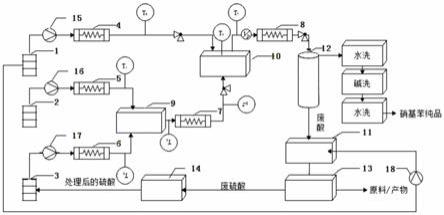
1.本实用新型涉及硝化反应装置领域,具体地说是一种用于硝化反应的微通道反应器系统。
背景技术:
2.硝化反应是工业生产中比较常见的反应之一,其硝化产物在医药、农药、染料等方面占据着重要的地位。
3.传统的硝化工艺一般采用间歇釜式反应器,通常是几个反应釜串联,通过机械搅拌对反应体系进行混合并反应,主要具有以下三个特点:一是反应速度快,放热量大,大多数硝化反应体系属于非均相,反应组分的不均匀分布容易引起局部过热导致危险;二是硝化剂具有强腐蚀性、强氧化性,与油脂、有机化合物(尤其是不饱和有机化合物)接触能引起燃烧或爆炸;三是硝化反应涉及到的物料如硝化产物、副产物酚类等均具有燃爆危险性。因此,一旦发生事故,往往反应时间短,破坏威力大,极易造成巨大的损失。
4.从化学反应上来说,一般瞬时和快速反应,在传统尺度反应设备内进行时主要受传递速率控制,也就意味着一旦传质条件不够,那么极有可能反应结果很差。
5.微通道反应器是指特征尺寸在几十到几百微米之间的,通过特殊工艺加工而得微型反应器。微米级的尺寸结构可令反应物在单位时间内以微米级的粒子状态下彼此相接触,传递速率呈数量级提高,反应速率将会大幅度提高,同时微小的内部空间也确保了有毒易爆物质的安全使用和不稳定物质合成反应的顺利进行。
6.得益于独特的特征尺寸,微通道反应器的比表面积增大了2~4个数量级,相较于一般釜式反应器的比表面积更大,散热能力更好,同时所呈现出的高传热特性,可实现对热量的快速输入、输出,从而维持几乎恒定的反应温度,如果能够将微通道反应器应用于硝化工艺,将获得比传统反应器更加优良的传热性能,以及更加安全的工艺过程。
技术实现要素:
7.本实用新型的目的在于提供一种用于硝化反应的微通道反应器系统,解决了现有硝化技术中存在的物料混合不均匀导致热点产生、副反应多等问题,且更加安全、高效、快速、节能。
8.本实用新型的目的是通过以下技术方案来实现的:
9.一种用于硝化反应的微通道反应器系统,包括原料配制微混合器、硝化微反应器、分液器、后处理微反应器、萃取器、废酸重用浓缩装置和多个储料罐,其中第一储料罐通过第一管路与硝化微反应器的第一输入端相连,第二储料罐通过第二管路与原料配制微混合器的第一输入端相连,第三储料罐通过第三管路与原料配制微混合器的第二输入端相连,所述原料配制微混合器的输出端通过第四管路与硝化微反应器的第二输入端相连,所述硝化微反应器的输出端通过第五管路与分液器相连,所述分液器、后处理微反应器、萃取器、废酸重用浓缩装置和第三储料罐依次串联,同时所述第一储料罐通过第六管路与所述后处
理微反应器的另一输入端相连;在所述第一管路、第二管路、第三管路、第六管路上均设有计量泵,在所述第一管路、第二管路、第三管路、第四管路、第五管路上均设有盘管式换热器和温度传感器。
10.所述第一管路上依次设有第一计量泵、第一盘管式换热器、第一温度传感器和第一安全阀。
11.所述第二管路和第三管路上均依次设有计量泵、盘管式换热器和温度传感器。
12.所述第四管路上依次设有第四温度传感器、第四盘管式换热器、第五温度传感器、第二安全阀。
13.所述第五管路上依次设有第六温度传感器、压力传感器、第五盘管式换热器和第三安全阀。
14.所述硝化微反应器设有多个接口且外层设有换热层,其中第一接口和第二接口为换热层接口,第三接口和第四接口与反应器内部相通,物料a经由第一接口流入换热层,并从第二接口流出后流入第四接口,物料b由第三接口流入并同第四接口流入的物料a进入反应器内部混合反应后由硝化微反应器下端的第五接口流出。
15.所述硝化微反应器内部包括依次相连的输入段、分裂混合段和输出段,其中输入段和输出段均为盘管式结构,分裂混合段包括多级分裂混合。
16.本实用新型的优点与积极效果为:
17.1、本实用新型具有良好的传热性能,硝化反应一般为为强放热反应,通常是在高温、强酸的环境下进行,生产过程的危险系数很高,而微反应器内部的比表面积一般能达到10000~50000m2/m3,传统常规反应器比表面积最大只能达到1000m2/m3,同时微反应器内液相传热系数可到达10000w/(m2·
k),比常规反应器最少大1个数量级以上,使得强放热、不易调控的硝化反应更容易被控制,大大的增加了实验的安全性,因此本实用新型采用微反应器进行硝化反应,在传热性能方面能够及时将反应热移除,进而减少常规反应器中的常见难点“热点”的出现。
18.2、本实用新型具有良好的传质性能,液液非均相硝化体系中,反应物之间的作用主要依靠于各物料之间的界面接触面积,相较于传统常规反应器中依靠机械搅拌,微反应器由于其独特结构使得其内部物料之间的流动形式为层流状态,传质主要依靠分子之间的扩散混合而反应,从微观意义上实现了物料之间的快速混合,极大程度上解决了物料返混和物料混合不均匀的现象,减少反应时间及副产物的生成,提高了产品选择性及转化率。
19.3、本实用新型的硝化微反应器外侧设有换热层,相当于微反应器与换热器集于一体,在0~60s内即能完成反应,更有效的节约了反应时间,所述微反应器使用钽材或其他材质能够运行20~50年,节约成本。
20.4、本实用新型可节省能源,硝化过程依靠硝化反应本身的化学热,被硝化物经过硝化反应的微反应器换热层带走热量后直接流入微反应器反应,极大程度上节约能源。
21.5、本实用新型生成的硝化产物选择性及转化率均高于现有硝化技术所得结果,并且由于微通道反应器持液量小,运行过程中可控性高,安全性高。
附图说明
22.图1为本实用新型装置的结构示意图,
23.图2为图1中的微反应器示意图。
24.其中,1为第一储料罐,2为第二储料罐,3为第三储料罐,4为第一盘管式换热器,5为第二盘管式换热器,6为第三盘管式换热器,7为第四盘管式换热器,8为第五盘管式换热器,9为原料配制微混合器,10为硝化微反应器,11为后处理微反应器,12为分液器,13为萃取器,14为废酸重用浓缩装置,15为第一计量泵,16为第二计量泵,17为第三计量泵,18为第四计量泵,19为第一接口,20为第二接口,21为第三接口,22为第四接口,23为第五接口,24为输入段,25为分裂混合段,26为输出段。
具体实施方式
25.下面结合附图对本实用新型作进一步详述。
26.如图1~2所示,本实用新型装置包括原料配制微混合器9、硝化微反应器10、分液器12、后处理微反应器11、萃取器13、废酸重用浓缩装置14和多个储料罐,其中第一储料罐1通过第一管路与硝化微反应器10的第一输入端相连,且所述第一管路上依次设有第一计量泵15、第一盘管式换热器4、第一温度传感器和第一安全阀,第二储料罐2通过第二管路与原料配制微混合器9的第一输入端相连,第三储料罐3通过第三管路与原料配制微混合器9的第二输入端相连,且所述第二管路上依次设有第二计量泵16、第二盘管式换热器5和第二温度传感器,所述第三管路上依次设有第三计量泵17、第三盘管式换热器6和第三温度传感器,所述原料配制微混合器9的输出端通过第四管路与硝化微反应器10的第二输入端相连,且所述第四管路上依次设有第四温度传感器、第四盘管式换热器7、第五温度传感器、第二安全阀,所述硝化微反应器10的输出端通过第五管路与分液器12相连,且所述第五管路上依次设有第六温度传感器、压力传感器、第五盘管式换热器8和第三安全阀,所述分液器12、后处理微反应器11、萃取器13、废酸重用浓缩装置14和第三储料罐3依次串联,同时所述第一储料罐1通过第六管路与所述后处理微反应器11的另一输入端相连,在所述第六管路上设有第四计量泵18。
