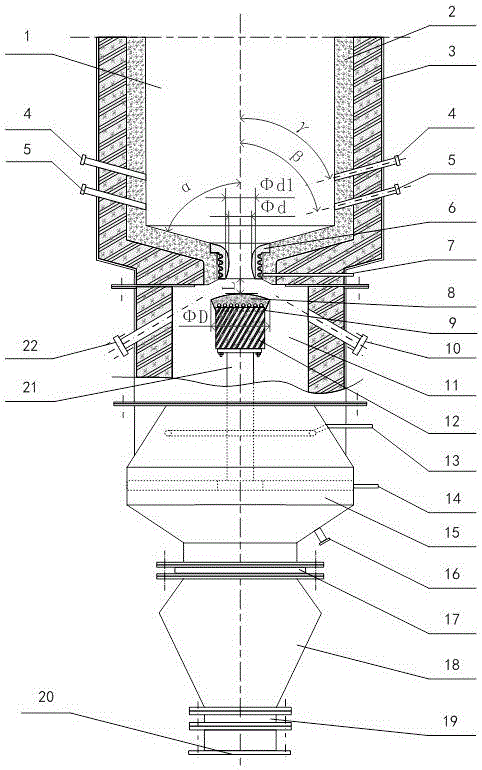
本实用新型涉及固废资源化利用处理领域,具体涉及到一种含热值废弃物固定床热解气化熔融排渣装置,可消除二噁英在炉渣中的生成和解决炉渣中重金属等有害物质带来的二次污染问题。
背景技术:
废弃物成分复杂,例如,城市生活垃圾,含有机氯化物(如聚氯乙烯塑料、氯苯等)和无机氯化物(如厨余垃圾中的氯化钠,氯化镁)等。氯元素的存在是产生二噁英的主要因素。二噁英是一族物质的总称,有剧毒,其毒性因各种异构体的不同而不同,其中毒性最强的是2、3、7、8—四氯二苯并二恶英,其毒性相当于氰化钾的1000倍。二噁英均为固体,熔点高,难溶于水,易溶于脂肪,易在生物体内积聚,能引起皮肤座疮、头痛、失聪、忧郁、失眠等症状。即使是很微量的情况下,长期摄取也会引起癌症、畸形等,因此,被称为世界上最毒的物质。二噁英产生主要有种情况:①不完全燃烧。垃圾在干燥过程中和燃烧初始阶段,当氧气含量充足时,垃圾中低沸点的烃类,气化或燃烧生成co、co2、h2o,但若氧气不足,就会生成二噁英前驱物,这些前驱物与垃圾中的氯化物、o2、氧离子进行复杂的热反应,生成二噁英物质。②燃烧后生成。不完全燃烧产生的二噁英前驱物以及垃圾中未燃尽的环烃物质在烟尘中的cu、ni、fe等金属颗粒催化作用下,与烟气中的氯化物和o2发生反应生成二噁英类物质,催化反应温度为300℃左右。
二噁英的熔点在303~306℃,沸点在421.2~446.5℃,裂解在700℃以上,目前关于二噁英裂解普遍看法是在850℃左右环境下停留2秒,或是在1000℃环境停留1秒,被认为二噁英可以完全裂解。所以,采用熔融排渣气化技术,熔融高温环境可以裂解二噁英,采用熔渣激冷避开前驱物生成二噁英的温度环境,从而抑制二噁英的产生。
目前城市生活垃圾的处理主要采用卫生填埋(占比约60%)和焚烧(占比约35%)。卫生填埋主要缺点:①占用土地;②可降解的有机物比例有限,资源化利用率低;③大量剩余垃圾及沼液不能有效处理(或处理代价高),仍对环境存在污染问题。与气化技术相比,焚烧的主要缺点:①炉渣中含有二噁英,对环境污染相对严重,处理代价高;②垃圾中的c元素不能充分利用,资源化利用率低,垃圾减量比低。
我国目前一些固废气化技术的研究大部分采用排灰方式,导致炉灰中的二噁英含量超标。我国生活垃圾热值较发达国家偏低,城市生活垃圾的热值普遍在4000kj/kg左右,只有在沿海发达地区新型住宅区所产生垃圾的热值才达到5500~8000kj/kg之间,给熔融排渣气化带来困难。针对我国生活垃圾热值偏低的特点,一些科研单位开发了先将煤和生活垃圾进行混合配料再进行熔融排渣气化的技术。对于气化而言,一般先将垃圾制成rdf粒料来增强气化反应动力学,但将煤和生活垃圾进行混合配料后会增加rdf制作的难度和成本。
废弃物气化源于煤气化技术,但煤的热值普遍高于生活垃圾,相对易于实现熔融排渣气化。目前bgl煤气化技术采用熔融排渣方式,但也存在排渣方式控制复杂,设备制造加工难度大,部分关键设备需要进口,运行可靠性低且投资大等问题。仍是制约其在工业固废、危险废弃物、生活垃圾等热解气化处理主要副产物灰渣无害化和技术商业化应用的瓶颈。
技术实现要素:
本实用新型的目的是在现有技术的基础上提出一种含热值废弃物固定床热解气化熔融排渣装置,用于废弃物资源化利用处理过程中消除二噁英在炉渣中的生成和解决炉渣中重金属等有害物质带来的二次污染问题。
为实现上述目的,本实用新型采用如下技术方案:
一种含热值废弃物固定床热解气化熔融排渣装置,包括:相互连接的氧化段熔渣室和过渡段,所述氧化段熔渣室上设置有若干个气化剂喷嘴,
所述氧化段熔渣室上设置有若干个燃气烧嘴,用于向氧化段熔渣室提供热量,
所述氧化段熔渣室的底部设置有渣口装置,
所述在过渡段内设置有支架用于支撑阻挡装置,所述阻挡装置设置在渣口装置的下方,阻挡装置与渣口装置构成连通氧化段熔渣室与过渡段之间的熔渣流道,
