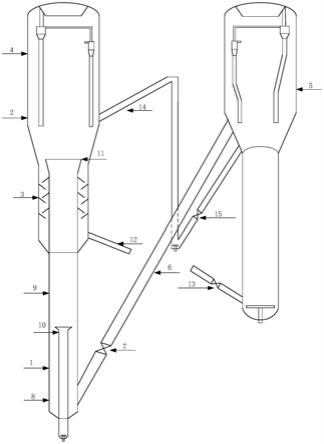
1.本发明涉及石油化工领域,具体地,涉及一种加氢生成油催化裂解的方法。
背景技术:
2.丙烯是重要的有机化工原料,随着世界经济的发展,对丙烯的需求也越来越高。从2006年至2016年,丙烯的产量与消费量逐年增加,且一直呈现供不应求的态势。预计到2020年,中国的丙烯需求量将达到4000万吨,年均增长率约为4.7%。从重质原料通过催化裂化等炼油装置生产低碳烯烃、芳烃等化工原料,是解决我国轻质原料油不足的问题的合理技术路径,而传统的催化加氢和催化裂化组合工艺一般是为了提高燃料油的产量、改善催化裂化的产品分布和产品质量。
3.专利us4619757公开了一种两段加氢处理从重质馏分油生产烯烃的方法。该方法包括一个加氢处理过程和一个热裂化过程,加氢处理过程分两段进行,第一段是选择性脱除多环芳烃,第二段是加氢脱硫和加氢脱氮。第一段过程采用含有沸石的加氢处理催化剂处理多环芳烃含量高的原料,第二段采用不含有沸石的加氢处理催化剂处理多环芳烃含量低的原料。该方法氢耗低,但烯烃收率不高。
4.专利cn1119397c公开了一种渣油加氢处理-催化裂化组合工艺方法,该方法中,渣油和澄清油一起进入加氢处理装置,在氢气和加氢催化剂存在下进行加氢反应;反应所得的加氢渣油进入催化裂化装置,在裂化催化剂存在下进行裂化反应,重循环油在催化裂化装置内部进行循环;反应所得的油浆经分离器分离得到澄清油,返回至加氢装置。此方法使催化裂化油浆转化为轻质油品,提高了汽油和柴油的收率,降低了重油的收率,但此方法产生的丙烯产率较低。
5.专利cn109704903a公开了一种多产丙烯和轻芳烃的方法,该方法包括,在第一提升管反应器中,重质烃油与裂化催化剂接触反应,得到积炭催化剂和第一油气产物;在流化床反应器中,加氢处理轻油与裂化催化剂接触反应,得到第二油气产物和积炭催化剂;在第二提升管反应器中,c4烯烃与再生裂化催化剂和来自所述流化床反应器的积炭催化剂接触反应,得到积炭催化剂和第三油气产物。该方法同时提高了丙烯和轻芳烃的产率。
6.专利cn109666506a公开了一种非加氢处理油和加氢处理油共同加工的方法。该方法包括,先将非加氢生成油从提升管反应器底部的重质油喷嘴喷入提升管反应器发生催化裂解反应,得到第一反应产物和半待生催化剂;将加氢生成油从重质油喷嘴的上方喷入到提升管反应器中与第一反应产物和半待生催化剂接触并进行第二催化裂解反应。该方法将加氢生成油和非加氢生成油进行分层进料,并可以调节反应系统的氢转移活性,提高低碳烯烃产率。
技术实现要素:
7.本发明的目的是提供一种加氢生成油催化裂解的方法,该方法可以提高产物中丙烯产率并降低干气含量。
8.为了实现上述目的,本发明提供一种加氢生成油催化裂解的方法,该方法包括:
9.(1)将重质油从提升管反应器底部的重油喷嘴喷入提升管反应器中与来自提升管反应器底部的催化裂解催化剂接触进行第一催化裂解反应,得到第一产物和第一积炭催化剂;
10.(2)将加氢生成油和富氢气体从所述提升管反应器下部的长管进料喷嘴喷入所述提升管反应器中,并与所述第一产物和所述第一积炭催化剂接触进行第二催化裂解反应,得到第二积炭催化剂和含有丙烯的第二产物;
11.其中,以所述催化裂解催化剂的总重量为基准,所述第一积炭催化剂的积炭量为0.1-0.5重量%;所述长管进料喷嘴位于所述重油喷嘴的下游。
