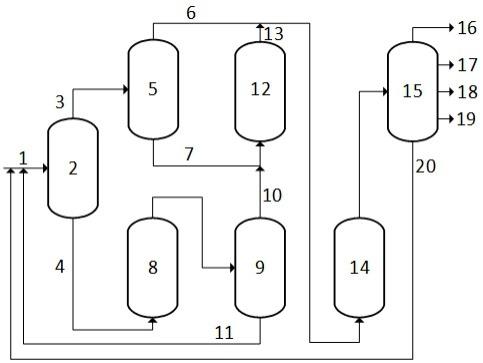
1.本方面属于石油化工技术领域,涉及一种用于劣质原料油轻质化处理工艺及系统。
背景技术:
2.目前炼油行业关注的重点是如何将重质稠油尽可能多地转化成轻质油品,进而实现炼厂效益的最大化。脱碳和加氢工艺是目前最重要的两种重油轻质化途径,脱碳工艺主要包括焦化工艺、溶剂脱沥青工艺,加氢工艺主要包括固定床加氢、沸腾床加氢等工艺,然而各加工工艺都有其优缺点,如焦化工艺对原料性质苛刻度很低,然而其油品性质差,同时会生产出大量低附加值高硫焦,固定床加氢生产油品性质较好,但是也存在对原料适应性差、空速低、运行周期短等问题,沸腾床加氢工艺对原料适应性强,催化剂可在线置换,同样也存在产品脱氮等效果差,反应过程中容易形成不溶物,导致装置和管线结焦,影响装置的长周期运行,溶剂脱沥青为物理抽提过程,无催化系统,不存在催化剂中毒和失活问题,可加工性质很差的重油,然而其只是物理分离过程,没有从结构上将大分子烃类转化成小分子。如何根据各加工工艺的特性,将不同工艺进行合理组合,是目前应对重油轻质化最有效的加工途径。
3.cn108018080、cn 108138057等专利公开了几种重油加工组合工艺,基本都是对现有加工工艺的简单组合,没有能够有效地根据重油中不同馏分的特性进行针对性的加工处理。分子炼油技术是近年来炼油界提出的一种突破传统的石油馏分粗放认知的全新炼油理念,从分子水平上认识、加工和管理石油资源,进而实现石油加工过程的精细化管理,达到“宜油则油、宜烯则烯、宜芳则芳”的目标。对于重油来说,现有的分析表征手段还不足以达到对其分子水平上的表征,但是依然可以将分子炼油理念应用到重油的加工过程优化中。多年研究表明,重油结构主要是由饱和分、芳香分、胶质和沥青质组成,它们形成了以沥青质为中心,往外延伸依次为胶质、芳香分和饱和分的胶体结构。如何能够现有工艺手段将不同特性的组分分子合理加工,进而最大限度实现重油轻质化,同时大幅度延长装置的运转周期,是当前炼油行业面临的技术革新问题。
技术实现要素:
4.针对现有技术中的不足之处,本发明提供了一种劣质原料油轻质化处理工艺及系统,所述处理工艺根据劣质原料油中烃类组成差异和处理工艺属性,实现了脱碳工艺和加氢工艺在劣质原料油轻质化中有机结合,最大限度实现劣质原料油轻质化,同时大幅度延长装置的运转周期。
5.本发明提供一种劣质原料油轻质化处理工艺,所述处理工艺包括如下内容:(1)劣质原料油进入溶剂脱沥青单元,与溶剂a接触处理后得到脱沥青油和脱油沥青;(2)脱沥青油进入脱胶质单元,在超临界条件下与溶剂b接触处理后得到第一轻馏分和第一重馏分;
(3)步骤(1)得到的脱油沥青、任选的催化柴油与氢气混合后进入沸腾床加氢反应区进行反应,反应流出物经分离后得到第二轻馏分和未转化尾油;(4)步骤(2)得到的第一重馏分和步骤(3)得到的第二轻馏分与氢气混合后进入加氢处理反应区进行反应;(5)步骤(2)得到的第一轻馏分和步骤(4)得到的加氢反应流出物混合后进入催化裂化反应区进行反应,反应流出物分离后得到干气、液化气、催化汽油、催化柴油、催化重油。
6.上述劣质原料油轻质化处理工艺中,步骤(3)中得到的未转化尾油可以全部或部分循环回溶剂脱沥青单元与劣质原料油混合处理,优选全部循环回溶剂脱沥青单元。
7.上述劣质原料油轻质化处理工艺中,步骤(1)中所述劣质原料油包括常压渣油、减压渣油、油田稠油、重质燃料油、油砂等中的一种或几种,同时进料中可掺炼催化油浆、减压蜡油或糠醛抽出油中的一种或几种。
8.上述劣质原料油轻质化处理工艺中,步骤(1)中溶剂脱沥青单元所使用的抽提溶剂a为烷烃或轻石脑油馏分,所示烷烃具体可以是丙烷、丁烷、戊烷、己烷、庚烷中的一种或几种,优选为丁烷和/或戊烷。溶剂脱沥青单元的操作条件为:温度为100~200℃,优选120~160℃,压力为2.0~6.0mpa,优选3.0~5.0mpa,溶剂体积比为1.0~10.0,优选3.0~8.0。进一步优选,所示脱油沥青中烃类组分中饱和分不高于20wt%。
