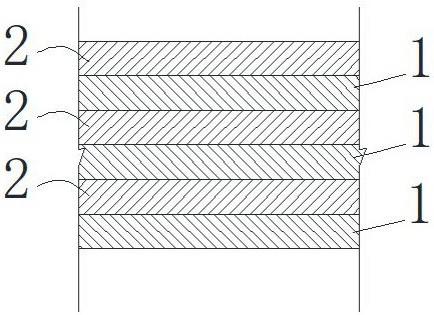
1.本发明涉及屏蔽材料技术领域,具体涉及一种高能射线屏蔽材料。
背景技术:
2.高能射线是指γ射线以及x射线为主的穿透性很强的放射性射线,这种射线具有很强的穿透性且会危害人体健康,故需要开发针对性的屏蔽材料。利用辐射屏蔽材料对高能射线源周围的人体和精密电子设备进行屏蔽防护是放射性射线应用过程中不可或缺的一部分。目前广泛使用的射线屏蔽材料铅的存在密度偏高(11.35 g/cm3)、强度偏低、耐碱腐蚀性差、回收成本很高等问题,而且铅还会危害环境和人体健康。
3.综合性能优良、环保无毒的金属钨及其合金对高能射线(如x射线、γ射线等)具有优异的衰减和吸收能力,在工业探伤、食品辐照、医疗诊治、和工业屏蔽领域都有潜在的利用环境。但钨的密度较高(19.35 g/cm3)、材料成本较高的问题,限制了其在射线屏蔽领域的应用。随着对辐射屏蔽材料要求的提高,单一的屏蔽材料难以满足防护要求,低密度、无铅、耐腐蚀、高结构强度的屏蔽复合材料才能更好的满足射线辐射屏蔽的要求。
4.cn202592851u曾公开了一种无铅环保高能射线屏蔽复合板,其结构包括屏蔽材料层和结构铝层;所述结构铝层一侧表面上固定有所述屏蔽材料层。该实用新型可以加工成各种零部件,用于检测,化工、安保,医疗、核工业等领域。其具有一定的高能射线屏蔽能力强,但是屏蔽效果有限。
5.cn110643859a公开了一种含钆钨元素的铝基复合材料及其应用,获得的复合材料具有一定射线屏蔽效果,但方案属于材料配比的改进,加工较为不便。同时其射线屏蔽效果仍然有限。
6.故如何提供一种从材料结构出发进行改进,使其更好地提高射线屏蔽能力,方便加工实现,成为本领域人员有待考虑解决的问题。
技术实现要素:
7.针对上述现有技术的不足,本发明所要解决的技术问题是:怎样提供一种通过结构改进来提高射线屏蔽效果,射线屏蔽效果优异的高能射线屏蔽材料,并使其易于制备。
8.了解决上述技术问题,本发明采用了如下的技术方案:一种高能射线屏蔽材料,包括呈层状结构设置的铝层和钨层,其特征在于,铝层和钨层为多层且交替叠放并结合固定为一体。
9.本发明方案中将多层连续屏蔽组元钨层与铝层结合,形成铝层和钨层交错叠放的结构再固定为一体,这样在材料中引入了包含多个铝/钨界面的层状结构,射线进入界面位置时,会产生部分透射、部分折射以及部分反射现象,故部分射线会在相邻两个界面之间来回反射并被材料吸收衰减,这样就利用了多个界面对射线的反射和吸收衰减作用,极大地提高了材料的射线屏蔽性能。
10.进一步地,所述结合固定为冶金结合。这样可以更好地提高结合固定的可靠性,且
更有利于反射界面的形成。
11.进一步地,铝层为铝箔材料,钨层为钨箔材料且交错叠合后采用冶金结合固定为一体。这样更加方便制备以及控制各层的厚度大小。
12.作为一种优化,铝层厚度为150
‑
200 μm,钨层厚度为35
‑
50 μm。
13.因为通常高能射线屏蔽材料的厚度可达2
‑
5厘米,所以铝层和钨层厚度最高可达到毫米级别甚至极限可达到一个厘米左右厚度。上述厚度要求作为优化是取最薄的情况,这样可以尽量增加叠合层数,可达到上百层数量的铝层和钨层,以增加界面数量来提高射线在界面之间的反射吸收效果。如果再薄则不利于制造。实施时,钨的质量分数可以优选为60
‑
65 %,使其具有更好的屏蔽效果。
14.作为优化,上述材料可以采用以下方法制备:先将多层厚度为35
‑
40 μm的钨箔和厚度为150
‑
200 μm 铝箔进行交替顺序叠放,形成钨 铝的多层结构;然后采用放电等离子体烧结工艺使钨箔和铝箔之间达到冶金结合形成层状复合材料。
15.这样,可以方便快捷地完成所述屏蔽材料的制备。
16.具体地说上述方法包括以下步骤:a、将钨箔和铝箔放入超声波清洗机中采用无水乙醇清洗10 min,去除表明油污和杂质,并干燥备用;b、将清洗后的多层钨箔和铝箔顺序交替叠放后放入石墨模具中;c、将石墨模具放入等离子体烧结设备中,在30