12.以所述催化裂解催化剂的总重量为基准,所述第一积炭催化剂的积炭量为0.15-0.35重量%。
13.可选地,步骤(1)中,所述第一催化裂解反应的条件包括:所述重质油的停留时间为0.1-3秒,所述重油喷嘴处的温度为600-700℃,压力为 0.15-0.4mpa。
14.可选地,所述催化裂解催化剂与所述重质油用量的重量比为30-300。
15.可选地,所述重质油选自常压渣油、减压渣油、油浆和回炼油中的一种或多种。
16.可选地,步骤(2)中,所述第二催化裂解反应的条件包括:所述提升管反应器的出口温度为540-580℃,所述加氢生成油的停留时间为0.5-2.0秒,压力为0.15-0.4mpa。
17.可选地,所述富氢气体与所述加氢生成油的重量比为0.00005-0.20。
18.可选地,所述加氢生成油的进料温度为80-200℃。
19.可选地,所述富氢气体为氢气或干气。
20.可选地,该方法还包括:将所述第二产物和所述第二积炭催化剂送入所述提升管反应器上部的流化床反应器中,使所述第二产物与补充再生剂和所述第二积炭催化剂接触进行第三催化裂解反应。
21.可选地,所述第三催化裂解反应的温度为500-650℃,重时空速为2-20 小时-1
,压力为0.15-0.4mpa。
22.可选地,所述补充再生剂占所述提升管反应器中催化剂循环量的10-30 重量%。
23.可选地,以干基计并以所述催化裂解催化剂的总重量为基准,所述催化裂解催化剂含有1-60重量%的沸石混合物、5-99重量%的耐热无机氧化物和 0-70重量%的粘土,其中,以所述沸石混合物的总重量为基准,所述沸石混合物含有1-90重量%的改性β沸石和10-99重量%的具有mfi结构的沸石。
24.可选地,以干基计并以所述催化裂解催化剂的总重量为基准,所述催化裂解催化剂含有1-50重量%的沸石混合物、10-70重量%的耐热无机氧化物和0-60重量%的粘土。
25.通过上述技术方案,本发明的方法采用具有特定积炭量的催化裂解催化剂,并在临氢条件下使加氢生成油进行催化裂解反应,可以有效地抑制脱氢反应,在多产丙烯的同时还能够降低干气的产率。
26.本发明的其他特征和优点将在随后的具体实施方式部分予以详细说明。
附图说明
27.附图是用来提供对本发明的进一步理解,并且构成说明书的一部分,与下面的具
体实施方式一起用于解释本发明,但并不构成对本发明的限制。在附图中:
28.图1是本发明的方法所采用的催化裂解系统的一种具体实施方式的结构示意图。
29.附图标记说明
30.1提升管反应器
ꢀꢀꢀꢀꢀ
2流化床反应器
ꢀꢀꢀꢀꢀꢀꢀ
3汽提器
31.4沉降器
ꢀꢀꢀꢀꢀꢀꢀꢀꢀꢀꢀ
5再生器
ꢀꢀꢀꢀꢀꢀꢀꢀꢀꢀꢀꢀꢀ
6再生剂输送管
32.7流量控制阀
ꢀꢀꢀꢀꢀꢀꢀ
8重油喷嘴
ꢀꢀꢀꢀꢀꢀꢀꢀꢀꢀꢀ
9稀释蒸汽喷嘴
33.10长管进料喷嘴
ꢀꢀꢀꢀ
11出口分布器
ꢀꢀꢀꢀꢀꢀꢀꢀ
12待生剂输送管
34.13流量控制阀
ꢀꢀꢀꢀꢀꢀ
14补充再生剂输送管
ꢀꢀ
15流量控制阀
具体实施方式
35.以下结合附图对本发明的具体实施方式进行详细说明。应当理解的是,此处所描述的具体实施方式仅用于说明和解释本发明,并不用于限制本发明。
36.本发明提供一种加氢生成油催化裂解的方法,该方法包括:
37.(1)将重质油从提升管反应器底部的重油喷嘴喷入提升管反应器中与来自提升管反应器底部的催化裂解催化剂接触进行第一催化裂解反应,得到第一产物和第一积炭催化剂;
38.(2)将加氢生成油和富氢气体从提升管反应器下部的长管进料喷嘴喷入提升管反应器中,并与第一产物和第一积炭催化剂接触进行第二催化裂解反应,得到第二积炭催化剂和含有丙烯的第二产物;
39.其中,以催化裂解催化剂的总重量为基准,第一积炭催化剂的积炭量为 0.1-0.5重量%;长管进料喷嘴位于重油喷嘴的下游。
40.其中,长管进料喷嘴位于重油喷嘴的下游是指,重油喷嘴和长管进料喷嘴沿提升管内油气流动方向依次设置,长管进料喷嘴位于重油喷嘴的上方。
41.本发明的发明人经实验研究发现,由于加氢生成油具有特殊的性质,在与强酸性催化剂接触发生催化裂解反应时,易发生脱氢反应和氢转移反应,会使丙烯的产率偏低,同时会生成大量的干气。基于上述问题,本发明的方法使加氢生成油与具有特定积炭量的积炭催化剂接触进行催化裂解反应,可以有效地降低加氢生成油转化过程中的氢转移反应;并且在临氢条件下进行第二催化裂解反应,能够显著降低加氢生成油转化过程中的脱氢反应,在多产丙烯的同时有效地降低干气产率,延长催化剂的使用寿命。
42.根据本发明,以催化裂解催化剂的总重量为基准,第一积炭催化剂的积炭量可以为0.1-0.5重量%,优选为0.15-0.35重量%。第一积炭催化剂的积炭量在上述范围内时,第一积炭催化剂可以更有效地降低加氢生成油转化过程中的氢转移反应,进一步提高产物中丙烯的产率。第一积炭催化剂的积炭量可以根据ripp 107-90方法,采用热重分析的方法测得。
43.根据本发明,步骤(1)中,重质油的停留时间和第一催化裂解的反应温度可以在较大的范围内变化,在一种具体实施方式中,第一催化裂解反应的条件包括:重质油的停留时间为0.1-3秒,重油喷嘴处的温度为600-700℃,压力为0.15-0.4mpa。优选地,重质油的停留时间为0.1-1.5秒,重油喷嘴处的温度为650-680℃,压力为0.18-0.35mpa。其中,重质油的停留时间是指重质油从重油喷嘴喷入提升管反应器到长管进料喷嘴出口处的时间。
44.根据本发明,在一种具体实施方式中,催化裂解催化剂与重质油用量的重量比可以为30-300,优选为60-200,以使第一积炭催化剂的积炭量在合适的范围内。
45.根据本发明,重质油为本领域的技术人员所熟知的,例如可以为选自常压渣油、减压渣油、油浆和回炼油中的一种或多种。
46.根据本发明,催化裂解反应的条件会对产物产生较为重要的影响。步骤 (2)中,第二催化裂解反应的条件包括:提升管反应器的出口温度可以为 540-580℃,加氢生成油的停留时间可以为0.5-2.0秒,压力可以为0.15-0.4mpa;优选地,提升管反应器的出口温度可以为550-570℃,加氢生成油的停留时间可以为1.2-1.8秒,压力可以为0.18-0.35mpa。其中,压力是指绝对压力,后文中压力的意义相同;加氢生成油的停留时间是指加氢生成油从长管进料喷嘴喷入提升管反应器开始至提升管反应器出口处的时间。在上述条件下,有利于进一步提高催化裂解反应中丙烯的产率,降低干气的产率。
