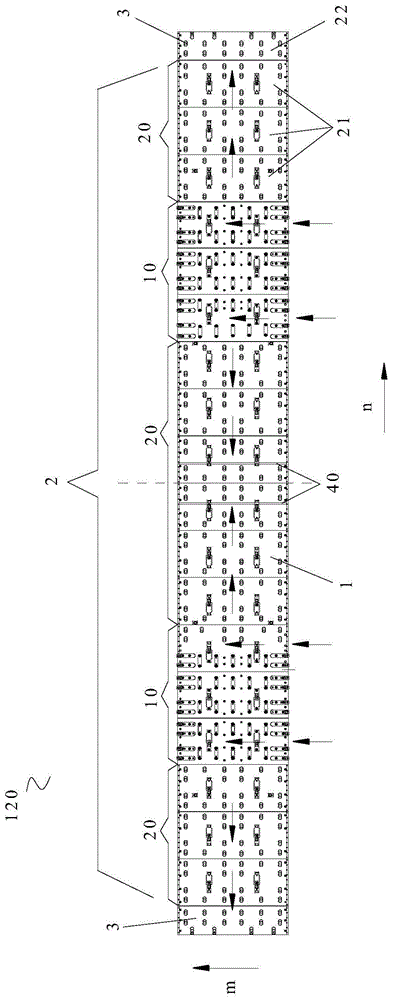
本发明涉及铁路货运设备领域,具体而言,涉及一种地板、车厢以及铁路棚车。
背景技术:
随着国民经济结构调整和网络经济的兴起,近年来全社会货物运输结构发生重大变化,以邮件、包裹为代表的高附加值零散货物的运输需求快速增加。
铁路棚车是铁路物流中应用的主要铁道车辆之一,主要用于运输防雨、雪、潮且防丢失的贵重物品。铁路棚车装卸的货物,大多采用散装、托盘或集装箱笼等方式装载,装卸时大多通过人力将货物码放规整。这种方式会耗费大量人力且装卸效率极低,无法保证电商等货物运输的时效性。为了提升货物的装卸效率,现有技术中采用叉车对棚车内的货物进行码放,这种方式虽然能够提升货物装卸效率,但叉车作业对棚车的内衬的损坏非常严重,导致棚车的维修成本增加。
技术实现要素:
本发明的主要目的在于提供一种地板、车厢以及铁路棚车,以解决现有技术中的铁路棚车的装卸效率低的问题。
为了实现上述目的,根据本发明的一个方面,提供了一种地板,包括:第一地板模组,包括多个;第二地板模组,包括多个,第一地板模组与第二地板模组在预设方向n上交替布置;减摩结构,包括设置于第一地板模组上的多向减摩结构和设置于第二地板模组上的单向减摩结构。
进一步地,两个第一地板模组之间的第二地板模组上设置有标识结构。
进一步地,标识结构包括两条第一标识线,第一标识线与其所在的第二地板模组的中心线之间的距离在575mm至579mm之间;和/或,标识结构包括两条第二标识线,第二标识线与其所在的第二地板模组的中心线之间的距离在1170mm至1174mm之间。
进一步地,地板还包括:第一纵向限位结构,为一个或多个,至少一个第一纵向限位结构设置于标识结构处,第一纵向限位结构包括相对布置的两个第一限位面,两个第一限位面的法线方向与预设方向n平行。
进一步地,第一地板模组为n个,n为偶数,第二地板模组为n 1个,设置于地板的中部的两个第一地板模组之间的第二地板模组的长度为其他第一地板模组的长度以及其他第二地板模组的长度的二倍。进一步地,第一地板模组与第二地板模组均包括多个地板模块,地板还包括:多个第一纵向限位结构,每块地板模块上均设置有第一纵向限位结构,第一纵向限位结构包括相对布置的两个第一限位面,两个第一限位面的法线方向与预设方向n平行。
进一步地,每块地板模块上均设置有两个第一纵向限位结构,两个第一纵向限位结构沿垂直于预设方向n的方向m间隔布置。
进一步地,第一纵向限位结构包括双向卡爪,双向卡爪包括铰接连接的两个相反设置的第一卡钩,两个第一限位面分别设置于对应的两个第一卡钩上,双向卡爪包括凸出于第一地板模组和第二地板模组的上表面的第一工作位置和低于第一地板模组和第二地板模组的上表面第一回收位置。
进一步地,多个第一地板模组与多个第二地板模组形成主地板,地板还包括:两个端板模组,分别位于主地板在预设方向n上的两端;多个第二纵向限位结构,每个端板模组上设置有至少一个第二纵向限位结构,第二纵向限位结构的朝向主地板中心线的一侧具有第二限位面,第二限位面的法线方向与预设方向n平行。
进一步地,第二纵向限位结构包括单向卡爪,单向卡爪包括凸出于第二地板模组的上表面并固定设置的第二卡钩,第二限位面设置于第二卡钩上。
进一步地,第一地板模组与第二地板模组均包括多个地板模块,地板还包括:多个横向限位结构,每块地板模块在垂直于预设方向n的方向m上均设置有相对的两个横向限位结构,横向限位结构包括第三限位面,两个横向限位结构的第三限位面相对,且第三限位面的法线方向与方向m平行。
进一步地,多个横向限位结构包括设置于第一地板模组上的可翻转单向卡爪,第三限位面设置于可翻转单向卡爪上,可翻转单向卡爪包括凸出于第一地板模组和第二地板模组的上表面的第二工作位置和低于第一地板模组和第二地板模组的上表面第二回收位置;和/或,多个横向限位结构包括设置于第二地板模组上的多个第一滚轮,位于同一侧的多个第一滚轮的与集装器具接触的面形成第三限位面。
