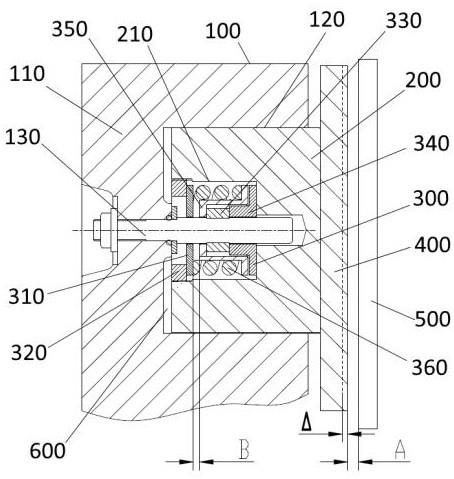
1.本发明属于制动器领域,尤其是一种行车盘式制动器的磨损补偿装置及其自补偿方法。
背景技术:
2.盘式制动器,包括动力源,运动传动动力的传动组件,以及与制动盘相抵用于实现制动效果的摩擦片。常见的传动组件包括:活塞推杆、齿轮传动等方式,干式摩擦片长期使用后会产生磨损。如果没有磨损自动补偿,必然会引起导致系统响应延迟,车辆刹车距离延长,运行平稳性降低。加入磨损自动补偿装置,可以改变制动器活塞的初始位置,保证活塞行程始终一致,从而使车辆始终保持良好的制动性能。
3.现有的磨损补偿装置,一般需要人工或传感器进行频繁的测量,获得摩擦盘的磨损量,然后根据这个磨损量进一步执行磨损补偿,通常自动化水平低,维护运营成本较高,容易受到外界环境的干扰,形成安全隐患。
技术实现要素:
4.为了克服上述技术缺陷,本发明提供一种行车盘式制动器的磨损补偿装置及其自补偿方法,以解决背景技术所涉及的问题。
5.本发明提供一种行车盘式制动器的磨损补偿装置,其特征在于,所述制动器包括:钳体,包括本体部,设置在所述本体部一侧、一端敞开的第一安装空间,以及一端固定安装在所述本体部上、另一端位于所述第一安装空间中部的固定杆;活塞,安装在所述本体部和固定杆之间,可沿着所述第一安装空间水平移动;所述活塞靠近钳体的一侧敞开形成第二安装空间;补偿装置,设置在所述第二安装空间内,适于调整所述钳体和活塞之间的相对位置;其中,所述补偿装置包括:滑动安装在所述固定杆上的弹簧压板,过盈安装在所述活塞内壁上、适于限定所述弹簧压板位置的固定螺母,与所述固定杆过盈配合的调节胀套,设置在所述调节胀套一侧、呈“l”形的调节衬套,放置在所述调节胀套和调节衬套上的弹簧导套,以及一端设置在所述弹簧导套上、另一端与所述弹簧压板相连接的弹性件。
6.优选地或可选地,所述活塞远离钳体的外侧安装有摩擦片,在所述活塞的带动下与制动盘相抵,实现制动。
7.优选地或可选地,所述弹簧导套靠近弹簧压板的一侧设置有下翻边,所述下翻边与所述固定杆相抵;所述弹簧导套的另一侧设置有上翻边,所述上翻边与所述调节衬套上边缘相对齐,所述上翻边与所述弹性件的一端相抵。
8.优选地或可选地,所述固定杆的一端穿过所述本体部,其外侧通过防松垫圈和安装螺母固定限位。
9.优选地或可选地,所述固定杆和本体部之间通过密封圈和密封压板进行密封。
10.优选地或可选地,所述密封圈为角密封。
11.优选地或可选地,所述钳体、所述活塞内侧、固定螺母和弹簧压板形成压力腔室,所述压力腔室适于提供所述活塞制动的动力。
12.优选地或可选地,所述压力腔室与液压机或气源相连接。
13.本发明还提供一种行车盘式制动器的磨损补偿装置的自补偿方法,所述方法包括:当摩擦片出现磨损后,开始制动时,活塞上的固定螺母推动弹簧压板移动距离a,所述距离a为摩擦片未磨损时,活塞的正常行程;然后,活塞继续运动至与制动盘相抵,同时,固定螺母继续推动弹簧导套与调节胀套向前移动距离δ,所述距离δ应当与摩擦片的摩擦损耗量相同;制动缓解时,活塞不再受外力作用,弹性件储存的回弹力推动弹簧压板、固定螺母和活塞回位,直至弹性件恢复原长,此时活塞的位置相对于初始位置向前移动了距离δ。
14.优选地或可选地,所述方法还包括:所述调节胀套与固定杆的过盈力大于所述弹性件的紧压力,小于所述固定螺母与活塞之间过盈力。
