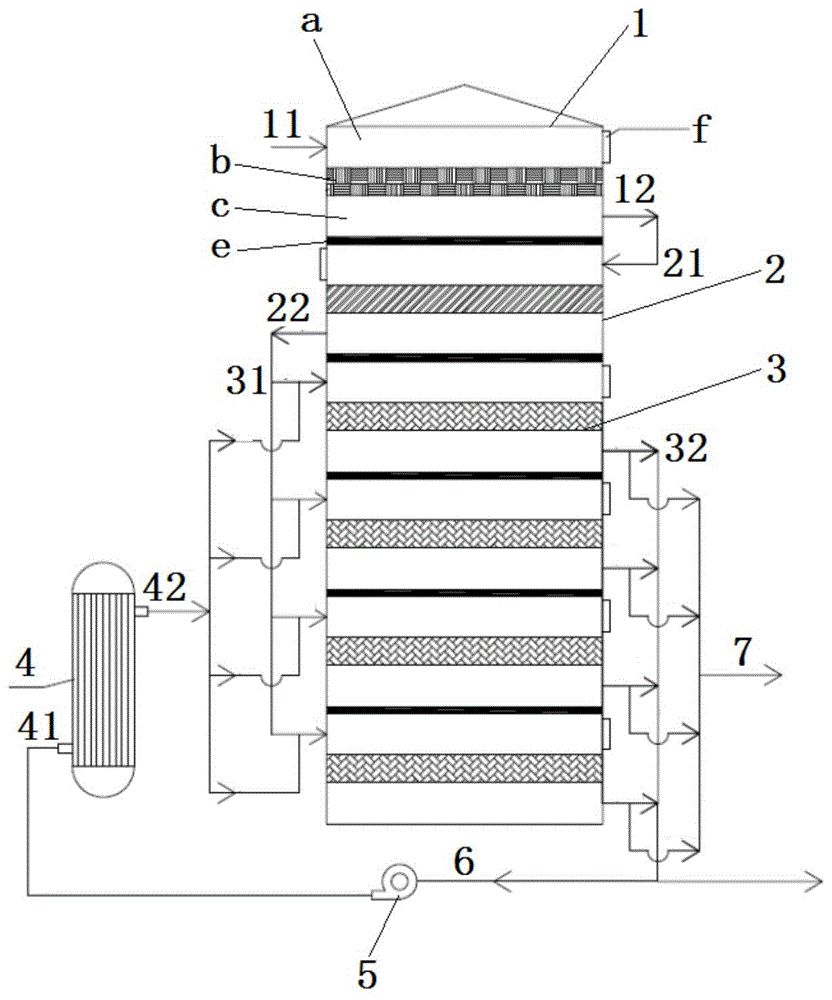
本实用新型涉及大气净化环境保护技术领域,具体涉及一种大气量常压低阻力高炉煤气脱硫系统。
背景技术:
高炉煤气具有可观的燃烧价值,其中一氧化碳的体积含量大约为28%,氢气的体积含量大约为1%,甲烷的体积含量大约为0.5%。高炉煤气通常以燃料的方式送往热风炉、加热炉、焦炉、锅炉、燃气机组进行燃烧使用。然而高炉煤气中除了上述气体外,还存在cos(羰基硫)、cs2、h2s等硫化物,在这些硫化物中其中主要成分是cos,总硫浓度一般达到200mgs/nm3以上。这些硫化物如果不加限制会以so2的形式排放到空气中,进而造成大量的酸雨形成。随着人们环保意识的增加,对硫的排放限值也日益严格,每个使用高炉煤气的终端都建立起庞大的烟气脱硫装置。如此分散的脱硫装置不但大大浪费有限的钢厂空间,而且烟气脱硫的成本及二次污染也日益突显出来。因此,与终端脱硫技术相比,对高炉煤气采取源头脱硫就成为一种理想的处理硫物种的方法。
现有技术cn110218590a公开了一种高炉煤气脱硫方法及系统,其中所述高炉煤气脱硫方法包括如下步骤:1)将经过压缩的原料气通入水解塔中进行cos水解,生成含硫化氢的混合气体;2)将所述含硫化氢的混合气体通入变压吸附提纯二氧化碳装置中进行粗脱硫,得到粗脱硫气体并对吸附了二氧化碳及硫化氢的吸附剂进行吸附剂解吸;3)将所述粗脱硫气体通入精脱硫塔中进行精脱硫,得到精脱硫气体;4)将所述精脱硫气体通入变压吸附提纯一氧化碳工段,提纯一氧化碳得到脱硫高炉煤气。但是,高炉煤气的气量庞大,一座1000立方的高炉每小时能产生大于10万标准立方的高炉煤气,其压力一般大于100kpa,经余压透平发电装置(trt)回收的压力能后,压力降为5-20kpa之间。然而对于如此庞大的气量进行变压,将消耗大量的能量。但是如果进行常压吸附,那么采用传统吸附剂填充方式的脱硫系统,其阻力降问题将导致吸附剂的用量不能过高,吸附剂用量太低又会造成吸附频繁更换等问题。
技术实现要素:
本实用新型旨在解决现有脱硫系统对所处理高炉煤气的压力需求大,处理费用高的问题,从而提供一种大气量常压低阻力高炉煤气脱硫系统。
本实用新型采用如下技术方案:
一种大气量常压低阻力高炉煤气脱硫系统,包括脱氯脱氧装置、水解装置和吸附装置,所述脱氯脱氧装置上设有高炉煤气进气口和脱氧脱氯出气口,所述水解装置上设有水解进气口和水解出气口,所述吸附装置上设有吸附进气口和吸附出气口,所述脱氧脱氯出气口与所述水解进气口连通,所述水解出气口与所述吸附进气口连通;所述脱氯脱氧装置、水解装置和吸附装置内均为3层结构,自上而下依次设有上方气压缓冲区、填料层和下方气压缓冲区,所述高炉煤气进气口、水解进气口和吸附进气口分别设置在其所在装置上方气压缓冲区的一侧侧壁上,所述脱氧脱氯出气口、水解出气口和吸附出气口分别设置在其所在装置下方气压缓冲区的另一侧侧壁上。
