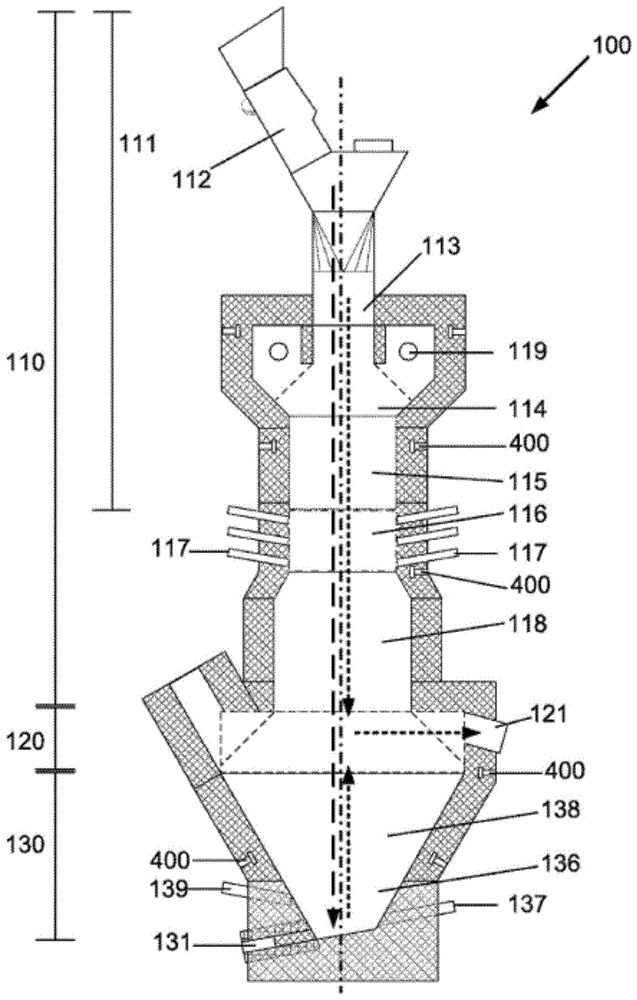
本发明涉及用于气化和/或熔化物质的方法和反应器。特别地,本发明涉及任何废物的材料和/或能量回收,所述废物例如但不限于家庭废物、废旧轮胎、危险废物、石棉、医疗废物、煤或煤渣。该反应器和方法也适合于任何组合原料的气化和熔化,或适于通过使用废物和/或煤来产生能量。
背景技术:
一段时间以来,一直在寻求热处理各种类型的废物和其他材料的解决方案。除燃烧方法外,已知各种气化方法,其主要目标是达到降低污染物对环境的负荷的结果,降低处理原料的成本以及处理过程中产生的气体。然而,已知方法的特点是,难以掌握的复杂技术以及相关的待处理的原料或废物的高处置成本。
例如,ep1261827b1公开了一种用于气化和/或熔化原料的反应器。该反应器没有采用以前常用的循环气工艺的方式。相反,其公开的反应器采用并流原理进行操作。完全消除了传统的再循环气体管理,避免了许多与热解产物冷凝和不希望的沉积物形成有关的问题。此外,ep1261827b1公开了反应器的上部,由于散装材料(散装柱)的急速加热,原料发生了部分聚集,因此基本上排除了与反应器内壁的粘附。在ep1261827b1中公开了在两个注入装置之间形成还原部分,所有气体在取出之前通过该还原部分,从而在很大程度上将其还原。
尽管ep1261827b1中公开的反应器极大地还原了原料,但是由于反应器的出口温度,从反应器中排出的气体如果没有进一步加热就不能用于冶金反应器中以还原熔化。
技术实现要素:
因此,本发明的目的是提供一种用于气化和/或熔化物质的新反应器和方法,其至少部分地克服了上述缺点和/或将是现有气化和/或熔化物质的反应器和方法的有用的替代。
根据本发明的第一方面,提供了一种使用反应器气化含碳原料以产生热还原气体的方法,该方法包括以下步骤:
-通过闸门对含碳原料进行进料,以在反应器的热解区中形成排出床;
-加热所述热解区中的所述排出床,以引发含碳原料的热解并形成热解产物;
-通过在热解区下方的位置向所述反应器供给至少800℃的氧气源,在所述反应器中提供下部高温的上部氧化区;
-将热解产物和如果存在,剩余未热解的含碳原料在所述高温的上部氧化区进行气化,以在所述反应器的上部还原区形成半焦床,所述上部还原区位于所述高温的上部氧化区的下方;
-在所述上部还原区将热能转化为化学能;
-通过在所述反应器的下部还原区下方的位置向所述反应器提供至少800℃温度的氧气源,以在所述反应器中提供下部高温的下部氧化区;
-收集所述下部氧化区中存在的任何金属和/或炉渣熔体;
-去除所述下部氧化区中存在的金属和/或炉渣熔体;和
-通过位于所述反应器的气体出口部分的气体出口排出所述上部还原区内产生的温度至少为1300℃且co/co2比≥5的热还原气体,所述气体出口部分位于所述反应器的所述上部还原区和所述下部还原区之间。
氧气源可以是空气或纯氧。
下部氧化区中存在的金属和/或炉渣熔体可以通过将金属和/或炉渣的熔体开孔从下部氧化区中去除。
提供了排出的热还原气体,其co/co2比≥15。
该方法可以包括以下另外的步骤:向热解区提供热气体(例如,通过燃烧器或喷嘴供应的预热空气或燃烧气体),以引发含碳原料的热解并形成热解产物。
提供将热解区中的排出床逐步加热到至少700℃的温度,温度逐步升高以防止含碳原料和热解产物的分解。有利地,这防止了可能使反应器阻塞的细的或粉末状的含碳原料、热解产物和焦炭的形成。因此,该方法和反应器可以在压力低于形成细的或粉末状含碳原料、热解产物和焦炭的情况下操作。例如,该方法和反应器可以在50kpa的压力下实施和/或操作。
可以控制热气体的体积流量以逐步加热热解区中的排出床。
该方法可以包括以下另外的步骤:在将含碳原料滞塞进料到反应器之前,对含碳原料进行干燥。
可以控制氧气源至下部氧化区的体积流量,以防止炭粉在下部氧化区中的积聚。为了增加在下部氧化区中炭粉的消耗速率,可以增加氧气源至下部氧化区的体积流量。
该方法可以进一步包括以下步骤:在反应器的缓冲区中预热和预干燥含碳原料,所述缓冲区位于反应器的热解区的上方。
通过将含碳原料进料到热解区中,可以形成具有排出锥斗的排出床,并且使所述热解区的横截面相对于缓冲区的横截面而增大。
提供的方法包括以下另外的步骤:在反应器的中间区热解和干燥含碳原料,所述中间区位于热解区的下方。
该方法可以包括以下又进一步的步骤:从所述反应器的至少一个气体出口排出在所述反应器的并流部分中产生的具有至少1300℃温度的热还原气体,所述并流部分包括:
-所述反应器的充气区,所述充气区包括:
○所述反应器的进料区;
○所述反应器的缓冲区;
○所述反应器的热解区;和
○所述反应器的中间区;
-所述反应器的上部氧化区;和
-所述反应器的上部还原区。
提供的方法包括以下步骤:通过位于所述反应器的气体出口部分的所述气体出口排出在反应器的逆流部分中产生的具有至少1300℃温度的热还原气体,所述逆流部分可以包括所述反应器的下部氧化区和下部还原区。
所述上部氧化区的体积与所述充气区的体积的体积比可以为1:n体积单位,其中4≤n≤20。
所述上部氧化区的体积与所述上部还原区和所述充气区的总体积的体积比为1:n体积单位,其中7≤n≤25。
所述逆流部分的体积与所述反应器的总体积的体积比为1:n体积单位,其中1≤n≤10。
通过在中间区下方供应至少800℃的热氧气和/或热空气,可形成一个高温的上部氧化区,该高温的上部氧化区在内衬的特定区域温度高于1800℃以及在床的温度为2000℃至4000℃。热解产物和部分原料在该高温的上部氧化区燃烧、裂解和/或熔化,因此,尚未转化的原料发生进一步结焦。在随后的上部还原区中,热能随后转化为化学能。通过将co2还原为co,可部分实现热能中化学能的转换。此处,气体出口的co/co2气体体积比可能大于10或甚至大于15。例如,co/co2气体体积比可以在10与1000之间,15与10000之间,甚至在15与107之间(基本上不含co2)。
在并流部分中,气体可以从进料区并流流向气体出口。
通过提供至少1000℃的热氧气和/或热空气,也可以在锥形下部氧化区中产生温度在1800℃至4000℃之间的高温区。也可以在向下布置的高温下部氧化区中收集金属和/或炉渣熔体。这些炉渣熔体和/或金属熔体可以根据需要通过开孔排出(例如在模具中)或根据需要连续地烧尽(例如烧至炉渣造粒)。在锥形下部氧化区和锥形下部还原区,也可能产生温度高于1000℃,甚至高达2000℃的高温气体,它们沿气体出口的方向向上(逆流)流动。在下部还原区,部分通过将co2还原为co,热能还可以转化为化学能。这确保了在达到气体出口时,co/co2气体体积比大于10或甚至大于15。例如,co/co2气体体积比在10至1000之间,优选地在15至10000之间,并且特别优选地在15至107之间(基本上不含co2)。来自并流部分的气体(从顶部到底部)和来自逆流部分的气体(从底部到顶部)通过至少一个气体出口从气体出口部分排出。来自并流部分的气体和来自逆流部分的气体的温度在1500℃至1750℃之间,优选在1600℃至1750℃之间。
对于本发明必不可少的有利的方法步骤还可以进一步包括通过抽吸排尽在并流部分产生的气体和在逆流部分产生的气体。为此,可以使用气体抽吸装置。抽吸可以在反应器中产生负压。在反应器中使用负压可以允许在操作期间维护反应器,因为当打开气化器时可能会吸入空气,但是没有气体能够逸出。
根据本发明的第二方面,提供了一种在气化含碳原料的方法中使用的反应器,该反应器包括:
-并流部分,包括:
○充气区,包括:
■具有闸门的进料区,其中原料通过所述进料区从上方引入反应器中;
■缓冲区;
■与所述缓冲区底部邻接的内衬耐火材料的热解区,同时提供横截面扩大;和
■与所述热解区底部邻接的内衬耐火材料的中间区;
○与所述中间区的底部邻接的内衬耐火材料的上部氧化区,并包括在至少一个平面上的多个风口;和
○与所述上部氧化区的底部邻接的内衬耐火材料的上部还原区;
-内衬耐火材料的气体出口部分,包括至少一个气体出口;和
-内衬耐火材料的逆流部分,包括:
○与所述气体出口部分邻接的锥形下部还原区;和
○与所述锥形下部还原区邻接的锥形下部氧化区,锥形下部氧化区包括至少一个风口和开孔,
其中,所述内衬耐火材料的上部氧化区的体积与所述充气区的体积的体积比为1:n体积单位,其中4≤n≤20。
所述内衬耐火材料的上部氧化区的体积与所述内衬耐火材料的上部还原区的体积和所述充气区的体积的总体积的体积比为1:n体积单位,其中7≤n≤25。
所述内衬耐火材料的逆流部分的体积与所述反应器的总体积的体积比为1:n体积单位,其中1≤n≤10。
提供了反应器的至少一个内衬耐火材料部由至少两个彼此叠置的内衬部分组成,其中,在彼此叠置的内衬部分之间形成凸舌-凹槽连接,其中一个所述内衬部分在朝向所述反应器内部的一侧上具有凹槽,而另一个内衬部分在朝向反应器内部的一侧上具有凸舌,其中凸舌-凹槽连接在凹槽和凸舌之间具有与温度相关的间隙开口。
在至少两个内衬部分之间布置有周向水冷式控制台。
