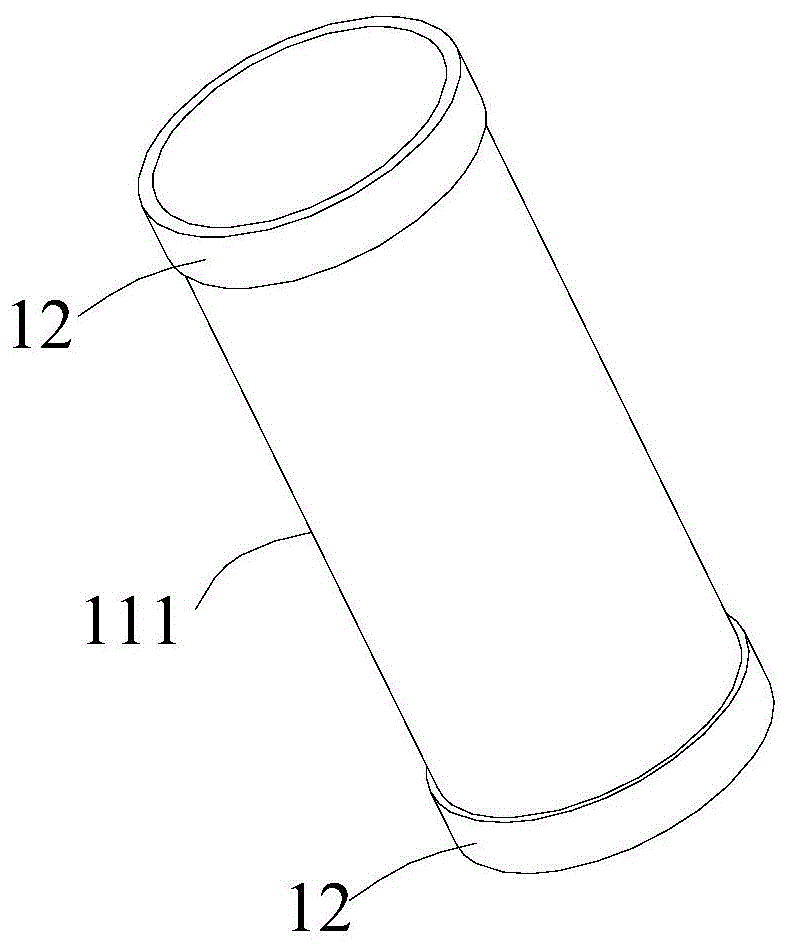
【技术领域】
本发明涉及气溶胶装置领域,尤其涉及一种用于气溶胶生成装置的加热组件及气溶胶生成装置。
背景技术:
目前市场上应用于气溶胶生成装置的加热不燃烧组件,其加热元件采用的是在氧化锆片等基体上印刷具有一定电阻阻值的例如金、银、铂和/或镍等金属浆料形成的导电轨迹,通电后导电轨迹产生热量传递氧化锆片上,从而通过氧化锆片实现对气溶胶形成基质进行加热。一方面,由于是通过导电轨迹传递热量给氧化锆片,这样就会造成导电轨迹跟氧化锆片之间有温度差,同时靠近导电轨迹的部位温度高,远离导电轨迹的部位温度低,温度分布不均,会造成释放的气溶胶一致性差,不能满足人们的使用需求;另一方面,使用过程中,导电轨迹在高温下容易与基体脱落。
技术实现要素:
本发明的主要目的在于提供一种加热组件及气溶胶生成装置,以加热不燃烧的方式,使加热温度分布的均匀性及产出的气溶胶的一致性。
为达成上述目的,本发明所提供的技术方案是,其第一方面提供一种用于气溶胶生成装置的加热组件,包括控制器、与所述控制器电连接的供电电源和加热元件,所述加热元件包括用于加热气溶胶形成基质以产出气溶胶的整体导电的气溶胶产生基质发热体和设置到所述发热体的电极,所述发热体通过该电极与所述控制器电连接。本发明所述的整体导电发热体是指该发热体由于其自身具有导电特性,而能完成现有技术需要基体与导电轨迹结合方能胜任的工作,并且由于其整体导电,加热更均匀、一致。
作为优选的技术方案,所述电极还具有伸出的引脚,所述发热体通过该电极引脚与所述控制器电连接。
作为优选的技术方案,所述发热体的原料组分包括基质粉末、金属粉末、高温粘结相粉末。
所述基质粉末质量占发热体质量的80%~92.5%,所述金属粉末质量占发热体质量的5%~15%,所述高温粘结相物质粉末质量占发热体质量的2.5%~5%。。
所述基质粉末为氧化物粉末、氮化物粉末或碳化物粉末。
所述氧化物粉末为zro2、sio2或al2o3中的至少一种。
所述氮化物粉末为sin、tin和aln中的至少一种。
所述碳化物粉末是选自粉末状sic、tic和alc中的至少一种。
所述金属粉末是选自过渡金属单质粉末或金属合金粉末;作为更进一步优选的技术方案,所述过渡金属包括ag、co、ti、cu、pt、mo、ni、cr或w。
所述高温粘结相是在高温下(1500℃~1800℃)用于基质粉末和金属粉末的粘结作用,作为优选的技术方案,所述高温粘结相物质粉末为玻璃相物质粉末,即在高温下能形成玻璃的氧化物;作为更进一步优选的技术方案,所述玻璃相物质粉末是选自sio2、al2o3、cao、b2o3、bi2o3粉末中的至少一种。
所述基质粉末、过渡金属粉末、高温粘结相物质粉末的粒度为1~20μm。
所述发热体的电阻率为5μω·m~5000μω·m,更优选10μω·m~1000μω·m。
所述发热体以包含下述步骤的方法制成:
(1)、配料:按事先确定的比例分别称取基质粉末、金属粉末、玻璃相物质粉末,并混合均匀;
(2)、磨料:将上述混合后的原料粉末投入磨料机中研磨;
(3)、干燥成坯:研磨后的原料经干燥后加入成型剂混合均匀,以干压、流延或挤出方式经模具制成为坯体;
(4)、烧结成型:成型后的坯体移至烧结炉内常压或热压烧结,再经随炉冷却后即制得所述发热体。
所述步骤(3)中的成型剂为石蜡、桐油、聚乙二醇、聚乙烯醇或聚甲基纤维素中的至少一种。
作为优选的技术方案,所述发热体为两端开口的筒状体,所述筒状体的内腔用于放置气溶胶形成基质;所述筒状体的两端分别设置有一个所述电极,两个电极的极性相反。
所述发热体包括至少两个依次连接的筒状体,所述筒状体的两端开口,所述至少两个筒状体的内腔用于放置气溶胶形成基质;所述至少两个筒状体中,相邻的两个筒状体之间的连接处设置有一个所述电极,第一个筒状体的远离与其相邻的筒状体的一端设置有一个所述电极,最后一个筒状体的远离与其相邻的筒状体的一端设置有一个所述电极,相邻的两个电极的极性相反。
