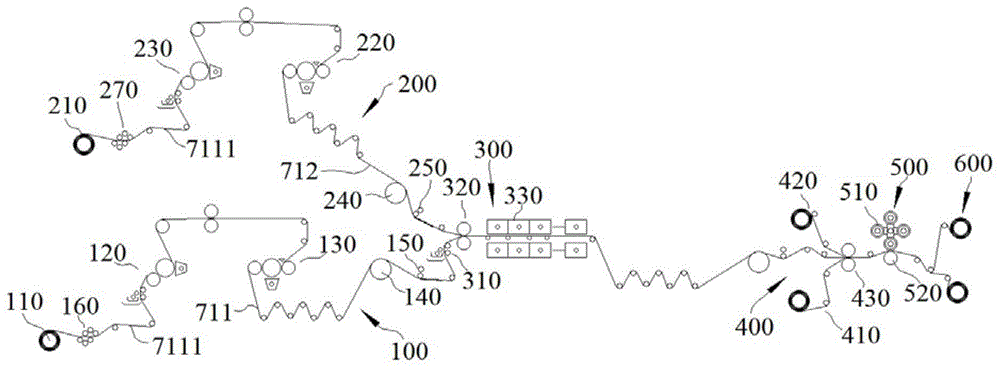
本申请涉及光学膜加工技术领域,尤其涉及一种一体化光学膜加工设备。
背景技术
目前,背光模组中通常会设置有两层增光膜,以对背光源进行增亮效果提升。现有技术中,通常是将两层增光膜单独裁切成型后,再将两层增光膜组装于背光模组中。然而,增光膜自身的厚度较薄,通常不足1mm,因此裁切增光膜存在较大的难度。相应的,在加工一背光模组时,则需要裁切两次增光膜,无疑增加了背光模组的加工难度,同时也会降低加工效率。
技术实现要素:
本申请提供了一种一体化光学膜加工设备,可降低背光模组的生产难度,提高生产效率。
本申请提供了:
一种一体化光学膜加工设备,包括第一供料单元、第二供料单元和贴合单元,所述第一供料单元的出料端和所述第二供料单元的出料端均连接至所述贴合单元的进料端;
所述第一供料单元用于向所述贴合单元输送第一光学膜,所述第二供料单元用于向所述贴合单元输送第二光学膜,所述贴合单元用于将所述第二光学膜贴合于所述第一光学膜上,以形成复合光学膜。
通过本申请提供的一体化光学膜加工设备可直接制得具有两层光学膜的复合光学膜,从而,在后续背光模组的加工过程中,仅需对复合光学膜进行一次裁切即可获得背光模组所需的光学膜片材,相应的,可减少加工工序。同时,由于复合光学膜相较于单层的光学膜较厚,更加方便裁切,对裁切要求会有所降低,也可降低背光模组的加工难度。由此,可明显提高背光模组的生产效率、降低生产难度。
在一些可能的实施方式中,所述贴合单元包括依次设置的上胶机构、压合机构和固化机构;其中,所述上胶机构与所述第一供料单元的出料端或所述第二供料单元的出料端连接,所述上胶机构用于在对应的光学膜表面涂布胶层;所述压合机构用于挤压所述第二光学膜和所述第一光学膜,以将所述第二光学膜贴合于所述第一光学膜,所述胶层位于所述第一光学膜和所述第二光学膜之间;所述固化机构用于固化所述胶层。
从而,可使第一光学膜和第二光学膜稳定粘接,避免第一光学膜和第二光学膜随意分离。
在一些可能的实施方式中,所述固化机构包括多个固化区,所述多个固化区沿所述复合光学膜的传输路径排布设置。从而,可对复合光学膜中的胶层逐步固化,确保固化质量。
在一些可能的实施方式中,所述固化机构包括紫外线固化区和/或热固化区。
在一些可能的实施方式中,所述固化机构包括若干个紫外线固化区和若干个热固化区,所述若干个紫外线固化区和所述若干个热固化区依次交替设置。
通过交错设置的紫外线固化区和热固化区,可提高胶层的固化效率,进而提高光学膜加工效率。
在一些可能的实施方式中,所述固化机构包括依次设置的预热段、固化段和应力释放段,所述预热段靠近所述压合机构设置,所述固化区为热固化区;所述预热段包括至少一所述固化区,所述固化段包括至少一所述固化区,所述应力释放段包括至少一所述固化区。由此,可使胶层逐步固化,且避免胶层出现崩裂等问题,确保第一保护膜和第二保护膜的粘接强度。
在一些可能的实施方式中,所述固化机构还包括有若干个第一送风机和若干个第二送风机,所述第一送风机和所述第二送风机分设于所述复合光学膜的两侧面;
沿所述复合光学膜的传输路径,所述第一送风机和所述第二送风机依次交替设置。由此可使复合光学膜悬浮于固化机构中,减少对复合光学膜的磨损。
在一些可能的实施方式中,所述上胶机构包括滚涂上胶组件、夹缝上胶组件和微凹上胶组件中的一种。
在一些可能的实施方式中,所述压合机构包括相对设置的第一压合轮和第二压合轮;
所述第一光学膜和所述第二光学膜经过所述压合机构时,所述第一压合轮和所述第二压合轮同时挤压所述第一光学膜和所述第二光学膜。
在一些可能的实施方式中,所述第一供料单元和/或所述第二供料单元包括有除尘机构,所述除尘机构用于去除对应所述光学膜表面的灰尘。从而可确保对应光学膜表面的洁净度,也可提高后续的光学膜产品的质量。
附图说明
为了更清楚地说明本申请实施例的技术方案,下面将对实施例中所需要使用的附图作简单地介绍,应当理解,以下附图仅示出了本申请的某些实施例,因此不应被看作是对范围的限定,对于本领域普通技术人员来讲,在不付出创造性劳动的前提下,还可以根据这些附图获得其他相关的附图。
图1示出了一些实施例中一体化光学膜加工设备的结构示意图;
图2示出了另一些实施例中一体化光学膜加工设备的结构示意图;
图3示出了一些实施例中第一供料单元的结构示意图;
图4示出了一些实施例中第一光学膜的结构示意图;
图5示出了一些实施例中滚涂上胶组件的结构示意图;
图6示出了一些实施例中夹缝上胶组件的结构示意图;
图7示出了一些实施例中微凹上胶组件的结构示意图;
图8示出了另一些实施例中第一供料单元的结构示意图;
图9示出了一些实施例中第二供料单元的结构示意图;
图10示出了一些实施例中贴合单元的结构示意图;
图11示出了一些实施例中复合光学膜的结构示意图;
图12示出了另一些实施例中复合光学膜的结构示意图;
图13示出了一些实施例中固化机构的结构示意图;
图14示出了另一些实施例中固化机构的结构示意图;
图15示出了一些实施例中固化机构中送风机的分布结构示意图;
图16示出了一些实施例中覆膜单元和裁切单元的结构示意图;
图17示出了一些实施例中切刀机构的结构示意图;
图18示出了一些实施例中裁切单元裁切光学膜料带时的结构示意图。
主要元件符号说明:
100-第一供料单元;110-第一输料轮;120-第一结构层成型机构;121-第一上料组件;1211-容器;1212-漏胶斗;1213-上胶轮;1214-涂布轮;1215-上胶板;1216-微凹涂布辊;122-第一成型组件;1221-第一前压轮;1222-第一成型轮;1223-第一UV固化装置;1224-第一后压轮;130-第二结构层成型机构;131-第二上料组件;132-第二成型组件;1321-第二前压轮;1322-第二成型轮;1323-第二UV固化装置;1324-第二后压轮;140-第二输料轮;150-第三除尘机构;160-第一除尘机构;161-粘尘组件;1611-粘尘轮;1612-粘尘纸轮;200-第二供料单元;210-第三输料轮;220-第三结构层成型机构;230-第四结构层成型机构;240-第四输料轮;250-第四除尘机构;260-调节轮;270-第二除尘机构;280-辅助轮;300-贴合单元;310