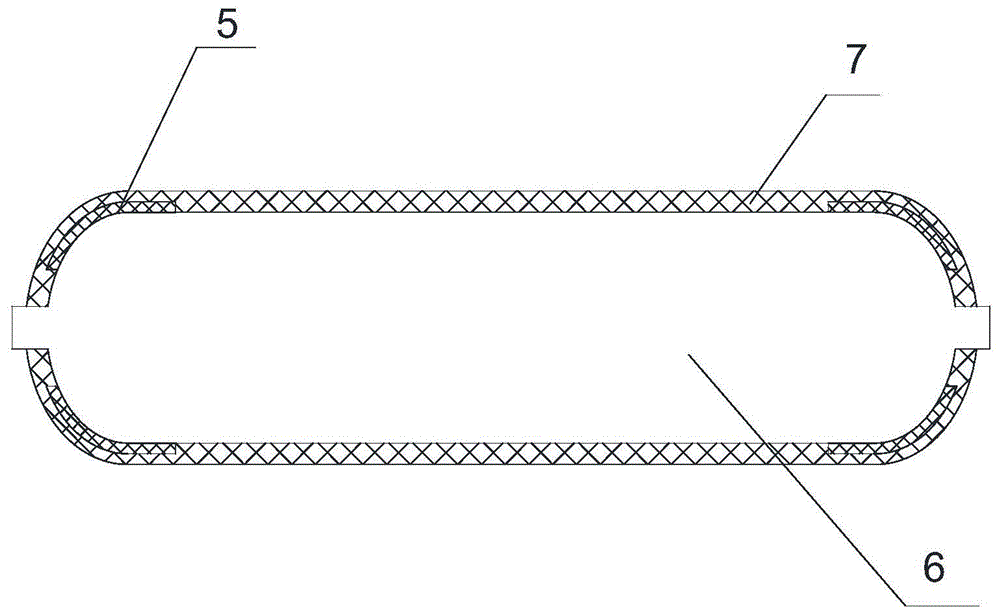
本实用新型涉及一种复合材料气瓶,属于复合材料成型技术领域。
背景技术:
复合材料气瓶在航空航天和新能源汽车领域内运用越来越广泛,主要作为储能设备使用。对于复合材料气瓶而言,保证其爆破压力和爆破模式是第一要素,这是气瓶安全性能的表征,爆破压力就是气瓶爆破时的最终压力,爆破模式就是气瓶爆破的位置,一般要求气瓶爆破在筒身位置,以保证气瓶爆破之后依然是一个整体,防止有高速飞溅物质对周围造成伤害。气瓶的强度通过纤维缠绕成型的外部复合材料层提供,一般该复合材料采用碳纤维制作而成,有两种缠绕方式,一种是环向缠绕,主要提供气瓶环向强度,一种是螺旋缠绕,主要提供气瓶在轴向的强度,同时也会承载少部分的环向载荷。
由于环向缠绕只能缠绕气瓶的直筒段,所以为了补强气瓶封头的强度采用螺旋缠绕方式,但在纤维连续全缠绕工艺下,需要对气瓶整体进行纤维螺旋缠绕,而爆破的压力主要取决于环向爆破压力,使得复合材料气瓶的直筒段的螺旋向纤维的利用效率低,往往需要缠绕较厚的纤维层,造成原材料的浪费,成本的升高。为了提升螺旋方向纤维发挥强度,国外采用机器人自动铺丝技术,且在干法缠绕工艺上实现,设备投资成本高,技术难度大、原材料成本高。
技术实现要素:
本实用新型目的在于克服现有技术不足,提供一种复合材料气瓶,在保证爆破安全的前提下增加封头的强度。
一种复合材料气瓶,包括内胆,复合材料气瓶整体缠绕纤维增强层,纤维增强层与内胆的封头之间设有封头补强件。封头补强件可以增强封头处的强度,使得气瓶在爆破时金属边缘处不发生破坏,破坏集中在筒身段,使得复合材料气瓶爆破数据稳定,安全性能稳定。
作为优选,封头补强件是由纤维以螺旋缠绕方式单独成型的,其形状与封头相适配并套在封头上。以螺旋缠绕方式缠绕封头补强件,增加了封头径向和环向的的强度。
作为优选,纤维增强层的缠绕方式为螺旋缠绕与环向缠绕交替。螺旋缠绕与环向缠绕交替,相较于单纯的螺旋缠绕方式,增加了气瓶内胆直筒段的径向强度,提高了纤维的利用效率。
作为优选,封头补强件由碳纤维或玻璃纤维制成,厚度为3mm至5mm。
作为优选,纤维增强层由碳纤维或玻璃纤维制成,厚度为27mm至32mm。
一种复合材料气瓶的制备方法,采用以下步骤实现:
步骤1,制作封头补强件,
s1.1铸造砂型模,砂型模的封头部分与内胆的封头部分尺寸一致,砂型模的直筒段长度小于内胆的直筒段长度;
s1.2,缠绕纤维,采用螺旋缠绕的方式将纤维缠绕到砂型模上;
s1.3,旋转固化,固化砂型模上的纤维层,优化固化制度,使固化时树脂不完全固化,依然具有环氧官能团供后续分层固化使用;
s1.4,裁切冲洗脱模,将固化后的制件沿垂直于砂型模主轴的方向裁切开,用高压水枪冲洗砂型模残留物,留下复合材料封头补强件。
步骤2,安装封头,将封头补强件套在气瓶内胆上,由于砂型模的封头与内胆的封头尺寸一致,可以完全匹配,对封头补强件的边缘部分进行倒角处理,用液态树脂填充空隙部分,确保封头补强件与内胆的封头完全贴合。