所述至少两个筒状体可独立工作从而可实现对气溶胶形成基质进行分段加热。
作为优选的技术方案,所述发热体为片状体,所述片状体用于部分或全部插设到气溶胶形成基质的内部;所述片状体设有贯通其正面和背面的至少一条贯通槽,所述贯通槽沿所述片状体的轴向延伸,且所述贯通槽的一端延伸至所述片状体的第一端,另一端靠近所述片状体的第二端,所述片状体的第一端在位于每个所述贯通槽的两侧分别设置有一个所述电极,相邻的两个电极的极性相反。
所述片状体的第二端形成有尖端以方便片状体插设到气溶胶形成基质的内部。
所述发热体还可以包括筒体或杯体,片状体部分或全部收容于筒体或杯体内,所述筒体或杯体的内腔用于放置气溶胶形成基质;所述片状体用于部分或全部插设到气溶胶形成基质的内部,所述筒体或杯体的两端设置分别设置有一个电极,两个电极的极性相反。
作为优选的技术方案,所述发热体为针状体,所述针状体用于部分或全部插设到气溶胶形成基质的内部;所述针状体设有贯通其外周面的贯通槽,所述贯通槽沿所述针状体的轴向延伸,且所述贯通槽的一端延伸至所述针状体的第一端,另一端靠近所述针状体的第二端,所述针状体的第一端在位于所述贯通槽的两侧分别设置有一个所述电极,两个电极的极性相反。
为加强发热体硬度或防止气溶胶形成基质在贯通槽内残留,贯通槽也可用绝缘材料填充。
所述针状体的第二端为尖端以方便针状体插设到气溶胶形成基质的内部。
所述发热体还可以包括筒体或杯体,针状体部分或全部收容于筒体或杯体内,所述筒体或杯体的内腔用于放置气溶胶形成基质;所述针状体用于部分或全部插设到气溶胶形成基质的内部,所述筒体或杯体的两端设置分别设置有一个电极,两个电极的极性相反。
作为优选的技术方案,所述发热体为一端开口的杯状体,所述杯状体的内腔用于放置气溶胶形成基质;所述杯状体的两端分别设置有一个所述电极,两个电极的极性相反。
所述杯状体的底部设有通气孔。
作为优选的技术方案,所述电极为低熔点金属合金材料件,所述低熔点金属合金材料件以钎焊或卡钳紧固方式设置到所述发热体。
所述金属合金材料件的电阻率大于0μω·m且小于0.11μω·m。
本发明的第二方面还在于,提供一种气溶胶生成装置,包括上述技术方案中所述的加热组件。
本发明提供的加热组件及气溶胶生成装置,通过发热体整体导电发热来产生热量,相较于在发热体上面印刷导电轨迹,以加热不燃烧的方式实现对气溶胶形成基质的加热,更能保证发热体的温度分布均匀性,加热过程中不会出现局部温度过高或过低的情况,保证了产出的气溶胶的一致性,满足了人们的使用需求。
另外,本发明的加热组件及气溶胶生成装置,贯通槽填充绝缘物质,可以加强发热体硬度及防止气溶胶形成基质在贯通槽内残留,从而口感更好。
【附图说明】
为进一步揭示本案之具体技术内容,首先请参阅附图,其中:
图1为本发明一实施例提供的一种加热组件的加热元件的结构示意图;
图2为图1所示加热元件的第一种替换方案的结构示意图;
图3为图1所示加热元件的第二种替换方案的结构示意图;
图4为图1所示加热元件的第三种替换方案的结构示意图;
图5为图1所示加热元件的第四种替换方案的结构示意图;
图6为图1所示加热元件的第五种替换方案的结构示意图。
符号说明:
筒状发热体111片状发热体112
针状发热体113第二片状发热体114
杯状发热体115
电极12贯通槽13
尖端14通气孔15
【具体实施方式】
本发明的实施例提供一种气溶胶生成装置,包括外壳和设置在外壳内的加热组件。外壳的一端开口,便于放置气溶胶形成基质。加热组件包括控制器、与控制器电连接的供电电源和加热元件。控制器用于控制加热元件的工作。供电电源用于给加热元件供电。供电电源例如为电池,电池提供例如2.0-5.0v的输出电压。
