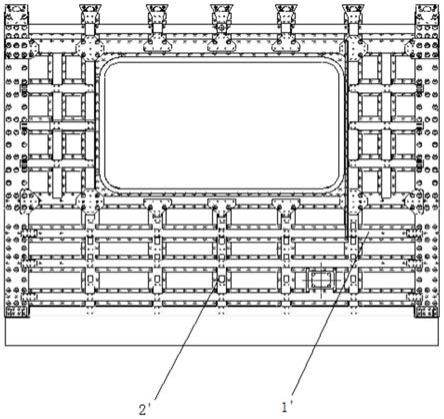
本发明涉及轨道车辆技术领域,尤其是一种轨道车辆侧墙单元模块化组焊结构及组焊方法。
背景技术:
城轨不锈钢车辆侧墙钢结构是一种由上边梁连接的若干个侧墙单元构成典型的薄壁板梁结构,其外板影响整车商品化外观,内侧骨架涉及内装接口。由于城轨产品的定制化要求多、结构差异大,而传统的侧墙单元采用如图1所示的立柱横梁等断面结构,横梁1′的两端与门立柱焊接固定,相邻横梁之间布置多根短纵梁2′,提高侧墙强度,短纵梁与侧墙或立柱横梁焊接固定,焊点、焊缝的排布受梁柱布置及刚度差异的影响,而且焊点多,侧墙单元存在凹凸波浪变形等视觉效果不良的问题。基于上述结构的侧墙单元,在焊接过程中,存在工艺流程长、工装费用大和项目转换周期长等问题。
技术实现要素:
本发明主要目的在于解决上述问题和不足,提供了一种轨道车辆侧墙单元模块化组焊结构,使侧墙单元结构规则,结构强度高,并进一步提供了一种轨道车辆侧墙单元模块化组焊方法,提高焊接质量,焊点、焊缝均匀。
为实现上述目的,本发明首先提供了一种轨道车辆侧墙单元模块化组焊结构,其技术方案是:
一种轨道车辆侧墙单元模块化组焊结构,包括侧墙板,还包括直接与所述侧墙板焊接的横梁组成模块、与所述横梁组成模块卡接后再与所述侧墙板焊接的上层梁柱组成模块,所述横梁组成模块包括窗框、分布在所述窗框四周的与所述侧墙板通长的窗上横梁、窗下横梁及窗框两侧的窗间横梁,所述上层梁柱组成模块包括通过连接梁相互连接的与所述侧墙高度通长的立柱、窗立柱、所述窗框上下两端的窗上立柱及窗下立柱。
进一步的,各横梁上设置有与对应立柱卡接连接卡口。
进一步的,所述侧墙板包括沿所述窗框下边沿切分的上墙板和下墙板。
进一步的,所述下墙板的上方固定乙型梁。
进一步的,所述窗框包括窗框横梁和窗框立柱,所述窗框横梁与所述窗框立柱之间通过弧形窗角板连接。
进一步的,所述窗框横梁与所述窗框立柱的连接处还设有弧形被板。
进一步的,所述弧形窗角板包括弧形段和弧形段两端的直线段,所述直线段分别与所述窗框横梁和窗框立柱固定。
进一步的,所述窗框横梁与所述连接梁为一体结构。
为实现另一发明目的,本发明进一步的提供了一种轨道车辆侧墙单元模块化组焊方法,采用如下技术方案:
一种轨道车辆侧墙单元模块化组焊方法,侧墙单元包括侧墙板、横梁组成模块、上层梁柱组成模块,所述横梁组成模块包括窗框、窗上横梁、窗下横梁及窗间横梁,所述上层梁柱组成模块包括立柱、窗立柱、窗上立柱及窗下立柱,采用如下方式进行组焊:
墙板、横梁组成模块组焊,在焊接平台上进行侧墙板定位,将各横梁按预定位置在侧墙板上初步定位后,进行点焊定位,去掉靠模后,将各横梁焊接在侧墙板上;
上层梁柱组成模块组焊,在连接梁相对窗框位置处预组连接板,以预组后的连接梁为自约束,将立柱、窗立柱、窗上立柱、窗下立柱与连接梁的组装及焊接,形成上层梁柱组成模块;
侧墙单元组焊,在组焊平台上,将上层梁柱组成模块与已组焊后的墙板、横梁组成模块组装,在约束状态下,将上层梁柱组成模块与侧墙焊接。