步骤3,缠绕纤维增强层,先对封头补强件边缘部分进行倒角处理,用液态树脂填充空隙部分,再对已经安装封头补强件的内胆外部缠绕纤维增强层。
步骤4,整体固化,将封头补强件与纤维增强层一同固化。
作为优选,步骤1铸造砂型模的步骤为:
s1.11,将铸造型砂与粘结剂混合,并进行充分搅拌,铸造型砂采用化学硬化砂,粘合剂采用合成树脂或水玻璃。化学硬化砂的强度高,铸型能够准确地反映模样的尺寸和轮廓形状,在以后的工艺中也不容易变形,制得的铸件尺寸精度较高,用水玻璃作粘结剂的化学硬化砂成本低、使用中工作环境无气味,用树脂作粘结剂的化学硬化砂成本较高,但浇注以后铸件易于和型砂分离,铸件清理的工作量减少,而且用过的大部分砂子可再生回收使用。
s1.12,塑成砂型模。
s1.13,加工螺纹,待砂型模形状固定后,采用车床,加工两端螺纹至与缠绕机的转接轴配合。
作为优选,步骤s1.2中的纤维以及步骤3中的纤维增强层采用碳纤维或玻璃纤维,步骤s1.2与步骤3使用的缠绕方法为湿法缠绕。碳纤维有优良的纤度和高拉力性能,还有耐高温、耐腐蚀等一系列优良性能,玻璃纤维价格便宜、拉伸强度高。
作为优选,步骤s1.2的螺旋缠绕的角度为30至50度,缠绕张力为单束纤维20n至35n,缠绕厚度为3mm至5mm。张力过小会使得纤维的强度偏低,容器的疲劳性能差,张力过大会使得纤维的磨损大,使制品强度下降,本实用新型采用的单束纤维20n至35n为适中、均匀的张力大小。
作为优选,步骤3的缠绕方式为螺旋缠绕和环向缠绕交替,缠绕厚度为27mm至32mm。
作为优选,步骤s1.3的固化温度为120℃±10℃,固化时间为2至3小时。由于封头补强件的缠绕厚度为3mm至5mm,用的树脂量少,可以不进行排泡处理,直接固化成型。
作为优选,步骤4固化制度为:(1)将温度升至80℃±5℃,对树脂进行排气泡处理,固化时间为4至6小时;(2)将温度升至120℃±10℃,进行分层固化。
有益效果:
1.在气瓶封头处增设封头补强件,增强了封头处的径向及环向的强度,使得气瓶在爆破时金属边缘处不发生破坏,破坏集中在筒身段,使得复合材料气瓶爆破数据稳定,安全性能稳定。
2.相较于传统的纤维连续全缠绕方式,采用先补强封头,再整体缠绕的方法,在保证爆破安全的前提下增强了气瓶封头的强度;利用螺旋缠绕和环向缠绕交替的缠绕方式整体缠绕,相较于单纯的螺旋全缠绕方式,提高了瓶身直筒段的径向强度,同时节省了纤维材料,避免了浪费、减少了成本;
3.采用分层固化工艺,降低了固化的温度,减小因放热导致的质量损害,增强了树脂的强度,同时减少了树脂的变形情况;
4.采用湿法缠绕的工艺,相较于干法缠绕工艺减少了预浸渍设备的投入,并且便于选材,更易实现;
5.采用旋转固化工艺,便于树脂流动,多余树脂沿样件边界留下,方便控制树脂含量,避免干法缠绕工艺中,树脂在线激光固化,降低了成本。
附图说明
图1为本实用新型的一个实施例中的复合材料气瓶结构示意图;
图2为本实用新型的一个实施例中的复合材料气瓶制备方法步骤s1.1示意图;
