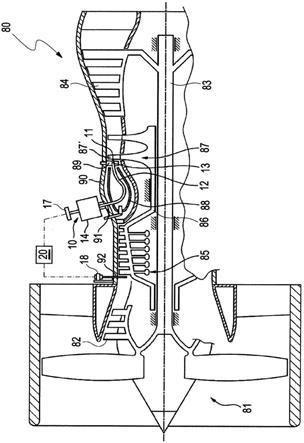
1.本发明涉及用于对构件、特别是燃气涡轮机、即例如飞机发动机中的涡轮机和/或压缩机叶片进行内孔窥视仪检查的方法和设备。
背景技术:
2.在现有技术中,已知各种用于对燃气轮机、特别是飞机发动机、如喷气发动机进行光学检查的方法,其中,内孔窥视仪穿过侧面的开口引入到完整安装的燃气轮机中,以便能够如此随后光学检查燃气轮机的内部。
3.由于运行中出现的负荷,相应的内孔窥视仪尤其用于检查飞机发动机的涡轮机和压缩机叶片。为此,将内孔窥视仪侧面地引入飞机发动机中进而在气体通道的内部中定位成,使得涡轮机或压缩机级的叶片以及发动机叶片的接口区域(在发动机叶片较大的情况下为叶片表面的预设的高度区域)完全位于内孔窥视仪的图像区域内。然后旋转涡轮机或压缩机级,由此能够由内孔窥视仪动态地检测相应级的全部发动机叶片。
4.在此,产的图像或视频拍摄被人工分析,以便表明发动机叶片的结构状态。在严重损坏的情况下,能够对单个发动机叶片进行手动静态三维检测,以便能够更精确地分析损坏。然而,三维检测非常复杂且耗时,使得其仅在特殊情况下执行。
技术实现要素:
5.本发明所基于的目的是创建一种用于对构件进行内孔窥视仪检查的方法和一种为此构造的设备,方法和设备具有对构件内部中的表面的改进的三维检测和自动化的损坏评估。
6.目的通过根据独立权利要求的方法和根据权利要求9的设备来实现。有利的改进形式是从属权利要求的主题。
7.相应地,本发明涉及一种用于对构件进行内孔窥视仪检查的方法,其中,使用立体内孔窥视仪来拍摄构件,其特征在于,设有以下步骤:
8.‑
通过立体内孔窥视仪产生两个立体部分图像;
9.‑
通过立体部分图像计算三维三角测量数据;
10.‑
在求出投影点的情况下将三维三角测量数据登记到由立体内孔窥视仪检测的构件的三维cad参考模型上;
11.‑
将从立体部分图像中求出的二维图像数据投影到求出的投影点的三维cad参考模型上;和
12.‑
通过对投影的二维图像数据进行图像分析和通过确定登记的三维三角测量数据相对于参考模型的偏差来求出损坏。
13.本发明还涉及一种用于对构件进行内孔窥视仪检查的设备,设备包括立体内孔窥视仪和与其连接的计算机单元,计算机单元能够访问包括待检查的构件的三维cad参考模型的存储器,其中,该设备构造用于执行根据本发明的方法。
14.首先,阐述一些结合本发明使用的术语。
[0015]“立体内孔窥视仪”是构造用于立体拍摄的内孔窥视仪。为此,立体内孔窥视仪具有两个彼此间隔开的图像获取单元,图像获取单元的拍摄锥头在拍摄平面中叠加,使得在拍摄平面中产生共同的拍摄区域,拍摄区域由两个拍摄锥头检测。两个图像获取单元的结果首先是“二维图像数据”,即图像点的网格形的布置,图像点具有颜色信息或者具有亮度信息(灰度级)。由于两个图像获取单元的距离和在拍摄区域上的从中产生的不同的观察角度,对于拍摄区域中的实际的每个点都能够借助于三角测量法求出与图像获取单元的距离作为“三维三角测量数据”。适合与此的方法以术语“立体视觉”已知。从图像信息中能够连同三维三角测量数据一起产生由内孔窥视仪拍摄的物体或图像区域的三维模型。
[0016]
