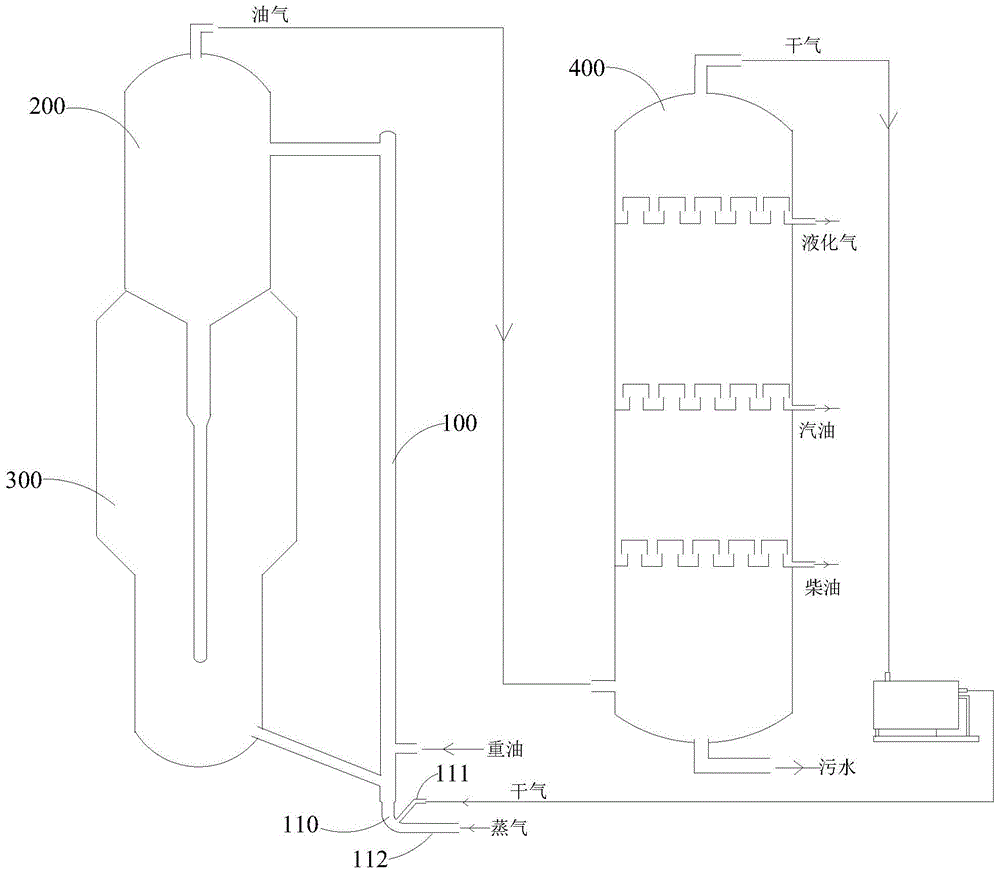
本发明属于石油加工技术领域,具体涉及一种重油深加工方法及装置。
背景技术:
随着交通运输燃料需求量的快速上升,我国的炼油工业把更多的重油,特别是减压渣油,进行深加工。
国内外常用的重油深加工手段主要有热裂化、焦化、催化裂化和加氢裂化等。而热裂化由于技术落后很少发展,而且正逐渐被淘汰,焦化只适用于加工减压渣油,加氢裂化虽然技术上先进、产品收率高、质量好、灵活性大,但设备复杂,而且需大量氢气,因此,技术经济上受到一定限制,所以,使得催化裂化在石油的深加工过程中占居首位。它不仅能将廉价的重质原料变成高价、优质、市场需要的产品,而且现代化的催化裂化装置具有结构简单,原料广泛,运转周期长、操作灵活,催化剂多种多样,操作简便和操作费用低等优点,因此,它在炼油工业中得到广泛的应用。
现有技术中,重油催化裂化反应采用蒸气为流化介质,但存在的问题是反应需要大量蒸气,产生的污水排放量大,耗能,在蒸气作用下高温催化剂易裂崩,成本高,产品中汽油和柴油的含量较低。
技术实现要素:
有鉴于此,有必要提供一种重油深加工方法以解决采用蒸气为流化介质,产生的污水排放量大,耗能,在蒸气作用下高温催化剂易裂崩,成本高,产品中汽油和柴油的含量较低问题。
本发明还提供实现上述方法的重油深加工装置。
为实现上述目的,一方面,本发明提供一种重油深加工方法,包括:以底部设置有预提升气进料管的提升管反应器为反应装置,以干气和蒸气的混合气作为预提升气,以带动催化剂流动,使得重油发生催化裂化反应。
优选的,所述预提升气中干气占总量的10%~30%,其余为蒸气。
优选的,所述干气可以是催化裂化反应产生的干气。
优选的,所述催化剂为分子筛催化剂。
优选的,所述重油催化裂化反应的反应温度为500~520℃,反应压力为0.09~0.12mpa。
另一方面,本发明还提供一种实施上述方法的重油深加工装置,该装置包括:
提升管反应器,所述提升管反应器用于进行催化裂化反应,底部设置有预提升气进料管和重油入口管,所述预提升气进料管设置蒸气进料管和干气进料管,所述蒸气进料管和干气进料管通过比例控制器控制。
优选的,所述重油深加工装置还包括沉降器,所述沉降器用于气固分离,设置有油剂混合物入口、油气出口和催化剂出口,所述油剂混合物入口连接所述提升管反应器的油剂混合物出口。
优选的,所述重油深加工装置还包括再生器,所述再生器用于催化剂再生,设置在沉降器下部,所述再生器的催化剂入口连接沉降器的催化剂出口,所述再生器的催化剂出口连接提升管反应器的催化剂入口。
优选的,所述重油深加工装置还包括分馏塔,所述分馏塔用于油气分馏,底部设置油气入口和污水出口,中部设置液化气出口、汽油出口和柴油出口,顶部设置干气出口,所述分馏塔的油气入口连接沉降器的油气出口,所述分馏塔的干气出口通过空压机后连接干气进料管。
本发明采用上述技术方案,其有益效果在于:
在本发明提供的重油深加工方法,将蒸气和干气以预定比例混合,形成预提升气,以预提升气为催化裂化反应的流化介质,一方面部分干气的存在使得催化剂在提升管反应器中向上流动时不易裂崩,从而在一定程度上保护了催化剂,使得催化剂活性和选择性增强,进而改善了产品分布,提高了产品中汽油和柴油的收率同时降低了干气的产量,增加了经济效益。另一方面干气取代部分蒸气,节能环保,减少了污水排放。