15.本发明涉及一种行车盘式制动器的磨损补偿装置及其自补偿方法,相较于现有技术,具有如下有益效果:1、本发明可根据摩擦片实时磨损量,精确调节活塞初始位置,不需要进行人工手动测量,也不需要添加任何传感器,降低了维护运营等成本;2、本发明磨损补偿装置在制动器的内部,避免了泥沙走石等外界的干扰,安全可靠;而且不需要借助或改变任何外部动力源,比如电机,或改变制动液压强等,避免了紧急情况下的无法调节;3、本发明通过弹性件,将活塞压回,保证摩擦片不会与制动盘拖磨,从而避免持续生热引起制动器密封失效,导致行车安全。避免无效制动引起摩擦片寿命降低,有利于延长维保时间。且弹性件初末位置随着磨损的增加而改变,保证弹性件压缩量始终一致,从而保证活塞回位力稳定持续;4、本发明的活塞始终保持统一较小的行程,避免了运动距离变化引起的冲击,既能保证了运行平稳性,也能保证液压系统响应时间始终一致,从而保证制动性能始终如一;5、本发明的活塞初始位置首次设定完成即可,日常维修保养过程中,不再需要特别关注,使用方便;6、本发明的整体尺寸较小,且补偿装置整体安装在活塞内腔,不影响活塞推力及制动力。特别适合空间受限的场合;7、本发明通过在调节胀套的径向开槽,过盈力过大时,槽口尺寸会变大,接触的周长变小,从而降低了过盈力,保证过盈力合适,降低加工难度;8、通过一定厚度定制螺母轴向定位,并辅助螺纹胶等手段实现防松,因此所述固定螺母能承受较大轴向力,更调整精确可靠。
附图说明
16.图1是本发明的结构示意图一。
17.图2是本发明的结构示意图二。
18.图3是本发明中密封圈的局部放大图。
19.图4是本发明中固定螺母的截面示意图。
20.图5是本发明中固定螺母的安装示意图。
21.图6是现有技术中调节胀套的形状示意图。
22.图7是本发明中调节胀套的形状示意图。
23.附图标记为:钳体100、本体部110、第一安装空间120、固定杆130、防松垫圈131、安装螺母132、密封圈133、密封压板134、角密封133a;活塞200、第二安装空间210;补偿装置300、弹簧压板310、固定螺母320、调节胀套330、调节衬套340、弹簧导套350、外螺纹321、安装槽322、铁丝323、螺纹胶324、下翻边351、上翻边352、弹性件360;摩擦片400、制动盘500、压力腔室600;距离a为活塞行程、距离b为弹簧压板与弹簧导套之间的间隙、距离δ为摩擦片磨损值。
具体实施方式
24.在下文的描述中,给出了大量具体的细节以便提供对本发明更为彻底的理解。然而,对于本领域技术人员而言显而易见的是,本发明可以无需一个或多个这些细节而得以实施。在其他的例子中,为了避免与本发明发生混淆,对于本领域公知的一些技术特征未进行描述。
25.参阅附图1至7,一种行车盘式制动器的磨损补偿装置,其中,所述制动器包括:钳体100、本体部110、第一安装空间120、固定杆130、防松垫圈131、安装螺母132、密封圈133、密封压板134、角密封133a、活塞200、第二安装空间210、补偿装置300、弹簧压板310、固定螺母320、调节胀套330、调节衬套340、弹簧导套350、外螺纹321、安装槽322、铁丝323、螺纹胶324、下翻边351、上翻边352、弹性件360、摩擦片400、制动盘500、压力腔室600。