上部内衬部分可以具有凹槽,并且下部内衬部分可以具有凸舌。
至少两个内衬部分可以具有一个耐火内部内衬和一个包围该内部耐火内衬的外部内衬。
所述内部耐火内衬可以是由烧结砖制成的内衬或整体式内衬。
所述周向水冷式控制台由碳钢或不锈钢组成。
所述内衬耐火材料的上部氧化区和/或内衬耐火材料的锥形下部氧化区的风口由陶瓷制成。
在替代实施方案中,内衬耐火材料的上部氧化区的风口和/或内衬耐火材料的锥形下氧化区的风口可以由铜或钢制成,其中在每个风口中布置有内部陶瓷管,并且其中在陶瓷内管和相应的风口之间布置有可压缩且耐温的层。
所述内衬耐火材料的上部氧化区的锥角为5°至30°。
所述内衬耐火材料的上部还原区可以布置于内衬耐火材料的气体出口部分的上方,使得所述内衬耐火材料的气体出口部分邻接所述内衬耐火材料的上部还原区的底部,同时提供横截面的扩大。
部分内衬耐火材料的上部还原区可以布置在内衬耐火材料的气体出口部分中,且所述内衬耐火材料的气体出口部分相对于所述内衬耐火材料的上部还原区具有横截面的扩大。
所述内衬耐火材料的锥形下部还原区与所述内衬耐火材料的锥形下部氧化区的锥角为50°至70°。
气体供应装置可以布置在内衬耐火材料的热解区的横截面扩大的区域中。
内衬耐火材料的上部氧化区的风口可布置在多个平面中。
提供了至少一个另外的风口布置在所述内衬耐火材料的锥形下部还原区的另外的平面中;或者一个另外的风口布置在所述内衬耐火材料的锥形下部还原区的另外的平面中,和至少一个额外的风口布置在内衬耐火材料的上部还原区中。
至少一个另外的风口可以布置在所述内衬耐火材料的锥形下部氧化区的另外的平面中。
为了能够从气体出口排出温度大于1500℃,例如在1600℃和1750℃之间的高温气体,如此设计反应器,使得至少在内衬耐火材料的上部氧化区中可以达到:散装物料(或床)的外围区域的温度高于1800℃,散装物料(或床)的中心区域的温度为2000℃至4000℃。这些高温导致内衬耐火材料(例如内衬砖)在轴向、切向和径向上膨胀,每米内衬膨胀达20mm,从而使内衬产生应力,进而在径向上影响反应器的外钢壳。
为了使反应器的稳定性不受这些高温和内衬所产生的应力的损害,根据本发明,反应器的至少一个耐火内衬部分由至少两个彼此叠置的内衬部分组成。所述至少一个内衬耐火材料部分可以是内衬耐火材料的热解区、内衬耐火材料的缓冲区、内衬耐火材料的上部氧化区、内衬耐火材料的上部还原区、内衬耐火材料的气体出口部分、内衬耐火材料的逆流部分或其组合。
在此可以设想,反应器的耐火内衬每2到4米高有一个另外的内衬部分。
对于气体出口温度为1500℃至1600℃的反应器,可以提供,耐火内衬每3到4米高有一个另外的内衬部分。对于气体出口温度为1600℃和1750℃的反应器,可以提供,耐火内衬每2至3米高有一个另外的内衬部分。
因为在内衬的上部氧化区和内衬的下部氧化区中产生特别高的温度(在1800℃和4000℃之间的温度),所以可以提供以这样的方式彼此叠置的内衬部分,使得每一个在内衬的上部氧化区和内衬的下部氧化区恰好布置一个内衬部分。此外可以提供,在氧化区的下方和上方设置另外的内衬部分。这确保了每个高温氧化区仅由一个内衬部分组成,其中,每个衬里部分可在各自的进一步衬里部分的方向上膨胀,使得在这些区域中不需要设置可以在高温下损坏的另外的控制台或其他固定装置。
为了避免热气体或高温继续通过所述至少两个内衬部分之间的区域逸出到外面,还提供,在彼此叠置的耐火内衬部分之间形成凸舌-凹槽连接,其中一个所述内衬部分在朝向所述反应器内部的一侧上具有凹槽,而另一个内衬部分在朝向反应器内部的一侧上具有凸舌。如此设计凸舌-凹槽连接,使得即使当反应器处于静止状态时,凹槽中的凸舌也以正锁紧方式布置,由此凸舌的垂直外壁连接到凹槽的垂直壁,但在凹槽和凸舌之间存在间隙开口。该优点可以确保尽管存在间隙开口,但在反应器启动或高热期间,不会有气体逸出。此外,可以提供,凹槽和凸舌之间的间隙开口是与温度相关的间隙开口。凹槽和凸舌之间的与温度相关的间隙开口可以是例如50mm。如上所述,内衬可以在高温下膨胀,其中由于凸舌-凹槽连接,凸舌能够膨胀到凹槽中。
此外提供了,在所述至少两个彼此叠置的内衬部分之间布置有用于在反应器的加热和冷却期间保持耐火内衬和稳定内衬的周向水冷式控制台。该周向水冷式控制台能够通过弯曲具有方形或矩形横截面的中空圆柱管而无焊缝地制造的。这里可以有利地提供具有高热流的水冷控制台,高热流通过连接法兰提供并由流速为2m/s到25m/s的冷却水来实现。当周向控制台布置在高温(>1500)区域时,这些高流速的冷却水有利于保持其热稳定性和机械稳定性。