请参阅图1,加热元件包括用于加热气溶胶形成基质以产出气溶胶的筒状发热体111(筒状体)和设置在筒状体111上的电极12。电极12可以是印刷或贴片设置在发热体上的电触点/电触片,电极12与筒状体111电连接,筒状体111经由电极12与控制器电连接。为节省空间,也可以在电极12上伸出引脚(图1中未显示)与控制器电连接,从而供电电源经控制器、引脚、电极12给筒状体111供电。气溶胶形成基质为一种类似香烟形状的气溶胶生成制品。通过该种结构,本发明通过筒状体111自身导电发热来产生热量,从而实现加热气溶胶形成基质,保证了加热温度分布的均匀性,不会出现局部温度过高或过低的情况,保证了产出的气溶胶的一致性,并且筒状体111具有升温快、热效率高、热导率高等特点,还保证了产出的气溶胶的高效性,极大的满足了人们的使用需求。
在发热体电极上是否设置引脚,当视气溶胶生成装置的空间大小而定。在需要将气溶胶生成装置小型化时,加热体与控制器不必直接接触且装配在同一位置,可视需要将发热体与控制器分别设置在便利的空间,之间通过引脚实现电连接;在气溶胶生成装置具有充裕空间的情况下,则可以将发热体与控制器设置在一起,通过电触点/触片式电极而实现二者之间直接的电连接。
筒状体111的电阻率为5μω·m(微欧姆·米)~5000μω·m,优选为10μω·m~1000μω·m。
电极12为低电阻率金属合金材料件,低电阻率金属合金材料件以钎焊或卡钳紧固方式设置到筒状体111。低电阻率金属合金材料件的电阻率大于0μω·m且小于0.11μω·m,优选为0.09μω·m。低电阻率金属合金材料件包含的原料组分为ag62%,cu28%,in8%,ti2%。
本实施例中,两端开口的筒状体111的内腔用于放置气溶胶形成基质,在实际应用时,可通过外壳一端的开口将气溶胶形成基质放置到筒状体111的内腔。筒状体111的两端分别设置有一个环状的电极12。两个电极12的极性相反。
请参阅图2,在第一种替换方案中,发热体包括至少两个依次连接的筒状体111,筒状体111的两端开口,所述至少两个筒状体111的内腔用于放置气溶胶形成基质,在实际应用时,可通过外壳一端的开口将气溶胶形成基质放置到至少两个筒状体111的内腔。所述至少两个筒状体111中,相邻的两个筒状体111之间的连接处设置有一个环状的电极12,第一个筒状体111的远离与其相邻的筒状体111的一端设置有一个环状的电极12,最后一个筒状体111的远离与其相邻的筒状体111的一端设置有一个环状的电极12。相邻的两个电极12的极性相反。本实施例展示了两个依次连接的筒状体111。
所述至少两个筒状体111可组合工作。可以理解地,所述至少两个筒状体111也可独立工作从而可实现对气溶胶形成基质进行分段加热,从而可实现控制生成气溶胶的量。每个筒状体111的独立工作可通过控制器进行控制。
本实施例的筒状体111的数量还可以是例如三个、四个、五个等等,可根据实际情况进行设置。
请参阅图3,在第二种替换方案中,发热体为片状发热体112(片状体)。片状体112用于部分或全部插设到气溶胶形成基质的内部,在实际应用时,可通过外壳一端的开口将气溶胶形成基质插到片状体112,以使片状体112部分或全部插设到气溶胶形成基质的内部。片状体112设有贯通其正面和背面的贯通槽13。贯通槽13沿片状体112的轴向延伸,且贯通槽13的一端延伸至片状体112的第一端,另一端靠近片状体112的第二端。片状体112的第一端在位于贯通槽13的两侧分别设置有一个电极12。每个电极12包括两个部分,两个部分分别位于片状体112的第一端的正面和背面。两个电极12的极性相反。如前所述,视气溶胶生成装置的空间情况,可以在电极12上设置引脚或不设置引脚。
片状体112的第二端形成有三角形尖端14以方便片状体112插设到气溶胶形成基质的内部。