立体内孔窥视仪能够基于“视频内孔窥视仪”的原理,其中,由在内孔窥视仪的自由端部处的光学装置拍摄的图像不经由光学线路引导至内孔窥视仪的另一端部处的目镜或相机,而是借助合适的半导体元件作为图像获取单元直接在自由端部处转换成电子的图像信息,电子的图像信息随后经由数据连接例如传输给显示器或传输给用于继续处理的计算机单元。相应的半导体元件、如光学电荷耦合器件(ccd)或互补氧化物半导体(cmos)传感器在现有技术中已知。还能够直接在光学半导体元件的区域中设有另外的集成电路,集成电路能够预处理由半导体元件检测到的电子图像信息,以便例如通过数据减少来减少待经由数据连接传输的数据量。能够通过压缩源自半导体元件的电子图像信息来实现数据减少。附加地或替代地,也可行的是,使得集成电路、例如“现场可编程门阵列”(fpga)从电子图像信息中去除以下数据,该数据不描绘最终的、由两个半导体元件检测到的共同的拍摄区域。下面描述的计算、例如三维三角测量数据的求出或二维图像数据的产生能够至少部分地通过相应的集成电路执行。其他的子步骤、例如将三维三角测量数据登记到三维cad模型上优选地通过外部计算机单元、例如计算机执行,计算机经由数据连接从立体内孔窥视仪获得为此所需的数据。
[0017]
在第一步骤中,通过立体内孔窥视仪,通过图像获取单元同时检测共同的拍摄区域或待拍摄的构件或其一部分的图像产生两个立体部分图像。同时的检测有利于,能够直接排除两个依次的拍摄之间的可能的时间变化,例因为待拍摄的构件被移动。如果图像获取单元是半导体元件,则优选的是,图像获取单元配备有全局快门,以便将运动伪影的风险降至最低。
[0018]
如果需要,能够根据预设的校准来校正由两个图像获取单元检测的立体部分图像,以便补偿可能的失真和/或执行色彩调准。相应的校正能够简化后续的计算和/或提高计算结果的准确性。
[0019]
然后,从两个可能校正过的立体部分图像中产生三维三角测量数据。为此所需的立体视觉计算和方法在现有技术中还是已知的,并且关于此点不需要任何进一步阐述。结果,在拍摄区域中的大量的点的计算之后,存在关于他们相对于图像获取单元的距离的信息。
[0020]
然后,将三维三角测量数据登记到由立体内孔窥视仪检测的构件的三维cad参考模型上。为此,在自动化方法中基于三维三角测量数据求出相对于三维cad参考模型的投影点,从投影点起,三维三角测量数据最佳地与三维cad参考模型一致。在自动化方法中直接从三维三角测量数据中获得投影点,能够在经由立体内孔窥视仪或其图像获取单元的以不
同方式求出的位置来确定投影点的位置时排除可能的不准确性。然而,通常有利的是,始于立体内孔窥视仪的例如可经由内孔窥视仪引导设备求出的位置进行自动化地求出投影点。即使由于测量不准确性等原因可求出的位置可能与最终的投影点不精确一致,则位置通常仍位于寻找的投影点附近。结果,与在用于求出投影点的任意的起点相比,始于立体内孔窥视仪的可求出的位置通常能够更快地求出期望的投影点。也能够在原则上考虑多个投影点的情况下通过将立体内孔窥视仪的可求出的位置预设为起点,来有助于投影点求出的唯一性。所求出的位置通常也包括立体内孔窥视仪的图像获取单元的定向。
[0021]
例如通过最小化三维三角测量数据与三维cad参考模型之间的偏差,能够求出投影点,在三维cad参考模型中逐步地改变投影点,直至调节三维三角测量数据的各个点与三维cad参考模型的偏差的期望的最小值,和/或直至偏差的标准偏差最小。
[0022]
如果求出了投影点,则可行的是,使得随后根据三维三角测量数据调整三维cad参考模型。换言之,在三维三角测量数据与三维cad参考模型之间得出的偏差例如因为从三维三角测量数据中得出拍摄的构件的变形而应该被传输到三维cad参考模型中,因此,然后三维cad参考模型提供构件的尽可能精确的图像。
[0023]
与三维cad参考模型是否根据三维三角测量数据进行匹配无关,然后始于投影点将二维图像数据投影到参考模型上,以便将三维cad参考模型纹理化。为此,能够使用立体部分图像之一。但是,优选的是,通过将两个立体部分图像彼此叠加产生二维图像数据,以便如此减小可能的阴影效果等。借助于从之前求出的投影点起进行二维图像数据的投影,实现二维图像数据到三维模型上的投影与构件的实际情况的良好一致。
