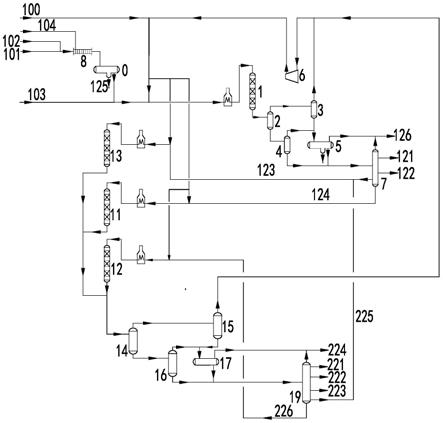
1.本发明属于费托合成产品加工领域,涉及一种提高费托合成油品生产柴油的工艺的柴油收率的方法。
背景技术:
2.近年来,随着石油资源的日趋枯竭,寻找替代能源已成为一项国家战略性的课题。我国煤炭资源丰富,发展煤制油化工产业,对于缓解石油供需矛盾,实现煤炭清洁利用具有重要意义。费托合成油品与常规石油衍生物相比,组成以直链烃类为主,具有低硫、低氮、无芳烃,含有一定量的含氧化合物等特点。由于费托合成油品含有一定量的酸,因此费托合成油品加氢之前的设备、管线、仪表、管件等材料选择为不锈钢材质,这样大大的增加了工程建设投资。另外,费托合成重组分馏程范围宽,直链烃组成易裂解,在加氢异构裂化过程中容易发生过度裂化生成石脑油和lpg,降低柴油收率。
3.cn104560136b公开了一种费托合成蜡的异构加氢裂化方法,该方法以费托合成蜡为原料,在异构加氢裂化反应器内注入氢气和氨气的混合气体,通过控制异构加氢裂化反应器内氨浓度梯度,改善异构加氢裂化催化剂温度敏感性,提高中间馏分油的收率。然而,控制反应器内氨浓度梯度,需采用新鲜氢一次通过模式,不设置循环氢回路,此模式不适合应用在工业生产中。由于费托油品中含有较高含量的烯烃和含氧化合物,原料管线、仪表、设备等需要选择不锈钢材质,极大增加了装置投资。另外不经过加氢的原料直接与异构裂化催化剂接触,容易导致催化剂局部放热量过大,造成催化剂结焦失活,影响催化剂的稳定性和运转周期,且得到的产品质量较差。此外,异构产物中大于370℃馏分直接循环回裂化反应器,未经过降凝,造成了部分重柴油裂解为石脑油,柴油收率降低。
4.cn103146426b提供了一种费托合成产物转化为石脑油、柴油和液化气的方法。该工艺直接将费托油品先经过加氢精制反应器,精制反应产物经过分馏后得到柴油、重油和精制尾油。精制重油去降凝反应器,精制尾油去裂化反应器。降凝反应产物和裂化反应产物混合经过分馏后得到裂化柴油、裂化重油和裂化尾油,裂化重油和裂化尾油作为循环油返回裂化反应器。裂化重油和尾油循环裂化工艺会造成裂化重油的过度裂解,降低柴油收率。而且,如上文所述,费托油品直接进行加氢精制由于费托油品的特性不仅会增加装置投资,另外费托油品在后续会过度裂化,造成柴油的收率较低且得到的产品质量较差。
5.因此,需要开发出能够更进一步提高柴油产品收率的方法。
技术实现要素:
6.针对现有技术中存在的上述技术问题,本发明人通过研究发现,在利用费托合成油品生产柴油的过程中,如果预先对费托合成轻质油和费托合成重质油进行氨水中和,并将从加氢精制反应产物中分离出的精制尾油以及从降凝反应产物和裂化反应产物中分离出的裂化尾油分别进行裂化反应,不仅能够降低设备等的投资,而且还能明显地提高作为期望的终产品的柴油的收率。
7.本发明的目的在于提供了一种提高费托合成油品生产柴油的工艺的柴油收率的方法,其中,该方法包括:
8.(1)将费托合成轻质油和费托合成重质油先进行氨水中和,中和后的物料经油水分离后,油相部分与费托合成重质蜡混合,得到的混合物与氢气混合后进行加氢精制反应,得到加氢精制反应产物;
9.(2)将所述加氢精制反应产物进行气液分离和分馏,得到精制石脑油、精制柴油、精制重油、精制尾油和释放气;
10.(3)使所述精制尾油进行裂化反应,得到裂化反应产物;
11.(4)使所述精制重油进行降凝反应,得到降凝反应产物;
12.(5)将所述降凝反应产物和裂化反应产物进行裂化分离和分馏,得到lpg、裂化石脑油、裂化柴油、裂化重油、裂化尾油和干气;以及
13.(6)使部分或全部的所述裂化尾油进行裂化反应,得到的裂化反应产物返回步骤(5)进行裂化分离和分馏;所述裂化重油返回步骤(4)与精制重油混合进行降凝反应。
14.另一方面,本发明提供了一种用于实施上述方法的装置,其中,该装置包括:
15.氨水中和单元;
16.加氢精制单元,所述加氢精制单元以流体的连通方式连接至所述氨水中和单元;
17.降凝反应单元,所述降凝反应单元以流体的连通方式连接至所述加氢精制单元;以及
18.裂化单元,所述裂化单元以流体的连通方式连接至所述加氢精制单元和所述降凝反应单元,并且包括分别用于对精制尾油和裂化尾油进行裂化处理的两个分开设置的加氢裂化反应器。
19.有益效果
20.(1)将费托合成轻质油和费托合成重质油先进行氨水中和,一方面降低了加氢精制反应器之前的设备、管线、仪表、管件等的投资,另一方面能够部分抑制后续的裂化反应和降凝反应的催化剂的活性,从而可降低这两种催化剂的床层温升,抑制原料过度裂化,提高了柴油的收率。
21.(2)通过将裂化重油返回与精制重油一起进行降凝反应,可利用降凝反应催化剂对重油的异构与缓和裂化作用,将重油高收率地转化为裂化柴油,从而进一步提高了柴油收率。