至少两个叠置的凸舌-凹槽连接的内衬耐火材料部分和周向水冷式控制台的上述布置可以布置在并流部分和/或气体出口部分和/或逆流部分。每个部分还可以具有两个内衬耐火材料部分的多种布置,两个内衬耐火材料部分彼此叠置,具有凸舌-凹槽连接和周向水冷式控制台。
根据本发明的反应器的并流部分,包括部分内衬的充气区,内衬的上部氧化区和内衬的上部还原区。
部分内衬的充气区包括:具有至少一个闸门的进料区、缓冲区、内衬的热解区和内衬的中间区。
经由带有闸门的进料区,可以从上方将诸如废物、有毒或生物废物、水、废旧轮胎、生物质、木材、煤炭、汽车切碎残渣、骨料等原料进料到反应器中。闸门确保尽可能避免环境空气不受控制地进入和气体从反应器中的排出。期望闸门可以具有液压、气动或电动的闸口。优选地设计这些闸口,使得在反应器中意外的过压的情况下,额外地封闭闸口,而不会有气体无意地逸出。
充气区还包括用于缓冲和预干燥进料体积的缓冲区。缓冲区的温度优选是可调节的。例如,可以提供约100℃到200℃设定温度,用于废物的预干燥。
另外,充气区内提供内衬耐火材料的热解区,其通过产生横截面扩大,优选地突然的横截面扩大来连接到缓冲区的底部。优选地,横截面扩大至少两倍。横截面的扩大确保降低原料的下沉速度,并确保在反应器的气体空间内形成由散装材料制成的锥形排出区(排出锥斗)。排料锥斗集中装有预干燥的原料(来自缓冲区)。
可以通过燃烧器、喷嘴、壁孔或其他装置将热气体(例如燃烧气体,暂时存储或再循环的过量气体或由燃烧提供的惰性燃烧气体)供应到内衬耐火材料的热解区的排放锥斗。床在表面由热气冲击加热,从而尽可能防止原料与内衬(如砖衬或浇注料内衬)粘附。例如,可以通过径向指向床的燃烧器来实现冲击加热。替代地或附加地,也可以借助于环形通道实现冲击加热,火焰在环形通道中旋转。该旋转可以通过将热气切向吹向排出锥斗并将其燃烧来有益地实现。
充气区还包括位于内衬耐火材料的热解区下方并与之邻接的内衬耐火材料的中间区。在中间区,来自热解区的热量和来自内衬耐火材料的上部氧化区下方的废热用于原料的最终干燥和完全热解。可能有利地,中间区包括内衬的(例如,砖内衬的或可浇铸内衬的)钢壳,其中内衬的厚度可以与其他区域的厚度相似。该实施方式简化了反应器的调试(启动),因为在中间区也能够产生高温。在中间区的下部区域中提供锥形横截面可能是有利的,该横截面改变了原料下沉的速率。
在带状内衬耐火材料的并流部分中内衬耐火材料的中间区的下方,有内衬的上部氧化区,在该氧化区内布置有多个风口。这些风口布置在至少一个水平上(距反应器底部的高度或垂直距离)。如上所述,由于反应器具有周向水冷式控制台和两个彼此叠置并具有凸舌-凹槽连接的内衬部分,因此可以将内衬耐火材料区域中上部氧化区的温度提高到高于1800℃,并且通过提供至少1000℃的热氧气和/或热空气可以将散装原料(床)中心的温度提高到2000℃至4000℃之间,而不会损害反应器的稳定性。
通过高温,所有材料都可以转化为无机气体,例如一氧化碳(co)、氢气(h2)、水(h2o)、二氧化碳(co2)、硫化氢(h2s)、氨气(nh3)、二氧化氮(no2)、二氧化硫(so2),或液态金属或液态炉渣,焦炭或碳(c)。
在上部氧化区的下方,在内衬的并流部分中布置内衬的上部还原区,基本上没有有机成分进入该内衬的并流部分。
可以提供有利地,与上部氧化区相比,内衬的上部还原区具有横截面扩大,这改变了原料的沉降率并且增加了在相同水平上停留时间。在内衬的上部还原区,气体以并流的方式流经焦化的固定床,热能转化为化学能,产生一氧化碳(co)和氢(h2)。特别地,将二氧化碳(co2)转化为一氧化碳(co),将水(h2o)转化为氢(h2),从而使仍包含在床中的碳进一步气化。可在反应器中实现将co2还原为co,使得co/co2气体体积比大于10或甚至大于15。例如,co/co2气体体积比在10至1000之间,优选地在15至10000之间,并且特别优选地在15至107之间(基本上不含co2)。
当它们通过上部还原区时,气体同时被冷却,例如冷却到大约1000℃至1600℃的温度。由于所有物料流必定流经上部氧化区且无法返回,因此在经过上部还原区后,与氧化区上方的未反应物料不再有任何接触。通过这种方式,所有干净的裂解和/或熔化的纯无机物质到达气体出口部分,不会再次受到污染。
