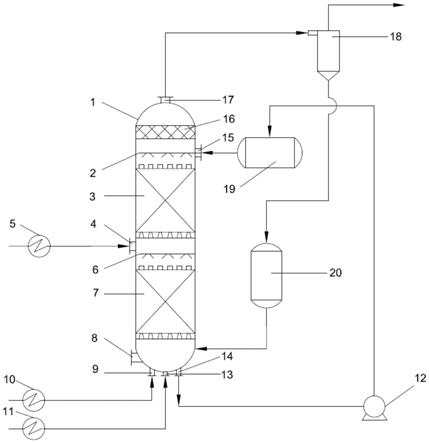
1.本发明涉及有机硅单体生产技术,尤其是涉及一氯甲烷的合成方法及其装置。
背景技术:
2.一氯甲烷是有机硅单体合成的主要原料,我国目前主要采用液相催化法,将hcl和甲醇,以氯化锌水溶液为催化剂,在气液鼓泡反应器中进行合成。气液鼓泡反应器一般是在搪瓷釜底部装配气体分布器。但受到搪瓷设备加工窑炉尺寸的制约,搪瓷釜直径受限,从而制约了鼓泡反应器的最大生产能力。另外,液相催化法中,hcl转化率偏低,产生大量稀酸使其处理困难。而醇酸比的变化会影响原料转化率和杂质含量。一般而言,醇过量,可以提高hcl的转化率,但是副产物二甲醚会随之增加;醇略过量时,hcl转化率大约在94%左右;hcl过量可减少副产物产生但极大抑制hcl转化率,产生更多的废酸,甚至需要在后系统中用碱液洗涤合成气中未反应的hcl。此外,根据nigar kantarci,fahir borak,kutlu o.ulgen发表的《bubble column reactors》中对鼓泡塔气速对流态以及传质传热影响的描述,为了达到理想传质效果且避免气体夹带催化剂造成催化剂损失,鼓泡反应器一般气速都不超过20cm/s,这进一步制约了采用鼓泡反应器生产一氯甲烷的效率。
3.现有技术中,为了改进采用鼓泡式反应器生产一氯甲烷的上述缺陷,采用了以下不同的技术手段:
4.通过改进气体分布器的结构或设置,改进气体分布,例如cn2903055y和cn205127937u。在鼓泡式反应器中,通过将氯化氢分散在液相甲醇,再与催化剂充分接触进行反应,其生产效率很大程度上决定于氯化氢气体的分散程度。但这些技术方法仍然受限于鼓泡反应器的最大可操作气速上限(20cm/s),无法提高生产能力。
5.通过改进后续程序设置,增加盐酸脱吸回收系统,例如cn205258343u和cn205257999u,来处理大量未反应的氯化氢,但仍然不能很好的解决副产较多二甲醚的问题。
6.传统的鼓泡反应器一般气速都不超过20cm/s,再加上连续性操作后,反应速率下降,因而很难在单一反应器中达到较大反应物转化率,为此cn105985217b采用多级鼓泡反应器串联,反应条件为50-300℃,压力0.05mpa-0.5mpa,以提高反应物的转化率。尽管,多级反应器串联一定程度上能够缓解副产酸含量高的问题,但设备占地面积大,投资高。
技术实现要素:
7.本发明提供一种一氯甲烷合成方法,其包括:在催化或无催化体系下,在填料反应塔内进行hcl和甲醇的气液相反应。
8.根据本发明,所述hcl和甲醇从填料塔底以气体形式进料,生成的一氯甲烷从塔顶排出。
9.根据本发明,塔底液体从填料塔底排出后,再从塔顶进入填料塔循环使用。
10.根据本发明,在使用催化剂的反应体系中,催化剂水溶液从塔顶进料。
11.本发明采用填料塔,因此本发明方法适用于低空塔气速或高空塔气速,根据本发明的方法,所述反应时填料塔内可操作空塔气速范围为1cm/s≤空塔气速≤180cm/s,例如可以为10cm/s≤空塔气速≤180cm/s。本领域技术人员能判断并选择合适的塔内空塔气速,避免过低或过高导致其经济性或可控制性不合适。当然,由于采用填料塔,可以将空塔气速提高超过常规鼓泡塔的气速,从而极大提高反应效率,即可选用20cm/s≤空塔气速≤150cm/s,例如,25cm/s≤空塔气速≤100cm/s。
12.根据本发明,所述反应的反应压力为0.1-0.5mpag,本领域技术人员可以根据实际需要确定是否使用催化剂,和/或进行反应压力的调节。一般而言,有催化剂存在时,反应压力可以适当降低;无催化剂时,反应压力可以适当提高。
13.根据本发明,所述反应的温度为120-170℃,例如130~140℃,150~160℃等。
14.根据本发明,所述气液相法一氯甲烷合成催化剂可以是zncl2或fecl3或cacl2,或其任意两种或三种的混合物,所述催化剂优选为水溶液形式,例如50%的zncl2水溶液或50%的fecl3水溶液或更高浓度的水溶液,例如75%的zncl2水溶液。