进一步的,所述窗框包括窗框横梁和窗框立柱,所述窗框横梁与所述窗框立柱之间通过弧形窗角板连接,在进行侧墙单元模块化组焊时,将窗框横梁、窗口立柱及弧形窗角板组装后进行定位焊,再进行组焊,完成窗框组焊后,再与侧墙板组焊。
综上所述,本发明提供的一种轨道车辆侧墙单元模块化组焊结构及组焊方法,通过上下分层模块化结构设计,兼顾外观质量和内侧功能接口,制造工艺简单,经济性良好,与现有技术相比,具有如下有益效果:
1、上下分层模块化设计,分离了外观模块和内侧功能模块,结构形式简单;
2、墙板横梁组成为通用结构,同时实现了焊点/焊缝的规则排布,极大的提升了外观商品化效果;
3、上层梁柱组成保留内装功能接口,其梁柱布置可据项目需求进行适当调整;
4、墙板横梁组成采用通用平台辅以定位靠模,即可实现墙板横梁组装,制造装备型式简单、通用性强,适用于单面点焊/半熔透激光焊两种工艺;
5、上层梁柱组成采用自约束搭接结构,利用梁柱插接口进行自约束,辅以通用组焊工装,即可实现该模块的电阻点焊,工艺方法简单、装备通用性强、经济性良好。
6、侧墙单元制造工艺流程由串行的“侧墙骨架组焊→骨架调修铺板→侧墙单元焊接”,调整为并行的“墙板横梁组成 上层梁柱组成→侧墙单元组焊”,缩短了制造周期,提高了经济性;
7、墙板横梁组成和上层梁柱组成模块均采用了低热输入的点焊、激光焊工艺,有效的控制了焊接变形量,提升了产品外观质量;采用电弧焊工艺进行两个模块的连接,提升了产品的工作效率。
附图说明:
图1:传统技术中侧墙单元结构示意图;
图2:本发明提供的一种轨道车辆侧墙单元模块化组焊结构示意图;
图3:本发明提供的一种轨道车辆侧墙单元模块化组焊结构中墙板、横梁组成模块的示意图;
图4:本发明提供的一种轨道车辆侧墙单元模块化组焊结构中墙板、横梁组成模块侧视图;
图5:本发明提供的一种轨道车辆侧墙单元模块化组焊结构中上层梁柱组成模块结构示意图;
图6:本发明提供的一种轨道车辆侧墙单元模块化组焊结构中窗上连接梁结构示意图;
图7:本发明提供的一种轨道车辆侧墙单元模块化组焊结构中窗上连接梁结构侧视图;
图8:本发明提供的一种轨道车辆侧墙单元模块化组焊结构中连接梁与各立柱连接关系分解示意图;
图9:本发明提供的一种轨道车辆侧墙单元模块化组焊结构中窗框结构示意图;
图10:本发明提供的一种轨道车辆侧墙单元模块化组焊结构中窗框横梁结构示意图;
图11:本发明提供的一种轨道车辆侧墙单元模块化组焊结构中窗口立柱结构示意图;
图12:本发明提供的一种轨道车辆侧墙单元模块化组焊结构中窗角补板结构示意图;
图13:本发明提供的一种轨道车辆侧墙单元模块化组焊结构中窗角的结构示意图;
图14:本发明提供的一种轨道车辆侧墙单元模块化组焊方法中墙板、横梁组成模块靠模示意图;
其中,横梁1′,短纵梁2′,上墙板1,下墙板2,窗框3,窗上横梁4,窗间横梁5,乙型梁6,窗下横梁7,下边梁8,门区立柱9,立柱10,窗立柱11,窗上立柱12,窗下立柱13,窗上连接梁14,窗下连接梁15,窗角补板16,连接板17,窗框立柱18,窗角19,窗角补强板20,通用组焊平台21,组装靠模22,墙板/横梁组成23,上层梁柱组成模块24。
