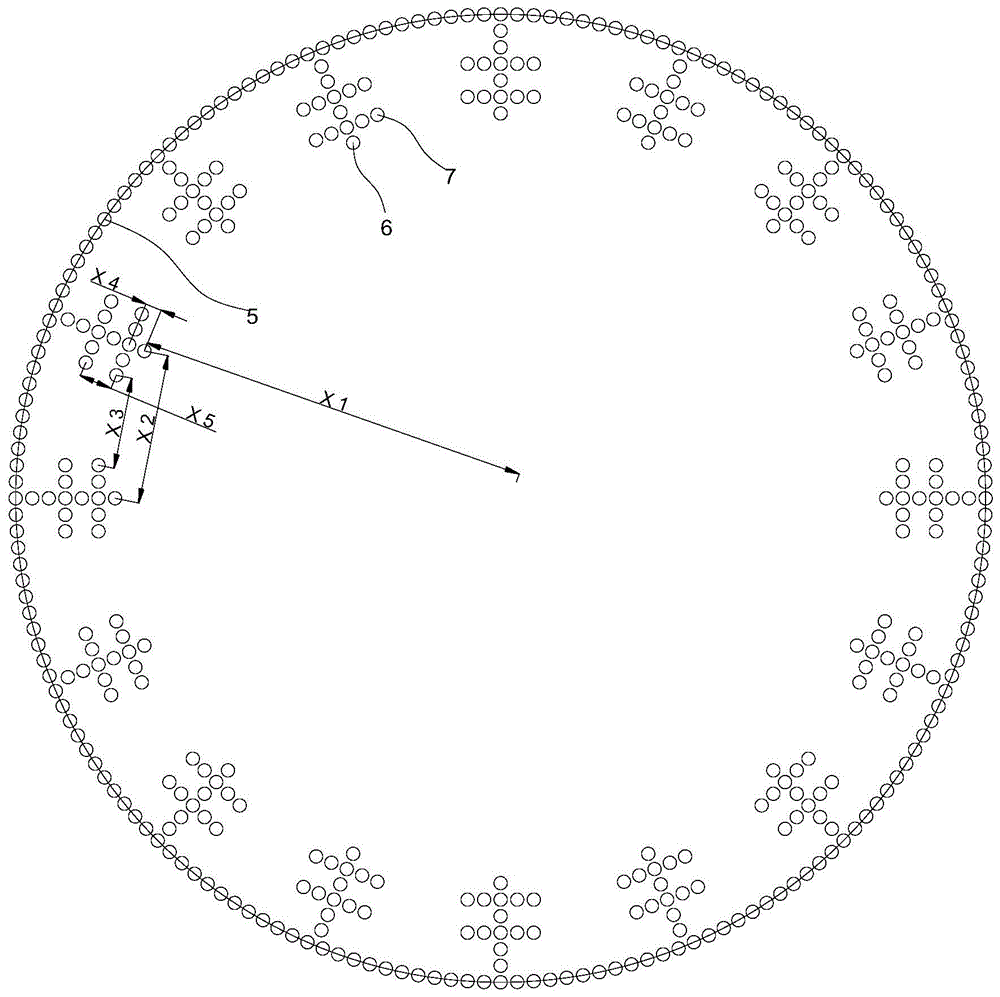
本发明涉及一种水冷壁衬里及包含其的辐射废锅和气化炉。
背景技术:
煤炭在现阶段仍是我国的重要基础能源和原料。近年来,我国现代煤化工产业发展迅速,以气流床煤气化为代表的煤炭清洁高效利用技术是发展现代煤化工产业的核心技术和龙头技术。我国在煤气化技术基础研究、技术开发、工程示范与应用等方面成绩显著,开发了以多喷嘴对置式水煤浆气化技术等为代表的大型煤气化技术,可满足多元化煤化工产品对气化技术的需求,对保障国家能源安全发挥了重要作用。
气流床煤气化技术主要包括激冷流程、废锅流程、废锅-激冷联合流程(亦即半废锅流程),其中,激冷流程应用最为广泛且装置投资低,由于气化炉产生的高温合成气在激冷后水气比较高,可满足全变换的蒸汽需要,该流程工艺主要应用于煤制合成氨、煤制氢等产业。废锅流程能源利用率高,通过设置在气化炉燃烧室出口的辐射废锅和对流废锅充分回收高温合成气热量,但因设备庞大且装置复杂,其一次投资较高,主要应用于igcc发电等行业。半废锅流程气化技术的开发介于激冷流程和废锅流程之间,既可以提高能源利用效率又可以适当降低设备投资,对于煤制甲醇、煤制油f-t合成等采用部分变换工艺的行业以及电力行业更为适用,应用前景较为广阔。
目前,关于半废锅气化技术的开发,国内的多喷嘴对置式煤气化技术、晋华炉气化技术等已完成了工程示范。半废锅气化炉在运行过程中除面临水冷壁表面易积灰、结渣等问题外,辐射废锅尺寸大、设备高度高也是半废锅气化技术的一项短板,这也是该类型装置投资增加的主要原因。半废锅气化炉与传统激冷型气化炉相比,相当于将激冷型气化炉的气化/燃烧室与激冷室两部分分开后,在原气化炉中部加入辐射废锅,变成由气化/燃烧室、辐射废锅和激冷室三部分组成。以单炉日处理煤2000吨级气化炉为例,半废锅流程气化炉较激冷流程气化炉高度增加约20米,气化框架高度也相应增加,导致气化炉本体和气化框架工程造价同时增加。若可以在保障热量有效回收的基础上进一步降低设备高度,对提高该技术的竞争优势具有重要意义。
在辐射废锅内部增设水冷壁,以增加单位体积废锅的换热面积,强化换热效果,这在本领域技术人员而言,是比较容易实现,但是水冷壁的增加会造成水冷壁间距缩小,很容易形成积灰、挂渣、架桥等现象,影响辐射废锅长期运行的换热效率。当前急需开发一种既能强化换热效果、降低废锅高度,又能减少水冷壁积灰等问题的水冷壁结构。
技术实现要素:
本发明解决的技术问题是克服现有技术半废锅气化炉单位体积内热量回收效率不高、设备尺寸大、高度太高,水冷壁易积灰导致换热效率下降的缺陷,提供了一种水冷壁衬里及包含其的辐射废锅和气化炉。本发明提供的水冷壁衬里在相同换热量下,能有效降低废锅和气化炉的高度,同时有效减少水冷壁积灰,提高水冷壁的长周期运行效率。
为了实现上述目的,本发明采用如下技术方案:
本发明提供了一种水冷壁衬里,其包括:
筒体水冷壁,所述筒体水冷壁周向设置,形成辐射废锅炉膛;
多组换热单元,所述多组换热单元设置在所述辐射废锅炉膛内且沿周向分布;
每组所述换热单元包括鳍片水冷壁ⅰ和至少一组鳍片水冷壁ⅱ;
所述鳍片水冷壁ⅰ沿由所述筒体水冷壁到所述辐射废锅炉膛的中心轴方向分布;
所述鳍片水冷壁ⅱ周向设置且与所述鳍片水冷壁ⅰ交叉;
所述鳍片水冷壁ⅰ的前端与所述中心轴的间距x1为d1~2d1,其中所述d1为合成气入口的直径,所述“前端”指的是靠近所述中心轴的一端;
相邻两组所述鳍片水冷壁ⅰ的前端间距x2大于300mm;
相邻两组所述换热单元中,设置在前端的两组所述鳍片水冷壁ⅱ的周向间距x3大于200mm。
本发明中,所述筒体水冷壁可为本领域常规,较佳地包括多根水冷管,相邻两根所述水冷管之间由筋板连接。
本发明中,所述间距x1较佳地为1.2d1~1.8d1,例如1.3d1、1.4d1、1.5d1或1.6d1,更佳地为1.5d1。
本发明经过发明人长期的实验探索,发现所述间距x1在上述范围内,合成气中灰渣与鳍片水冷壁ⅰ碰撞的概率大幅减小,同时也能有效利用辐射废锅炉膛的空间,增加单位体积内的换热面积,提高换热效率。
本领域技术人员应当了解,所述鳍片水冷壁ⅰ的前端积灰程度不仅与所述间距x1直接相关,也与灰渣粒径大小相关。粒径越小(例如小于30μm)的灰渣颗粒的气流跟随性越好,越容易弥散在辐射废锅的整个炉膛内,而粒径较大(例如大于200μm)的灰渣颗粒则在重力作用下集中于中心流道,对鳍片水冷壁ⅰ的渣蚀越不明显。
本发明中,所述鳍片水冷壁ⅰ的结构形式可为本领域常规,一般地由多根水冷管等间距排布组成。
其中,相邻两个所述水冷管之间的间距可为本领域常规。
当所述鳍片水冷壁ⅰ由多根水冷管等间距排布组成时,所述水冷管的数量可为1~12根,较佳地为5~10根,例如6根、7根、8根或9根。
其中,所述水冷管的外径可为本领域常规,一般地为20~100mm,例如32mm、38mm、45mm、57mm或76mm。
本发明中,所述间距x2较佳地为300~900mm,更佳地为400~800mm例如450mm、500mm、550mm、600mm、650mm或700mm。
经过发明人长期的实验探究,发现所述间距x2在上述范围时,相邻两组所述鳍片水冷壁ⅰ之间不易出现结渣、架桥或堵塞的现象,同时也能充分利用辐射废锅炉膛的空间,多设置几组鳍片水冷壁ⅰ,增加换热面积,提高换热效率。