由于所有物料流必定流经上部氧化区且无法返回,因此在经过上部还原区后,与氧化区上方的未反应物料不再有任何接触。通过这种方式,所有干净的裂解和/或熔化的纯无机物质到达气体出口部分,不会再次受到污染。上部氧化区的气体在通过内衬的上部还原区时被冷却。可提供在内衬的上部氧化区中产生的气体温度非常高,以致流过上部还原区导致冷却到1500℃和1750℃之间的温度,其中,在冷却之后,这些热气体到达气体出口。
提供所述气体出口部分包括至少一个气体出口。还可以设想,多个(例如,四个)气体出口被全方位布置,优选径向分布。
在内衬的气体出口部分下方,有一个基本为锥形的内衬的逆流部分。它包括一个锥形下部还原区,以将来自锥形下部氧化区的气体的热能转换成化学能(主要是co)并产生逆流。该锥形下部还原区与内衬的气体出口部分连接。在锥形下部还原区的下方,布置了锥形下部氧化区,圆锥的切割尖端指向下方。在锥形下部氧化区,残留的焦化材料转化为气体。在锥形下部氧化区,至少一个风口布置在至少一个平面上,通过该风口可以引入至少1000℃的热空气和/或热氧气,这将导致下部氧化区的床的温度在1800℃至4000℃之间。这些高温使炉渣和金属通过至少一个开孔以液态形式排出,以便收集和排放。
产生的气体以逆流的方式流过锥形下部还原区至气体出口部分,在此气体冷却到大约1500℃至1750℃的温度。在此可以提供,在下部氧化区中产生的气体如此高温,以致流过下部还原区导致气体冷却到1500℃至1750℃,或1600℃至1750℃之间的温度,然后通过还原区的气体出口排出。
根据本发明,由于反应器具有在逆流部分中的还原区和在并流部分中的上部还原区,因此总还原区体积(上部和锥形下部还原区的体积之和)比已知反应器的一个还原区大得多。作为示例,参考ep1261827b1,其中在气体出口部分的区域中仅布置一个还原区。
因此,根据本发明,反应器实现了原料的简单、廉价和环境友好的材料和/或能量利用。另外,采用本文描述的反应器能够增加容量和化学能和热能的收率。
在反应器的一种实施方式中提供了,上部内衬部分具有凹槽,而下部内衬部分具有凸舌。
当暴露在高温下时,这可能导致内衬向上膨胀。
该反应器的另一实施方式提供了,所述至少两个内衬部分中的每一个包括至少一个耐火内部内衬和包围该耐火内部内衬的外部内衬,其中耐火内部内衬是由耐火砖制成的内衬或整体式(例如可浇铸)的内衬。
此外,可以提供内衬部分,包括耐火内部内衬和外部内衬,布置在稳定钢壳中。
还可能有利的是,在外部内衬和钢壳之间设置至少一个另外的绝缘层。额外的绝缘层可以由纸板、高温毡或高温泡沫组成。
该实施方案确保钢壳被更好地绝缘。例如,可以这样设计额外的隔热层,使得与没有额外的隔热层的反应器相比,通过钢壳的热损失改善了2%以上,从而降低了钢壳的外部温度。例如,这种设计可使钢壳的外部温度在反应器运行期间保持低于60℃,这意味着不需要接触保护。此外,绝缘层可以用于补偿内部内衬和/或外部内衬的可能的径向热膨胀。
为了减少耐火内部内衬的磨损,也可以提供内部内衬由尖晶石刚玉、铬刚玉或碳化物组成的耐火砖组成。可以提供,这些石材的热导率>3w/mk。
此外,可以提供,通过炉渣冻结来保护反应器的较热区域(温度>1500℃)中的耐火砖不受化学和/或热条件的影响。
为了使这种炉渣冻结,外部内衬可以由导热材料组成,由此可以实现冷却介质(例如,带有冷却水的盘管)到内部内衬的充分的热传递。
在此可以设想,外部内衬由泡沫耐火材料(例如泡沫铝)形成,由此可以浇铸泡沫耐火材料,从而实现冷却介质(例如,带冷却水的盘管)和内部内衬之间的正连接。对于反应器的较热区域(温度>1500℃),还可以提供由尖晶石刚玉或铝刚玉组成的泡沫耐火材料。可替代地,外部内衬由自由流动的铸块组成,该铸块具有较高的稳定性,但是由此导致绝缘性能降低。
对于温度较低的区域(温度<1500℃),外部内衬可以由导热率小于1w/mk的浇铸绝缘泡沫耐火材料制成,以减少热量损失。这种设计确保了在温度较高区域中导热性更高的材料有利于炉渣毛皮的形成,而在温度较低区域中导热性更差的材料可减少热量损失。这是特别有利的,因为温度较低的区域比温度较高的区域覆盖了更多的反应器区域。
本发明的另一个有利的实施方式,周向水冷式控制台由碳钢或不锈钢制成。
使用碳钢还是不锈钢取决于反应器的使用和操作。碳钢比不锈钢便宜,并且具有更高的热导率。但是,不锈钢在热和化学方面比碳钢更稳定。有限元热模拟(finiteelementthermalsimulation)可以帮助确定应将哪种材料用于预期的应用。
