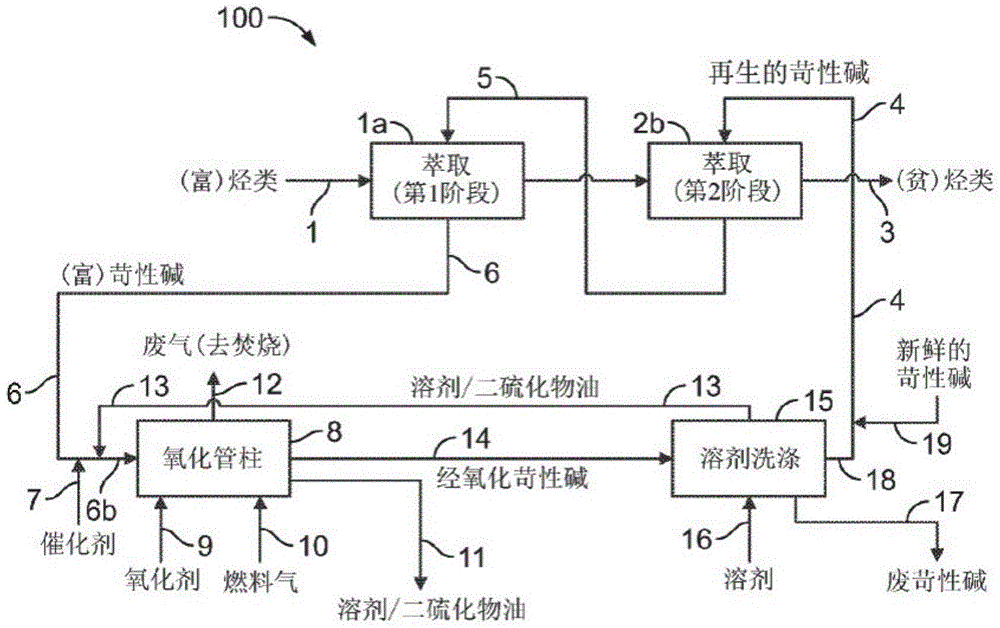
本申请是申请日为2017年6月9日、申请号为“201780038976.x”、名称为“氧化工艺”的发明专利申请的分案申请。
本发明大体上涉及一种用于氧化硫醇,确切地说从液体苛性碱物料流移除硫化合物的改良工艺。更具体来说,本发明关于一种处理富苛性碱的工艺,其在含有垂直悬挂纤维的单一管柱或容器内使用三相氧化将硫醇催化氧化为二硫化物油,以制备可再用于烃脱硫工艺的再生的苛性碱物料流。本发明还可以作为改造部分集成到用于从烃移出硫污染物的现有工艺中,因此取消昂贵的设备并保存空间。
背景技术:
使用苛性碱从烃物料流移除硫污染物,确切地说硫醇为已知的。同样地,通过使富苛性碱物料流与催化剂在氧气存在下接触,之后使二硫化物与经处理苛性碱来将这些硫醇氧化为二硫化物也是已知的。出于经济原因,处理废苛性碱且后续回收再生的苛性碱为重要的。同样地,降低对过多设备的需求且随之引起的土地空间的节省是持续的期望目标。
通常,将液-液接触器和在某些情况下纤维-膜接触器用于烃的苛性碱处理,如美国专利第3,758,404号、第3,977,829号和第3,992,156号所描述,所述专利全部以引用的方式并入本文中。这类工艺之后通常为苛性碱再生器工艺,其涉及氧化反应器,之后为一或多个分离容器。用于处理烃的典型的工艺流程方案涉及第一苛性碱处理,其使用至少一个液体-液体接触器以从烃类进料萃取硫污染物(通常为硫醇),从而产生富含硫醇或称为“富苛性碱”的“废”苛性碱溶液;在接触器中分离经处理烃;氧化富苛性碱以将硫醇转化为二硫化物(通常称为二硫化物油(“dso”)),产生“经氧化”苛性碱溶液,且随后使用重力分离器以从经氧化苛性碱溶液分离dso。在一些实例中,使用颗粒煤床结合重力沉降装置作为聚结器以进一步帮助使dso与经氧化苛性碱分离。在移除dso之后,可进一步处理再生的苛性碱且随后回收,其中使所述苛性碱与新鲜的补充苛性碱混合且在液-液接触器中用于处理烃类进料。更通常,需要另外的净化处理以便将未转化的硫醇和残余dso以硫形式减少到优选地低于5重量ppm。不希望在再生的苛性碱中存在大量硫醇,因为硫醇可导致萃取效率损失并可能导致二硫化物的下游形成。在再生的苛性碱中存在大量dso导致在烃苛性碱萃取工艺期间,dso不合需要地再进入烃或反萃取到烃中。
溶剂洗涤是已知技术且常用作净化步骤以从苛性碱萃取残余dso。然而,由于质量转移和平衡限制,这些溶剂洗涤单元操作通常需要多个具有较高资金和操作成本的阶段。此外,溶剂洗涤从苛性碱移除硫醇的效率较低。类似地,离心工艺和膜分离受高成本困扰且难以获得小于5重量ppm硫。
吸附净化是可使用的另一技术。已应用吸附脱硫以从烃(诸如汽油和柴油)移除硫化合物。实例展示于美国专利7,093,433、7,148,389、7,063,732和5,935,422中。然而,这些专利和其它文献中所报导的吸附剂对苛性碱介质的效率较低。
因此,仍需要研发可经济地从苛性碱移除二硫化物和硫醇两者以获得小于15重量ppm硫、优选地小于7.5ppm的技术。
本工艺使用单一管柱或容器氧化不溶性二硫化物和硫醇且从富苛性碱进料将两者移除。另外,相比于从苛性碱溶液移出残余硫化合物的传统方法,通过最小化资金和操作成本,本工艺为极其经济的。这些和其它优势将从本发明的以下更详细描述变得显而易见。
技术实现要素:
如所提及,本发明涉及采用三相催化氧化反应,使用单一管柱移除富苛性碱进料中的硫化合物的工艺。本发明产生再生的苛性碱物料流,其含有少于15ppm重量、优选地少于7.5ppm重量(呈硫形式)的硫化合物。
尽管已知使用氧化作为将硫醇转化为dso的手段,但这类已知工艺通常未将全部硫醇转化为dso,因此在氧化反应产物流中留下高达5%或更多的硫醇。在本发明之前,未转化的硫醇始终以未转化形式留在再生的苛性碱中,这不利地影响后续苛性碱-烃萃取工艺。在本发明之前尚未意识到的是:伴随通常在富苛性碱物料流的氧化之后在分离工艺中未移除的残余dso,可全部在单一管柱中使用至少两个反应区且在第二反应区内采用垂直悬挂纤维,将那些残余硫醇转化为dso,所述第二反应区以包含约20体积%到约100体积%蒸气的气体连续相运行。本工艺可轻易集成到新的和现有苛性碱再生工艺流动方案中(例如经由改造),其中在使由处理烃物料流产生的硫污染物与贫苛性碱(新鲜和/或回收)接触时,产生富苛性碱物料流。
如本文所用,二硫化物油或dso意味着包括可能的二硫化物的混合物,包括二甲基二硫化物、二乙基二硫化物、甲基乙基二硫化物和高级二硫化物。同样地,术语硫醇意味着包括一类有机硫化合物中的任一种,所述有机硫化合物类似于醇和苯酚,但含有硫原子代替氧原子,并且特别包括硫醇盐。含有直接连接至碳的作为主要基团的-sh的化合物称为“硫醇”。
本发明的一个方面涉及从苛性碱进料流移除残余硫化合物的工艺,其中将含有硫醇和液体催化剂的液体物料流提供于含有一束垂直悬挂纤维的管柱的顶部。使含有氧气的气体与液体物料流混合以形成混合物,之后使所述混合物与垂直悬挂纤维接触。随后引导所述混合物向下朝纤维流动且进入包含约20体积%到约100体积%蒸气的气体连续相反应区。在连续相反应区中,在混合物向下朝反应区中的纤维流动时,将硫醇氧化为二硫化物油。收集、分离制备的dso,且将其从管柱移除。
在本发明的另一个方面,存在一种用于再生苛性碱溶液的方法,所述苛性碱溶液包含含有硫醇的富苛性碱液体,所述富苛性碱液体与液体催化剂混合以形成液体苛性碱催化剂混合物。随后将此液体苛性碱催化剂混合物引入垂直管柱的底部部分,所述垂直管柱经配置以使液体苛性碱催化剂混合物在管柱内部向上流动,其中将含有氧气的气体注射或鼓泡到液体苛性碱催化剂混合物中以形成气体液体混合物,所述气体液体混合物在管柱内部向上流动,从而进入第一反应区。第一反应区可包含支撑的填充材料床作为气体液体混合物的接触表面。在此第一反应区中,将硫醇氧化为二硫化物油,形成经氧化的气体液体混合物,随后将经氧化的气体液体混合物引入安置于顶部塔盘与底部塔盘之间的管道,使得二硫化物油和苛性碱的液体混合物离开顶部塔盘顶表面上的管道,所述顶部塔盘固定地附接到管柱的上部部分。优选地将顶部塔盘上方管柱的上部部分的内部维持为非爆炸环境,此非爆炸环境可通过将燃料气或惰性气体引入上部部分来实现。
将二硫化物油和苛性碱的液体混合物引入连接到顶部塔盘下表面的护罩,其中二硫化物油和苛性碱的液体混合物接触一束垂直悬挂纤维,使得二硫化物油和苛性碱的液体混合物向下朝所述束中的单独纤维流动并进入第二反应区。将第二反应区维持为包含约20体积%到约100体积%蒸气的气体连续相且以此运行,以使二硫化物油和苛性碱的液体混合物中的硫醇氧化,同时使二硫化物油和苛性碱的液体混合物向下朝第二反应区中的纤维流动,以形成再生的苛性碱和二硫化物油混合物。以足以使二硫化物油与再生的苛性碱分离的滞留时间在底部塔盘上收集再生的苛性碱和二硫化物油混合物。从管柱移除分离的二硫化物油的连续物料流和再生的苛性碱的物料流。