本发明中,所述间距x3较佳地为200~500mm,更佳地为300~500mm,例如350mm、400mm或450mm。
同样的,所述间距x3处于本发明限定的范围内时,相邻两组所述换热单元中的所述鳍片水冷壁ⅱ之间不容易出现结渣、架桥或堵塞,同时也能充分利用炉膛空间。
本发明中,同一所述换热单元中,所述鳍片水冷壁ⅱ与所述鳍片水冷壁ⅰ的前端的间距x4可为0~250mm,较佳地为50~160mm,例如72mm、91mm或144mm,其中,当所述换热单元中包含多组所述鳍片水冷壁ⅱ时,所述间距x4指的是设置在最前端的所述鳍片水冷壁ⅱ与所述鳍片水冷壁ⅰ之间的距离。
本发明中设置的所述鳍片水冷壁ⅱ既能增加单位体积空间内的换热面积,同时合成气中的灰渣优先沉积在设置在前端的所述鳍片水冷壁ⅱ上,从而能有效减少其后的水冷壁的积灰。但是鳍片水冷壁ⅱ设置得太靠前时,鳍片水冷壁ⅱ表面积灰会有所增加,反而不利于水冷壁长期的运行。
本发明中,单个所述换热单元中,所述鳍片水冷壁ⅱ的组数优选为多组,进一步优选为2~4组,例如3组。
本发明中,单个所述换热单元中,所述鳍片水冷壁ⅱ的组数为多组时,相邻两组所述鳍片水冷壁ⅱ的间距x5可为60mm≤x5≤400mm,例如144mm、216mm、288mm或360mm。
所述间距x5设置过小时,同一换热单元中的相邻两组鳍片水冷壁之间也容易出现结渣、架桥或堵塞的现象,所述间距x5设置过大,又会影响鳍片水冷壁的设置数量,影响换热面积,本发明中的所述间距x5是发明人综合考虑换热面积和减少积灰得来的较佳范围。
本领域技术人员根据本发明的技术方案、选定的水冷管外径以及常规的水冷管的间隙,可以合理的设计出所述换热单元的组数、所述鳍片水冷壁ⅰ和所述鳍片水冷壁ⅱ的水冷管的根数,从而布置出本发明的水冷壁衬里。
本发明中,所述鳍片水冷壁ⅰ和所述鳍片水冷壁ⅱ的支撑方式可为本领域常规,较佳地,所述的鳍片水冷壁ⅰ的水冷管经筒体水冷壁穿入所述辐射废锅炉膛,在筒体水冷壁壁面上垂直支撑;所述鳍片水冷壁ⅱ的水冷管经筒体水冷壁顶部穿入所述辐射废锅炉膛,在筒体水冷壁上部向下支撑。
本发明的所述鳍片水冷壁ⅰ和所述鳍片水冷壁ⅱ的支撑方式可以避免高温热负荷剧烈变化引起水冷管之间的膨胀影响。
本发明还提供一种包含上述水冷壁衬里的辐射废锅。
本发明还提供一种包含上述辐射废锅的气化炉。
在符合本领域常识的基础上,上述各优选条件,可任意组合,即得本发明各较佳实例。
本发明的积极进步效果在于:
(1)同等换热需求下,采用本发明的水冷壁衬里可大幅降低辐射废锅的高度、对应框架的高度以及气化炉的高度,降低了装置总投资,同时也提高气化炉的安装稳定性和安全性;
(2)减少水冷壁衬里表面积灰、结渣等对换热效果的影响,长期运行的换热效果良好。
附图说明
图1为实施例1水冷壁结构示意图;
图2为实施例1辐射废锅结构示意图。
1-辐射废锅炉膛;2-金属壳体;3-合成气入口;4-合成气出口;5-筒体水冷壁;6-鳍片水冷壁ⅰ;7-鳍片水冷壁ⅱ。
具体实施方式
下面通过实施例的方式进一步说明本发明,但并不因此将本发明限制在所述的实施例范围之中。下列实施例中未注明具体条件的实验方法,按照常规方法和条件,或按照商品说明书选择。
实施例1
参照图1和图2所示,辐射废锅的金属壳体(2)的直径为6.0m,辐射废锅高度为11.0m,筒体水冷壁(5)的直径为4.8m,换热单元为16组,均匀地周向设置于辐射废锅炉膛(1)。每组换热单元中,鳍片水冷壁i(6)水冷管数量均为6根,鳍片水冷壁ii(7)设置两排,每排水冷管数量4根,水冷管尺寸均为
实施例2
辐射废锅金属壳体直径为5.0m,辐射废锅高度为14.0m,筒体水冷壁直径为4.0m。每组换热单元中,鳍片水冷壁i的水冷管数量为5根,鳍片水冷壁ii设置一排,单排水冷管数量4根。x1为1.34d1,其他参数与设置均与实施例1相同。x1-x4的值见表1。
对比例1
辐射废锅金属壳体直径为4.2m,辐射废锅高度为21.0m,筒体水冷壁直径为3.2m。每组换热单元中鳍片水冷壁i的水冷管数量为5根,不设置鳍片水冷壁ii。x1为d1,其他参数与设置均与实施例1相同。x1-x2的值见表1。
效果实施例
参照图2所示,采用实施例1~2以及对比例1的辐射废锅,在日处理煤2000吨的激冷流程水煤浆气化炉上进行换热实验。气化炉的气化压力为6.5mpa,气化温度为1300℃,合成气(co h2)产量为135000nm3/h。气化室产生的1300℃高温合成气与灰渣从合成气入口(3)进入辐射废锅炉膛(1),经过与水冷壁的热量交换,温度下降,并从合成气出口(4)流出,冷却后的合成气进洗涤冷却室,合成气温度降至约800℃,出气化界区进变换工段的粗合成气中水气比约0.7。进汽包锅炉给水温度218℃,压力11.57mpa,经换热后,出汽包蒸汽压力11.07mpa,蒸汽温度319℃,蒸汽量100t/h。
表1各实施例和对比例的参数设置
由表1可以看出,在合成气处理量以及合成气进出口温度均相同的情况下,实施例1~2的辐射废锅的高度均较对比例1有大幅下降,其中实施例1的高度下降超过50%,实施例2的废锅高度较对比例1下降33%。
本文用于企业家、创业者技术爱好者查询,结果仅供参考。