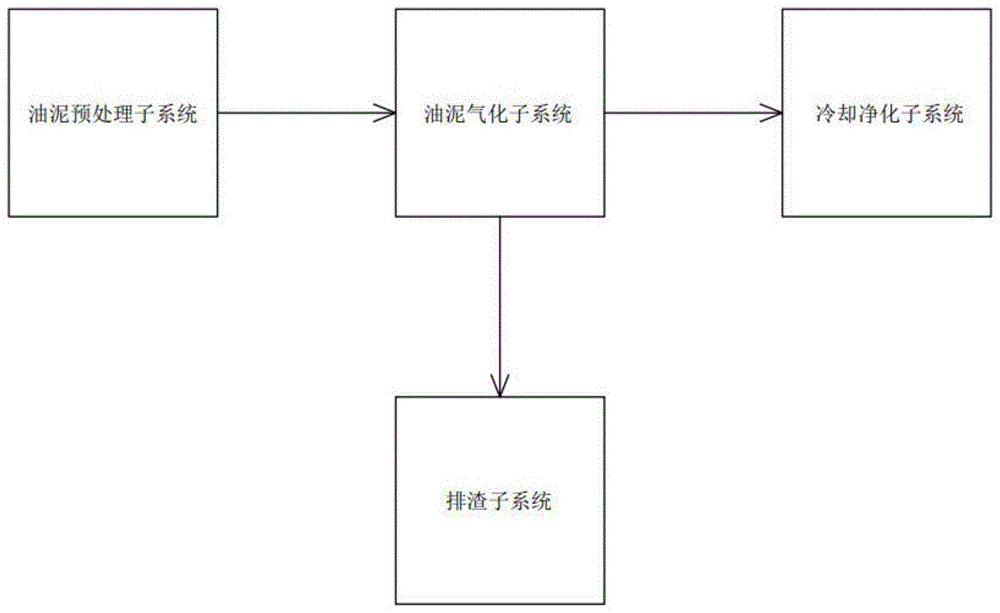
本申请涉及一种油泥气化系统及方法。
背景技术:
含油污泥是一类含有石油等有机质与水、泥沙等组成的稳定胶状体系,其中的有机质除含有重质化原油、半成品渣油及成品油外还含油大量稠环芳烃及有害微生物,其对人体及环境危害巨大,已经被我国列为固体危险废弃物(hw08)项,必须经过有效处理无害化后才可排放。目前国内已有的处理含油污泥的方法,归纳起来有:焚烧法、焦化法、填埋法、地耕法、溶剂萃取法、含油污泥综合利用、固化法、化学破乳法及生物治理等,这些方法均存在处理油泥综合成本高、设备投资大、资源回收率低、二次污染严重,经济性较差,难以大面积推广。
因此,如何能尽可能减少油泥分离处理工艺、将其中的石油类资源充分利用、油泥深度无害化处理并能实现油泥处理经济产出,做到油泥处理良性可收益性发展就成为油泥处理的关键所在。
技术实现要素:
为了解决现有技术的不足之处,作为本申请一方面,本申请提供一种油泥气化系统,包括:油泥预处理子系统,用于将油泥湿磨为油泥浆;油泥气化子系统,用于使油泥浆至少分解出的燃气和熔渣;排渣子系统,用于排出和收集油泥气化子系统分解出的熔渣;冷却净化子系统,用于冷却和净化油泥气化子系统分解出的燃气;其中,油泥预处理子系统连接至油泥气化子系统,油泥气化子系统分别连接至排渣子系统和冷却净化子系统。
进一步地,油泥预处理子系统包括:球磨机、棒磨机或盘式研磨机。
进一步地,油泥气化子系统包括:高压给料泵、油泥浆槽、高压喷嘴、油泥气化炉;其中,高压给料泵连接在油泥浆槽和高压喷嘴之间以使油泥浆槽中的油泥浆送入至高压喷嘴中并在高压喷嘴中与氧气混合,高压喷嘴设置在油泥气化炉内部,油泥汽化炉设有耐火衬,耐火衬围成反应空间,高压喷嘴将油泥浆喷射至反应空间中以使油泥浆在耐火衬的高温辐射下反应分解出燃气。
进一步地,排渣子系统包括:急冻室、渣罐、锁斗、熔渣槽、分离器、沉清槽和循环泵;急冻室连接至油泥汽化炉以使油泥汽化炉中炉渣在重力作用下落入急冻室;渣罐连接至急冻室以使熔渣在被急冷固化后落入渣罐;锁斗连接至渣罐以使渣罐中的熔渣在锁斗中泄压;熔渣槽连接至锁斗以使泄压后的熔渣落入熔渣槽,分离器用于将熔渣槽中的熔渣进行分离以使熔渣被分为粗渣和细灰;沉清槽连接至分离器以使分离器分离出的细灰被送至沉清槽;循环泵连接至沉清槽以使沉清槽沉淀下的细灰经由循环泵循环至油泥气化炉。
进一步地,冷却净化子系统包括:旋风分离器、换热装置和水洗塔;其中,旋风分离器连接至油泥气化炉以使油泥气化炉分解出的燃气进入旋风分离器以进行燃气中固体颗粒物的脱除;换热装置连接至旋风分离器以使燃气携带的热量能用于对油泥进行预热;水洗塔连接至换热装置以使水洗塔对燃气进行净化和降温。
作为本申请的另一方面,本申请还提供一种油泥气化方法,油泥气化方法由一个油泥气化系统所执行,油泥气化系统包括:油泥预处理子系统,用于将油泥湿磨为油泥浆;油泥气化子系统,用于使油泥浆至少分解出的燃气和熔渣;排渣子系统,用于排出和收集油泥气化子系统分解出的熔渣;冷却净化子系统,用于冷却和净化油泥气化子系统分解出的燃气;其中,油泥预处理子系统连接至油泥气化子系统,油泥气化子系统分别连接至排渣子系统和冷却净化子系统;油泥气化方法包括如下步骤:将油泥在油泥预处理子系统中研磨形成油泥浆;将油泥浆输送至油泥气化子系统以使油泥分解出燃气和熔渣;将熔渣输送至排渣子系统以使熔渣被排出或收集;将燃气输送至冷却净化子系统以使燃气被冷却和净化。
