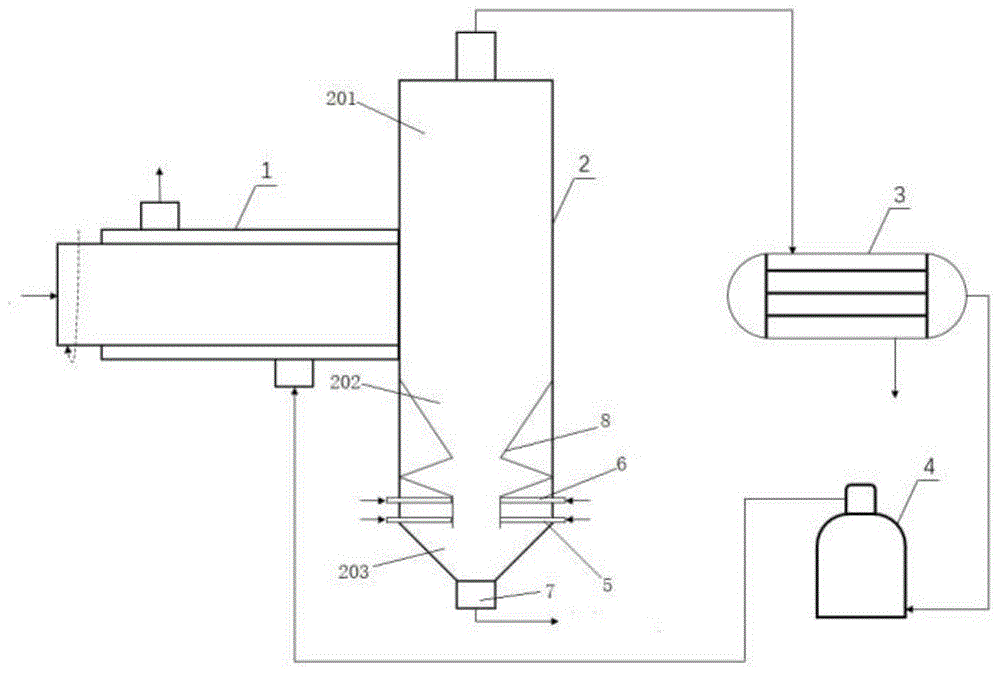
本实用新型属于废旧轮胎资源化利用技术领域,尤其涉及一种废旧轮胎改性热解制备高品质热解油热解炭装置。
背景技术:
随着全球汽车保有量的增加,每年废旧轮胎产生量稳步增加,并且长期保持在较高的水平。在我国,仅2015年全国废弃轮胎的产生量就已经达到3.3亿条左右,总重约合1200万吨,预计到2020年,我国废弃轮胎产生量将达到2000万吨。废旧轮胎主要由橡胶、炭黑、磺化剂等化学添加剂以及钢丝和尼龙材料等制成,其具有随意丢弃环境污染大,回收价值高的特点。因此,废旧轮胎的资源化利用是废旧轮胎处置的重要手段。
目前,我国废旧轮胎主要采取制再生胶粉的方式进行回用。但是由于再生胶粉的质量通常较低以及合成橡胶产品对再生胶粉市场的挤占,由废旧轮胎制再生胶粉的处置路线已不能满足每年大量产生的废旧轮胎的处置需求。在此背景下,废旧轮胎热解回收热解油和热解炭技术在近年逐渐兴起。此工艺的优点在于热解处置效率高,可以满足废旧轮胎的处置需求;热解后的产品市场需求量较大,因此热解项目具有较好的市场潜力。
目前,热解工艺所面临的主要问题是热解产品的品势还待提升。比如,由于橡胶轮胎的化学组成较为复杂,经热解后收集的热解油成棕黑色,并且存在着密度偏大(0.95-0.97g·cm-3),热值偏小(41-45mj·kg-1),闪电较低的缺点,从而大大降低了气市场价值。对于热解炭,通常可作为炭黑产品出售。但是在传统的热解工艺中,为保证热解油的产率,热解温度通常不能过高,一般为(400-500℃),从而导致热解炭中仍然可能含油较高的含量的可挥发分,不能满足热解炭再利用的要求。可见,废旧轮胎热解是目前废旧轮胎资源化利用的重要手段,但此工艺仍然存在着技术上的难题,限制了此技术在市场上的大规模应用。
技术实现要素:
本实用新型的主要目的在于提供一种废旧轮胎改性热解制备高品质热解油热解炭装置,旨在针对热解气及热解炭的不同改性工况需求,同时实现废旧轮胎的热解及热解气、热解炭的改性。
为实现上述目的,本申请采用如下技术方案:
一种废旧轮胎改性热解制备高品质热解油热解炭装置,包括热解炉、上吸式固定床气化炉和冷凝器,所述上吸式固定床气化炉从上到下依次分为气相改性区、气化反应区和积灰区;
所述气相改性区的顶部设有与所述热解炉的出料端对接的进料口,底部设有空气进口和水蒸气进口;所述气化反应区的顶部设有与所述冷凝器的热解气进口对接的热解气出口,所述积灰区的底部设有排渣口。
具体的,所述热解炉采用回转窑热解炉。
具体的,还包括燃烧室,所述冷凝器的热解气出口与所述燃烧室连通,所述燃烧室的烟气出口与所述回转窑热解炉的热气进口连接。
具体的,所述回转窑热解炉倾斜设置,且出料端位于低端。
具体的,所述积灰区呈倒锥形。
具体的,所述热解炉热解温度控制在400-500℃。
在本实用新型装置为两段式设计,分为前段热解段和后段气化改性段。热解段采用回转窑式热解炉,经热解后,废旧轮胎裂解成为含油大量可燃物的气相产物以及以热解炭黑为主的固相产物。此时热解气和热解炭的温度仍然较高,约为300-400℃。气相中可燃物组分较为复杂,此时对气相产物进行直接冷凝会产生大量的重质焦油;在热解过程中,固相与气相充分接触,导致固相产物中仍吸附有大量有机物,不能完全满足热解炭的对加热减量、ctab吸附比表面积等指标的要求。
