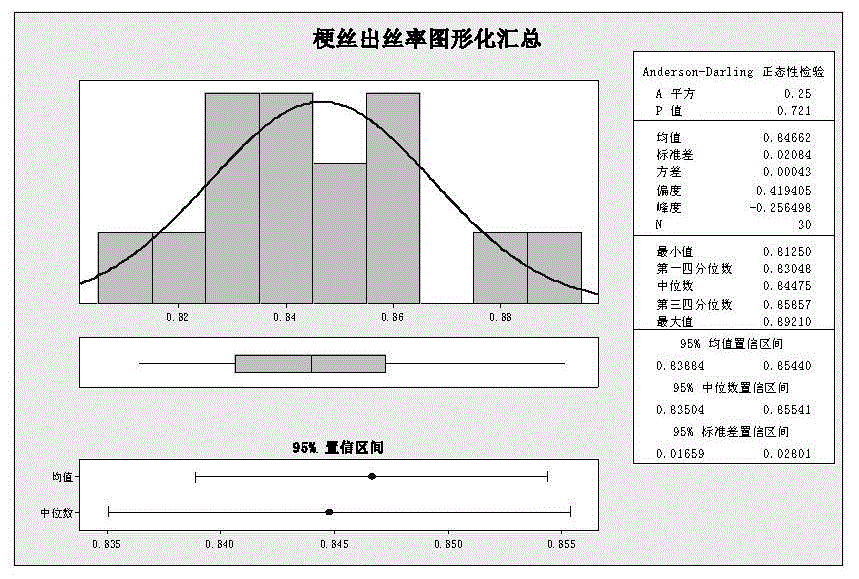
本发明属于卷烟制造
技术领域:
,具体涉及一种提高梗丝出丝率的方法。
背景技术:
:烟草生产中,梗丝出丝率大大影响着烟草生产的成本。经调取erp系统1-3月份烟梗总投料重528746.7kg、总梗丝重447616.6kg,计算得出梗丝出丝率为84.66%。通过调查、统计分析平均梗丝出丝率水平达到88.50%为正常状态,与之相比,现在的烟梗梗丝出丝率至少还有3.84%的提高潜力。再者,依据国家局提质、降本增效总体部署,梗丝出丝率提高后可减少烟梗投入量,降低成本,使梗丝质量更加稳定,提高精细化加工水平,能够取得的很好的经济效益和质量效益。因此,有必要针对提高梗丝出丝率而提出新的改进。技术实现要素:本发明解决的技术问题:提供一种提高梗丝出丝率的方法,本发明将烟草生产中的梗丝出丝率从84.66%提高到88.5%,提高梗丝出丝率,降低生产成本,梗丝质量稳定。本发明采用的技术方案:提高梗丝出丝率的方法,包括以下步骤:步骤一:确定影响生产中梗丝出丝率的主要影响因子:对与梗丝出丝率相关的加工段即切梗丝段出丝率、梗丝加料段出丝率、梗丝膨化段出丝率进行测量分析,通过sipoc模模型图进行原因收集,形成fema表,运用fema进行第一次的原因筛选,根据rpn风险数的大小,筛选出分值高于120分的潜在的失效原因;再采用因果矩阵进行第二次筛选,按照因果矩阵的程序,对收集到的原因进行影响因素的权重赋值并分析;利用因果矩阵表的结果和总体计算的百分比对流程输入变量进行再次筛选,最后确定需要改善的输入变量;通过对过程的测量系统进行分析,采用统计分析的方法对筛选出的需改进原因进行一一验证,确定出影响梗丝出丝率的主要因子为:碎梗筛分量、梗头风选量、水洗梗水温、水泵电机转速、切梗厚度;步骤二:针对各影响因子,从管理原因上确定选择改进措施的标准及标准权重,从技术原因上采用doe的方法寻找合理的参数搭配:(1)碎梗筛分量;加强投料烟梗的检验,发现碎梗过多进行退货,由物流中心重新筛分;(2)梗头风选量:梗头风选量与梗丝风选风门开度有关,固通过doe试验找到合理搭配参数,提高切丝质量后,可降低梗头风选量;对梗头含丝量进行检验,加强操作人员对梗头含丝量的自检;(3)水洗梗水温:采用doe方法确定合理的搭配参数;(4)水泵电机转速:采用doe方法确定合理的搭配参数:(5)切梗厚度:采用doe方法确定合理的搭配参数。上述步骤二(2)中,所述梗头风选量中的风门开度选用0.2。上述步骤二(3)中,所述水洗梗水温选用55℃。上述步骤二(4)中,所述水泵电机转速选用42hz。上述步骤二(5)中,所述切丝厚度选用0.17mm。本发明现有技术相比的优点:1、本方案通过定义、测量、分析、改进和控制等阶段将烟草生产中的梗丝出丝率从84.66%提高到88.5%,大大提高了梗丝出丝率,减少烟梗投入量,降低生产成本;2、本方案使烟梗出丝率水平提高后,对工厂提高梗丝质量、降低消耗等做出了一定的贡献,梗线加工水平提高,梗丝质量稳定。附图说明图1为本发明中梗丝出丝率图形化汇总;图2为本发明中出丝率均值图表;图3为本发明中梗加料前水分仪测量系统分析;图4为本发明中梗加料后水分仪测量系统分析;图5为本发明中膨化塔出口水分仪测量系统分析;图6为本发明中梗丝加香出口水分仪测量系统分析;图7为本发明中出丝率的概率图;图8为本发明中出丝率等方差检验;图9为本发明中出丝率与水洗梗水温的箱线图;图10为本发明中出丝率与水洗梗水温的单值图;图11为本发明中出丝率残差图;图12为本发明中出丝率的概率图;图13为本发明中出丝率等方差检验;图14为本发明中水泵电机转速与出丝率的单值图;图15