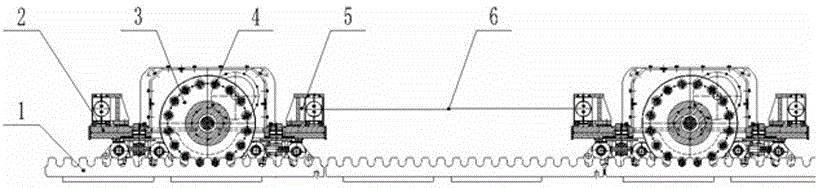
本发明属于矿用齿轨卡轨机车驱动监测领域,尤其涉及矿用齿轨卡轨机车驱动监测与分析方法。
背景技术:
目前国内所使用的齿轨卡轨机车,主要以进口产品为主,其牵引驱动系统,以防爆柴油机为动力源,带动一套闭式液压系统,驱动多组驱动液压马达进行牵引,齿轨卡轨机车在驱动牵引过程中,会根据所需驱动牵引力不同,采用2组、3组或4组驱动装置,每组驱动装置上安装驱动液压马达,以实现单组驱动装置和整车的牵引力需求;
齿轨卡轨机车在驱动牵引过程中,各驱动装置的驱动液压马达之间采用并联方式供液,在正常行驶时驱动轮的滚子销与轨道的齿条啮合,使各驱动轮同步旋转,各驱动装置上的驱动液压马达也以相同转速输出。
在驱动轮的滚子销发生断裂或损伤后,产生断裂的驱动轮会产生空转,带动该驱动装置上的驱动液压马达空转,由于各驱动液压马达采用并联供液方式,当一个马达空转时,则整个液压系统会瞬间失压,造成整个驱动牵引系统瞬间牵引力丢失,特别是在爬坡过程中,产生该种情况时,整个机车会发生溜车风险,造成更大的安全事故。
技术实现要素:
为解决上述问题,本发明提供一种矿用齿轨卡轨机车驱动监测与分析方法,通过“旋速对比——滤除速度误差——驱动轮运行状态断判——机车运行状态断判——上坡或下坡坡度计算——坡度值输出”的方法,实现中央控制器对各驱动轮的状态进行监测与分析,对机车制动进行保护,减少安全隐患。
为实现上述目的,本发明采用如下技术方案:
矿用齿轨卡轨机车驱动监测与分析方法,该方法涉及的装置包括齿轨卡轨轨道、驱动装置架体、驱动轮架、驱动滚子销、驱动装置连杆座、驱动装置连杆、驱动液压马达、驱动连接套筒、旋转编码器、承载导向小车、供电电源、电缆和控制器,若干个驱动滚子销固定于驱动轮架上,驱动轮架通过驱动连接套筒与驱动装置架体连接,驱动轮架能够以驱动连接套筒的中心轴线旋转运动;驱动液压马达与旋转编码器分别固定于驱动连接套筒的两端,使驱动液压马达能够带动驱动连接套筒旋转,并使旋转编码器能够检测到旋转信号;左侧为驱动装置一,右侧为驱动装置二,两个驱动装置连杆座分别固定在驱动装置架体的前后两端;驱动装置连杆的两端与两个驱动装置的驱动装置连杆座连接,组成两组驱动装置的同步运行;四个承载导向小车安装于驱动装置架体的下侧,使驱动装置架体能够在齿轨卡轨轨道上前后移动,移动过程中驱动滚子销与齿轨卡轨轨道中的齿条啮合,实现两组驱动装置的同步移动;2个旋转编码器分别安装于两个驱动装置上,整车安装一个速度传感器,并且两个旋转编码器分别通过电缆与控制器相连,使旋转编码器的信号能够传递给控制器;供电电源通过电缆与控制器连接,以提供控制系统所需要的电源,其步骤如下:
s1:采集数据:旋转编码器与驱动轮传动轴连接,驱动轮的旋转速度与旋转编码器的旋转速度一致;旋转编码器的信号电缆与控制器连接,其中信号结构为脉冲信号,信号电缆与控制器的脉冲采集i/o点连接,旋转编码器的周脉冲量为100pps(即每秒旋转一周的频率为100hz)。
s2:旋速对比:分为各旋转编码器的自对比和两个旋转编码器之间的对比;
