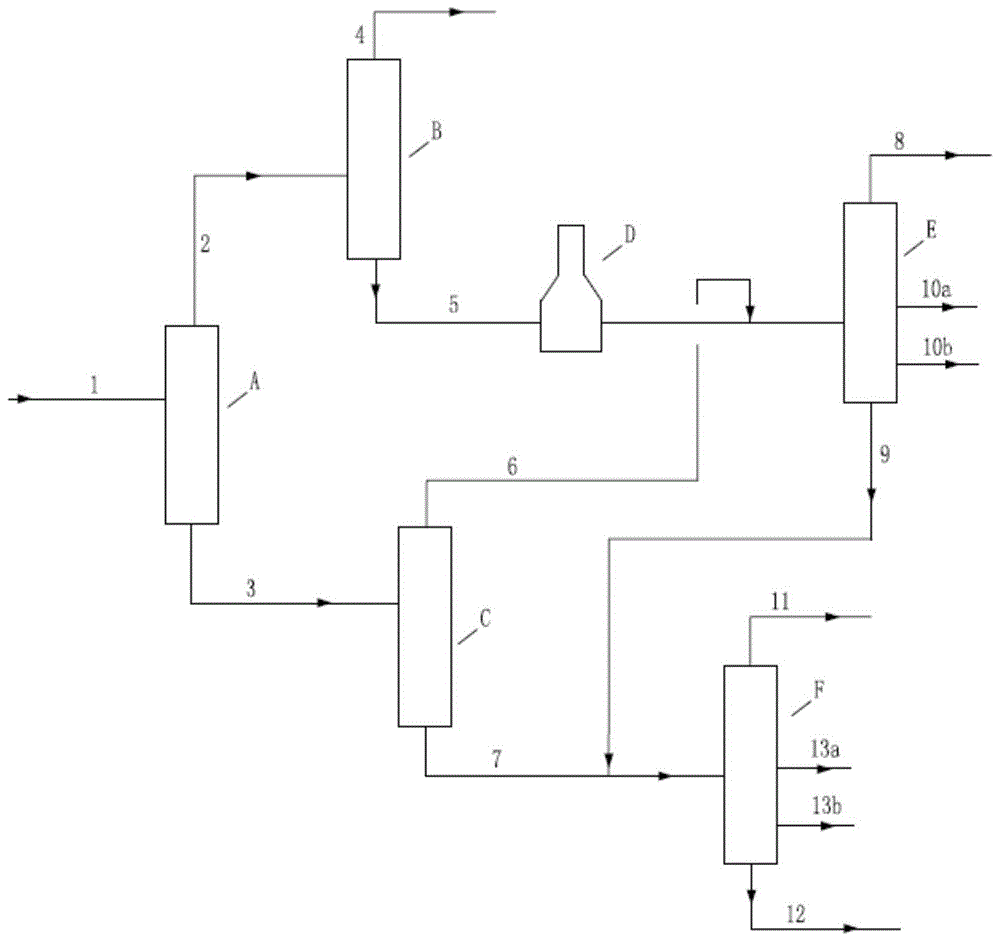
本发明属于化工领域,更进一步涉及了一种重油/渣油改质技术领域,具体地,涉及了一种浆态床加氢裂化反应产物的分离方法及分离系统。
背景技术:
中国一直严重依赖原油进口,进口重质原油或高硫石油是大势所趋,而重油所产生的渣油处理是世界难题。目前国内每年渣油加工处理约1~2亿吨,采用传统延迟焦化技术的收率大约60~70%左右,采用高压沸腾床加氢技术其收率大约60-75%左右,且延迟焦化技术在国家日益严格的环保要求下,可预期的前景黯淡;固定床渣油加氢不仅受制于原料杂质的限制,即使采用最先进的催化剂与工艺流程技术其操作周期无法突破22个月,无法与三年或者四年的检修周期相匹配;而沸腾床渣油加氢由于无法保证产品中沥青质的稳定性,分馏系统易出现堵塞,进而影响装置的稳定操作,使转化率无法逾越75~80%的天花板。
浆态床临氢热裂化工艺对所加工原料中杂质的含量几乎没有限制,甚至可以加工沥青和油砂,浆态床加氢裂化工艺由于转化率高,可以达到90~95%以上,在设备条件允许的前提下几乎无装置操作周期的限制,无操作初、末期的区别,因而被视为对于劣质重、渣油轻质化的一条比较有效的途径,也是替代现有焦化装置,大幅度提高全厂原油加工灵活性和提高全厂轻油收率的重要技术手段。
浆态床加氢裂化反应遵循自由基的反应机理,在氢气与催化剂的氛围下,合理控制反应条件可以有效抑制反应结焦。催化剂及催化剂的活性组分、脱金属反应生成的金属硫化物、反应生成的微量焦等固态物质富集于浆态床加氢裂化的未转化油中,混合后形成浆态床加氢裂化反应浆液,浆液随反应产物进入后续的分离与分馏系统中。浆液中的固体物质极易阻塞浆液流经工艺路径上的设备、管道与阀门,在没有充分优化浆液工艺路径的前提下,若出现浆液污染了与重油组分分离、分馏过程中不相关系统的情况,将会大幅降低装置的安全平稳性并显著增加装置的投资费用及设计难度。浆态床加氢裂化反应所添加的催化剂以及最终形成的催化剂活性组分,如二硫化钼,在高温条件下会发生升华现象,当二硫化钼进一步凝华在设备、管道、阀门上会堵塞系统,将对装置的稳定、安全的运行产生不利的影响。有鉴于此,对于浆态床加氢裂化装置不宜沿用传统加氢装置的分离-常压-减压顺序的分离与分馏流程,而提出一种新的适用于浆态床加氢裂化装置的工艺是非常有必要的。
技术实现要素:
本发明的目的是提供一种防体系间污染、防阻塞的浆态床加氢裂化装置的分离与分馏系统及方法,用以防止浆态床加氢裂化反应产物轻、重油体系间不必要的污染,防止浆态床催化剂活性体高温升华低温凝华现象导致的阻塞问题,进而增强分离及分馏系统的长周期操作的稳定性,另外,还可以通过控制重油组分进入减压塔的温度进而优化减压塔系统的热量平衡对降低装置的能耗具有积极作用。
为了实现上述目的,本发明一方面提供一种浆态床加氢裂化反应产物的分离方法,该分离方法包括:
将来自浆态床加氢裂化反应装置的反应产物送至轻/重组分分离系统,分离出的气相轻油经降温及任选的减压后送至轻油气液分离系统,分离出的液相重油经减压及任选的降温后送至重油气液分离系统;
气相轻油经轻油气液分离系统再次进行分离,分离出的气相送至下游装置,分离出的液相经加热后送至常压塔,常压塔塔顶气相送至下游装置,塔底液相送至减压塔,侧线采出轻油;
