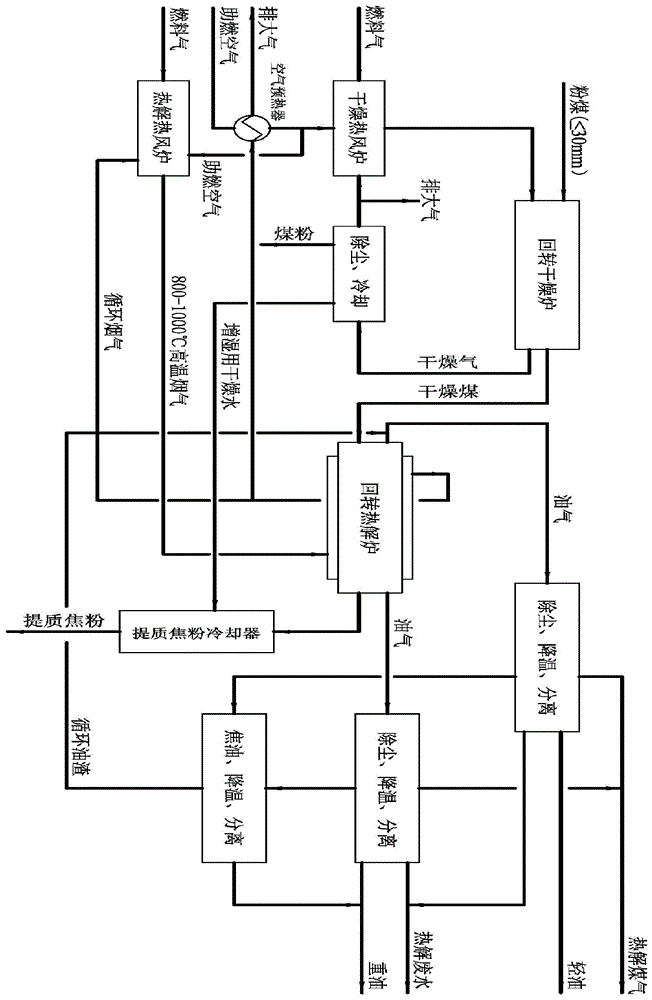
本发明属于新型煤化工技术,特别适用于煤炭分质利用领域,具体涉及一种带油渣循环的低阶粉煤回转热解方法。
背景技术:
低阶煤是煤化程度较低的煤,外观一般呈灰黑色至黑色,粉末从棕色到黑色,由有光泽的和无光泽的部分互相集合合成层状,具明显的条带状、凸镜状构造。根据其挥发分含量、胶质层厚度或工艺性质,可分为长焰煤、气煤、肥煤、焦煤、贫煤、瘦煤等。
低阶煤占煤炭总量的50%以上,通常具有高氧含量、高水分、稳定性差及热值低等特点,因此该类煤难以作为大规模的工业气化原料,更多的仅仅是用于局部地区的动力燃料。低阶煤热解提质技术是一种低阶煤高效利用的有效途径,不但有利于弥补部分石油天然气资源缺口,而且能提高低阶煤的利用水平,促进经济的发展。
当前对低阶煤热解提质技术的研究较多,但多数热解工艺仍不成熟,尚处于试验或示范阶段,如何提高煤焦油的回收率、降低重油产品中的尘含量是研究的重点。另外,对于常规回转热解工艺,由于采用纯外热式烟气加热方式和湿式除尘工艺,导致回转设备尺寸较大、油渣(危废无法利用)产量较多,因此如何实现设备规格的减量化、降低油渣产量也是回转热解工艺关注的重点。
技术实现要素:
因此,本发明要解决的技术问题在于克服现有技术中低阶煤热解工艺中产品煤焦油尘含量有待进一步降低、油渣没有实现资源化利用等缺陷,从而提供一种带油渣循环的低阶粉煤回转热解方法。
本发明采用带油渣循环的回转反应炉,实现了油渣的资源化利用,提高了焦油的总回收率。回转反应炉采用内外热结合式结构,大大提高了单位加热强度,减少了设备投资,经济效益十分显著。
为此,本发明提供如下技术方案:
本发明提供一种带油渣循环的低阶粉煤回转热解方法,包括如下步骤:
a)将粒度≤30mm的低阶粉煤进行加热并除尘,至所述粉煤中85%以上的粒度<0.5mm煤尘被除去,得到干燥煤,所述干燥煤的含水量≤1.0wt%;
b)将上述干燥煤加热至500~700℃发生热解反应,生成提质焦粉和高温油气,将所述高温油气从热解炉的炉头和炉尾同时引出,其中,从炉头引出的高温油气经轻油湿式除尘、降温、分离后得到热解煤气i、轻油产品、热解废水i和含尘焦油i;从炉尾引出的高温油气经干式除尘、重油湿式除尘、降温、分离后得到热解煤气ii、重油产品ii、热解废水ii和含尘焦油ii;
c)将所述的含尘焦油i和含尘焦油ii经降温、分离后得到重油产品iii和油渣;所述油渣循环回步骤b)中,洗涤所述炉头产生的高温油气,并与所述干燥煤混合后,一同发生热解反应;
d)步骤b)中所得提质焦粉经冷却降温、增湿后作为产品。
可选的,所述增湿步骤可选择步骤a)中产生的干燥水。
可选的,所述步骤a)在带除尘的回转干燥炉中进行,500-600℃的高温烟气与粒度≤30mm的低阶粉煤并流直接接触,兼具加热和除尘载体,得到干燥煤与干燥气。
可选的,所述步骤b)的热解反应选用的热解炉为内外热结合式回转热解炉。
可选的,在内外热结合式回转热解炉中,所述干燥煤和循环油渣被800-1000℃的高温烟气内外同时双向间接加热至500-700℃,发生热解反应。
可选的,所述内外热结合式回转热解炉内设置一层或多层非圆形加热管,炉外设置全覆盖夹套结构;高温烟气走炉内加热管和炉外夹套。
