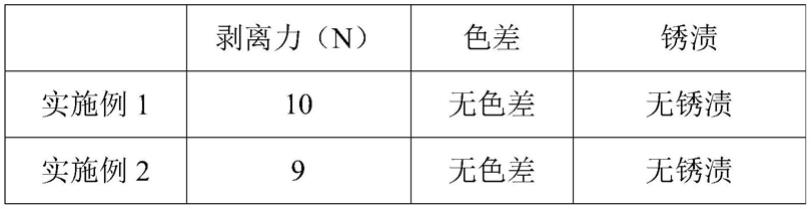
1.本发明属于麂皮面料技术领域,具体涉及一种汽车麂皮面料顶蓬及其制备方法和应用。
背景技术:
2.随着人们生活水平的不断提高,人们对汽车的要求不在是作为一种代步工具,而是要求在代步的同时秉承着外观性,舒适性等特点;汽车内饰作为影响消费者购车欲望的高感区域,主要包含仪表板,中控台,顶蓬等,它结合实用性,安全性,美观和功能性等要求,直接影响消费者的驾乘体验。
3.汽车顶蓬安装在汽车车顶,具有装饰、吸音、隔音、隔热等特点,在越来越追求高性能,环保型,轻量化的时代,汽车内饰顶蓬成为人们选车的一个重要因素,因此对汽车内饰件的要求越来越高。目前顶蓬面料主要包括针织复合面料及无纺复合面料,现有复合面料主要存在以下问题:外观性较差;手感差;易脏污;无纺布面料部耐磨;透气性不良,吸音差,voc不符合要求等缺点。为了提高消费者的造型感知和使用体验,相较于传统针织面料顶蓬麂皮面料顶蓬具有手感柔软及透气防水,耐磨吸音好等特点受到了广大人民的喜爱。
4.cn104890257a公开了一种汽车麂皮面料顶蓬的生产方法,步骤包括:(1)将麂皮面料铺放台上;(2)将聚丙烯复合板材通过烘箱加热软化;(3)将麂皮面料和加热后的聚丙烯复合板材置入模具型腔内采用压力7~9mpa,成型31~35s后进行模压成型制成半成品;(4)将模压成型后的半成品切割成所需尺寸,切割水压为40000~50000psi,切割气压为0.4~0.7mpa;(5)将天窗框架粘贴好并进行翻边。本发明工艺步骤简单,采用麂皮面料制备汽车顶篷外观高雅,手感舒畅;透气性好,耐磨性好,易洗涤,冬暖夏凉且具有高吸音性,能够很好地满足主机厂的技术要求和客户使用要求。cn112080841a公开了一种汽车顶棚用仿麂皮面料的制备方法,通过采用单丝常规纱线进行圆编方式编织坯布,坯布再经过预定型、染色、仿麂皮烘干、起毛和仿麂皮定型步骤的处理;制备出一种能应用于汽车顶棚用的轻量化仿麂皮面料,该仿麂皮面料包括面料层和支撑层,其重量为190~225g/m2;直接使用常规涤纶纱线制作,在染色过程中,不需要强碱强酸溶液处理,减少了生产工艺的难度,降低对环境的污染;且单丝涤纶纱线比碱处理过的纱线略粗,减少处理加工步骤;其支撑层纱线作为成品面料的主体来支撑整个面料,从而保证强度;该轻量化仿麂皮面料还具有较好的阻燃性、较高拉伸强度和收缩弹性、耐磨耗性和耐光色牢度强的优点。
5.然而,麂皮面料表面有绒毛,成型时很容易因上模温度的影响导致绒毛烫伤存在色差影响美观和手感。
6.因此,开发一种贴合牢度高且能够得到无色差的汽车麂皮面料顶蓬的制备方法,是目前本领域急需解决的技术问题。
技术实现要素:
7.针对现有技术的不足,本发明的目的在于提供一种汽车麂皮面料顶蓬及其制备方
法和应用,所述制备方法包括:将麂皮面料进行滚胶、与基材贴合成型,冷切定型,得到所述汽车麂皮面料顶蓬;所述贴合成型在上模温度为55~65℃以及下模温度为145~155℃的模具中进行,所述制备方法通过控制上模温度和下模温度,可以在保证麂皮面料与基材具有较高的贴合牢固性的同时避免麂皮面料因烫伤表面产生色差。
8.为达此目的,本发明采用以下技术方案:
9.第一方面,本发明提供一种汽车麂皮面料顶蓬的制备方法,所述制备方法包括:将麂皮面料进行滚胶、与基材贴合成型,冷切定型,得到所述汽车麂皮面料顶蓬;