为了实现气溶胶基质的内外部更均匀加热,发热体还可以包括筒体或杯体,片状体部分或全部收容于筒体或杯体内,在筒体或杯体的内腔放置气溶胶形成基质;片状体可部分或全部插设到气溶胶形成基质的内部,在筒体或杯体的两端设置分别设置有一个极性相反的电极。
请参阅图4,在第三种替换方案中,发热体为针状发热体113(针状体)。针状体113用于部分或全部插设到气溶胶形成基质的内部,在实际应用时,可通过外壳一端的开口将气溶胶形成基质插到针状体113,以使针状体113部分或全部插设到气溶胶形成基质的内部。针状体113设有贯通其外周面的贯通槽13。贯通槽13沿针状体113的轴向延伸,且贯通槽13的一端延伸至针状体113的第一端,另一端靠近针状体113的第二端,针状体113的第一端在位于贯通槽13的两侧分别设置有一个半圆状的电极12。两个电极12的极性相反。如前所述,视气溶胶生成装置的空间情况,可以在电极12上设置引脚或不设置引脚。
针状体113的第二端为锥形尖端14以方便针状体113插设到气溶胶形成基质的内部。
为了实现气溶胶基质的内外部更均匀加热,发热体还可以包括筒体或杯体,针状体部分或全部收容于筒体或杯体内,在筒体或杯体的内腔放置气溶胶形成基质;针状体可部分或全部插设到气溶胶形成基质的内部,在筒体或杯体的两端设置分别设置有一个极性相反的电极。
请参阅图5,在第四种替换方案中,发热体为第二片状发热体114(第二片状体)。第二片状体114用于部分或全部插设到气溶胶形成基质的内部,在实际应用时,可通过外壳一端的开口将气溶胶形成基质插到第二片状体114,以使第二片状体114部分或全部插设到气溶胶形成基质的内部。第二片状体114设有贯通其正面和背面的至少两个贯通槽13。贯通槽13沿第二片状体114的轴向延伸,且贯通槽13的一端延伸至第二片状体114的第一端,另一端靠近第二片状体114的第二端。第二片状体114的第一端在位于每个贯通槽13的两侧分别设置有一个电极。每个电极12包括两个部分,两个部分分别位于第二片状体114的第一端的正面和背面。相邻的两个电极12的极性相反。如前所述,视气溶胶生成装置的空间情况,可以在电极12上设置引脚或不设置引脚。
本实施例展示的贯通槽13为两个。可以理解地,贯通槽13的数量也可以是例如三个、四个等等,可根据实际情况进行设置。
为加强发热体硬度或防止气溶胶形成基质在贯通槽内残留,贯通槽也可用绝缘材料填充。
第二片状体114的第二端形成有三角形尖端14以方便第二片状体114插设到气溶胶形成基质的内部。
请参阅图6,在第五种替换方案中,发热体为一端开口的杯状发热体115(杯状体)。杯状体115的内腔用于放置气溶胶形成基质,在实际应用时,可通过外壳一端的开口将气溶胶形成基质放置到杯状体115的内腔。杯状体115的两端分别设置有一个环状的电极(图6中未显示)。两个电极的极性相反。如前所述,视气溶胶生成装置的空间情况,可以在电极12上设置引脚或不设置引脚。
杯状体115的底部设有通气孔15,通气孔15方便外部的空气进入,以便和产生的气溶胶一起供使用者吸食。
此外,应用于本发明的整体导电的气溶胶产生基质发热体的原料组分为包括基质粉末、金属粉末、高温粘结相的整体导电发热坯体一体烧结成型。基质粉末可以为氧化物粉末(如zro2、al2o3或sio2)、氮化物粉末(sin、tin或/和aln)或碳化物粉末(sic、tic或/和alc),但是碳化物粉末制得的发热体热分布最均匀。
金属粉末质量占发热体的5~15%,金属粉末质量占发热体质量的5%~15%,高温粘结相物质粉末质量占发热体质量的2.5%~5%。金属粉末是选自过渡金属单质粉末或合金粉末,根据需要,过渡金属粉末可以选择ag、co、ti、cu、pt、mo、ni、cr或w,选择ag、cu和ni的单质粉末或者合金粉末,获得的发热体电阻率相对较低,选择pt、w的单质粉末或者合金粉末,获得的发热体电阻率相对较高。
粘结相粉末是用于基质粉末和金属粉末的粘结作用可以为玻璃相物质粉末,比如sio2、al2o3、cao、b2o3、bi2o3粉末中的至少一种。