[0024]
由于对于三维三角测量数据相对于三维cad参考模型的偏差以及对于二维图像数据到参考模型的投影的根据本发明达到的准确性,最后能够自动地求出所拍摄的构件处的损坏。在此,能够对投影到三维cad参考模型上的二维图像数据进行图像分析,利用图像分析能够例如根据图像数据相对于之前利用根据本发明的方法记录的构件状态或者通过例如在撕裂的情况下确定阴影来求出较小的损坏。登记的三维三角测量数据与原始的三维cad参考模型或之前利用根据本发明的方法记录的构件状态的偏差同样能够指示构件处的损坏。因为这些检验根据通过二维图像数据纹理化的三维cad参考模型进行,能够实现所有可能的损坏的精确定位。
[0025]
在许多情况下,无法通过利用立体内孔窥视仪的单次拍摄来检测构件。因此,优选的是,设有内孔窥视仪引导设备,利用内孔窥视仪引导设备能够可控地移动立体内孔窥视仪和尤其其图形检测单元。此外,优选的是,控制内孔窥视仪引导设备,使得依次地由立体内孔窥视仪检测构件的全部预设的区域,其中,分别经由立体部分图像对产生的三维三角测量数据和/或二维图像数据借助于参考模型组合。如上所述,经由参考模型能够准确地求出用于登记三维三角测量数据和/或投影二维图像数据的投影的投影点,使得能够在两次拍摄的三维三角测量数据和/或二维图像数据部分叠加时使用已知的方法、例如缝合方法,以便能够以高的准确性将不同拍摄的数据拼合成唯一的纹理化的三维cad参考模型。
[0026]
根据本发明的方法特别适用于燃气轮机、特别是飞机发动机的叶片的内孔窥视仪检查。在此,相应的叶片已知地组合成环形的涡轮机或压缩机级。
[0027]
由于涡轮机或压缩机级的叶片的通常的均匀性,通常无法单独通过立体内孔窥视仪的拍摄来确定涡轮机或压缩机级的哪些叶片实际上位于立体内孔窥视仪的拍摄区域内,
因此三维三角测量数据的登记以及将二维图像数据随后投影到三维cad参考模型上通常不是明确可行的。为了解决这个问题,优选的是,在将三维三角测量数据登记到参考模型上时,考虑将待拍摄的(多个)叶片相对于相应的级的旋转轴线的实际的旋转角度位置。换言之,投影点的确定参考相应拍摄的压缩机或涡轮机级的实际角位置进行,使得进行三维三角测量数据的最终登记以及将二维图像数据投影到涡轮机或压缩机级的三维cad参考模型的实际拍摄的(多个)发动机叶片上。
[0028]
在对涡轮机或压缩机级的发动机叶片进行内孔窥视仪检查时,优选的是,控制待拍摄的涡轮机或压缩机叶片的旋转角位置,使得检测涡轮机或压缩机级的所有涡轮机或压缩机叶片。由此,能够对涡轮机或压缩机级的所有叶片进行自动化检测和损坏分析。
[0029]
为了阐述根据本发明的设备,参考上述实施方案。
附图说明
[0030]
现在根据优选的实施方式参考附图示例性地描述本发明。附图示出:
[0031]
图1示出用于在飞机发动机处使用时进行内孔窥视仪检查的根据本发明的设备的一个实施例;
[0032]
图2示出图1中的设备的细节图;
[0033]
图3a、3b、3c示出检测到的和处理过的图像和三维三角测量数据的示意图;
[0034]
图4示出图1中的涡轮机叶片的三维cad参考模型的示意图;
[0035]
图5示出根据本发明的方法的示意图。
具体实施方式
[0036]
图1示出根据本发明的设备1在用于发动机80的内孔窥视仪检查期间的一个实施例。
[0037]
剖视图中所示的发动机80是双轴发动机,其中,风扇81以及低压压缩机82经由第一轴83与低压涡轮机84转动连接,而高压压缩机85经由第二轴86与高压涡轮机87转动连接。在高压压缩机85与高压涡轮机87之间布置有燃烧室88。
[0038]