进一步地,油泥预处理子系统中研磨形成的油泥浆中固体颗粒物的粒度小于等于90微米的部分质量比例取值范围为40%至86%。
进一步地,油泥气化子系统包括一个用于油泥气化反应的油泥气化炉,油泥气化炉的炉内温度取值范围为1300摄氏度至1500摄氏度。
进一步地,油泥气化炉的炉内压力为2mpa至3.8mpa。
进一步地,冷却净化子系统包括:换热装置,用于预热油泥;油泥气化方法还包括如下步骤:将燃气输送至换热装置以在冷却之前将热量传递至未进入油泥气化炉的油泥。
本申请的有益之处在于:提供一种能有效实现燃气释放同时又能有效利用能源回收的油泥气化系统及方法。
附图说明
构成本申请的一部分的附图用来提供对本申请的进一步理解,使得本申请的其它特征、目的和优点变得更明显。本申请的示意性实施例附图及其说明用于解释本申请,并不构成对本申请的不当限定。在附图中:
图1是根据本申请一种实施例的油泥气化系统的组成示意图;
图2是根据本申请一种实施例的油泥气化系统的一个具体实例结构示意图;
图3是根据本申请一种实施例的油泥气化系统中的油泥气化炉的结构示意图;
图4是根据本申请一种实施例的油泥气化方法的步骤示意图。
具体实施方式
为了使本技术领域的人员更好地理解本申请方案,下面将结合本申请实施例中的附图,对本申请实施例中的技术方案进行清楚、完整地描述,显然,所描述的实施例仅仅是本申请一部分的实施例,而不是全部的实施例。基于本申请中的实施例,本领域普通技术人员在没有做出创造性劳动前提下所获得的所有其他实施例,都应当属于本申请保护的范围。
需要说明的是,本申请的说明书和权利要求书及上述附图中的术语“第一”、“第二”等是用于区别类似的对象,而不必用于描述特定的顺序或先后次序。应该理解这样使用的数据在适当情况下可以互换,以便这里描述的本申请的实施例。此外,术语“包括”和“具有”以及他们的任何变形,意图在于覆盖不排他的包含,例如,包含了一系列步骤或单元的过程、方法、系统、产品或设备不必限于清楚地列出的那些步骤或单元,而是可包括没有清楚地列出的或对于这些过程、方法、产品或设备固有的其它步骤或单元。
在本申请中,术语“上”、“下”、“左”、“右”、“前”、“后”、“顶”、“底”、“内”、“外”、“中”、“竖直”、“水平”、“横向”、“纵向”等指示的方位或位置关系为基于附图所示的方位或位置关系。这些术语主要是为了更好地描述本申请及其实施例,并非用于限定所指示的装置、元件或组成部分必须具有特定方位,或以特定方位进行构造和操作。
并且,上述部分术语除了可以用于表示方位或位置关系以外,还可能用于表示其他含义,例如术语“上”在某些情况下也可能用于表示某种依附关系或连接关系。对于本领域普通技术人员而言,可以根据具体情况理解这些术语在本申请中的具体含义。
此外,术语“安装”、“设置”、“设有”、“连接”、“相连”、“套接”应做广义理解。例如,可以是固定连接,可拆卸连接,或整体式构造;可以是机械连接,或电连接;可以是直接相连,或者是通过中间媒介间接相连,又或者是两个装置、元件或组成部分之间内部的连通。对于本领域普通技术人员而言,可以根据具体情况理解上述术语在本申请中的具体含义。
需要说明的是,在不冲突的情况下,本申请中的实施例及实施例中的特征可以相互组合。下面将参考附图并结合实施例来详细说明本申请。
参照图1和图2所示,本申请的油泥气化系统,包括:油泥预处理子系统,用于将油泥湿磨为油泥浆;油泥气化子系统,用于使油泥浆至少分解出的燃气和熔渣;排渣子系统,用于排出和收集所述油泥气化子系统分解出的熔渣;冷却净化子系统,用于冷却和净化所述油泥气化子系统分解出的燃气;其中,所述油泥预处理子系统连接至所述油泥气化子系统,所述油泥气化子系统分别连接至所述排渣子系统和冷却净化子系统。