为本发明中出丝率的箱线图;图16为本发明中出丝率残差图;图17为本发明中出丝率的概率图;图18为本发明中出丝率等方差检验;图19为本发明中出丝率与切丝厚度的单值图;图20为本发明中出丝率的箱线图;图21为本发明中出丝率残差图;图22为本发明中出丝率的概率图;图23为本发明中出丝率等方差检验图;图24为本发明中出丝率与贮存时间的单值图;图25为本发明中出丝率的箱线图;图26为本发明中c37残差图;图27为本发明中出丝率与风选梗头量的散点图;图28为本发明中风选梗头量出丝率残差图;图29为本发明中出丝率与筛分碎梗量的散点图;图30为本发明中出丝率残差图;图31为本发明中出丝率残差图;图32为本发明中残差与水洗梗水温图;图33为本发明中残差与水泵电机转速图;图34为本发明中残差与切丝厚度图;图35为本发明中残差与风门开度图;图36为本发明中出丝率主效应图;图37为本发明中出丝率交互作用图;图38为本发明中出丝率的等值线图;图39为本发明中出丝率的曲面图;图40为本发明中出丝率优化曲线图;图41为本发明中改进前后箱线比较图;图42为本发明中改进前后箱线比较图;图43为本发明中出丝率图表;图44为本发明中出丝率的箱线图;图45为本发明中出丝率的xbar-s控制图;图46为本发明中出丝率的概率图;图47为本发明中c12的过程能力图。具体实施方式请参阅图1-47,详述本发明的实施例。提高梗丝出丝率的方法:确定影响生产中梗丝出丝率的主要影响因子:对与梗丝出丝率相关的加工段即切梗丝段出丝率、梗丝加料段出丝率、梗丝膨化段出丝率进行测量分析,通过sipoc模模型图进行原因收集,形成fema表,运用fema进行第一次的原因筛选,根据rpn风险数的大小,筛选出分值高于120分的潜在的失效原因;再采用因果矩阵进行第二次筛选,按照因果矩阵的程序,对收集到的原因进行影响因素的权重赋值并分析;利用因果矩阵表的结果和总体计算的百分比对流程输入变量进行再次筛选,最后确定需要改善的输入变量;通过对过程的测量系统进行分析,采用统计分析的方法对筛选出的需改进原因进行一一验证,确定出影响梗丝出丝率的主要因子为:碎梗筛分量、梗头风选量、水洗梗水温、水泵电机转速、切梗厚度。具体的实时方式如下1、测量阶段:1.1定义:梗丝出丝率=梗丝重量/烟梗重量*100%按加工段分层:切梗丝段出丝率、梗丝加料段出丝率、梗丝膨化段出丝率测量结果分析①测量当前水平:指标的具体值为,梗丝出丝率为84.66%。由于出丝率是由两个连续数据相除得出的,而且通过长期数据显示,出丝率符合正态分布,可以作为连续数据进行处理分析。如图1所示。分析:检验趋势性的近似p值为0.211,远大于0.05.结论:梗丝出丝率的趋势稳定。②按对于梗丝出丝率的各层进行图表分析,对梗丝出丝率按加工段进行分层分析根据目标,要求三个加工段总的合格率达到88.5%,如果三个加工段的目标平均出丝率达到0.9601,则可以保证达到目标。因此将0.9600作为流程改进的目标。如图2所示。通过对三个加工段出丝率进行统计分析,梗切丝段为93.81%,梗加料段为99.07%,梗膨化段为91.09%,可以视其为已经达到了小目标96%,所以测量点是梗丝膨化段和梗切丝段,使他们出丝率均达到96%,即可达到总体目标88.5%。1.2确定数据收集对象1)提出原因:初认定切梗丝段出丝率、梗烘丝段出丝率是影响梗丝出丝率的几个关键工序,针对梗丝出丝率,根据详细sipoc图,对可能的原因进行收集,最后形成fema表。