-上胶机构;320-压合机构;321-第一压合轮;322-第二压合轮;330-固化机构;330a-预热段;330b-固化段;330c-应力释放段;331-固化区;3311-加热件;3312-UV灯;3321-第一送风机;3322-第二送风机;400-覆膜单元;410-第一保护膜输料机构;411-第六输料轮;412-第一张力检测展开轮;413-第一压制轮;420-第二保护膜输料机构;421-第七输料轮;422-第二压制轮;423-第二张力检测展开轮;430-粘贴机构;431-第三压合轮;432-第四压合轮;440-第五输料轮;450-第五除尘机构;500-裁切单元;510-切刀机构;511-切刀组;5111-切刀;512-刀架;513-第一转轴;514-第二转轴;520-支撑轮;600-收卷单元;610-第一收料轮;620-第二收料轮;700-光学膜料带;700a-子光学膜料带;710-复合光学膜;711-第一光学膜;7111-基材;7112-第一结构层;7113-第二结构层;712-第二光学膜;713-胶层;720a-第一保护膜;720b-第二保护膜;800-张紧摆轮;900-自由导轮;1000-张力检测轮。
具体实施方式
下面详细描述本申请的实施例,所述实施例的示例在附图中示出,其中自始至终相同或类似的标号表示相同或类似的元件或具有相同或类似功能的元件。下面通过参考附图描述的实施例是示例性的,仅用于解释本申请,而不能理解为对本申请的限制。在本申请的描述中,“多个”的含义是两个或两个以上,“多排”的含义是两排或两排以上,“多种”的含义是两种或两种以上,“多组”的含义是两组或两组以上,“多条”的含义是两条或两条以上,“若干个”的含义是一个、两个或两个以上,除非另有明确具体的限定。
如图18所示,建立笛卡尔坐标系,定义光学膜料带700的长度方向平行于x轴所示方向,定义光学膜料带700的宽度方向平行于y轴所示方向。可以理解的,以上定义仅是为了便于理解光学膜加工设备及光学膜料带700中各部件的相对位置关系,不应理解为对本申请的限制。
本申请提供了一种一体化光学膜加工设备,可用于光学膜的加工。在一些实施例中,光学膜可以是增光膜等光学薄膜中的一种。
如图1和图2所示,一体化光学膜加工设备包括有第一供料单元100、第二供料单元200和贴合单元300。其中,第一供料单元100的出料端和第二供料单元200的出料端均连接至贴合单元300的进料端。第一供料单元100可向贴合单元300供给第一光学膜711,第二供料单元200可向贴合单元300供给第二光学膜712。
贴合单元300可将第二光学膜712贴合于第一光学膜711上,从而形成复合光学膜710。
在光学膜的加工过程中,本申请提供的一体化光学膜加工设备可直接生产出具有两层光学膜的复合光学膜710。进而在后续背光模组的生产过程中,仅需要对复合光学膜710进行一次裁切,即可获得背光模组所需的光学膜片材,可减少光学膜的裁切次数,减少裁切工序。同时,复合光学膜710的厚度会大于单层的光学膜厚度,更加便于裁切操作,降低裁切难度,相应的,可降低加工难度,进一步提高加工效率。
可以理解的,一体化光学膜加工设备还可包括有机架(图未示)和控制器。一体化光学膜加工设备中的第一供料单元100、第二供料单元200和贴合单元300等各单元均可安装于机架一安装面上。在一些实施例中,机架的该安装面可垂直于地面设置。
在另一些实施例中,机架中用于安装各单元的安装面也可平行于地面或相对于地面倾斜设置。
一体化光学膜加工设备中,第一供料单元100、第二供料单元200和贴合单元300等各单元中的电性部件均可电连接至控制器,并由控制器控制一体化光学膜加工设备中各电性部件的工作。
如图1、图3和图4所示,在一些实施例中,第一供料单元100可用于制作第一光学膜711,并向贴合单元300供给第一光学膜711。具体的,第一供料单元100可用于在基材7111的一侧面制作第一结构层7112,以及在基材7111的另一侧面制作第二结构层7113。其中,基材7111设置有第一结构层7112的一侧面可记为第一侧面,基材7111设置有第二结构层7113的一侧面可记为第二侧面。在一些实施例中,第一结构层7112可以是扩散层,第二结构层7113可以是棱镜层。
如图1和图3所示,第一供料单元100可包括依次设置的第一输料轮110、第一结构层成型机构120、第二结构层成型机构130和第二输料轮140。其中,第二输料轮140远离第二结构层成型机构130的一侧可连接至贴合单元300的进料端。第一输料轮110转动安装于机架上,第一输料轮110可用于承载基材7111的料卷。可通过转动第一输料轮110,以使基材7111的料卷逐渐释放,以实现放料。
在一些实施例中,第一输料轮110与第一结构层成型机构120之间还设置有第一除尘机构160,用于除去基材7111表面的灰尘。如图3所示,第一除尘机构160可包括有至少一组粘尘组件161。在一些实施例中,第一除尘机构160可包括有两组粘尘组件161,两组粘尘组件161分设于基材7111的两侧面,两组粘尘组件161均可用于粘取基材7111对应侧面上的灰尘。
在另一些实施例中,第一除尘机构160还可包括一组、三组、四组等数量的粘尘组件161。
粘尘组件161可包括有粘尘轮1611和粘尘纸轮1612,其中,粘尘轮1611可设置有两个。当然,在另一些实施例中,粘尘轮1611也可设置有一个。两粘尘轮1611可沿基材7111的传输路径间隔设置,且两粘尘轮1611均与基材7111的同一侧面相接触。粘尘纸轮1612对应两粘尘轮1611中间位置进行设置,且粘尘纸轮1612同时与两粘尘轮1611背离基材7111的一侧相接触。可以理解的,粘尘轮1611和粘尘纸轮1612均转动设置,且粘尘轮1611和粘尘纸轮1612的表面均设置有粘尘膜。工作过程中,粘尘轮1611可粘取基材7111表面的灰尘,随后再由粘尘纸轮1612粘取粘尘轮1611表面的灰尘。实施例中,粘尘纸轮1612表面的粘接力大于粘尘轮1611表面的粘接力。同时,粘尘纸轮1612上已使用的粘尘膜可根据需要进行定期剥离,以便于粘尘纸轮1612上未使用的粘尘膜外露,以粘取粘尘轮1611上的灰尘,确保除尘效果。
