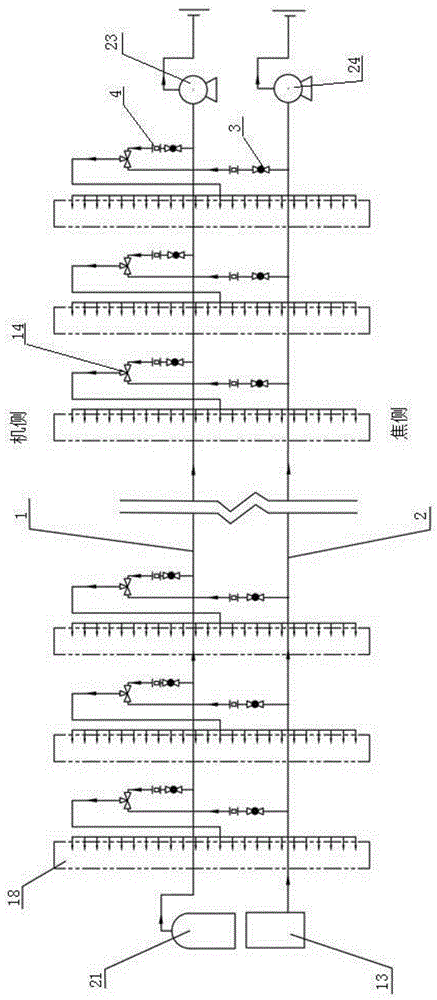
本发明涉及焦炉生产技术领域,尤其涉及一种焦炉废气回配与炉内脱硝耦合系统及方法。
背景技术:
目前,焦化行业脱硝多采用炉外烟气脱硝的方式,主要采用非选择性催化还原脱硝(sncr)或选择性催化还原脱硝(scr)。两种脱硝方法的实际效果与温度密切相关,sncr法应用的最佳温度区间为800℃~1100℃;scr方法应用的最佳温度区间为450℃以下。炉外烟气脱硝方式需要另外建造脱硝反应器,通过风机将脱硝后烟气输入烟囱排放。而炉内脱硝方式是利用焦炉本体构造,在炉内将nox与还原剂nh3反应使其还原为n2,此种方式能够极大地减少项目建造投入。
废气回配技术是从焦炉分烟道抽取燃烧后的废气,与空气掺混后,通过废气开闭器通入小烟道,经蓄热室送入燃烧室进行贫氧燃烧,能够有效改善高向加热均匀性,降低炉内温度,从而减少氮氧化物生成。公开号为cn111286346a的中国专利申请公开了“一种焦炉的烟气回配系统及回配方法”,公开号为cn109957407a的中国专利申请公开了“一种焦炉废气脱硝及改善焦炉加热装置”,2个技术方案的管道出口均与废气开闭器相连,此种布置方式使得废气通入焦炉小烟道,在焦炉小烟道内进行空气与废气掺混,由于沿程阻力影响,焦炉小烟道内部掺混程度不同,从而影响了气体比例,导致各燃烧室立火道内的燃烧情况不同,增大了生产调火难度。
废气回配与炉内sncr脱硝方法均能有效降低氮氧化物的生成,而两者要求工况不同,因此,亟需一种能够将两者耦合的系统,实现在生产中精准调节掺混气量,配合焦炉煤气交换传动装置,实现全过程脱硝。
焦炉蓄热室主要由主墙、单墙、格子砖等组成。其中蓄热室主墙两侧的蓄热室内气流相反,蓄热室单墙两侧的蓄热室内气流流向相同;蓄热室内的上升气流为空气及助燃气体,下降气流为燃烧废气。蓄热室主墙与蓄热室单墙之间摆放格子砖,单个蓄热室内沿机侧-焦侧方向设置隔墙,将蓄热室分格。
蓄热室内格子砖的铺设形式为废气与空气掺混提供了良好环境,流经蓄热室内的废气温度符合炉内sncr方法应用的最佳温度区间。基于此,本发明提出了一种焦炉废气回配与炉内脱硝耦合系统及方法。
技术实现要素:
本发明提供了一种焦炉废气回配与炉内脱硝耦合系统及方法,按照焦炉煤气交换制度,通过气路切换装置控制废气与氨气交替通入蓄热室掺混区,能够有效改善炉内高向加热情况,并减少氮氧化物生成。
为了达到上述目的,本发明采用以下技术方案实现:
一种焦炉废气回配与炉内脱硝耦合系统,包括废气回配管路、氨气管路及气路切换装置;所述废气回配管路由废气回配主管道、废气直立管及废气引风机组成;所述氨气管路由氨气储存罐、氨气输送管道、氨气直立管及氨气引风机组成;所述气路切换装置由交换旋塞及交换旋塞切换装置组成;
所述废气回配主管道与氨气输送管道沿焦炉纵向并排设于焦炉地下室内,废气回配主管道的一端与焦炉汇总烟道的抽气口相连,另一端连接废气引风机;所述氨气输送管道的一端与氨气储存罐相连,另一端连接氨气引风机;废气回配主管道上与蓄热室单墙一一对应地设置多个废气直立管,氨气输送管道上与蓄热室单墙一一对应地设置多个氨气直立管;废气直立管、氨气直立管并列设于蓄热室单墙正下方;废气直立管与氨气直立管连接三通管式的交换旋塞,交换旋塞的另一个出口通过连接管与横向支管相连,横向支管通过下喷管与砖气流道相连;砖