10.所述贴合成型在上模温度为55~65℃(例如56℃、57℃、58℃、59℃、60℃、61℃、62℃、63℃或64℃等)以及下模温度为145~155℃(例如146℃、147℃、148℃、149℃、150℃、151℃、152℃、153℃或154℃等)的模具中进行。
11.本发明提供的汽车麂皮面料顶蓬的制备方法首先将麂皮面料进行滚胶,然后将滚胶后的麂皮面料与基材进行贴合成型,通过控制贴合成型中上模的温度为55~65℃以及下模温度为145~155℃,避免了因为上模温度太高容易造成麂皮面料绒毛烫形成色差以及因为上模温度低造成的上下模温差大导致的模具易生锈的问题,进而就可以在保证得到的汽车麂皮面料顶蓬具有较高的贴合牢固性的同时避免了其因烫伤造成的表面色差的问题;且可将滚胶后的麂皮面料与基材先复合好后再放置于模具中贴合保压,避免因基材提前放置于模具时间过长造成水分挥发影响贴合效果;最后将成型后的麂皮面料与基材经冷切定型,即可得到所述汽车麂皮面料顶蓬;所述制备方法整体操作简单,可以有效改善汽车麂皮面料顶蓬的外观,使其表面无色差无白色印痕,进而减少了产品的报废率,具有重要的研究意义。
12.优选地,所述滚胶后麂皮面料的含胶量为5g/0.4m2,为了使得麂皮面料和基布贴合效果更好,还可在贴合时进行喷水。
13.优选地,所述基材通过如下方法制备得到,所述方法包括:将pu泡棉依次进行滚胶、喷水、材料组合、热压成型、冷却定型和水刀切割,得到所述基材。
14.优选地,所述材料组合包括将pu泡棉、玻璃纤维、pe膜、基布和底布组合。
15.优选地,所述滚胶后pu泡棉的上含胶量为20~30g/0.4m2,例如21g/0.4m2、22g/0.4m2、23g/0.4m2、24g/0.4m2、25g/0.4m2、26g/0.4m2、27g/0.4m2、28g/0.4m2或29g/0.4m2,以及上述点值之间的具体点值,限于篇幅及出于简明的考虑,本发明不再穷尽列举所述范围包括的具体点值。
16.优选地,所述滚胶后pu泡棉的下含胶量为20~40g/0.4m2,例如22g/0.4m2、24g/0.4m2、26g/0.4m2、28g/0.4m2、30g/0.4m2、32g/0.4m2、34g/0.4m2、36g/0.4m2或38g/0.4m2,以及上述点值之间的具体点值,限于篇幅及出于简明的考虑,本发明不再穷尽列举所述范围包括的具体点值。
17.优选地,所述喷水后pu泡棉的含水量为90~130g/0.4m2,例如93g/0.4m2、96g/0.4m2、99g/0.4m2、112g/0.4m2、116g/0.4m2、120g/0.4m2、124g/0.4m2、126g/0.4m2或128g/0.4m2,以及上述点值之间的具体点值,限于篇幅及出于简明的考虑,本发明不再穷尽列举所述范围包括的具体点值。
18.优选地,所述贴合成型前还包括喷洒催化剂于基材上表面的步骤。
19.所述催化剂为固氨(kc100l),催化剂的用量为水的3%。
20.优选地,所述贴合成型的成型压力为8~12mpa,例如8.3mpa、8.6mpa、8.9mpa、9.2mpa、9.5mpa、9.8mpa、10.3mpa、10.6mpa、10.9mpa、11.3mpa、11.6mpa或11.9mpa,以及上述点值之间的具体点值,限于篇幅及出于简明的考虑,本发明不再穷尽列举所述范围包括的具体点值。
21.优选地,所述贴合成型的保压时间为100~140s,例如105s、110s、115s、120s、125s、130s、135s或140s,以及上述点值之间的具体点值,限于篇幅及出于简明的考虑,本发明不再穷尽列举所述范围包括的具体点值。