在一些实施例中,第一除尘机构160还可包括有静电消除器(图未示),可用于消除基材7111表面的静电,同时,也可减少基材7111表面灰尘的附着。静电消除器可位于第一输料轮110和粘尘组件161之间。工作时,基材7111可先从静电消除器内经过,以消除基材7111上的静电;随后,基材7111再从粘尘组件161处经过,以去除灰尘。基材7111表面的静电消除后,也可降低灰尘在基材7111表面的附着力,更利于粘尘轮1611粘除基材7111表面的灰尘。
如图3所示,在一些实施例中,第一除尘机构160与第一结构层成型机构120之间还设置有自由导轮900和张力检测轮1000。其中,自由导轮900可用于支撑基材7111,以实现基材7111的传输。
张力检测轮1000可用于检测基材7111的张力,以便在发生异常时,一体化光学膜加工设备可及时作出调整。具体的,张力检测轮1000可由辊轮及设置于辊轮内的称重传感器组成,其中,称重传感器可用于检测第一光学膜711施加于辊轮上的作用力,从而反映出基材7111传输过程中的张力。可以理解的,称重传感器可位于张力检测轮1000靠近基材7111的一侧。
如图3所示,实施例中,第一结构层成型机构120可用于在基材7111的第一侧面制作第一结构层7112。具体的,第一结构层成型机构120可包括依次设置的第一上料组件121和第一成型组件122,第一上料组件121靠近第一输料轮110设置。其中,第一上料组件121用于在基材7111的第一侧面涂布第一胶水层,随后,可由第一成型组件122对第一胶水层进行成型及固化,以形成第一结构层7112。
如图5所示,在一些实施例中,第一上料组件121可以是滚涂上胶组件。具体的,第一上料组件121包括有容器1211、上胶轮1213和涂布轮1214。其中,容器1211可固定安装于机架上,容器1211可用于盛装胶水。上胶轮1213可转动地设置于容器1211中,涂布轮1214与上胶轮1213相切设置,且涂布轮1214凸出于容器1211的开口设置,以便涂布轮1214背离上胶轮1213的一侧可与基材7111的第一侧面接触。当然,涂布轮1214也可转动安装于机架上。工作过程中,随着上胶轮1213的转动,上胶轮1213可不断从容器1211中蘸取胶水,随后再传递至涂布轮1214。涂布轮1214在与基材7111接触时,可将胶水涂布于基材7111的第一侧面,以形成第一胶水层。实施例中,上胶轮1213可连接有驱动电机,用于驱动上胶轮1213转动。当然,在另一些实施例中,上胶轮1213也可由涂布轮1214带动转动,涂布轮1214可由基材7111带动转动。
在基材7111背离涂布轮1214一侧的位置,机架上可转动安装有两自由导轮900。沿基材7111的传输路径,涂布轮1214可对应于两自由导轮900的中间位置设置。两自由导轮900可用于支撑对应位置的基材7111,以便于涂布轮1214将胶水涂布于基材7111的第一侧面。同时,也可使涂布轮1214将胶水抵压于基材7111上,以便胶水粘接于基材7111的第一侧面。
在一些实施例中,第一上料组件121还包括有漏胶斗1212,用于承接涂胶过程中滴落的胶水,避免胶水随意滴落而污染设备。在重力方向上,漏胶斗1212可设置于涂布轮1214的下方。
如图6所示,在另一些实施例中,第一上料组件121还可以是夹缝上胶组件。具体的,第一上料组件121可包括有上胶板1215,其中,上胶板1215上设置有两端开口的夹缝。其中,夹缝的一开口端可对应基材7111设置,且位于基材7111上胶位置的上方。夹缝的另一开口端可连通盛装有胶水的容器,以供给胶水。从而,胶水可经过夹缝源源不断的流向基材7111表面,以在基材7111表面形成第一胶水层。可以理解的,基材7111与上胶板1215对应的位置,基材7111可沿水平方向设置或相对于水平方向有较小的倾角,以便胶水可顺利落在基材7111上,避免胶水从基材7111表面滑脱。当然,第一上料组件121还包括有漏胶斗1212,用于承接上胶时滴落的胶水。
如图7所示,在另一些实施例中,第一上料组件121还可选用微凹上胶组件。具体的,第一上料组件121可包括有容器1211和微凹涂布辊1216,其中,容器1211用于盛装胶水。微凹涂布辊1216转动设置于容器1211中,且微凹涂布辊1216凸出于容器1211的开口端设置,微凹涂布辊1216凸出于容器1211的部分可与基材7111表面接触。上胶时,微凹涂布辊1216可通过其表面的微凹结构携带胶水,在转动至与基材7111接触时,可将胶水涂布于基材7111的第一侧面上。微凹涂布辊1216也可连接相应的驱动电机驱动。相应的,基材7111背离微凹涂布辊1216的一侧可由自由导轮900支撑。当然,第一上料组件121还可包括有漏胶斗1212,用于承接上胶时滴落的胶水。
如图3所示,第一成型组件122可包括有转动安装的第一前压轮1221、第一成型轮1222和第一后压轮1224。第一前压轮1221、第一成型轮1222和第一后压轮1224可沿着基材7111的传输方向依次设置,其中,第一前压轮1221靠近第一上料组件121设置,基材7111可依次经过第一前压轮1221、第一成型轮1222和第一后压轮1224。其中,第一前压轮1221和第一后压轮1224均与基材7111的第二侧面接触贴合,第一成型轮1222与基材7111的第一侧面贴合,即第一成型轮1222可与第一胶水层接触。从而,可避免第一前压轮1221损坏第一胶水层。在一些实施例中,第一前压轮1221、第一成型轮1222和第一后压轮1224可由下至上依次设置。在另一些实施例中,第一前压轮1221、第一成型轮1222和第一后压轮1224也可沿着水平方向依次排布设置,如图8所示。当然,在另一些实施例中,不排除将第一前压轮1221、第一成型轮1222和第一后压轮1224所在连接线相对于水平面倾斜设置。
如图1和图3所示,在一些实施例中,第一前压轮1221和/或第一后压轮1224相对于第一成型轮1222活动设置,即第一前压轮1221和/或第一后压轮1224在机架上的位置可调。从而,可调节基材7111与第一成型轮1222之间包角大小,以满足不同加工工艺需要。示例性的,第一后压轮1224可沿着水平方向或竖直方向活动安装,即第一后压轮1224在水平或竖直方向上的位置可调。当第一后压轮1224沿着水平方向或竖直方向移动时,可调节基材7111与第一成型轮1222之间的包角。可以理解的,在确定第一后压轮1224的位置后,第一后压轮1224可通过插销等锁紧件定位于机架上的特定位置,第一后压轮1224仍可顺利自转。在一些实施例中,第一后压轮1224可连接有电缸等驱动件,可用于带动第一后压轮1224调节位置。