液相重油经重油气液分离系统再次进行分离,分离出的气相送至常压塔,分离出的液相送至减压塔,减压塔塔顶气相送至下游装置,塔底浆液送至下游装置,侧线采出重油。
本发明公开的分离方法中待分离的原料来自浆态床加氢裂化反应的反应产物,该反应优选采用天然矿物或工业废渣等固体粉末催化剂、有机金属催化剂或无机化合物作为催化剂,且催化剂的活性组分为二硫化钼。由于活性组分二硫化钼在高温条件下容易发生升华、在低温条件下发生凝华现象而堵塞减压系统,本发明中优选不设置减压炉。
本发明公开的分离方法适用范围广泛,浆态床加氢裂化反应的反应原料包括但不限于减压渣油、脱油沥青、乙烯裂解焦油、煤焦油、超稠原油(稠油粘度大于50000mpa·s)以及炼油厂污泥中的至少一种。将上述反应产物通过轻/重组分分离系统分离,分离出的气相轻烃包括轻石脑油、重石脑油、航煤以及柴油中的至少一种;分离出的液相重烃包括轻蜡油、重蜡油、未转化油以及固体颗粒,其中,固体颗粒包括但不限于催化剂、脱金属反应生成的金属硫化物和反应生成的微量焦等。优选地,所述轻/重组分分离系统的操作压力为8~20mpa,进一步优选为10~15.5mpa,操作温度为350~450℃,进一步优选为390~420℃。
本发明将轻/重组分分离系统分离出的气相轻油经降温减压后送至轻油气液分离系统,气相轻油包括主要的轻石脑油、重石脑油、航煤以及柴油中至少一种,还包括氢气、甲烷、乙烷、丙烷、丁烷、乙烯、丙烯、丁烯、煤油中的至少一种以及微量的蜡油;优选地,所述轻油气液分离系统的操作压力为0.1~20mpa,进一步优选为2~3mpa,操作温度为50~350℃,进一步优选为50~100℃;分离出的液相重油经减压后送至重油气液分离系统,液相重油包括主要的轻蜡油、重蜡油、未转化油以及固体颗粒中的至少一种,其中,未转化油为浆态床加氢裂化反应的反应原料,即减压渣油、脱油沥青、乙烯裂解焦油、煤焦油、超稠原油以及炼油厂污泥等;固体颗粒包括但不限于催化剂、脱金属反应生成的金属硫化物和反应生成的微量焦,液相重油还包括微量的氢气、甲烷、乙烷、丙烷、丁烷、乙烯、丙烯、丁烯、石脑油、煤油,重柴油;优选地,所述重油气液分离系统的操作压力为0.1~8mpa,进一步优选为0.1~0.5mpa,操作温度为350~450℃,进一步优选为350~400℃。
本发明中,从轻/重组分分离系统分离出的气相轻油经轻油气液分离系统再次进行分离,分离出的气相可以送至脱硫系统、循环氢系统、氢气回收系统等下游装置进行处理,分离出的液相经常压炉加热后送至常压塔,优选地,所述常压塔的操作温度为250~350℃。常压塔塔顶采出气相送至下游装置进一步回收轻烃组分,塔底液相主要为蜡油,其次为重柴油送至减压塔,侧线采出轻油,采出轻油优选为燃料气、液化气、石脑油和柴油中的至少一种。
本发明中,从轻/重组分分离系统分离出的液相重油经减压后送至重油气液分离系统继续进行分离,分离出的气相送至常压塔,分离出的液相送至减压塔,减压塔塔顶气相送至下游装置,塔底浆液包括蜡油、未转化油、二硫化钼微粒、金属硫化物、焦中的至少一种,送至尾渣汽化装置、焦化装置、cfb锅炉等下游装置进行处理,侧线采出重油,采出重油优选为燃料气、重柴油、轻蜡油和重蜡油中的至少一种。