47.根据本发明,富氢气体的用量对脱氢反应的反应过程具有一定的影响,为了进一步减少加氢生成油转化过程中的脱氢反应,富氢气体与加氢生成油的重量比可以为0.00005-0.20,优选为0.0001-0.1。在上述条件,富氢气体与加氢生成油的比例适宜,可以有效地减小脱氢反应,从而有效地进一步降低干气的产率。
48.根据本发明,第一积炭催化剂可以全部参与步骤(2)中的第二催化裂解反应。
49.根据本发明,加氢生成油的进料温度可以为80-200℃,优选为 100-150℃。
50.根据本发明,富氢气体可以为氢气或干气,优选为干气。
51.根据本发明,该方法还可以包括:将第二产物和第二积炭催化剂送入提升管反应器上部的流化床反应器中,使第二产物与补充再生剂和第二积炭催化剂接触进行第三催化裂解反应,以进一步提高丙烯的产率。其中,流化床为本领域的技术人员所熟知,例如可以为密相流化床反应器,其他种类的流化床反应器在此不再赘述。
52.根据本发明,在一种具体实施方式中,离开提升管反应器的第二产物和第二积炭催化剂从流化床反应器的底部引入流化床反应器中,反应后的补充再生剂和第二积炭催化剂也从流化床反应器的底部引出,第三催化裂解反应的反应产物从流化床反应器的顶部引出后送入沉降器,在沉降器中分离出其中夹带的催化剂后引入分馏系统;分离出的催化剂引入汽提器,汽提出吸附的烃类物质后引入再生器进行再生,得到再生催化裂解催化剂。
53.在一种具体实施方式中,再生催化裂解催化剂中的一部分作为补充再生剂,由与流化床流体连通的补充再生剂输送管送入流化床,另一部分作为步骤(1)中的催化裂解催化剂,由与提升管反应器流体连通的再生剂输送管送入提升管反应器底部。其中,补充再生剂输送管内的提升气可以为本领域的技术人员所熟知的,例如可以为水蒸气、干气和碳四馏分中的一种或几种,优选碳四馏分。
54.根据本发明,补充再生剂可以占提升管反应器中催化剂循环量的10-30 重量%,优选为15-25重量%,以进一步提高丙烯的产率。其中,催化剂循环量是指首次随重质油进入提升管反应器中的新鲜催化裂解催化剂的量,这些新鲜催化裂解催化剂经反应后再生得到再生催化裂解催化剂,再生催化裂解催化剂不断循环使用,在此过程中不再向提升管反应器中补充新鲜催化裂解催化剂。
55.根据本发明,第三催化裂解反应的温度可以为500-650℃,重时空速可以为2-20小时-1
,压力可以为0.15-0.4mpa;优选地,第三催化裂解反应的温度可以为550-600℃,重时空
速可以为10-15小时-1
,压力可以为 0.25-0.35mpa。
56.根据本发明,催化裂解催化剂是本领域技术人员所熟知的。在一种具体实施方式中,以干基计并以催化裂解催化剂的总重量为基准,催化裂解催化剂含有1-60重量%的沸石混合物、5-99重量%的耐热无机氧化物和0-70重量%的粘土,其中,以沸石混合物的总重量为基准,沸石混合物含有1-90重量%的改性β沸石和10-99重量%的具有mfi结构的沸石。
57.在一种优选的具体实施方式中,催化裂解催化剂含有1-50重量%的沸石混合物、10-70重量%的耐热无机氧化物和0-60重量%的粘土,其中,以沸石混合物的总重量为基准,沸石混合物含有1-75重量%的改性β沸石和10-99 重量%的具有mfi结构的沸石;优选地,以沸石混合物的总重量为基准,沸石混合物含有10-70重量%的改性β沸石和30-90重量%的具有mfi结构的沸石。改性β沸石为本领域的技术人员所熟知的,例如可以为磷和过渡金属 m改性的β沸石。