如图3和图4所示,第一成型轮1222的表面可设置有与第一结构层7112对应的结构,以便在基材7111经过第一成型轮1222时,可对第一胶水层成型。可以理解的,基材7111在传输过程中可始终处于张紧状态,在基材7111经过第一成型轮1222时,可在基材7111与第一成型轮1222的挤压作用下,使第一胶水层成型。
实施例中,第一成型组件122还包括有第一UV(Ultraviolet,紫外线)固化装置1223,第一UV固化装置1223可朝向第一成型轮1222设置,且靠近第一成型轮1222贴合基材7111的一侧。在紫外线的照射下,可使基材7111表面的第一胶水层固化,以在基材7111的第一侧面形成第一结构层7112。
在一些实施例中,第一UV固化装置1223内可设置有一排或多排UV灯管。当第一UV固化装置1223内设置多排UV灯管时,多排UV灯管可沿着基材7111的传输路径排布设置,多排UV灯管可设置成波长相等或不等的UV灯管。示例性的,第一UV固化装置1223内可包括有多排不同波长的UV灯管,第一UV固化装置1223可包括365nm、375nm、385nm、395nm、405nm等波长的UV灯管,可提高固化效率及质量。
如图3所示,在一些实施例中,第一结构层成型机构120与第二结构层成型机构130之间可设置有若干个自由导轮900,一方面可用于支撑、传输基材7111,另一方面,也可用于改变基材7111的传输路径。当然,在一些实施例中,第一结构层成型机构120与第二结构层成型机构130之间也可设置有张力检测轮1000,可用于检测基材7111的张力。第一结构层成型机构120与第二结构层成型机构130之间还设置有一辅助轮280,辅助轮280与一自由导轮900相对设置,基材7111可从辅助轮280与该自由导轮900之间穿过。辅助轮280可连接有驱动电机,用于带动辅助轮280转动。从而,可由辅助轮280带动基材7111移动,以为基材7111的传输提供动力。在一些实施例中,与辅助轮280相对的自由导轮900还可连接有电缸等驱动件,电缸可带动该自由导轮900靠近或远离辅助轮280,以调节辅助轮280和自由导轮900施加于对应基材7111的压力,进而可调节基材7111的传输速度。
进一步的,如图3所示,第二结构层成型机构130可包括第二上料组件131和第二成型组件132。第二上料组件131用于在基材7111的第二侧面涂抹胶水,以形成第二胶水层。
第二成型组件132包括转动安装的第二前压轮1321、第二成型轮1322和第二后压轮1324,第二前压轮1321、第二成型轮1322和第二后压轮1324可沿着基材7111的传输方向依次设置。在一些实施例中,第二前压轮1321和第二后压轮1324均可与基材7111的第一结构层7112相贴合,第二成型轮1322可与基材7111的第二侧面相贴合,第二成型轮1322可与基材7111上的第二胶水层相接触。可以理解的,第二成型轮1322上可设置有与第二结构层7113相对应的结构,以便在基材7111的第二侧面成型第二结构层7113。第二前压轮1321、第二成型轮1322和第二后压轮1324可沿着水平方向依次排布设置,且第二前压轮1321、第二成型轮1322和第二后压轮1324相互贴近,第二前压轮1321与第二成型轮1322之间的夹缝以及第二成型轮1322与第二后压轮1324之前的夹缝可允许基材7111顺利通过。实施例中,第二前压轮1321和第二后压轮1324也可相对于第二成型轮1322活动安装,以调节基材7111与第二成型轮1322之间的包角大小。
实施例中,第二后压轮1324也可连接有驱动电机,用于带动第二后压轮1324自转,进而再由第二后压轮1324带动基材7111移动,为基材7111的传输提供动力。
如图3和图4所示,在一些实施例中,第二上料组件131可以是滴胶机等设备,用于在基材7111的第二侧面涂抹胶水。第二上料组件131的滴胶口可朝向第二前压轮1321与第二成型轮1322之间的夹缝位置,且同时朝向基材7111的第二侧面。由此,可在基材7111移动至第二前压轮1321与第二成型轮1322之间时涂抹胶水,以在基材7111的第二侧面形成第二胶水层。随后,基材7111经过第二成型轮1322时,可在第二成型轮1322与基材7111的挤压作用下,使第二胶水层成型。
第二成型组件132还包括有第二UV固化装置1323,第二UV固化装置1323可朝向第二成型轮1322设置,且第二UV固化装置1323可位于第二成型轮1322贴合有基材7111的一侧,以便于第二胶水层成型后可在第二UV固化装置1323的作用下进行固化。由此,可在基材7111的第二侧面制得第二结构层7113,进而也可完成第一光学膜711的加工。实施例中,第二UV固化装置1323的结构可与第一UV固化装置1223的结构相同。
如图8所示,在另一些实施例中,第二成型组件132中的第二前压轮1321、第二成型轮1322和第二后压轮1324也可由上至下依次排布设置,且相对于竖直方向具有一定的倾角。相应的,第二上料组件131也可设置于第二前压轮1321的上方,以使胶水在重力作用下顺利滴落在基材7111上。
如图1和图3所示,实施例中,第二结构层成型机构130与贴合单元300之间还设置有张紧摆轮800和第二输料轮140,其中,张紧摆轮800靠近第二结构层成型机构130设置,基材7111可依次经过张紧摆轮800和第二输料轮140后进入贴合单元300。
其中,张紧摆轮800摆动安装于机架上。可以理解的,张紧摆轮800可包括有辊轮及连接于辊轮端部的摆臂,辊轮可通过摆臂悬吊摆动安装于机架上,同时,辊轮可相对于摆臂自由转动。通过张紧摆轮800的设置,可适应性调整第一光学膜711的张力,避免第一光学膜711受到的张力过大或过小。另外,通过移动张紧摆轮800,可调节第一光学膜711移动路径的长度,从而可调整第一供料单元100向贴合单元300的供料速度,以使第一供料单元100和第二供料单元200的供料速度一致,同时,也可使第一光学膜711和第二光学膜712的张力一致。实施例中,张紧摆轮800的数量可根据需要进行设置,示例性的,张紧摆轮800的数量可以设置成一个、四个、五个、六个、七个、八个等数量,在此不作具体限制。
