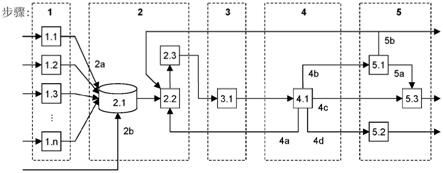
一种生产合成喷气燃料的方法
1.相关申请的交叉引用
2.本申请要求于2019年1月30日递交的us临时专利申请62/798,636号的优先权,其全部内容通过引用并入本文。
技术领域
3.本公开内容总体上涉及用于生产喷气燃料的方法。更具体地,本公开内容涉及一种用于生产合成喷气燃料的方法。
背景技术:
4.从原料(如可再生生物质和/或废物原料)生产航空涡轮燃料(也称为喷气燃料)的工艺是有价值的。喷气燃料是最不可能被非烃类燃料(例如电力)替代的运输燃料。
5.在设计一种从原料(如可再生材料和/或废物材料)生产喷气燃料的工艺方面存在挑战。
6.一个挑战是与生物质向液体转化相关的进料物流运输;例如,如文献(zwart,r.w.r.;boerrigter,h.;van der drift,a.energy fuels 2006,20,2192
‑
2197)中所述的。作为代表性原料的生物质主要由木质纤维素物质组成,并且是必须在大范围内收集的原料。生物质具有低物理密度(即单位体积的质量)和低能量密度(即单位体积的燃烧能量)。拥有将生物质转化为喷气燃料的集中化处理设施通常是首选,但远距离运输如此低密度的原料可能成本高昂(例如,在经济和能耗方面),并且通常需要在运输前对生物质进行致密化处理。对于废物原料来说,进料物流运输的挑战较小,其中废物收集通常作为一项对社区居民的服务通过污水系统和城市废物(垃圾)收集系统来提供。
7.与进料物流运输相关的另一个挑战是原料的高含水量,例如生物质和废物原料。尽管干燥和其他形式的除水方法是已知的(例如,allardice,d.j.;caffee,a.l.;jackson,w.r.;marshall,m.in advances in the science of victorian brown coal;li,c
‑
z.ed.elsevier,2004,p.85
‑
133),降低含水量以增加能量密度会增加成本。
8.另一个挑战是进料异质性。对于本质上主要是固体的原料,异质性通常是指物理和化学多样性。当工艺对进料变化敏感时,必须花费精力来均质化原料,这会增加成本。
9.另一个挑战与原料(例如生物质和废物原料)中氢、碳和氧的摩尔比有关。生物质和废物原料含有含氧化合物,其中超过1/3的总质量可以是氧。这与几乎不含氧的化石原油原料相反。当这种含氧原料转化为喷气燃料时,氧通常会随着氢的损失作为水被消除或随着碳的损失作为一氧化碳或二氧化碳被消除。然而,喷气燃料规格通常需要近乎完全的脱氧。通常,生物质和生物废物原料的氢碳摩尔比通常约为1.4:1,而喷气燃料通常需要约为2:1的更高的氢碳摩尔比,这是喷气燃料规格(如烟点和重量能量密度)的结果。
10.另一个挑战与用于精炼含有含氧化合物(含氧化物)的生物原油产物的技术有关;例如,当存在于产物的<350℃沸点馏分中时。用含有含氧化物的产物评价石油精炼技术运行的实验研究表明,经常需要对石油精炼技术进行改进,即使对于加氢处理也是如此;例
如,leckel,d.o.energy fuels 2007,21,662
‑
667;cowley,m.energy fuels 2006,20,1771
‑
1776;smook,d.;de klerk,a.ind.eng.chem.res.2006,45,467
‑
471。已经审阅了含氧化物对催化剂和精炼用催化作用的影响(例如,de klerk,a.;furimsky,e.catalysis in the refining of fischer
‑
tropsch syncrude;royal society of chemistry,2010)。传统的炼油厂可能不得不进行变革,以便将生物原油用作喷气燃料的原料。
技术实现要素:
11.在本公开内容的一个方面,提供了一种生产合成喷气燃料的方法,包括将原料转化为合成气;将合成气转化为包含液态烃的混合物;精炼包含液态烃的混合物以分离煤油产物;和加氢处理煤油产物以形成合成喷气燃料。