上述基质粉末、过渡金属粉末、玻璃相粉末的粒度为1~20μm。
下面通过制备例、对比例对本发明提供的发热体及加热元件等的制备进行详细阐述,并与其它类型的加热产品作性能测试与比较。
制备例1
本制备例的具体步骤如下:
(1)配料
分别取90克sic粉(纯度≥95%,优选的纯度为99%)与10克tic粉(纯度≥95%,优选的纯度为99%),加入15克金属单质ni粉,同时加入5克玻璃相物质粉料(玻璃相物质主要成份为sio2、al2o3、b2o3,其中重量比sio2:al2o3:b2o3=9:4:3);上述原料粉末的粒度d50为5μm;
(2)磨料
将上述称量后的各原料投入到球磨机中,同时加入去离子水作为分散介质,锆球是磨料,其中原料:锆球:水的重量比为1:2:0.6,球磨时间22h;
(3)喷雾干燥
将球磨好的料浆,经蠕动泵直接压入到离心干燥机内,经过高温加热脱水后将其中含有的水分蒸发出来,使粉料变为干燥粉末;
(4)成坯
将喷雾造粒后的粉末,加入总量占粉料重量5%的桐油、聚甲基纤维素、聚乙二醇等添加剂作为成型剂(其中桐油、羧甲基纤维素、聚乙二醇重量比为0.5:1:1),同时加入重量比为10%的去离子水,将粉料,去离子水与上述成型剂在搅拌机内搅拌2-3h,使其混合充分,从机器内取出后,密封陈腐20-24h;
将上述泥料,通过挤压成型机在20-30mpa的压力下,挤出成型为筒状坯体,挤出的产品置于微波炉中快速烘干,使其硬化防止开裂、变形;
(5)烧结
将坯体移至高温耐火材料的匣钵内,在1个大气压的n2保护气氛下,升温速度为8℃/min,升至最高温度为1500℃保持4h常压烧结,烧结完成后自然随炉冷却;
(6)后加工
将烧结成型的筒状发热体通过无心磨,将其外表面磨平整以达到标准厚度(0.5-1.0mm),采用超声波清洗,使其表面的粉尘去除干净,得到发热体a。
后续使用
筒状发热体制作好后,将材料为低熔点金属合金的电极以钎焊或卡钳紧固方式设置到筒状发热体的两端,从而制得上述的加热元件。将加热元件、控制器和供电电源装置到外壳后即制得上述的气溶胶生成装置,当供电电源提供电压时,筒状发热体导电将电能转换为热能,瞬间产生高温,产生的热量加热气溶胶形成基质,从而产生气溶胶供使用者吸食。
制备例2
本制备例的具体步骤如下:
(1)配料
分别取sic粉(纯度≥95%,优选的纯度为99%)与tin粉(纯度≥95%,优选的纯度为99%)95克、5克,加入12克的金属粉末混合物(金属粉末为ni、cr、mo合金粉末,其中ni:cr:mo重量比为75:23:2),同时加入3克玻璃相物质粉末(玻璃相物质主要成份为sio2、al2o3、cao,其中重量比sio2:al2o3:cao=4:2:0.5),上述原料粉末的粒度d50为20μm;
(2)磨料
按照步骤(1)称量后的原料投入到球磨机中,同时加入去离子水作为分散介质,锆球是磨料,球磨时间24h,其中原料:锆球:水=1:2:0.6;
(3)喷雾造粒
将球磨好的料浆,出料前1-2h内加入8-10%的pva水溶液(浓度10%)作为成型剂与水料混合均匀,经蠕动泵直接压入到离心喷雾机内,再经高温加热脱水造粒是粉料直接变为球状,颗粒大小为100-200μm;
(4)成坯
将前述完成的粒料,在30mpa的压力经干压成型机压制成片状坯体;
(5)烧结
将坯体移至高温耐火材料的匣钵内,在一个大气压n2保护气氛下,升温速度为10℃/min,升至最高温度为1300℃保持3h热压烧结(热压压力为30mpa),烧结完成后自然随炉冷却;
(6)后续加工
将烧结后的片状发热体经过磨加工,使其上下表面磨平整以达到标准厚度(0.5-1.0mm),中部的缝隙可通过模具直接成型或者在通过后加工切割而成,采用超声波清洗,使其表面的粉尘去除干净,得到发热体b。
后续使用
