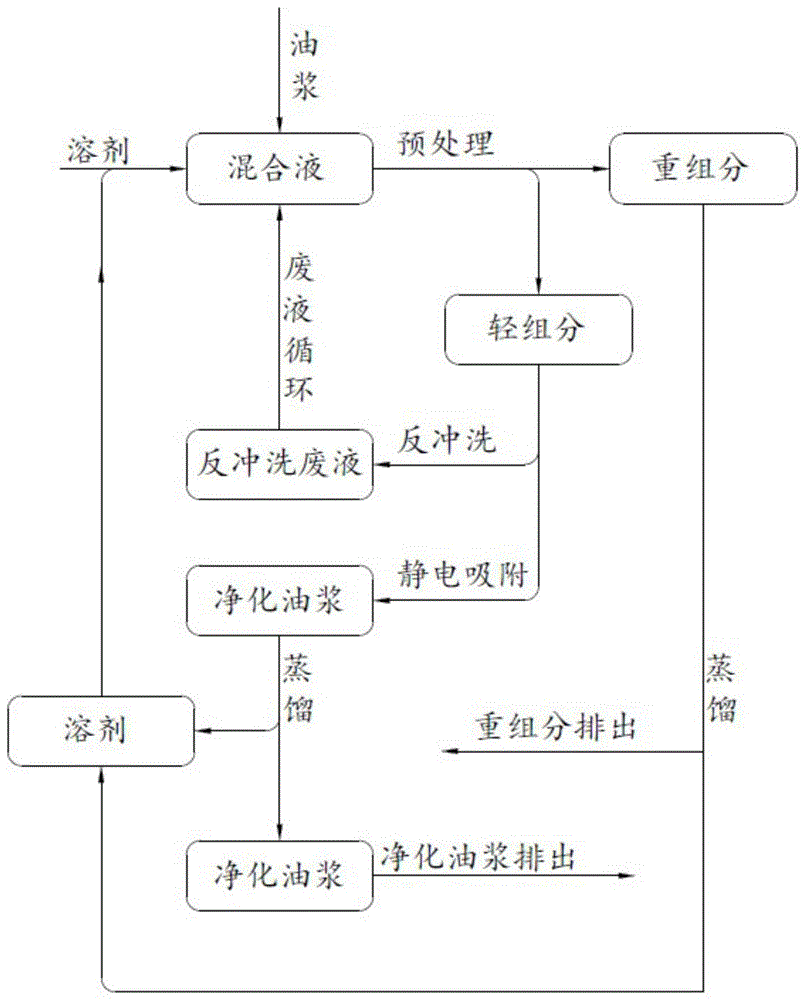
本发明涉及油浆净化处理技术领域,具体为一种催化裂化油浆净化处理的组合工艺。
背景技术:
催化油浆是重油催化裂化工艺过程中所产生的一种性质极为特殊的副产品,因其比重大、分子量大、粘度高并含有较多的催化剂固体颗粒,使其利用率受到限制。近年来,国内外针对催化油浆脱除催化剂颗粒物进行了大量研究,目前主要有静电分离法、自然沉降法、沉降剂沉降法、高温离心分离技术、水洗法分离技术、金属滤芯过滤法分离技术、无机膜过滤技术。静电分离法是近年来发展起来的一种新型液—固分离技术,适用于固体颗粒直径很小、颗粒浓度相对较低且液相电阻率较大的液-固体系;自然沉降法,通常炼厂的外甩油浆均存于油浆沉降罐中进行自然沉降,其温度为80℃-90℃,沉降一段时间后备用,沉降罐约2000-5000m3,操作简单,运行成本低;沉降剂沉降法是近年来发展起来的一种经济有效的方法,通过添加沉降剂可显著提高催化剂细粉的沉降速度和脱离程度,该法不但操作简单,而且投资少;高温离心分离技术,利用催化剂细粉在离心机中获得的离心力远远大于其重力而加速沉降到器壁的分离技术。分为旋流分离法和离心分离法,旋流分离法是让液体在旋流芯管内高速旋转,利用两种互不相溶介质的密度差,通过高速旋转产生的离心力实现两相分离;水洗法分离技术,沉降剂工业应用获得成功后,对其进行了改进,考虑到催化剂粉末加速沉降后,可能要增加油罐的清渣次数,因油罐清渣目前都是人工操作,劳动强度大,若能解决自动清渣问题,则工业上更加有推广前景,于是研究了水洗法,即用水把催化剂粉末洗下去,并在切水时把催化剂粉末携带出去;金属滤芯过滤法分离技术美国pall公司生产的油浆滤芯以不锈钢烧结丝网微孔材料为过滤介质,其主要特点是利用固性颗粒物在丝网滤芯表面形成滤饼进行分离,而滤芯本身耐高温、抗热震性好且具有较好的清洗再生性能。
然而,上述方法在时间生产过程中均存在缺点,单一静电分离技术脱油浆灰分的效果受油浆理化性质的影响较大,该技术在国内尚无长周期运行成功案例,二是针对国内高含稠环芳烃、胶质、沥青质的催化油浆适应性有待考察;三是静电设施对原料含水等异常情况适应性有待考察;自然沉降法沉降效果不好,当沉降温度为250℃,沉降深度为60cm,催化剂粉末脱除率达85%时,所需的沉降时间为20000多小时,显然沉降时间太长,无法实现工业化;沉降剂沉降法,该技术采用的沉降剂承受不了高温,遇高温会分解(不能超过250℃)。油浆罐中的沉渣需定期清理,环保治理费用高;高温离心分离法利用高温试管沉降离心机将fcc油浆净化。该离心法分离效果好,但是处理量不大,而且操作不便、维护困难、运行成本高。我国还没有成功的工业实例;水洗法分离技术,该技术对催化油浆的密度要求较高,最好要<0.96,像南京、大连、哈尔滨等地的油浆密度在1.04左右,无法使用该技术,同时仅限于试验水平,工业连续生产条件下难以实现;金属滤芯过滤法分离技术,从国内炼厂应用的状况来看,采用不锈钢金属烧结丝网滤芯过滤,经常需要频繁的进行清洗,且清洗再生性能差,导致油浆过滤系统无法长周期运行,需要经常更换滤芯,目前国内的油浆金属滤芯过滤装置很多都不能长期运行,无机膜过滤技术,错流依靠大循环比,循环回流依然需要定期排渣,给组合工艺的自动控制带来较大麻烦。