具体实施方式
下面结合附图与具体实施方式对本发明作进一步的详细描述。
本发明首先提供了一种轨道车辆侧墙单元模块化组焊结构,包括侧墙板,还包括直接与侧墙板焊接的横梁组成模块、与横梁组成模块卡接后再与侧墙板焊接的上层梁柱组成模块,横梁组成模块包括窗框3、分布在窗框3四周的与车体侧墙板通长的窗上横梁4、窗下横梁7及窗框3两侧的窗间横梁5,上层梁柱组成模块包括通过连接梁相互连接的与侧墙板高度通长的立柱、窗立柱、所述窗框上下两端的窗上立柱及窗下立柱。
如图2至图13所示,本发明提供的一种轨道车辆侧墙单元模块化组焊结构,可实现模块化生产、组装以及焊接组装,如图2所示,从车厢外由外至内依次包括车体侧墙板、直接与侧墙板固定的横梁组成模块以及与固定在侧墙板上的横梁组成模块卡接后再与侧墙板焊接固定的上层梁柱组成模块。
如图2所示,在本实施例中,侧墙板或与车体(车辆前进方向)长度相等,或由多块板材相互焊接而成,在侧墙板上按车体规划,设置有多个窗口,以其中一个窗口位置处为例,进行后续的结构方面的具体结构。侧墙板包括上墙板1和下墙板2,上墙板1和下墙板2在窗框3的下边缘处切分分割,上墙板1和下墙板2可通过焊接连接,或为一块整板,通过折弯形成,窗框的下边缘与上/下墙板1、2的连接处平齐。为加强车体侧墙强度,与车体内装保持一定距离,并为车体内部线路提供走线空间和相就能的接口,需要侧墙板内侧设置侧墙板内侧(非外观面的一侧)设置支撑和/或加强侧墙强度的结构,如前文所述的横梁组成模块,如图3所示,从上至下,布置有窗上横梁4、窗间横梁5,窗下横梁7及下边梁8,窗上横梁4与侧墙板等长,如图4所示,截面为帽型梁,底部的两个折边与侧墙板的内侧面焊接固定,多根窗上横梁4在窗框3的上方均衡分布。在相邻两窗框3之间,均衡分布多根窗间横梁5,窗间横梁5的两端分别与相邻两窗框3的立柱连接固定。窗框3的下边沿与上墙板1的下边沿平齐或是略高于上墙板1的下边沿,下墙板2的上端固定有乙型梁6,或乙型梁6的与下墙板2固定底板的上边沿与下墙板2的上边沿平齐或略低。下墙板2的最下端,固定下边梁8,如图4所示,下边梁8为正反相连的两个“凵”型结构,即帽型结构的一侧折边具有向上折弯壁,且此所述折弯壁在下墙板2的下侧,且距离下墙板2的下边沿具有一定距离,可使下墙板与车体的其他型材或固定结构固定。在乙型梁6与下边梁8之间,均衡设置多道窗下横梁7,同样的,窗下横梁7也与侧墙体等长。如图4所示,窗下横梁7和窗间横梁5的结构相同,也为帽型结构,但与窗上横梁4的帽型结构的区别在于,窗下横梁7和窗间横梁5的帽型部分非矩形结构,而是等腰梯形结构,梯形的短边朝向车体内侧,以便更好的对车内装饰板进行起来有效支撑。