片状发热体制作好后,将材料为低熔点金属合金的电极以钎焊或卡钳紧固方式设置到片状发热体的第一端的正面和背面并位于相应的贯通槽的两侧,从而制得上述的加热元件。将加热元件、控制器和供电电源装置到外壳后即制得上述的气溶胶生成装置,当供电电源提供电压时,片状发热体导电将电能转换为热能,瞬间产生高温,产生的热量加热气溶胶形成基质,从而产生气溶胶供使用者吸食。
制备例3
本制备例的具体步骤如下:
(1)配料
分别取sic粉(纯度≥95%,优选的纯度为99%)与aln粉(纯度≥95%,优选的纯度为99%)85克、15克,加入8克的钨(w)金属粉末,同时加入3克玻璃相物质(玻璃相物质主要成份为sio2、al2o3,其中重量比sio2:al2o3=4:2),上述原料粉末的粒度d50为5μm;
(2)磨料
将上述称量后的原料投入到球磨机中,同时加入去离子水作为分散介质,锆球是磨料,其中原料:锆球:水=1:2:0.6,球磨时间22h;
(3)喷雾干燥
将球磨好的料浆,经蠕动泵直接压入到离心干燥机内,经过高温加热脱水后将其中含有的水分蒸发出来,使粉料变为干燥粉末;
(4)搅拌成坯
将喷雾造粒后的粉料,加入总量占粉末重量15%的石蜡作为成型剂,将粉料与石蜡在搅拌机内搅拌20h,同时加温80℃,使其混合充分;然后将料浆转移至成型的搅拌料筒内,在气压压力为0.6mpa的压力下,将料浆注入到预先的模具内做成针状坯体,冷却后成型;
(5)烧结
将产品埋入氧化铝粉中,经过高温500-600℃/30min处理后将其中石蜡等有机成型剂排除干净,筛除氧化铝粉,将产品转移至高温气氛炉内,在一个大气压的n2或ar气保护气氛下,以升温速度为5-10℃/min,升至温度为1300-1500℃保持2-4h常压烧结,烧结完成后自然随炉冷却;
(6)后续加工
将烧结完成的针状发热体通过磨床,将其外表面磨光滑直至达到要求尺寸,采用超声波清洗,使其表面的粉尘去除干净,得到发热体c。
后续使用
针状发热体制作好后,将材料为低熔点金属合金的电极以钎焊或卡钳紧固方式设置到针状发热体的第一端并位于贯通槽的两侧,从而制得上述的加热元件。将加热元件、控制器和供电电源装置到外壳后即制得上述的气溶胶生成装置,当供电电源提供电压时,针状发热体导电将电能转换为热能,瞬间产生高温,产生的热量加热气溶胶形成基质,从而产生气溶胶供使用者吸食。
制备例4
本制备例的具体步骤如下:
(1)配料
分别取100克sic粉(纯度≥95%,优选的纯度为99%),加入15克金属单质ni粉,同时加入5克玻璃相物质粉料(玻璃相物质主要成份为sio2、al2o3、b2o3,其中重量比sio2:al2o3:b2o3=9:4:3);上述原料粉末的粒度d50为5μm;
(2)磨料
将上述称量后的各原料投入到球磨机中,同时加入去离子水作为分散介质,锆球是磨料,其中原料:锆球:水的重量比为1:2:0.6,球磨时间22h;
(3)喷雾干燥
将球磨好的料浆,经蠕动泵直接压入到离心干燥机内,经过高温加热脱水后将其中含有的水分蒸发出来,使粉料变为干燥粉末;
(4)成坯
将喷雾造粒后的粉末,加入总量占粉料重量5%的桐油、聚甲基纤维素、聚乙二醇等添加剂作为成型剂(其中桐油、羧甲基纤维素、聚乙二醇重量比为0.5:1:1),同时加入重量比为10%的去离子水,将粉料,去离子水与上述成型剂在搅拌机内搅拌2-3h,使其混合充分,从机器内取出后,密封陈腐20-24h;
将上述泥料,通过挤压成型机在20-30mpa的压力下,挤出成型为筒状坯体,挤出的产品置于微波炉中快速烘干,使其硬化防止开裂、变形;
(5)烧结
将坯体移至高温耐火材料的匣钵内,在1个大气压的n2保护气氛下,升温速度为8℃/min,升至最高温度为1500℃保持4h常压烧结,烧结完成后自然随炉冷却;
(6)后加工
将烧结成型的筒状发热体通过无心磨,将其外表面磨平整以达到标准厚度(0.5-1.0mm),采用超声波清洗,使其表面的粉尘去除干净,得到发热体d。