其中,过渡金属m可选自fe、co、ni和cu中的一种或几种,优选为fe和/或cu。具有mfi结构的沸石也为本领域的技术人员所熟知的,例如可以为具有pentasil结构的高硅沸石,优选地,为zrp系列沸石和/或zsm-5沸石。在一种具体实施方式中,具有mfi结构的沸石为含稀土的zrp沸石、含磷的zrp沸石、含磷和稀土的zrp沸石、含磷和碱土金属的zrp沸石,以及,含磷和过渡金属的zrp沸石中的一种或几种。β沸石和具有mfi结构的沸石可以由商购得到,也可以采用本领域熟知的方法进行制备,在此不再赘述。耐热无机氧化物可以选自sio2和/或al2o3。粘土可以为本领域常规使用的各种粘土,如高岭土和/或多水高岭土。
58.根据本发明,可以采用本领域的技术人员所熟知的方法制备得到改性的β沸石。在一种具体实施方式中,在合成β沸石的过程中引入磷和过渡金属 m;在另一种具体实施方式中,在合成β沸石后采用铵交换、磷改性、过渡金属m改性及焙烧处理等步骤来引入磷和过渡金属m。
59.根据本发明,在一种具体实施方式中,在催化裂解的反应过程中,可以向提升管反应器中注入稀释剂,以降低油气的分压。稀释剂可以为本领域的技术人员所熟知的,例如可以选自水蒸气、氮气和c1-c4烷烃中的一种或几种,优选为水蒸气,水蒸气与加氢生成油的重量比可以为(0.01-2):1,优选为(0.1-1):1。
60.本发明还提供了一种可用于本发明提供的催化裂解反应的催化裂解装置,包括提升管反应器、与提升管反应器串联的流化床反应器。提升管反应器从下到上依次设置有长管进料喷嘴、重油喷嘴、稀释蒸汽喷嘴。提升管反应器可以为等直径提升管、等线速提升管或变直径提升管,优选为等直径提升管。流化床反应器可以为密相流化床反应器、鼓泡床反应器、湍流床反应器或快速床反应器,优选为湍流床反应器。
61.一种优选的具体实施方式,如图1所示,重油喷嘴8将重质油喷入提升管反应器1的下部,与来自经由再生器5、再生剂输送管6和流量控制阀7 的热再生催化剂接触进行第一催化裂解反应,得到第一产物与第一积炭催化剂;将加氢生成油和富氢气体从提升管反应器底部的长管进料喷嘴10(位于重油喷嘴的下游)喷入,在提升管反应器1的中部位置喷出,与第一产物和第一积炭催化剂混合,发生第二催化裂解反应,得到含有丙烯的第二产物和第二积炭催化剂。第二产物与第二积炭催化剂继续提升,与稀释蒸汽喷嘴9 喷出的稀释蒸汽通过出口分布器11共同输送到流化床反应器2中,与通过补充再生剂输送管14和流量控制阀15输送的再生催化裂解催化剂接触,发生第三催化裂解反应。流化床反应器2中反应后
的再生催化裂解催化剂和反应后的第二积炭催化剂通过流化床反应器底部进入汽提器3,汽提后通过待生剂输送管12和流量控制阀13进入再生器5再生,使流化床反应器2中得到的产物由流化床反应器2的顶部进入沉降器4,再经旋风分离器除去其中携带的催化剂进入分馏装置分馏。汽提器3与流化床反应器2气固连通,通过调节汽提器3向再生器5排出待生催化剂的流量控制阀13,或者控制再生器5输送至流化床反应器2的补充剂的流量控制阀15,可以直接控制流化床反应器2中催化剂的量,进而控制流化床反应器内反应的重时空速。再生器 5中的再生催化裂解催化剂通过再生剂输送管6引入提升管反应器1中。
62.下面通过实施例来进一步说明本发明,但是本发明并不因此而受到任何限制。
63.实施例1