可选的,所述从炉头引出的高温油气与从炉尾引出的高温油气温度分别为200~500℃和500℃~600℃;通过控制引出的高温油气的温度可以降低油气的流速,从而降低尤其夹带的粉尘量;
所述从炉头引出的高温油气与从炉尾引出的高温油气的体积比为1:0.5-2.0,且炉头导气管内设置至少一层油渣喷淋。
可选的,所述油渣中焦油含量≤40wt%,温度为90-100℃。
可选的,所述轻油湿式除尘出口气体温度80~110℃,重油湿式除尘出口气体温度70~90℃;干式除尘为至少二级旋风分离式除尘。
可选的,所述步骤d)中提质焦粉采用具有立式复合间接换热结构的冷却器进行冷却;
可选的,所述冷却器分为高温段和低温段,所述高温段设置换热盘管,所述低温段设置板式换热元件。
可选的,来自步骤a)的干燥气经除尘、回收干燥水后,70~80%的干燥气送至干燥热风炉经多级低氧燃烧至出口烟气氧含量≤5vol%后,返回至回转干燥炉,剩余部分高点排空;
来自步骤b)内外热结合式回转热解炉出口的高温烟气,80~90%送至热解热风炉经多级低氧燃烧至出口烟气氧含量≤5vol%后,返回至内外热结合式回转热解炉;剩余部分预热助燃空气后高点排空。
具体地,本发明提供的带油渣循环的低阶粉煤回转热解方法,包括下列步骤:
(1)带除尘的回转干燥系统:
将粒度≤30mm的低阶粉煤送至回转干燥炉,炉内通入500~600℃的高温烟气与原料煤并流直接接触,并将原料煤干燥至水含量≤1.0wt%;同时,煤中粒度<0.5mm、85%以上的煤尘被烟气带出至除尘器,经除尘器将煤尘分离下来后,依次经洗涤塔冷却降温、风机加压,大部分(占比70~80%)返回至干燥热风炉,少量高点排空。洗涤塔冷却降温过程中回收的干燥水全部作为降温、增湿用水送至提质焦粉冷却器。
(2)带油渣循环的内外热结合式回转热解系统:
回转干燥系统来0.5~30mm的干燥煤,进入带油渣循环的内外热结合式回转热解炉,被800~1000℃的高温烟气从炉内外同时双向间接加热至500~700℃,发生热解反应,生成提质焦粉和高温油气;高温油气从热解炉炉头和炉尾同时引出,分别经除尘、降温、分离后得到热解煤气、轻油、重油和热解废水。
步骤(2)中热解炉内设置一层或多层非圆形加热管,炉外设置全覆盖夹套结构;加热管和夹套内通入热解热风炉来的800~1000℃高温烟气,作为粉煤热解的热源;热解炉出口的烟气温度450~550℃,大部分返回至热解热风炉低氧燃烧,剩余部分预热助燃空气后排空。
步骤(2)中热解炉夹套内烟气,优选采用与煤逆流换热,也可采用并流、“一进多出”、“多进一出”等方式。
步骤(2)中热解炉炉头导气管中设置一层或多层油渣喷淋。
(3)提质焦粉冷却系统:
热解炉出口的高温提质焦粉温度约550℃,进入提质焦粉冷却器冷却至100℃,然后喷入干燥水降温、增湿后作为产品。其中,提质焦粉冷却器为立式复合间接换热结构,分为高温段和低温段:高温段设置换热盘管,低温段设置板式换热元件。
(4)油气回收系统:
热解炉炉头引出的高温油气,喷入循环油渣除尘、降温;然后经轻油湿式除尘、降温至80~110℃,然后经过水冷至40℃、分离后得到热解煤气i、轻油产品和热解废水i。
热解炉炉尾引出的高温油气,经两级旋风干式除尘、重油湿式除尘、降温至70~90℃,然后经过水冷至40℃、分离后得到热解煤气ii、重油产品ii和热解废水ii。