如图9所示,本发明提供的窗框3的结构示例,包括依窗口大小而设置的沿车体前进方向横向设置的两根窗框横梁和两横梁之间的两根窗框立柱18,窗框横梁与窗框立柱18之间通过弧形窗角板连接。窗框立柱18的两端通过弧形的窗角19与两端的窗框横梁连接。为加强连接强度,在窗角19处还设置有窗角补板16。如图13所示,窗角14为弧形平板结构,采用“激光切割机-卷弧成型”工艺制备,弧形曲率大小可根据具体设计要求确定,在两端保留10mm以上的直线段,配合窗角补板16,避免弧形区域焊接的应力集中问题。如图13所示,窗角补板16为平板结构,采用激光打印机切割机工艺制备,其内外弧度由窗角14弧度确定,两端同样预留10mm以上直线段,配合窗角14,避免窗角结构处的弧形区域焊接的应力集中问题。如图11所示,窗框立柱18截面为乙型结构,采用“激光切割-折弯-线切割齐头”流程制备,两端分别与两组窗角14和窗角补板17的组合结构固定。如图10所示,窗角14的一端与窗框横梁固定,另一端与窗框立柱18固定,配合图3所示,窗框横梁为反帽型结构,可与车体侧墙板等长(沿车体前进方向),中部保留了窗框立柱18连接接口,采用“激光切割-折弯-切切割齐头”工艺制备,接口处保证折弯后齐头,便于固定窗角14及窗角补板17,保证侧墙外观效果。窗框3的各组件制备完成后,采用工装依次组装窗框横梁、窗框立柱18、窗角14和窗角补板16,组装间隙精度满足激光焊接要求≤0.2mm,并采用激光焊进行定位,然后依次进行焊缝的激光焊接。整体焊接完毕后,按照图纸要求检查焊缝质量,并在气动压紧约束的状态下,检测窗框3的平面度,必要时进行矫形。在本发明提供的实施例中,窗框3为立体结构型式,通过设置窗角补板16,使窗框3具备足够的窗角强度,替代了传统的窗角补强,提升了窗角区域的外观效果。各部件采用激光焊接工艺组焊而成,产品平面度达到0.2mm,解决了现有技术中三维窗角无法模压成型的难题,产品精度高、制造成本低。
在各横梁7上设置有多个卡槽,用于与上层梁柱组成模块的相应部件卡接,上层梁柱组成模块包括多根与固定在侧墙板上的各横梁对应卡接后,再与侧墙板焊接固定的立柱。如图5所示,上层梁柱组成模块包括两端与车箱两端的车门结构连接的门区立柱9、侧墙的窗框结构对应的由窗上连接梁14、窗下连接梁15、窗立柱11围成的窗口结构。在门区立柱9与窗立柱11之间或相邻窗立柱11之间,设置一根或多根立柱10,在窗上连接梁14的上方、窗下连接梁15的下方,对应设置有多根窗上立柱12和窗下立柱13。
窗上连接梁14与窗下连接梁15结构相同,镜像对称,以窗上连接梁14为例,介绍窗上/下连接梁14/15的具体结构。如图6所示,窗上连接梁14与车体等长,对应窗框3的窗框立柱18的接口处的外侧,设置有窗立柱11的卡口,并在卡口处设置连接板17,用于与窗立柱11与窗上连接梁连接固定,并在对应窗口13的窗角14处,设置有窗角补强板20。同样的,在窗上连接梁14上设置有与各立柱连接的卡口。
在窗上连接梁14和窗下连接梁15的各个卡处,分别卡接安装门区立柱9、立柱10、窗立柱11及窗上/下立柱12/13,如图8所示,门区立柱9主体呈帽型结构,并在外侧(朝向车门方向)的竖向折边上设置向外的连续的台阶状向外拆弯结构,窗上/下连接梁14的端部两侧壁切割,只留底板,帽型结构的底面与窗上连接梁14端部的底板焊接固定。立柱10、窗上立柱12、窗下立柱13均为帽型结构,卡接到窗上/下连接梁14/15的相应接口处,在窗上/下连接梁14/15的各接处,设置有突出连接梁主体结构的突板,各立柱在接口处与突板焊接,加强焊接固定强度。窗立柱11同样为帽型结构,与其他立柱结构的区别在于,窗立柱11非对称结构,朝向窗口一侧的折边较长,以覆盖窗框立柱18与窗立柱11之间的接缝。