本发明的氧化反应器还可以包含具有垂直轴线、上部部分和下部部分的管柱,其中第一反应区定位于下部部分上方。第一反应区可包含支撑的填充材料床从而提供用于气体-液体接触增大的表面区域。第二反应区定位于第一反应区上方和上部部分下方且由顶部塔盘和底部塔盘界定,其中两个盘固定地附接到管柱且具有上表面和下表面。流体导管安置于顶部塔盘与底部塔盘之间,所述流体导管经配置以在底部塔盘下表面与顶部塔盘上表面之间提供流体连通。这允许流体(即气体和液体混合物)的向上流动,从而从底部塔盘下方的第一反应区移动到管柱的上部部分和顶部塔盘上方。安置护罩,使得其从顶部塔盘下表面向下垂直延伸。护罩在顶部塔盘上表面与第二反应区之间提供流体连通。多个悬挂纤维平行于管柱的垂直轴线安置且部分地含于护罩内,使得悬挂纤维在护罩的下端向下延伸到第二反应区中。
本发明的氧化反应器还可以具有经修改或延长的护罩,所述护罩包含脱离装置,其界定具有一或多个开口的聚结区,所述开口经配置以允许护罩内的液体经由一或多个开口沿不平行于垂直轴线的流动路径离开护罩。
本工艺的又一方面涉及改造现有和先前使用的氧化反应器的方法,其中对现有先前使用的氧化反应器的内部构件列清单以确定现有组件的存在。测定反应器的内部尺寸且随后安装新的组件,或修改反应器中的现有组件,使得经改造的氧化反应器包含位于反应器的上部部分的顶部塔盘和底部塔盘,其中两个塔盘具有上表面和下表面,且管道安置于顶部塔盘与底部塔盘之间。此管道经配置以在底部塔盘的下表面与顶部塔盘的上表面之间提供流体连通。此经改造容器/反应器也将含有护罩,所述护罩经定位,使得其从顶部塔盘的下表面向下垂直延伸且在顶部塔盘的上表面与底部塔盘的顶表面之间提供流体流通。多根悬挂纤维定位于护罩内部,所述悬挂纤维平行于反应器的垂直轴线定位且在护罩下端和顶部塔盘顶表面上方向下延伸。
从管柱移除的再生或贫苛性碱物料流具有少于15重量ppm、优选地少于7.5重量ppm(呈硫形式)的硫化合物。管柱的操作温度在约50到约212℉、优选地约75到约175℉且最优选约75到约150℉范围内。本工艺可在环境压力下或在通常在苛性碱再生工艺流程方案中所遇到的操作压力下操作。
用于氧化工艺的液体催化剂组合物优选地是液体螯合的多价金属催化剂溶液。多价催化剂包括但不限于金属酞菁,其中金属阳离子选自由以下组成的群组:钒(v)、锰(mn)、铁(fe)、钴(co)、镍(ni)、铜(cu)、锌(zn)、钌(ru)、铑(rh)、钯(pd)、银(ag)等。催化剂浓度为约10到约10,000ppm、优选地约20到约4000ppm。
用于本氧化工艺的液体催化剂组合物还可以包括大气压沸点为65℃到225℃的一或多种醇。这些醇包括但不限于甲醇、乙醇、1-丙醇、2-丙醇、2-甲基-1丙醇、2-甲基-2-丁醇、环己醇、苯酚、甲酚、二甲苯酚、对苯二酚、间苯二酚、儿茶酚、苄醇、乙二醇、丙二醇和其它烷基酚。当与一或多种碱金属氢氧化物混合时,形成优选地浓度为约5到约40wt%、最优选地约10到约35wt%的醇的碱金属盐。优选醇的一种类型是芳香族醇,即由通式芳基-oh表示的化合物。芳基可以是苯基、苯硫基、吲哚基、甲苯基、二甲苯基等。优选的芳香族醇包括苯酚、甲酚、二甲苯酚、甲基乙基苯酚、乙基苯酚、三甲基苯酚、萘酚、烷基萘酚、苯硫酚、烷基苯硫酚和类似酚类。非芳香族醇可以是伯醇、仲醇或叔醇,其包括甲醇、乙醇、正丙醇、异丙醇、环己醇、2-甲基-1-丙醇和2-甲基-2-丁醇。还可以使用不同醇的混合物。优选醇的大气压沸点为约80℃到约215℃。优选的醇的碱金属盐包括但不限于环己醇钾、异丙醇钾、丙二醇二钾、甲酚钾以及其钠对应物,和其混合物。