22.优选地,所述冷却定型于冷却工装中进行。
23.作为本发明的优选技术方案,所述制备方法包括如下步骤:
24.(1)将pu泡棉依次进行滚胶、喷水、与玻璃纤维、pe膜、基布和底布进行组合、热压成型、冷却定型和水刀切割,得到基材;
25.(2)在步骤(1)得到的基材表面喷洒催化剂,将滚胶后的麂皮面料在上模温度为55~65℃、下模温度为145~155℃的模具中,按照成型压力为8~12mpa,保压时间为100~140s进行贴合成型,冷切定型,得到所述汽车麂皮面料顶蓬。
26.第二方面,本发明提供一种汽车麂皮面料顶蓬,所述汽车麂皮面料顶蓬采用如第一方面所述的制备方法发制备得到。
27.第三方面,本发明提供一种如第二方面所述的汽车麂皮面料顶蓬在汽车中的应用。
28.相对于现有技术,本发明具有以下有益效果:
29.本发明的目的在于提供一种汽车麂皮面料顶蓬的制备方法,所述制备方法包括:将麂皮面料进行滚胶、与基材贴合成型,冷切定型,得到所述汽车麂皮面料顶蓬;所述贴合成型在上模温度为55~65℃以及下模温度为145~155℃的模具中进行;所述制备方法通过控制上模温度为55~65℃,下模温度为145~155℃,避免了因上模温度太高容易造成麂皮面料绒毛烫形成色差的问题;同时控制下模温度为145~155℃,避免了因上下模温差大模具容易使得模具生锈的问题;所述制备方法整体操作简单,可以有效改善汽车麂皮面料顶蓬的外观;具体而言,采用本发明提供的制备方法得到的汽车麂皮面料顶蓬的剥离均可达到9~10n,完全满足要求,且表面无色差、无锈渍、无白色印痕,进而减少了产品的报废率,具有重要的研究意义。
具体实施方式
30.下面通过具体实施方式来进一步说明本发明的技术方案。本领域技术人员应该明了,所述实施例仅仅是帮助理解本发明,不应视为对本发明的具体限制。
31.实施例1
32.一种汽车麂皮面料顶蓬的制备方法,具体包括如下步骤:
33.(1)将pu泡棉进行滚胶,使其上含胶量为25g/0.4m2、下含胶量为30g/0.4m2,喷水,使其含水量为110g/0.4m2、与玻璃纤维、pe膜、基布和底布进行组合、在130℃下热压成型、冷却定型、水刀切割,得到基材;
34.(2)在步骤(1)得到的基材表面喷洒催化剂(固氨(kc100l)、上海凯众),与其含胶量为5g/0.4m2的麂皮面料在上模温度为60℃、下模温度为150℃的模具中,成型压力为
10mpa,保压时间为120s下进行贴合成型,冷切定型,得到所述汽车麂皮面料顶蓬。
35.实施例2
36.一种汽车麂皮面料顶蓬的制备方法,具体包括如下步骤:
37.(1)将pu泡棉进行滚胶,使其上含胶量为20g/0.4m2、下含胶量为20g/0.4m2,喷水,使其含水量为90g/0.4m2、与玻璃纤维、pe膜、基布和底布进行组合、130℃下热压成型、冷却定型、水刀切割,得到基材;
38.(2)在步骤(1)得到的基材表面喷洒催化剂(固氨(kc100l)、上海凯众,与含胶量5g/0.4m2的为麂皮面料在上模温度为55℃、下模温度为145℃的模具中,成型压力为10mpa,保压时间为140s下进行贴合成型,冷切定型,得到所述汽车麂皮面料顶蓬。
39.实施例3
40.一种汽车麂皮面料顶蓬的制备方法,具体包括如下步骤:
41.(1)将pu泡棉进行滚胶,使其上含胶量为30g/0.4m2、下含胶量为40g/0.4m2,喷水,使其含水量为130g/0.4m2、与玻璃纤维、pe膜、基布和底布进行组合、130℃下热压成型、冷却定型、水刀切割,得到基材;