在各横梁、各立柱上均设置有各种必须的内装功能接口或卡口,用于车体侧墙内的线缆或其他部件的走线、布线等,实现现有技术中侧墙结构的相应功能。
在现场生产时,先进行侧墙板、横梁组成模块的组焊,如图14所示,侧墙板放置在通用组焊平台上21,采用整体组装靠模22对侧墙及各横梁等部件进行定位,或采用现有技术以及将来可能出现的其他压紧/制挠装置,将各横梁等部件压紧在侧墙上,并确保一定的挠度,压紧定位后,去掉组装靠模22再进行点焊/激光焊接,形成侧墙/横梁组成模块;将窗上/下连接梁分别与连接板17预组,并形成如图7所示的自约束连接梁,如图8所示,进行立柱10、窗立柱11,窗上/下立柱12/13等零件进行组装以及焊接,形成上层梁柱组成模块。在组焊工装21上,将组装好的上层梁柱组成模块安装在侧墙/横梁组成模块上,使上层梁柱组成模块上的各立柱与各横梁上的相关接口插接定位,在约束状态下,进行电弧焊接,形成完成的侧墙单元。为保证侧墙单元平面度,组焊工装需中部预置向上的反变形,以避免焊后的调修。
需要说明的是,在本实施例中,各横梁、立柱在侧墙板上均衡分面点,以保证组焊完成后的侧墙单元的整体强度均衡,在实际应用中,可根据侧墙结构特征、走/布线的需要等要求,对横梁和/立柱的位置进行相应的调整。
综上所述,本发明提供的一种轨道车辆侧墙单元模块化组焊结构及组焊方法,通过上下分层模块化结构设计,兼顾外观质量和内侧功能接口,制造工艺简单,经济性良好,与现有技术相比,具有如下有益效果:
1、上下分层模块化设计,分离了外观模块和内侧功能模块,结构形式简单;
2、墙板横梁组成为通用结构,同时实现了焊点/焊缝的规则排布,极大的提升了外观商品化效果;
3、上层梁柱组成保留内装功能接口,其梁柱布置可据项目需求进行适当调整;
4、墙板横梁组成采用通用平台辅以定位靠模,即可实现墙板横梁组装,制造装备型式简单、通用性强,适用于单面点焊/半熔透激光焊两种工艺;
5、上层梁柱组成采用自约束搭接结构,利用梁柱插接口进行自约束,辅以通用组焊工装,即可实现该模块的电阻点焊,工艺方法简单、装备通用性强、经济性良好。
6、侧墙单元制造工艺流程由串行的“侧墙骨架组焊→骨架调修铺板→侧墙单元焊接”,调整为并行的“墙板横梁组成 上层梁柱组成→侧墙单元组焊”,缩短了制造周期,提高了经济性;
7、墙板横梁组成和上层梁柱组成模块均采用了低热输入的点焊、激光焊工艺,有效的控制了焊接变形量,提升了产品外观质量;采用电弧焊工艺进行两个模块的连接,提升了产品的工作效率。
如上所述,结合所给出的方案内容,可以衍生出类似的技术方案。但凡是未脱离本发明技术方案的内容,依据本发明的技术实质对以上实施例所作的任何简单修改、等同变化与修饰,均仍属于本发明技术方案的范围内。
本文用于企业家、创业者技术爱好者查询,结果仅供参考。