22.(3)由于精制尾油含有约95wt%以上的正构烷烃,裂化尾油含有约85wt%以上的异构烷烃,正构烷烃和异构烷烃的裂化温度不同,将精制尾油和裂化尾油分别进行裂化反应,通过控制二者具有不同的反应温度,进一步提高了柴油收率。
附图说明
23.图1为本发明的示例性的能够以高的柴油收率从费托合成油品生产柴油的装置的示意图;
24.图2为本发明的比较例2的从费托合成油品生产柴油的装置的示意图;
25.其中,各附图标记分别表示:
26.0油水分离器;1加氢精制反应器;2精制热高压分离器;3精制冷高压分离器;4精制
热低压分离器;5精制冷低压分离器;6循环氢压缩机;7精制分馏系统;8氨水中和单元;11,12加氢裂化反应器;13降凝反应器;14裂化热高压分离器;15裂化冷高压分离器;16裂化热低压分离器;17裂化冷低压分离器;19裂化分馏系统。
27.100新鲜氢;101费托合成轻质油;102费托合成重质油;103费托合成重质蜡;104氨水;121精制石脑油;122精制柴油;123精制重油;124精制尾油;125污水;126释放气;221液化石油气;222裂化石脑油;223裂化柴油;224裂化干气;225裂化重油;226裂化尾油。
具体实施方式
28.在下文中,通过示例性的实施方式对本发明进行说明,但是本发明的保护范围并不限于此。
29.在一个实施方式中,本发明涉及一种提高费托合成油品生产柴油的工艺的柴油收率的方法,其中,该方法包括:
30.(1)将费托合成轻质油和费托合成重质油先进行氨水中和,中和后的物料经油水分离后,油相部分与费托合成重质蜡混合,得到的混合物与氢气混合后进行加氢精制反应,得到加氢精制反应产物;
31.(2)将所述加氢精制反应产物进行气液分离和分馏,得到精制石脑油、精制柴油、精制重油、精制尾油和释放气;
32.(3)使所述精制尾油进行裂化反应,得到裂化反应产物;
33.(4)使所述精制重油进行降凝反应,得到降凝反应产物;
34.(5)将所述降凝反应产物和裂化反应产物进行裂化分离和分馏,得到lpg、裂化石脑油、裂化柴油、裂化重油、裂化尾油和干气;以及
35.(6)使部分或全部的所述裂化尾油进行裂化反应,得到的裂化反应产物返回步骤(5)进行裂化分离和分馏;所述裂化重油返回步骤(4)与精制重油混合进行降凝反应。
36.在本发明中,精制重油是指馏程在310~450℃的精制馏分。精制尾油是指馏程大于450℃的精制馏分。裂化重油是指馏程在370~450℃的裂化馏分。裂化尾油是指馏程大于450℃的裂化馏分。
37.在一些优选的实施方式中,在步骤(1)中,氨水的浓度为5wt%~50wt%,优选地,氨水浓度为10wt%~30wt%(例如15wt%、20wt%)。优选地,在进行所述氨水中和后,所述中和后的物料的ph值为6~8(优选地,ph值为6.5~7.5)。可采用本领域已知的常规手段控制中和后的物料的ph值,例如通过ph在线分析仪控制注氨的量,从而控制中和后的物料的ph值。
38.在本发明中,加氢精制反应器中的精制催化剂可根据实际需要从已知的常规的精制催化剂中进行选择,例如,加氢催化剂采用氧化铝或含硅氧化铝为载体,以vib(如mo、w等)和/或viii(如ni、fe、co等)族非贵金属为活性组分,金属含量以氧化态计为1wt%~40wt%。加氢催化剂中还可以含有适量的助剂,如选自磷、氟、钛、锆和硼等中的一种或多种。催化剂的制备方法为业内所熟知,也可以采用商业加氢精制催化剂,如中科合成油技术有限公司研制的zkh系列催化剂,但不限于此。
39.在一些优选的实施方式中,在步骤(1)中,得到的混合物与氢气混合并加热至200~350℃(优选240~300℃),然后进行加氢精制反应。
40.在一些优选的实施方式中,在步骤(1)中,所述加氢精制反应的反应条件为:反应压力2~12mpag,反应温度120~450℃,液相物料液时体积空速0.2~6.0h
‑1,氢油体积比200~1000。优选地,所述反应条件为:反应压力5~10mpag(例如7mpag、8mpag),反应温度200~400℃(例如240℃、300℃),液相物料液时体积空速0.5~4.0h
‑1(例如1.5h
‑1、2.0h
‑1),氢油体积比300~800(例如500)。
41.在一些优选的实施方式中,在步骤(2)中,所述气液分离包括:精制热高压分离、精制冷高压分离、精制热低压分离和精制冷低压分离。
42.在进一步优选的实施方式中,所述精制热高压分离的操作温度为120~450℃,操作压力为2~12mpag。优选地,所述精制热高压分离的操作温度为170~370℃(例如230℃、260℃),操作压力为4.5~9.5mpag(例如6.0mpag、6.5mpag、8.0mpag)。
43.在进一步优选的实施方式中,所述精制热低压分离的操作温度为120~450℃,操作压力为0.5~4.0mpag。优选地,所述精制热低压分离的操作温度为170~370℃(例如230℃、260℃),操作压力为2.0~4.0mpag(例如3.5mpag)。