湿式除尘步骤会产生含尘焦油,将其降温至90~100℃,然后经离心分离得到重油产品iii和油渣:重油中尘含量<2.0wt%;油渣中焦油含量≤40wt%,油渣加压后循环至热解炉炉头,发生二次裂解和缩合反应,生成油气和提质焦粉。
热解煤气i和热解煤气混合后送至气柜缓存。
热解废水i和热解废水ii混合后送至污水处理。
本发明技术方案,具有如下优点:
本发明提供的带油渣循环的低阶粉煤回转热解方法,包括如下步骤:a)将粒度≤30mm的低阶粉煤进行加热并除尘,至所述粉煤中85%以上的粒度<0.5mm煤尘被除去,得到干燥煤,所述干燥煤的含水量≤1.0wt%;b)将上述干燥煤加热至500~700℃发生热解反应,生成提质焦粉和高温油气,将所述高温油气从热解炉的炉头和炉尾同时引出,其中,从炉头引出的高温油气经轻油湿式除尘、降温、分离后得到热解煤气i、轻油产品、热解废水i和含尘焦油i;从炉尾引出的高温油气经干式除尘、重油湿式除尘、降温、分离后得到热解煤气ii、重油产品ii、热解废水ii和含尘焦油ii;c)将所述的含尘焦油i和含尘焦油ii经降温、分离后得到重油产品iii和油渣;所述油渣循环回步骤b)中,洗涤所述炉头产生的高温油气,并与所述干燥煤混合后,一同发生热解反应;d)步骤b)中所得提质焦粉经冷却降温、增湿后作为产品。本发明提供的方法通过对热解炉内流场、温度场以及固颗粒运动轨迹的模拟研究,改变了高温油气的引出方式、引出位置和引出温度,实现在热解炉的炉头和炉尾同时分别引出不同组分及尘含量的高温油气,然后根据气体组成特点,采用不同的除尘组合工艺,经过进一步的净化处理可分别得到轻油和重油两种产品,其中轻油可直接作为商品燃料油使用,重油经进一步加氢精制后也可作为商品燃料油,同时能够进一步降低重油产品中的尘含量,其中,重油产品中尘含量≤2.0wt%(常规工艺中重油产品中的尘含量约为5~10wt%)。然后,将含尘焦油中分离出来的油渣循环至热解炉中进行二次反应,一方面避免了废油渣的排放,在解决油渣(属于危废)排放问题的同时,重油产品总收率提高了5%以上,实现油渣的资源化利用并提高了重油总收率。另一方面,将所述得含尘焦油i和含尘焦油ii经降温、分离得到重油产品和油渣,将油渣循环回步骤b)中,洗涤所述炉头产生的高温油气,与高温油气逆流接触,还具有一定的除尘效果,将高温油气中的煤尘粘附到油渣上,进一步降低产品热解煤气和重油产品中的尘含量。另外,油渣与高温油气逆流接触进入热解炉,还能避免直接引入油渣导致的结焦问题。
本发明提供的带油渣循环的低阶粉煤回转热解方法,所述步骤a)在带除尘的回转干燥炉中进行,500-600℃的高温烟气与粒度≤30mm的低阶粉煤并流直接接触,得到干燥煤与干燥气。所用高温烟气兼具加热和除尘作用,烟气与原料并流直接接触,干燥强度高,设备规格小,除掉了煤中85%以上粒度<0.5mm的煤尘,大幅减少了进入油气回收系统的煤尘,确保了在线率。
本发明提供的带油渣循环的低阶粉煤回转热解方法,所述步骤b)的热解反应选用的热解炉为内外热结合式回转热解炉,所述内外热结合式回转热解炉内设置一层或多层非圆形加热管,炉外设置全覆盖夹套结构;高温烟气走炉内加热管和炉外夹套。采用高温烟气从炉内外同时双向间接加热:炉内设置非圆形加热管兼具抄料板作用;炉外设置全覆盖夹套,高温烟气在加热管和夹套内流动为粉煤热解提供热源。该结构单位体积换热面积大,易于实现大型化。