本发明中,为了进一步优化减压塔系统的热量平衡,降低装置能耗,优选地,所述减压塔的操作温度为350~400℃,进一步优选为365~400℃。
本发明另一方面提供一种浆态床加氢裂化反应产物的分离系统,所述分离系统包括轻/重组分分离系统、轻油气液分离系统、重油气液分离系统、加热装置、换热器、常压塔以及减压塔;其中,
浆态床加氢裂化反应装置的反应产物出口管线与所述轻/重组分分离系统连接,
所述轻/重组分分离系统分别与重油气液分离系统以及轻油气液分离系统连接,所述轻/重组分分离系统与轻油气液分离系统连接的管线上设置有换热装置;所述轻/重组分分离系统与重油气液分离系统连接的管线上设置有减压装置;
所述轻油气液分离系统气相采出管线与下游装置连接,液相采出管线依次与加热装置、常压塔连接;
所述重油气液分离系统气相采出管线与常压塔连接,液相采出管线与减压塔连接;所述常压塔塔顶与下游装置连接,塔底与减压塔连接,侧线设有轻油采出管线;
所述减压塔塔顶与下游装置连接,塔底与下游装置连接,侧线设有重油采出管线。
本发明中涉及的常压塔即为本领域技术人员惯用的常压塔系统,包括侧线塔、侧线塔底泵、塔顶回流罐、塔顶冷却器、塔顶回流泵、塔顶产品泵,常压塔底泵等。减压塔的设置也如上述常压塔,包括侧线塔、侧线塔底泵、侧线抽出泵、塔顶抽真空系统、减压塔底泵等一些常规设置。
根据本发明,优选地,所述轻油气液分离系统气相采出管线与脱硫系统、循环氢系统和氢气回收系统中的至少一种连接;所述减压塔塔底与尾渣汽化装置、焦化装置、cfb锅炉中的至少一种连接。
根据本发明,优选地,所述加热装置为常压炉。
本发明对轻/重组分分离系统没有特别的限制,可以为热高压分离器、温高压分离器、热中压分离器、温中压分离器等任一种可实现轻/重油组分的分离器中的至少一种,本领域技术人员根据常规技术进行选择即可。
本发明中轻油气液分离系统以及重油气液分离系统的选择也同样没有限制,轻油气液分离系统可以为包括温高压分离器、冷高压分离器、温中压分离器、冷中压分离器、温低压分离器、冷低压分离器中的至少一种的分离器;重油气液分离系统可以为包括热中压分离器、温中压分离器、热低压分离器、温低压分离器中的至少一种的分离器。
根据本发明,优选地,所述分离系统不包括减压炉。
本发明通过充分考虑浆态床反应的特点,利用各级平衡相态将反应产物分离为轻油组分与重油组分,将轻油组分送入常压塔系统处理,重油组分送入减压塔系统处理,避免重油组分及含有催化剂、金属硫化物、焦等固体物质污染轻油及常压塔体系,将重组分、减压与轻组分、常压两类系统在工艺流程上进行隔离,最后含有催化剂、金属硫化物、焦等的固体物质随减压塔塔底浆液一同排出分离系统。同时,本发明减压系统可以不设置减压炉,以避免采用活性组分为二硫化钼的催化剂在高温条件下发生升华、在低温条件下发生凝华现象而堵塞减压系统。本发明将重油组分的进料温度控制在合理的范围还可以优化减压塔系统的热量平衡。与现有技术相比,本发明提供的浆态床加氢裂化反应产物的分离方法及分离系统不仅可以解决困扰浆态床技术大范围推广需要面对的长周期、稳定操作的问题,还能降低装置能耗。
本发明的其它特征和优点将在随后具体实施方式部分予以详细说明。
附图说明
