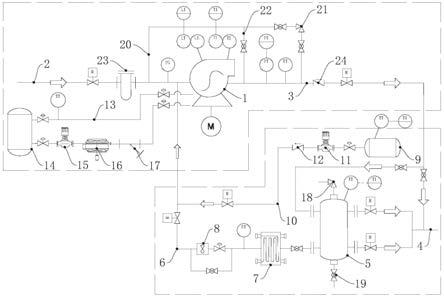
1.本实用新型涉及油气输送技术领域,具体是一种补液式油气混输装置及方法。
背景技术:
2.西部油区,以长庆油田(中国第一大油田)和塔里木油气田(中国第三大油气田)为代表。西部天然气产量远超原油,作为西气东输的起点,已成为国家重要的清洁能源来源地。
3.数口生产单井的油气汇聚后进入外输站,再输送到大型处理站对油气进行处理。传统输送方式为:将油气进行分离,分离出的气体通过压缩机输送到处理站脱水除硫,分离出的油水混合物通过泵送或汽车运送的方式输送或运送到处理站脱水除砂处理。传统处理方式往往需要分别建设油气两条输送管线,同时设置大型分离器、加热装置(例如加热炉)、压缩机、外输泵等,投资较大,特别是在黄土高原和塔里木盆地沙漠产区,生产管理成本也增大,已不适应目前国际形势以及提质增效的要求。
4.目前,新兴的输送方式为:采出油气不进行分离、不建外输站、不上分离器和加热炉,直接进行混输,只通过一条混输管线输送到大站再进行分离处理。新兴的输送方式可大幅减低投资成本、降低管理难度人工成本;同时,由于取消了压力容器,安全等级下降,降低了生产能耗。现有的混输泵,通常只能适应含气率80%以下工况,而上述油田工况,含气率往往都超过95%甚至更高。在如此高含气率的工况下,混输泵升温快,导致混输泵无法正常工作。
技术实现要素:
5.本实用新型提供一种补液式油气混输装置,解决现有油气混输装置在高含气率工况下出现段塞流,混输泵容易出现故障的问题。
6.本实用新型解决上述技术问题所采用的技术方案是:补液式油气混输装置,包括混输泵,混输泵的入口端连接混输进入管,混输泵的出口端连接混输排出管,混输排出管连接三通,三通的一个支管设置阀门并连接混输排出总管,三通的另一个支管设置阀门并连接气液分离器,气液分离器的气体出口设置阀门并连接混输排出总管,气液分离器的液体出口设置阀门并连接混输排出总管,气液分离器的液体出口还通过第一补液管与混输泵的入口端相连,第一补液管上设置阀门。
7.进一步的是:第一补液管上设置第一冷却器。
8.更进一步的是:第一补液管从进液端至出液端顺次设置阀门、第一冷却器、温度计、流量计和阀门。
9.进一步的是:补液式油气混输装置还包括补液罐,补液罐通过第二补液管与混输泵的入口端相连,第二补液管上设置第一管道泵和阀门,其中第一管道泵的进液端与补液罐相连。
10.更进一步的是:第二补液管上还设置第一止回阀,气液分离器和补液罐设置于补
液撬。
11.进一步的是:混输泵设置冷却结构。
12.具体的:冷却结构为:混输泵设置泵体夹层,泵体夹层设置进液口和出液口,进液口和出液口设置冷却管路,冷却管路从出液口到进液口依次设置阀门、冷却介质箱、第二管道泵、第二冷却器和过滤器。
13.进一步的是:气液分离器的顶部设置第一安全阀,底部设置排空阀,气液分离器还设置测温器。
14.进一步的是:混输泵的入口端和出口端之间设置旁通管,旁通管上设置第二安全阀,第二安全阀的入口端和出口端分别设置阀门,第二安全阀入口端的阀门的入口端与混输泵出口端之间设置连接管,连接管上设置阀门。
15.进一步的是:混输进入管上设置阀门和过滤装置,混输排出管上设置第二止回阀。
16.本实用新型的有益效果是:油气混合物经过混输泵增压后,进入气液分离器,分离出来的液体通过第一补液管进入混输泵,从而提高进入输泵增的液体的占比,适应高含气率、频繁段塞流的生产工况。
17.第一补液管上设置第一冷却器,使分离出来的液体降温后再进入混输泵,利于控制混输泵的温度。补液式油气混输装置还包括补液罐,通过第二补液管可向混输泵进行补液,提高进入输泵增的液体的占比。混输泵设置冷却结构,对混输泵进行降温,保证混输泵安全正常地运行。
附图说明
18.图1是本实用新型补液式油气混输装置的示意图。
19.附图标记:混输泵1、混输进入管2、混输排出管3、混输排出总管4、气液分离器5、第一补液管6、第一冷却器7、流量计8、补液罐9、第二补液管10、第一管道泵11、第一止回阀12、冷却管路13、冷却介质箱14、第二管道泵15、第二冷却器16、过滤器17、第一安全阀18、排空阀19、旁通管20、第二安全阀21、连接管22、过滤装置23、第二止回阀24。
具体实施方式
20.下面结合附图对本实用新型作进一步说明。