进一步的,如图1和图10所示,第一供料单元100还包括有第三除尘机构150,第三除尘机构150可位于第二输料轮140与贴合单元300之间。第三除尘机构150可用于对第一光学膜711的表面进行除尘,以确保第一光学膜711表面洁净。实施例中,第三除尘机构150也可包括有相应的粘尘组件161和静电消除器,第三除尘机构150的结构可与第一除尘机构160的结构相同,在此不再赘述。
实施例中,第一供料单元100与贴合单元300之间还布设有一张力检测轮1000,具体的,该张力检测轮1000可位于第三除尘机构150与贴合单元300的进料端之间。张力检测轮1000可用于检测第一光学膜711的张力,以便一体化光学膜加工设备可根据需要及时调整第一光学膜711传输过程中的张力,避免损坏第一光学膜711,也可避免出现褶皱、不平整等问题,确保加工质量。
如图1、图9至图11所示,在一些实施例中,第二供料单元200可用于制作第二光学膜712,以向贴合单元300供给第二光学膜712。具体的,第二供料单元200可在对应基材7111的一侧面制作第二结构层7113,第二结构层7113可以是棱镜层。
具体的,如图9和图10所示,第二供料单元200可包括有依次设置的第三输料轮210、第二除尘机构270、第三结构层成型机构220、第四输料轮240和第四除尘机构250。其中,第三输料轮210可用于承载对应的基材7111料卷。第二除尘机构270可用于对该基材7111的表面进行除尘,第二除尘机构270的结构可与第一除尘机构160的结构相同,在此不再详述。
在一些实施例中,第二除尘机构270与第三结构层成型机构220之间还可设置有张力检测轮1000和多个自由导轮900,多个自由导轮900可沿基材7111的传输路径依次排布设置,张力检测轮1000靠近第二除尘机构270设置。同时,第二除尘机构270与第三结构层成型机构220之间也设置有另一辅助轮280,辅助轮280可位于一自由导轮900的上方,且辅助轮280可抵接于对应位置的基材7111背离自由导轮900的一侧。在一些实施例中,辅助轮280可连接有驱动电机,可用于带动该辅助轮280转动,从而再由辅助轮280驱动对应基材7111移动,为对应基材7111的传输提供动力。实施例中,与该辅助轮280相对的自由导轮900还可连接有电缸等驱动件,从而可由驱动件带动自由导轮900靠近或远离辅助轮280,以调节该辅助轮280和自由导轮900施加于对应基材7111的压力,进而可调节对应基材7111的传输速度。
第三结构层成型机构220可在对应基材7111的一侧面成型第二结构层7113,以制得第二光学膜712。实施例中,第三结构层成型机构220的结构可与第二结构层成型机构130的结构相同,在此不再赘述。其中,第三结构层成型机构220中的成型轮可与第二结构层7113相匹配。
如图9所示,第三结构层成型机构220与第四输料轮240之间还依次设置有张紧摆轮800和用于检测第二光学膜712张力的张力检测轮1000。其中,张紧摆轮800可用于调节第二光学膜712的张力以及传输路径的长度。相应的,可通过张紧摆轮800调节第二供料单元200向贴合单元300的供料速度。由此,可使得第二光学膜712的张力和供料速度,与第一光学膜711的张力和供料速度相匹配一致。实施例中,在第二光学膜712传输路径上,张紧摆轮800的数量也可根据需要进行设置,示例性的,张紧摆轮800可设置为一个、三个、四个、五个、六个、七个、八个等数量,在此不作具体限制。
如图10所示,在一些实施例中,第四输料轮240与贴合单元300的进料端之间还设置有第四除尘机构250和调节轮260。在第二光学膜712的传输路径上,调节轮260可位于第四除尘机构250靠近贴合单元300的一端。第四除尘机构250的结构可与第一除尘机构160的结构相同,具体的,第四除尘机构250也可包括有相应的粘尘组件161和静电消除器。其中,粘尘组件161中的一粘尘轮1611与第二光学膜712接触的一侧可集成有称重传感器,可用于检测第二光学膜712的张力。调节轮260可移动地安装于机架上,可用于辅助调节第二光学膜712的张力。可以理解的,调节轮260可连接有电缸等驱动件,用于调整调节轮260的位置,以调节第二光学膜712的张力。调节轮260也可相对于机架进行自转。
如图2和图12所示,在另一些实施例中,第二供料单元200还可包括有第四结构层成型机构230,可用于在第二光学膜712对应的基材7111上制作第一结构层7112,第一结构层7112可以是扩散层。即,使得第二光学膜712同时具有第一结构层7112和第二结构层7113,进而使得复合光学膜710集成有两层扩散层。在后续背光模组的加工过程中,无需再额外设置扩散膜,也可省去扩散膜的加工裁切等工序,提高生产效率。第四结构层成型机构230的结构可与第一结构层成型机构120的结构相同,在此不再赘述。其中,第四结构层成型机构230中成型轮的结构可与第一结构层7112相匹配。实施例中,第四结构层成型机构230可设置于第三结构层成型机构220与第二除尘机构270之间。
在另一些实施例中,第一供料单元100可直接选用已制成的第一光学膜料卷,第一光学膜料卷可套设于对应的第二输料轮140上进行供料。相应的,第二供料单元200也可直接选用已制成的第二光学膜料卷,第二光学膜料卷可套设于对应的第四输料轮240上以进行供料。
进一步的,如图1、图10和图11所示,在一些实施例中,贴合单元300可包括有依次设置的上胶机构310、压合机构320和固化机构330。
在一些实施例中,上胶机构310可连接于第一供料单元100的出料端,上胶机构310用于对第一光学膜711的侧面涂布胶水以形成胶层713,以便第一光学膜711与第二光学膜712粘接。具体的,可在第一光学膜711的第一结构层7112一侧涂布胶水,第一光学膜711的第一结构层7112可靠近第二光学膜712设置。从而,第一光学膜711经过上胶机构310上胶后进入压合机构320,第二光学膜712可直接由第二供料单元200的出料端进入压合机构320,压合机构320可实现第二光学膜712与第一光学膜711之间的压合粘接,第二光学膜712的第二结构层7113可靠近第一光学膜711设置。当然,在另一些实施例中,上胶机构310也可连接于第二供料单元200的出料端。