技术实现要素:
鉴于现有技术中所存在的问题,本发明开发一种“催化油浆预处理-静电吸附过滤-汽提或蒸馏”组合工艺路线,去除掉催化裂化油浆中的亚微米级催化剂颗粒和沥青质。针对各种催化油浆处理方法的优点进行组合,得到一种催化油浆净化的组合工艺,经过本组合工艺处理后的催化油浆品质大幅上升,沥青质含量可降低至1%以下,催化油浆的灰分可降低至50ppm以下,精细处理可降至10ppm以下。采用的方案是:包括以下步骤:
step.1催化油浆预处理:取萃取溶剂,将溶剂与油浆按照质量比0.3-5:1的比例进行混合,混合温度为60℃以上,利用油浆中的各组分在溶剂中的溶解度的不同,轻组分可溶于溶剂当中,重组分不溶于溶剂或少量溶于溶剂,混合均匀后,将混合物分离为预分离轻组分和预分离重组分,混合物中不溶于溶剂的油浆重组分密度大于溶解的了油浆轻组分的混合溶液,利用密度差可将混合物分为两股物料,分别为预分离轻组分和预分离重组分,大部分饱和分、芳分、溶剂集中在预分离轻组分当中,部分催化剂、大部分沥青质及部分胶质等其他杂质富集到预分离重组分当中。
step.2催化油浆静电吸附:在静电吸附器上施加高压电场,温度为60-120℃,预分离轻组分通过动力设施,被送入流过静电吸附器中预分离轻组分通过静电吸附器,催化剂颗粒al2o3·sio2等被吸附在静电吸附器中的填料层之上,预分离轻组分排出静电吸附器,从而将催化剂颗粒从预分离轻组分中分离出来;静电吸附器经过一段时间的吸附后,断开高压电源,关闭静电吸附器净化产品出口及反冲洗废液出口,打开反冲洗氮气出口,使用预处理后的预分离轻组分作为反冲洗的原料,浸没填料层,原料进料口切换到氮气管线,使用氮气在0.5~1.1mpa压差作用下使反冲洗原料在静电吸附器中扰动,氮气冲洗模式为脉冲形式,每隔1-50s喷出氮气,催化剂颗粒从填料层上脱落,完成后关闭原料进料口,打开反冲洗废液出口,催化剂颗粒随反冲洗废液排出静电吸附器,填料层恢复到可以高效吸附的状态,继续重复吸附-反冲过程。
step.3产品处理:预处理得到的预分离重组分、经静电吸附后的预分轻组分通过汽提或蒸馏等方式回收溶剂,回收的溶剂循环利用,得到的油浆重组分与油浆轻组分到下游工艺深加工。
所述step.1中的萃取溶剂为c5-c20的烃类中的一种或几种。
所述step.1中的混合方式为静态混合器、齿轮泵循环或搅拌器搅拌。
所述step.1中的分离方法为离心法、旋流法或沉降法。
所述step.2中静电吸附器的填料层中添加球状填料,填料介电常数为6-12,粒径为1-8mm。
所述球状填料类型可选陶瓷、石材、云母或者玻璃。
本发明的有益效果:针对现有催化油浆脱固净化的方法,解决了如下几方面问题:
1、离心分离法温度很高,一般为150-300℃,由于高温的问题,带来了诸多其他问题,例如操作不便、维护困难、运行成本高,但由于本技术方案不仅采用了离心分离技术,而且在催化油浆中加入了特殊溶剂,调和了催化油浆,混合物的性质较催化油浆大大提升,例如粘度降低,催化油浆中的各组分由于添加了溶剂的原因,分离更容易,操作温度大大降低,目前操作温度为80-100℃,操作难度降低,维护更容易,转速下降,运行成本降低.