26.其中,所述钳体100的本体部110的截面形状为“匚”,在所述本体部110的一侧设置第一安装空间120,所述第一安装空间120一侧敞开,形成开口部,在所述第一安装空间120内安装有所述制动器的传动组件。固定杆130的一端穿过所述本体部110、并通过防松垫圈131和安装螺母132固定在所述本体部110上,另一端位于所述第一安装空间120的中部。所述固定杆130通过与钳体100内圆配合、周向定位,在固定端阶梯轴肩轴向定位,具有更好的轴向稳定性,保证其它零件具有良好的对中性。
27.所述活塞200安装在所述本体部110和固定杆130之间,具体地,所述活塞200外部与钳体100相抵,内部套装在所述固定杆130内,可沿着所述第一安装空间120水平移动,在所述活塞200远离钳体100的外侧安装有摩擦片400,在所述活塞200的带动下与制动盘500相抵,实现制动。所述固定杆130和本体部110之间通过密封圈133和密封压板134进行密封,优选地,所述密封圈133为角密封133a。所述角密封133a能够实现轴向密封,结构更简单实用,加工面少。另外,在所述活塞200靠近钳体100的一侧敞开形成第二安装空间210,在所述第二安装空间210内安装有补偿装置300,用于调整所述活塞200的位置,实现摩擦片400磨损后的自动补偿。
28.所述补偿装置300包括:滑动安装在所述固定杆130上的弹簧压板310,过盈安装在所述活塞200内壁上、适于限定所述弹簧压板310位置的固定螺母320,与所述固定杆130过盈配合的调节胀套330,设置在所述调节胀套330一侧、呈“l”形的调节衬套340,放置在所述调节胀套330和调节衬套340上的弹簧导套350,以及一端设置在所述弹簧导套350上,另一端与所述弹簧压板310相连接的弹性件360。在本实施例中,所述弹性件360为回弹弹簧。
29.具体而言,所述弹簧导套350靠近弹簧压板310的一侧设置有下翻边351,所述下翻边351与所述固定杆130相抵;所述弹簧导套350的另一侧设置有上翻边352,所述上翻边352与所述调节衬套340上边缘相对齐,适于与所述弹性件360的一端相抵。由于弹性件360在组装时既需要有一定压紧力,因此,所述弹簧导套350应该具有一定刚度,防止压弯变形,否则衬套会在第二安装空间210内晃动,引起异响;如此设置,通过具有一定刚度的弹簧导套350限制所述弹性件360的位置,从而避免弹性件360的松动,避免异响的发生,延长弹性件360的使用寿命。
30.在进一步实施例中,所述钳体100、所述活塞200内侧、固定螺母320和弹簧压板310形成压力腔室600,所述压力腔室600与液压机或气源相连接,通过液压油或压力气体,提供活塞200运动的动力,实现对制动盘500的制动。当然对于本领域技术人员而言,所述压力腔室600还可以为其它形式的动力源。
31.在进一步实施例中,在安装过程中,需要保证所述固定螺母320与活塞200之间过盈力大于所述调节胀套330与固定杆130的过盈力,所述调节胀套330与固定杆130的过盈力大于所述弹性件360的紧压力;在本实施例中,由于所述固定螺母320与活塞200之间采用铁丝和螺纹胶连接,因此,所述固定螺母320与活塞200之间过盈力即为所述固定螺母320与活塞轴向粘结力。否则,在实际补偿过程中,固定螺母320和弹性件360会优先于所述调节胀套330发生相对滑移,进而导致会出现定位不准,在间隙调节过程中可能导致准确性降低。
32.具体而言,由于现有的弹性止挡件一般只能限位,承受轴向力有限,产生弹性变形后,间隙调节准确性大幅度降低。因此,在本实例中,对弹簧压板310进行弹性止挡时,通过一定厚度固定螺母320轴向定位,并辅助螺纹胶324等手段实现防松,因此所述固定螺母320能承受较大轴向力,安装过程可调试空间更大、方便安装,间隙调节更为过程精确可靠。