本发明提供的重油深加工装置能够实现上述重油深加工方法,结构简单,便于操作。
附图说明
图1为重油深加工装置的示意图。
图中:提升管反应器100、沉降器200、再生器300、分馏塔400、预提升气进料管110、干气进料管111、蒸气进料管112。
具体实施方式
为了更清楚地说明本发明实施例的技术方案,下面将对实施例中所需要使用的附图作简单的介绍,显而易见地,下面描述中的附图是本发明的一些实施例,对于本领域普通技术人员来讲,在不付出创造性劳动的前提下,还可以根据这些附图获得其他的附图。
本发明实施例提供了一种重油深加工方法,实现该方法所用的装置如图1所示,包括:以底部设置有预提升气进料管的提升管反应器为反应装置,以干气和蒸气的混合气作为预提升气,以带动催化剂流动,使得重油发生催化裂化反应。
该方法将蒸气和干气混合形成预提升气,替代传统的预提升蒸气,在部分干气的存在下使得催化剂在提升管反应器中向上流动时不易裂崩,从而在一定程度上保护了催化剂,使得催化剂活性和选择性增强,进而改善了产品分布,提高了产品中汽油和柴油的含量,另外干气取代部分蒸气,节能环保,减少了污水排放。
进一步的,所述预提升气中干气占总量的10%~30%,其余为蒸气。
进一步的,所述干气可以是催化裂化反应产生的干气,反应得到的干气通入预提升气进料管,实现干气的循环利用,装置自身产生的干气被循环利用,节约资源,降低成本。
进一步的,所述催化剂为分子筛催化剂,所述分子筛催化剂可以是rey型分子筛催化剂或rehy型分子筛催化剂。
进一步的,所述重油催化裂化反应的反应温度为500~520℃,反应压力为0.09~0.12mpa。
请参看图1本发明还提供一种实施上述方法的重油深加工装置,该装置包括:提升管反应器100,所述提升管反应器100用于进行催化裂化反应,底部设置有预提升气进料管110和重油入口管,所述预提升气进料管110设置有蒸气进料管111和干气进料管112,所述蒸气进料管111和干气进料管112通过比例控制器控制。
进一步的,所述重油深加工装置还包括沉降器200,所述沉降器200用于气固分离,设置有油剂混合物入口、油气出口和催化剂出口,所述油剂混合物入口连接所述提升管反应器100的油剂混合物出口。
进一步的,所述重油深加工装置还包括再生器300,所述再生器300用于催化剂再生,设置在沉降器200下部,所述再生器300的催化剂入口连接沉降器200的催化剂出口,所述再生器300的催化剂出口连接提升管反应器100的催化剂入口。
进一步的,所述重油深加工装置还包括分馏塔400,所述分馏塔400用于油气分馏,底部设置油气入口和污水出口,中部设置液化气出口、汽油出口和柴油出口,顶部设置干气出口,所述分馏塔400的油气入口连接沉降器200的油气出口,所述分馏塔400的干气出口通过空压机后连接干气进料管111。
以下通过具体实施例进一步详细说明本发明的技术效果。
实施例1
将预提升气通入提升管反应器100底部的预提升气进料管110,预提升气的加入量为1.5t/h,其中干气为0.15t/h,蒸气为1.35t/h。将重油从重油入口管通入提升管反应器100,重油的加入量为22.8t/h,同时催化剂自再生器300出口进入提升管反应器100,在预提升气的带动下向上流动,当催化剂接触重油后在提升管反应器100内进行催化裂化反应,提升管反应器100的反应区的反应条件为:反应温度505℃,反应压强0.1mpa,生成的油气和催化剂一起进入沉降器200实现气固分离,催化剂自沉降器200出口进入再生器300再生,再生催化剂由再生器300出口流出再次进入提升管反应器100。