42.(2)在步骤(1)得到的基材表面喷洒催化剂(固氨(kc100l)、上海凯众),与含胶量为100g/0.4m2的麂皮面料在上模温度为65℃、下模温度为155℃的模具中,成型压力为12mpa,保压时间为100s下进行贴合成型,冷切定型,得到所述汽车麂皮面料顶蓬。
43.实施例4
44.一种汽车麂皮面料顶蓬的制备方法,其与实施例1的区别仅在于,上模温度为65℃,其他条件和步骤均与实施例1相同。
45.实施例5
46.一种汽车麂皮面料顶蓬的制备方法,其与实施例1的区别仅在于,上模温度为55℃,其他条件和步骤均与实施例1相同。
47.实施例6
48.一种汽车麂皮面料顶蓬的制备方法,其与实施例1的区别仅在于,下模温度为145℃,其他条件和步骤均与实施例1相同。
49.实施例7
50.一种汽车麂皮面料顶蓬的制备方法,其与实施例1的区别仅在于,下模温度为155℃,其他条件和步骤均与实施例1相同。
51.实施例8
52.一种汽车麂皮面料顶蓬的制备方法,其与实施例1的区别仅在于,上模温度65℃,下模温度150℃,其他条件和步骤均与实施例1相同。
53.对比例1
54.一种汽车麂皮面料顶蓬的制备方法,其与实施例1的区别仅在于,上模温度为30℃,其他条件和步骤均与实施例1相同。
55.对比例2
56.一种汽车麂皮面料顶蓬的制备方法,其与实施例1的区别仅在于,上模温度为80℃,其他条件和步骤均与实施例1相同。
57.对比例3
58.一种汽车麂皮面料顶蓬的制备方法,其与实施例1的区别仅在于,下模温度为130℃,其他条件和步骤均与实施例1相同。
59.对比例4
60.一种汽车麂皮面料顶蓬的制备方法,其与实施例1的区别仅在于,下模温度为180℃,其他条件和步骤均与实施例1相同。
61.对比例5
62.一种汽车麂皮面料顶蓬的制备方法,其与实施例1的区别仅在于,上下模温度均为150℃,其他条件和步骤均与实施例1相同。
63.性能测试:
64.(1)剥离力:采用拉力计进行测试;(2)色差:灯光下目测;
65.(3)表面洁净度:目测。
66.按照上述测试方法对实施例1~8和对比例1~5得到的汽车麂皮面料顶蓬进行测试,测试结果如表1所示:
67.表1
68.[0069][0070]
根据表1数据可以看出:采用实施例1~8提供的制备方法得到的汽车麂皮面料顶蓬的剥离均可达到9~10n,完全满足要求,且表面均无色差、无锈渍。
[0071]
比较实施例1和对比例1~2可以发现,上模温度过低,会造成上下模温差变大,进而得到的汽车麂皮面料顶蓬表面出现锈渍(对比例1);上模温度过高,容易造成汽车麂皮面料顶蓬烫伤,进而形成色差(对比例2)。
[0072]
比较实施例1和对比例3~4可以发现,下模温度过低,则会造成汽车麂皮面料顶蓬的剥离较低,无法满足要求(对比例3);而下模温度过高,同样会造成上下模温差较大,使得汽车麂皮面料顶蓬表面出现锈渍(对比例4)。
[0073]
比较实施例1和对比例5可以发现,上下模温度同为150℃,会直接烫伤汽车麂皮面料顶蓬。
[0074]
申请人声明,本发明通过上述实施例来说明一种汽车麂皮面料顶蓬及其制备方法和应用,但本发明并不局限于上述实施例,即不意味着本发明必须依赖上述实施例才能实施。所属技术领域的技术人员应该明了,对本发明的任何改进,对本发明产品各原料的等效替换及辅助成分的添加、具体方式的选择等,均落在本发明的保护范围和公开范围之内。
再多了解一些
本文用于企业家、创业者技术爱好者查询,结果仅供参考。