本发明提供的带油渣循环的低阶粉煤回转热解方法,所述步骤d)中提质焦粉采用具有立式复合间接换热结构的冷却器进行冷却;可选的,所述冷却器分为高温段和低温段,所述高温段设置换热盘管,所述低温段设置板式换热元件。采用所述结构的冷却器,使得提质焦粉冷却器中固体物料依靠重力作用进行流动,同时起到辅助低压蒸汽的作用;冷却效果好,占地面积小,分级回收提质焦粉能量,大大节约了整个系统的热量消耗,提高了整个系统的能效。
本发明提供的带油渣循环的低阶粉煤回转热解方法,来自步骤a)的干燥气经除尘、回收干燥水后,70~80%的干燥气送至干燥热风炉经多级低氧燃烧至出口烟气氧含量≤5vol%后,返回至回转干燥炉,剩余部分高点排空;来自步骤b)内外热结合式回转热解炉出口的高温烟气,80~90%送至热解热风炉经多级低氧燃烧至出口烟气氧含量≤5vol%后,返回至内外热结合式回转热解炉;剩余部分预热助燃空气后高点排空。如此能够提高烟气中能量利用效率。
附图说明
为了更清楚地说明本发明具体实施方式或现有技术中的技术方案,下面将对具体实施方式或现有技术描述中所需要使用的附图作简单地介绍,显而易见地,下面描述中的附图是本发明的一些实施方式,对于本领域普通技术人员来讲,在不付出创造性劳动的前提下,还可以根据这些附图获得其他的附图。
图1是本发明实施例1中提供的带油渣循环的低阶粉煤回转热解方法的工艺流程图。
具体实施方式
提供下述实施例是为了更好地进一步理解本发明,并不局限于所述最佳实施方式,不对本发明的内容和保护范围构成限制,任何人在本发明的启示下或是将本发明与其他现有技术的特征进行组合而得出的任何与本发明相同或相近似的产品,均落在本发明的保护范围之内。
实施例中未注明具体实验步骤或条件者,按照本领域内的文献所描述的常规实验步骤的操作或条件即可进行。所用试剂或仪器未注明生产厂商者,均为可以通过市购获得的常规试剂产品。
实施例1
本实施例提供一种带油渣循环的低阶粉煤回转热解方法,其流程图如图1所示,具体包括如下步骤:
将60t/h水含量17.0wt%、粒度<30mm的低阶粉煤连续送至回转干燥炉,从回转干燥炉炉头通入干燥热风炉来的550℃高温烟气(氧含量~2.0vol%),高温烟气兼具加热和除尘作用。在回转干燥炉中,煤被干燥至水含量~0.5wt%,温度~150℃。炉尾排出的干燥煤经排料阀进入热解炉;炉尾排出的干燥气温度~180℃并夹带有少量煤尘,经除尘器脱除掉煤尘、水冷至60℃、引风机加压后,大部分(~80%)返回至干燥热风炉进行低氧燃烧,剩余部分排至大气。
在内外热结合式回转热解炉中,干燥煤在隔绝空气状态下受热发生热解反应,产生提质焦粉和高温油气:炉尾排出的提质焦粉进入提质焦粉冷却器,经高温段、低温段冷却并回收热量后温度为95℃,喷入干燥水继续降温、增湿(水含量8wt%)后作为产品。高温油气同时从炉头和炉尾引出:炉头出口油气温度约450℃,在炉头导气管中喷入循环油渣降温、除尘后,经轻油湿式除尘、冷却至40℃并分液后得到热解煤气i、轻油产品和热解废水i;炉尾出口油气温度约580℃,经两级串联旋风分离器除尘、重油湿式除尘、冷却至40℃并分液后得到热解煤气ii、重油产品ii和热解废水ii。热解煤气i和热解煤气ii均送至气柜中缓存。热解废水i和热解废水ii混合后送至污水处理。轻油湿式除尘和重油湿式除尘底部排出的含尘焦油固含量约6.5wt%,通过焦油冷却器冷却至95℃,然后经高速离心机分离得到重油产品iii和油渣:其中油渣中焦油含量约32wt%,经泵加压后返回至热解炉炉头;重油产品iii中固含量约1.0wt%,将重油产品ii、重油产品iii与炉尾分离的重油混合后作为重油产品,重油产品收率为10.2wt%。