44.在进一步优选的实施方式中,所述精制冷高压分离的操作温度为20~100℃,操作压力为2.0~12.0mpag。优选地,所述精制冷高压分离的操作温度为40~80℃(例如50℃、55℃),操作压力为4.5~9.5mpag(例如6.0mpag、6.5mpag、8.0mpag)。
45.在进一步优选的实施方式中,所述精制冷低压分离的操作温度为20~100℃,操作压力为0.5~4.0mpag。优选地,所述精制冷低压分离的操作温度为40~80℃(例如50℃、55℃),操作压力为2.0~4.0mpag(例如3.5mpag)。
46.在本发明中,步骤(2)和步骤(5)中的分馏均采用本领域常规的操作进行,而无需特别限制。
47.在本发明中,所述加氢裂化催化剂和降凝催化剂可采用本领域已知的常规的加氢裂化催化剂和降凝催化剂,例如,以氧化铝或含硅氧化铝为载体且以vib(如mo、w等)和/或viii(如ni、fe、co等)族非贵金属为活性组分的催化剂,该催化剂可以根据本领域技术人员熟知的方法制备,也可以选自各种商业可购的催化剂,例如加氢裂化催化剂可选用中科合成油技术有限公司研制的zhc系列催化剂,但不限于此;降凝催化剂可选用中科合成油技术有限公司研制的zhi系列催化剂等,但不限于此。
48.在一些优选的实施方式中,在步骤(3)中,所述裂化反应的反应条件为:反应压力2~18mpag,反应温度200~480℃,液相物料液时体积空速0.5~6.0h
‑1,氢油体积比200~1000。优选地,所述裂化反应的反应条件为:反应压力5~10mpag(例如6.5mpag、8.0mpag),反应温度280~450℃(例如300℃、330℃、360℃、400℃),液相物料液时体积空为0.5~4.0h
‑1(例如1.5h
‑1、2.0h
‑1),氢油体积比300~800(例如700)。
49.在一些优选的实施方式中,在步骤(4)中,所述降凝反应的反应条件为:反应压力2~18mpag,反应温度200~480℃,液相物料液时体积空速0.5~6.0h
‑1,氢油体积比200~1000。优选地,所降凝反应的反应条件为:反应压力5~10mpag(例如6.5mpag、8.0mpag),反应温度280~450℃(例如300℃、320℃、350℃),液相物料液时体积空速0.5~4.0h
‑1(例如1.5h
‑1、2.0h
‑1),氢油体积比300~800(例如700)。
50.在一些优选的实施方式中,在步骤(5)中,所述裂化分离包括:裂化热高压分离、裂化冷高压分离、裂化热低压分离和裂化冷低压分离。
51.在进一步优选的实施方式中,所述裂化热高压分离的操作温度为200~480℃,操作压力为2~15mpag。优选地,所述裂化热高压分离的操作温度为250~420℃(例如260℃、280℃),操作压力为4.5~9.5mpag(例如6.0mpag、7.5mpag、8.0mpag)。
52.在进一步优选的实施方式中,所述裂化热低压分离的操作温度为200~480℃,操作压力为0.5~4.0mpag。优选地,所述裂化热低压分离的操作温度为250~420℃(例如280℃、300℃),操作压力为2.0~4.0mpag(例如3.5mpag)。
53.在进一步优选的实施方式中,所述裂化冷高压分离的操作温度为20~100℃,操作压力为2.0~15.0mpag。优选地,所述裂化冷高压分离的操作温度为40~80℃(例如50℃、55℃),操作压力为4.5~9.5mpag(例如6.0mpag、7.5mpag、8.0mpag)。
54.在进一步优选的实施方式中,所述裂化冷低压分离的操作温度为20~100℃,操作压力为0.5~4.0mpag。优选地,所述裂化冷低压分离的操作温度为40~80℃(例如50℃、55℃),操作压力为2.0~4.0mpag(例如3.5mpag)。
55.在一些优选的实施方式中,通过上述气液分离得到的氢气经过压缩后循环利用。优选地,将所述氢气压缩至压力为4.0~20.0mpag、更优选6.0~15.0mpag(例如7.0mpag、7.5mpag、9.0mpag)。
56.在一些优选的实施方式中,在步骤(6)中,所述裂化反应的反应条件为:反应压力2~18mpag,反应温度200~500℃,液相物料液时体积空速0.5~6.0h
‑1,氢油体积比200~1200。优选地,所述裂化反应的反应条件为:反应压力5~10mpag(例如6.0mpag、6.5mpag、8.0mpag),反应温度280~480℃(例如300℃、400℃),液相物料液时体积空速0.5~4.0h
‑1(例如1.5h
‑1、2.0h
‑1),氢油体积比300~1000(例如700、800)。
57.在一个实施方式中,本发明涉及一种用于实施上述方法的装置,其中,该装置包括:
58.氨水中和单元;
59.加氢精制单元,所述加氢精制单元以流体的连通方式连接至所述氨水中和单元;
60.降凝反应单元,所述降凝反应单元以流体的连通方式连接至所述加氢精制单元;以及