在一些实施例中,上胶机构310可选用滚涂上胶组件、夹缝上胶组件和微凹上胶组件中的一种。上胶机构310的具体结构可与第一上料组件121的结构相同,在此不再赘述。
如图10,压合机构320可包括相对设置的第一压合轮321和第二压合轮322,第一压合轮321和第二压合轮322均可转动安装于机架上。其中,第二压合轮322可连接有相应的驱动电机,驱动电机可带动第二压合轮322进行转动,从而再由第二压合轮322带动第二光学膜712或复合光学膜710移动,以为第二光学膜712的传输或复合光学膜710的传输提供动力。
再一并结合图11,第一压合轮321和第二压合轮322之间可设置有间隙,可供第一光学膜711和第二光学膜712穿过。同时,在第一光学膜711和第二光学膜712穿过压合机构320时,第一压合轮321和第二压合轮322可同时挤压第一光学膜711和第二光学膜712,以使第一光学膜711和第二光学膜712在胶层713的作用下粘接,从而形成复合光学膜710。可以理解的,胶层713可位于第一光学膜711和第二光学膜712之间。相应的,复合光学膜710可包括依次设置的第一光学膜711、胶层713以及第二光学膜712,其中,第一光学膜711中的第一结构层7112(即扩散层)靠近胶层713设置,第二光学膜712中的第二结构层7113(即棱镜层)靠近胶层713设置。在一些实施例中,第一压合轮321和第二压合轮322,施加于第一光学膜711和第二光学膜712上的压力可以设定为0.05MPa~0.5MPa。
如图10、图13至图15所示,固化机构330可包括多个固化区331,多个固化区331可沿着复合光学膜710的传输路径排布。复合光学膜710可从各固化区331内经过,从而可由固化机构330对复合光学膜710中的胶层713进行固化,以确保第一光学膜711与第二光学膜712之间的稳定连接。
实施例中,固化区331可以是热固化区或紫外线固化区。相应的,固化机构330可包括有热固化区或紫外线固化区。当然,固化机构330也可同时包括有热固化区和紫外线固化区。
如图13所示,在一些实施例中,固化机构330包括热固化区。固化机构330包括有预热段330a、固化段330b和应力释放段330c,预热段330a、固化段330b和应力释放段330c沿着复合光学膜710传输方向依次排布,且预热段330a靠近压合机构320一端设置。预热段330a可包括有至少一个热固化区,固化段330b可包括有至少一个热固化区,应力释放段330c也可包括有至少一个热固化区。
示例性的,预热段330a可包括有五个热固化区,固化段330b可包括有十个热固化区,应力释放段330c可包括有五个热固化区。预热段330a的五个热固化区温度可以设定在30℃~150℃。固化段330b的十个热固化区温度可设定在150℃~250℃。应力释放段330c的五个固化区温度可设定在150℃~300℃。实施例中,固化机构330中各固化区331的温度可呈阶梯式分布,使得温度过度更顺滑,确保固化质量。
当然,在另一些实施例中,预热段330a、固化段330b和应力释放段330c所包括固化区331的数量可分别根据需要进行设置,例如可分别设置成两个、三个、六个、七个、十二个等数量。
实施例中,热固化区内可设置有用于加热的电热丝或红外加热管等加热件3311。当复合光学膜710经过热固化区时,可在高温的作用下使复合光学膜710中的胶层713逐渐固化。在一些实施例中,复合光学膜710的传输速度可设定为4~8m/min。
在另一些实施例中,固化机构330可包括有多个紫外线固化区,也可用于对复合光学膜710中的胶层713进行固化。示例性的,固化机构330可包括有二十个波长为365nm、386nm或395nm的紫外线固化区。当然,固化机构330也可包括多种不同波长的紫外线固化区,例如:依次设置五个波长为365nm的紫外线固化区、五个波长为385nm的紫外线固化区、五个波长为395nm的紫外线固化区和五个波长为385nm的紫外线固化区,或者十个波长为365nm的紫外线固化区配合十个波长为385nm的紫外线固化区,或者十个波长为365nm的紫外线固化区配合十个波长为395nm的紫外线固化区,或者十个波长为385nm的紫外线固化区配合十个波长为395nm的紫外线固化区等。可以理解的,紫外线固化区内可设置有UV灯3312,并朝向复合光学膜710照射,如图14所示。在另一些实施例中,紫外线固化区还可设置有用375nm、405nm等波长的UV灯3312。
如图14所示,在另一些实施例中,固化机构330也可同时包括有若干个热固化区和若干个紫外线固化区。沿复合光学膜710的传输路径,热固化区和紫外线固化区可依次交替设置,从而,可提高固化效率,也可提高光学膜加工效率。各热固化区的温度可依次升高。紫外线固化区内可选择地安装有365nm、375nm、385nm、395nm、405nm等波长的UV灯3312。
在一些实施例中,复合光学膜710穿过固化机构330时,可通过自由导轮900进行传输,即固化机构330内布设有传输复合光学膜710的自由导轮900,自由导轮900可转动安装于各固化区331内。
如图15所示,在另一些实施例中,复合光学膜710在穿过固化机构330时,也可通过气悬浮的方式进行输送,从而可减少对复合光学膜710的磨损。具体的,固化机构330可包括有若干个第一送风机3321和若干个第二送风机3322,第一送风机3321和第二送风机3322分设于复合光学膜710的两侧面。沿复合光学膜710的传输路径,第一送风机3321和第二送风机3322依次交替设置。第一送风机3321和第二送风机3322均可集成于对应位置的固化区331内。第一送风机3321和第二送风机3322可分别从复合光学膜710的两侧面进行送风,从而使得复合光学膜710可以悬浮设置。在一些实施例中,第一送风机3321的送风量和第二送风机3322的送风量均可设置在10~10000m3/h,第一送风机3321的送风频率和第二送风机3322的送风频率均可设置为0~120Hz。当固化区331为热固化区时,通过设置送风机,也可使得热气流循环,加快胶层713的固化,提高生产效率。