热解炉设置有全烟气外夹套和内部8层加热管,夹套烟气采用“一进三出”方式。热解热风炉来800℃烟气温度,同时通过夹套和加热管与干燥煤间接换热,换热后的混合烟气温度为560℃,经循环烟气风机加压后~90%返回至热解热风炉,剩余部分预热助燃空气后放空。
系统设置有干燥热风炉和热解热风炉,采用多级低氧燃烧控制出口烟气氧含量为3.0vol%,然后分别送至回转干燥炉和热解炉作为热源。热风炉用燃料气低位热值为2600kcal/nm3,由外部提供。
对比例1
本对比例提供一种低阶粉煤回转热解方法,具体包括如下步骤:
将60t/h水含量17.0wt%、粒度<30mm的低阶粉煤连续送至回转干燥炉,从回转干燥炉炉头通入干燥热风炉来的550℃高温烟气(氧含量~2.0vol%),高温烟气兼具加热和除尘作用。在回转干燥炉中,煤被干燥至水含量~0.5wt%,温度~150℃。炉尾排出的干燥煤经排料阀进入热解炉;炉尾排出的干燥气温度~180℃并夹带有少量煤尘,经除尘器脱除掉煤尘、水冷至60℃、引风机加压后,大部分(~80%)返回至干燥热风炉进行低氧燃烧,剩余部分排至大气。
在热解炉中,干燥煤在隔绝空气状态下受热发生热解反应,产生提质焦粉和高温油气:炉尾排出的提质焦粉进入提质焦粉冷却器,经高温段、低温段冷却并回收热量后温度为95℃,喷入干燥水继续降温、增湿(水含量8wt%)后作为产品。高温油气从炉尾引出,炉尾出口油气温度约580℃,经两级串联旋风分离器除尘、重油湿式除尘、冷却至40℃并分液后得到热解煤气ii、重油产品ii和热解废水ii。热解煤气ii均送至气柜中缓存。热解废水ii送至污水处理。重油湿式除尘底部排出的含尘焦油固含量约9.0wt%,通过焦油冷却器冷却至95℃,然后经高速离心机分离得到重油产品iii和油渣:其中油渣中焦油含量约40wt%;重油中固含量约1.2wt%,将重油产品ii、重油产品iii与炉尾分离的重油混合后作为重油产品,重油产品收率为9.6%。
热解炉设置有全烟气外夹套和内部8层加热管,夹套烟气采用“一进三出”方式。热解热风炉来800℃烟气温度,同时通过夹套和加热管与干燥煤间接换热,换热后的混合烟气温度为560℃,经循环烟气风机加压后~90%返回至热解热风炉,剩余部分预热助燃空气后放空。
系统设置有干燥热风炉和热解热风炉,采用多级低氧燃烧控制出口烟气氧含量为3.0vol%,然后分别送至回转干燥炉和热解炉作为热源。热风炉用燃料气低位热值为2600kcal/nm3,由外部提供。
显然,上述实施例仅仅是为清楚地说明所作的举例,而并非对实施方式的限定。对于所属领域的普通技术人员来说,在上述说明的基础上还可以做出其它不同形式的变化或变动。这里无需也无法对所有的实施方式予以穷举。而由此所引申出的显而易见的变化或变动仍处于本发明创造的保护范围之中。
本文用于企业家、创业者技术爱好者查询,结果仅供参考。