64.本实施例所用的催化裂解催化剂组成如下:以干基计并以催化裂解催化剂总重量为基准,含10重量%的β沸石、20重量%的zsm-5沸石、45重量%的高岭土和25重量%的铝粘结剂。
65.催化裂解催化剂采用如下方法制备:将dasy沸石(含2重量%re2o3,中石化催化剂齐鲁分公司产品)与zsm-5(中石化催化剂齐鲁分公司产品,含1.1重量%re2o3,1.2重量%磷)用水打浆,制得固含量为30重量%的浆液,将高岭土(苏州中国高岭土公司出品)、拟薄水铝石(山东铝业公司出品)以及水混合打浆制备固含量30重量%浆液,将上述两种浆液混合,于 50℃下搅拌30分钟得到催化剂浆液,将催化剂浆液喷雾干燥即得到催化裂解催化剂。
66.本实施例的流程如图1所示,将重质油(性质见表1)送入提升管反应器1与来自再生器5的再生催化裂解催化剂(相当于新鲜的催化裂解催化剂) 接触进行第一催化裂解反应后,生成第一产物与第一积炭催化剂;将加氢生成油(性质见表2)和干气从提升管反应器底部的长管进料喷嘴10加入,在提升管反应器1的上部位置喷出并与第一产物和第一积炭催化剂混合,发生第二催化裂解反应,生成第二产物和第二积炭催化剂。将第二产物与第二积炭催化剂继续提升,同稀释蒸汽喷嘴9喷出的稀释蒸汽共同输送到流化床反应器2(密相流化床反应器)中,与通过补充再生剂输送管14输送的补充再生剂接触,发生第三催化裂解反应。反应后的待生催化剂由流化床反应器2 的底部离开并进入汽提器3,第三催化裂解反应得到的产物从流化床反应器 2的顶部离开,进入沉降器4,分离出携带的催化剂后进入分馏装置;反应条件以及反应结果见表3。
67.加入的加氢生成油的进料温度为100℃,干气与加氢生成油的重量比为 0.0002,第一积炭催化剂的积炭量为0.18重量%,补充再剂占提升管催化剂循环量的20重量%。
68.表1
[0069][0070][0071]
表2
[0072][0073][0074]
实施例2
[0075]
本实施例的流程及催化裂解催化剂同实施例1,加入的干气与加氢生成油的重量比为0.0005。其他反应条件以及反应结果见表3。
[0076]
实施例3
[0077]
本实施例的流程及催化裂解催化剂同实施例1,第一积炭催化剂的积炭量为0.25重量%。其他反应条件以及反应结果见表3。
[0078]
实施例4
[0079]
本实施例的流程同实施例1,催化裂解催化剂组成如下:以干基计并以催化剂总重量为基准,催化裂解催化剂中含10重量%的β沸石、30重量%zsm-5沸石、40重量%高岭土和20重量%的铝粘结剂。其他反应条件以及反应结果见表3。
[0080]
实施例5
[0081]
本实施例的流程及所用催化裂解催化剂同实施例1,不同之处仅在于,催化裂解催化剂与重质油的重量比为350,第一积炭催化剂的积炭量为0.11 重量%。其他反应条件以及反应结果见表3。
[0082]
实施例6
[0083]
本实施例的流程及所用催化裂解催化剂同实施例1,不同之处仅在于,催化裂解催化剂与重质油的重量比为15,第一积炭催化剂的积炭量为0.41 重量%。其他反应条件以及反应结果见表4。
[0084]
实施例7
[0085]
本实施例的流程及所用催化裂解催化剂同实施例1,不同之处仅在于,干气与加氢生成油的重量比为0.00001。其他反应条件以及反应结果见表4。
[0086]
实施例8
[0087]