图3为本实用新型的一个实施例中的复合材料气瓶制备方法步骤s1.2示意图;
图4为本实用新型的一个实施例中的复合材料气瓶制备方法步骤s1.3示意图;
图5为本实用新型的一个实施例中的复合材料气瓶制备方法步骤s1.4示意图;
图6为本实用新型的一个实施例中的复合材料气瓶制备方法步骤2示意图;
图7为本实用新型的一个实施例中的复合材料气瓶制备方法步骤3示意图;
图8为本实用新型的一个实施例中的复合材料气瓶制备方法步骤4示意图;
附图标记:1砂型模、2碳纤维层、3缠绕机、4旋转固化、5封头补强件、6内胆、7纤维增强层。
具体实施方式
下面将结合本实用新型实施例中的附图,对本实用新型实施例中的技术方案进行清楚、完整地描述,显然,所描述的实施例仅仅是本实用新型一部分实施例,而不是全部的实施例。基于本实用新型中的实施例,本领域普通技术人员在没有做出创造性劳动前提下所获得的所有其他实施例,都属于本实用新型保护的范围。
如图1所示,为本实用新型提供的一种复合材料气瓶的结构示意图,一种复合材料气瓶,包括内胆6,复合材料气瓶整体缠绕纤维增强层7,纤维增强层7与内胆6的封头之间设有封头补强件5,封头补强件5是由纤维以螺旋缠绕方式单独成型的,其厚度为3mm至5mm,其形状与封头相适配并套在封头上。纤维增强层的缠绕方式为螺旋缠绕与环向缠绕交替,为h-z-h-z……h-z-h-z,也可以为h-h-h-h…z-z-z-z,其中z为螺旋缠绕,h为环向缠绕,缠绕的厚度为27mm至32mm。
结合图2至图8,为一种复合材料气瓶的制备方法示意图,本实用新型提供的复合材料气瓶的制备方法采用以下步骤实现:
如图2至图5所示,为步骤1的示意图。
步骤1,制作封头补强件,
s1.1铸造砂型模1:
s1.11将铸造型砂与粘结剂混合,并进行充分搅拌,铸造型砂优选采用化学硬化砂,粘合剂优选采用合成树脂或水玻璃,化学硬化砂的强度高,铸型能够准确地反映模样的尺寸和轮廓形状,在以后的工艺中也不容易变形,制得的铸件尺寸精度较高。
s1.12,塑成砂型模1,砂型模1的封头部分与内胆6尺寸一致,使得制造的封头补强件能够与内胆6的封头匹配,砂型模1的直筒段长度小于内胆6直筒段长度,避免浪费;粘合剂在硬化剂的作用下发生化学反应而导致砂型模自行硬化。
s1.13,加工螺纹,待砂型模形状固定后,采用车床加工两端螺纹至与缠绕机的转接轴配合,方便将砂型模连接到缠绕机3上。
s1.2,缠绕纤维,将砂型模1固定在缠绕机3的主轴上,采用螺旋缠绕的方式将纤维缠绕到砂型模1上,纤维采用碳纤维或玻璃纤维,缠绕角度为30度至50度,缠绕张力为单束纤维20n至35n,缠绕厚度为3mm至5mm。本实施例优选采用t300碳纤维,缠绕角度为30°,缠绕张力为单束纤维20n,缠绕成厚度为3mm的碳纤维层2,张力过小会使得纤维的强度偏低,容器的疲劳性能差,张力过大会使得纤维的磨损大,使制品强度下降,本实施例采用的单束纤维20n为适中、均匀的张力大小。