本发明的一个实施方式提供,(上部和锥形下部氧化区的)风口由铜或钢制成。此外,可以提供,风口之一具有陶瓷内管,或者一些风口具有相应的陶瓷内管,或者每个风口具有相应的陶瓷内管。风口的这种实施方式(具有陶瓷内管)保护风口免受通过添加氧气和/或空气的金属熔化,由此也可以将氧气和/或空气预热(例如,温度>1000℃)。在陶瓷内管和风口之间设置可压缩且耐温的层也是有利的,由此可以补偿由热引起的机械应力。该可压缩且耐高温的层例如由高温毡、高温纸板或高温泡沫组成。
本发明的另一实施方式提供了,(上部和锥形下部氧化区的)风口可以完全由陶瓷制成。通过该实施方式,例如可以实现,氧化区可以在供应温度高于1000℃的热空气和/或热氧气且因此床温高于2000℃的情况下进行操作,因为陶瓷可以承受比金属更高的温度。
对于完全由陶瓷制成的风口来说,不必进行金属风口不可避免的必要冷却,因此热损失可减少5%以上。通过将具有良好导热性的陶瓷(例如,85w/mk的碳化硅)和熔渣冻结以及绝缘陶瓷(例如,小于4w/mk的尖晶石刚玉)相结合,可以实现这些风口在不冷却的情况下熔化产生的化学负荷和高热应力。
对于反应器来说,内衬的上部氧化区的锥角(α)在5°至30°之间也是有利的。
上部氧化区的这种锥形形状有利地实现了一部分炉渣保留在内衬的表面上,由此实现了在该区域中炉渣的形成。
对于反应器的另一实施方式,希望将内衬的上部还原区布置在气体出口部分的上方,其中,气体出口部分通过扩大横截面,与内衬的上部还原区的下部邻接。在这里可以想到,横截面的扩大是突然的。
优选地,气体出口部分的横截面扩大至少上部还原区的横截面面积的两倍。
该实施方式确保了床呈圆锥形加宽,从而增加床的表面积或排出面积。对于截锥形设计,床的表面或排出区域基本上与外表面相对应。
一个实施方式提供,横截面扩大使得床的排出面积至少是上部还原区的横截面积的三倍。此外,横截面扩大可以大到使得床的排出面积是上部还原区的横截面面积的至少7倍或甚至至少9倍。
对于该实施方式或另一实施方式,还可以提供,气体出口部分的横截面扩大使得床的排出面积增加至少上部氧化区的横截面积的5倍。此外,横截面扩大可以大到使得床的排出面积至少是上部氧化区的横截面面积的9倍。
上述实施方式的优点在于(通过气体出口)的气体流速与扩大的床(与已知反应器相比)的排出面积成比例地减小,使床的粉尘夹带降至最低。
可替代地,对于反应器可以提供,至少部分布置在并流部分中的内衬上部还原区被布置在或插入气体出口部分中。
该实施方式还可提供气体出口部分具有比上部还原区更大的横截面。
在该实施方式中,部分上部还原区的并流部分被引入或部分地插入到气体出口部分中。例如,上部还原区的内衬(例如砖内衬或可浇铸内衬)突出到气体出口部分中。由于气体出口部分的横截面面积大于上部还原区,并且至少一个气体出口位于气体出口部分的边缘部分,因此并流部分中产生的气体必须绕过延伸到气体出口部分的衬里(如砖内衬或浇注料衬里),以到达气体出口,从而使更少的灰尘进入灰尘分离装置。该实施方式减少了反应器的整体高度,其中同时可以改善灰尘分离,因为气体和夹带的灰尘必须另外向上流动以便到达至少一个气体出口。
还可以提供,延伸到气体出口部分中的上部还原区的内衬(例如砖内衬或可浇铸内衬)形成为中空圆柱形状。中空圆柱体形状可以制成为钢保持器结构,该结构在两侧都衬有内衬,该内衬受到水冷的保护,免受高热和随之而来的机械应力的影响。
对于本发明的另一实施方式,上部氧化区的体积与充气区的体积的体积比为1∶n体积单位,其中n为大于或等于(≥)4,且小于或等于(≤)20的数。
因此,与先前已知的反应器相比,上部氧化区的体积大很多倍,由此可以获得相当高的容量。在此还可以想到5≤n≤15,或甚至6≤n≤11。
在反应器实施方式中,上部氧化区的体积与上部还原区的体积和充气区的体积的总体积的体积比为1∶n体积单位,其中n为大于或等于(≥)7,且小于或等于(≤)25的数。
另一实施方式,上部氧化区的体积与上部还原区的体积和充气区的体积的总体积的体积比为1∶n体积单位,其中8≤n≤15,或甚至9≤n≤14。
反应器的该实施方式的优点在于,在假设相同高度的反应器中获得了更大的容量。这是可能的,因为与氧化体积相比,充气区的体积具有已知反应器中更小的比率。
反应器的另一实施方式提供,逆流部分的体积与反应器的总体积的体积比为1∶n体积单位,其中n为1至10之间的数字(1≤n≤10)。在此还可以想到2≤n≤7,或甚至3≤n≤5。
由于气体出口区和逆流部分的横截面的扩大,锥形下部还原区中的排放锥面面积也扩大了,从而较小的气流速度从床中流出,并带走了较少的粉尘。