15.根据本发明,从填料塔底进料的hcl和甲醇的摩尔比为0.8:1到1.5:1。
16.根据本发明,所述填料塔可以为一段式或多段式填料塔。所述一段式或多段式填料塔是指填料塔内独立的填料段的段数是一段或多段,各填料段沿着气体物料流动的方向排布。选择一段式或多段式填料塔的依据为原料的转化率,特别是hcl的转化率。优选为两段或两段以上的多段式填料塔。特别优选为两段式填料塔结构。
17.根据本发明,当填料塔为多段式填料塔时,在每两个相邻填料段之间补充甲醇和/或hcl进料,以使前一个填料段中未反应完的原料与补充进料,在后一填料段中进行反应。在本发明中,“前一个填料段”、“前填料段”和“后一个填料段”、“后填料段”是按照气体物料流经顺序的先后描述,先流经的填料段为“前”,后流经的填料段为“后”。
18.补充进料的种类和量,根据塔底进料的hcl和甲醇的摩尔比进行调整,以使总体反应中甲醇略过量为优,例如,使总体反应中hcl与甲醇的摩尔比为1:(1-1.3)。
19.例如,当填料塔为两段式,从塔底进料的hcl和甲醇的摩尔比为1:(0.7-1)时,则在两个填料段之间补充适量的甲醇,以使在第一填料段未反应完的hcl,在第二填料段中,与补充的甲醇进行反应,所补充的甲醇摩尔量可以是塔底进料hcl摩尔量的0.05-0.8。这样设置,第一填料段中hcl过量,有利于抑制副产物二甲醚的生成,第二填料段醇过量,增加hcl的转化率。最终大部分反应在第一填料段完成,少部分反应在第二填料段完成,既提高了hcl的转化率,又抑制了副产物二甲醚的量。
20.优选,本发明提供一种一氯甲烷合成方法,其包括:在催化或无催化体系下,在填料反应塔内进行hcl和甲醇的气液相反应,所述填料塔为两段式填料塔,特别优选为上下分布的两个填料段。当选择上下分布的两个填料段时,从塔底气体进料经过的填料段顺序,下段填料段就是第一填料段,上段填料段就是第二填料段。
21.根据上述方法,其中在两个填料段之间,例如,上段填料段和下段填料段之间,补充甲醇和/或hcl进料。
22.在本发明的一个实施方式中,上段填料段和下段填料段之间补充甲醇进料,其补充量根据下段填料段hcl与甲醇进料的摩尔比调节,确保总体反应中甲醇:hcl的摩尔比为(1-1.2):1。例如,下段填料段进料中hcl与甲醇的摩尔比为1:(0.7-1),则在上段填料段和
下段填料段之间补充的甲醇的进料摩尔量,相当于塔底hcl的进料摩尔量的0.05-0.5之间。
23.根据本发明,为提高液体进料的均匀性,在液体物料进入填料区之前进行分散处理,例如可以在液体物料进入填料区前的位置加装液体分布器。在本发明的一个实施方式中,在塔顶进料口和填料区之间安装液体分布器。在本发明的另一个实施方式中,在每两个相邻填料区之间安装液体分布器。在本发明的另一个实施方式中,在第一填料区和第二填料区之间安装液体分布器。
24.根据本发明,生成的一氯甲烷从塔顶排出后,进行气液分离,分离出来的液体再返回塔釜底部循环使用。
25.根据本发明,生成的一氯甲烷在从塔顶排出前,进行除沫处理,以减少一氯甲烷气体夹带的液体。
26.本发明提供一种一氯甲烷合成装置,其是填料塔,填料塔底部分别设有氯化氢气体进料口和甲醇蒸汽进料口,塔顶设有一氯甲烷出料口。
27.根据本发明,优选塔顶还设有回流液进料口。
28.根据本发明,所述填料塔为一段式或多段式填料塔。优选为两段填料塔型式,进一步优选所述两段填料为上下分布的两段填料。
29.根据本发明,多段式填料塔,在每相邻的填料段之间的塔身位置,设置甲醇蒸汽侧线进料口和/或氯化氢气体侧线进料口,甲醇蒸汽或氯化氢气体由此从塔身中段进入塔内参与反应。在本发明的一个实施方式中,对上下分布的两段式填料塔,在上段填料和下段填料之间的塔身位置,设置甲醇蒸汽侧线进料口和/或氯化氢气体侧线进料口。