气流道由高向砖气流道和横向砖气流道组成,高向砖气流道设于蓄热室单墙内,高向砖气流道的下端与下喷管相连,上端与横向砖气流道的中部相连,横向砖气流道贯穿对应的蓄热室单墙,两端开口正对两侧蓄热室掺混区的中心;所述交换旋塞切换装置由斜齿轮组及链轮链条传动机构组成,链条沿焦炉纵向通长设置,对应各蓄热室的交换旋塞分别通过对应斜齿轮组与链轮链条传动机构相连,斜齿轮组中的一个斜齿轮与交换旋塞中的角阀同轴相连,另一个斜齿轮与链轮同轴相连;对应单号蓄热室单墙的斜齿轮组齿轮旋向与对应双号蓄热室单墙的斜齿轮组齿轮旋向相反;所述链条与焦炉交换传动装置相连。
所述废气回配主管道上设置压力计与膨胀节,靠近焦炉汇总烟道取气口的一端设置废气主阀门。
所述氨气输送管道上设置压力计与膨胀节,与氨气储存罐连接处设置氨气主阀门。
按照气流流向,所述废气直立管上依次设置调节旋塞、孔板盒及流量计。
按照气流流向,所述氨气直立管上依次设置调节旋塞、孔板盒及流量计。
所述交换旋塞内设置带润滑油杯的角阀,交换旋塞为三通管结构,两端开口分别连接废气直立管及氨气直立管,顶部开口与连接管相连;所述斜齿轮组外侧设齿轮箱。
所述砖气流道由管状耐火材料经砌筑或拼接形成。
所述蓄热室根据工作温度划分为3个区域,分别为:低于800℃的低温区、800℃~1000℃的蓄热室掺混区,以及高于1000℃的高温区;低温区与高温区内填充格子砖,蓄热室掺混区内无填充;单个蓄热室通过若干隔墙形成分格结构。
一种焦炉废气回配与炉内脱硝耦合方法,包括:
1)根据焦炉煤气交换制度,通过交换旋塞切换装置转动交换旋塞内的角阀;
2)在对应蓄热室单墙两侧的蓄热室内为上升气流时,使废气直立管与连接管连通,通过横向支管将回配废气分配至各下喷管,并通过砖气流道将回配废气直接送至蓄热室掺混区;上升气流流经蓄热室掺混区的过程中,废气与空气掺混,使燃烧室内进行贫氧燃烧,从而改善炉内高向加热均匀性;
3)在对应蓄热室单墙两侧的蓄热室内为下降气流时,使氨气直立管与连接管连通,通过横向支管将氨气分配至各下喷管,并通过砖气流道将氨气直接送至蓄热室掺混区;下降气流流经蓄热室掺混区的过程中,通过氨气喷吹,进行sncr脱硝反应,从而减少氮氧化物生成。
与现有技术相比,本发明的有益效果是:
1)将炉内脱硝功能与废气回配功能耦合在同一系统内,上升气流流经蓄热室内掺混区过程中,使回配废气与空气掺混,从而使燃烧室内进行贫氧燃烧,有效改善炉内高向加热情况;下降气流流经蓄热室掺混区过程中,通过氨气喷吹进行sncr脱硝反应,有效降低氮氧化物生成;本发明实现了焦炉生产全过程降低氮氧化物生成;
2)通过设置调节旋塞及孔板,精准控制进入各个蓄热室的气量,配合流量计与压力计可实现数据监控;针对上升气流工况,可根据蓄热室上方对应燃烧室内的燃烧情况,调节废气的掺混比例;针对下降气流工况,通过调节氨气流量,可控制脱硝效率,防止氨气过量;
3)通过交换旋塞与斜齿轮组配合,通过链轮链条传动机构连接焦炉煤气交换传动装置,与焦炉加热换向实现联动,通过交换旋塞改变通入蓄热室掺混区的气体;有效降低操作人员的劳动强度,降低事故率;
4)蓄热室单墙内根据蓄热室分格数设置了相同数量的砖气流道,砖气流道布置在蓄热室单墙内,能够有效防止高温导致的气体窜漏,同时减少了外部管道的搭建;每个蓄热室分格内均设置蓄热室掺混区,提高了气体掺混效率。
附图说明