(1)各旋转编码器的自对比,通过采集旋转编码器前三秒的脉冲量,并做数值对比处理,以中间数值作为对比数值,通过取三次对比数值的平均数值作为当前的速度旋转编码器的当前脉冲量(或当前频率f),通过脉冲量数值对比平均处理,进行信号的初步过滤,滤除误差,并将处理过后的信号作为真正的速度信号;
自对比中的数值对比逻辑:
设三个数值为f1、f2、f3,若f1≤f2≤f3,则取f2值;若f1≤f3≤f2,则取f3值;若f2≤f3≤f1,则取f3值;若f2≤f1≤f3,则取f1值;若f3≤f1≤f2,则取f1值;若f3≤f2≤f1,则取f2值;
对比后的平均逻辑:
取前三秒的当前频率f,相加后除以3,为过滤后最终频度;
数学逻辑解释:
启动开始前6秒内,时间从前至后,旋转编码器的输出频率为f1、f2、f3、f4、f5、f6,则对应过滤信号后的频率f为
fa=median(f1,f2,f3);//第三秒时的频率
fb=median(f2,fa,f4);//第四秒时的频率
fc=median(fa,fb,f5);//第五秒时的频率
fd=median(fb,fc,f6);//第六秒时的频率
其中“median()”函数为取中间数函数;
(2)两个旋转编码器之间的对比,通过采集两个旋转编码器的两个当前频率,将这两个数值进行对比。
s3:驱动轮运行状态判断:
驱动滚子销断裂分析:当两个速度信号中的某一个速度突然增大,并速度增大信号与原信号比值大于1.5时,可判定为速度突然增大的驱动装置发生滚子销断裂现象,控制器对外输出停车保护信号;其中驱动轮运行状态判断信号为0或1值,若为1,则驱动轮正常;若为0,则判断为驱动轮有问题,机车的控制器会控制机车驱动系统停止运行并控制制动系统电磁阀复位;
制动结构采用一种失效制动方式的液压系统,当液压电磁阀复位,使液压系统无液压时,制动器抱死驱动轮,整个机车系统处于制动状态;当机车开始工作时,液压电磁阀动作,给液压系统加压,打开制动器,松开驱动轮,整个机车系统处于工作状态。
s4:上坡或下坡坡度计算:
(1)上坡或下坡的变坡分析:两个驱动装置从左向右运行,采集两个驱动装置的驱动轮旋转速度信号,并将驱动装置二的旋转速度与驱动装置一的旋转速度进行一下比值,当比值大于1并小于1.5时,驱动装置二的驱动轮的旋转速度略高,可判定为上坡变坡状态;当比值小于1且大于0.67时,驱动装置二的驱动轮的旋转速度略低,可判定为下坡变坡状态;
根据上下坡的变坡状态判断,控制器对外输出变坡状态信号,用于在人机交互的显示器上显示出变坡状态;其中机车运行状态判断信号为0或1值,若为1,则为上坡;若为0,则为下坡;通过机车控制器对信号的转化,在机车司机室内的人机交互显示器上显示出上坡或下坡提示;
(2)上坡的坡度分析:
两个驱动装置从左向右运行,齿轨卡轨轨道的变坡半径为r米,驱动轮半径为r,驱动装置一的驱动轮旋转角速度为ω1,驱动装置二的驱动轮旋转角速度为ω2;
在上坡过程中,可分为四个状态,分别为驱动装置二开始变坡状态,为t0状态;驱动装置一开始变坡并且驱动装置二在上变坡道内,为t1状态;驱动装置二驶出上变坡道并且驱动装置一在上变坡道内,为t2状态;驱动装置一驶出上变坡道,为t3状态;
在不同状态下驱动装置一与驱动装置二的驱动轮旋转角速度有一定关系,可以通过关系条件进行状态判断并计时:
当
当
当
当
根据驱动装置二的驱动轮在上变坡道上的旋转角度,可计算出爬坡角度α:
通过积分算法进行过滤上坡过程中的变速影响,
(3)下坡的坡度分析:
两个驱动装置从左向右运行,齿轨卡轨轨道的变坡半径为r米,驱动轮半径为r,驱动装置一的驱动轮旋转角速度为ω1,驱动装置二的驱动轮旋转角速度为ω2;
在下坡过程中,可分为四个状态,分别为驱动装置二开始变坡状态,为t0状态;驱动装置一开始变坡并且驱动装置二在下变坡道内,为t1状态;驱动装置二驶出下变坡道并且驱动装置一在下变坡道内,为t2状态;驱动装置一驶出下变坡道,为t3状态;
在不同状态下驱动装置一与驱动装置二的驱动轮旋转角速度有一定关系,可以通过关系条件进行状态判断并计时:
当
当
当
当
根据驱动装置二的驱动轮在下变坡道上的旋转角度,可计算出爬坡角度α:
通过积分算法进行过滤下坡过程中的变速影响:
控制器将根据(2)和(3)计算之后的上下坡的坡度数据,对外输出,用于在人机交互的显示器上显示出坡度值数据;其中计算后的坡度值,能以数值形式对外传输;通过机车控制器对信号的数值进行转化,在机车司机室内的人机交互显示器上显示出具体的坡度数值大小,方便司机查看并对速度提前控制,减少安全隐患。
在实际环境中,有各种各样的坡,有连续大角度长坡,有局部小坡,也有上下起伏的坡,根据爬坡角度的不同,会造成变坡向上或向下曲线弧长的不同,但坡度的计算与分析都可以采用这种监测分析驱动轮旋转角度的方法进行。
与现有技术相比,本发明取得的有益效果:
(1)通过对旋转编码器数值采集对比并平均的处理方法,可以使机车运行速度的监测更准确;
(2)通过对各驱动轮的状态进行监测与分析,可实现各驱动轮的运动状态进行实时监测,当某个驱动轮转速突然增大时,可判断为驱动轮滚子销断裂,进行机车制动保护,在机车运行过程中,使用更安全;
(3)通过控制器对各驱动轮的状态进行监测与分析,可实现机车前方是上坡或下坡状态的判断。分析前部驱动装置的驱动轮转速与后部驱动装置的驱动轮转速比值,当比值大于1,为前方轨道上曲变坡状态;当比值小于1,为前方轨道下曲变坡状态。通过转速差值与差值时间,可对上坡或下坡的角度进行预判;坡度的预判,可以方便司机人员对运行速度的提前控制,特别是所运输货物在司机室前方时,司机人员无法看到前方状况,以提高机车运输货物中运行的安全性;
(4)通过算法,可实现机车所运行坡度的计算,减少专用的角度陀螺仪传感器,以降低机车成本。
附图说明
图1为驱动装置连接结构图;
图2为驱动装置剖视图;
图3为控制系统框图;
图4为上下坡变频状态示意图;
图5为坡度分析上坡t0状态图;
图6为坡度分析上坡t1状态图;
图7为坡度分析上坡t2状态图;
图8为坡度分析上坡t3状态图;
图9为坡度分析下坡t0状态图;
图10为坡度分析下坡t1状态图;
图11为坡度分析下坡t2状态图;
图12为坡度分析下坡t3状态图。
1、齿轨卡轨轨道;2、驱动装置架体;3、驱动轮架;4、驱动滚子销;5、驱动装置连杆座;6、驱动装置连杆;7、驱动液压马达;8、驱动连接套筒;9、旋转编码器;10、承载导向小车;11、供电电源;12、电缆;13、控制器。
具体实施方式
下面结合具体实施方式对本发明做进一步说明。