9.上述劣质原料油轻质化处理工艺中,步骤(2)中所述脱胶质单元中使用的溶剂b包括烷烃和助剂,所述助剂含量为0.1-5wt%;所示烷烃具体可以是丙烷、丁烷、戊烷、己烷、庚烷中的一种或几种,优选为丙烷,所述助剂为马来酸双十八酯、烷基酚聚氧乙烯醚、辛基酚聚氧乙烯醚的一种或几种,优选为马来酸双十八酯。所述脱胶质单元的温度为100~200℃,压力为5.0~10.0mpa,优选为6.5~10.0mpa;所述脱胶质单元的温度和压力要保证溶剂b的处于超临界状态。一般脱沥青油和溶剂的体积比一般为5~15,优选7~10;通过控制压力来调整第一轻馏分的收率和残炭值,一般要求第一轻馏分的残炭值不高于5.0wt%。所述脱胶质单元可以采用管式沉降塔,可根据原料情况在沉降塔中还可以添加填料,填料一般选择自于格栅、拉西环、鲍尔环中的一种或几种,优选为格栅。
10.上述劣质原料油轻质化处理工艺中,步骤(3)中沸腾床加氢反应区操作条件为:反应温度350~450℃,优选400~440℃,反应压力10.0~18.0mpa,优选15.0~18.0mpa,氢油体积比500~2000,优选800~1500,液时体积空速0.1~5.0h-1
,优选0.2~2.0h-1
。
11.上述劣质原料油轻质化处理工艺中,步骤(3)中沸腾床加氢反应区包括1个以上沸腾床反应器,优选设置1或2个沸腾床反应器,当设置2个以上沸腾床反应器时,物料依次通过串联设置的反应器。所述沸腾床反应器内装填有沸腾床加氢催化剂,所述催化剂包括载体和活性金属,其中活性金属可以为镍、钴、钼或钨中的一种或几种;载体可以为氧化铝、氧化硅、氧化铝-氧化硅、氧化钛中的一种或几种。所述催化剂堆密度为0.3~0.8g/cm3,颗粒直径(球形直径或条形直径)为0.3~1.0mm,比表面积为80~120m2/g,催化剂具有双峰分布的孔结构,其中,孔直径在5~50nm 的孔容占总孔容的30~65%,孔直径大于100nm的孔容占总孔容的20~35%。
12.上述劣质原料油轻质化处理工艺中,步骤(3)中所述催化柴油循环量占沸腾床加氢反应区总进料重量的比例不超过20wt%。
13.上述劣质原料油轻质化处理工艺中,沸腾床加氢反应区得到的反应流出物中金属
含量小于150μg/g,优选小于100μg/g,沸腾床加氢反应流出物进入分馏装置经分离后得到第二轻馏分和未转化尾油,所述第二轻馏分和未转化尾油的分馏点为450~550℃,其中,第二轻馏分的金属含量不大于80μg/g。
14.上述劣质原料油轻质化处理工艺中,步骤(4)中所述加氢处理反应区的操作条件为:反应温度为350℃~420℃,优选为350℃~400℃;反应压力为10mpa~ 25mpa,优选为10mpa~15mpa;氢油体积比为300~1500,优选为500~800;液时体积空速为0.15h-1
~2h-1
,优选为0.3h-1
~1h-1
。
15.上述劣质原料油轻质化处理工艺中,步骤(4)中所述加氢处理反应区设置1个或多个反应器,优选设置1或2个反应器。所述反应器可以采用固定床反应器、悬浮床反应器、流化床反应器、沸腾床反应器中的一种或几种。反应器内装填的加氢催化剂为本领域现有加氢催化剂,其中活性金属含有第vib族金属和/或viii族金属中的至少一种,载体含有氧化铝、无定型硅铝和二氧化硅中的至少一种。
16.上述劣质原料油轻质化处理工艺中,步骤(5)中所述催化裂化反应区包括至少一套催化裂化装置,每套装置至少包括一个反应器、一个再生器和一个分馏塔。催化裂化催化剂为硅铝催化剂、硅镁催化剂、酸处理后的白土、x型分子筛、zsm-5分子筛等裂化催化剂中的一种。