催化剂的其它成分可包括一或多种羧酸,包括一或多种羧酸。这类酸包括但不限于脂肪酸、环烷酸、氨基酸、酮酸、α羟基酸、二羧酸和三羧酸。这些酸还与碱金属氢氧化物反应以制备浓度为约0到约40wt%、优选地约5到约25wt%的其碱金属盐。一般来说,羧酸可包括烷酸和环烷酸,其中烷酸由r-cooh表示,其中r是氢或在ch3-(即乙酸)到ch3(ch2)18-(即花生酸)范围内的烷基。环烷酸是多种环戊基羧酸与环己基羧酸的混合物,其中主要级分优选地具有9到20个碳的碳骨架。多种羧酸化合物的混合物还可以用作处理溶液的部分。
液体催化剂调配物的另外其它成分可以是选自以下各项的碱金属氢氧化物:氢氧化锂(lioh)、氢氧化钠(naoh)、氢氧化钾(koh)、氢氧化铷(rboh)和氢氧化铯(csoh)。可使用超过一种碱金属氢氧化物。碱金属氢氧化物的浓度超过足以确保全部醇和羧酸形成其对应碱金属盐的浓度。优选的是氢氧化钠和尤其氢氧化钾。
根据以下包含的优选实施例的细节描述,这些和其它目标将变得更加清楚。
附图说明
图1示意性地说明本发明改良的氧化工艺作为烃脱硫工艺的部分的一种可能应用;
图2是本发明氧化管柱的一个实施例的截面视图;
图3是连接到护罩和界定聚结区的脱离装置的一种可能设计的示意图;且
图4是图3中所示的脱离装置的截面部分的示意图。
具体实施方式
如前所述,本发明涉及一种使用氧化反应将硫醇转化为二硫化物油(dso)的新颖方法。此工艺可以集成到烃脱硫工艺中作为苛性碱再生步骤的部分,所述苛性碱再生步骤经设计成从富苛性碱移除硫化合物,所述富苛性碱从富烃类进料萃取。更具体来说,本发明通过使用单一管柱或其它容器进行硫醇氧化和由经处理苛性碱形成的dso的分离来消除对多个过多容器和额外单元操作的需求。经处理苛性碱优选地具有少于7.5ppm重量硫化合物且适用于再循环回到烃脱硫工艺。本发明工艺利用维持为气体连续相的反应区,所述气体连续相包含约20体积%到约100体积%蒸气且利用垂直悬挂纤维。
图1说明集成到烃脱硫工艺100中的本发明的一个实施例。然而,本发明可以是从大量不同来源接受富苛性碱的独立式氧化工艺。图1展示正在逆流多阶段萃取工艺中处理的富烃类进料1。通常,富烃类1混杂有硫醇化合物,例如甲基和乙基硫醇盐。将贫或再生的苛性碱4进料到最后阶段2b中,在最后阶段中,贫苛性碱首先在阶段2a中处理之后从进入阶段2b的烃类萃取硫醇。从第二阶段移除苛性碱作为物料流5,其中在第一阶段2a中,使其接触进入的富烃类进料1。从阶段2a移除富或废苛性碱且移除经处理贫烃类作为脱硫烃类3以用于例如在烷基化单元中进一步处理。脱硫烃类3现在基本上不含硫,意味着烃类的硫含量为<150ppm总硫量、优选地<30ppm总硫量并且更优选<10ppm总硫量。
烃类/苛性碱处理部分的特定设计对本发明并不关键;然而,优选的设计包括按如图1中所示意性说明的逆流配置操作的分阶段接触器,其中最优选的接触器配置使用纤维膜液-液接触器帮助硫醇从烃类质量转移到苛性碱处理溶液中。这些以及其它接触器配置为所属领域的技术人员已知。苛性碱4可以是甜味烃类领域已知的任何类型,包括包含naoh、koh、ca(oh)2、na2co3、氨、有机酸的萃取物或其混合物的溶液。优选地,苛性碱包含浓度为约1重量%到约50重量%、更优选地约3重量%到约25重量%、仍更优选地约5重量%到约20重量%碱金属氢氧化物的氢氧化钾水溶液和氢氧化钠水溶液。