矿用齿轨卡轨机车驱动监测与分析方法,如图1-3,该方法涉及的装置包括齿轨卡轨轨道1、驱动装置架体2、驱动轮架3、驱动滚子销4、驱动装置连杆座5、驱动装置连杆6、驱动液压马达7、驱动连接套筒8、旋转编码器9、承载导向小车10、供电电源11、电缆12和控制器13,十六个驱动滚子销4固定于驱动轮架3上,驱动轮架3通过驱动连接套筒8与驱动装置架体2连接,驱动轮架3能够以驱动连接套筒8的中心轴线旋转运动;驱动液压马达7与旋转编码器9分别固定于驱动连接套筒8的两端,左侧为驱动装置一,右侧为驱动装置二,两个驱动装置连杆座5分别固定在驱动装置架体2的前后两端;驱动装置连杆6的两端与两个驱动装置的驱动装置连杆座5连接,组成两组驱动装置同步运行;四个承载导向小车10安装于驱动装置架体2的下侧,使驱动装置架体2能够在齿轨卡轨轨道1上前后移动;移动过程中驱动滚子销4与齿轨卡轨轨道中的齿条啮合,实现两组驱动装置的同步移动;2个旋转编码器9分别安装于两个驱动装置上,并且两个旋转编码器9分别通过电缆12与控制器13相连,供电电源11通过电缆12与控制器13连接,其步骤如下:
s1:采集数据:旋转编码器与驱动轮传动轴连接,驱动轮的旋转速度与旋转编码器的旋转速度一致;旋转编码器的信号电缆与控制器连接,其中信号结构为脉冲信号,信号电缆与控制器的脉冲采集i/o点连接,旋转编码器的周脉冲量为100pps(即每秒旋转一周的频率为100hz);
s2:旋速对比:分为各旋转编码器的自对比和两个旋转编码器之间的对比;
(1)各旋转编码器的自对比,通过采集旋转编码器前三秒的脉冲量,并做数值对比处理,以中间数值作为对比数值,通过取三次对比数值的平均数值作为当前的速度旋转编码器的当前脉冲量(或当前频率f),通过脉冲量数值对比平均处理,进行信号的初步过滤,滤除误差,并将处理过后的信号作为真正的速度信号;
自对比中的数值对比逻辑:
设三个数值为f1、f2、f3,若f1≤f2≤f3,则取f2值;若f1≤f3≤f2,则取f3值;若f2≤f3≤f1,则取f3值;若f2≤f1≤f3,则取f1值;若f3≤f1≤f2,则取f1值;若f3≤f2≤f1,则取f2值;
对比后的平均逻辑:
取前三秒的当前频率f,相加后除以3,为过滤后最终频度;
数学逻辑解释:
启动开始前6秒内,时间从前至后,旋转编码器的输出频率为f1、f2、f3、f4、f5、f6,则对应过滤信号后的频率f为
fa=median(f1,f2,f3);//第三秒时的频率
fb=median(f2,fa,f4);//第四秒时的频率
fc=median(fa,fb,f5);//第五秒时的频率
fd=median(fb,fc,f6);//第六秒时的频率
其中“median()”函数为取中间数函数;
(2)两个旋转编码器之间的对比,通过采集两个旋转编码器的两个当前频率,将这两个数值进行对比;
s3:驱动轮运行状态判断:
驱动滚子销断裂分析:当两个速度信号中的某一个速度突然增大,并速度增大信号与原信号比值大于1.5时,可判定为速度突然增大的驱动装置发生滚子销断裂现象,控制器对外输出停车保护信号;
其中驱动轮运行状态判断信号为0或1值,若为1,则驱动轮正常;若为0,则判断为驱动轮有问题,机车的控制器会控制机车驱动系统停止运行并控制制动系统电磁阀复位;