61.裂化单元,所述裂化单元以流体的连通方式连接至所述加氢精制单元和所述降凝反应单元,并且包括分别用于对精制尾油和裂化尾油进行裂化处理的两个分开设置的加氢裂化反应器。
62.在一些优选的实施方式中,所述氨水中和单元可以是静态混合器、不带搅拌的中和罐、或带搅拌的中和罐。
63.在一些优选的实施方式中,所述加氢精制单元包括串联设置的如下部分:加氢精制反应器、气液分离系统和精制分馏系统。
64.在进一步优选的实施方式中,所述气液分离系统包括以流体连通的方式连接的精制热高压分离器、精制冷高压分离器、精制热低压分离器、精制冷低压分离器和循环氢压缩机。
65.在进一步优选的实施方式中,所述分馏系统包括串联设置的精制常压塔、精制减压塔和精制稳定塔。
66.在一些优选的实施方式中,所述裂化单元包括:分别用于对精制尾油和裂化尾油
进行裂化处理的两个分开设置的加氢裂化反应器;裂化分离系统和裂化分馏系统。
67.在进一步优选的实施方式中,所述裂化分离系统包括以流体连通的方式连接的裂化热高压分离器、裂化冷高压分离器、裂化热低压分离器、裂化冷低分压离器和循环氢压缩机。
68.在进一步优选的实施方式中,所述分馏系统包括串联设置的常压塔、减压塔、吸收脱吸塔和稳定塔。
69.本发明的示例性的技术方案可通过如下编号段落中的内容进行说明,但本发明的保护范围并不限于此:
70.1.一种提高费托合成油品生产柴油的工艺的柴油收率的方法,其中,所述方法包括:
71.(1)将费托合成轻质油和费托合成重质油先进行氨水中和,中和后的物料经油水分离后,油相部分与费托合成重质蜡混合,得到的混合物与氢气混合后进行加氢精制反应,得到加氢精制反应产物;
72.(2)将所述加氢精制反应产物进行气液分离和分馏,得到精制石脑油、精制柴油、精制重油、精制尾油和释放气;
73.(3)使所述精制尾油进行裂化反应,得到裂化反应产物;
74.(4)使所述精制重油进行降凝反应,得到降凝反应产物;
75.(5)将所述降凝反应产物和裂化反应产物进行裂化分离和分馏,得到lpg、裂化石脑油、裂化柴油、裂化重油、裂化尾油和干气;以及
76.(6)使部分或全部的所述裂化尾油进行裂化反应,得到的裂化反应产物返回步骤(5)进行裂化分离和分馏;所述裂化重油返回步骤(4)与精制重油混合进行降凝反应。
77.2.如段落1所述的方法,其中,在步骤(1)中,氨水的浓度为5wt%~50wt%。
78.3.如段落1或2所述的方法,其中,在步骤(1)中,所述中和后的物料的ph值为6~8。
79.4.如段落1
‑
3中任一段所述的方法,其中,在步骤(1)中,得到的混合物与氢气混合并加热至200~350℃,然后进行加氢精制反应。
80.5.如段落1
‑
4中任一段所述的方法,其中,在步骤(1)中,所述加氢精制反应的反应条件为:反应压力2~12mpag,反应温度120~450℃,液相物料液时体积空速0.2~6.0h
‑1,氢油体积比200~1000。
81.6.如段落1
‑
5中任一段所述的方法,其中,在步骤(2)中,所述气液分离包括:精制热高压分离、精制冷高压分离、精制热低压分离和精制冷低压分离。
82.7.如段落6所述的方法,其中,所述精制热高压分离的操作温度为120~450℃,操作压力为2~12mpag。
83.8.如段落6或7所述的方法,其中,所述精制热低压分离的操作温度为120~450℃,操作压力为0.5~4.0mpag。
84.9.如段落6
‑
8中任一段所述的方法,其中,所述精制冷高压分离的操作温度为20~100℃,操作压力为2.0~12.0mpag。
85.10.如段落6
‑
9中任一段所述的方法,其中,所述精制冷低压分离的操作温度为20~100℃,操作压力为0.5~4.0mpag。
86.11.如段落1
‑
10中任一段所述的方法,其中,在步骤(3)中,所述裂化反应的反应条
件为:反应压力2~18mpag,反应温度200~480℃,液相物料液时体积空速0.5~6.0h
‑1,氢油体积比200~1000。
87.12.如段落1
‑
11中任一段所述的方法,其中,在步骤(4)中,所述降凝反应的反应条件为:反应压力2~18mpag,反应温度200~480℃,液相物料液时体积空速0.5~6.0h
‑1,氢油体积比200~1000。
88.13.如段落1
‑
12中任一段所述的方法,其中,在步骤(5)中,所述裂化分离包括:裂化热高压分离、裂化冷高压分离、裂化热低压分离和裂化冷低压分离。
89.14.如段落13所述的方法,其中,所述裂化热高压分离的操作温度为200~480℃,操作压力为2~15mpag。
90.15.如段落13或14所述的方法,其中,所述裂化热低压分离的操作温度为200~480℃,操作压力为0.5~4.0mpag。
91.16.如段落13
‑
15中任一段所述的方法,其中,所述裂化冷高压分离的操作温度为20~100℃,操作压力为2.0~15.0mpag。