进一步地,多向减摩结构包括滚珠;和/或,单向减摩结构包括第二滚轮。
根据本发明的另一方面,提供了一种车厢,包括:车厢本体,车厢本体的侧壁上具有沿其长度方向上间隔的布置的多组车门;地板,地板为上述的地板,地板设置于车厢本体内,地板的各第一地板模组均与车门相对。
进一步地,每组车门均包括设置在车厢本体的相对的两个侧壁上的第一车门和第二车门。
根据本发明的另一方面,提供了一种铁路棚车,包括:车厢,车厢包括首尾连接的多个,车厢为上述的车厢。
应用本发明的技术方案,在地板上设置减摩结构,减摩结构能够大大降低货物与地板之间的摩擦力,从而便于货物在地板上移动。因此在码放货物时,可通过人力推动装载货物的集装器具,这种方式与一方面能够提升货物的码放效率,从而提升货物的装卸效率。另一方面能够避免叉车对棚车的内衬造成损伤,降低了棚车的维护成本。减摩结构包括单向减摩结构和多向减摩结构,单向减摩结构能够降低货物在朝向预设方向n移动时货物与地板之间的摩擦力。多向减摩结构能够降低货物在朝向各个方向移动时货物与地板之间的摩擦力。在装载货物时,可先集装器具放置在第一地板模组上,由于第一地板模组上设置多向减摩结构,因此操作人员可对集装器具进行姿态调节,再将集装器具沿预设方向n推至第二地板模组上。本发明的地板排布方式可以实现同时装卸至少三个集装器具,因此能够大大提升货物的装卸效率。
附图说明
构成本申请的一部分的说明书附图用来提供对本发明的进一步理解,本发明的示意性实施例及其说明用于解释本发明,并不构成对本发明的不当限定。在附图中:
图1示出了根据本发明的地板的实施例的俯视图;
图2示出了图1的地板的第一地板模组中的地板模块的俯视图;
图3示出了图2的地板模块侧视图;
图4示出了图1的地板的第二地板模组中的地板模块的俯视图;
图5示出了图1的地板的端板的俯视图;
图6示出了图5的端板的侧视图;
图7示出了图1的地板的第一纵向限位结构位于第一回收位置时的立体结构示意图;
图8示出了图7的地板的第一纵向限位结构位于第一工作位置时的立体结构示意图;
图9示出了图1的地板的可翻转单向卡爪位于第二回收位置时的立体结构示意图;
图10示出了图9的地板的可翻转单向卡爪位于第二工作位置时的立体结构示意图;
图11示出了图1的地板上装载集装器具时的立体结构示意图;
图12示出了图1的地板上装载集装器具时的步骤图;以及
图13示出了根据本发明的车厢的实施例的主视图。
其中,上述附图包括以下附图标记:
1、地板模块;2、主地板;3、端板模组;10、第一地板模组;20、第二地板模组;30、减摩结构;31、多向减摩结构;32、单向减摩结构;40、标识结构;50、第一纵向限位结构;51、第一卡钩;70、第二纵向限位结构;71、第二卡钩;80、集装器具;90、横向限位结构;91、可翻转单向卡爪;92、第一滚轮;110、车门;100、车厢本体;120、地板;130、车厢;140、安装架。
具体实施方式
需要说明的是,在不冲突的情况下,本申请中的实施例及实施例中的特征可以相互组合。下面将参考附图并结合实施例来详细说明本发明。
如图1、图2、图4和图5所示,本实施例的地板包括:第一地板模组10、第二地板模组20以及减摩结构30。其中,第一地板模组10包括多个;第二地板模组20包括多个,第一地板模组10与第二地板模组20在预设方向n上交替布置;减摩结构30包括设置于第一地板模组10上的多向减摩结构31和设置于第二地板模组20上的单向减摩结构32。