经过热阶段后,热解气及热解炭送入后段气化改性段,后段气化改性段采用上吸式固定床气化炉,轮胎热解炭向下落入气化反应区,并在狭口中汇集堆积形成气化炉料层,气化炉料层上层高度不超过热解炉的出料端。在气化反应区水蒸气与热解炭发生气化反应,高分子有机物被气化成为低分子量有机物,以合成气的形式从热解炭中释放,从而提高热解炭的比表面积,降低了热解炭的加热减量率,从而大大提高了固相产品的品质,可以作为热解炭黑或吸附剂出售。与此同时,高分子有机物与水蒸气反应伴随有氢气的产生,从而使得合成气富含氢气。合成气向上运动,与热解气在气化炉上层的气相改性区完全混合。此时,混合气温度可达600℃。在氢气氛围下,含有大量高分子量有机气组分的热解气进一步裂解并与氢气发生反应。首先,在较高温度下,高分子量有机气体发生裂解生成较小分子量产物,从而减少后续冷凝段重油的产生量,提高轻质油的产生量。同时,原热解气中氧、有机硫及有机氮的含量较高,经过冷凝后会降低热解油的热值,提高热解油中杂质元素的量,从而降低了热解油的油品。在氢气氛围下,含氧、含氮、含硫官能团可与氢气发生反应,从而转移到不凝气中,从而大大提高了热解油品质。经改性后,热解炭黑连续从气化炉下端积灰区排出,经冷却后可作为热解炭产品出售。热解气连续从气化炉上端排出。经冷凝后,可凝组分以热解油的形式冷凝下来,可作为热解油出售;不凝气送入燃烧室焚烧,用于前端热解段供热。
本实用新型创新地将热解后产物直接进入气化炉,其中气化反应区温度较高(可达900℃),可以实现对热解炭的改性;而气相产物直接进入气相改性区。气相改性区主要含有由热阶段来的高重油含量的热解气,以及来自气化反应区的高氢气含量的气化合成气,在气相改性区较高的温度下(约600℃),热解气与氢气还原氛围下实现了脱硫、脱氧、脱氮,并且继续裂解成分子量较小的物质,从而大大降低低品质重油的产量,增加了高品质轻油的产量。并且,由于热解炭、热解气没有经过冷却直接进入气相改性区,其温度仍然较高,可大大节约改性的能耗。综上,本申请可以实现轮胎直接热解、改性,从而大大提高热解产品的品质,提高废旧轮胎热解项目的经济效益,促进废旧轮胎热解资源化项目的普及开展,从而解决我国废旧轮胎处置难的问题。
与现有技术相比,本实用新型具有的有益效果在于:
本实用新型针对热解气及热解炭的不同改性工况需求,同时实现废旧轮胎的热解及热解气、热解炭的改性,整体装置结构紧凑,能效高,无需额外采购改性剂且改性效果明显,可以大大提高热解产物的品质,解决了废旧轮胎热解产品品质低的痛点。
附图说明
为了更清楚地说明本实用新型实施例中的技术方案,下面将对实施例描述中所需要使用的附图作简单地介绍,显而易见地,下面描述中的附图仅仅是本实用新型的一些实施例,对于本领域普通技术人员来讲,在不付出创造性劳动的前提下,还可以根据这些附图获得其他的附图。
图1是本实用新型实施例的结构示意图;
其中:1-热解炉;2-上吸式固定床气化炉;201-气相改性区;202-气化反应区;203-积灰区;3-冷凝器;4-燃烧室;5-空气进口;6-水蒸气进口;7-排渣口;8-狭口。
具体实施方式
下面将结合本实用新型实施例中的附图,对本实用新型实施例中的技术方案进行清楚、完整地描述,显然,所描述的实施例仅仅是本实用新型一部分实施例,而不是全部的实施例。基于本实用新型中的实施例,本领域普通技术人员在没有作出创造性劳动前提下所获得的所有其他实施例,都属于本实用新型保护的范围。