使从烃脱硫工艺移出的富苛性碱6与液体催化剂7混合,优选地作为液体催化剂的新鲜补充物料流,以便补充在催化剂与苛性碱一起在整个工艺100中移动经由降解所损失的催化剂。优选的液体催化剂是通过向碱金属氢氧化物的水溶液添加金属酞菁催化剂来制得。另一优选的液体催化剂溶液进一步含有醇和至少一种羧酸,诸如环烷酸或乙基己酸。
在本发明的一个替代实施例中,可以将小体积溶剂物料流13添加至富苛性碱6。优选地,此溶剂物料流13获自下游溶剂洗涤步骤15且可含有少量dso。溶剂物料流可以在进入单一氧化器管柱8之前与富苛性碱混合或其可作为分离流注入单一氧化器管柱8的底部。所述溶剂可以是任何轻质烃或轻质烃的混合物,其将有助于在氧化硫醇之后使dso与苛性碱溶液分离,然而,优选的溶剂包括石脑油和煤油。尽管尚不明确了解溶剂促进dso与经氧化苛性碱分离的确切机制,但一种理论是溶剂对dso的溶解度远高于苛性碱,其溶解度差异提供萃取驱动力。因为如将在下文更详细地阐释的单一氧化器管柱利用纤维-膜技术,提供比其它形式的接触装置更高的界面表面积,所以进一步放大此作用。以与富苛性碱一起或单独引入氧化器中的富苛性碱进料的体积百分比计的溶剂量对本发明并不十分关键,只要使用使单一管柱氧化器8内的分离性能最大化的最小量即可。如所提及,仅需要小体积溶剂,最小溶剂注射的优选范围是约0.1体积%到约10.0体积%、优选地约0.5体积%到约5.0体积%的富苛性碱进料6。
除了进料到单一管柱氧化器8的富苛性碱、液体催化剂和溶剂之外,还将氧化剂9(诸如空气)、过氧化氢或其它含有氧气的气体引入到单一管柱氧化器8。添加至氧化器的氧化剂量足以实现最初存在于富烃类中的硫醇90 %的氧化和向二硫化物化合物的转化,最优选地99 %氧化。可将第二任选的氧化剂进料80(参见图2)添加至氧化器8,以便以包含约20体积%到约100体积%蒸气的气体连续相维持第二反应区。
单一管柱氧化器8的操作条件的优选范围包括约75℉到约200℉的温度和高至60lhsv的苛性碱流动速率,但优选地为约100℉到约150℉和小于5lhsv。本发明工艺的操作压力可以是大气压到约100psig。
从单一管柱氧化器8中移出的经氧化或贫苛性碱14可以接着在溶剂洗涤工艺15中处理,在所述工艺中,溶剂16优选地以逆流流动配置与贫苛性碱14接触以移除未在单一管柱氧化器8中分离的任何残余dso。从溶剂洗涤步骤15中移出完全再生的苛性碱18。在将产生的苛性碱4回收回到萃取阶段2a和2b之前,可以添加一定量的补充新鲜苛性碱19。
接下来转而描述单一管柱氧化器8的细节,图2示意性说明本发明的一个实施例,其中在单一容器中出现硫醇到dso的催化氧化以及经氧化苛性碱的分离。换句话说,处理含有高达50,000ppm总硫化合物的富苛性碱物料流且产生具有少于5ppm硫醇和少于400ppm总硫化合物的经氧化苛性碱物料流不需要其它容器或设备。氧化器8优选地是具有垂直轴线8a的垂直管柱。管柱8具有引入液体苛性碱催化剂混合物6b的下部部分29。如所提及,此液体混合物6b可包含富苛性碱、液体催化剂和溶剂。引导液体混合物6b在管柱8内向上流动,在所述管柱中使其与经由一或多个喷布器20引入下部部分29中的氧化剂9(优选地空气)混合。氧化剂流动的速率使得氧化剂在整个管柱的第一反应区22中充分分布。所得气体液体混合物在管柱中在管柱8中向上流动且进入第一反应区22。此反应区可以填充有作为固体床支撑在可选的床载体21与23之间的无规填充材料(诸如球、环或鞍形物)、结构化填料(诸如波纹板、编织纤维或悬挂纤维)。填充材料提供高表面积以改良气体/液体接触。随着气体液体混合物向上移动通过管柱8,在第一反应区22中开始发生硫醇氧化。