2)fema表(经过因果图分解后,运用fema进行第一次的原因筛选)根据rpn风险数的大小,筛选出分值高于120分的潜在的失效原因如下表:序号原因rpn风险是否考虑1操作者责任心168是2烟梗配方225是3水洗梗水温224是4水洗梗水流速度/水泵电机转速224是5烟梗贮存时间224是6切丝厚度432是7梗头风选量180是8碎梗筛分量240是3)因果矩阵:经过第一阶段的fema筛选后,再使用因果矩阵进行第二次筛选。按照因果矩阵的程序,对原因进行影响因素的权重赋值并分析(赋值按其相关程度依次赋0,1,3,5)。利用因果矩阵表的结果和总体计算的百分比对流程输入变量进行再次筛选,最后确定需要改善的输入变量,如下表:水洗梗水温537713.87水洗梗水流速度/水泵电机转速537713.87烟梗贮存时间537713.87切丝厚度537713.87梗头风选量15559.91碎梗筛分量537713.871.3测量系统分析为了保证数据的有效性,便于实施,对过程的测量系统进行分析。1)水分仪测量系统分析2)①梗加料前水分仪测量系统分析,如图3所示。由上面结论可知,测量系统变差为总变差的5.71%<10%,说明测量系统良好;分辨力等级为24>10,且xbar控制图与r控制图没有异常,整体说明测量系统有效。②梗加料后水分仪测量系统分析,如图4所示。由上面结论可知,测量系统变差为总变差的8.27%<10%,说明测量系统良好;分辨力等级为16>10,且xbar控制图与r控制图没有异常,整体说明测量系统有效。③膨化塔出口水分仪测量系统分析,如图5所示。由上面结论可知,测量系统变差为总变差的5.00%<10%,说明测量系统良好;分辨力等级为28>10,且xbar控制图与r控制图没有异常,整体说明测量系统有效。④梗丝加香出口水分仪测量系统分析,如图6所示。由上面结论可知,测量系统变差为总变差的11.71%<30%,测量系统仍可用,说明这是受水分仪测量系统的限制,无法改进;分辨力等级为11>10,且xbar控制图与r控制图没有异常,测量系统满足项目数据需要,是可以接受的,整体说明测量系统有效。1.4测量阶段结论:确定需要改善的输入变量:水洗梗水温、水洗梗水流速(水泵电机转速)、烟梗贮存时间、切丝厚度、梗头风选量、碎梗筛分量。2、分析阶段2.1原因验证:为了证明确定的原因是否正确,采用统计分析的方法对筛选出的需改进原因进行一一验证。(1)水洗梗水温原因验证①数据收集方案:按照工艺标准规定水洗梗水温35-75℃,根据生产经验将水洗梗水温分为3个水平,分别为:40℃、55℃、70℃,确定α=0.05,β=0.1,再根据界定阶段统计的出丝率标准偏差和出丝率差值确定样本数量:根据数据收集难易程度,确定每个水平采集5个数据。然后采用单因子方差分析进行验证:②正态性检验,如图7所示结论:从p值来看,三水平的数据均大于0.05,因此认为其服从正态分布。③独立性检验结论:从p值看,三水平相互独立。④等方差检验结论:从图8可知,bartlett检验p值大于0.05,因此,符合等方差假设。综合上述三种检验,收集的数据可以进行单因子方差分析。⑤单因子方差分析:从如9、10、11分析:a、残差是正态分布,且均值为0,方差恒定,因此没有足够理由拒绝模型。b、p值小于0.05,拒绝原假设,至少有一个水平的出丝率更高。c、由多重比较(tukey)检验可知,与55比较,70的置信区间包含0,意味着这两个水平不存在统计显著性差异。结论:55、70的两个水平的水洗梗温度之间没显著差异,与40水平具有显著性差异。(2)水洗梗水水泵电机转速原因验证①数据收集方案:把水泵电机转速分为3个水平,分别为:38hz、40hz、42hz,确定α=0.05,β=0.1,再根据界定阶段统计的出丝率标准偏差和出丝率差值确定样本数量:功效和样本数量单因子方差分析根据数据收集难易程度,确定每个水平采集5个数据。