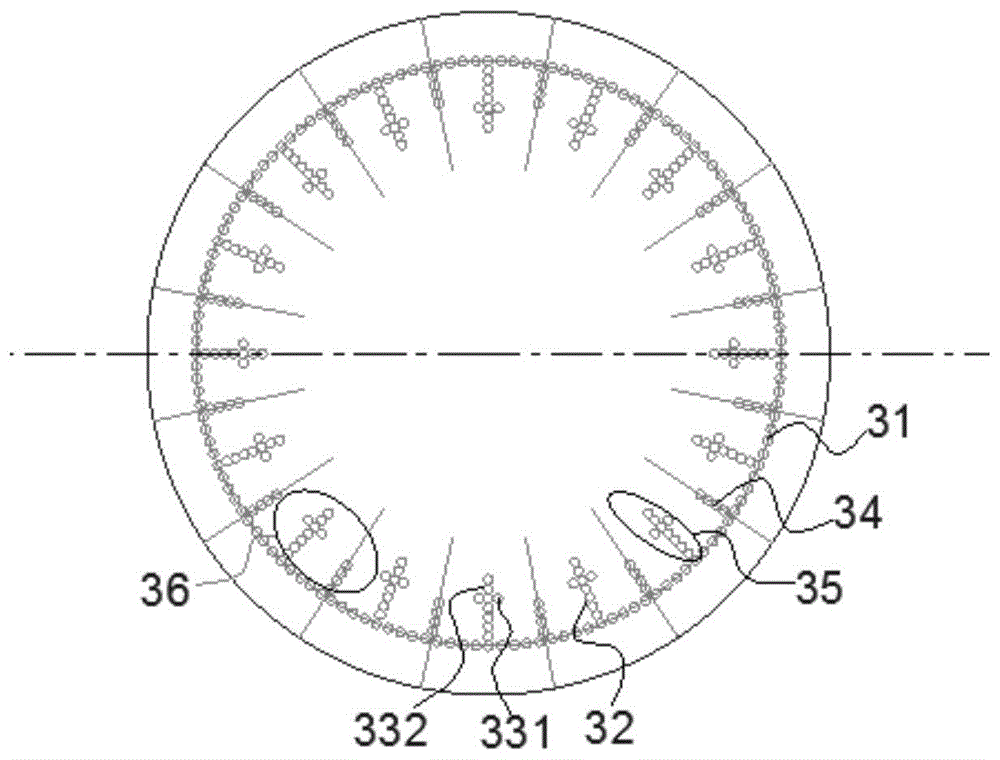
本发明涉及辐射废锅及含其的气化炉、热量回收系统及热量回收工艺。
背景技术:
煤炭气化过程是以氧气(空气、富氧或工业纯氧)、水蒸气作为气化剂,通过化学反应将煤或煤焦中的可燃部分转化为合成气/可燃性气体的工艺过程。气流床气化技术因其良好的技术指标、高处理负荷和环境友好等特点,成为当今煤炭气化的主流技术。气流床气化工艺特点是高温,即利用纯氧/氧化剂与煤发生部分氧化反应,使得煤中的大部分可燃物在1300℃的高温下转化为合成气/可燃气。在如此高的温度下,出气化炉的高温合成气/燃气含有大量高品位显热。随着对煤炭转化过程中能源利用率要求的提高,如何对出气化室的高温合成气进行有效的热量回收成为了越来越迫切需要解决的问题。
针对高温合成气显热回收,已经开发出了相应的辐射锅炉,比如ge水煤浆气化辐射废锅、多喷嘴水煤浆气化辐射废锅、晋华炉水煤浆气化辐射废锅等技术,且均实现工业运行。中国专利文献cn201110083947.x、cn201310322452.7、cn201320708028、201520077861.x、cn201810001028.5公开了高温合成气通过辐射传热方式回收显热的方法或设备。以上现有技术,实现了高温合成气冷却,同时副产一定压力等级的饱和蒸汽。但是其是通过增设辐射屏或增加辐射废锅高度来增大辐射传热面积,以实现对高温合成气热量的有效回收,因此都存在投资高、不能副产过热蒸汽的局限性。中国专利文献cn108410510a公开了一种废锅除灰一体式煤气化炉,其将水冷壁分为上下两段,下段为蒸发段,产生饱和蒸汽,上段为过热段,产生过热蒸汽。其虽解决了不能副产过热蒸汽的局限,但是其过热段直接暴露在高温合成气的高热流密度中,其管道两侧温差很大,容易导致干烧而损坏。并且过热段和蒸发段上下设置,使得在锅炉中部必须设有进出口管道,具有设计复杂、可靠性差的缺点。
技术实现要素:
本发明要解决的技术问题是克服现有技术不能副产过热蒸汽、投资成本高的缺陷,提供了一种低成本、同时能副产过热蒸汽的辐射废锅及含其的气化炉、热量回收系统及热量回收工艺。本发明提供的辐射废锅能副产过热蒸汽,相同处理能力下,本发明的辐射废锅高度较现有技术大幅降低。
本发明是通过下述技术方案来解决上述技术问题:
本发明提供一种辐射废锅,其包括:
筒体水冷壁,所述筒体水冷壁沿所述辐射废锅的内壁面周向设置形成周向密封的辐射废锅空腔;
多组换热单元,所述多组换热单元设置在所述辐射废锅空腔内且沿周向分布;
每组所述换热单元包括对流段和第一辐射屏,所述对流段和所述第一辐射屏处于同一条直线上,且沿由所述筒体水冷壁到所述辐射废锅空腔的中心轴方向依次排列;
每组所述换热单元的所述第一辐射屏和所述对流段组成长辐射屏;
所述第一辐射屏的宽度大于所述对流段的宽度;
所述宽度指的是周向的最大尺寸。
本发明中,所述筒体水冷壁可采用本领域常规的辐射换热器形式,例如辐射面式或辐射管式,较佳地为辐射管式。
其中,所述辐射管式可由多根辐射管通过连接筋板连接而成。
本发明中,多组所述长辐射屏的长度可以相同或不同,较佳地为相同。
