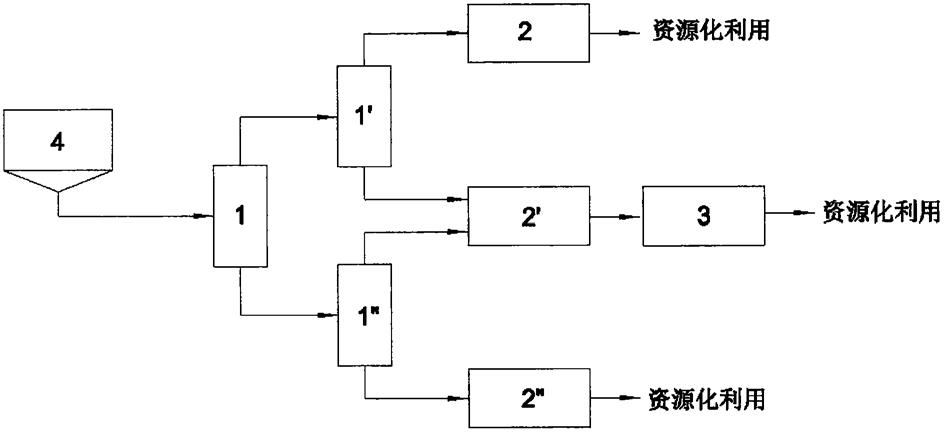
1.本发明属于煤气化领域,尤其是涉及一种气流床气化炉气化细灰分级脱水脱碳及综合利用工艺。
背景技术:
2.气流床气化炉包括水煤浆气流床气化技术和干煤粉气流床气化技术两种,特点是气化温度高,气化温度超过煤的流动温度。煤颗粒在气化炉中的停留时间是不同的,停留时间较长的,气化反应比较完全,以熔融态形式排出气化炉。停留时间较短的煤颗粒,由于气化反应不完全,煤颗粒没有完全熔融,以细灰形式排出气化炉。
3.气化细灰主要有三种成分:未反应的碳、熔融渣、未熔融的灰。气化细灰是三种物质的混合物,有以下特点:
4.1.空隙发达,吸水能力强。气化细灰的比表面积介于50~300m3/g,测试结果表明碳含量越高比表面积越大,碳的孔隙率更高。由于气化细灰的空隙比较发达,经过水洗后的气化细灰,水分进入细灰孔道,由于受到孔道作用力的影响,水分很难被脱除,所以一般的机械手段,如挤压、离心、吸附等很难降低气化细灰的水含量,给气化细灰的综合利用带来了难度。
5.2.挥发分低,着火温度高。由于气化细灰经过了较高的气化温度,含有的挥发分几乎全部析出,细灰的主要可燃物成份为碳,与煤炭相比,着火温度提高了200℃左右,达到了600~700℃,所以气化细灰与煤炭掺混燃烧后,两者有着不同的着火温度,同样的燃烧条件,不能同时起燃。
6.3.燃尽指数低,更难燃尽。与煤炭相比,气化细灰的燃尽指数低,燃烧同样质量的煤炭和同样质量的气化细灰,气化细灰所需的时间明显较长,因此,以煤炭为原料设计的锅炉,在确定的燃烧时间条件下,气化细灰无法燃尽。
7.4.平均粒径小,很难捕捉分离。干煤粉气化技术产生的气化细灰平均粒径为200~300微米,水煤浆气化技术产生的气化细灰平均粒径为300~500微米,而锅炉煤的平均粒径为5000~20000微米,气化细灰的粒径与锅炉煤的粒径存在数量级的差异,循环流化床锅炉设计的旋风分离器按照锅炉煤设计,无法分离粒度更细的气化细灰。
8.5、灰、渣、碳比重不同,碳比重最小,渣比重最大,灰介于中间,气化细灰作为灰、渣、碳的混合物,基于比重的不同,在旋流器的离心作用下,可实现碳与灰渣的分离。
9.截至2020年底,我国气流床气化炉产生的灰渣量约为1亿吨,其中气化细灰的量约为6000万吨,主要处理方法有以下几种:
10.1、渣场填埋。填埋方式的处理量约占气化细灰总量的90%以上。气化细灰现有的脱水设备大多采用真空带式过滤机,脱水后的气化细灰含水率仍然高达50
‑
60%,在装车、运输、倾倒渣场整个过程中,均有水分溢出,造成环境污染。由于水分高,气化细灰往往以类似泥汤的形式存在,给渣场填埋夯实和防水处理造成严重困扰。由于气化细灰中的碳含量和水含量都很高,又造成水资源和能量浪费。
11.2、掺烧锅炉。掺烧锅炉方式的处理量约占气化细灰量的5%。部分企业由于没有可填埋的渣场,不得不采用了掺烧锅炉的方式处理,主要通过浆体泵将初步脱水后含水率60
‑