然后采用单因子方差分析进行验证:②正态性检验如图12所示,结论:从p值来看,三水平的数据均大于0.05,因此认为其服从正态分布。③独立性检验结论:从p值看,三水平相互独立。④等方差检验:结论:从图13可知,bartlett检验p值大于0.05,因此,符合等方差假设。综合上述三种检验,收集的数据可以进行单因子方差分析。⑤单因子方差分析从图14-16分析:a、残差是正态分布,且均值为0,方差恒定,因此没有足够理由拒绝模型。b、p值小于0.05,拒绝原假设,至少有一个水平的出丝率更高。c、由多重比较(tukey)检验可知,与38hz比较,40hz的置信区间包含0,意味着这两个水平不存在统计显著性差异。结论:38hz、40hz的这两个水平的水洗梗温度之间没有显著性差异,与42hz水平具有显著性差异。(3)切梗丝厚度原因验证①数据收集方案:把切梗丝厚度分为3个水平,分别为:0.15mm、0.16mm、0.17mm,确定α=0.05,β=0.1,再根据界定阶段统计的出丝率标准偏差和出丝率差值确定样本数量:功效和样本数量单因子方差分析根据数据收集难易程度,确定每个水平采集5个数据。然后采用单因子方差分析进行验证。②正态性检验如图17所示,从p值来看,三水平的数据均大于0.05,因此认为其服从正态分布。③独立性检验结论:从p值看,三水平相互独立。④等方差检验:c17与c16结论:从图18可知,bartlett检验p值大于0.05,因此,符合等方差假设。综合上述三种检验,收集的数据可以进行单因子方差分析。⑤单因子方差分析单因子方差分析:c17与c16从图19-21分析:a、残差是正态分布,且均值为0,方差恒定,因此没有足够理由拒绝模型。b、p值小于0.05,拒绝原假设,至少有一个水平的出丝率更高。c、由多重比较(tukey)检验可知,与0.16mm比较,0.17mm的置信区间包含0,意味着这两个水平不存在统计显著性差异。结论:0.16mm、0.17mm的这两个水平的切梗丝厚度之间没有显著性差异,与0.15mm水平具有显著性差异。(4)贮存时间原因验证①数据收集方案:把贮存时间分为3个水平,分别为:4-10h、10-15h、15h以上,确定α=0.05,β=0.1,再根据界定阶段统计的出丝率标准偏差和出丝率差值确定样本数量:功效和样本数量单因子方差分析根据数据收集难易程度,确定每个水平采集5个数据。然后采用单因子方差分析进行验证:②正态性检验如图22所示结论:从p值来看,三水平的数据均大于0.05,因此认为其服从正态分布。③独立性检验结论:从p值看,三水平相互独立。④等方差检验等方差检验:c22与c21结论:从图23可知,bartlett检验p值大于0.05,因此,符合等方差假设。综合上述三种检验,收集的数据可以进行单因子方差分析。⑤单因子方差分析从图24-26分析:a、残差是正态分布,且均值为0,方差恒定,因此没有足够理由拒绝模型。b、p值大于0.05,不能拒绝原假设,统计检验不显著。结论:三个水平的出丝率没有显著性差异。(5)风选梗头量原因验证①数据收集方案:收集梗丝出丝率与风选梗头量的对应数据,根据数据收集难易程度和项目需要,收集10组数据,然后进行回归分析。②做出散点图如图27所示由散点图可知,二者之间没有高次项,可能存在线性相关关系。③进行回归分析出丝率与风选梗头量的pearson相关系数=-0.895p值=0.000回归分析:从图28分析:a、残差是正态分布,且均值为0,方差恒定,因此没有足够的理由拒绝模型。b、p值小于0.05,r=-0.895,说明α=0.05水平上梗丝出丝率与风选梗头量之间有负相关关系。结论:梗丝出丝率与风选梗头量之间有负相关关系。