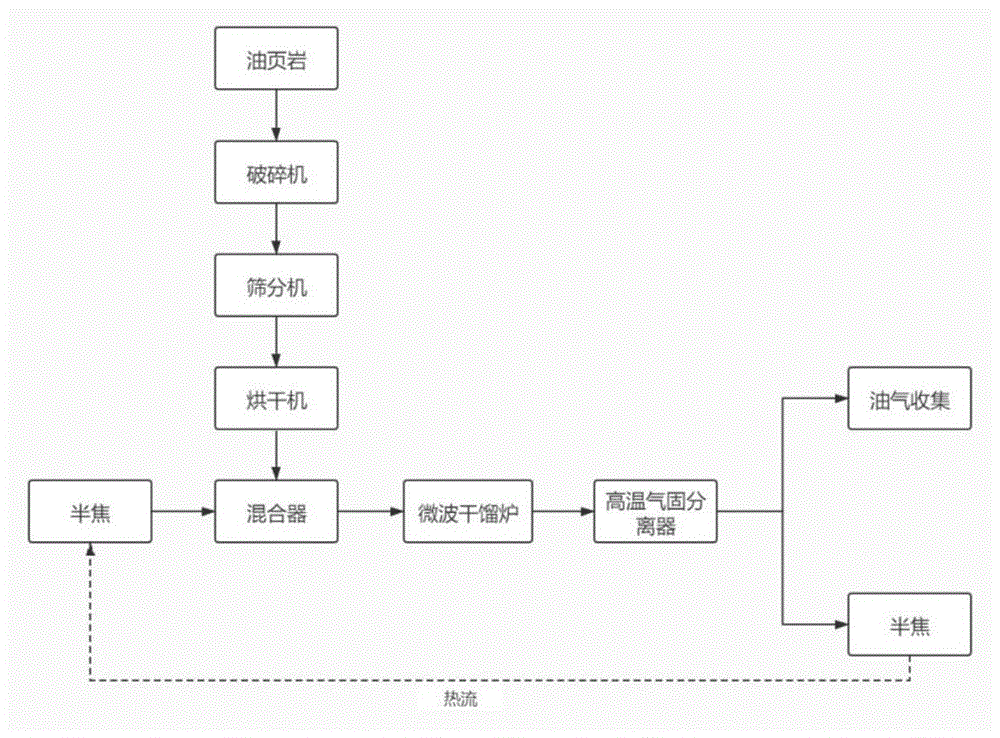
本发明涉及矿物开采利用技术领域,尤其涉及一种地面干馏油页岩的方法。
背景技术:
全世界蕴藏着巨大的油页岩资源,据不完全统计,约有10万亿吨,比煤资源量7万亿吨还多40%,我国油页岩远景储量约2万亿吨,相当于800亿吨页岩油,居世界第四位。油页岩是一种含有有机质的沉积岩,油页岩中含的油母为不溶于有机溶剂的高分子聚合物,干馏后可降解为烃类页岩油,俗称人造石油。
现有的干馏制取页岩油主要有两种方法,即气体热载体法和固体热载体法。气体热载体法靠加热干馏瓦斯气提供干馏热源,一般处理15~75mm的大颗粒油页岩,而15mm以下的小颗粒的油页岩不能进入干馏炉内被利用,而白白的浪费掉。固体热载体法主要是沙子等固体颗粒加热到一定温度后成为固体热载体与油页岩混合,在此接触过程中,固体热载体通过导热将热量传给油页岩实现油页岩干馏,虽然其可以处理25mm以下的小颗粒的油页岩,但是其炼油产率一般较低,只有铝甄油收率的60~85%,且制备的页岩油氮、硫含量较高,品质较差。
因此,如何提高干馏油页岩的油收率和油品质成为现有技术的难题。
技术实现要素:
本发明的目的在于提供一种地面干馏油页岩的方法。本发明采用微波干馏方法处理油页岩,能够提高油收率,同时提高页岩油碳含量,降低页岩油氮、硫含量,提高油品质。
本发明提供了一种地面干馏油页岩的方法,包括:将油页岩原料与热载体混合进行微波干馏,得到页岩油和半焦。
优选地,所述油页岩原料的粒径为25mm以下。
优选地,所述半焦作为热载体循环利用。
优选地,所述微波干馏的温度为550~650℃。
优选地,所述微波干馏的时间为30~120min。
优选地,所述微波干馏的微波功率为400~1000w。
优选地,所述油页岩原料与热载体的质量比为(3~7):1。
优选地,所述油页岩原料在混合前进行烘干处理。
优选地,所述烘干的温度为200~300℃。
优选地,所述烘干的时间为10~30min。
本发明提供了一种地面干馏油页岩的方法,包括:将油页岩原料与热载体混合进行微波干馏,得到页岩油和半焦。本发明采用微波干馏油页岩,利用微波的热效应,电磁能直接作用于介质分子转换成热,且透射性能使物料内外介质同时受热,加热速度快且加热均匀,微波加快了分子的碰撞,从而加剧了反应的进行,进而提高了油页岩的利用率,增加了油收率;同时由于微波本身特性所引起的非热效应,导致了油页岩分子中某些含硫化学键的断裂,从而提高了页岩油中碳含量,降低了页岩油氮、硫含量,提高了油品质。实验结果表明,本发明提供的地面干馏油页岩方法得到的油收率达到7.2%,且页岩油中碳含量增加至87.8%,氮含量降低至1.14%,硫含量降低至0.32%。
附图说明
图1为本发明实施例1中地面干馏油页岩的流程图。
具体实施方式
本发明提供了一种地面干馏油页岩的方法,包括:将油页岩原料与热载体混合进行微波干馏,得到页岩油和半焦。
本发明将油页岩原料与热载体混合,得到混合体。
在本发明中,所述油页岩原料在使用前优选进行烘干处理。在本发明中,所述烘干的温度优选为200~300℃,更优选为250℃;所述烘干的时间优选为10~30min,更优选为20min。
在本发明中,所述烘干处理能够避免干馏过程中水分消耗热量,从而进一步提高油收率。
在本发明中,所述烘干处理优选在烘干机中进行。
在本发明中,所述油页岩原料的粒径优选为25mm以下。在本发明中,当所述油页岩原料的粒径不在上述范围内时,本发明优选对油页岩原料进行破碎和筛分处理。本发明对所述破碎和筛分的操作没有特殊的限定,采用本领域技术人员熟知的破碎和筛分的操作即可。在本发明中,所述破碎优选在破碎机中进行;所述筛分优选在分级筛中进行。