27.所述第一盘管式换热器4、第二盘管式换热器5、第三盘管式换热器6、第四盘管式换热器7、第五盘管式换热器8均为盘管式盘管式换热器,所述各个盘管式换热器、各个温度传感器、压力传感器、安全阀均为本领域公知技术且为市购产品。
28.所述分液器12可采用与专利cn202620788u中的连续分液装置相同的结构,所述萃取器13可采用天一萃取cwl
‑
m型离心萃取机,所述废酸重用浓缩装置14可采用德国普霖克搪瓷废酸浓缩机。
29.如图2所示,所述硝化微反应器10为外层设有换热层的微混合器(双面换热),其包括至少四个接口,其中第一接口19和第二接口20为换热层接口,物料a经由第一接口19流入换热层,并从第二接口20流出后直接流入第四接口22,物料b由第三接口21流入并同第四接口22流入的物料a经过微反应器内部的混合区域混合反应后由第五接口23流出。
30.所述硝化微反应器10内部混合区域结构可选择为分裂
‑
重组式多层混合/静态混合式,所述混合区域包括盘管式的输入段24和输出段26,在所述输入段24和输出段26之间设有多级分裂混合的分裂混合段25。所述硝化微反应器10内部通道特征尺寸直径范围在0.5~2mm,长度范围10~50cm。
31.所述原料配制微混合器9和后处理微反应器11为带双面换热的微混合器,其内部
结构为简单碰撞式结构,比如可采用市场购买的康宁微通道g1代玻璃反应器。
32.本实用新型的工作原理为:
33.本实用新型硝化反应的生产工艺包括以下步骤:
34.一、混合酸的制备:将水、硫酸、发烟硝酸分别同时注入至原料配制微混合器9中进行混合,其中发烟硝酸存放于第二储料罐2中,并通过第二计量泵16作用经第二盘管式换热器5进入所述原料配制微混合器9中,硫酸存放于第三储料罐3中,并通过第三计量泵17作用经第三盘管式换热器6进入所述原料配制微混合器9中,硫酸和发烟硝酸在所述原料配制微混合器9中混合均匀,获得原料混合酸。
35.二、硝化反应:将上述混合好的混合酸与被硝化物分别同时注入硝化微反应器10为中进行混合、反应,其中如图1所示,被硝化物存放于第一储料罐1中,并通过第一计量泵15作用经第一盘管式换热器4进入所述硝化微反应器10中,并且如图2所示,被硝化物先经第一接口19流入硝化微反应器10的换热层,并经第二接口20流出换热层,再经第四接口22流入硝化微反应器10内的混合反应区域,原料配制微混合器9内的原料混合酸则经第三接口21流入硝化微反应器10内的混合反应区域,所述硝化微反应器10内的混合反应区域包括输入段24、分裂混合段25和输出段26,其中盘管式的输入段24和输出段可延长反应时间,以达到反应完全效果。
36.三、后处理阶段:所述硝化微反应器10输出的混合物先流入分液器12中连续分液,分离出硝化产物和废酸,硝化产物经过水洗、碱洗、水洗工序获得纯品,废酸则进入后处理微反应器11中,第一储料罐1通过第六管路与所述后处理微反应器11相连,被硝化物通过第六管路上的第四计量泵18作用流入所述后处理微反应器11中反应,后处理微反应器11输出的物料进入萃取器13中进行萃取,其中废硫酸流入废酸重用浓缩装置14进行处理,处理的硫酸可重新流入储存硫酸的第三储料罐3中。
37.下面列举一个应用例进一步说明。
38.本应用例的被硝化物为苯,首先通过原料配制微混合器9连续化配制一种含54%硫酸,30%发烟硝酸,16%水的硝酸和硫酸的混合酸,然后混合酸与苯分别输入硝化微反应器10中,选择硝酸与苯的物质的量比为1,待系统稳定,苯经由硝化微反应器10换热层流动后经硝化微反应器10的第四接口22流入。苯流入换热层前温度为30.5℃,流出后温度为43.2℃,总流量55.8ml/min时,微反应器出口温度为53.1℃,再经过40.3s延时管停留时间后,反应基本完全,所得硝基苯选择性为99.53%,苯的转化率为99.47%。
再多了解一些
本文用于企业家、创业者技术爱好者查询,结果仅供参考。