其中,所述长度指的是沿径向的尺寸。
本发明中,所述对流段可采用本领域常规的换热器形式,例如列管式或盘管式,较佳地为列管式。
本发明中,所述第一辐射屏可采用本领域常规的换热器形式,例如列管式或盘管式,较佳地为列管式。
本发明中,所述第一辐射屏的宽度w1与所述对流段的宽度w2的比值可为3~7,较佳地为4。
所述第一辐射屏和所述对流段的宽度比值可影响所述对流段所受的热流密度的高低,合适的宽度比可使对流段的换热管不会出现干烧,同时也能产生一定过热度的过热蒸汽。
本发明中,所述第一辐射屏的长度l1和所述对流段的长度l2的比值可为0.4~3,较佳地为0.75,所述长度指的是径向的尺寸。
所述第一辐射屏的长度l1和所述对流段的长度l2的比值可影响所述对流段的换热面积,从而影响所述对流段产生的过热蒸汽的过热度。
本发明中,较佳地,所述第一辐射屏的形状为倒t形,所述第一辐射屏包括:
第一辐射屏端部,所述第一辐射屏端部靠近所述对流段;
第一辐射屏腹部,所述第一辐射屏腹部靠近所述辐射废锅空腔的中心轴。
本发明中,相邻两组所述长辐射屏的间距x1可为(0.05-0.4)d2,其中d2为所述筒体水冷壁的内直径。
较佳地,相邻两组所述长辐射屏的间距x1的范围为300~1000mm,例如419mm、628mm、838mm、977mm,更佳地为628mm。
所述间距x1指的是相邻两组所述长辐射屏的前端之间的距离。
所述前端指的是靠近所述辐射废锅空腔的中心轴的一端。
本发明中,较佳地,每组所述换热单元还包括一个或多个第二辐射屏,所述第二辐射屏的后端紧邻所述筒体水冷壁设置,且所述第二辐射屏的长度l4小于所述长辐射屏的长度l3。
其中,所述长辐射屏的长度l3与所述第二辐射屏的长度l4的比值较佳地为(1.2~3):1,更佳的为2:1。
其中,所述第二辐射屏可采用本领域常规的换热器形式,例如列管式或管式,较佳地为列管式。
其中,每组所述换热单元包括的所述第二辐射屏的数目优选为1个。
其中,较佳地,所述多组换热单元的所述第二辐射屏与所述长辐射屏交替设置。
其中,更佳地,各组所述换热中的所述第二辐射屏与所述长辐射屏交替设置且任意两相邻的所述长辐射屏与所述第二辐射屏的间距x2均相同,所述间距x2指的是所述长辐射屏的后端和所述第二辐射屏的后端之间的周向距离。
其中,所述第二辐射屏与所述长辐射屏的间距x2可为(0.05~0.15)d2,其中d2为所述筒体水冷壁的内直径。
较佳地,所述第二辐射屏与所述长辐射屏的间距x2为300~500mm,例如314mm、418mm、488mm,更佳地为314mm。
现有技术中,辐射废锅空腔中的辐射屏的长度一般都相同,为了减少辐射屏积灰和挂渣,辐射屏之间的距离通常设置得较大,由此导致单位换热空间内的有效换热面积不足,换热效率较低,不能有效回收合成气中的热量。本发明采用长短辐射屏交替设置的方式,既保证了辐射屏间的距离,又有效利用了辐射废锅空腔的空间,有效提升了换热面积,提高了换热效率。
本发明中,较佳地,所述筒体水冷壁的下集箱、各组所述第一辐射屏的下集箱和各组所述第二辐射屏的下集箱相连,形成下辐射集箱,所述下辐射集箱与冷却水进水管相连通。