33.所述固定螺母320的结构见附图4和附图5,外圆周方向加工外螺纹321,与活塞200内螺纹拧紧,固定螺母320端面与活塞200端面均开槽,形成安装槽322,在所述安装槽322内安装铁丝323,将固定螺母320和活塞200固定在一起,再配合高强度螺纹胶324,实现双重防松。在本实施例中,所述固定螺母320的厚度为5.5mm,当然这不意味着所述固定螺母320为标准件,在实际操作过程中,需要根据实际轴向力大小,计算得到适合的厚度。
34.通过上文,可以发现调节胀套330安装时的过盈力大小,决定了整个磨损补偿装置300的精度和使用寿命,参见附图6,现有的常规调节胀套330的形状为圆环形,需要精确保证调节胀套330内孔尺寸和固定杆130尺寸,从而保证过盈力,但是这大大的增大了加工难度。因此,在实施例中,参阅附图7,通过在调节胀套330的径向开槽,过盈力过大时,槽口尺寸会变大,接触的周长变小,从而降低了过盈力,保证过盈力合适,降低加工难度。
35.其中,调节胀套330应采用具有一定塑性、弹性且耐磨的材料,防止过盈力压裂损坏,一般这样的材料成本较高。而在本实施例中,所述调节衬套340用于转接调节胀套330,直接限定活塞200初始位置,具有一定抗压能力即可。不仅能够降低调节胀套330的材料成
本,而且能够更好的调整所述限定活塞200的位置。
36.为了方便理解行车盘式制动器的磨损补偿装置300的技术方案,对其工作原理做出简要说明:对于本领域技术人员而言,可以理解的是,所述活塞200的初始位置由调节胀套330确定。因此,在制动实施时,外力推动活塞200向右侧移动,进而推动摩擦片400压紧制动盘500,实现制动。同时,与活塞200连接的固定螺母320推动弹簧压板310和弹簧向同方向移动,由于所述调节胀套330与固定杆130的过盈力大于所述弹性件360的紧压力,调节胀套330相对固定杆130静止,弹簧导套350被调节胀套330限位,导致活塞200向右侧移动过程中,弹性件360被持续压紧。制动缓解时,活塞200不再受外力作用,弹性件360储存的弹力推动弹簧压板310、固定螺母320和活塞200回位,直至弹性件360恢复原长。
37.也就是说,摩擦片400未磨损前,活塞200行程为距离a,由于弹簧压板310与弹簧导套350之间的间隙距离b大于或等于活塞200行程距离a,因此弹簧压板310不会与弹簧导套350发生相互作用。当摩擦片400磨损距离δ后,活塞200上的固定螺母320推动弹簧压板310移动距离a后,继续推动弹簧导套350与调节胀套330向前移动距离δ,进而,使得活塞200的初始位置也向前移动了距离δ,正好补偿了摩擦片400磨损,实现磨损自动补偿。该磨损自动补偿装置300不需要通过测量磨损值,手动调节;根据实际磨损值,精确调节间隙,调节量的多少随着磨损量的变化而变化,调节胀套330与固定杆130的过盈量控制在一定范围内,既能在制动过程中,保证调节胀套330位置不会随意变化;也能在自补偿过程中,保证固定螺母320能够推动调节胀套330移动实现磨损量补偿。
38.另外需要说明的是,在上述具体实施方式中所描述的各个具体技术特征,在不矛盾的情况下,可以通过任何合适的方式进行组合。为了避免不必要的重复,本发明对各种可能的组合方式不再另行说明。
再多了解一些
本文用于企业家、创业者技术爱好者查询,结果仅供参考。