通过结合附图对本发明示例性实施方式进行更详细的描述,本发明的上述以及其它目的、特征和优势将变得更加明显,其中,在本发明示例性实施方式中,相同的参考标号通常代表相同部件。
图1示出了本发明一个具体实施例的浆态床加氢裂化反应产物的分离流程图。
附图标记说明:
a、轻/重组分分离系统;b、轻油气液分离系统;c、重油气液分离系统;d、常压炉;e、常压塔;f、减压塔;
1、来自浆态床加氢裂化反应装置的反应产物;2、气相轻油;3、液相重油;4、轻油分离系统分离出的气相;5、轻油分离系统分离出的液相;6、重油分离系统分离出的气相;7、重油分离系统分离出的液相;8、常压塔塔顶气相;9、常压塔塔底液相;10a、轻油ⅰ;10b、轻油ⅱ;11、减压塔塔顶气相;12、减压塔塔底浆液;13a、重油ⅰ;13b、重油ⅱ。
具体实施方式
下面将更详细地描述本发明的优选实施方式。虽然以下描述了本发明的优选实施方式,然而应该理解,可以以各种形式实现本发明而不应被这里阐述的实施方式所限制。
实施例
一种浆态床加氢裂化反应产物的分离系统,包括轻/重组分分离系统a、轻油气液分离系统b、重油气液分离系统c、常压炉d、换热器、常压塔e以及减压塔f;其中,
浆态床加氢裂化反应装置的反应产物出口管线与轻/重组分分离系统a连接,轻/重组分分离系统a分别与重油气液分离系统c以及轻油气液分离系统b连接,轻/重组分分离系统a与轻油气液分离系统b连接的管线上设置有换热装置;轻/重组分分离系统a与重油气液分离系统c连接的管线上设置有减压装置;轻油气液分离系统b气相采出管线与脱硫系统连接,液相采出管线依次与常压炉d、常压塔e连接;重油气液分离系统c气相采出管线与常压塔e连接,液相采出管线与减压塔f连接;常压塔e塔顶与轻烃回收系统连接,塔底与减压塔f连接,侧线设有两支轻油采出管线;减压塔f塔顶与火炬系统连接,塔底与尾渣汽化装置连接,侧线设有两支重油采出管线。该分离系统不设置减压炉。
采用上述分离系统进行浆态床加氢裂化反应装置的反应产物分离,分离流程如图1所示,该分离方法包括:
将来自浆态床加氢裂化反应装置的反应产物送至轻/重组分分离系统a,轻/重组分分离系统a的操作压力为8~20mpa,操作温度为350~450℃,分离出的气相轻油经降温减压后送至轻油气液分离系统b,分离出的液相重油经减压后送至重油气液分离系统c;
气相轻油经轻油气液分离系统b再次进行分离,轻油气液分离系统b的操作压力为0.1~20mpa,操作温度为50~350℃;分离出的气相送至脱硫系统,分离出的液相经加热后送至常压塔,常压塔的操作温度为250~350℃,常压塔塔顶气相送至轻烃回收系统进一步回收轻烃,塔底液相送至减压塔f,侧线采出石脑油以及柴油;
液相重油经重油气液分离系统再次进行分离,重油气液分离系统的操作压力为0.1~8mpa,操作温度为350~450℃;分离出的气相送至常压塔,分离出的液相送至减压塔,减压塔的操作温度为350~400℃,减压塔塔顶气相送至火炬,塔底浆液送至尾渣汽化装置,侧线采出重柴油和蜡油。
以上已经描述了本发明的各实施例,上述说明是示例性的,并非穷尽性的,并且也不限于所披露的各实施例。在不偏离所说明的各实施例的范围和精神的情况下,对于本技术领域的普通技术人员来说许多修改和变更都是显而易见的。
本文用于企业家、创业者技术爱好者查询,结果仅供参考。