12.在本公开内容的一个实施方案中,提供了一种方法,其中将原料转化为合成气包括:在含水条件下热解原料以形成包含生物原油的混合物。
13.在另一个实施方案中,提供了一种方法,其中原料包含具有高含水量的生物质、有机材料、废物料流或它们的组合。
14.在另一个实施方案中,提供了一种方法,其中将原料转化为合成气包括:热解原料以形成包含生物原油的混合物。
15.在另一个实施方案中,提供了一种方法,其中原料包含具有低含水量的生物质、有机材料、废物料流或它们的组合。
16.在另一个实施方案中,提供了一种方法,其中将原料转化为合成气还包括:气化包含生物原油的混合物以形成合成气。
17.在另一个实施方案中,提供了一种方法,其中气化包含生物原油的混合物包括:将包含生物原油的混合物进行超临界水气化,以形成包含ch4、co、co2和h2的混合物;和将包含ch4、co、co2和h2的混合物重整以形成合成气。
18.在另一个实施方案中,提供了一种方法,其中重整包括干式重整和蒸汽重整。
19.在另一个实施方案中,提供了一种方法,其中当将原料转化为合成气时,该方法进一步包括:在气化之前将油原料、糖原料和/或醇原料添加到包含生物原油的混合物中。
20.在另一个实施方案中,提供了一种方法,其中合成气包含小于2:1的h2:co比率。
21.在另一个实施方案中,提供了一种方法,其中合成气包含小于2:1的(h2‑
co2)/(co co2)的化学计量比。
22.在另一个实施方案中,提供了一种方法,其中合成气包含小于1:1的(h2)/(2co 3co2)的ribblet比率。
23.在另一个实施方案中,提供了一种方法,其中将合成气转化为包含液态烃的混合物包括:进行费
‑
托合成以将合成气转化为包含液态烃的混合物。
24.在另一个实施方案中,提供了一种方法,其中使用铁基催化剂进行费
‑
托合成。
25.在另一个实施方案中,提供了一种方法,其中当进行费
‑
托合成以将合成气转化为包含液态烃的混合物时,该方法还包括:水煤气变换反应以提高h2的浓度。
26.在另一个实施方案中,提供了一种方法,其中在约2mpa的压力下;或在大于2mpa;或约2.5mpa;或约2.8mpa的压力下进行费
‑
托合成。
27.在另一个实施方案中,提供了一种方法,其中在约1.5mpa至5mpa范围内;或在约
2mpa至约4mpa的范围内;或在约2mpa至约3mpa的范围内;或在约1.5至约2.5mpa的范围内;或在约2mpa至约2.5mpa的范围内的压力下进行费
‑
托合成。
28.在另一个实施方案中,提供了一种方法,其中在大于2mpa的压力下进行费
‑
托合成。
29.在另一个实施方案中,提供了一种方法,其中包含液态烃的混合物包含大于1:1的烯烃与烷烃之比。
30.在另一个实施方案中,提供了一种方法,其中精炼包含液态烃的混合物以分离煤油产物包括:对包含液态烃的混合物进行气液平衡分离;和将混合物分离成煤油产物以及含水产物、石脑油和气体产物或瓦斯油和重质产物中的至少一种。
31.在另一个实施方案中,提供了一种方法,其中作为单级分离和/或多级分离进行气液平衡分离。
32.在另一个实施方案中,提供了一种方法,其中当分离含水产物时,精炼包含液态烃的混合物以分离煤油产物进一步包括:在将原料转化为合成气时气化包含生物原油的混合物之前,将分离的含水产物添加到包含生物原油的混合物中。
33.在另一个实施方案中,提供了一种方法,其中当分离石脑油和气体产物时,精炼包含液态烃的混合物以分离煤油产物进一步包括:将石脑油和气体产物低聚以形成包含第一附加煤油产物的混合物。
34.在另一个实施方案中,提供了一种方法,其中石脑油和气体产物的低聚在约2.5mpa,或约2mpa的压力下进行。
35.在另一个实施方案中,提供了一种方法,其中石脑油和气体产物的低聚在约1.5mpa至3mpa范围内;或在约1.5mpa至约2.5mpa的范围内;或在约2mpa至约2.5mpa的范围内的压力下进行。
36.在另一个实施方案中,提供了一种方法,其中使用非硫化催化剂进行石脑油和气体产物的低聚。