s1.3,旋转固化4,固化砂型模上的碳纤维层2,固化温度为120℃±10℃,固化时间为2至3小时。由于制作封头补强件的碳纤维层较为薄,树脂用量不大,可以直接固化,省略排泡过程,但需保证固化过程中树脂不完全固化,依然具有环氧官能团供后续分层固化使用。
s1.4,裁切冲洗脱模,将固化后的制件沿垂直于砂型模主轴的方向裁切开,保证切口平直,切开部分为左右两个完整、对称的封头补强件5。用高压水枪冲洗砂型模具,将全部砂型模残留物冲洗干净,留下复合材料封头补强件5,调节高压水枪的压力,可以在冲洗掉砂型模残留物的前提下不伤害复合材料的树脂层。
如图6所示,为步骤2的示意图。
步骤2,安装封头,将封头补强件5清理干净,套在气瓶内胆6上,由于砂型模1的封头部分与内胆6的尺寸一致,可以保证顺利安装,如果在安装的过程中封头补强件5与内胆6有间隙,可以采用橡胶锤轻轻敲击封头补强件5,直至与内胆6完全贴合。
如图7所示,为步骤3的示意图。
步骤3,缠绕纤维增强层7,先对封头补强件边缘部分进行倒角处理,用液态树脂填充空隙部分,以减小湿法缠绕的纤维与封头补强件之间的间隙,再对已经安装封头补强件的内胆外部缠绕纤维增强层7,纤维增强层7采用碳纤维或玻璃纤维,本实施例优选采用t300碳纤维,缠绕方法为螺旋缠绕和环向缠绕交替,为h-z-h-z……h-z-h-z,也可以为h-h-h-h…z-z-z-z,其中z为螺旋缠绕,h为环向缠绕,螺旋缠绕角度为30度至50度,环向缠绕角度为90度,缠绕厚度为27mm至32mm,本实施例优选h-z-h-z……h-z-h-z的缠绕方式,螺旋缠绕角度30度,环向缠绕角度90度,缠绕厚度30mm。
如图8所示,为步骤4的示意图。
步骤4,整体固化,将封头补强件5与纤维增强层7一同固化,首先将温度升至80℃±5℃,对树脂进行排气泡处理,合成树脂粘度较高,粘结面容易进气体,影响粘结质量,操作时需要将树脂层压实,排除气泡和裂隙,方便与后续的方法中的树脂进行粘结,4至6小时后再将温度升至120℃±10℃,进行分层固化,必要时可以增加粘结剂来提高树脂层之间润湿性,使得分层固化后的树脂强度更高,固化完成后复合材料气瓶即制备完成。
对本实用新型的复合材料气瓶进行室温爆破试验,室内爆破压力为190mpa,大大提高了复合材料气瓶的安全性。
本实用新型工艺简单,易实现,先对封头进行补强后,再对复合材料气瓶进行统一缠绕纤维,增强气瓶封头的强度的同时减少了材料的浪费,同时避免了干法缠绕工艺将原材料加工成预浸料,使用湿法缠绕工艺即可实现,降低了成本;采用直接缠绕工艺制样,避免了采用机器人自动铺丝技术,解决了设备高投资、技术高难度、材料高成本的问题。
最后应说明的是:以上所述仅为本实用新型的优选实施例而已,并不用于限制本实用新型,尽管参照前述实施例对本实用新型进行了详细的说明,对于本领域的技术人员来说,其依然可以对前述各实施例所记载的技术方案进行修改,或者对其中部分技术特征进行等同替换。凡在本实用新型的精神和原则之内,所作的任何修改、等同替换、改进等,均应包含在本实用新型的保护范围之内。
本文用于企业家、创业者技术爱好者查询,结果仅供参考。