应用本实施例的技术方案,在地板上设置减摩结构30,减摩结构30能够大大降低货物与地板之间的摩擦力,从而便于货物在地板上移动。因此在码放货物时,可通过人力推动装载货物的集装器具80,这种方式一方面能够提升货物的码放效率,从而提升货物的装卸效率。另一方面能够避免叉车对棚车的内衬造成损伤,降低了棚车的维护成本。减摩结构30包括单向减摩结构32和多向减摩结构31,单向减摩结构32能够降低货物在水平移动(沿图中n向或与n向相反的方向)时货物与地板之间的摩擦力。多向减摩结构31能够降低货物在朝向水平面内各个方向移动时货物与地板之间的摩擦力。在装载货物时,可先集装器具80放置在第一地板模组10上,由于第一地板模组10上设置多向减摩结构31,因此操作人员可对集装器具80进行姿态调节,再将集装器具80沿预设方向n或与预设方向n向相反的方向推至第二地板模组20上。以第一地板模组10和第二地板模组20均包括2个为例,在放置集装器具80时,可在位于两个第二地板模组20之间的第一地板模组10上放置两个集装器具80,调节好集装器具80的姿态后,第一个集装器具80推至第一地板模组10前端的第二地板模组20上,将第二个集装器具80推至该第一地板模组10后端的第二地板模组20上。在位于端部的第一地板模组10上放置第三个集装器具80,调节好第三个集装器具80的姿态后,将第三个集装器具80推至第二个集装器具80所在的第二地板模组20上。货物的卸载过程为装载过程的逆过程,在此不做赘述。本实施例的地板排布方式可以实现同时装卸至少三个集装器具80,因此能够大大提升货物的装卸效率。
需要说明的是,上述的“前方“指的是棚车的前进方向,上述的“后方”指的是棚车的后退方向。
还需要说明的是,在图中未示出的其他实施例中,减摩结构30也可仅包括多向减摩结构31。但是多向减摩结构31的生产成本高于单向减摩结构32。本实施例同时设置单向减摩结构32和多向减摩结构31有利于降低生产成本。
如图1所示,在本实施例中,两个第一地板模组10之间的第二地板模组20上设置有标识结构40。具体地,在装载货物时,相邻的第一地板模组10需要向两个第一地板模组10之间的第二地板模组20上码放集装器具80,但在第一次向该第二地板模组20上放置集装器具80时,操作人员容易不清楚将集装器具80放置在哪个位置才能使后续从两个第一地板模组10分别码放至第二地板模组20上的集装器具80数量均等。上述结构中,设置有标识结构40使得操作人员第一次向两个第一地板模组10之间的第二地板模组20上码放集装器具80时能够找准集装器具80的放置位置,从而最大程度地提升货物的装卸效率。
需要说明的是,使后两个第一地板模组10分别码放至第二地板模组20上的集装器具80数量均等能够最大程度地提升集装器具80的装卸效率。
还需要说明的是,在地板上承载的集装器具80总数为奇数个,且地板为中心对称结构的情况下,第一次向两个第一地板模组10之间的第二地板模组20上放置第一个集装器具80时,需要将第一个集装器具80放置在两个第一地板模组10之间的第二地板模组20的中心处。这样能够保证后续从两个第一地板模组10移动到该第二地板模组20上的集装器具80的数量均等。后续再向该第二地板模组20码放集装器具80时,可在两个第一地板模组10上分别放置一个集装器具80,并将这两个集装器具80同时推向该第二地板模组20上,使这两个集装器具80紧邻已经放置好的集装器具80。
为了便于操作人员找准第一次放置在两个第一地板模组10之间的第二地板模组20上的集装器具80的具体位置,如图1所示,在本实施例中,标识结构40包括两条第一标识线,第一标识线与其所在的第二地板模组20的中心线之间的距离在575mm至579mm之间。上述结构中,在放置集装器具80时,可将集装器具80推至两条第一标识线内,这种方式便于操作人员找到集装器具80的具体放置位置,从而方便后续的集装器具80装载。
