主要是市场较为常见的带肋钢筋和高速线材。为了提高产品质量和生产效率,该公司150吨转炉冶炼同样采取了远高于行业平均水平的底吹强度,使得熔炼区钢水对炉衬产生强烈冲刷。另外,由于低碳钢冶炼要求,钢水终点[o]较高,终渣氧化强,渣子非常稀,不仅渐渣护炉效果差,还对炉衬砖具有异常的渗透侵蚀能力。针对上述冶炼条件,本实施例将本发明技术方案用于在该转炉熔炼区耐火衬体的构建上。在本实施例中,首弧区、平行区、尾弧区的工作层与永久层的结构特点及各部位的连接方式、砌筑方法等与前文所描述的技术方案一致,此处不作赘述,但为了能更好地说明本发明在本实施例中所起到的有益效果,以下具体技术信息有必要列出:炉底工作层选用mt
‑
12b镁碳砖,砖长为800mm;首弧区砌体3共7层,由砖长为800mm、牌号为mt
‑
14a镁碳砖砌成,首弧区永久层共5层,经测量,其炉内端圆弧半径实际值为1485mm,而首弧区衬体炉外端半径为1482mm,通过塞尺测量,工作层与永久层之间缝隙小于1mm,圆弧贴合度符合设计要求;平行区砌体4共4层,每层层高150mm,由砖长为800mm、牌号为mt
‑
14a镁碳砖砌成,平行区永久层共3层,经塞尺测量工作层与永久层之间缝隙小于1mm,贴合度符合设计要求;尾弧区砌体5共5层,由砖长为800mm、牌号为mt
‑
14a镁碳砖砌成,尾弧区永久层共2层,经测量,其炉内端圆弧半径实际值为1565mm,而尾弧区衬体炉外端半径为1563mm,经塞尺测量,工作层与永久层之间缝隙小于1mm,圆弧贴合度符合设计要求;首弧区和尾弧区中间热应力吸收缓冲层由长度为800mm的超高碳镁碳砖砌筑而成,该超高碳镁碳砖是以48%的电熔黑瓦片、48%的v96高碳混合目鳞片状石墨、2%的(al mg tib2)复合
抗氧化剂、2%的碳化硅晶须(增韧剂)为原料,外加3%热固性酚醛数值为结合剂,经1300吨摩擦压砖机生产而成,经检测,其化学成分为mgo=47.15wt%、c=46.53wt%。
[0041]
对比例2:在采用本发明前,该转炉熔炼区也采用了如附图1所示的传统的“翻身砖”式炉衬结构设计,为对比例2。在对比例2中,熔炼区工作层的长度和镁碳砖的材质和配方和实施例1完全一致,即:炉底镁碳砖长度为800mm,牌号为mt
‑
12b,熔池镁碳砖长度也为800mm,牌号为mt
‑
14a。
[0042]
实施例2和对比例2的使用效果见下表:从表中可见,采用本发明后,该转炉寿命大幅度提高,增幅约29.8%,而补炉料用量和耐材单耗却大幅下降,降幅分别高达14.3%、22.7%,相对于对比例2,由于实施例2设计的熔炼区衬体砌筑面始终保持“面
‑
面”无缝衔接、且具有很好的热应力释放能力,整个炉役过程中,始终维持圆滑过渡的底角形貌,彻底解决了对比例2所出现的“深坑”问题。
再多了解一些
本文用于企业家、创业者技术爱好者查询,结果仅供参考。