为了检查高压涡轮机87的第一级的涡轮机叶片87',将立体内孔窥视仪10引入穿过发动机80的壁部90中的第一开口91,立体内孔窥视仪的自由端部在图2中详细示出。
[0039]
立体内孔窥视仪10设计为柔性的内孔窥视仪,其中,实际的杆11是可弯曲的并通过弯曲的引导管12被推动穿过发动机80的燃烧室88并穿过高压涡轮机87的导向叶片89之间。在此,立体内孔窥视仪10的位置主要通过引导管12的自由端部13确定,能够通过固定在发动机80的壁部90的外侧处的内孔窥视仪引导设备14控制该自由端部。同时,内孔窥视仪引导设备14提供关于立体内孔窥视仪10相对于涡轮机叶片87'的位置的信息,该位置可基于可在内孔窥视仪引导设备14中读取的数据来求出。
[0040]
在立体内孔窥视仪10的杆11的自由端部处设有两个彼此间隔开的图像获取单元15、16,图像获取单元朝向相同的拍摄区域,使得图像获取单元拍摄立体部分图像。图像获取单元15、16是具有全局快门或滚动快门的cmos或ccd传感器。
[0041]
立体内孔窥视仪10具有接口17,经由接口能够将两个图像获取单元15、16的图像数据、但是还有关于立体内孔窥视仪10的可求出的位置的信息传输给上级的计算机单元
20。经由接口17,立体内孔窥视仪10还能够从计算机单元20获得控制命令,以便在必要时借助内孔窥视仪引导设备14改变立体内孔窥视仪10的位置。
[0042]
此外,计算机单元20还与另一个内孔窥视仪18连接,该内孔窥视仪穿过发动机80的壁部90中的第二开口92引入,并且经由该内孔窥视仪能够观察高压压缩机85的叶片。在当前情况下,内孔窥视仪18用于确定高压压缩机85的叶片的旋转角位置,从中由于高压压缩机85以及高压涡轮机87与轴86的固定连接也能够求出高压涡轮机87的叶片87'的旋转角位置。高压涡轮机87的叶片87'由于通过来自燃烧室88的热气产生的充斥于那里的负荷而通常不具有可由立体内孔窥视仪10检测到的个性化特征,能够经由(其中有相当大的可能性的)高压压缩机85以及通过准确了解壁部中两个开口91、92的方位和可经由内孔窥视仪引导设备14求出的位置来确定:高压涡轮机87的第一级的哪个涡轮机叶片87'处于立体内孔窥视仪10的拍摄区域中。
[0043]
在图3a中,示例性地示出两个由立体内孔窥视仪10的图像获取单元15、16同时拍摄的立体部分图像。能够通过以名称“立体视觉”已知的方法将两个立体部分图像、或者在其校正以便校准可能的角度误差等之后通过计算机单元20组合成三维三角测量数据,如其在图3b中所示。
[0044]
借助于三维三角测量数据,该三维三角测量数据能够提供关于图像获取单元15、16相对于拍摄对象的相对位置的信息,然后根据三维三角测量数据求出相对于待拍摄的构件(在此为压涡轮机78的第一级的涡轮机叶片87')的三维cad参考模型30的投影点31。。
[0045]
相应的三维cad参考模型30在图4中示意性地示出。在此,三维cad参考模型30包括高压涡轮机87的第一级的所有涡轮机叶片87'并且基于发动机80的设计图。
[0046]
由于各个涡轮机叶片87'的均匀性,无法仅基于三维三角测量数据确定投影点31的明确位置。然而,能够通过发动机80的内部中的立体内孔窥视仪10的经由内孔窥视仪引导设备14求出的位置连同高压涡轮机87进而涡轮机叶片87'的可经由内孔窥视仪92求出的旋转角位置求出图像获取单元15、16相对于发动机叶片87'的至少近似的位置32,进而求出相对于三维cad参考模型30的投影点31。该近似的位置32用作为用于求出投影点31的实际位置的起点,其中,然后通常能够假设投影点31位于近似的位置32的附近。
[0047]