所述渣口装置与所述阻挡装置均为电加热装置。
在上述技术方案中,所述渣口装置与所述阻挡装置同轴设置,渣口装置与所述阻挡装置之间形成环型熔渣流道。
在上述技术方案中,所述渣口装置的内侧为流线型喇叭口结构,渣口装置的外侧沿着周向设有电加热结构,所述渣口装置的外侧与熔渣室的内壁固定连接并可拆卸维护。
在上述技术方案中,所述阻挡装置包括绝热块和设置在绝热块上的加热头,所述加热头与绝热块之间设置有电加热体。
在上述技术方案中,所述加热头为球面结构,加热头的球面与渣口装置的喇叭口之间形成喇叭环型熔渣流道。
在上述技术方案中,所述氧化段熔渣室内的下端为锥形结构,锥型斜面与氧化段熔渣室中心轴线呈呈α角度,α角为10~45°夹角,若干个燃气烧嘴在同一圆周方向布置着,在氧化段熔渣室的下部、气化剂喷嘴下方设置。
在上述技术方案中,所述所有的燃气烧嘴的中心轴线的俯视投影与渣口装置的渣口上口外缘相切,且燃气烧嘴与氧化段熔渣室中心轴线呈呈β角,β角为45~80°夹角。
在上述技术方案中,所述燃气烧嘴为两通道结构,同时提供燃气与氧气。
在上述技术方案中,熔渣激冷室通过法兰结构连接在过渡段下方,且从氧化段熔渣室流出处的熔渣通过过渡段的阻挡装置后直接进入所述熔渣激冷室。
综上所述,由于采用了上述技术方案,本实用新型的有益效果是:
由于在气化炉氧化段熔渣室设置燃气烧嘴向气化炉氧化段熔渣室补充热量,满足低热值废弃物熔融气化对热量的需求;在气化炉氧化段熔渣室底部设置电加热渣口装置和在过渡段设置加热球头使熔渣不会产生冷凝,实现熔融排渣;采用熔渣激冷,消除前驱物生成二噁英的温度环境,并使炉渣中的重金属得以由炉渣封存,解决了二次污染问题。
附图说明
本实用新型将通过例子并参照附图的方式说明,其中:
图1是本实用新型的结构示意图;
其中:1是气化炉氧化段熔渣室;2是耐火保护衬里;3是耐火保温层;4是气化剂喷嘴;5是燃气烧嘴;6是渣口装置;7是渣口装置导线引出孔;8是加热球头;9是球头阻挡装置;10是视镜安装口;11是过渡段;12是绝热块;13是进水管;14是加热头导线引出孔;15是熔渣激冷室;16是出水口;17是上渣阀;18是渣锁;19是下渣阀;20是排渣口;21是支架;22是点火器烧嘴。
具体实施方式
本说明书中公开的所有特征,或公开的所有方法或过程中的步骤,除了互相排斥的特征和/或步骤以外,均可以以任何方式组合。
本说明书(包括任何附加权利要求、摘要和附图)中公开的任一特征,除非特别叙述,均可被其他等效或具有类似目的的替代特征加以替换。即,除非特别叙述,每个特征只是一系列等效或类似特征中的一个例子而已。
现在将参照附图描述本实用新型的实施例。下列描述本质上仅仅是示例性的,并不限于本实用新型及其应用或使用。
如图1所示,本实用新型包括气化炉氧化段及熔渣室1、气化剂喷嘴安4、燃气烧嘴5、渣口装置6、渣口装置导线引出孔14过渡段11、视镜安装口10、球头阻挡装置9、加热头导线引出孔14、熔渣激冷室15、进水管13、出水口16、上渣阀17、渣锁18、下渣阀19、排渣口20。
炉氧化段及熔渣室1、渣口装置6、过渡段11、熔渣激冷室15、上渣阀17、渣锁18、下渣阀19及排渣口20均采用法兰连接。
气化炉氧化段及熔渣室1底部内部外形为锥型,锥型斜面与中心轴线呈α角度,α角为10~45°。
气化炉氧化段及熔渣室1为至少三层结构,内壁层为耐火保护衬里,中间层为耐火保温层,外层为炉体金属外壳体。耐火保护衬里和所述耐火保温层均采用气化炉领域常规材料。耐火保护衬里可以采用耐温不低于1500℃高温和耐液渣冲刷的耐火材料,具体为刚玉、高铬、碳化硅或氮化硅结合碳化硅。