作为具体方案,油泥预处理子系统包括:球磨机、棒磨机或盘式研磨机。具体而言,油泥预处理子系统采用油泥用球磨机、棒磨机或盘式研磨机,将油泥湿磨成油泥浆,油泥中固体颗粒物的粒度小于90微米的达到40%至86%,将制成的油泥浆以液力输送至油泥浆槽。
具体而言,油泥气化子系统包括:高压给料泵、油泥浆槽、高压喷嘴、油泥气化炉;其中,高压给料泵连接在油泥浆槽和高压喷嘴之间以使油泥浆槽中的油泥浆送入至高压喷嘴中并在高压喷嘴中与氧气混合,高压喷嘴设置在油泥气化炉内部,油泥汽化炉设有耐火衬,耐火衬围成反应空间,高压喷嘴将油泥浆喷射至反应空间中以使油泥浆在耐火衬的高温辐射下反应分解出燃气。
油泥气化子系统采用高压气化炉,高压给料泵把油泥浆从油泥浆槽送入高压喷嘴,在高压喷嘴中与来自空分系统的氧气混合,油泥通过喷嘴在高速氧气的作用下,破碎、雾化喷入气化炉,每个气化炉设置1至4个油泥浆槽。油泥加压气化过程属于气流床疏相并流反应。氧气和油泥在炉内受到耐火衬里的高温辐射作用,迅速经历预热、水分蒸发、油泥的干馏、挥发物的裂解燃烧以及碳的气化等一系列复杂的物理、化学过程,最后生成以一氧化碳、氢气、二氧化碳和水蒸气为主要成分的湿燃气、熔渣和未反应的碳。
作为更具体的方案,油泥气化炉由上、下两部分组成,气化炉上部是部分氧化室,内壁衬有多层耐火砖,外壁为圆筒形高压容器。内、外壁分别承担耐高温和耐高压的职能,炉壁内衬长期在高温下工作,经受高速油泥浆的冲刷,所以必须具备耐高温和耐磨损的性能。炉壁内衬的耐火材料以氧化铬为主,同时添加少量的氧化铝或氧化镁,视煤灰渣的酸碱性而定。氧化铝适用于酸性灰渣,氧化镁适用于碱性灰渣。油泥采取高压气化,能有效地提高油泥处理能力和燃气品质。
油泥浆和氧气从炉顶的喷嘴高速连续地喷人部分氧化室。高温状态下工作的喷嘴设有冷却水装置。油泥浆喷人气化炉内迅速发生反应,3至15秒钟内即完成气化过程,炉内达到1300至1500℃,气化压力为2.0至3.8mpa。以湿法进料,对油泥的含水率要求更宽泛,含水率可以10至30%;通过燃气与油泥的热交换降低了油泥的粘度,解决了油泥进料时对高压给料泵堵塞问题。
具体而言,排渣子系统包括:急冻室、渣罐、锁斗、熔渣槽、分离器、沉清槽和循环泵。
其中,急冻室连接至油泥汽化炉以使油泥汽化炉中炉渣在重力作用下落入急冻室;渣罐连接至急冻室以使熔渣在被急冷固化后落入渣罐;锁斗连接至渣罐以使渣罐中的熔渣在锁斗中泄压;熔渣槽连接至锁斗以使泄压后的熔渣落入熔渣槽,分离器用于将熔渣槽中的熔渣进行分离以使熔渣被分为粗渣和细灰;沉清槽连接至分离器以使分离器分离出的细灰被送至沉清槽;循环泵连接至沉清槽以使沉清槽沉淀下的细灰经由循环泵循环至油泥气化炉。
排渣子系统包括急冷室和渣罐及配套锁斗及泵等配套设备,在油泥气化系统生成的,以一氧化碳、氢气、二氧化碳和水蒸气为主要成分的湿燃气、熔渣和未反应的碳,一起同流向下,离开反应区,进入炉子底部激冷室水浴,熔渣激冷固化后被分离出来并落入灰锁斗,灰渣在锁斗中泄压后进入熔渣槽,再由熔渣分离器分离出粗熔渣去处理,分离出细灰渣送至沉清槽,沉淀下细灰及煤焦或者再循环入炉,或者送出处理。
具体而言,冷却净化子系统包括:旋风分离器、换热装置和水洗塔;其中,旋风分离器连接至油泥气化炉以使油泥气化炉分解出的燃气进入旋风分离器以进行燃气中固体颗粒物的脱除;换热装置连接至旋风分离器以使燃气携带的热量能用于对油泥进行预热;水洗塔连接至换热装置以使水洗塔对燃气进行净化和降温。