70%的气化细灰以浆体形式打入锅炉中。这种方法处理气化细灰主要存在的问题是:浆体打入锅炉后,水迅速气化成蒸汽,与烟气混合后,整个气体混合物的体积增加,气体流速增加,造成锅炉内件严重冲刷磨蚀。实际运行过程中,企业不得不以减少加入量、降低锅炉负荷的方式操作,从而影响了锅炉效率,增加了运行成本。这种处理方式实际上有很少的气化细灰通过锅炉实现燃烧脱碳,仅仅是通过吸收锅炉热量,进行了水分的脱除,由于掺烧量不大,经过脱水后的气化细灰与锅炉的粉煤灰混合在一起,实现了总体碳含量的降低。
12.3、做建筑材料。部分企业将气化细灰经过晾晒脱水后,掺入水泥原料、混凝土、硅酸盐建筑制品等材料中。由于气化细灰的含碳量过高(15
‑
45%),按照国家和行业标准,气化细灰的含碳量大大超过了以上材料对碳含量的要求(水泥活性混合材料含碳量要求≤8%、混凝土含碳量要求≤10%、硅酸盐建筑材料含碳量要求≤10%),严重影响了产品质量。因此,气化细灰作为建筑材料使用应进行脱碳处理。
13.综合所述,现有技术瓶颈主要存在以下方面:(1)气化细灰发达的空隙结构造成水分难以脱除,增加了气化细灰资源化利用的难度;(2)气化细灰具有颗粒粒径小、挥发分低、燃尽指数低等特点,现有燃煤锅炉技术无法实现深度脱碳,脱碳燃烧技术亟待突破;(3)部分气化技术产生的气化细灰碳含量低于25%,高于10%,既不能直接做建筑材料,热值又低,资源化利用气化细灰不具有经济性,需要开发碳和灰分的分离技术;(4)没有系统性将分碳、脱水干化、脱碳技术进行耦合,形成系统化解决气化细灰资源化利用的瓶颈问题。
技术实现要素:
14.本发明的目的是提供气流床气化炉气化细灰综合处理利用工艺,包括分碳、脱水、脱碳工艺及其组合,本发明的工艺极大地提高了气化细灰资源化利用效率,打破了气化细灰的资源化利用技术瓶颈,减少了固体废物排放,提高了煤炭资源的利用率。
15.本发明的技术方案包括一种气流床气化炉气化细灰脱碳工艺,其中:
16.脱碳设备包括脱碳炉、旋风分离器、返料器、气化细灰仓、原煤仓,所述脱碳炉及返料器底部设有空气入口,原煤仓出料口与脱碳炉下部连接,返料器物料出口连接脱碳炉下部,脱碳炉物料出口连接旋风分离器,旋风分离器出料口与返料器中部连接,旋风分离器顶部设热烟气出口,气化细灰仓出料口与返料器顶部连接;
17.具体步骤为:气化黑水沉降槽中的高含水灰浆经处理后制得含水量为20%~35%、含碳量为30%~60%(干基)的气化细灰;脱碳炉启动阶段,先用原煤仓的原料煤启动,待炉况稳定后,由返料器顶部加入气化细灰,同时减少加入的煤量,混合后的高温热物料以及空气经返料器加入脱碳炉下部,经高温脱碳,热物料由脱碳炉顶部进入旋风分离器进一步分离,高温烟气由旋风分离器顶部排出;原煤与气化细灰的掺混后热值≥1800kcal/kg;
18.本发明所述的碳含量为干基碳含量。
19.所述脱碳炉的循环倍率为10~40倍,脱碳炉下段温度为850℃~1035℃,中段温度为900℃~1100℃,上段温度为925℃~980℃,脱碳炉内物料流速为1.5~2.5m/s,压力差为5~20kpa;返料器内温度为800℃~950℃;得到的脱碳产品含水0%、含碳≤5%。