参见图1,一种废旧轮胎改性热解制备高品质热解油热解炭装置,包括热解炉1、上吸式固定床气化炉2、冷凝器3和燃烧室4,上吸式固定床气化炉2从上到下依次分为气相改性区201、气化反应区202、积灰区203。
参见图1,具体的,气相改性区201的顶部设有与热解炉1的出料端对接的进料口,底部设有空气进口5和水蒸气进口6,并且水蒸气进口6位于空气进口5的上方,气化反应区202的顶部与冷凝器3的热解气进口连通,积灰区203的底部设有排渣口7,冷凝器3的热解气出口与燃烧室4连通,燃烧室4的烟气出口与热解炉1的热气进口连接。
可以理解的是,在实际应用中,热解炉1采用回转窑热解炉,回转窑热解炉倾斜设置,且出料端位于低端,积灰区203呈倒锥形,气化反应区202中设有形成有上端大下端小的狭口8,从而便于物料的汇聚。
参见图1,本实施例的工作过程如下:加热空气从热解炉1下部通入,经过换热后从热解炉1上部排出。通过控制加热气的通入量,将热解炉1热解温度控制在400-500℃范围内。物料由进料端进入回转窑热解炉的回转窑滚筒内,通过滚筒的小角度倾角以及不间断的旋转,推动物料向前移动。在向前移动的过程中,原料中有机物逐渐被分解成气相产物以及残留的热解炭,至于回转窑热解炉的具体结构,均为现有技术,在此不再赘述。
废旧轮胎片经破碎、抽除钢丝后置于进料机构内,待进料,先对回转窑热解炉进行预热,待温度温度维持在工艺设计所需的400℃-500℃时,开始进料。与此同时,上吸式固定床气化炉2也已预先填充有上次气化处理的热解炭床层,并点火,从空气进口5向气化反应区202通入空气,直至形成稳定高温层后,水蒸气经水蒸气进口6通入气化反应区202。水蒸气通入量应逐渐增加,直至热解炭的进料速率的50%。设备启动初期,热解炉1供热由焚烧炉中燃料的焚烧获得。等到热解改性稳定进行时,冷凝器3产生的不凝可燃气经燃烧室4燃烧后,为回转窑热解炉1供热,可满足整个系统运行的能耗需求,此时无需额外消耗燃料,运行过程能耗低。至此,热阶段和气化改性段均已实现稳定运行,此时每小时经由热解段送入气化改性段的热解炭的量与气化改性段处置的热解炭的量维持平衡,使得气化改性段热阶段的料层高度维持稳定。此时,气化改性段中气化反应区的温度控制在900℃左右;热解气与合成气混合区的气相温度约为600℃。通过排料机构实现对热解炭产品的连续排料。热解炭冷却后,可作为产品出售。改性后的热解气经冷凝器3冷凝,高品质热解油被冷凝下来,收集作为油品出售。不凝气持续通入燃烧室4燃烧,燃烧后产生的高温烟气作为热源对热解炉1进行供热,经换热后的烟气可经烟气处理系统处理后排空。由于高分子量的重质可燃气已经在冷凝段被冷凝下来,因此,焚烧室焚烧完全,过程中不会产生黑烟。后续的烟气处理系统主要需要对烟气进行除酸处理。停机过程为:先停止回转窑热解炉1进料,待热解完成后停止热解炉1供热。吸式固定床气化炉2维持排料速率,直至炉体中物料排空,停止水蒸气通入,维持空气通入吹扫,直至炉体内无可燃气残留,后方可停止空气通入,关闭相关阀门,关闭系统。
上述实施例仅仅是清楚地说明本实用新型所作的举例,而非对实施方式的限定。对于所属领域的普通技术人员来说,在上述说明的基础上还可以做出其它不同形式的变化或变动。这里也无需也无法对所有的实施例予以穷举。而由此所引申出的显而易见的变化或变动仍处于本实用新型的保护范围之中。
本文用于企业家、创业者技术爱好者查询,结果仅供参考。