30.根据本发明,所述填料塔内顶部位于进料口下方设置液体分布器,以将塔顶所进液体物料均匀分布淋入上段填料。
31.根据本发明,多段式填料塔,在每相邻的填料段之间设置液体分布器。在本发明的一个实施方式中,对上下分布的两段式填料塔,在上段填料和下段填料之间,安装有液体分布器(又可称为“再分布器”)。从塔顶进入的液体物料经上段填料后,在进入下段填料前,经过再分布器,使液体物料均匀分布淋入下段填料。
32.根据本发明,塔底的氯化氢进料管线上设有换热器,甲醇蒸汽进料管线上设有甲醇蒸发器,所述换热器和甲醇蒸发器用于控制进料状态。
33.根据本发明,填料塔材质可为本领域常用的填料塔材质,例如,可以为搪玻璃或者内衬碳砖等具有防腐结构的填料塔。填料可以是本领域常用的填料材质及其形状,例如,可以是塑料鲍尔环、花环等乱堆填料,陶瓷的鲍尔环,矩鞍环,十字环乱堆填料,陶瓷规整填料等。
34.根据本发明,塔底原料为气体形态进料,汽化方式可以使用现有技术中常用的方式进行,如蒸发器,换热器等。优选在氯化氢进料管线上设有换热器,甲醇蒸汽进料管线上设有的甲醇蒸发器,通过控制上述换热器和甲醇蒸发器用于控制进料状态。甲醇侧线进料和氯化氢侧线进料也采用气体状态进料,使用例如甲醇蒸发器、氯化氢换热器等进行气化,并控制进料状态。
35.根据本发明,在填料塔底还设置有含酸液出料口。
36.根据本发明,所述装置进一步包括回流泵和回流罐,所述回流泵连接含酸液出料口和回流罐,回流罐与塔顶进料口连接,使含酸液经出料口出料后,由回流泵泵入回流罐,
再经过回流罐由塔顶进料口进入填料塔内,实现含酸液的循环利用。
37.根据本发明,反应生成的一氯甲烷从塔顶的一氯甲烷出料口产出。
38.根据本发明,一氯甲烷出料口后连接气液分离装置,一氯甲烷出料进入该气液分离装置,分离出液体,气体产物出料,进入下一工段。所述气液分离装置可采用本领域已知和常规的装置,包括但不限于丝网除沫器、旋风分离器、折流分离装置、重力分流装置等。
39.进一步,为防止液沫夹带问题,非必需的,在塔顶一氯甲烷出料口前设置除沫装置,如除沫器。
40.根据本发明,优选在气液分离装置后连接收集罐,将分离出的液体收集至罐中,再返回塔顶或塔釜底部循环使用。
41.根据本发明,在塔底部可进一步设置排空口。
42.本发明的合成方法能够实现如下有益效果:
43.1、填料塔与传统的鼓泡反应器中的管式气相分布器相比,可以使气液接触更充分,气液传质效率更高。以上下分布的两段式填料塔为例,将填料设计为两段,相当于做成两级反应器,下段填料反应区中控制hcl过量,使大部分反应在下段完成。未反应的hcl和气体,进入上段填料,在两段填料之间,补加气相甲醇,使上段填料区中醇过量,来提高hcl转化率。由于大部分反应在下段hcl过量的情况下完成,也就有效控制了副产物二甲醚的生成。总体实现了提高盐酸转化率、减少副产物产生量的效果,降低了后续处理成本。
44.2、本发明反应器采用填料塔,可操作气速高,同时在塔内形成两段反应区,等效为两级反应器串联,总体实现了减小设备占地面积,简化设备结构,却提高生产能力的效果。
45.3、盐酸在塔中循环回流,可以降低整体盐酸使用量,节省原料,减轻后续稀酸处理压力及环境污染。
46.4、在出料口之前增加除沫器,解决了填料塔高气速运行下的液沫夹带问题,减少了催化剂损失。
47.5、在进一步增加气液分离装置后,减少液体夹带,从而使一氯甲烷产出物中含水量降低,节约后续干燥过程中浓硫酸用量。
48.本发明中,“mpag”表示“表压”,相应的压力值均为表压压力。
附图说明
49.图1:本发明实施例所使用的一氯甲烷合成装置示意图。图中:1-反应塔塔体、2-液体分布器、3-上段填料、4-甲醇蒸汽侧线进料口、5-甲醇蒸发器、6-再分布器、7-下段填料、8-排空口、9-氯化氢进料口、10-换热器、11-甲醇蒸发器、12-回流泵、13-甲醇蒸汽进料口、14-含酸液出料口、15-回流进料口、16-除沫器、17-塔顶出料口、18-旋风分离器、19-回流罐、20-收集罐。