制动结构采用一种失效制动方式的液压系统,当液压电磁阀复位,使液压系统无液压时,制动器抱死驱动轮,整个机车系统处于制动状态;当机车开始工作时,液压电磁阀动作,给液压系统加压,打开制动器,松开驱动轮,整个机车系统处于工作状态;
s4:上坡或下坡坡度计算:
(1)上坡或下坡的变坡分析:如图4,两个驱动装置从左向右运行,采集两个驱动装置的驱动轮旋转速度信号,并将驱动装置二的旋转速度与驱动装置一的旋转速度进行一下比值,当比值大于1并小于1.5时,驱动装置二的驱动轮的旋转速度略高,可判定为上坡变坡状态;当比值小于1且大于0.67时,驱动装置二的驱动轮的旋转速度略低,可判定为下坡变坡状态;
根据上下坡的变坡状态判断,控制器对外输出变坡状态信号,用于在人机交互的显示器上显示出变坡状态;其中机车运行状态判断信号为0或1值,若为1,则为上坡;若为0,则为下坡;通过机车控制器对信号的转化,在机车司机室内的人机交互显示器上显示出上坡或下坡提示;
(2)上坡的坡度分析:
如图5-8,两个驱动装置从左向右运行,齿轨卡轨轨道的变坡半径为r米,驱动轮半径为r,驱动装置一的驱动轮旋转角速度为ω1,驱动装置二的驱动轮旋转角速度为ω2;
在上坡过程中,可分为四个状态,分别为驱动装置二开始变坡状态,为t0状态;驱动装置一开始变坡并且驱动装置二在上变坡道内,为t1状态;驱动装置二驶出上变坡道并且驱动装置一在上变坡道内,为t2状态;驱动装置一驶出上变坡道,为t3状态;
在不同状态下驱动装置一与驱动装置二的驱动轮旋转角速度有一定关系,可以通过关系条件进行状态判断并计时:
当
当
当
当
根据驱动装置二的驱动轮在上变坡道上的旋转角度,可计算出爬坡角度α:
通过积分算法进行过滤上坡过程中的变速影响,
(3)下坡的坡度分析:
如图9-12,两个驱动装置从左向右运行,齿轨卡轨轨道的变坡半径为r米,驱动轮半径为r,驱动装置一的驱动轮旋转角速度为ω1,驱动装置二的驱动轮旋转角速度为ω2;
在下坡过程中,可分为四个状态,分别为驱动装置二开始变坡状态,为t0状态;驱动装置一开始变坡并且驱动装置二在下变坡道内,为t1状态;驱动装置二驶出下变坡道并且驱动装置一在下变坡道内,为t2状态;驱动装置一驶出下变坡道,为t3状态;
在不同状态下驱动装置一与驱动装置二的驱动轮旋转角速度有一定关系,可以通过关系条件进行状态判断并计时:
当
当
当
当
根据驱动装置二的驱动轮在下变坡道上的旋转角度,可计算出爬坡角度α:
通过积分算法进行过滤下坡过程中的变速影响:
控制器将根据(2)和(3)计算之后的上下坡的坡度数据,对外输出,用于在人机交互的显示器上显示出坡度值数据;其中计算后的坡度值,能以数值形式对外传输;通过机车控制器对信号的数值进行转化,在机车司机室内的人机交互显示器上显示出具体的坡度数值大小,方便司机查看并对速度提前控制,减少安全隐患。
在实际环境中,有各种各样的坡,有连续大角度长坡,有局部小坡,也有上下起伏的坡,根据爬坡角度的不同,会造成变坡向上或向下曲线弧长的不同,但坡度的计算与分析都可以采用这种监测分析驱动轮旋转角度的方法进行。
本文用于企业家、创业者技术爱好者查询,结果仅供参考。