图1是本发明所述一种焦炉废气回配与炉内脱硝耦合系统的结构示意图。
图2是本发明所述一种焦炉废气回配与炉内脱硝耦合系统的局部立体结构示意图。
图3是本发明所述气路切换装置的结构示意图。
图4是本发明所述焦炉蓄热室的结构示意图。
图中:1.废气回配主管道2.氨气输送管道3.调节旋塞4.孔板盒5.角阀6.齿轮箱7.斜齿轮组8.连接管9.横向支管10.下喷管11.链条12.链轮13.氨气储存罐14.交换旋塞15.蓄热室主墙16.蓄热室单墙17.砖气流道18.蓄热室掺混区19.焦炉小烟道20.格子砖21.焦炉汇总烟道22.隔墙23.废气引风机24.氨气引风机
具体实施方式
下面结合附图对本发明的具体实施方式作进一步说明:
如图1、图2所示,本发明所述一种焦炉废气回配与炉内脱硝耦合系统,包括废气回配管路、氨气管路及气路切换装置;所述废气回配管路由废气回配主管道1、废气直立管及废气引风机23组成;所述氨气管路由氨气储存罐13、氨气输送管道2、氨气直立管及氨气引风机24组成;所述气路切换装置由交换旋塞14及交换旋塞切换装置组成;
所述废气回配主管道1与氨气输送管道2沿焦炉纵向并排设于焦炉地下室内,废气回配主管道1的一端与焦炉汇总烟道21的抽气口相连,另一端连接废气引风机23;所述氨气输送管道2的一端与氨气储存罐13相连,另一端连接氨气引风机24;废气回配主管道1上与蓄热室单墙16一一对应地设置多个废气直立管,氨气输送管道2上与蓄热室单墙16一一对应地设置多个氨气直立管;废气直立管、氨气直立管并列设于蓄热室单墙16正下方;废气直立管与氨气直立管连接三通管式的交换旋塞14,交换旋塞14的另一个出口通过连接管8与横向支管相连,横向支管9通过下喷管10与砖气流道17相连;砖气流道17由高向砖气流道和横向砖气流道组成,高向砖气流道设于蓄热室单墙16内,高向砖气流道的下端与下喷管10相连,上端与横向砖气流道的中部相连,横向砖气流道贯穿对应的蓄热室单墙16,两端开口正对两侧蓄热室掺混区的中心;如图3所示,所述交换旋塞切换装置由斜齿轮组7及链轮链条传动机构组成,链条11沿焦炉纵向通长设置,对应各蓄热室的交换旋塞14分别通过对应斜齿轮组7与链轮链条传动机构相连,斜齿轮组7中的一个斜齿轮与交换旋塞14中的角阀同轴相连,另一个斜齿轮与链轮12同轴相连;对应单号蓄热室单墙的斜齿轮组7齿轮旋向与对应双号蓄热室单墙的斜齿轮组7齿轮旋向相反;所述链条11与焦炉交换传动装置相连。
所述废气回配主管道1上设置压力计与膨胀节,靠近焦炉汇总烟道21取气口的一端设置废气主阀门。
所述氨气输送管道2上设置压力计与膨胀节,与氨气储存罐13连接处设置氨气主阀门。
按照气流流向,所述废气直立管上依次设置调节旋塞3、孔板盒4及流量计。
按照气流流向,所述氨气直立管上依次设置调节旋塞3、孔板盒4及流量计。
所述交换旋塞14内设置带润滑油杯的角阀5,交换旋塞14为三通管结构,两端开口分别连接废气直立管及氨气直立管,顶部开口与连接管8相连;所述斜齿轮组7外侧设齿轮箱6。
所述砖气流道17由管状耐火材料经砌筑或拼接形成。
如图4所示,所述蓄热室根据工作温度划分为3个区域,分别为:低于800℃的低温区、800℃~1000℃的蓄热室掺混区18,以及高于1000℃的高温区;低温区与高温区内填充格子砖20,蓄热室掺混区18内无填充;单个蓄热室通过若干隔墙22形成分格结构。