具体实施方式
50.以下结合实施例对本发明做进一步描述。需要说明的是,实施例不能作为对本发明保护范围的限制,本领域的技术人员理解,任何在本发明基础上所作的改进和变化都在本发明的保护范围之内。
51.以下实施例所用的常规化学试剂,均可商购获得或者采用常规方法制备。
52.以下实施例中使用了如图1所示的一氯甲烷合成反应塔及其流程,采用上下分布的两段填料塔型式。包括反应塔塔体1,和上下两段填料3和7,塔底下部分别设有氯化氢进料口9和新鲜甲醇蒸汽进料口13,两股进料分别设有换热器10和甲醇蒸发器11用于控制进料状态。在塔底还设置有含酸液出料口14,塔底出液经由回流泵12进入回流罐19,之后由塔顶回流进料口15进入,管线延伸进入塔内部,经液体分布器2均匀分布淋入填料,物料经上段填料3进入下段填料7前,需经过再分布器6。两段填料中部设置有甲醇蒸汽侧线进料口4,甲醇蒸汽由此从中段进入塔内参与反应,侧线进料状态由甲醇蒸发器5控制。最终反应生成的一氯甲烷从塔顶出口17产出,为防止液沫夹带问题产生,塔顶出料口前设置有除沫器16。为防止塔顶出料仍夹带液滴造成催化剂损失,出料进入旋风分离器18,夹带液滴经分离器18下部出口收集至收集罐20后返回塔釜底部补充。气相产物从分离器18上部离开进入下一工段。塔底部另设有排空口8。
53.实施例1-2与对比例的实验结果测量方法:为检测本发明所述方法的试验效果,将生成的气相产物进行冷却至15~25℃之间,将物料冷凝下来进行气液分离,分别测量液相和气相产品的组成。
54.实施例1:
55.在本发明的填料塔中,由塔釜底部氯化氢进料口9和新鲜甲醇蒸汽进料口13进料的甲醇和氯化氢摩尔比为1:1。上段填料下方的甲醇侧线进料,甲醇进料量与从塔釜底部进料的hcl的摩尔比为0.1:1,以75%zncl2水溶液为触媒,反应压力为0.13mpag,反应温度控制在150~160℃之间,塔内的空塔气速为80cm/s,其hcl转化率为98%。反应体系稳定后,将塔顶出料口的生成的气相产物进行冷却至15-25℃,测定冷却洗涤下来的液相组成和未冷凝的气相组成。其中液相组成中的酸浓度为2.84%,甲醇含量为3.88%;气相组成中二甲醚含量为10646ppm。
56.实施例2:
57.在本发明的填料塔中,由塔釜底部氯化氢进料口9和新鲜甲醇蒸汽进料口13进料的甲醇和氯化氢摩尔比为1:1。上段填料下方的甲醇侧线进料,甲醇进料量与从塔釜底部进料的hcl的摩尔比为0.1:1,采用无催化剂工艺,控制反应器顶部压力0.40~0.42mpag,反应温度控制在130~140℃,塔内空塔气速为30cm/s,其氯化氢转化率为99%。反应体系稳定后,将塔顶出料口的生成的气相产物进行冷却至15-25℃,测定冷却洗涤下来的液相组成和未冷凝的气相组成。其中液相组成中的酸浓度为1.97%,甲醇含量为13.7%,气相组成中二甲醚含量为5204ppm。
58.对比例:
59.在一个传统的搪瓷反应釜鼓泡反应器中,以甲醇和氯化氢以1.04:1的摩尔比进料,以75%zncl2水溶液为触媒,反应压力在0.08-0.09mpag,反应温度为150~160℃,反应釜内表观气速15cm/s,其氯化氢转化率为95%。反应体系稳定后,将生成的气相产物进行冷却至15-25℃,测定冷却洗涤下来的液相组成和未冷凝的气相组成。其中液相组成中酸浓度为8%,甲醇含量为6.6%;气相组成中二甲醚含量为16229ppm。
60.从对比数据看,本发明的实施例1-2方法相对于鼓泡反应器得到的产物,盐酸含量低,二甲醚含量低。表明本发明的方法具有hcl反应完全,副产物二甲醚被降低的优点。由于本发明方法的hcl转化率高,使得生成的一氯甲烷中酸含量低,从而能使后续对一氯甲烷进
行脱酸时,难度降低、成本降低,并且由此产生的脱酸后的含氯酸水浓度低,可以直接排放至污水处理厂进行常规处理。
再多了解一些
本文用于企业家、创业者技术爱好者查询,结果仅供参考。