92.17.如段落13
‑
16中任一段所述的方法,其中,所述裂化冷低压分离的操作温度为20~100℃,操作压力为0.5~4.0mpag。
93.18.如段落1
‑
17中任一段所述的方法,其中,通过所述气液分离得到的氢气经过压缩后循环利用。
94.19.如段落1
‑
18中任一段所述的方法,其中,在步骤(6)中,所述裂化反应的反应条件为:反应压力2~18mpag,反应温度200~500℃,液相物料液时体积空速0.5~6.0h
‑1,氢油体积比200~1200。
95.20.一种用于实施段落1
‑
19中任一段所述的方法的装置,其中,所述装置包括:
96.氨水中和单元;
97.加氢精制单元,所述加氢精制单元以流体的连通方式连接至所述氨水中和单元;
98.降凝反应单元,所述降凝反应单元以流体的连通方式连接至所述加氢精制单元;以及
99.裂化单元,所述裂化单元以流体的连通方式连接至所述加氢精制单元和所述降凝反应单元,并且包括分别用于对精制尾油和裂化尾油进行裂化处理的两个分开设置的加氢裂化反应器。
100.21.如段落20所述的装置,其中,所述氨水中和单元是静态混合器、不带搅拌的中和罐、或带搅拌的中和罐。
101.22.如段落20或21所述的装置,其中,所述加氢精制单元包括串联设置的如下部分:加氢精制反应器、气液分离系统和精制分馏系统。
102.23.如段落22所述的装置,其中,所述气液分离系统包括以流体连通的方式连接的精制热高压分离器、精制冷高压分离器、精制热低压分离器、精制冷低压分离器和循环氢压缩机。
103.24.如段落22或23所述的装置,其中,所述精制分馏系统包括串联设置的精制常压塔、精制减压塔和精制稳定塔。
104.25.如段落20
‑
24中任一段所述的装置,其中,所述裂化单元包括:分别用于对精制尾油和裂化尾油进行裂化处理的两个分开设置的加氢裂化反应器;裂化分离系统和裂化分
馏系统。
105.26.如段落25所述的装置,其中,所述裂化分离系统包括以流体连通的方式连接的裂化热高压分离器、裂化冷高压分离器、裂化热低压分离器、裂化冷低分压离器和循环氢压缩机。
106.27.如段落25或26所述的装置,其中,所述裂化分馏系统包括串联设置的常压塔、减压塔、吸收脱吸塔和稳定塔。
107.实施例
108.除非另有说明,下述实施例中涉及的试剂、材料和装置均为本领域常规的可商购得到的;下述实施例中涉及的常规操作可见于本领域已公开的专利、专利申请和出版物等中(例如,贺永德主编,《现代煤化工技术手册》,化学工业出版社,2003年,但不限于此)。
109.如下的实施例1
‑
实施例2以及比较例1
‑
比较例3中所用的费托合成轻质油101、费托合成重质油102和费托合成重质蜡103的主要性质如下表1所示。
110.表1费托合成轻质油101、费托合成重质油102和费托合成重质蜡103的主要性质
[0111][0112]
实施例1
[0113]
将费托合成轻质油101、费托合成重质油102与20wt%氨水104在静态混合器8中混合,通过ph在线分析仪控制注氨的量,中和后的物料的ph值为7.0。中和后的物料进入油水分离器0进行脱水,脱水后得到的油品先与费托合成重质蜡103混合,再与氢气混合并加热至240℃后,进入加氢精制反应器1与加氢精制反应的催化剂接触并进行加氢精制反应,得到加氢精制反应产物。其中,加氢精制反应的催化剂为中科合成油技术有限公司开发的zkh系列催化剂;加氢精制反应的条件为:反应温度为240℃,反应压力为7.0mpag,液相物料液时体积空速为2.0h
‑1,氢油体积比为500。
[0114]
上述的加氢精制反应产物离开加氢反应器1后进入气液分离系统进行气液分离,得到气液分离产品。气液分离系统由如下构成:精制热高压分离器、精制冷高压分离器、精制热低压分离器、精制冷低压分离器和循环氢压缩机。其中,精制热高压分压离器2的操作温度为230℃,操作压力为6.6mpag;精制冷高压分压离器3的操作温度为50℃,操作压力为6.6mpag;精制热低压分离器4的操作温度为230℃,操作压力为3.2mpag;精制冷低压分离器5的操作温度为50℃,操作压力为3.1mpag;循环氢压缩机6的出口压力为7.7mpag,得到的氢气在该体系中循环利用。上述气液分离产品进入分馏系统7进行分馏,获得释放气产品126、精制石脑油产品121、精制柴油产品122、精制重油123、精制尾油124。分馏系统由如下构成:常压塔、减压塔和稳定塔。常压塔的操作压力0.1mpag,塔顶温度125℃,塔底温度300℃;减压塔的操作压力
‑
0.09mpag,塔顶温度为65℃,塔底温度为290℃;稳定塔的操作压力0.45mpag,塔顶温度63℃,塔底温度192℃。
[0115]
精制尾油进入裂化反应器11,与加氢裂化反应的催化剂接触并进行加氢裂化反应,得到裂化反应产物。精制重油123进入降凝反应器13,与加氢降凝反应的催化剂接触并