20.所述气化黑水沉降槽中的高含水灰浆的处理方法包括将高含水灰浆经一级或多级分碳步骤得到两股或多股不同含碳量的分碳物料。
21.所述气化黑水沉降槽中的高含水灰浆的处理方法进一步包括将所述一级或多级分碳得到的多股物料经板框式压滤机进行初步脱水。
22.优选的所述灰浆分碳为二级分碳,具体步骤为:
23.将沉降槽底部的灰浆加入一级旋流分离器,将灰浆分离成含碳量较高的溢流部分和含碳量较低的底流部分,其中,沉降槽底部的灰浆含水75%~95%、含碳15%~45%,溢流部分含水75%~95%、含碳50%~80%,底流部分含水75%~95%、含碳5%~50%;
24.将溢流部分加入二级旋流分离器i进一步分碳,得到高碳部分和富碳部分,其中,高碳部分含水75%~95%、含碳≥80%,富碳部分含水75%~95%、含碳30%~60%;
25.将底流部分加入二级旋流分离器ii进一步分碳,得到富碳部分和低碳部分,其中富碳部分含水75%~95%、含碳30%~60%,低碳部分含水75%~95%、含碳≤10%。
26.包括进一步的脱水步骤:
27.将所述高碳部分、富碳部分、低碳部分分别在板框压滤机内进行脱水处理,高碳部分脱水产品含水5%~35%、含碳≥80%,富碳部分脱水产品含水20%~35%、含碳30%~60%,低碳部分脱水产品含水5%~35%、含碳≤10%。
28.所述富碳部分的脱水步骤为:利用泵压将物料通过滤布排出,直至物料充满滤室;通过高压水产生的压榨力,使滤饼压密,将残留在颗粒中间的滤液挤出,降低滤饼水分;利用压缩空气强气流吹扫30s~10min进行穿流置换,进一步降低滤饼中的水分。
29.优选的所述气流吹扫时间为2min~3min。
30.所述高碳部分和低碳部分的脱水步骤为:利用泵压将物料通过滤布排出,直至物料充满滤室;通过高压水产生的压榨力,使滤饼压密,将残留在颗粒中间的滤液挤出,降低滤饼水分;在滤板中通入热水,加热腔室内的滤饼,同时开启真空泵对滤饼腔室抽真空,使其内部形成负压,降低水的沸点,滤饼中的水分沸腾汽化,蒸汽排出。
31.所述高碳部分脱水产品用于活性炭制备,富碳部分脱水产品在脱碳过程中副产蒸汽,低碳部分脱水产品用于建工建材。
32.气流床气化炉气化黑水经沉降槽沉降后形成的灰浆含水75%~95%、含碳15%~45%,其含水含碳量高,无法作为建材原料,如果其中的碳也不加以利用,那将会造成巨大的资源浪费。气流床气化炉气化细灰资源化利用一方面是分离其中的碳,用于制备高附加值的活性炭等产品,另一方面是取得碳分离后的低碳产品,这种低碳产品可用于建筑材料等领域。本发明将介于高碳产品和低碳产品之间的富碳产品分流出来,利用其存在的可回收价值的热值,作为燃料,经脱碳炉脱碳后,还可再次产生低碳产品,用于建筑材料等领域。本发明的工艺将气化细灰经过分碳工艺处理,形成不同碳含量的产品,实现资源利用的最大化,具有重要的环境及经济意义。
33.本发明的技术方案是气流床气化炉气化细灰综合处理工艺,为了达到最大化资源有效利用,具体地,本发明的技术方案设置了分碳、脱水、脱碳步骤。