进一步的,如图1和图2所示,实施例中,一体化光学膜加工设备还包括有依次设置的覆膜单元400、裁切单元500和收卷单元600,覆膜单元400可衔接于贴合单元300与裁切单元500之间。在一些实施例中,贴合单元300与覆膜单元400之间还设置有张紧摆轮800,可用于调节复合光学膜710的张力。实施例中,该张紧摆轮800也可设置为一个、两个、三个、五个、六个、八个等数量,在此不作具体限制。
实施例中,覆膜单元400可用于在复合光学膜710的两侧面覆上保护膜,以对复合光学膜710进行保护,避免复合光学膜710的表面被刮伤损坏。
如图16所示,覆膜单元400可包括有第五输料轮440、第一保护膜输料机构410、第二保护膜输料机构420以及粘贴机构430。其中,第五输料轮440转动安装于机架上,第五输料轮440用于承接复合光学膜710,以将复合光学膜710向粘贴机构430输送。第一保护膜输料机构410可向粘贴机构430供给第一保护膜720a,第二保护膜输料机构420可向粘贴机构430供给第二保护膜720b。粘贴机构430可将第一保护膜720a和第二保护膜720b粘贴于复合光学膜710的两侧面。
传动工艺中,需要在两光学膜的表面分别覆保护膜,然后在后续加工过程中再将保护膜揭除,将两保护膜粘贴在一块。本申请中则是直接在复合光学膜710的表面覆保护膜,一方面可减少保护膜的使用,另一方面也可减少对应的揭膜工序。相较于传统工艺,本申请可降低加工成本,提高生产效率。
如图16所示,在一些实施例中,第五输料轮440与粘贴机构430之间还可设置有第五除尘机构450,可用于对复合光学膜710的表面除尘,以确保复合光学膜710表面的洁净度。实施例中,第五除尘机构450的结构可与第一除尘机构160的结构相同,在此不再赘述。
第五输料轮440与粘贴机构430之间还可设置有张力检测轮1000,可用于检测复合光学膜710的张力。在复合光学膜710的传输路径上,张力检测轮1000可设置于第五除尘机构450与粘贴机构430之间。当然,第五输料轮440与粘贴机构430之间还可设置有一定数量的自由导轮900,用于传输复合光学膜710,示例性的,自由导轮900可设置为一个、两个、三个等数量。
如图16所示,实施例中,第一保护膜输料机构410可包括有第六输料轮411,第六输料轮411上可套设有保护膜卷,第六输料轮411可用于带动保护膜卷放料,以使第一保护膜720a源源不断的输出。相应的,第六输料轮411可连接有驱动电机,用于带动第六输料轮411转动,以实现放料。第一保护膜720a经第六输料轮411输出后,可逐渐传输至粘贴机构430。
在第一保护膜720a的传输路径上,还可设置有一自由导轮900和第一张力检测展开轮412,其中,自由导轮900靠近第六输料轮411设置。第一张力检测展开轮412一方面可用于第一保护膜720a的展开传输,避免第一保护膜720a上出现褶皱。另一方面,第一张力检测展开轮412也可用于检测第一保护膜720a传输过程中的张力,以便第一保护膜720a维持在合适的张力范围内。相应的,第一张力检测展开轮412靠近第一保护膜720a的一侧可设置有相应的称重传感器,可对第一保护膜720a的张力进行检测,以便控制器及时调整第六输料轮411的转速。
在另一些实施例中,第一保护膜输料机构410还包括有第一压制轮413,第一压制轮413可设置于第六输料轮411的出料一侧,辅助第一保护膜720a的剥离,同时,也可用于改变第一保护膜720a从第六输料轮411剥离时的角度。使用中,第一压制轮413可抵压于保护膜卷的放料位置,即第一保护膜720a与保护膜卷分离的位置。可以理解的,第一保护膜720a的一面可为黏着面,另一面可为光滑面。实施例中,第一压制轮413与第一保护膜720a的光滑面相接触。
在一些实施例中,第二保护膜输料机构420的结构可与第一保护膜输料机构410的结构大致相同。具体的,第二保护膜输料机构420可包括第七输料轮421和第二压制轮422。其中,第七输料轮421上可套设有保护膜卷,第七输料轮421可用于带动保护膜卷放料,以使第二保护膜720b源源不断的输出。第七输料轮421也可连接有相应的驱动电机,用于带动第七输料轮421转动,以实现放料。
第二压制轮422可设置于第七输料轮421的出料一侧,辅助第二保护膜720b的剥离。使用中,第二压制轮422可抵压于保护膜卷放料的位置,即第二保护膜720b与保护膜卷分离的位置。可以理解的,第二保护膜720b的一面可为黏着面,另一面可为光滑面。实施例中,第二压制轮422可与第二保护膜720b的光滑面相接触。
第二保护膜720b从第七输料轮421位置输出后,可连接至粘贴机构430。在一些实施例中,第二保护膜720b的传输路径上还可设置有第二张力检测展开轮423,即第二张力检测展开轮423可用作展开轮使用,以使第二保护膜720b顺利展开传输,避免第二保护膜720b上出现褶皱。同时,第二张力检测展开轮423上可集成有称重传感器,可对第二保护膜720b的张力进行检测,以便控制器及时调整第七输料轮421的转速,以使第二保护膜720b的张力维持在合适范围内。实施例中,第二张力检测展开轮423可位于第七输料轮421与粘贴机构430的进料端之间。
在粘贴机构430的进料端一侧,第一保护膜720a可对应设置于复合光学膜710的一侧面。第二保护膜720b可位于复合光学膜710背离第一保护膜720a的一侧面。可以理解的,第一保护膜720a的黏着面靠近复合光学膜710设置,第二保护膜720b的黏着面靠近复合光学膜710设置。
粘贴机构430可包括有相对设置的第三压合轮431和第四压合轮432,第三压合轮431和第四压合轮432之间设置有间隙,以便第一保护膜720a、复合光学膜710和第二保护膜720b穿过,并使第一保护膜720a和第二保护膜720b贴合于复合光学膜710的对应侧。