反应器的另一个有利的实施方式提供,锥形下部还原区的锥角和锥形下部氧化区的锥角在50°至70°之间。由于该实施方式,在锥形下部氧化区和锥形下部还原区中,在足够高的温度下保持液态的熔渣更好地排出,因为炉壁以沿水平方向大约50°-70°,优选地约60°的角度运行,或沿垂直方向以20°到40°的角度运行。
反应器的另一实施方式提供,在热解区中,在横截面扩大的区域中设置气体供应装置。该实施方式确保将热气体(例如,预热的空气或燃烧气体)供应到排放锥斗。
本发明的一种实施方式还提供,上部氧化区的风口布置在几个水平(高度)上。这是特别有利的,因为通过床的均匀加热实现了更好的气体分配。另外,该实施方式确保尽可能避免内衬(例如砖内衬或可浇铸内衬)的局部过热。
反应器的另一有利的实施方式,至少一个风口布置在锥形下部还原区的一个水平(高度)上。
另一个风口以限定的方式额外提供空气和/或氧气,因此不产生co2,几乎完全是co。此外,通过该实施方式可以实现提高产量。此外,该实施方式能够在不损害气体质量的情况下增加产量并增加气体出口处的气体出口温度高于1500℃。
对于热能优于化学能的应用,在上部还原区中布置至少一个额外的风口可能是更有利的。通过该实施方式,可以有利地实现通过将co氧化为co2以及将h2氧化为h2o将化学能(co,h2)转换回热能。
另一实施方式提供,在锥形下部氧化区的另一水平(高度)上布置至少另一个风口。下一水平的风口最好位于开孔上方。
通过将风口布置在开孔上方,可以在开孔的区域中促进熔化,因为热量是在熔体流出液体的区域产生的。同时,在开孔上方布置风口确保了在开孔相对侧上所需的凝固熔体(所谓的炉渣冻结,保护了内衬例如砖内衬)不会液化,并因此不会流出。
根据本发明的第三方面,提供了根据本发明的第二方面的反应器用于提供温度在1500℃至1750℃之间且co/co2比≥15的气体的用途,其中,将气体引入冶金反应器中以还原熔化。气体的温度优选在1600℃至1750℃之间。此外提供,可以将气体引入冶金反应器中以还原熔化。引入冶金反应器以进行还原熔化的气体的co/co2气体体积比可以大于10或甚至大于15。例如,co/co2气体体积比在10至1000之间,优选地在15至10000之间,并且特别优选地在15至107之间(基本上不含co2)。
根据本发明的第四方面,提供了一种系统,该系统包括根据本发明的第二方面的反应器和与所述反应器连接的以进行还原熔化的冶金反应器。在此可以设想,反应器以上述方法运行,从而在反应器和用于还原熔化的冶金反应器之间的区域(连接部分)中的co/co2气体体积比大于10或甚至大于15。例如,co/co2气体体积比在10至1000之间,优选地在15至10000之间,并且特别优选地在15至107之间(基本上不含co2)。
用于还原熔化的冶金反应器可以是能够由矿石还原金属的任何反应器或高炉(blastfurnace)。
根据本发明的第五方面,提供了根据本发明的第二方面的反应器的用途,其用于向熔化含金属原料的方法提供高温气体。融化含金属原料的方法可以是荷兰优先创始专利申请2023109号中描述的工艺,其名为“融化含金属原料的方法”,以非洲彩虹矿业有限公司(africanrainbowmineralslimited)的名义提出。
根据本发明的第六方面,提供了根据本发明第二方面的反应器在根据本发明第一方面的方法中的用途。
参考附图,从本发明的以下描述中得出其他优点,细节和改进。
附图的简要说明
图1示出了根据本发明的反应器的简化截面图。
图2示出了根据本发明的反应器的简化截面图的剖视图,该反应器具有两个内衬部分以及凸舌-凹槽连接。
图3示出了周向水冷式控制台的透视图,其可被放置在两个内衬部分之间并且在凸舌-凹槽连接的区域中。
具体实施方式
这些图中相同编号的元件是相同的或实现相同的功能。如果功能相同,则先前讨论的元件不必在后面的图中进行讨论。
在下文中,图1描述了根据本发明的基本圆柱形的反应器100。结合对反应器细节的说明,还详细说明了原料处理和产生气体出口处高于1500℃的气体期间的工艺步骤。
通过使用其他原料,对反应器和/或方法的修改可能是有用的。通常,还可以组合不同的原料(例如低级煤),例如通过在气化/熔化无机原料期间添加具有较高能量值的原料(例如有机废物、受污染的废木料、汽车轮胎等)。