17.上述劣质原料油轻质化处理工艺中,步骤(5)中所述催化裂化反应区的操作条件为:反应温度450~600℃,再生温度600~800℃,剂油重量比2~30,反应时间0.1~15秒,反应压力0.1~0.5mpa。催化裂化生成油进分离后得到干气、液化气、催化汽油、催化柴油、催化重油,其中至少部分催化重油循环到溶剂脱沥青单元,催化重油循环量占催化重油总量的重量比为0.4~1.0。
18.本发明第二方面提供一种劣质原料油轻质化处理系统,所述系统包括:溶剂脱沥青单元:其用于接收重质原料油和溶剂a,处理后得到脱沥青油和脱油沥青;脱胶质单元:其用于接收并处理来自溶剂脱沥青单元的脱沥青油和溶剂b,处理后得到第一轻馏分和第一重馏分;沸腾床加氢反应区:其用于接收来自溶剂脱沥青单元的脱油沥青和氢气,在沸腾床加氢催化剂作用下进行加氢反应,得到反应流出物;第一分离系统:其用于接收并分离处理来自沸腾床加氢反应区的反应流出物,分离后得到第二轻馏分和未转化尾油;加氢处理反应区:其用于接收来自预处理单元的第一重馏分和来自第一分离系统的第二轻馏分与氢气,在催化剂作用下进行反应得到反应流出物;催化裂化反应区:其用于接收并处理来自预处理单元的第一轻馏分和来自加氢处理反应区的反应流出物,处理后得到干气、液化气、催化汽油、催化柴油、催化重油。
19.上述劣质原料油轻质化处理系统中,催化柴油经管线循环回沸腾床加氢反应区。
20.上述劣质原料油轻质化处理系统中,催化重油经管线循环回溶剂脱沥青单元。
21.上述劣质原料油轻质化处理系统中,所述溶剂脱沥青单元采用现有溶剂脱沥青装置,所述溶剂脱沥青装置可以设置一个以上,当设置两个以上溶剂脱沥青装置时,以串联方式连接。
22.上述劣质原料油轻质化处理系统中,所述脱胶质单元可以采用管式沉降塔,可根
据原料情况在沉降塔中添加填料,填料一般选择自于格栅、拉西环、鲍尔环中的一种或几种,优选为格栅。
23.上述劣质原料油轻质化处理系统中,沸腾床加氢反应区包括1个以上沸腾床反应器,优选设置1或2个沸腾床反应器,当设置2个以上沸腾床反应器时,物料依次通过串联设置的反应器。
24.上述劣质原料油轻质化处理系统中,所述加氢处理反应区设置1个或多个反应器,优选设置1或2个反应器。所述反应器可以采用固定床反应器、悬浮床反应器、流化床反应器、沸腾床反应器中的一种或几种。
25.上述劣质原料油轻质化处理系统中,所述催化裂化反应区包括至少一套催化裂化装置,每套装置至少包括一个反应器、一个再生器和一个分馏塔。
26.与现有技术相比,本发明劣质原料轻质化处理工艺及系统具有以下优点:1、本发明劣质原料轻质化处理工艺及系统中,将脱碳和加氢工艺有机地结合在一起,能够灵活的处理不同劣质重质原料油。
27.2、本发明劣质原料轻质化处理工艺及系统中,创新地设置脱胶质单元,实现重油中稳定性较差的胶质、沥青质、油分三相之间的分离,进而减缓其随脱油沥青进入沸腾床加氢单元处理时造成其过多地转化成沥青质,造成重油整体加工流程的轻油收率较低,同时也可避免胶质与油分直接进催化裂化单元而导致的催化剂结焦严重,影响催化裂化的产品分布和性质。
28.3、本发明劣质原料轻质化处理工艺及系统中,溶剂脱沥青单元中采用高萃取率操作模式,使得脱油沥青中油分和胶质含量尽可能低,从而完成沥青质相的分离;同时在脱油沥青沸腾床加氢过程中,掺炼部分具有供氢效果的催化柴油馏分,可以有效地降低加氢过程结焦发生,实现装置长周期平稳运行。
29.4、本发明劣质原料轻质化处理工艺及系统中,脱胶质单元得到的富含胶质组分的第一重馏分和第二轻馏分混合进入加氢处理单元,第二轻馏分是富氢馏分和良好的胶质溶剂,第一重馏分中胶质组分能够很好地在第二轻馏分中分散溶解,然后在加氢催化剂的作用下,较大程度地实现胶质向轻质油分的转化,大大抑制结焦现象的发生。
附图说明
30.图1 为本发明劣质原料油轻质化处理工艺与系统的示意图。