后续使用
筒状发热体制作好后,将材料为低熔点金属合金的电极以钎焊或卡钳紧固方式设置到筒状发热体的两端,从而制得上述的加热元件。将加热元件、控制器和供电电源装置到外壳后即制得上述的气溶胶生成装置,当供电电源提供电压时,筒状发热体导电将电能转换为热能,瞬间产生高温,产生的热量加热气溶胶形成基质,从而产生气溶胶供使用者吸食。
制备例5
本制备例的具体步骤如下:
(1)配料
分别取100克sin粉(纯度≥95%,优选的纯度为99%),加入15克金属单质ni粉,同时加入5克玻璃相物质粉料(玻璃相物质主要成份为sio2、al2o3、b2o3,其中重量比sio2:al2o3:b2o3=9:4:3);上述原料粉末的粒度d50为5μm;
(2)磨料
将上述称量后的各原料投入到球磨机中,同时加入去离子水作为分散介质,锆球是磨料,其中原料:锆球:水的重量比为1:2:0.6,球磨时间22h;
(3)喷雾干燥
将球磨好的料浆,经蠕动泵直接压入到离心干燥机内,经过高温加热脱水后将其中含有的水分蒸发出来,使粉料变为干燥粉末;
(4)成坯
将喷雾造粒后的粉末,加入总量占粉料重量5%的桐油、聚甲基纤维素、聚乙二醇等添加剂作为成型剂(其中桐油、羧甲基纤维素、聚乙二醇重量比为0.5:1:1),同时加入重量比为10%的去离子水,将粉料,去离子水与上述成型剂在搅拌机内搅拌2-3h,使其混合充分,从机器内取出后,密封陈腐20-24h;
将上述泥料,通过挤压成型机在20-30mpa的压力下,挤出成型为筒状坯体,挤出的产品置于微波炉中快速烘干,使其硬化防止开裂、变形;
(5)烧结
将坯体移至高温耐火材料的匣钵内,在1个大气压的n2保护气氛下,升温速度为8℃/min,升至最高温度为1500℃保持4h常压烧结,烧结完成后自然随炉冷却;
(6)后加工
将烧结成型的筒状发热体通过无心磨,将其外表面磨平整以达到标准厚度(0.5-1.0mm),采用超声波清洗,使其表面的粉尘去除干净,得到发热体e。
后续使用
筒状发热体制作好后,将材料为低熔点金属合金的电极以钎焊或卡钳紧固方式设置到筒状发热体的两端,从而制得上述的加热元件。将加热元件、控制器和供电电源装置到外壳后即制得上述的气溶胶生成装置,当供电电源提供电压时,筒状发热体导电将电能转换为热能,瞬间产生高温,产生的热量加热气溶胶形成基质,从而产生气溶胶供使用者吸食。
制备例6
本制备例的具体步骤如下:
(1)配料
分别取100克zro2粉(纯度≥95%,优选的纯度为99%),加入15克金属单质ni粉,同时加入5克玻璃相物质粉料(玻璃相物质主要成份为sio2、al2o3、b2o3,其中重量比sio2:al2o3:b2o3=9:4:3);上述原料粉末的粒度d50为5μm;
(2)磨料
将上述称量后的各原料投入到球磨机中,同时加入去离子水作为分散介质,锆球是磨料,其中原料:锆球:水的重量比为1:2:0.6,球磨时间22h;
(3)喷雾干燥
将球磨好的料浆,经蠕动泵直接压入到离心干燥机内,经过高温加热脱水后将其中含有的水分蒸发出来,使粉料变为干燥粉末;
(4)成坯
将喷雾造粒后的粉末,加入总量占粉料重量5%的桐油、聚甲基纤维素、聚乙二醇等添加剂作为成型剂(其中桐油、羧甲基纤维素、聚乙二醇重量比为0.5:1:1),同时加入重量比为10%的去离子水,将粉料,去离子水与上述成型剂在搅拌机内搅拌2-3h,使其混合充分,从机器内取出后,密封陈腐20-24h;
将上述泥料,通过挤压成型机在20-30mpa的压力下,挤出成型为筒状坯体,挤出的产品置于微波炉中快速烘干,使其硬化防止开裂、变形;
(5)烧结
将坯体移至高温耐火材料的匣钵内,在1个大气压的n2保护气氛下,升温速度为8℃/min,升至最高温度为1500℃保持4h常压烧结,烧结完成后自然随炉冷却;
(6)后加工