本发明将油页岩原料的粒径限定在上述范围内,能够充分利用干馏厂尾矿,使小粒径油页岩得到综合利用,提高资源利用率;同时由于粒径较小,能够在短时间内被加热到油页岩颗粒的中心,从而使油页岩裂解充分并减少裂解气的停留时间,进一步提高油收率。
本发明对所述油页岩原料的来源没有特殊的限定,采用本领域技术人员熟知的油页岩原料即可。
在本发明中,所述热载体优选包括半焦。在本发明中,所述半焦优选来自微波干馏后得到的半焦。在本发明中,所述半焦作为热载体,能够利用半焦中固定碳燃烧热量对系统供热,系统热效率高;同时半焦作为微波吸收剂循环使用,使半焦得到充分的利用。
在本发明中,所述油页岩原料与热载体的质量比优选为(3~7):1,更优选为(4~6):1,最优选为5:1。本发明将油页岩原料与热载体的质量比限定在上述范围内,油页岩可以更好的与热载体混合接触,使干馏反应完全,且增加了热载体的质量流量,能够为干馏反应提供足够的热量;同时能够吸收更多的微波能量,促进干馏反应的进行,进一步提高油收率及油品质。
本发明对所述油页岩原料与热载体的混合的操作没有特殊的限定,采用本领域技术人员熟知的混合物料的技术方案即可。在本发明中,所述油页岩原料与热载体的混合优选在混合器中进行。
混合完成后,本发明将所述混合得到的产物进行微波干馏,得到页岩油和半焦。
在本发明中,所述干馏的温度优选为550~650℃,更优选为570~620℃,最优选为600℃;所述干馏的时间优选为30~120min,更优选为50~100min,最优选为80min。本发明将干馏的温度和时间限定在上述范围内,能够使得干馏过程充分进行,又避免温度过高引发页岩油蒸汽在高温区的二次裂解,进一步提高油收率。
在本发明中,所述微波干馏的微波功率优选为400~1000w,更优选为500~800w,最优选为600w。本发明将微波干馏的微波功率限定在上述范围内,能够充分发挥微波的热效应,加快分子的碰撞,加剧反应的进行,进一步增加油收率;同时能使油页岩分子中某些含硫化学键断裂,提高页岩油中碳含量,降低页岩油氮、硫含量,进一步提高油品质。
在本发明中,所述微波干馏优选在微波干馏炉中进行。
微波干馏完成后,本发明优选对所述微波干馏的产物进行分离,得到油气和半焦。在本发明中,所述分离优选在高温气固分离器中进行。
得到油气后,本发明优选将所述油气进行冷凝得到页岩油。在本发明中,所述冷凝的温度优选为30~50℃。
得到半焦后,本发明优选将半焦作为热载体和微波吸收剂送入混合器中循环使用。在本发明中,所述微波干馏得到的半焦优选作为热载体循环利用。在本发明中,所述微波干馏得到的半焦作为热载体,利用半焦中固定碳燃烧热量对系统供热,系统热效率高;同时半焦作为微波吸收剂循环使用,使半焦得到充分的利用。
本发明采用微波干馏油页岩,利用微波的热效应,加快了分子的碰撞,加剧了反应的进行,提高了油页岩的利用率,增加了油收率;同时由于微波本身特性所引起的非热效应,导致了油页岩分子中某些含硫化学键的断裂,提高了页岩油中碳含量,降低了页岩油氮、硫含量,提高了油品质。
下面将结合本发明中的实施例,对本发明中的技术方案进行清楚、完整地描述。显然,所描述的实施例仅仅是本发明一部分实施例,而不是全部的实施例。基于本发明中的实施例,本领域普通技术人员在没有做出创造性劳动前提下所获得的所有其他实施例,都属于本发明保护的范围。
实施例1
本实施例中地面干馏油页岩的流程如图1所示,
(1)将开采后的油页岩矿石通过破碎机破碎成为粉末状;