燃气的冷却与净化系统可以采用旋风分离器、油泥储罐换热系统和水洗塔等。最后燃气和饱和蒸汽进入冷却净化系统,先进入旋风分离器脱除参与的固体颗粒物,再与油泥储罐进行热交换,回收余热,同时预热油泥,降低油泥的粘度以利于油泥的加压喷射,最后用水洗塔彻底降温及净化燃气。
参照图4所示,油泥气化方法包括如下步骤:将油泥在油泥预处理子系统中研磨形成油泥浆;将油泥浆输送至油泥气化子系统以使油泥分解出燃气和熔渣;将熔渣输送至排渣子系统以使熔渣被排出或收集;将燃气输送至冷却净化子系统以使燃气被冷却和净化。
具体而言,油泥预处理子系统中研磨形成的油泥浆中固体颗粒物的粒度小于等于90微米的部分质量比例取值范围为40%至86%。
具体而言,油泥气化子系统包括一个用于油泥气化反应的油泥气化炉,油泥气化炉的炉内温度取值范围为1300摄氏度至1500摄氏度。
具体而言,油泥气化炉的炉内压力为2mpa至3.8mpa。
具体而言,冷却净化子系统包括:换热装置,用于预热油泥;油泥气化方法还包括如下步骤:将燃气输送至换热装置以在冷却之前将热量传递至未进入油泥气化炉的油泥。
作为优选方案,参照图3所示,作为一种优选方案,壳体1为压力容器壳体,壳体1周壁的中部设有进料口13,壳体内上部设有与进料口13相连通的水冷壁气化室2,气化室的下端出口连通水冷壁渣屏4;水冷壁渣屏4的出口连通渣室3的物料进口。
渣室的上端设有用于向进入渣室内的油泥渣喷淋激冷水的激冷环管6;渣室的下端通过锥形的渣斗5连接设置在壳体底部的出渣口7;渣室的周壁上设有与激冷水系统相连接的喷水管10,喷水管10上设有多个喷水口。喷水口所喷出的水可使用与激冷环管6同源的水,也可在气化炉外另接水。本实施例中喷水口10的数量为四,且沿渣室的同一圆周周壁均匀布置,喷水口的数量可以根据喷水口的大小即供水流量以及气化炉的尺寸来确定。本实施例中各喷水口10的喷水方向即喷水口横截面的垂线方向与各自对应的渣室外周壁的切线方向的夹角α为40°。
渣室3的内周壁上设有多块用于破碎渣块的凸起14。
渣斗5的周壁上设有多个高压喷水8,本实施例中高压喷水口8的数量为四,这些高压喷水口8位于同一圆周上并沿渣斗的周壁对称布置。根据需要,高压喷水口还可以有多排,即设置在多个圆周上。
具体而言,图3所示方案的工作原理如下:油泥从进料口13进入气化室2内,在气化室2内发生部分氧化反应后,生成的粗合成气上行出气化炉,熔融态的灰渣在重力作用下下行出气化室下部经水冷壁渣斗5进入气化炉渣室3。大部分熔渣直接向下,少部分熔渣附着在渣屏4上沿渣屏向下,这些熔渣下落中被激冷水喷淋激冷后落入渣室水中,熔融态渣激冷后破碎为固态细渣。从喷水口10喷出的水使渣室内的水旋转。旋转的渣水可起到两方面作用:一方面渣块向渣室壁面运动与渣室发生碰装,使渣破碎;另一方面,旋转的渣块可减少熔融渣在渣水中团聚。旋转渣水在旋转过程中碰触到渣室内周壁上的凸起,能进一步破碎渣块。固态细渣经过渣斗5汇集经气化炉的出渣口7排出。
高压喷水口8外接气化炉外高压水系统,在气化炉渣使排渣不畅时打开阀门12,高压水势能转化为动能,利用水击将大渣快打碎。待排渣顺畅时,再关闭阀门12。
以上所述仅为本申请的优选实施例而已,并不用于限制本申请,对于本领域的技术人员来说,本申请可以有各种更改和变化。凡在本申请的精神和原则之内,所作的任何修改、等同替换、改进等,均应包含在本申请的保护范围之内。
本文用于企业家、创业者技术爱好者查询,结果仅供参考。