当然,在图中未示出的其他实施例中,在地板上承载的集装器具总数为偶数个,且地板为中心对称结构的情况下,第一次向两个第一地板模组之间的第二地板模组上放置集装器具时,可在两个第一地板模组上分别放置一个集装器具,并将这两个集装器具同时推向该第二地板模组上,使这两个集装器具分别位于该第二地板模组的中心线的两侧即可。后续再向该第二地板模组码放集装器具时,可重复上述操作,将后续码放到第二地板模组上的集装器具紧邻已经放置好的集装器具即可。
同样地,为了便于操作人员找准第一次放置在两个第一地板模组之间的第二地板模组上的集装器具的具体位置,可在该第二地板模组上设置第二标识线,具体地,第二标识线包括两条,第二标识线与其所在的第二地板模组的中心线之间的距离在1170mm至1174mm之间。上述结构中,在放置集装器具时,用户可将两个集装器具推至两条第二标识线内,这种方式便于操作人员找到集装器具的具体放置位置,从而方便后续的集装器具装载。
如果仅将第一次放置在两个第一地板模组10之间的第二地板模组20上的集装器具80推送至指定位置,在集装器具80装载的过程中,已经放置好集装器具80容易因碰撞而发生偏移。为了解决上述问题,如图1、图2、图4以及图5所示,在本实施例中,地板还包括第一纵向限位结构50,第一纵向限位结构50为一个或多个,至少一个第一纵向限位结构50设置于标识结构40处,第一纵向限位结构50包括相对布置的两个第一限位面,两个第一限位面的法线方向与预设方向n平行。上述结构中,在集装器具80已经放置到预定位置处以后,可通过第一纵向限位结构50对集装器具80进行限位,从而避免位于预定位置的集装器具80的位置发生改变。
需要说明的是,上述的“第一纵向限位结构50设置于标识结构40处”指的并非第一纵向限位结构50设置在第一标识线上,而指的是第一纵向限位结构50设置于靠近标识结构40的区域内。第一纵向限位结构50能够标识结构40配合,将集装器具80稳定地限位在预定位置处。
如图1、图11和图12所示,在本实施例中,第一地板模组10为2个,第二地板模组20为3个,设置于地板的中部的两个第一地板模组10之间的第二地板模组20的长度为其他第一地板模组10的长度以及其他第二地板模组20的长度的二倍。即上述地板为中心对称结构。在装载货物时,可先在3个第二地板模组20上分别放置一个集装器具80。其中,位于端部的两个第二地板模组20上的集装箱体分别位于第二地板模组20的远离地板中心线的一端。位于两个第一地板模组10之间的第二地板模组20上的集装器具80位于该块第二地板模组20的中心处。将3个集装器具80分别放置好之后,可在第一个第一地板模组10上放置两个集装器具80,调整好这两个集装器具80的姿态后,同时将集装器具80朝相反方向分别推至与第一个第一地板模组10相邻的两个第二地板模组20上,且使后放置的集装器具80紧邻预先放置好的集装器具80。同样地,也可在第二个第一地板模组10上放置两个集装器具80,这两个集装器具80的码放方式与第一个第一地板模组10上的两个集装器具80相同。需要说明的是,上述结构可同时在两个第一地板模组10上分别放置两个集装器具80,分别放置在两个第一地板模组10上的集装器具80的码放方式互不干涉,因此当最初的3个集装器具80放置好之后,可同时在地板上放置4个集装器具80,并通过4名操作人员同时将这四个集装器具80推送至指定位置,完成货物的码放。卸载货物的过程为上述过程的逆过程在此不做赘述。采用上述的地板排布方式可以实现同时装卸4个集装器具80,因此能够进一步提升货物的装卸效率。
需要说明的是,在图中未示出的其他实施例中,第一地板模组10为n个,n为大于2的偶数,第二地板模组20为n 1个,设置于地板的中部的两个第一地板模组10之间的第二地板模组20的长度为其他第一地板模组10的长度以及其他第二地板模组20的长度的二倍。采用上述的地板排布方式可以实现同时装卸2n个集装器具80,因此能够进一步提升货物的装卸效率。