分离出的油气自沉降器200顶部出口流出并从分馏塔400底部进入进行分馏,分馏出的干气自分馏塔400顶部出来并通过空压机后进入干气进料管111,液化气自液化气出口流出并进入液化气储罐,汽油自汽油气出口流出并进入汽油储罐,柴油自柴油出口流出并进入柴油储罐,污水从分馏塔400底部流出并进行处理,达标后排放。以蒸气为预提升气时,平均每天补加催化剂1.5t,按照本方案实施,平均每天根据使用情况补加催化剂1.24t。
为验证本发明的效果,采用图1所述的装置和工艺流程,进行多次试验得到产品分布的平均值与对比例得到产品分布的平均值比较可见表1,其中对比例是以蒸气为预提升气,其他条件均与实施例1相同。
表1产品分布
由表1可看出使用本装置和本发明的方法,得到的产品中汽油收率提高0.48%,柴油收率提高了0.32%,干气的收率降低了0.8%,平均每天可节约催化剂260kg,减少成本2600元,并且减少了污水排放量。
实施例2
将预提升气通入提升管反应器100底部的预提升气进料管110,预提升气的加入量为1.5t/h,其中干气为0.22t/h,蒸气为1.28t/h。将重油从重油入口管通入提升管反应器100,重油的加入量为22.8t/h,同时催化剂自再生器300出口进入提升管反应器100,在预提升气的带动下向上流动,当催化剂接触重油后在提升管反应器100内进行催化裂化反应,提升管反应器100的反应区的反应条件为:反应温度505℃,反应压强0.1mpa,生成的油气和催化剂一起进入沉降器200实现气固分离,催化剂自沉降器200出口进入再生器300再生,再生催化剂由再生器300出口流出再次进入提升管反应器100。
分离出的油气自沉降器200顶部出口流出并从分馏塔400底部进入进行分馏,分馏出的干气自分馏塔400顶部出来并通过空压机后进入干气进料管111,液化气自液化气出口流出并进入液化气储罐,汽油自汽油气出口流出并进入汽油储罐,柴油自柴油出口流出并进入柴油储罐,污水从分馏塔400底部流出并进行处理,达标后排放。以蒸气为预提升气时,平均每天补加催化剂1.5t,按照本方案实施,平均每天根据使用情况补加催化剂1.23t。
为验证本发明的效果,采用图1所述的装置和工艺流程,进行多次试验得到产品分布的平均值与对比例得到产品分布的平均值比较可见表2,其中对比例是以蒸气为预提升气,其他条件均与实施例2相同。
表2产品分布
由表1可看出使用本装置和本发明的方法,得到的产品中汽油收率提高0.54%,柴油收率提高了0.36%,干气的收率降低了0.9%,平均每天可节约催化剂270kg,减少成本2700元,并且减少了污水排放量。
实施例3
将预提升气通入提升管反应器100底部的预提升气进料管110,预提升气的加入量为1.5t/h,其中干气为0.27t/h,蒸气为1.23t/h。将重油从重油入口管通入提升管反应器100,重油的加入量为22.8t/h,同时催化剂自再生器300出口进入提升管反应器100,在预提升气的带动下向上流动,当催化剂接触重油后在提升管反应器100内进行催化裂化反应,提升管反应器100的反应区的反应条件为:反应温度505℃,反应压强0.1mpa,生成的油气和催化剂一起进入沉降器200实现气固分离,催化剂自沉降器200出口进入再生器300再生,再生催化剂由再生器300出口流出再次进入提升管反应器100。