在复合光学膜710和两保护膜经过第三压合轮431和第四压合轮432之间时,两保护膜分设于复合光学膜710的两侧面。同时,第三压合轮431和第四压合轮432会施加于对应侧保护膜一定的压力,以使对应侧保护膜可以黏着于复合光学膜710上,确保保护膜与复合光学膜710之间的连接强度,避免保护膜与复合光学膜710分离。其中,第三压合轮431和第四压合轮432施加的压力可根据需要进行设置,一方面确保不会压损复合光学膜710和保护膜,另一方面确保使保护膜可稳定黏着于复合光学膜710上。由此,可获得光学膜料带700,如图16所示。在一些实施例中,第三压合轮431可连接有驱动电机,用于带动第三压合轮431转动,以为光学膜料带700的传输提供动力。同时,第四压合轮432也可连接有电缸、气缸等驱动装置,用于带动第四压合轮432靠近或远离第三压合轮431,以配合第三压合轮431进行保护膜的贴合,也可调节贴合速度。
在一些实施例中,粘贴机构430与裁切单元500之间也可设置有相应数量的自由导轮900,以辅助光学膜料带700的传输,避免光学膜料带700受损。
在一些实施例中,裁切单元500可用于对光学膜料带700进行分切,即在光学膜料带700的宽度上,将光学膜料带700分切成多条对应宽度的子光学膜料带700a。
如图16至图18所示,裁切单元500可包括有相对设置的支撑轮520和切刀机构510,切刀机构510可用于对光学膜料带700进行裁切。支撑轮520可用于对光学膜料带700提供相应的支撑作用,以便于切刀机构510对光学膜料带700进行裁切。
切刀机构510可包括有刀架512和若干个切刀组511。刀架512可相对于支撑轮520转动安装,且刀架512的转动轴平行于支撑轮520,若干个切刀组511均可安装于刀架512上。当切刀组511设置有多组时,多组切刀组511可环绕刀架512的转动轴分布设置。刀架512相对于支撑轮520转动时,可带动多个切刀组511同步转动,以使不同的切刀组511靠近支撑轮520,以进行相应的裁切动作。可以理解的,多组切刀组511之间相互间隔设置,避免相互干扰。实施例中,支撑轮520的轴线可平行于光学膜料带700的宽度,支撑轮520轴向上的延伸长度可大于或等于光学膜料带700的宽度,以便为光学膜料带700提供稳定的支撑。
在一些实施例中,刀架512可通过第一转轴513转动安装于机架上,第一转轴513可连接有驱动电机。从而可由驱动电机带动刀架512转动,以使不同的切刀组511切换至与支撑轮520对应。
示例性的,切刀机构510可包括有四组切刀组511,四组切刀组511可环绕第一转轴513间隔均匀分布。四组切刀组511的结构和安装方式可大致相同,以其中一切刀组511为例进行详述描述。
如图18所示,切刀组511可包括有一个、两个、三个、四个等数量的切刀5111,切刀5111的数量可根据光学膜料带700的裁切需要进行设置,在此不作具体限制。示例性的,如将光学膜料带700分切成两条子光学膜料带700a时,切刀组511可设置成一个切刀5111;当需要将光学膜料带700分切成三条子光学膜料带700a时,切刀组511可包括两个切刀5111。
当切刀组511包括有多个切刀5111时,多个切刀5111相互平行,且多个切刀5111同轴设置。在一些实施例中,多个切刀5111可通过第二转轴514转动安装于刀架512的一连接臂上。具体的,多个切刀5111均可固定安装于第二转轴514上,第二转轴514可转动安装于对应的连接臂上。可理解的,多个切刀5111相互间隔设置,相邻两切刀5111之间的间距可根据所需子光学膜料带700a的宽度进行设置。
如图16和图18所示,其他切刀组511也可分别包括有一个、两个、三个、四个等数量的切刀5111。各切刀组511中的切刀5111在支撑轮520上的垂直投影,可沿支撑轮520的轴错位设置。具体的,其中一切刀组511中相邻两切刀5111之间的间隔大小,与另一切刀组511中相邻两切刀5111之间的间隔大小不同。从而,通过不同的切刀组511对光学膜料带700进行裁切时,可获得不同宽度的子光学膜料带700a。相应的,当需要裁切出不同宽度的子光学膜料带700a时,可直接通过转动刀架512来切换成所需的切刀组511,无需再进行切刀5111的拆装,从而可实现自动换刀,减少换刀时间,进而可提高生产效率,也可减少工作人员的工作量。
在另一些实施例中,切刀机构510也可包括一组、三组、四组等数量的切刀组511,各切刀组511可对应裁切出不同宽度的子光学膜料带700a。
如图16和图18所示,实施例中,支撑轮520可连接有驱动电机,可用于驱动支撑轮520转动。工作过程中,可由支撑轮520带动光学膜料带700移动,同时,也可驱使对应的切刀5111进行转动,以使切刀5111对光学膜料带700进行裁切。
如图16所示,在一些实施例中,收卷单元600可包括两个、三个等数量的收料轮,其中,收料轮的数量可根据裁切单元500裁切出的子光学膜料带700a的数量进行设置。例如,裁切单元500裁切出两个子光学膜料带700a时,收卷单元600可包括两收料轮,即第一收料轮610和第二收料轮620,第一收料轮610和第二收料轮620可与两子光学膜料带700a一一对应设置,以分别对两个子光学膜料带700a进行收卷。当然,机架上也可预先设置多个收料轮,用户可根据需要进行选择使用。实施例中,收料轮可连接有驱动电机,用于驱动收料轮转动,以进行收料。
在子光学膜料带700a的传输路径上也可设置有相应数量的自由导轮900,以支撑和改变子光学膜料带700a的传输路径。子光学膜料带700a的传输路径上还设置有对应的张力检测轮1000,用于检测子光学膜料带700a传输路径上的张力,以便于对子光学膜料带700a顺利收卷。在一些实施例中,任一子光学膜料带700a的传输路径上均可设置有一个张力检测轮1000。当然,在另一些实施例中,各子光学膜料带700a也可共用一张力检测轮1000。
实施例中,子光学膜料带700a的传输路径上还可设置有静电消除器(图未示),用于消除子光学膜料带700a上的静电。
本申请提供的一体化光学膜加工设备,可实现第一结构层7112和第二结构层7113的制作、两层光学膜的贴合、覆保护膜、裁切等工序。一方面可减少中间物料的收卷、拆卷等工序,也可减少中间物料的搬运,从而可提高生产效率,降低成本。
尽管上面已经示出和描述了本申请的实施例,可以理解的是,上述实施例是示例性的,不能理解为对本申请的限制,本领域的普通技术人员在本申请的范围内可以对上述实施例进行变化、修改、替换和变型。
本文用于企业家、创业者技术爱好者查询,结果仅供参考。