在气体液体混合物离开第一反应区22时,引导所述气体液体混合物且使其流入管道25。管道25的下部开口处于或低于底部塔盘24的下表面24a且提供从底部塔盘24下方至顶部塔盘31的上表面31b以及管柱8的上部部分27的流体路径。管道25的上端优选地是盖26,其用以防止携带液体进入过量废气12中。优选地,通过引入气体10,例如燃料气、惰性气体或这类气体的混合物来将管柱8的上部部分27维持为非爆炸环境。过量气体作为废气12移除且通常送去以例如通过焚烧弃置。
二硫化物油与苛性碱的液体混合物离开管道25到顶部塔盘31的上表面31b,将其引导到顶部塔盘中的开口并进入连接到顶部塔盘的下表面31a的护罩30中。护罩30内是多个或一束垂直悬挂纤维45,其与管柱8的纵向轴线8a大体对准(即大体平行)。垂直悬挂纤维束提供较大表面积以允许反应物接触并最终分离所形成的所得不可混溶液体。
优选地,垂直悬挂纤维包含由选自(但不限于)由以下组成的群组的材料制成的细长长丝或带状物:满足以下两个准则的金属纤维、玻璃纤维、聚合物纤维、石墨纤维和碳纤维:(1)纤维材料必须优先由至少两种不可混溶的液体的混合物润湿;且(2)纤维必须是不会染污工艺或不会被所述工艺例如通过腐蚀破坏的材料。另外,必须允许以非分散方式剂进行质量转移和分离。
护罩30的下端或底部在分离区52中终止,所述分离区界定于液体烃顶表面79(即dso和溶剂的混合物)与顶部塔盘31的下表面31a之间。任选地,在氧化剂80的第二物料流进入护罩30的顶部后,可以注射或以其它方式使其与二硫化物油和苛性碱的液体混合物混合。二硫化物油和苛性碱的液体混合物接触一束垂直悬挂纤维,使得二硫化物油和苛性碱的液体混合物向下朝构成第二反应区的束中的单独纤维流动。
将护罩30内部所含有的第二反应区维持为包含约20体积%到约100体积%蒸气的气体连续相。此蒸气连续相中的过量氧化剂为残余硫醇的氧化提供极佳的质量传输条件。因为气流和液体同时存在,所以由于流动对流动速率没有限制。护罩开口必须定位于液体烃相51上方。苛性碱中的残余硫醇在第二反应区中经氧化且转化为dso。底部塔盘24的上表面24b收集分离区52中的液体混合物。使液体混合物的收集物分离成烃类上部层51和下部水层50。上部烃类层51包含dso和/或溶剂,且下部水层50包含液体催化剂和基本上不含硫的经氧化贫/再生的苛性碱溶液。分别以可变流速经由管线11和14从管柱8中移出上部层51和下部层50,以便维持足以实现由边界界面72界定的两个层的分离。传送上部层中的移出dso和溶剂进行存储或进一步处理。从下部层移出的苛性碱和催化剂优选地传送到溶剂洗涤步骤15(见图1)。经由管线40移出分离区52中的任何过量气体。
在本发明的另一实施例中,包含第二反应区的护罩可进一步包含两个区:上部接触区和强化聚结区(enhancedcoalescingzone;ecz)。ecz安置在护罩底部且由脱离装置界定,所述脱离装置经配置以允许护罩内一部分液体混合物径向向外流动以经由一或多个开口沿不平行于垂直轴线的流动路径离开护罩,从而接触与脱离装置相连的聚结表面。上部接触区由护罩的上部界定。在护罩的上部接触区内,进料到垂直悬挂纤维的液体混合物含于护罩内且在液体平行于管柱8的垂直轴线向下流动时接触纤维。上部和下部接触区中的护罩侧壁是实体(即不含开口)且可采用管状或管道状结构(可以是圆形、椭圆形、方形、矩形或任何形状)的形式,以确保悬挂纤维与液体混合物接触。护罩的实际横截面形状对本发明并不重要且护罩可能具有或可能不具有与脱离装置相同的直径或形状。因为护罩的上部接触区在侧壁中不具有开口,所以液体混合物必须平行于垂直轴线向下流动。