进行加氢降凝反应,得到降凝反应产物。其中,加氢裂化反应的催化剂为中科合成油技术有限公司开发的zhc系列催化剂;降凝反应的催化剂为中科合成油技术有限公司开发的zhi系列催化剂。加氢裂化反应的条件为:反应压力6.5mpag,反应温度为330℃,液相物料液时体积空速为2.0h
‑1,氢油体积比为800;降凝反应的条件为:反应压力6.5mpag,反应温度为320℃,液相物料液时体积空速为2.0h
‑1,氢油体积比为800。
[0116]
上述的裂化反应产物和降凝反应产物混合进入裂化分离系统,进行裂化分离。裂化分离系统由如下构成:裂化热高压分离器、裂化冷高压分离器、裂化热低压分离器、裂化冷低压分离器和循环氢压缩机。其中,裂化热高压分离器14的操作温度为260℃,操作压力为6.0mpag;裂化冷高压分离器15的操作温度为50℃,操作压力为6.0mpag;裂化热低压分离器16的操作温度为250℃,操作压力为3.2mpag;裂化冷低压分离器17的操作温度为50℃,操作压力为3.1mpag;循环氢压缩机的出口压力为7.7mpag,得到的氢气在该体系中循环利用。分离产品进入分馏系统19进行分馏,获得液化石油气产品221、裂化石脑油产品222、裂化柴油产品223、裂化重油225、裂化尾油226和裂化干气224。分馏系统由如下构成:常压塔、减压塔、吸收脱洗塔和稳定塔。其中,常压塔的操作压力0.1mpag,塔顶温度125℃,塔底温度310℃,减压塔的操作压力
‑
0.09mpag,塔顶温度为65℃,塔底温度为300℃。吸收脱吸塔的操作压力0.7mpag,塔顶温度45℃,塔底温度122℃,稳定塔的操作压力0.95mpag,塔顶温度63℃,塔底温度192℃。
[0117]
裂化重油225返回与精制重油123混合后进入降凝反应器进行降凝反应。裂化尾油226进入裂化反应器12进行裂化反应,得到裂化反应产物。该裂化反应产物返回与上述的裂化反应器11的裂化反应产物和降凝反应器13的降凝反应产物混合进行上述的裂化分离和分馏。裂化反应器12中的加氢裂化反应的催化剂为中科合成油技术有限公司开发的zhc系列催化剂;加氢裂化反应的条件为:反应压力6.5mpag,反应温度为340℃,液相物料液时体积空速为1.5h
‑1,氢油体积比为800。
[0118]
本实施例的进料和产物出料的结果在表2中示出;加氢精制反应器、裂化反应器和降凝反应器的温升情况以及原料总氢耗和总的柴油收率在表3中示出。
[0119]
实施例2
[0120]
将费托合成轻质油101、费托合成重质油102与30wt%氨水104在带搅拌的中和罐8中混合,通过ph在线分析仪控制注氨的量,中和后的物料的ph值为7.1。中和后的物料进入油水分离器0进行脱水,脱水后得到的油品先与费托合成重质蜡103混合,再与氢气混合并加热至300℃后,进入加氢精制反应器1与加氢精制反应的催化剂接触并进行加氢精制反应,得到加氢精制反应产物。其中,加氢精制反应的催化剂为中科合成油技术有限公司开发的zkh系列催化剂;加氢精制反应的条件为:反应温度为300℃,反应压力为8.0mpag,液相物料液时体积空速为1.5h
‑1,氢油体积比为800。
[0121]
上述的加氢精制反应产物离开加氢反应器1后进入气液分离系统进行气液分离,得到气液分离产品。气液分离系统由如下构成:精制热高压分离器、精制冷高压分离器、精制热低压分离器、精制冷低压分离器和循环氢压缩机。其中,精制热高压分压离器2的操作温度为260℃,操作压力为7.6mpag;精制冷高压分压离器3的操作温度为55℃,操作压力为7.6mpag;精制热低压分离器4的操作温度为260℃,操作压力为2.3mpag;精制冷低压分离器5的操作温度为55℃,操作压力为2.2mpag;循环氢压缩机6的出口压力为8.7mpag,得到的氢
气在该体系中循环利用。上述气液分离产品进入分馏系统7进行分馏,获得释放气产品126、精制石脑油产品121、精制柴油产品122、精制重油123、精制尾油124。分馏系统由如下构成:常压塔、减压塔和稳定塔。常压塔的操作压力0.15mpag,塔顶温度128℃,塔底温度305℃;减压塔的操作压力
‑
0.09mpag,塔顶温度为65℃,塔底温度为295℃;稳定塔的操作压力0.4mpag,塔顶温度60℃,塔底温度190℃。
[0122]
精制尾油进入裂化反应器11,与加氢裂化反应的催化剂接触并进行加氢裂化反应,得到裂化反应产物。精制重油123进入降凝反应器13,与加氢降凝反应的催化剂接触并进行加氢降凝反应,得到降凝反应产物。其中,加氢裂化反应的催化剂为中科合成油技术有限公司开发的zhc系列催化剂;降凝反应的催化剂为中科合成油技术有限公司开发的zhi系列催化剂。加氢裂化反应的条件为:反应压力8.0mpag,反应温度为360℃,液相物料液时体积空速为1.5h
‑1,氢油体积比为700;降凝反应的条件为:反应压力8.0mpag,反应温度为350℃,液相物料液时体积空速为1.5h