‑
40 mpa的轴向压力下,以50
‑
100℃/min的升温速率加热到600
‑
615 ℃并保温8
‑
10 min,保证铝与钨层间形成良好的冶金结合;d、保温完成后,在保持轴向压力不变的情况下,试样随炉冷却至室温得到层状铝/钨复合材料。
17.这样,采用等离子体烧结设备,辅助以适宜的轴向压力和温度,可以更加快速,稳定地完成钨箔和铝箔之间的快速结合固定,使得材料产品的制备方便快捷稳定可靠,提高了生产效率。
18.进一步地,至少具有部分铝层和钨层之间的结合界面为相互平行对应的锯齿形。
19.这样射线进入锯齿形的结合界面时,改变了射线和结合界面的入射方向,更加有利于射线在界面之间以多种角度形成折射反射,并吸收耗散,更好地提高了对射线的屏蔽效果。
20.进一步地,材料中形成有多个锯齿形界面,且各个锯齿形界面具有不同的锯齿倾斜角度。
21.这样,无论从任何角度射入到材料上的射线,都更容易找到对应该入射角度进入后能够更好地形成吸收耗散的锯齿形界面,故能够更好地提高材料的整体射线屏蔽效果。
22.进一步地,至少在部分锯齿形结合的铝层和钨层之间还结合固定设置有一层粉末材料层,所述粉末材料层为铝粉和钨粉均匀混合制得,粉末材料层与铝层和钨层之间为冶金结合固定。
23.这样,在铝层和钨层之间增加了一层混合粉末材料的中间层,不仅仅增加了材质不同的一层两侧表面为锯齿形的屏蔽材料,更好地提高对射线的屏蔽效果。而且粉末材料冶金结合固定后,内部容易残留间隙空间,这样极大地提高了射线在材料内部行进路径的复杂情况,极大地提高了对射线的耗散屏蔽效果。
24.进一步地,所述粉末材料层在周边设置有一圈小粒径的粉末材料。
25.这样,在粉末材料中,周边一圈材料的粉末粒径小于内部材料的粉末粒径,使得在冶金结合固定时,周边的粉末材料能够更好地熔融压平并实现层与层之间的结合固定,避免内部粉末漏出,同时使得内部的粉末材料大部分仍然保持为颗粒状。这样可以最大程度地在粉末材料层内部形成颗粒之间的残留间隙空间,最大程度地提高了对射线的耗散屏蔽效果。
26.上述材料可以采用以下方法步骤制备:a、制得多层钨箔和铝箔,部分钨箔和铝箔整体呈锯齿形,且具有多种不同斜度大小的锯齿,再制备粗细不同的两种钨粉和铝粉颗粒材料(粗细大小以细颗粒的粉料能够在烧结设备中烧结固化为准,粗颗粒的粉料大于细颗粒粉料使其在烧结设备中不能完全烧结熔融为准),分别进行混合均匀(质量比例可以不限,但以质量分数一比一左右比例混合为较优选择)形成两种不同颗粒大小的粉末材料;b、将钨箔和铝箔放入超声波清洗机中采用无水乙醇清洗10 min,去除表明油污和杂质,并干燥备用;c、将清洗后的多层钨箔和铝箔顺序交替叠放,部分锯齿形界面之间铺设好一层粉末材料,铺设时先在周边铺设一圈细颗粒混合材料,然后在中部铺设粗颗粒混合材料;然后整体放入石墨模具中;d、将石墨模具放入等离子体烧结设备中,在30
‑
40 mpa的轴向压力下,以50
‑
100℃/min的升温速率加热到600
‑
615 ℃并保温8
‑
10 min,保证铝层与钨层之间以及和细颗粒粉末材料之间形成良好的冶金结合;f、保温完成后,在保持轴向压力不变的情况下,试样随炉冷却至室温得到层状铝/钨复合材料产品。
27.这样,可以方便快捷地完成多层钨箔和铝箔之间以及混合粉末材料层之间的结合固定,形成的材料产品中,具有不同斜度的多个锯齿形结合界面,而且存在内部仍然保留大量间隙的粉末状屏蔽材料层,故可以最大程度地实现对高能射线的屏蔽效果。
28.综上所述,本发明具有射线屏蔽效果优异且易于制备生产的优点。
附图说明
29.图1为具体实施方式1的层状结构示意图。
30.图2为具体实施方式2的层状结构示意图。
具体实施方式
31.下面结合具体实施方式对本发明作进一步的详细说明。
32.具体实施方式一:一种高能射线屏蔽材料,包括呈层状结构设置的铝层和钨层,其中,铝层和钨层为多层且交替叠放并结合固定为一体。