(6)筛分碎梗量原因验证①数据收集方案:收集梗丝出丝率与筛分碎梗量的对应数据,根据数据收集难易程度和项目需要,收集10组数据,然后进行回归分析。②做出散点图,如图29可知,二者之间没有高次项,可能存在线性相关关系。③进行回归分析由图30分析:a、残差是正态分布,且均值为0,方差恒定,因此没有足够的理由拒绝模型。b、p值小于0.05,r=-0.972,说明α=0.05水平上梗丝出丝率与筛分碎梗量之间有负相关关系。结论:梗丝出丝率与筛分碎梗量之间有负相关关系。2.2原因验证结果:通过上面对筛选出原因的验证,对主要原因进行再确认:3改进阶段3.1提出并选择改进措施1)针对各影响因子,从管理原因上确定选择改进措施的标准及标准权重,从技术原因上采用doe的方法寻找合理的参数搭配:(1)碎梗筛分量;加强投料烟梗的检验,发现碎梗过多进行退货,由物流中心重新筛分;(2)梗头风选量:梗头风选量与梗丝风选风门开度有关,固通过doe试验找到合理搭配参数,提高切丝质量后,可降低梗头风选量;对梗头含丝量进行检验,加强操作人员对梗头含丝量的自检;(3)水洗梗水温:采用doe方法确定合理的搭配参数;(4)水泵电机转速:采用doe方法确定合理的搭配参数:(5)切梗厚度:采用doe方法确定合理的搭配参数。2)针对技术原因应用doe找到最佳方案①试验目的:提高梗丝出丝率;②试验指标:梗丝出丝率;③确定因子与水平四个因子水平根据分析阶段对各因子方差分析的结果,确定合理的因子水平(这四个因子的水平都是设备的设定值,所以没有设定允差)。因子水平表因子/水平12a:水洗梗水温3555b:水泵电机转速3842c:切丝厚度0.150.17d:风选风门开度/风选梗头量0.20.8选择正交表:根据银子的个数和水平选择全因子并安排4个中心点(即24 4)的试验。④设计全因子试验设计表全因子试验设计表⑤全因子试验设计分析a、按照全因子试验设计分析的步骤,对试验设计进行了分析,不断修改拟合模型中的“选项”,去掉不显著的项,这个过程需要,重新进行计算,最后得到如下的计算结果:拟合因子:出丝率与水洗梗水温,水泵电机转速,切丝厚度,风门开度b、对最后的结果进行分析:第一步,拟合选定模型。首先将全部被选项列入模型,其计算结果如下:从anova表中可以清楚的看出,主效应中,p-value为0.029,,显示所选定的模型总的效果是显著的。在弯曲一栏中,p-value为0.558,显示相应变量没有明显的弯曲,在失拟一栏中,p-value为0.269,显示对相应变量的拟合没有明显的失拟。第二步,残差分析。如图31-35所示观察残差对于观测值顺序的散点图,可以看到对观测顺序的散点图中各点是随机在水平轴上下无规则的波动,没有不正常的现象。观察残差对于拟合值得散点图,可以看到散点图中各个点没有“漏斗形”和“喇叭形”,残差没有不正常观察残差的正态性检验图,可以看到残差时服从正态分布的。观察残差对于各自变量的散点图,可以看到没有弯曲的趋势。第三步,判断模型是否需要改进。由上述分析,可以认定已经选定了最终的模型。确定对原始数据的回归方程:y=0.388828 0.0106001a 0.0306153b 4.76225c 0.364064d-0.0109604a*c 0.00075044a*d第四步,对选定的模型进行分析解释。输出各因子的主效应图、交互作用图。如图36、37所示,从图中可以看出,四个因子对相应变量影响确实是显著的。因子水洗梗水温和水泵电机转速、水泵电机转速和风门开度的交互作用对于相应变量的影响确实是很显著的。输出等值线图、响应曲面图。如图38和39所示,从以上两图中可以看出,各个因子的交互作用对于相应变量的影响是显著的。第五步,实现最优化。