图1中所示的反应器100具有三个部分。部分内衬的并流部分110,内衬耐火材料的气体出口部分120和内衬耐火材料的逆流部分130。并流部分110,气体出口部分120和逆流部分130基本上彼此同中心地布置(由基本上穿过反应器中心的垂直点划线表示)。如图所示,在并流部分110和逆流部分130中显示了几个周向水冷式控制台400。周向水冷式控制台400布置在至少两个耐火内衬部分之间,该耐火内衬部分在凸舌-凹槽连接(未示出)的区域中彼此叠置(未示出)。在并流部分中,布置了无内衬的充气区111、内衬耐火材料的上部氧化区116和内衬耐火材料的上部还原区118。充气区111包括带有闸门112的进料区,由此原料例如废物、水、汽车轮胎、添加剂或其他原料,通过进料区从上方进料到反应器中。固体的物流从上到下以虚线箭头显示。在热解区114的下方布置有下游缓冲区,用于缓冲和预干燥原料体积,下游缓冲区与缓冲区的底部邻接,从而产生横截面扩大。在热解区114,排出锥斗可以由进料形成(由斜虚线表示;在114和119之间)。因此,热解可发生在床的表面上。热解区也可以用燃烧气体或任何其他低氧气体(例如n2或co2)变成惰性的,因此移动到闸门112的可燃气体安全燃烧。在热解区114的下方有一个内衬的中间区115,该中间区配置用于最终干燥和完全热解。内衬耐火材料的上部氧化区116与内衬耐火材料的中间区115邻接,其中在上部氧化区116,风口在多个平面中沿圆周布置,如图所示。通过风口117供给至少1000℃的热氧气和/或热空气,这将使温度升高到1800℃以上和最高4000℃,从而所有物质均转化为无机气体、液态金属、焦炭、碳和/或矿渣。在与内衬的上部氧化区116邻接并基本上布置在随后的内衬的气体出口部分120上方的内衬耐火材料的上部还原区118中,发生热能到化学能的吸热转化。同时,在此产生从充气区到内衬耐火材料的上部还原区118从顶部到底部产生的气体并流(由上至下的虚线箭头表示),并引入内衬耐火材料的气体出口部分120。
如图所示,内衬耐火材料的气体出口部分120连接到内衬耐火材料的上部还原区118,从而产生横截面扩大。产生的气体-大约与床成横流-通过至少一个气体出口121在气体出口部分120排放(由从左到右的虚线箭头显示)。例如,可以提供四个或更多的沿圆周径向分布(未示出)的气体出口121,使得在并流部分和逆流部分中产生的气体可以在横流中径向转移。排出的气体的co/co2气体体积比为10至1000,优选为15至10000,特别优选为15至107(基本上不含co2)。
气体出口部分的下方是内衬耐火材料的锥形下部还原区138。在内衬耐火材料的锥形下部还原区138中,也发生了热能到化学能的转化。
如图所示,在内衬的锥形下部还原区下方有一个内衬的锥形下部氧化区136,其中布置有至少一个风口137和开孔131。风口137引入至少1000℃的热空气和/或热氧气以氧化剩余的焦化材料并防止熔体固化。金属熔体和炉渣熔体的收集和排放在开孔131中进行。
在锥形下部氧化区和锥形下部还原区中产生的气体也与固体流逆流流过床层(由从底部到顶部的虚线箭头表示)到内衬耐火材料的气体出口部分120,在这里通过至少一个气体出口121排出。
根据本发明的反应器可以具有以下内部体积,例如:
表1
图2示出了根据本发明的反应器的内衬耐火材料的中间区115的简化截面图的剖视图,该中间区具有两个内衬部分200、300和周向的凸舌-凹槽连接。如内衬的中间区115的示例所示,其中,每个内衬部分相互还可以具有至少两个带有周向的凸舌-凹槽连接的内衬部分200、300,则反应器的该内衬部分具有至少两个彼此叠置的内衬部分200、300。至少两个内衬部分200、300中的每一个包括至少一个内部耐火内衬202、302和包围内侧耐火内衬的外部内衬203、303。可以想到的是,内部耐火内衬202、302是由烧结砖制成的内衬或整体(例如铸造)内衬。如图2还显示,在彼此叠置的内衬部分200、300之间形成凸舌-凹槽连接,其中一个衬里部分200在朝向反应器内部的一侧上具有凹槽201,并且另一个衬里部分300在朝向反应器内部的一侧上具有凸舌301。如图所示,可以提供,上部内衬部分200具有凹槽201,而下部内衬部分300具有凸舌301。此外,凸舌-凹槽连接在凹槽201和凸舌301之间具有(垂直的)温度相关的间隙开口400。如进一步所示,周向水冷式控制台400布置在至少两个彼此叠置的内衬部分200、300之间。
在图3的透视图中示出了用于在反应器的高加热和冷却期间保持砖衬和稳定砖衬的周向水冷控制台400。该周向水冷式控制台400是通过弯曲具有正方形或矩形横截面的中空圆柱管而无焊缝地制造的,并且由碳钢制成。如图所示,可以通过连接法兰401将冷却水供应到水冷控制台400和从水冷控制台400中排出。
本文用于企业家、创业者技术爱好者查询,结果仅供参考。