33.本发明方案中将多层连续屏蔽组元钨层与铝层结合,形成铝层和钨层交错叠放的结构再固定为一体,这样在材料中引入了包含多个铝/钨界面的层状结构,射线进入界面位置时,会产生部分透射、部分折射以及部分反射现象,故部分射线会在相邻两个界面之间来回反射并被材料吸收衰减,这样就利用了多个界面对射线的反射和吸收衰减作用,极大地
提高了材料的射线屏蔽性能。
34.其中,所述结合固定为冶金结合。这样可以更好地提高结合固定的可靠性,且更有利于反射界面的形成。
35.其中,铝层为铝箔材料,钨层为钨箔材料且交错叠合后采用冶金结合固定为一体。这样更加方便制备以及控制各层的厚度大小。
36.其中,铝层厚度为150
‑
200 μm,钨层厚度为35
‑
50 μm。
37.因为通常高能射线屏蔽材料的厚度可达2
‑
5厘米,所以铝层和钨层厚度最高可达到毫米级别甚至极限可达到一个厘米左右厚度。上述厚度要求作为优化是取最薄的情况,这样可以尽量增加叠合层数,可达到上百层数量的铝层和钨层,以增加界面数量来提高射线在界面之间的反射吸收效果。如果再薄则不利于制造。实施时,钨的质量分数可以优选为60
‑
65 %,使其具有更好的屏蔽效果。
38.本实施例中的材料采用以下方法制备:先将多层厚度为35
‑
40 μm的钨箔和厚度为150
‑
200 μm 铝箔进行交替顺序叠放,形成钨 铝的多层结构;然后采用放电等离子体烧结工艺使钨箔和铝箔之间达到冶金结合形成层状复合材料。
39.这样,可以方便快捷地完成所述屏蔽材料的制备。
40.具体地说上述方法包括以下步骤:a、将钨箔和铝箔放入超声波清洗机中采用无水乙醇清洗10 min,去除表明油污和杂质,并干燥备用;b、将清洗后的多层钨箔和铝箔顺序交替叠放后放入石墨模具中;c、将石墨模具放入等离子体烧结设备中,在30
‑
40 mpa的轴向压力下,以50
‑
100℃/min的升温速率加热到600
‑
615 ℃并保温8
‑
10 min,保证铝与钨层间形成良好的冶金结合;d、保温完成后,在保持轴向压力不变的情况下,试样随炉冷却至室温得到层状铝/钨复合材料。
41.这样,采用等离子体烧结设备,辅助以适宜的轴向压力和温度,可以更加快速,稳定地完成钨箔和铝箔之间的快速结合固定,使得材料产品的制备方便快捷稳定可靠,提高了生产效率。
42.本实施方式一中获得产品的层状结构参见图1示意,图中,标号1表示铝层,标号2表示钨层,若干铝层和钨层交替设置构成材料产品。
43.具体实施方式二一种高能射线屏蔽材料,包括呈层状结构设置的铝层和钨层,其中,铝层和钨层为多层且交替叠放并结合固定为一体。
44.其中所述结合固定为冶金结合。这样可以更好地提高结合固定的可靠性,且更有利于反射界面的形成。
45.其中,铝层为铝箔材料,钨层为钨箔材料且交错叠合后采用冶金结合固定为一体。这样更加方便制备以及控制各层的厚度大小。
46.其中,至少具有部分铝层和钨层之间的结合界面为相互平行对应的锯齿形。
47.这样射线进入锯齿形的结合界面时,改变了射线和结合界面的入射方向,更加有利于射线在界面之间以多种角度形成折射反射,并吸收耗散,更好地提高了对射线的屏蔽效果。
48.其中,材料中形成有多个锯齿形界面,且各个锯齿形界面具有不同的锯齿倾斜角度。
49.这样,无论从任何角度射入到材料上的射线,都更容易找到对应该入射角度进入后能够更好地形成吸收耗散的锯齿形界面,故能够更好地提高材料的整体射线屏蔽效果。
50.其中,至少在部分锯齿形结合的铝层和钨层之间还结合固定设置有一层粉末材料层,所述粉末材料层为铝粉和钨粉均匀混合制得,粉末材料层与铝层和钨层之间为冶金结合固定。
51.这样,在铝层和钨层之间增加了一层混合粉末材料的中间层,不仅仅增加了材质不同的一层两侧表面为锯齿形的屏蔽材料,更好地提高对射线的屏蔽效果。而且粉末材料冶金结合固定后,内部容易残留间隙空间,这样极大地提高了射线在材料内部行进路径的复杂情况,极大地提高了对射线的耗散屏蔽效果。