本实施例的流程及所用催化裂解催化剂同实施例1,不同之处仅在于,干气与加氢生成油的重量比为0.3。其他反应条件以及反应结果见表4。
[0088]
实施例9
[0089]
本实施例的流程及所用催化裂解催化剂同实施例1,本实施例中加氢生成油的进料温度为380℃,其他反应条件以及反应结果见表4。
[0090]
实施例10
[0091]
本实施例的流程同实施例1,本实施例中催化裂解催化剂组成如下:以干基计并以催化裂解催化剂的总重量为基准,催化裂解催化剂含有10重量%的y沸石、20重量%zsm-5沸石、45重量%高岭土和25重量%的铝粘结剂,其他反应条件以及反应结果见表4。
[0092]
对比例1
[0093]
本对比例所用的催化裂解催化剂同实施例1,不同之处在于,将加氢生成油送入提升管反应器1与来自再生器5的再生催化剂接触进行第一催化裂解反应。反应后的油气混合产物和催化剂继续提升,同稀释蒸汽喷嘴9喷出的稀释蒸汽共同输送到流化床反应器2中,与通过补充再生剂输送管14输送的再生催化裂解催化剂接触,发生第二催化裂解反应。反应后的待生催化剂引至湍流流化床反应器2的底部,并在流化床反应器2的底部离开并进入汽提器3,第二催化裂解反应得到的产物从流化床反应器2的顶部离开,进入沉降器4,分离出携带的催化剂后进入分馏装置。其他反应条件以及反应结果见表5。
[0094]
对比例2
[0095]
本对比例的流程及所用催化裂解催化剂同实施例1,不同之处仅在于,将加氢生成油经过长管进料喷嘴输送至提升管反应器中,不加入干气。其他反应条件以及反应结果见表5。
[0096]
对比例3
[0097]
本对比例的流程及所用催化裂解催化剂同实施例1,不同之处在于,将加氢生成油
和干气送入提升管反应器1与来自再生器5的再生催化剂接触进行第一催化裂解反应。反应后的油气混合产物和催化剂继续提升,同稀汽喷嘴9喷出的稀释蒸汽共同输送到流化床反应器2中,与通过补充再生剂输送管14输送的再生催化裂解催化剂接触,发生第二催化裂解反应。反应后的待生催化剂引至流化床反应器2的底部,并在流化床反应器2的底部离开并进入汽提器3,第二催化裂解反应得到的产物从流化床反应器2的顶部离开,进入沉降器4,分离出携带的催化剂后进入分馏装置。其他反应条件以及反应结果见表5。
[0098]
表3
[0099][0100][0101]
表4
[0102][0103][0104]
表5
[0105]
[0106][0107]
由上述可知,本发明的方法使催化裂解催化剂具有特定的积炭量,并使加氢生成油在临氢条件下进行催化裂解反应,使得催化裂解反应在多产丙烯的同时还能够有效地降低干气的产率。
[0108]
以上结合附图详细描述了本发明的优选实施方式,但是,本发明并不限于上述实施方式中的具体细节,在本发明的技术构思范围内,可以对本发明的技术方案进行多种简单变型,这些简单变型均属于本发明的保护范围。
[0109]
另外需要说明的是,在上述具体实施方式中所描述的各个具体技术特征,在不矛盾的情况下,可以通过任何合适的方式进行组合,为了避免不必要的重复,本发明对各种可能的组合方式不再另行说明。
[0110]
此外,本发明的各种不同的实施方式之间也可以进行任意组合,只要其不违背本发明的思想,其同样应当视为本发明所公开的内容。
再多了解一些
本文用于企业家、创业者技术爱好者查询,结果仅供参考。