如图1、图2、图4以及图5所示,在本实施例中,第一地板模组10与第二地板模组20均包括多个地板模块1,地板还包括多个第一纵向限位结构50,每块地板模块1上均设置有第一纵向限位结构50,第一纵向限位结构50包括相对布置的两个第一限位面,两个第一限位面的法线方向与预设方向n平行。上述结构中,第一纵向限位结构50能够限制集装器具80在预设方向n上的位移,防止棚车加速或者制动时集装器具80因惯性的作用发生碰撞,造成集装器具80内货物的损坏。上述结构使得每个集装器具80均能够被第一纵向限位结构50限位,从而降低了集装器具80因惯性的作用而发生碰撞的概率。
需要说明的是,每块地板模块1均包括金属框架、硬质金属板以及设置在硬质金属板上表面的橡胶。橡胶的耐磨效果好,能够提升地板模块1的使用寿命。另外,地板模块1的面积较小,有利于拼接形成第一地板模组10和第二地板模组20。
如图1、图2、图4以及图5所示,在本实施例中,每块地板模块1上均设置有两个第一纵向限位结构50,两个第一纵向限位结构50沿垂直于预设方向n的方向m间隔布置。上述结构使得每个集装器具80均能够两个第一纵向限位结构50限位,使得集装器具80被更稳定地限位在预定位置,从而进一步降低了集装器具80因惯性的作用而发生碰撞的概率。
如图7和图8所示,在本实施例中,第一纵向限位结构50包括双向卡爪,双向卡爪包括铰接连接的两个相反设置的第一卡钩51,两个第一限位面分别设置于对应的两个第一卡钩51上,双向卡爪包括凸出于第一地板模组10和第二地板模组20的上表面的第一工作位置和低于第一地板模组10和第二地板模组20的上表面第一回收位置。上述结构中,第一纵向限位结构50的初始位置为第一回收位置,当每块集装器具80推送至指定位置后,需要向下按压双向卡爪,使双向卡爪由第一回收位置移动至第一工作位置,从而对刚放置好的集装器具80进行限位。上述结构使得第一纵向限位结构50在起到限位作用的同时不会对集装器具80的移动造成干涉。
需要说明的是,在本实施例中,在预设方向n上集装器具80和双向卡爪交替布置,即在预设方向n上相邻的两个双向卡爪限位一个集装器具80,上述结构使得每个集装器具80均能够被限位,从而降低了集装器具80因惯性的作用而发生碰撞的概率。
如图1、图4和图5所示,在本实施例中,多个第一地板模组10与多个第二地板模组20形成主地板2,地板还包括两个端板模组3,分别位于主地板2在预设方向n上的两端;多个第二纵向限位结构70,每个端板模组3上设置有至少一个第二纵向限位结构70,第二纵向限位结构70的朝向主地板2中心线的一侧具有第二限位面,第二限位面的法线方向与预设方向n平行。上述结构中,第二纵向限位结构70能够降低集装器具80碰撞到棚车端盖的概率,从而降低了棚车的维护成本。
如图5和图6所示,在本实施例中,第二纵向限位结构70包括单向卡爪,单向卡爪包括凸出于第二地板模组20的上表面并固定设置的第二卡钩71,第二限位面设置于第二卡钩71上。上述结构中,第二卡钩71固定设置,当集装器具具有朝向棚车的端盖移动的趋势时,第二卡钩71的第二限位面能够对集装器具进行止挡,降低集装器具碰撞到棚车的端盖的概率。上述结构简单,便于生产加工。
棚车在运行过程中一方面需要经常拐弯,另一方面也会经常生产生晃动,这两种情况都会在成集装器具80在方向m或其反向上移动。如果不对集装器具80进行限位,集装器具80就会碰撞棚车的侧壁或者车门,增加棚车的维护成本。为解决上述问题,如图1至图6所示,在本实施例中,第一地板模组10与第二地板模组20均包括多个地板模块1,地板还包括多个横向限位结构90,每块地板模块1在垂直于预设方向n的方向m上均设置有相对的两个横向限位结构90,横向限位结构90包括第三限位面,两个横向限位结构90的第三限位面相对,且第三限位面的法线方向与方向m平行。上述结构中,当集装器具具有朝向棚车的侧壁或者车门移动的趋势时,横向限位结构90会对集装器具形成止挡,从而降低集装器具碰撞棚车的侧壁或者车门的概率,降低了棚车的维护成本。