本发明中,较佳地,所述筒体水冷壁的上集箱、各组所述第一辐射屏的上集箱和各组所述第二辐射屏的上集箱相连,形成上辐射集箱,所述上辐射集箱与饱和汽水混合物的出水管相连通。
本发明中,较佳地,各组所述对流段的下集箱相连,形成下对流集箱,所述下对流集箱与饱和蒸汽的进气管相连通。
本发明中,较佳地,各组所述对流段的上集箱相连,形成上对流集箱,所述上对流集箱与过热蒸汽的出气管相连通。
其中,所述饱和蒸汽为所述饱和汽水混合物进行气液分离所得的气相,所述饱和汽水混合物进行气液分离所得的液相与外来冷却水混合形成所述冷却水。
其中,所述上辐射集箱与所述上对流集箱均设置于所述辐射废锅空腔的顶部。
其中,所述下辐射集箱和所述下对流集箱均设置于所述辐射废锅空腔的底部。
其中,所述上辐射集箱对出所述筒体水冷壁、所述第一辐射屏和所述第二辐射屏的饱和汽水混合物实现汇集;所述下辐射集箱对入冷却水进行分配,分别进入所述筒体水冷壁、所述第一辐射屏和所述第二辐射屏;所述上对流集箱对出所述对流段的过热蒸汽实现汇集;所述下对流集箱对饱和蒸汽进行分配,分别进入所述对流段的各换热管。
本发明中,较佳地,所述新型辐射废锅还包括合成气入口,所述合成气入口设置于所述辐射废锅空腔的顶部,来自气化室的合成废气由所述合成气入口进入所述辐射废锅空腔。
本发明中,所述辐射废锅空腔可以为带上锥和下锥的组合体,也可以为直筒式结构,较佳地为直筒式结构。
现有技术中,辐射废锅空腔的底部通常设有缩口,用于将合成气和熔渣导入激冷室。然而实际工业运行中,缩口处经常发生熔渣堵塞。本发明辐射废锅空腔较佳地选择直筒式结构,可有效减少熔渣堵塞的发生。
其中,所述辐射废锅空腔的高径比h/d可为(2~20):1,较佳地为(3~10):1,更佳地为4:1。
本发明中,较佳地,所述辐射废锅还包括顶部水冷壁段,所述顶部水冷壁段周向设置于所述辐射废锅空腔的顶部,形成所述合成气入口。
本发明中,较佳地,所述辐射废锅还包括激冷段,所述激冷段设置于所述辐射废锅空腔的底部,所述激冷段面向所述辐射废锅空腔的一侧设置有喷淋装置,所述喷淋装置喷射冷却介质对合成气及灰渣进一步冷却降温。
其中,所述喷淋装置包括50~300个激冷水喷头。
进一步的,所述激冷水喷头可为压力旋流雾化喷头。
进一步的,所述激冷水喷头的出口直径可为2~20mm,较佳地为5mm。
进一步的,所述激冷水喷头与所述辐射废锅空腔的径向可呈0~60°角,较佳地为15°。
进一步的,所述激冷水喷头的入口直径可为8~20mm,较佳地为10mm。
进一步的,所述激冷水喷头的水室直径可为30~80mm,较佳地为50mm。
进一步的,所述激冷水喷头的外径可为38~88mm,较佳地为58mm。
本发明中,所述辐射废锅还包括激冷室。
其中,所述激冷室可为本领域常规设置,一般地设置于所述激冷段的下方。
所述激冷室一方面用于储存喷淋水,另一方面对液体熔渣进一步固化使其与合成气分离。
本发明还提供一种包含上述辐射废锅的气化炉。
本发明还提供一种利用上述辐射废锅进行热量回收的系统。
本发明还提供一种利用上述辐射废锅进行热量回收的工艺。