气化剂喷嘴4为偶数个,在同一水平面均匀布置,其中心轴线向下倾斜角度呈γ角,γ角为45~80°。所安装的所有气化剂喷嘴的中心轴线的俯视投影与渣口装置的渣口上口外缘相切,且周向偏向为一个方向。燃气烧嘴安装口为偶数个,在同一水平面均匀布置,其中心轴线向下倾斜角度呈β角,β角为45~80°。所安装的所有气化剂喷嘴的中心轴线的俯视投影与渣口装置的渣口上口外缘相切,且周向偏向为一个方向。
燃气烧嘴安装口位于气化剂喷嘴安装口的下方。烧嘴为两通道结构,一个通道为富氧,另一个通道为燃气,燃气所用燃气为气化炉自产燃气或天然气(或液化气),在气化炉启动初期用天然气或液化气,正常工作状态用气化炉自产燃气,由控制系统程序切换,且供给压力或流量由控制系统自动调节。烧嘴为渣池提供热量,补充渣池底部因灰渣热值低、气化剂温度相对较低条件下,熔渣所需能量。
渣口装置6的渣口流道采用流线型喇叭口设计,流道最小部位尺寸为φd,φd为φ20~φ80mm。材料选用耐高温且热传导系数较高材料(具体为刚玉),烧结制作而成,其外侧周向设置能固定电加热体的结构,电加热体选用工作温度不低于1200℃的电加热体,安装b型或s型温度传感器。渣口装置设置加热体和温度传感器导线引出孔14,由控制系统实现温度闭环控制,使熔渣流道保持相应的温度,以防止熔渣经过流道时产生冷凝。渣口装置的设计满足可更换,便于维护。电加热体具体为cr20ni80电阻丝、硅碳棒、硅钼棒或石墨棒等。渣口装置固定电加热体的外侧的设计,要求电加热体置于相对密封的空间内,避免高温氧化降低电加热体使用寿命。渣口装置温度控制系统周波pwm控制,须可实现温度缓慢升/降。
过渡段11设置视镜安装口10和点火器烧嘴安装口22。
球头阻挡装置9位于渣口装置6正下方,过渡段11内,由加热球头8、绝热块12和支架21组成,加热球头8与渣口装置6的排渣下口形成喇叭环型熔渣流道。加热球头8采用耐高温且热传导系数较高材料(刚玉),烧结制作而成,底部安装电加热体,并设置b型或s型温度传感器,由控制系统实现温度闭环控制,使熔渣流经球头阻挡装置9时保持相应的温度,以防止熔渣流经渣口装置6的下渣口与加热球头8形成的流道时产生冷凝。加热球头8的俯视投影尺寸φd为d1~(d1 100)。加热球头8顶部距离渣口装置6底部尺寸为l,l尺寸为20~60mm。球头阻挡装置9的绝热块12位于加热球头8下方,用于支撑和固定加热球头8,选用耐高温且热传导系数较低的材料,制作而成。绝热块12下方为金属支架,用于固定加热球头8和绝热块12。电加热体具体为cr20ni80电阻丝、硅碳棒、硅钼棒或石墨棒等。设置进出线孔,加热球头8的电加热线缆和温度传感器的线缆经进出线孔由导线引出孔14引出,接入温度控制系统。加热球头固定电加热体的一侧的设计,要求电加热体置于相对密封的空间内,避免高温氧化降低电加热体使用寿命。加热球头的设计满足可更换,便于维护的原则。加热球头温度控制系统周波pwm控制,须可实现温度缓慢升/降。
熔渣激冷室15通过法兰连接于过渡段下方,熔渣通过过渡段后进入熔渣激冷室快速激冷,避开二噁英前驱物生成二噁英的温度条件,避免二噁英在炉渣中的生成。激冷室水温和水位由外部循环水供给系统自动控制。
熔渣激冷室15底部通过法兰连接上渣阀17。上渣阀17通过法兰连接下部的渣锁18。在渣锁18底部连接下渣阀19。下渣阀19通过法兰连接下部排渣口。控制系统对上渣阀和下渣阀互锁控制。根据激冷室的水位判断激冷室内渣量,当渣量达到设定值时,控制系统协调控制激冷室外部循环水供给系统和上渣阀,打开上渣阀使激冷后的炉渣进入渣锁储存。当渣锁内达到设定量时,打开下渣阀使炉渣由排渣口排出炉外。
以上仅为的实用新型的具体实施例,但本实用新型的技术特征并不局限于此。任何以本实用新型为基础,为解决基本相同的技术问题,实现基本相同的技术效果,所作的简单变化,皆涵盖与本实用新型的保护范围之中。本实用新型并不局限于前述的具体实施方式。本实用新型扩展到任何在本说明书中披露的新特征或任何新的组合,以及披露的任一新的方法或过程的步骤或任何新的组合。
本文用于企业家、创业者技术爱好者查询,结果仅供参考。