一种焦炉废气回配与炉内脱硝耦合方法,包括:
1)根据焦炉煤气交换制度,通过交换旋塞切换装置转动交换旋塞14内的角阀5;
2)在对应蓄热室单墙16两侧的蓄热室内为上升气流时,使废气直立管与连接管8连通,通过横向支管9将回配废气分配至各下喷管10,并通过砖气流道17将回配废气直接送至蓄热室掺混区18;上升气流流经蓄热室掺混区18的过程中,废气与空气掺混,使燃烧室内进行贫氧燃烧,从而改善炉内高向加热均匀性;
3)在对应蓄热室单墙16两侧的蓄热室内为下降气流时,使氨气直立管与连接管8连通,通过横向支管9将氨气分配至各下喷管10,并通过砖气流道17将氨气直接送至蓄热室掺混区18;下降气流流经蓄热室掺混区18的过程中,通过氨气喷吹,进行sncr脱硝反应,从而减少氮氧化物生成。
以下实施例在以本发明技术方案为前提下进行实施,给出了详细的实施方式和具体的操作过程,但本发明的保护范围不限于下述的实施例。任何熟悉本技术领域的技术人员在本发明揭露的技术范围内,根据本发明的技术方案及其发明构思加以等同替换或改变,都应涵盖在本发明的保护范围之内。
【实施例】
在浇筑焦炉顶板前,沿蓄热室单墙16中心线,在蓄热室分格中心处,预埋下喷管10。
蓄热室砌筑时,按照预先设计的蓄热室工作温度区间,将蓄热室沿高向分为三部分,分别为低于800℃的低温区,800℃~1000℃的蓄热室掺混区18,高于1000摄氏度的高温区。低温区与高温区内用格子砖20填充,蓄热室掺混区18不填充任何物体,从而为气体掺混提供充分空间。
在单个蓄热室内沿机侧-焦侧方向砌筑若干隔墙22,隔墙22设置在蓄热室主墙15与蓄热室单墙16之间,将单个蓄热室分格。蓄热室单墙16中用管砖沿高向砌筑高向砖气流道,高向砖气流道的顶端位于蓄热室掺混区18的中心位置,在高向砖气流道的顶部砌筑水平的横向砖气流道,横向砖气流道的两端贯穿蓄热室单墙16,形成三通形式。
焦炉地下室沿焦炉中心线铺设废气回配主管道1,废气取气口位于焦炉汇总烟道21顶部,靠近取气口一端的废气回配主管道1上设置压力计,废气回配主管道1的终端连接废气引风机23。氨气输送管道2与废气回配主管道1并排布置,一端连接氨气引风机24,另一端与氨气储存罐13相连,且在相连处安装压力计。沿气流方向,废气回配主管道1及氨气输送管道2上分别设置压力计、膨胀节,废气回配主管道1、氨气输送管道2在对应蓄热室单墙16的正下方开设若干孔,开孔处焊接对应的废气直立管、氨气直立管,废气直立管、氨气直立管均与蓄热室单墙16一一对应设置。废气直立管、氨气直立管上沿气流方向依次设置调节旋塞3、孔板盒4及流量计,通过弯管将并列设置的废气直立管与氨气直立管变为相对设置,两者之间安装交换旋塞14。
交换旋塞14的内部设置带润滑油杯的角阀5,每个交换旋塞14的正面布置齿轮箱6,齿轮箱6内安装润滑油杯及斜齿轮组7,2个斜齿轮轴线垂直相互啮合,一个斜齿轮通过销连接交换旋塞14内角阀安装轴,另一个斜齿轮通过销连接链轮安装轴。相邻2个齿轮箱6内的斜齿轮组7的齿轮旋向相反,即如果将蓄热室单墙16按照单双号分组,单号蓄热室单墙对应的斜齿轮组7的齿轮旋向与双号蓄热室单墙对应的斜齿轮组7的齿轮旋向相反;链条11与焦炉交换传动装置连接,焦炉交换传动装置动作时,通过链条11带动对应的链轮12及斜齿轮组7动作,最终实现以下功能:
1)蓄热室内为上升气流时,通过交换旋塞14内的角阀5旋转,使废气直立管与连接管8相通。