(2)将粉碎后的油页岩粉末通过分级筛进行筛分,获得粒径在25mm以下的油页岩原料;
(3)将油页岩原料在烘干机中250℃烘干20min;
(4)将烘干后的油页岩原料与半焦按质量比5:1在混合器中混合均匀,然后进入微波干馏炉中进行微波干馏,微波功率600w,微波干馏温度为550~650℃,微波干馏时间80min,得到干馏产物;
(5)将干馏产物通入到高温气固分离器中,分离出油气和半焦,将油气在30~50℃进行冷凝,得到页岩油;半焦送入混合器中作为微波吸收剂和热载体循环使用。
实施例2
(1)将开采后的油页岩矿石通过破碎机破碎成为粉末状;
(2)将粉碎后的油页岩粉末通过分级筛进行筛分,获得粒径在25mm以下的油页岩原料;
(3)将油页岩原料在烘干机中250℃烘干20min;
(4)将烘干后的油页岩原料与半焦按质量比5:1在混合器中混合均匀,然后进入微波干馏炉中进行微波干馏,微波功率400w,微波干馏温度为550~650℃,微波干馏时间80min,得到干馏产物;
(5)将干馏产物通入到高温气固分离器中,分离出油气和半焦,将油气在30~50℃进行冷凝,得到页岩油;半焦送入混合器中作为微波吸收剂和热载体循环使用。
实施例3
(1)将开采后的油页岩矿石通过破碎机破碎成为粉末状;
(2)将粉碎后的油页岩粉末通过分级筛进行筛分,获得粒径在25mm以下的油页岩原料;
(3)将油页岩原料在烘干机中250℃烘干20min;
(4)将烘干后的油页岩原料与半焦按质量比5:1在混合器中混合均匀,然后进入微波干馏炉中进行微波干馏,微波功率800w,微波干馏温度为550~650℃,微波干馏时间80min,得到干馏产物;
(5)将干馏产物通入到高温气固分离器中,分离出油气和半焦,将油气在30~50℃进行冷凝,得到页岩油;半焦送入混合器中作为微波吸收剂和热载体循环使用。
对比例1
(1)将开采后的油页岩矿石通过破碎机破碎成为粉末状;
(2)将粉碎后的油页岩粉末通过分级筛进行筛分,获得粒径在25mm以下的油页岩原料;
(3)将油页岩原料在烘干机中250℃烘干20min;
(4)将烘干后的油页岩原料与半焦按质量比5:1在混合器中混合均匀,然后进入干馏炉中进行干馏,干馏温度为550~650℃,干馏时间80min,得到干馏产物;
(5)将干馏产物通入到高温气固分离器中,分离出油气和半焦,将油气在30~50℃进行冷凝,得到页岩油;半焦送入混合器中作为微波吸收剂和热载体循环使用。
计算实施例1~3和对比例1页岩油收率及页岩油中碳、氮、硫含量。经计算,实施例1得到的页岩油的油收率为7.2%,页岩油中碳、氮、硫含量分别为87.80%、1.14%、0.32%;实施例2得到的页岩油的油收率为6.95%,页岩油中碳、氮、硫含量分别为86.80%、0.86%、0.42%;实施例3得到的页岩油的油收率为7.01%,页岩油中碳、氮、硫含量分别为86.50%、0.87%、0.44%;对比例1得到的页岩油的油收率为6.70%,页岩油中碳、氮、硫含量分别为86.44%、1.22%、0.45%。从上述结果可以看出,实施例1~3与对比例1相比,页岩油的收率有所提高,页岩油中碳含量提高,氮、硫含量降低。
综上,本发明提供的地面干馏油页岩的方法中采用微波干馏方法处理油页岩,能够提高油收率,同时提高页岩油碳含量,降低页岩油氮、硫含量,提高油品质。
以上所述仅是本发明的优选实施方式,应当指出,对于本技术领域的普通技术人员来说,在不脱离本发明原理的前提下,还可以做出若干改进和润饰,这些改进和润饰也应视为本发明的保护范围。
本文用于企业家、创业者技术爱好者查询,结果仅供参考。