从如此求出的投影点31开始,将三维三角测量数据用于将三维cad参考模型30匹配于实际情况。换言之,三维cad参考模型30因此被改变成,使得其与三维三角测量数据尽可能一致。
[0048]
于是随后,通过叠加从立体部分图像中获得的二维图像数据从之前求出的投影点31投影到三维cad参考模型30上,由此对三维cad参考模型纹理化。结果在图3c中示出。
[0049]
特别地,如果依次创建高压涡轮机的第一级的涡轮机叶片87'的如此多的拍摄并且如上所述转移到三维cad参考模型30,使得存在整个有关的涡轮机级的完全纹理化的模型,则随后能够通过图像分析以及检测到的实际结构与原始的三维cad参考模型30的比较来执行自动化的损坏分析。因此,由于模型纹理的染色,能够确定各个涡轮机叶片87'中的小的损坏和特别是裂纹,而与原始三维cad参考模型30的偏差表明各个涡轮机叶片87'的变形,该变形可能需要更仔细地检查。通过三维三角测量数据的所描述的相应的登记以及二维图像数据到三维cad参考模型30的实际上位于立体内孔窥视仪10的拍摄区域中的涡流叶片上的投影,能够根据三维cad参考模型30来明确确定可能损坏的涡轮机叶片87'。
[0050]
在图5示出了如何完全自动化地检测图1示出的飞机发动机80的高压涡轮机87的第一级的涡轮机叶片87'并且能够检查损坏的方法流程100。
[0051]
在方法100的开始101处,假设经由内孔窥视仪引导设备14将在其位置方面可控的立体内孔窥视仪10引入到发动机80中,并且定向到待拍摄的涡轮机叶片87'之一上。此外,假设除了立体内孔窥视仪10的可经由内孔窥视仪引导设备14求出的位置之外,也(例如在第二内孔窥视仪18的辅助下)已知高压涡轮机87的第一级的涡轮机叶片87'的旋转角位置。
[0052]
在步骤102中,通过立体内孔窥视仪10产生立体部分图像。然后,将检测到的图像数据传输给计算机单元20(步骤103)。在计算机单元20中,借助于校准数据校正立体部分图像(步骤104)。
[0053]
随后,从立体部分图像中获得三维三角测量数据(步骤105),将三维三角测量数据登记到三维cad参考模型30上(步骤106)。为此,如上文结合图4所解释的那样,基于三维三角测量数据求出投影点31(步骤107),其中,如图4所表明的那样,能够迭代地求出。在成功登记三维三角测量数据进而求出投影点31之后,在步骤108中将在步骤102中检测到的立体部分图像的二维图像数据投影到三维cad参考模型30上。如此补充了纹理的三维cad参考模型30被存储在存储器中(步骤109)。
[0054]
随后,在步骤110中检查高压涡轮机87的第一级的涡轮机叶片87'的所有期望的区域是否已经被检测,其中,所有涡轮机叶片87'的完整拍摄也会是期望的。为此,例如能够根据三维cad参考模型30来检查有关的区域是否利用二维图像数据被纹理化,或者是否在有关的区域中登记三维三角测量数据。
[0055]
如果不是,则经由内孔窥视仪引导设备14和/或涡轮机叶片87'的旋转角位置来改变立体内孔窥视仪10的位置(步骤111),并且重复步骤102至110,直到完全检测期望的区域。
[0056]
如果在步骤110中确定检测了所有期望的区域,则在步骤112和113中基于在步骤109中存储在存储器中的三维cad参考模型执行损坏分析。为此,在步骤112中,分析为三维cad参考模型的纹理化而被处理的二维图像数据以及(在步骤113中)三维三角测量数据与原始三维cad参考模型的偏差,以便如此求出可能的损坏。
[0057]
该方法在步骤114结束,或者指示可能的损坏或者通知没有发现任何损坏。
再多了解一些
本文用于企业家、创业者技术爱好者查询,结果仅供参考。