所述上方气压缓冲区、填料层和下方气压缓冲区内体积比为1:(0.8-2):1。
优选地,所述上方气压缓冲区、填料层和下方气压缓冲区内体积比为1:1.5:1。
脱氯脱氧装置内所示填料层的填充高径比为1:10~1:30。
所述填料层的上端和下端分别设有格栅,所述填料层内的填料通过两所述格栅固定在所述上方气压缓冲区与下方气压缓冲区之间。
所述脱氯脱氧装置设置在所述水解装置的上方,所述吸附装置设置在所述水解装置的下方,在所述脱氯脱氧装置与所述水解装置之间、所述水解装置与所述吸附装置之间均设有隔热层。
所述脱氯脱氧装置内的所述填料层用于填充脱氧剂;所述水解装置内的所述填料层用于填充水解剂;所述吸附装置的所述填料层用于填充吸附剂。
所述系统包括至少两个并联设置的所述吸附装置,每个所述吸附装置竖向叠加设置在所述水解装置的下方,相邻两个所述吸附装置之间设置所述隔热层。
优选地,所述系统包括至少4个并联设置的所述吸附装置,其中3个并联设置的所述吸附装置用于对高炉煤气进行吸附处理,另一个备用或对吸附剂进行再生。
所述系统还包括换热装置,所述换热装置上设有换热进气口和换热出气口,所述换热进气口分别与4个所述吸附装置的吸附进气口联通,4个所述吸附装置的吸附出气口汇合后分两路,一路用于净化后的高炉煤气回收,另一路经再生进气口管路通过一气泵与所述换热进气口连通,净化后的部分高炉煤气通过所述换热装置加热后进入所述吸附装置内,用于所述吸附装置内吸附饱和的吸附剂进行再生。
本实用新型技术方案,具有如下优点:
a.本实用新型大气量常压低阻力高炉煤气脱硫系统,每一个处理装置均包括填料层的上方气压缓冲区、填料层以及填料层的下方气压缓冲区,降低了填料层的厚度,且预处理气体均采用上进下出的方式,能够有效地降低填料层的阻力降,降低了脱硫系统对高炉煤气的压力需要,该系统中高炉煤气的处理压力最低限为5kpa,每一组处理装置的阻力降小于500pa,提高了高炉煤气的有效处理量。
b.本实用新型中脱氯脱氧装置、水解装置和吸附装置采用上下竖向设置,大大减小了系统的占地面积,节约用地资源。
附图说明
为了更清楚地说明本实用新型具体实施方式,下面将对具体实施方式中所需要使用的附图作简单地介绍,显而易见地,下面描述中的附图是本实用新型的一些实施方式,对于本领域普通技术人员来讲,在不付出创造性劳动的前提下,还可以根据这些附图获得其他的附图。
图1为本实用新型大气量常压低阻力高炉煤气脱硫系统整体结构示意图;
图2为本实用新型中填料层结构示意图;
图3为本实用新型中格栅结构示意图。
图中标识如下:
1-脱氯脱氧装置,11-高炉煤气进气口,12-脱氧脱氯出气口;2-水解装置,21-水解进气口,22-水解出气口;3-吸附装置,31-吸附进气口,32-吸附出气口;4-换热装置,41-换热进气口,42-换热出气口;5-气泵;6-再生进气口管路;7-吸附再生出气口管路;