52.其中,所述粉末材料层在周边设置有一圈小粒径的粉末材料。
53.这样,在粉末材料中,周边一圈材料的粉末粒径小于内部材料的粉末粒径,使得在冶金结合固定时,周边的粉末材料能够更好地熔融压平并实现层与层之间的结合固定,避免内部粉末漏出,同时使得内部的粉末材料大部分仍然保持为颗粒状。这样可以最大程度地在粉末材料层内部形成颗粒之间的残留间隙空间,最大程度地提高了对射线的耗散屏蔽效果。
54.上述材料采用以下方法步骤制备:a、制得多层钨箔和铝箔,部分钨箔和铝箔整体呈锯齿形,且具有多种不同斜度大小的锯齿,再制备粗细不同的两种钨粉和铝粉颗粒材料(粗细大小以细颗粒的粉料能够在烧结设备中烧结固化为准,粗颗粒的粉料大于细颗粒粉料使其在烧结设备中不能完全烧结熔融为准),分别进行混合均匀(质量比例可以不限,但以质量分数一比一左右比例混合为较优选择)形成两种不同颗粒大小的粉末材料;b、将钨箔和铝箔放入超声波清洗机中采用无水乙醇清洗10 min,去除表明油污和杂质,并干燥备用;c、将清洗后的多层钨箔和铝箔顺序交替叠放,部分锯齿形界面之间铺设好一层粉末材料,铺设时先在周边铺设一圈细颗粒混合材料,然后在中部铺设粗颗粒混合材料;然后整体放入石墨模具中;d、将石墨模具放入等离子体烧结设备中,在30
‑
40 mpa的轴向压力下,以50
‑
100℃/min的升温速率加热到600
‑
615 ℃并保温8
‑
10 min,保证铝层与钨层之间以及和细颗粒粉末材料之间形成良好的冶金结合;f、保温完成后,在保持轴向压力不变的情况下,试样随炉冷却至室温得到层状铝/钨复合材料产品。
55.这样,可以方便快捷地完成多层钨箔和铝箔之间以及混合粉末材料层之间的结合固定,形成的材料产品中,具有不同斜度的多个锯齿形结合界面,而且存在内部仍然保留大量间隙的粉末状屏蔽材料层,故可以最大程度地实现对高能射线的屏蔽效果。
56.本实施方式中,钨箔和铝箔的厚度可以比实施方式一中的厚度略大,以方便制备锯齿形的钨箔和铝箔为准。同时,生产时,锯齿形的钨箔、铝箔和平板形的钨箔、铝箔之间可以铺设粉末材料实现过渡,提高材料整体性。
57.本实施方式二中获得产品的层状结构参见图2示意,图中,标号1表示平板状的铝
层,标号2表示锯齿形状的钨层,标号3表示锯齿形状的铝层,标号4表示两个锯齿形结合界面之间的粉末材料层,标号5表示一个锯齿形结合界面和一个水平界面之间的粉末材料层。
58.为进一步验证本发明效果,申请人分别采用上述实施方式一获得的材料和实施方式二获得的材料进行了γ射线屏蔽性能测试,测试材料厚度为3cm,同时采用了相同厚度的纯铅材料进行了对比测试。
59.本测试例利用德国pt钨电离室对实施例制备后的复合材料进行γ射线屏蔽性能测试,分别测试射线穿过屏蔽材料前后的入射强度i0和透射强度i后,再拟合计算出材料的射线线吸收系数μ。屏蔽测试中所用的射线源为
137
cs,射线源的初始剂量率为13.44 μgy/s,测试温度为23.1 ℃,湿度为rh 53%,测试总时间为60s。比测试的结果如下表所示。
60.厚度为3mm的层状复合屏蔽材料和纯铅材料的γ射线屏蔽性能表
材料密度(g/cm3)衰减率(%)线吸收系数μ(cm
‑1)质量吸收系数μ
m
(cm2/g)铅11.340.281.09610.0967实施方式15.890.240.91210.1549实施方式25.870.270.98790.1683
从表1中可以看出,实施方式1中获得材料对初始剂量率为13.44 μgy/s的
137
cs γ射线的衰减率和线吸收系数均已比较接近对比例纯铅的数据,实施方式2中获得材料的衰减率和线吸收系数高于实施方式1的数据,与对比例纯铅的屏蔽性能相当;而且比较相同质量下材料的屏蔽效果,更是远远超出了纯铅的质量吸收系数。故可以证明本发明的材料射线屏蔽效果优异。
再多了解一些
本文用于企业家、创业者技术爱好者查询,结果仅供参考。