在符合本领域常识的基础上,上述各优选条件,可任意组合,即得本发明各较佳实例。
本发明所用试剂和原料均市售可得。
本发明的积极进步效果在于:
本发明提供的新型辐射废锅能产生过热蒸汽,过热蒸汽的温度可高达420℃,同时产生过热蒸汽的水冷管不易干烧,也无需在锅炉中部设置进出口管道,克服了设计复杂、可靠性差的缺点;相同流量合成气处理能力情况下,本发明提供的辐射废锅的高度较传统辐射废锅可降低43%,大幅降低投资成本。
附图说明
图1为实施例1的水冷壁主体的截面示意图;
图2为图1的局部放大图;
图3为实施例1的辐射废锅应用系统示意图;
图4为实施例1的激冷水喷头的截面示意图。
1-合成气入口;2-辐射废锅空腔;31-筒体水冷壁;32-对流段;33-第一辐射屏;331-第一辐射屏端部;332-第一辐射屏腹部;34-第二辐射屏;35-长辐射屏;36-换热单元;4-顶部水冷壁段;5-激冷段;6-激冷室;7-激冷水喷头;81-下辐射集箱;82-上辐射集箱;83-下对流集箱;84-上对流集箱;91-冷锅炉水进水管;92-锅炉水进水管;93-汽水混合物出水管;94-饱和蒸汽进气管;95-过热蒸汽输出管;96-汽包;101-冷锅炉水;102-合成气;103-过热蒸汽;11-合成气出口;121-激冷水喷头水室;122-激冷水喷头入口;123-激冷水喷头出口;d1-金属壳体直径;d2-筒体水冷壁内径;h-辐射废锅高度;l1-第一辐射屏长度;l2-对流段长度;l3-长辐射屏长度;l4-第二辐射屏长度;w1-第一辐射屏宽度;w2-对流段宽度;d0-激冷水喷头外径;d1-激冷水喷头的水室直径;d2-激冷水喷头的入口直径;d3-激冷水喷头的出口直径。
具体实施方式
参照图1和图2所示,一种辐射废锅,包括:筒体水冷壁31,筒体水冷壁31沿辐射废锅的内壁面周向设置形成周向密封的辐射废锅空腔2;多组换热单元36,多组换热单元36设置在辐射废锅空腔2内且沿周向分布;每组换热单元36包括对流段32和第一辐射屏33,对流段32和第一辐射屏33处于同一条直线上,且沿由筒体水冷壁31向辐射废锅空腔2的中心轴方向依次排列;每组换热单元36的第一辐射屏33和对流段32组成长辐射屏35;第一辐射屏33的宽度大于对流段32的宽度;宽度指的是周向的最大尺寸。
第一辐射屏33的形状为倒t形,第一辐射屏33包括第一辐射屏端部331和第一辐射屏腹部332,第一辐射屏端部331靠近对流段32,第一辐射屏腹部332靠近辐射废锅空腔2的中心轴。
相邻两组长辐射屏35的间距为628mm。每组换热单元36还包括一个第二辐射屏34,第二辐射屏34的后端紧邻筒体水冷壁31设置,且第二辐射屏34的长度小于长辐射屏35的长度;后端为远离辐射废锅空腔2中心轴的一端;第二辐射屏34的长度与长辐射屏35的长度的比值为2:1。每组换热单元36的第二辐射屏34的数量为1个;多组换热单元36的第二辐射屏34与长辐射屏35交替设置。两相邻的第二辐射屏34和长辐射屏35的间距均为314mm。辐射废锅空腔2直筒式结构,辐射废锅空腔2的高径比为4:1。