a-上方气压缓冲区;b-填料层;c-下方气压缓冲区;d-格栅;e-隔热层;f-填料口。
具体实施方式
下面将结合附图对本实用新型的技术方案进行清楚、完整地描述,显然,所描述的实施例是本实用新型一部分实施例,而不是全部的实施例。基于本实用新型中的实施例,本领域普通技术人员在没有做出创造性劳动前提下所获得的所有其他实施例,都属于本实用新型保护的范围。
在本实用新型的描述中,需要说明的是,术语“中心”、“上”、“下”、“左”、“右”、“竖直”、“水平”、“内”、“外”等指示的方位或位置关系为基于附图所示的方位或位置关系,仅是为了便于描述本实用新型和简化描述,而不是指示或暗示所指的装置或元件必须具有特定的方位、以特定的方位构造和操作,因此不能理解为对本实用新型的限制。此外,术语“第一”、“第二”、“第三”仅用于描述目的,而不能理解为指示或暗示相对重要性。
在本实用新型的描述中,需要说明的是,除非另有明确的规定和限定,术语“安装”、“相连”、“连接”应做广义理解,例如,可以是固定连接,也可以是可拆卸连接,或一体地连接;可以是机械连接,也可以是电连接;可以是直接相连,也可以通过中间媒介间接相连,可以是两个元件内部的连通。对于本领域的普通技术人员而言,可以具体情况理解上述术语在本实用新型中的具体含义。
如图1所示,本实用新型提供了一种大气量常压低阻力高炉煤气脱硫系统,包括脱氯脱氧装置1、水解装置2和吸附装置3,脱氯脱氧装置1上设有高炉煤气进气口11和脱氧脱氯出气口12,水解装置2上设有水解进气口21和水解出气口22,吸附装置3上设有吸附进气口31和吸附出气口32,脱氧脱氯出气口12与水解进气口21连通,水解出气口22与吸附进气口31连通。脱氯脱氧装置1、水解装置2和吸附装置3内均为3层结构,自上而下依次设有上方气压缓冲区a、填料层b和下方气压缓冲区c,高炉煤气进气口11、水解进气口21和吸附进气口31分别设置在其所在装置上方气压缓冲区a的一侧侧壁上,脱氧脱氯出气口12、水解出气口22和吸附出气口32分别设置在其所在装置下方气压缓冲区c的另一侧侧壁上。上方气压缓冲区a、填料层b和下方气压缓冲区c内体积比为1:(0.8-2):1,脱氯脱氧装置1内所示填料层b的填充高径比为1:10~1:30。本实用新型中每一个处理装置均包括填料层的上方气压缓冲区、填料层以及填料层的下方气压缓冲区,降低了填料层的厚度,且预处理气体均采用上进下出的方式,能够有效地降低填料层的阻力降,降低了脱硫系统对高炉煤气的压力需要,提高了高炉煤气的有效处理量,该系统中高炉煤气的处理压力最低限为5kpa,每一组处理装置的阻力降小于500pa。