2、分离效果不稳定的问题,经过本组合方法,可稳定将催化油浆产品维持在优良的品质,分离效果稳定。
3、目前,静电分离法由于受油浆理化性质的影响较大,更确切的说,是油浆中的沥青质等重组分对静电分离的效果的影响,油浆中的沥青质等粘黏到填料层之上时,很难通过反冲洗的方式将其清理下来,进而导致静电分离法不能长期稳定的运行,但本发明当中,由于采用了催化油浆预处理工艺,在预处理当中,除去了催化油浆当中的大部分催化剂颗粒、大部分的沥青质等重组分以及其他杂质,使得静电分离过程进料条件较好并且进料稳定,不再发生沥青质等粘黏到填料层之上进而导致静电分离效率下降直至无效果的问题。
4、静电吸附器经过一段时间的吸附后,静电吸附器中填料层之上附着大量催化剂颗粒等,此时应进行反冲洗除去填料层之上附着的催化剂颗粒以使填料层恢复高效吸附的状态。具体实施为,断开高压电源,关闭静电吸附器净化产品出口及反冲洗废液出口,打开反冲洗氮气出口,使用预处理后的预分离轻组分作为反冲洗的原料,浸没填料层,原料进料口切换到氮气管线,使用氮气在0.5~1.1mpa压差作用下使反冲洗原料在静电吸附器中扰动,氮气冲洗模式为脉冲形式,每隔数秒至数十秒喷一股氮气,催化剂颗粒从填料层上脱落,完成后关闭原料进料口,打开反冲洗废液出口,催化剂颗粒随反冲洗废液排出静电吸附器,玻璃珠恢复到可以高效吸附的状态,继续重复吸附-反冲过程。
附图说明
图1为本发明的组合工艺流程图;
图2为本发明的静电场极化吸附原理图。
具体实施方式
实施例1
如图1所示,本发明公开了一种催化裂化油浆净化处理的组合工艺,包括“催化油浆预处理—催化油浆静电吸附—产品汽提或蒸馏”,其中“催化油浆预处理”的目的是除去催化油浆中大部分的沥青质等重组分、部分催化剂颗粒、水分以及其他固体杂质,“催化油浆预处理”得到预分离轻组分和预分离重组分,预分离轻组分进入“催化油浆静电吸附”工艺步骤,预分离重组分进“产品汽提或蒸馏”工艺步骤。“催化油浆静电吸附”的目的是除去“催化油浆预处理”得到的预分离轻组分当中所含的催化剂颗粒等,经静电吸附后的油剂混合溶液进“产品汽提或蒸馏”工艺步骤。“产品汽提或蒸馏”的目的是将经“催化油浆静电吸附”后得到的油剂混合溶液以及“催化油浆预处理”得到的预分离重组分当中的溶剂通过汽提或蒸馏的方法回收循环利用,得到净化油浆以及富含油浆重组分的油浆。采用的方案是:第一步,选取一种萃取溶剂,溶剂为c5-c20的烃类中的一种或几种,利用油浆中的各组分在溶剂中的溶解度的不同,轻组分可溶于溶剂当中,重组分不溶于溶剂或少量溶于溶剂,例如石脑油、催化柴油等,将溶剂与油浆按照质量比0.3:1到5:1的比例进行混合,混合温度为60℃以上,混合方式可采用静态混合器或齿轮泵循环或搅拌器搅拌等,混合均匀后,将混合物分为预分离轻组分和预分离重组分,分离方法可采用离心法/旋流法/沉降法,混合物中,不溶于溶剂的油浆重组分密度大于溶解的了油浆轻组分的混合溶液,利用密度差可将混合物分为两股物料,分别为预分离轻组分和预分离重组分。大部分饱和分、芳分、溶剂集中在预分离轻组分当中,部分催化剂、大部分沥青质及部分胶质等其他杂质富集到预分离重组分当中。采用中国石化九江分公司1#催化油浆为原料,原料油浆与预分离重油浆结果如表1所示。