参照图1和图3所示,冷锅炉水101通过冷锅炉水进水管91进入汽包96,作为汽包96的补水。来自辐射废锅的饱和汽水混合物在由汽水混合物出水管93进入汽包96,在汽包96内气液分离,液体水与冷锅炉水101在汽包96内混合,并在重力作用下经锅炉水进水管92进入下辐射集箱81,下辐射集箱81对锅炉水进行分配,分别进入第一辐射屏33、筒体水冷壁31和第二辐射屏34,接受高温合成气的辐射热量后,生成汽水混合物,经汽水混合物出水管93进入汽包96,在汽包96内气液分离,饱和蒸汽通过饱和蒸汽进入管94进入对流段32,在相对低热流密度的对流传热后生成过热蒸汽,通过过热蒸汽输出管95送出界区。
来自气化炉气化室的合成废气经合成气入口1进入辐射废锅空腔2,在辐射废锅空腔2内与水冷壁主体3和顶部水冷壁段4换热,合成废气经换热后温度大幅降低,激冷段5的喷淋装置上安装有激冷水喷头7,激冷水喷头7喷射激冷水对合成气102进一步冷却降温,合成气102中的熔渣在激冷室6内进一步固化并与合成气102分离,随后经合成气出口11输出气化炉。
参照图4所示,激冷水由激冷水喷头入口122进入激冷水喷头水室121,再由激冷水喷头水室121进入激冷水喷头出口123。激冷水喷头的出口直径d3为5mm,激冷水喷头的入口直径d2为10mm,激冷水喷头的外径d0为58mm,激冷水喷头的水室直径d1为50mm。
下面通过实施例的方式进一步说明本发明,但并不因此将本发明限制在所述的实施例范围之中。下列实施例中未注明具体条件的实验方法,按照常规方法和条件,或按照商品说明书选择。
实施例1
以用于生产化学品为最终用途的水煤浆气化装置,其气化炉的煤炭日处理规模1500t/d,出气化炉进入辐射废锅的高温煤气流量约为190000nm3/h,温度为1340℃,灰渣流量为6800kg/h(其中灰含量约占30%),压力为6.5mpa。为了回收高温煤气所携带的显热,在气化室底部设置一壳体内径d1为4200mm,水冷壁衬里内直径d2为3200mm,直段高度为12m.长辐射屏和第二辐射屏间隔设置,片数均为16片,长辐射屏间距628mm,长辐射屏与第二辐射屏间距314mm,第一辐射屏与对流段长度比为0.75,长辐射屏与第二辐射屏的长度比为2,第一辐射屏与对流段的宽度比为4(具体的,第一辐射屏包括5根水冷管,3根径向分布,2根周向分布,呈倒“t”型,对流段包括4根径向排布的水冷管,第二辐射屏包括4根径向排布的水冷管,水冷管直径为56mm),喷淋装置包括激冷水喷头150个,激冷水喷头的出口直径5mm,激冷水喷头与辐射废锅空腔的径向呈15°夹角,激冷水喷头的入口直径为10mm,激冷水喷头的水室直径为50mm,激冷水喷头的外径为58mm。详细参数如表中的实施例1所示。
通过这种设置,可以实现废锅的高效传热,其中过热蒸汽产量为111t/h,过热蒸汽温度为427℃,出废锅合成气温度约为685℃;辐射废锅高度h为12m,比传统辐射废锅高度降低43%。
实施例2
长辐射屏间距改为419mm,长辐射屏数量改为24组,不设置第二辐射屏,第一辐射屏与对流段的长度比改为0.4(具体的,第一辐射屏包括4根水冷管,2根径向排布分布,2根周向分布;对流段包括5根径向分布的水冷管),其他条件设置均与实施例1相同。