‑1,氢油体积比为700。
[0123]
上述的裂化反应产物和降凝反应产物混合进入裂化分离系统,进行裂化分离。裂化分离系统由如下构成:裂化热高压分离器、裂化冷高压分离器、裂化热低压分离器、裂化冷低压分离器和循环氢压缩机。其中,裂化热高压分离器14的操作温度为280℃,操作压力为7.5mpag;裂化冷高压分离器15的操作温度为55℃,操作压力为7.5mpag;裂化热低压分离器16的操作温度为280℃,操作压力为2.3mpag;裂化冷低压分离器17的操作温度为55℃,操作压力为2.2mpag;循环氢压缩机的出口压力为8.7mpag,得到的氢气在该体系中循环利用。分离产品进入分馏系统19进行分馏,获得液化石油气产品221、裂化石脑油产品222、裂化柴油产品223、裂化重油225、裂化尾油226和裂化干气224。分馏系统由如下构成:常压塔、减压塔、吸收脱洗塔和稳定塔。其中,常压塔的操作压力0.15mpag,塔顶温度130℃,塔底温度315℃,减压塔的操作压力
‑
0.09mpag,塔顶温度为65℃,塔底温度为305℃。吸收脱吸塔的操作压力0.75mpag,塔顶温度48℃,塔底温度128℃,稳定塔的操作压力0.9mpag,塔顶温度60℃,塔底温度190℃。
[0124]
裂化重油225返回与精制重油123混合后进入降凝反应器进行降凝反应。裂化尾油226进入裂化反应器12进行裂化反应,得到裂化反应产物。该裂化反应产物返回与上述的裂化反应器11的裂化反应产物和降凝反应器13的降凝反应产物混合进行上述的裂化分离和分馏。裂化反应器12中的加氢裂化反应的催化剂为中科合成油技术有限公司开发的zhc系列催化剂;加氢裂化反应的条件为:反应压力8.0mpag,反应温度为366℃,液相物料液时体积空速为1.5h
‑1,氢油体积比为700。
[0125]
本实施例的进料和产物出料的结果在表2中示出;加氢精制反应器、裂化反应器和降凝反应器的温升情况以及原料总氢耗和总的柴油收率在表3中示出。
[0126]
比较例1
[0127]
除了不将费托合成轻质油101和费托合成重质油102进行氨水中和之外,其它条件和操作流程均与实施例1相同。
[0128]
本比较例的进料和产物出料的结果在表2中示出;加氢精制反应器、裂化反应器和降凝反应器的温升情况以及原料总氢耗和总的柴油收率在表3中示出。
[0129]
比较例2
[0130]
将费托合成轻质油101、费托合成重质油102与30wt%氨水104在静态混合器8中混
合,通过ph在线分析仪控制注氨的量,中和后物料的ph值为7.2。中和后的物料进入油水分离器0进行脱水,脱水后得到的油品先与费托合成重质蜡103混合,再与氢气混合并加热至260℃后,进入加氢精制反应器1与加氢精制反应的催化剂接触并进行加氢精制反应,得到加氢精制反应产物。其中,加氢精制反应的催化剂为中科合成油技术有限公司开发的zkh系列催化剂;加氢精制反应的条件为:反应温度为260℃,反应压力为7.5mpag,液相物料液时体积空速为1.8h
‑1,氢油体积比为400。
[0131]
上述的加氢反应产物离开加氢反应器1后进入气液分离系统进行气液分离,得到气液分离产品。气液分离系统由如下构成:精制热高压分离器、精制冷高压分离器、精制热低压分离器、精制冷低压分离器和循环氢压缩机。其中,精制热高分压离器2的操作温度为250℃,操作压力为7.1mpag;精制冷高分压离器3的操作温度为50℃,操作压力为7.1mpag;精制热低压分离器4的操作温度为250℃,操作压力为3.2mpag;精制冷低压分离器5的操作温度为50℃,操作压力为3.1mpag;循环氢压缩机6的出口压力为8.1mpag,得到的氢气在该体系中循环利用。上述气液分离产品进入分馏系统7进行分馏,获得释放气产品126、石脑油产品121、精制柴油产品122、精制重油123、精制尾油124。分馏系统由如下构成:常压塔、减压塔和稳定塔。常压塔的操作压力0.15mpag,塔顶温度130℃,塔底温度310℃;减压塔的操作压力
‑
0.09mpag,塔顶温度为65℃,塔底温度为295℃;稳定塔的操作压力0.46mpag,塔顶温度65℃,塔底温度194℃。
[0132]
精制尾油124进入裂化反应器11,与加氢裂化反应的催化剂接触并进行加氢裂化反应,得到裂化反应产物。精制重油进入降凝反应器13,与加氢降凝反应的催化剂接触并进行加氢降凝反应,得到降凝反应产物。其中,加氢裂化反应的催化剂中科合成油技术有限公司开发的zhc系列催化剂,降凝反应的催化剂为中科合成油技术有限公司开发的zhi系列催化剂。其中加氢裂化反应的条件为:反应压力7.0mpag,反应温度为330℃,液相物料液时体积空速为1.5h
‑1,氢油体积比为750;降凝反应的条件为:反应压力7.0mpag,反应温度为325℃,液相物料液时体积空速为1.5h
‑1,氢油体积比为750。
[0133]