脱离装置可以是护罩的底部部分的延伸部分且界定ecz。悬挂纤维在护罩内和脱离装置内垂直安置,一般平行于管柱的垂直轴线悬挂。脱离装置内的纤维可以是分离的独立束或含于上部接触区内的纤维束的延伸部分。
在ecz中,一部分液体混合物沿径向流动路径离开脱离装置,所述径向流动路径不与悬挂纤维所界定的垂直轴线平行。在液体混合物的部分离开脱离装置后,一部分不可混溶液体中的一种聚结以形成聚结液体。根据聚结液体的特性,形成液滴、细流或小物料流,其向下降到脱离装置外部且平行于垂直轴线。如果聚结液体最初是较高密度液体的一部分,那么其将向下流动且将沉降到容器内部底部处的下部相层中。
脱离装置可以是连接到护罩的独立结构或护罩的延伸部分,限制条件为其允许液体混合物经由一或多个开口径向离开和经由平行于垂直轴线的开口端,与不平行于垂直轴线的径向流动路径相对离开。脱离装置的开口端防止与现有技术尝试相关的压降问题以消除或减少由低界面张力系统引起的分散液。优选的脱离装置包含连接到护罩底部的垂直区段,其处于下部接触区的末端且具有允许一部分液体混合物非平行流动的一或多个侧面开口或孔洞。脱离装置可以是处于下部接触区底部的护罩的穿孔延伸部分,优选地呈环带形式,或者其可以是网筛或其它笼样支撑结构。最优选地,脱离装置具有与其相关联的聚结表面,所述聚结表面经配置以接触液体混合物的部分,所述液体混合物的部分从脱离装置沿流动路径径向离开,所述流动路径大致垂直或相对于垂直轴线大致呈直角。
聚结表面选自由以下组成的组:线栅、多孔金属侧壁、开孔海绵、编织网筛、编织金属丝网、金属的编织或非编织纤维材料、聚合物树脂或金属和聚合物树脂的组合、多根共同编织细丝、填料、纤维过滤器和介质层的彼此组合。用于制造聚结表面的材料包括不锈钢、双相钢、合金、塑料、氟聚合物、纤维组分(聚烯烃、聚酯、玻璃纤维和类似材料)和其混合物。聚结表面最有利地经配置以与混合物中一种液体相互作用且形成小液滴。这些液滴的尺寸随后增长直到较重相的较大液滴,所述较大液滴随后可通过重力轻易从较轻液体沉降出来。聚结表面的体积空隙率应小于98%且最优选地小于或等于96%。
金属丝网聚结表面可包含金属丝和纤维的组合以便产生用于液滴聚结的最大表面积。在许多情况下,金属丝和纤维来自不同构造材料,其中一种具有亲水性(例如金属)且另一种具有促进分离的疏水性(例如聚烯烃或氟聚合物)。在两种材料之间的接合点处存在提高的聚结作用。因此,使用金属和聚合材料两种将显著提高聚结效率。本发明的聚结表面可采用物理包围的形式,或定位成邻近于脱离装置中的槽、孔洞、穿孔或其它开口。此包装聚结表面通过条带、系结、夹具或连接至脱离装置外表面的其它紧固件保持原地,其限制条件为强迫离开的液体混合物接触聚结表面。
最优选地,聚结表面呈环带或环形式并入,所述环带或环形成脱离装置的竖直长度且界定强化聚结区(ecz)。环带的内环或侧壁上是多个孔洞,所述空洞允许液体混合物穿入环带内部,在所述环带内部中,混合物接触安置或填充到环带中的聚结表面。环带的外环或侧壁同样地具有多个孔洞、槽、穿孔、筛或栅开口或其它这类开口以允许混合物传递到脱离装置的外部。用于外壁的开口类型可以与用于内壁的开口类型相同或可以不同。不管聚结表面位于环带中还是缠绕在脱离装置中的穿孔结构周围,聚结表面的体积空隙率优选地在约90%到约99%、更优选地约95%到98%的范围内。聚结表面所占体积应优选地足以消除分散液且形成呈液滴或连续液体流形式的聚结液体。可以改变聚结表面的量以提高或降低形成聚结液体所需的容纳量或滞留时间。优选的聚结材料是共同编织型材料,其由316不锈钢和聚四氟乙烯(teflon)纤维细丝构成,具有极细纤维尺寸和约15到30lb/ft3的安装密度。