21.如图1所示,本实用新型补液式油气混输装置,包括混输泵1,混输泵1的入口端连接混输进入管2,油气混合物从混输进入管2进入混输泵1进行增压混输。混输进入管2上设置阀门和过滤装置23,使油气混合物过滤杂质之后再进入混输泵1,达到保护混输泵1使其平稳运行。例如,混输进入管2上设置电动球阀,通过仪表传感器等控制电动球阀,进而可控制进出口流量。混输泵1的出口端连接混输排出管3,混输排出管3连接三通,三通的一个支管设置阀门并连接混输排出总管4,三通的另一个支管设置阀门并连接气液分离器5。为了避免返流,混输排出管3上设置第二止回阀24,第二止回阀24和三通之间设置电动球阀。
22.为了保证混输泵1的安全,防止混输排出管3压力过高对混输泵1造成损伤,混输泵1的入口端和出口端之间设置旁通管20,旁通管20上设置第二安全阀21,第二安全阀21的入口端和出口端分别设置阀门。第二安全阀21入口端的阀门的入口端与混输泵1出口端之间设置连接管22,连接管22上设置阀门。连接管22实质上直接连接混输泵1的入口端和出口
端,如果混输进入管2有正压力且混输泵1在做维护保养时,油气混合物可通过连接管22直接流出。混输泵1的出口侧和入口侧分别设置测温、测压装置。
23.气液分离器5的气体出口设置阀门并连接混输排出总管4,在图1中,气液分离器5的气体出口设置于气液分离器5的上部。气液分离器5的液体出口设置阀门并连接混输排出总管4,气液分离器5的液体出口还通过第一补液管6与混输泵1的入口端相连,第一补液管6上设置阀门。气液分离器5的顶部设置第一安全阀18,底部设置排空阀19,气液分离器5还设置测温器。当油气混输出现段塞流,混输泵1不能输送时,通过第一补液管6将分离出来的液体介质输送至混输泵1的入口端,降低进入混输泵1的油气混合物中的气体含量,以保证正常输送。
24.油气混合物的含气量越大,输送温度越高,同时混输泵1泵体温度也上升(可达120℃),补液介质的温度相应也高。气液分离器5分离出来的液体介质通常为低含水凝析油,在20℃开始馏分、80℃就汽化甚至专成成气态,达不到补液要求,反而使混输泵1泵体温度继续上升,形成恶性循环。所以须对补液液体进行降温,例如降温至50℃左右,使其基本处于液态,能润滑螺旋套并形成油膜密封腔,保证气体正常输送。第一补液管6上最好设置第一冷却器7。如图1所示,第一补液管6从进液端至出液端顺次设置阀门、第一冷却器7、温度计、流量计8和阀门。其中,流量计8先串联控制阀再并联球阀,流量计8出口的阀门最好为电动球阀。
25.为了避免第一补液管6补液不足的情况,补液式油气混输装置还包括补液罐9,补液罐9通过第二补液管10与混输泵1的入口端相连,第二补液管10上设置第一管道泵11和阀门,其中第一管道泵11的进液端与补液罐9相连。第二补液管10和第一补液管6独立控制,可同时进行补液,也可以选择任一进行补液。补液罐9内的液体可以是水,最好是油水混合物;可以用罐车向补液罐9补液,也通过管线来补液。第二补液管10上还设置第一止回阀12。
26.高含气工况输送液体少,甚至为纯气状态,混输泵1泵体温度将会逐渐上升,特别是出口端。为了对混输泵1进行降温,混输泵1设置冷却结构,冷却结构的冷却方式可为风冷、水冷或油冷。例如,如图1所示,混输泵1设置泵体夹层,泵体夹层设置进液口和出液口,进液口和出液口设置冷却管路13,冷却管路13从出液口到进液口依次设置阀门、冷却介质箱14、第二管道泵15、第二冷却器16和过滤器17。冷却管路13的出液口与冷却介质箱14之间可设置两个阀门,两个阀门之间设置测温装置。冷却介质箱14和第二管道泵15之间设置阀门。混输泵1为螺杆泵,通过变频电机驱动,混输泵1引入冷却介质循环降温散热冷却,来保证混输泵1的安全正常运行,同时可缓解第一补液管6和第二补液管10补液液体的汽化情况。
27.混输泵1在输送介质过程中会产生一定热量,一般通过介质带走。但是,当介质温度已经高于混输泵1产生的温度时,介质不紧不能带走热量,反而会让混输泵1泵体温度持续上升,进而影响混输泵1平稳运行。通过混输泵1的冷却结构,降低泵体温度,保证混输泵1平稳运行。
28.混输泵1的冷却结构已经混输泵1设置于泵撬,气液分离器5和补液罐9设置于补液撬,如图1中两个虚线框所示。撬房为保温瓦楞板房,配置气体检测装置、通风装置、加热采暖和视频监控装置。泵撬尺寸可为8000mm
×
3400mm
×
2950mm,补液撬尺寸可为7000mm
×
3000mm
×
2950mm。
再多了解一些
本文用于企业家、创业者技术爱好者查询,结果仅供参考。