31.其中1-原料,2-溶剂脱沥青单元,3-脱沥青油,4-脱油沥青,5-脱胶质单元,6-第一轻馏分,7-第一重馏分,8-沸腾床加氢反应区,9-分离单元,10-第二轻馏分,11-未转化尾油,12-加氢处理反应区,13-加氢处理生成油,14-催化裂化反应区,15-分馏单元,16-干气,17-液化气,18-催化汽油,19-催化柴油,20-催化重油。
具体实施方式
32.下一步通过实施例进一步描述本发明的技术特点,但这些实施例不能限制本发明。
33.如图1所示,本发明提供一种劣质原料油轻质化处理工艺,所示处理工艺内容为:渣油原料1进入溶剂脱沥青单元2,与溶剂接触处理后得到脱沥青油3和脱油沥青4;脱沥青
油3进入脱胶质单元5,在轻烃超临界条件萃取下得到第一轻馏分6和第一重馏分7;脱油沥青4、催化柴油20(由于管线图中没有画出直接将其返回8的管线)与氢气混合后进入沸腾床加氢反应区8进行反应,反应流出物经分离单元9后得到第二轻馏分10和未转化尾油11;第一重馏分7和第二轻馏分10与氢气混合后进入加氢处理反应区12进行反应;第一轻馏分6和加氢反应流出物混合13后进入催化裂化反应区14进行反应,反应流出物进入分馏单元15分离后得到干气16、液化气17、催化汽油18、催化柴油19、催化重油20,其中催化重油20和未转化油11全部循环回溶剂脱沥青单元2中。
34.以下实施例和对比例中使用劣质原料油为渣油,其性质见表1。沸腾床加氢反应区采用的为抚顺石油化工研究院开发的fes-30催化剂。所述加氢处理反应区采用常规固定床反应器,催化剂采用为fripp研发的ff-80牌号催化剂。催化裂化单元采用常规的提升管反应器,催化剂采用为长岭催化剂公司开发的dfc-1催化剂。
35.表1 渣油原料的性质性质数据密度(20℃),kg.m-3
1025.3硫含量,w%5.36氮含量,w%0.3964(ni v)含量,μg.g-1
192.3胶质 沥青质36.7残炭,w$.65实施例1实施例1采用本发明图1所示工艺流程,其中溶剂脱沥青单元使用的溶剂a为正丁烷和正戊烷混合溶剂,其中正戊烷重量分数50%,抽提温度135℃,压力4.0mpa,剂油体积比5.0;脱胶质单元使用的溶剂b为丙烷和马来酸双十八酯复配溶剂,丙烷含量为95wt%;抽提温度115℃,压力10mpa,剂油体积比6.0。沸腾床加氢反应区设置两个沸腾床加氢反应器,以串联方式连接,反应压力16mpa,氢油体积比800,其中第一反应器反应温度410℃,液时体积空速0.35h-1
,第二反应器反应温度420℃,液时体积空速0.4h-1
。加氢处理反应区采用固定床反应器,平均床层温度为350℃,压力10mpa,氢油体积比为600,液时体积空速为0.5。催化裂化反应区的反应温度485℃,再生温度690℃,剂油重量比8.2,反应压力0.2mpa。产品分布见表2。
36.实施例2实施例2采用本发明图1所示工艺流程,其中溶剂脱沥青单元使用的溶剂a为正丁烷溶剂,抽提温度125℃,压力4.0mpa,剂油体积比5.0;脱胶质单元使用的溶剂b为丙烷和马来酸双十八酯复配溶剂,丙烷含量为99wt%;抽提温度110℃,压力7mpa,剂油体积比10.0。沸腾床加氢反应区设置两个沸腾床加氢反应器,以串联方式连接,反应压力16mpa,氢油体积比800,其中第一反应器反应温度405℃,液时体积空速0.35h-1
,第二反应器反应温度420℃,液时体积空速0.4h-1
。加氢处理反应区采用固定床反应器,平均床层温度为380℃,压力15mpa,氢油体积比为600,液时体积空速为0.5。催化裂化反应区的反应温度485℃,再生温度690℃,剂油重量比8.2,反应压力0.2mpa。产品分布见表2。
37.对比例1
与实施例1基本相同,不同之处在于对比例2中没有设置脱胶质单元,脱沥青单元的脱沥青油全部与第二轻馏分混合进入加氢处理反应区进行处理,产品分布见表2。
38.表2 实施例和比较例中产品分布比较
再多了解一些
本文用于企业家、创业者技术爱好者查询,结果仅供参考。