上述的裂化反应产物和降凝反应产物混合进入裂化分离系统,进行裂化分离。裂化分离系统由如下构成:裂化热高压分离器、裂化冷高压分离器、裂化热低压分离器、裂化冷低压分离器和循环氢压缩机。其中,裂化热高分压离器14的操作温度为265℃,操作压力为6.5mpag;裂化冷高分压离器15的操作温度为50℃,操作压力为6.5mpag;裂化热低压分离器16的操作温度为265℃,操作压力为3.2mpag;裂化冷低压分离器17的操作温度为50℃,操作压力为3.1mpag;循环氢压缩机的出口压力为8.1mpag,得到的氢气在该体系中循环利用。分离产品进入分馏系统19进行分馏,获得液化石油气产品221、裂化石脑油产品222、裂化柴油产品223、裂化重油225、裂化尾油226和裂化干气224。分馏系统由如下构成:常压塔、减压塔、吸收脱洗塔和稳定塔。常压塔的操作压力0.15mpag,塔顶温度135℃,塔底温度315℃,减压塔的操作压力
‑
0.09mpag,塔顶温度为65℃,塔底温度为300℃。吸收脱吸塔的操作压力0.7mpag,塔顶温度45℃,塔底温度125℃,稳定塔的操作压力0.98mpag,塔顶温度65℃,塔底温度198℃。
[0134]
裂化重油225返回与精制重油123混合后进入降凝反应器进行降凝反应。裂化尾油226返回与精制尾油124混合后进入裂化反应器11进行裂化反应,得到裂化反应产物。该裂化反应产物返回与上述的裂化反应器11的裂化反应产物和降凝反应器13的降凝反应产物
混合进行上述的裂化分离和分馏。
[0135]
本比较例的进料和产物出料的结果在表2中示出;加氢精制反应器、裂化反应器和降凝反应器的温升情况以及原料总氢耗和总的柴油收率在表3中示出。
[0136]
比较例3
[0137]
除了不将费托合成轻质油101和费托合成重质油102进行氨水中和,以及裂化尾油直接进入裂化反应器11和仅精制重油进入降凝反应器之外,其它条件和流程均与比较例2相同。
[0138]
本比较例的进料和产物出料的结果在表2中示出;加氢精制反应器、裂化反应器和降凝反应器的温升情况以及原料总氢耗和总的柴油收率在表3中示出。
[0139]
实施例1
‑
实施例2以及比较例1
‑
比较例3中得到的液化石油气产品221、精制石脑油产品121、裂化石脑油产品222、精制柴油产品122和裂化柴油产品223均符合国家标准。其中,液化石油气满足国家标准(gb11174
‑
2011)商品丙丁烷混合物,柴油满足费托合成柴油组分油国家标准(gb/t 29720
‑
2013),石脑油满足煤基费托合成石脑油标准(gb/t36565
‑
2018)。
[0140]
表2实施例1和比较例1至比较例3之间的物料变化比较
[0141][0142][0143]
通过表2可以看出,与比较例1相比,实施例1和2通过进行氨水中和,使柴油出料量明显增加。与比较例2相比,实施例1和2通过将精制尾油和裂化尾油分别进行裂化反应,使得裂化柴油出料量增加。与比较例3相比,实施例1和2通过进行氨水中和、将精制尾油和裂化尾油分别进行裂化反应以及将裂化重油返回进行降凝反应,柴油出料量明显增高。
[0144]
表3实施例1和比较例1至比较例3之间的对比
[0145]
项目实施例1实施例2比较例1比较例2比较例3精制反应器1温升,℃8080818081裂化反应器11温升,℃1616.1331735裂化反应器12温升,℃141430
‑‑
降凝反应器13温升,℃14.514.51814.518
单位原料总氢耗,%1.381.381.601.431.66总柴油收率,%77.8777.8756.7574.7853.93
[0146]
通过表3可以看出,与实施例1和2相比,比较例1由于不进行氨水中和而表现出明显更高的裂化反应器和降凝反应器温升,并具有更高的氢耗,但是却产生更低的柴油收率(更低21.12%);比较例2由于未将精制尾油和裂化尾油分别进行裂化反应,使得氢耗升高而柴油收率有所降低(更低约3.1%);比较例3由于不进行氨水中和、未将精制尾油和裂化尾油分别进行裂化反应且裂化重油不返回进行降凝反应,不仅表现出明显更高的裂化反应器和降凝反应器温升,而且氢耗增加但柴油收率明显降低。
[0147]
综上所述,通过本发明所述的方法,在将费托合成原料进行氨水中和后,一方面降低费托合成油品管线、仪表、管件等材质,节省了装置建设投资成本,另一方面抑制原料过度裂化,从而降低催化剂床层温升,提高了柴油收率。
[0148]
另外,通过将精制重油和裂化重油一起进入降凝反应器,利用降凝催化剂对重油的异构和缓和裂化作用,将重油高收率地转化为柴油馏分,进一步提高了柴油收率。将富含正构烷烃的加氢精制尾油和富含异构烷烃的加氢裂化尾油分别设置裂化反应器,通过控制不同的反应温度,使得正构烷烃和异构烷烃分别在合适的温度下发生裂化反应,避免了正构烷烃过度裂解,提高了柴油收率。
再多了解一些
本文用于企业家、创业者技术爱好者查询,结果仅供参考。