过热蒸汽产量113t/h,过热蒸汽温度为527℃,出废锅合成气温度约为607℃;辐射废锅高度h为12m,比传统辐射废锅高度降低43%。
实施例3
废锅直段高度为15mm,长辐射屏数目改为12组,第二辐射屏12组,长辐射屏间距837mm,长辐射屏与第二辐射屏间距418mm,第一辐射屏与对流段长度比l1/l2为0.6,长辐射屏与第二辐射屏长度l3/l4为1.2(具体的,第一辐射屏包括5根水冷管,其中3根径向分布,2根周向分布在两侧;对流段包括5根径向分布的水冷管;第二辐射屏包括4根径向分布的水冷管),其他条件均与实施例1相同。
过热蒸汽产量约为107t/h,过热蒸汽温度为425℃,出废锅合成气温度约为713℃;辐射废锅高度h为12m,比传统辐射废锅高度降低43%。
实施例4
长辐射屏数目改为16组,第二辐射屏16组,长辐射屏间距628mm,长辐射屏与第二辐射屏间距314mm,第一辐射屏与对流段长度比l1/l2为2.5,长辐射屏与第二辐射屏长度l3/l4为3(具体的,第一辐射屏包括7根水冷管,其中5根径向分布,2根周向分布在两侧,呈倒“t”型;对流段包括2根径向分布的水冷管;第二辐射屏包括4根径向分布的水冷管),其他条件均与实施例1相同。
过热蒸汽产量约为122t/h,过热蒸汽温度为372℃,出废锅合成气温度约为612℃;辐射废锅高度h为15m,比传统辐射废锅高度降低29%。
实施例5
长辐射屏数目为9组,第二辐射屏9组,长辐射屏间距977mm,长辐射屏与第二辐射屏间距489mm,第一辐射屏与对流段长度比l1/l2为0.75,长辐射屏与第二辐射屏长度l3/l4为1.33(具体的,第一辐射屏包括5根水冷管,其中3根径向分布,2根周向分布在两侧,呈倒“t”型;对流段包括4根径向分布的水冷管;第二辐射屏包括6根径向分布的水冷管),其他条件均与实施例1相同。
过热蒸汽产量约为44t/h,过热蒸汽温度为421℃,出废锅合成气温度约为848℃;辐射废锅高度h为8m,比传统辐射废锅高度降低29%。
过热蒸汽产量约为44t/h,过热蒸汽温度为421℃,出废锅合成气温度约为850℃;辐射废锅高度h为8m,比传统辐射废锅高度降低约62%。
对比例1
采用传统辐射废锅,废锅内包括16组辐射屏,每组辐射屏包括5根径向分布的水冷管,其他条件均与实施例1相同。
通过这种设置,可以实现废锅副产饱和蒸汽产量约为108t/h,出废锅合成气温度约为780℃。
表1各实施例和对比例参数设置与效果数据
各实施例和对比例的辐射废锅的参数设置如表1所示。在相同合成气处理能力下实施例1~5能产生过热蒸汽,且实施例1~4产生的过热蒸汽的量均超过100t/h,过热蒸汽温度均高于350℃,有较高的工业应用价值,同时大幅降低了辐射废锅高度,实施例1~4的废锅高度较对比例1降低超过40%,实施例5的辐射废锅高度较对比例1降低超过60%,大幅降低了辐射废锅的体积,提高了单位体积辐射废锅的合成气处理能力。
本文用于企业家、创业者技术爱好者查询,结果仅供参考。