表1
通过实验,大部分的固体颗粒到预分离重组分当中,沥青质等油浆重组分富集到预分离重组分当中,实现了预处理的目标。
第二步,目标是将预处理得到的预分离轻组分中所含的催化剂颗粒等固含物脱除出来,静电吸附预分离轻组分当中所含的固体颗粒,达到高品质催化油浆。在静电吸附器上施加高压电场,绝缘电极材料可选聚四氟乙烯、特种陶瓷等,在本实施例中选用了聚四氟乙烯作为绝缘材料,后升级为陶瓷绝缘套管,外形结构是密封、加热控温立式塔,塔内有内构件,上下法兰连接;系统温度控制在60-120℃,静电吸附器中添加球状填料,填料材料类型可选陶瓷、石材、云母或者玻璃等,填料介电常数控制在6-12为佳,粒径在1-8mm范围内,在本实施例中,选用了粒径6mm特制玻璃珠作为填料材料,如图2所示,玻璃珠在高压直流电场e作用下发生电荷移动造成玻璃珠电荷分布不均,产生极化电场e,如此则在吸附空间中充满玻璃珠时,外加高压直流电场则将其中的玻璃珠极化产生无数小电场,预分离轻组分通过泵等其他动力设施,被送入流过静电吸附器,预分离轻组分通过吸附空间时,预分离轻组分中的催化剂颗粒al2o3·sio2等由于静电场的作用被吸附在筒壁、玻璃珠表面接触点,从而将催化剂颗粒从预分离轻组分中分离出来。
静电吸附器经过一段时间的吸附后,断开高压电源,关闭静电吸附器净化产品出口及反冲洗废液出口,打开反冲洗氮气出口,使用预处理后的预分离轻组分作为反冲洗的原料,浸没填料层,原料进料口切换到氮气管线,使用氮气在0.5~1.1mpa压差作用下使反冲洗原料在静电吸附器中扰动,氮气冲洗模式为脉冲形式,催化剂颗粒从填料层上脱落,完成后关闭原料进料口,打开反冲洗废液出口,催化剂颗粒随反冲洗废液排出静电吸附器,玻璃珠恢复到可以高效吸附的状态,继续重复吸附-反冲过程。
第三步,预处理得到的预分离重组分、经静电吸附后的预分轻组分通过汽提或蒸馏等方式回收溶剂,回收的溶剂循环利用,得到的油浆重组分与油浆轻组分到下游工艺深加工。
经过试验,通过预处理—静电吸附—产品汽提得到的净化轻质油浆灰分含量低于100ppm,精过滤可低于10ppm,沥青质含量可降低到1%以下,实验中取得的数据如表2所示。
本发明的实验方案为“催化油浆预处理—催化油浆静电吸附—产品汽提或蒸馏”的技术路线,具体实施为“萃取离心—静电过滤—产品汽提”技术路线。
其中催化油浆预处理部分可采用萃取离心、萃取旋流、萃取沉降的方式进行处理,预分离油浆中的各种大颗粒固体和大部分的油浆重组分,如沥青质等。催化油浆静电吸附部分可采用静电吸附过滤法、各种膜过滤、错流过滤等方式进行过滤除去催化剂颗粒。产品汽提或蒸馏部分可采用常压蒸馏、减压蒸馏、汽提、闪蒸等方式,分离“催化油浆预处理”时加入的溶剂,使溶剂与油浆分离,得到的溶剂循环利用,油浆重组分和油浆轻组分到下游工艺深度加工利用。
上述虽然对本发明的具体实施例作了详细说明,但是本发明并不限于上述实施例,在本领域普通技术人员所具备的知识范围内,还可以在不脱离本发明宗旨的前提下做出各种变化,而不具备创造性劳动的修改或变形仍在本发明的保护范围以内。
本文用于企业家、创业者技术爱好者查询,结果仅供参考。