图3说明展示为对护罩30的底部的添加的脱离装置60的一个可能实施例。相似参考编号具有如先前描述的相同意义。脱离装置60界定强化聚结区(ecz)且具有开口端62。在图3中示出的特定实施例中,脱离装置60包含环带64,所述环带变为护罩30的延伸部分且提供侧面开口66以允许液体混合物径向流动从而沿不平行于轴线8a的流动路径离开脱离装置。此环带64的截面说明于图4中,所述图4展示悬挂纤维束45含于形成内部容积70的内壁68内。
环带64的内壁68和外壁60两者均含有一或多个侧面开口66。环带内部安置聚结表面63。优选的聚结表面具有在约90%到约99%、更优选地约95%到98%范围内的体积空隙率。优选的聚结材料是共同编织型材料,其由316不锈钢和聚四氟乙烯(teflon)纤维细丝构成,具有极细纤维尺寸和约15到约30lb/ft3的安装密度。添加至环带或在包装配置情况下的聚结材料的量足够,使得存在足够的材料中的液体的滞留时间或停留时间以使液体聚结。多个开口66允许一部分液体混合物沿不平行于垂直轴线8a的径向流动路径流过环带。优选地,一或多个开口66表示在环带侧壁中至少50%开口面积。这些开口可以是任何形状或尺寸的槽、孔洞、刺孔或穿孔。
在混合物穿过环带64时,其接触聚结表面63,其中混合物中的任何分散液崩溃以形成液滴75(参见图2)。这些液滴75继续增长直至其下降穿过聚结材料或再次进入纤维束或经由外壁60中的开口66离开。换句话说,液滴75的形成和增长是混合物中一种液体(通常为较致密液体)的聚结。当液滴是较致密液体时,其增长且下降,向下沉降以变为层50中下部液体的部分。因为在聚结表面63上极少存在或不存在分散液,所以在层50中的较高密度液体与下部密度层51之间形成不同相界面72。这消除较高密度液体的携带且允许精确控制界面高度72,这避免泵气蚀和工艺管线11中的较轻液体的污染。
尽管第二反应区中的温度和压力可在约75℉到约200℉和0psig到约500psig范围内,但优选地两个反应区维持在约100℉到约150℉范围内的温度和在约0psig到约100psig范围内的压力下。
特定实施例的前文描述将如此完全揭示本发明的一般性质以至于通过利用当前知识,其他可以容易地修改和/或使这些特定实施例适应各种申请案而不脱离通用概念,并且因此打算在公开实施例的等效物的含义和范围内理解这些适应和修改。应理解本文中的成语或术语是出于描述而非限制的目的。
用于实现各种公开功能的方法、材料和步骤可以采取多种替代形成而不脱离本发明。因此,后接功能陈述的表述“用以……的手段”和“用于……的手段”或可在上文说明书或下文权利要求书中发现的任何方法步骤语言意欲定义和涵盖可现在或将来存在,执行所列举功能的任何结构、物理、化学品或电元件或结构、或任何方法步骤,无论是否准确等效于上文说明书中所公开的一或多个实施例,即,可使用用于进行相同功能的其它手段或步骤;且希望在所附权利要求书的项目内给以这类表达其最广泛解释。
本文用于企业家、创业者技术爱好者查询,结果仅供参考。