分离出的油气自沉降器200顶部出口流出并从分馏塔400底部进入进行分馏,分馏出的干气自分馏塔400顶部出来并通过空压机后进入干气进料管111,液化气自液化气出口流出并进入液化气储罐,汽油自汽油气出口流出并进入汽油储罐,柴油自柴油出口流出并进入柴油储罐,污水从分馏塔400底部流出并进行处理,达标后排放。以蒸气为预提升气时,平均每天补加催化剂1.5t,按照本方案实施,平均每天根据使用情况补加催化剂1.21t。
为验证本发明的效果,采用图1所述的装置和工艺流程,进行多次试验得到产品分布的平均值与对比例得到产品分布的平均值比较可见表3,其中对比例是以蒸气为预提升气,其他条件均与实施例3相同。
本装置进行试验得到产品的分布与未改进得到产品的分布比较可见表3。
表3产品分布
由表3可看出使用本装置和本发明的方法,得到的产品中汽油收率提高0.6%,柴油收率提高了0.4%,干气的收率降低了1%,平均每天可节约催化剂289kg,减少成本2890元,并且减少了污水排放量。
实施例4
将预提升气通入提升管反应器100底部的预提升气进料管110,预提升气的加入量为1.5t/h,其中干气为0.375t/h,蒸气为1.125t/h。将重油从重油入口管通入提升管反应器100,重油的加入量为22.8t/h,同时催化剂自再生器300出口进入提升管反应器100,在预提升气的带动下向上流动,当催化剂接触重油后在提升管反应器100内进行催化裂化反应,提升管反应器100的反应区的反应条件为:反应温度505℃,反应压强0.1mpa,生成的油气和催化剂一起进入沉降器200实现气固分离,催化剂自沉降器200出口进入再生器300再生,再生催化剂由再生器300出口流出再次进入提升管反应器100。
分离出的油气自沉降器200顶部出口流出并从分馏塔400底部进入进行分馏,分馏出的干气自分馏塔400顶部出来并通过空压机后进入干气进料管111,液化气自液化气出口流出并进入液化气储罐,汽油自汽油气出口流出并进入汽油储罐,柴油自柴油出口流出并进入柴油储罐,污水从分馏塔400底部流出并进行处理,达标后排放。以蒸气为预提升气时,平均每天补加催化剂1.5t,按照本方案实施,平均每天根据使用情况补加催化剂1.21t。
为验证本发明的效果,采用图1所述的装置和工艺流程,进行多次试验得到产品分布的平均值与对比例得到产品分布的平均值比较可见表4,其中对比例是以蒸气为预提升气,其他条件均与实施例4相同。
本装置进行试验得到产品的分布与未改进得到产品的分布比较可见表4。
表4产品分布
由表4可看出使用本装置和本发明的方法,得到的产品中汽油收率提高0.42%,柴油收率提高了0.28%,干气的收率降低了0.7%,平均每天可节约催化剂296kg,减少成本2960元,并且减少了污水排放量。
由以上实施例可看出在不影响空压机负荷的作用下,预提升气中干气的百分含量越大,每天节约催化剂的量增大。
以上所揭露的仅为本发明较佳实施例而已,当然不能以此来限定本发明之权利范围,本领域普通技术人员可以理解实现上述实施例的全部或部分流程,并依本发明权利要求所作的等同变化,仍属于发明所涵盖的范围。
本文用于企业家、创业者技术爱好者查询,结果仅供参考。