34.首先优选采用二次分碳方法,把灰浆分流成高碳、富碳、低碳部分,并且合理控制各部分的含水含碳量,使得后续即可得到理想比例的高附加值的活性炭等产品,也可得到理想比例的大宗工业建材原料,同时,分流出来的富碳部分还适合经过脱碳步骤副产蒸汽,
进一步扩大了资源利用率。
35.在脱水步骤中,富碳部分优选采用高压水隔膜压榨和强气流吹扫方法实现脱水。高压灰浆泵将气化灰浆打入压滤腔中,滤液经过滤布滤出,夹在滤板中的气化细灰经过高压隔膜压榨,进一步降低水分,最后通入强气流吹扫,该脱水方法通过对强气流吹扫时间的控制,可将气化细灰水分控制在20~35%。该水份范围的气化细灰,呈现滤饼状,无水分粘结,易于储存和输送。同时,保留一定的水分,气化细灰不会造成扬尘。此脱水方法在保证顺利输送至脱碳设备的前提下降低了脱水工艺成本。
36.高碳部分、低碳部分采用高压水隔膜压榨和真空加热方法脱水。该方法减去了强气流吹扫工艺,增加了滤板的加热功能和抽真空工艺。抽真空的目的是为了降低水的蒸发温度,滤板加热可不断补充热量,从而实现水分的持续蒸发脱除。通过控制真空加热的时间,可实现高碳产品和低碳产品的水分控制到20%以下,对产品水分有特殊要求的,可将水分控制在5%以内。
37.本发明的脱碳工艺针对的是分碳步骤分流得到的富碳产品的脱水产物,脱碳原料是含水量为20%~35%、含碳量为30%~60%的气化细灰产品。返料器中,气化细灰由顶部加入、旋风分离器物料从侧方中部加入、空气由底部加入、混合后的热物料从侧方中部排出。在脱碳炉的循环倍率为10~40倍的工况下,本发明的返料器物料进出方式不仅可以起到提前预热气化细灰的目的,还有利于物料的充分混合,保证气化细灰进入脱碳炉可以快速启燃。本发明优化了脱碳炉轴向温度分配,为确保气化细灰在炉内有足够的停留时间,炉内物料流速比普通锅炉气速降低30~50%、压力差控制在5~20kpa,上述各工艺条件的配合保证了脱碳的高效进行,得到的脱碳产品含水0%、含碳≤5%。此外,旋风分离器设计为可以分离300~500微米粒径的气化细灰,相比常规锅炉匹配的旋风分离效率更高。
38.本发明将分碳技术、脱水技术、脱碳技术有机结合,通过分碳步骤的分级和控制,将分碳产品按合理的比例进一步精细划分,进一步结合脱水和脱碳工艺,极大地提高了气化细灰资源化利用效率,打破了气化细灰的资源化利用技术瓶颈,提高了资源利用率。
附图说明
39.图1是本发明的气流床气化炉气化细灰综合处理利用工艺示意图
40.图2是脱碳设备示意图
41.图中:
42.1.一级旋流分离器,
[0043]1’
.二级旋流分离器i,
[0044]
1”.二级旋流分离器ii,
[0045]
2.真空干化板框压滤机,
[0046]2’
.吹气穿孔板框压滤机,
[0047]
2”.真空干化板框压滤机,
[0048]
3.脱碳设备,
[0049]
31.脱碳炉
[0050]
32.旋风分离器
[0051]
33.返料器
[0052]
34.气化细灰仓
[0053]
35.原煤仓
[0054]
4.沉降槽。
具体实施方式