进一步地,如图2、图3所示,填料层b的上端和下端分别设有格栅d,填料层b内的填料通过两格栅d固定在上方气压缓冲区a与下方气压缓冲区c之间。格栅d采用环形蜘蛛网结构,气体通过性好。
脱氯脱氧装置1的控制温度为80-150℃,其设置在水解装置2的上方,脱氯脱氧装置1内填料层b的填充高径比为1:10-1:30,吸附装置3设置在水解装置2的下方,在脱氯脱氧装置1与水解装置2之间、水解装置2与吸附装置3之间均设有隔热层e。脱氯脱氧装置1内的填料层b用于填充脱氧剂,脱氧剂可选自贵金属脱氧剂、非贵金属钴钼硫型脱氧剂中的至少一种;贵金属脱氧剂优选为负载型贵金属脱氧剂,负载型贵金属脱氧剂中活性成分选自金、铂、钯、钌中的一种或多种,载体为氧化物载体或陶瓷载体,其中氧化物载体选自氧化铝、氧化硅、氧化镁、氧化钛、氧化锆、氧化铈中的一种或多种;非贵金属钴钼硫型脱氧剂中活性成分选自como2s、como3s、como4s中的一种或多种;载体为氧化铝。水解装置2内的填料层b用于填充水解剂,水解剂为负载型水解剂,负载型水解剂的活性成分选自氢氧化钠、氢氧化钾、碳酸钠、碳酸钾、草酸钠、草酸钾、硫酸钠、硫酸钾中的一种或多种,载体选自氮化碳、氧化铝、氧化硅、氧化镁、氧化钛、氧化锆、氧化铈中的一种或多种。吸附装置3的填料层b用于填充吸附剂。吸附剂为负载型吸附剂,负载型吸附剂的活性成分选自氧化铁、氧化钴、氧化镍、氧化铜中的一种或多种,载体选自改性铝土矿、氮化碳、氧化铝、氧化硅、氧化镁、氧化钛、氧化锆、氧化铈中的一种或多种。
所述脱硫系统包括至少两个并联设置的吸附装置3,优选为4个,其中3个并联设置的吸附装置3用于对高炉煤气进行吸附处理,另一个备用或对吸附剂进行再生;每个吸附装置3竖向叠加设置在水解装置2的下方,相邻两个吸附装置3之间设置隔热层e。
使用时,待处理的高炉煤气通过高炉煤气进气口11进入到脱氯脱氧装置1处理后,得到脱氯脱氧处理后的原料气,脱氯脱氧处理后的原料气从脱氧脱氯出气口12排出,并通过水解装置2的水解进气口21进入水解装置2,并在水解装置2中进行水解,将高炉煤气中的有机硫cos转换为硫化氢,得到水解处理后的原料气,水解处理后的原料气通过吸附装置3的吸附进气口31进入吸附装置3,硫化氢在吸附装置3中被吸附,从而实现对水解处理后的原料气进行脱硫,得到脱硫后的高炉煤气。
本实用新型所述系统还包括换热装置4,换热装置4上设有换热进气口41和换热出气口42,换热进气口41分别与4个吸附装置3的吸附进气口31联通,4个吸附装置3的吸附出气口32汇合后分两路,一路用于净化后的高炉煤气回收,另一路经再生进气口管路6通过一气泵5与换热进气口41连通,净化后的部分高炉煤气通过换热装置4加热后进入吸附装置3内,当吸附装置3内吸附剂吸附硫化氢达到饱和时,可对吸附装置3内的吸附剂进行再生。