如图2、图3、图9和图10所示,在本实施例中,多个横向限位结构90包括设置于第一地板模组10上的可翻转单向卡爪91,第三限位面设置于可翻转单向卡爪91上,可翻转单向卡爪91包括凸出于第一地板模组10和第二地板模组20的上表面的第二工作位置和低于第一地板模组10和第二地板模组20的上表面第二回收位置。上述结构中,可翻转单向卡爪91的初始位置为第二回收位置,当第一地板模组10上的集装器具80推送至指定位置后,可将集装器具80在方向m两端的可翻转单向卡爪91由第二回收位置移动至第二工作位置,从而对集装器具80进行限位。上述结构使可翻转单向卡爪91在起到限位作用的同时不会对集装器具80的移动造成干涉,便于操作人员操作。
如图4和图5所示,在本实施例中,多个横向限位结构90包括设置于第二地板模组20上的多个第一滚轮92,位于同一侧的多个第一滚轮92的与集装器具80接触的面形成第三限位面。上述结构中,当集装器具80具有朝向棚车的侧壁移动的趋势时,第一滚轮92能够对集装器具80形成止挡,从而降低集装器具80碰撞到棚车的侧壁的概率,从而降低了棚车的维护成本。需要说明的是,第二地板模组20还包括安装架140,安装架140设置在第二地板模组20在方向m上的两端的边沿处,第一滚轮92的转轴穿设在安装架140上。
如图2和图3所示,在本实施例中,多向减摩结构31包括滚珠。上述结构中,滚珠包括第一外壳和可在外壳内滚动的钢珠,钢珠的上表面凸出于第一地板模组10的上表面。由于钢珠可在外壳内朝向各个方向滚动,因此当集装器具在第一地板模组10上朝多个方向移动时,滚珠均能够起到减摩的效果,上述结构能够便于对放置在第一地板模组10上的集装器具80进行姿态调节,便于将集装器具80沿预设方向推送至预定位置。
如图4至图6所示,在本实施例中,单向减摩结构32包括第二滚轮。上述结构中,滚轮包括第二外壳和设置在第二外壳内的滚柱,滚柱的上表面凸出于第二地板模组20的上表面。上述结构的第二滚轮的结构简单,生产成本低,当集装器具在第二地板模组20上沿预设方向n移动时,能够起到减摩的效果。
如图13所示,本申请还提供了一种车厢,根据本申请的车厢的实施例包括:车厢本体100以及地板120。其中,车厢本体100的侧壁上具有沿其长度方向上间隔的布置的多组车门110;地板120为上述的地板,地板120设置于车厢本体100内,地板120的各第一地板模组10均与车门110相对。具体地,在装载货物时,可从车门110直接将货物运送至第一地板模组10上,调整好货物的姿态后,再将货物从第一地板模组10上移动至相应的第二地板模组20上。上述结构中由于地板120具有能够提升货物的装卸效率的优点,因此具有其的车厢也具备上述优点。
如图13所示,在本实施例中,每组车门110均包括设置在车厢本体100的相对的两个侧壁上的第一车门和第二车门。上述结构中,在装载货物时,可利用叉车将第一个集装器具80从第一车门处装载到第一地板模组10上,同时将第二个集装器具80从第二车门处装载到第一地板模组10上,采用这种方式能够同时将两个集装器具装载到车厢上,第一车门和第二车门分别位于车厢本体100的两个侧壁上,避免两个叉车从同一个车门装载货物时形成干涉。
本申请还包括一种铁路棚车,根据本申请铁路棚车的实施例的包括车厢130,车厢130包括首尾连接的多个,车厢130为上述的车厢。上述结构中,由于车厢130具有能够提升货物的装卸效率的优点,因此具有其的铁路棚车也具备上述优点。
以上所述仅为本发明的优选实施例而已,并不用于限制本发明,对于本领域的技术人员来说,本发明可以有各种更改和变化。凡在本发明的精神和原则之内,所作的任何修改、等同替换、改进等,均应包含在本发明的保护范围之内。
本文用于企业家、创业者技术爱好者查询,结果仅供参考。