[0055]
以下以实施例进一步说明本发明。
[0056]
本实施例的脱碳工艺:
[0057]
先用原煤仓35的原料煤启动,待炉况稳定后,由返料器33顶部加入富碳部分脱水得到的含水25%、含碳55%的气化细灰,同时减少加入的煤量,混合后的高温热物料以及空气从返料器33中部加入脱碳炉31下部,原煤与气化细灰的掺混后热值为1800kcal/kg;在脱碳炉31底部的空气作用下以15倍的循环倍率在炉膛内反应,脱碳后的物料由脱碳炉31顶部进入旋风分离器32进一步分离,高温烟气由旋风分离器32顶部排出,经换热器副产蒸汽。脱碳炉31轴向温度由下向上测定为855℃、1081℃、1089℃、970℃、961℃、928℃。脱碳炉31内物料流速为1.5m/s,压力差为7.6kpa,返料器33内温度为860℃。得到的脱碳产品含水0%、含碳3.6%;
[0058]
脱碳步骤的原料由以下分碳、脱水方法得到:
[0059]
将沉降槽4中含水87%、含碳35%的灰浆加入一级旋流分离器1,将灰浆分离成含碳量较高的溢流部分和含碳量较低的底流部分,溢流部分含水87%、含碳78%,底流部分含水87%、含碳43%;
[0060]
将溢流部分加入二级旋流分离器i 1’进一步分碳,得到高碳部分和富碳部分,其中,高碳部分含水87%、含碳90%,富碳部分含水87%、含碳55%;
[0061]
将底流部分加入二级旋流分离器ii 1”进一步分碳,得到富碳部分和低碳部分,其中富碳部分含水87%、含碳90%,低碳部分含水87%、含碳7%;
[0062]
将上述高碳部分、富碳部分、低碳部分分别在板框压滤机中通过进行干燥脱水。
[0063]
高碳部分和低碳部分采用真空干化板框压滤机2、真空干化板框压滤机2”脱水。真空干化板框压滤机设有若干间隔设置的加热板和隔膜板,所述加热板和隔膜板之间留为物料截留区,所述隔膜板与物料截留区相接的侧面上设有可膨胀的隔膜,向隔膜板的隔膜腔内注入高压水,使隔膜膨胀并挤压滤饼,受挤压的滤饼进一步脱水,再向加热板内腔充入循环热水对滤饼加热,同时开启真空泵对滤饼腔室抽真空,使其内部形成负压,降低水的沸点,滤饼中的水分沸腾汽化。分别得到含水25%、含碳92%的脱水产品用于制备高附加值活性炭产品,以及含水25%、含碳7%的脱水产品用作建工建材。
[0064]
富碳部分采用吹气穿孔板框压滤机2’脱水,先用泵压将富碳部分通过滤布排出,直至物料充满滤室;再通过高压水产生的压榨力,使滤饼压密,将残留在颗粒中间的滤液挤出,降低滤饼水分;利用压缩空气强气流吹扫2min进行穿流置换,进一步降低滤饼中的水分,得到含水25%、含碳55%的脱水产品,用于进一步脱碳副产蒸汽。
[0065]
虽然以上描述了本发明的优选实施方案,但是本领域的技术人员应当理解,这仅是举例说明,本发明的保护范围是由所附权利要求书限定的。本领域的技术人员在不背离本发明的原理和实质的前提下,可以对这些实施方案做出多种变更或修改,但这些变更和修改均落入本发明的保护范围。
再多了解一些
本文用于企业家、创业者技术爱好者查询,结果仅供参考。