例如,将部分脱硫后的干净高炉煤气通过气泵5的输送,使之从换热装置4的换热进气口41进入换热装置4,以对干净高炉煤气进行加热提温到180-200℃,经过加热提温的干净高炉煤气从换热装置4的换热出气口42排出,由吸附装置3的吸附进气口31进入吸附装置,利用干净高炉煤气中还原性气氛对吸附剂进行再生,同时干净高炉煤气含有的特定量的氧气(0.1-0.3%)在180-200℃下可将吸附的硫化氢氧化为单质硫磺,使硫物种从有害废物变为可利用的硫磺单质。含有单质硫磺的高炉煤气然后由吸附装置3的吸附出气口32汇集到吸附再生出气口管路7排出。可选地,当并联设置4个吸附装置3时,水解处理后的原料气首先通过其中一个吸附装置3,待吸附装置3中的吸附剂吸附硫化氢达到饱和时,通过阀门控制,使水解处理后的原料气仅通过其余3个吸附装置3,得到脱硫后干净的高炉煤气。将部分脱硫后的干净高炉煤气通过气泵5的输送,使之从换热装置4的换热进气口41进入换热装置4,以对干净高炉煤气进行加热提温,经过加热提温的干净高炉煤气从换热装置4的换热出气口42排出,由吸附饱和的吸附装置3吸附进气口31进入对应吸附装置3,利用高炉煤气中的还原性气氛(如氢气、一氧化碳等)对吸附剂进行再生,同时高炉煤气中的氧气将硫化氢氧化为单质硫,然后由该吸附装置3的吸附出气口32排出。其余3个吸附装置3内吸附剂吸附硫化氢达到饱和时,可对其内的吸附剂进行再生,同时启动另一吸附装置3继续对高炉煤气进行脱硫吸附处理,如此交替使用,可实现高炉煤气脱硫工艺的连续化进行。
应用例:
将120000nm3/h、7kpa、90℃含有cos浓度为80mg/m3的高炉煤气从脱氧脱氯装置1的高炉煤气进气口11进入,经装有高径比为0.1的负载型钌金属催化剂的脱氧脱氯装置1后,其压力降约为200pa,含氧量低于0.005%,氯含量低于2mg/m3;脱氧脱氯后的高炉煤气进入水解装置2,经内装有高径比为0.1的cos水解催化剂7%na2co3/al2o3后,水解后的脱氧脱氯中cos浓度低于1mg/m3,其压力降约为200pa,物流进入装有高径比为0.1的fe2o3/al2o3-c3n4吸附剂的吸附装置3,经吸附装置脱硫后的高炉煤气中h2s的浓度低于1mg/m3,其压力降约为200pa。小部分的干净无氧无硫的高炉煤气经换热器提温到190℃,对吸附剂进行再生。再生完成后,降温到低于80℃时,切换阀门,与其它三个吸附装置3交替使用。
如上述步骤进行吸附、再生循环测试10次后,高炉煤气中h2s的浓度低于2mg/m3。
本实用新型未述及之处适用于现有技术。
显然,上述实施例仅仅是为清楚地说明所作的举例,而并非对实施方式的限定。对于所属领域的普通技术人员来说,在上述说明的基础上还可以做出其它不同形式的变化或变动。这里无需也无法对所有的实施方式予以穷举。而由此所引伸出的显而易见的变化或变动仍处于本实用新型的保护范围之中。
本文用于企业家、创业者技术爱好者查询,结果仅供参考。