根据本项目的目标要求,优化目标是属于“望大”型的,取最低值0.8477,取目标值0.90,计算后得到最大值的计算结果。如图40所示,当因子a水洗梗水温取55.069,水泵电机转速取42.255,切丝厚度取0.165,风门开度取0.214时,出丝率将会达到0.9050.第六步,验证目标是否已经达到在来料稳定和设备正常运行,其他工艺技术参数不变的情况下,设定水洗梗水温取55℃,水泵电机转速取42hz,风门开度取0.2,切丝厚度取0.16mm,时,出丝率达到89.25%;在来料稳定和设备正常运行,其他工艺技术参数不变的情况下,设定水洗梗水温取55℃,水泵电机转速取42hz,风门开度取0.2,切丝厚度取0.17mm,时,出丝率达到89.93%。将验证结果与试验目标相比较,达到目标,结束实验。3.2实施改进措施(1)实施改进措施,制定实施计划改进措施实施计划表(2)改进的效果描述及验证①梗头风选量假设:h0:μ2(改进后)≥μ1(改进前)h1:μ2(改进后)<μ1(改进前)统计检验方法:由于σ未知,所以选择双样本t检验。选择α=0.05,β=0.1双样本t检验和置信区间:改进前,改进后如图41所示,结论:p值小于0.05,所以拒绝原假设,改进后梗头风选占烟梗投料的比例明显降低。②筛分碎梗量假设:h0:μ2(改进后)≥μ1(改进前)h1:μ2(改进后)<μ1(改进前)统计检验方法:由于σ未知,所以选择双样本t检验。选择α=0.05,β=0.1双样本t检验和置信区间:改进前,改进后如图42所示,结论:p值小于0.05,所以拒绝原假设,改进后碎梗筛分量占烟梗投料的比例明显降低。③全因子设计的验证试验首先,求出预测值处单个值得预测区间:然后按照《卷烟工艺测试与分析大纲》进行测试验证。验证3次均值为89.61%。计算m个观测值的平均值95%的置信区间计算公式是式中,n是试验总次数;p是最终模型中所包含的项数(包括常数项);m是检验实验的次数。在本次试验中n=20,p=6,m=3,seoffits=0.003418,mes=0.00003225.查14个自由度的t分位数表可得t1-α(n-p)=t0.975(14)=2.145变动半径的公式如下所示:代入数值计算可得为0.01.因此可知,三个观测值的平均值的95%的置信区间为:y±σ=0.9050±0.01=(0.8950,0.9150)可见,验证结果均值落在95%置信区间内,说明一切正常,模型正确,预测结果可靠。(3)改进对比①进行fema分析,寻找潜在的失效,并进行改进通过对改进前后关键原因的fema分析,可以看出实施改进措施后关键原因的风险度rpn值都小于100,说明改进措施是有效的。3.3验证改进措施改进措施实施后,评估改进效果。(1)改进效果图示如图43所示,可以看出,改进效果明显,达到目标值。(2)对改进后出丝率的显著性进行假设检验问题:改进后的梗丝出丝率是否达到目标值88.5%目标:达到目标值88.5%假设:h0:μ1≤88.5h1:μ2>88.5%统计检验方法:由于σ未知,所以选择单样本t检验。选择α=0.05,β=0.1单样本t:如图44所示,结论:p值小于0.05,所以拒绝原假设,改进后出丝率大于88.5%。4、控制:按照出丝率的计算公式,以出柜梗丝重量作为变量,以投料烟梗重量作为子组大小,绘制控制图:如图45-47所示,从以上控制措施实施效果及出丝率控制图来看,过程控制平稳,改进后的出丝率平均为89.61%,超过了目标。上述描述的实施例仅仅是本发明一部分实施例,而不是全部的实施例。基于本发明中的实施例,本领域普通技术人员在没有做出创造性劳动前提下所获得的所有其他实施例,都属于本发明保护的范围。当前第1页12
再多了解一些
本文用于企业家、创业者技术爱好者查询,结果仅供参考。