将烧结成型的筒状发热体通过无心磨,将其外表面磨平整以达到标准厚度(0.5-1.0mm),采用超声波清洗,使其表面的粉尘去除干净,得到发热体f。
后续使用
筒状发热体制作好后,将材料为低熔点金属合金的电极以钎焊或卡钳紧固方式设置到筒状发热体的两端,从而制得上述的加热元件。将加热元件、控制器和供电电源装置到外壳后即制得上述的气溶胶生成装置,当供电电源提供电压时,筒状发热体导电将电能转换为热能,瞬间产生高温,产生的热量加热气溶胶形成基质,从而产生气溶胶供使用者吸食。
对比制备例1
本对比例的具体步骤如下:
(1)配料
分别取90克sic粉(纯度≥95%,优选的纯度为99%)与10克tic粉(纯度≥95%,优选的纯度为99%),上述粉料的粒度d50为5μm;
(2)磨料
将上述称量后的各原料投入到球磨机中,同时加入去离子水作为分散介质,锆球是磨料,其中原料:锆球:水的重量比为1:2:0.6,球磨时间22h;
(3)喷雾干燥
将球磨好的料浆,经蠕动泵直接压入到离心干燥机内,经过高温加热脱水后将其中含有的水分蒸发出来,使粉料变为干燥粉末;
(4)成坯
将喷雾造粒后的粉末,加入总量占粉料重量5%的桐油、聚甲基纤维素、聚乙二醇等添加剂作为成型剂(其中桐油、羧甲基纤维素、聚乙二醇重量比为0.5:1:1),同时加入重量比为10%的去离子水,将粉料,去离子水与上述成型剂在搅拌机内搅拌2-3h,使其混合充分,从机器内取出后,密封陈腐20-24h;
将上述泥料,通过流延成型为筒状坯体,挤出的产品置于微波炉中快速烘干,使其硬化防止开裂、变形;
(5)烧结
将坯体移至高温耐火材料的匣钵内,在1个大气压的n2保护气氛下,升温速度为8℃/min,升至最高温度为1500℃保持4h常压烧结,烧结完成后自然随炉冷却;
(6)后续加工:烧结体上、下面经过平面研磨加工,表面粗糙度达到ra≤0.3μm;
(7)印刷和烧结导电层:清洗烘干后印刷绝缘层玻璃介质浆料,印刷厚度为20-30μm,经高温1200℃/30min烧结后形成绝缘层,按照设计好的导电图案经网版丝印,将金属导电浆料(银钯浆料或铂浆等)印刷在已经烧结好的绝缘层上,印刷厚度为20-30μm,200℃/1h烘干后经高温1000℃/30min烧结形成导电层得到发热体x。
(8)接电极:将发热体x两端进行表面镀镍处理,再于镀镍处理后的部位进行钎焊引出电极。
性能测试与比较
取制备例和对比制备例获得的发热体进行如下指标测试:
(1)、电阻率:采用四探针电阻仪进行测试。
(2)、升温速率:向发热体两端电极部位提供15w供电功率,用热点偶测试仪测试距电极10mm处位置,记录每隔0.1秒的温度值,直至30s测试结束,取30s内温度变化值,换算为升温速度大小作为参数;
(3)、温度均匀性测试:向发热体两端电极部位提供15w供电功率,用热点偶测试仪分别测试距电极10mm,15mm,20mm三处发热体位置的温度,与平均温度的温差10℃以内视为均匀性好。
(4)、断裂韧性:按照单边预裂纹梁发法(sepb),在待测试样表面通过桥压法预制一条长度为l的裂纹,通过三点弯曲试验获得裂纹失稳扩展时的最大载荷pt,进而根据相应公式获得所测试验断裂韧性值;
表1制备例和对比制备例的发热体样品性能参数
从上表数据,不难看出,本发明实施例的发热体整体导电,对比制备例1样品x的面导电情况,发热体的温度分布更均匀均匀性,加热过程中不会出现局部温度过高或过低的情况。另外,本发明实施例的发热体断裂韧性更大,不容易折断,因此产品可靠性更好,使用寿命更长。
以上所述实施例仅表达了本发明的几种实施方式,其描述较为具体和详细,但并不能因此而理解为对本发明专利范围的限制。应当指出的是,对于本领域的普通技术人员来说,在不脱离本发明构思的前提下,还可以做出若干变形和改进,这些都属于本发明的保护范围。因此,本发明专利的保护范围应以所附权利要求为准。
本文用于企业家、创业者技术爱好者查询,结果仅供参考。