2)蓄热室内为下降气流时,通过交换旋塞14内的角阀5旋转,使氨气直立管与连接管8相通。
交换旋塞14的顶部开口与连接管8连接,连接管8与横向支管9相连,横向支管9沿焦炉机侧-焦侧方向布置在蓄热室单墙16的正下方,并与蓄热室单墙16一一对应设置。在横向支管9顶面开孔,开孔数量等于蓄热室分格数,该孔与蓄热室单墙16内的下喷管10连接。
废气回配与炉内脱硝耦合系统安装完毕后,需经打压测试管路的密闭性。然后,将全部调节旋塞3均完全关闭,打开孔板盒4放置孔板,检查焦炉交换传动装置能否带动所有交换旋塞14完成气体换向动作。
焦炉正产生产时,逐渐开大废气引风机23与氨气引风机24,检查废气回配主管道1及氨气输送管道2上的压力计是否正常,同时开启各个调节旋塞3。根据废气直立管及氨气直立管上的流量计所示流量,结合炉内燃烧情况与监测数据,合理调整各调节旋塞3的开度及孔板型号。
当蓄热室主墙15一侧的蓄热室内为上升气流时,焦炉交换传动装置通过链条11、对应链轮12带动对应斜齿轮组7正向转动,使交换旋塞14内的角阀5转动,将废气直立管与连接管8连通,回配废气经回配废气主管道1、废气直立管、连接管8、横向支管9、下喷管10、砖气流道17,最终在焦炉蓄热室掺混区18内与空气进行掺混,用以降低助燃气体的氧含量。此时,蓄热室主墙15另一侧蓄热室内为下降气流,链条11传动时,同时通过对应链轮12带动对应斜齿轮组7反向转动,使得氨气直立管与连接管8连通,氨气经氨气输送管道2、氨气直立管、连接管8、横向支管9、下喷管10、砖气流通道17,最终在对应蓄热室掺混区18内与燃烧后的气体发生还原反应,用于减少氮氧化物的生成。
废气直立管用于将废气回配主管道1内的回配废气引出,利用调节旋塞3控制对应废气直立管内的废气流量,利用孔板盒4内的孔板控制对应废气直立管内的废气流速,通过流量计监控对应废气直立管内的废气流量。
氨气直立管用于将氨气输送管道2内的氨气引出,利用调节旋塞3控制对应氨气直立管内的氨气流量,利用孔板盒4内的孔板控制对应氨气直立管内的氨气流速,通过流量计监控对应氨气直立管内的氨气流量。
调节旋塞3可人为或通过机械开闭,用于调整气体流量大小。调节旋塞3的上部设置孔板盒4,可在气体流量不变的情况下,通过调整孔板大小控制气体流速。
下喷管10布置在焦炉顶板中,上端连接蓄热室单墙16内的砖气流道17,下端与横向支管9相连。每个横向支管9连接的下喷管10数量与焦炉蓄热室分格数相同,下喷管10用于将横向支管9内的气体分配至各高向砖气流道。
砖气流道17布置在蓄热室单墙16中,其数量与焦炉蓄热室的分格数相等。高向砖气流道沿蓄热室单墙16的高向布置,每个高向砖气流道布置在两道焦炉蓄热室的隔墙22之间,高向砖气流道的下端与下喷管10相通,上端与横向砖气流道相连。横向砖气流道贯穿蓄热室单墙16,两端开口正对蓄热室掺混区18中心,用于将废气或氨气送入蓄热室掺混区18。
砖气流道17采用管状耐火材料,通过砌筑方式或拼接方式与焦炉蓄热室单墙16一同施工。
以上所述,仅为本发明较佳的具体实施方式,但本发明的保护范围并不局限于此,任何熟悉本技术领域的技术人员在本发明揭露的技术范围内,根据本发明的技术方案及其发明构思加以等同替换或改变,都应涵盖在本发明的保护范围之内。
本文用于企业家、创业者技术爱好者查询,结果仅供参考。