37.在另一个实施方案中,提供了一种方法,其中使用酸性zsm
‑
5沸石催化剂进行石脑油和气体产物的低聚。
38.在另一个实施方案中,提供了一种方法,其中第一附加煤油产物包含烯烃和芳族化合物。
39.在另一个实施方案中,提供了一种方法,其中第一附加煤油产物包含约0%至约60%的芳族化合物;约1%至约60%的芳族化合物;或约1%至约50%的芳族化合物;或约1%至约40%的芳族化合物;或约1%至约30%的芳族化合物;或约0%至约1%的芳族化合物;或约1%至约7%的芳族化合物;或约8%至约25%的芳族化合物;或约8%的芳族化合物。
40.在另一个实施方案中,提供了一种方法,其中当分离瓦斯油和重质产物时,精炼包含液态烃的混合物以分离煤油产物进一步包括:将瓦斯油和重质产物加氢裂化以形成包含第二附加煤油产物的混合物。
41.在另一个实施方案中,提供了一种方法,其中瓦斯油和重质产物的加氢裂化在约2.5mpa,或约2mpa的压力下进行。
42.在另一个实施方案中,提供了一种方法,其中瓦斯油和重质产物的加氢裂化在约
1.5mpa至3mpa范围内;或在约1.5mpa至约2.5mpa的范围内;或在约2mpa至约2.5mpa的范围内的压力下进行。
43.在另一个实施方案中,提供了一种方法,其中使用非硫化催化剂进行瓦斯油和重质产物的加氢裂化。
44.在另一个实施方案中,提供了一种方法,其中用负载在无定形二氧化硅
‑
氧化铝上的贵金属催化剂进行加氢裂化。在另一个实施方案中,催化剂是pt/sio2‑
al2o3。
45.在另一个实施方案中,提供了一种方法,其中加氢处理煤油产物以形成合成喷气燃料包括:加氢处理煤油产物,并且当分离石脑油和气体产物时,加氢处理第一附加煤油产物,以形成包含链烷烃的混合物;和分馏包含链烷烃的混合物,并且当分离瓦斯油和重质产物时,分馏包含第二附加煤油产物的混合物,以分离合成喷气燃料。
46.在另一个实施方案中,提供了一种方法,其中当分馏包含链烷烃的混合物和分馏包含第二附加煤油产物的混合物时,该方法进一步包括:在分馏之前将包含第二附加煤油产物的混合物加入到包含链烷烃的混合物中.
47.在另一个实施方案中,提供了一种方法,其中煤油产物、第一附加煤油产物和第二附加煤油产物中的每一个都具有约140℃至约300℃的标准沸点温度范围。
48.在另一个实施方案中,提供了一种方法,其中在约2.5mpa,或约2mpa的压力下进行加氢处理。
49.在另一个实施方案中,提供了一种方法,其中在约1.5mpa至3mpa范围内;或在约1.5mpa至约2.5mpa的范围内;或在约2mpa至约2.5mpa的范围内的压力下进行加氢处理。
50.在另一个实施方案中,提供了一种方法,其中使用非硫化催化剂进行加氢处理。
51.在另一个实施方案中,提供了一种方法,其中用负载在氧化铝或二氧化硅上的还原贱金属催化剂进行加氢处理。在另一个实施方案中,催化剂是还原的ni/al2o3。
52.在另一个实施方案中,提供了一种方法,其中合成喷气燃料是半合成喷气燃料、全合成喷气燃料或它们的组合。
附图说明
53.现在,将仅通过示例的方式参考附图来描述本公开内容的实施方案。
54.图1描绘了这里描述的方法的方框流程图。步骤由带虚线的方框表示,编号为1到5。在每个虚线方框内,提供了下一个级别的工艺细节。每个主要单元都有编号。只有需要澄清区别的料流才进行编号。
55.图2描绘了图1中第三步和第四步的详细流程框图,其中标识了主要料流。
56.图3更详细地描述了低聚单元,图1中的单元5.1,其中标识了主要料流。
57.图4描绘了图3的扩展图,显示了来自低聚单元的最轻的产物馏分(包括合成气化合物)是如何进一步加工的。
58.图5描绘了图3的扩展图,显示了如何可以提高合成喷气燃料的产率。
59.图6更详细地描绘了加氢裂化单元,图1中的单元5.2,其中标识了主要料流,未显示氢气进料和氢气循环。
60.图7更详细地描绘了加氢处理单元,图1中的单元5.3,其中标识了主要料流,未显示氢气进料和氢气循环。
61.图8描绘了图7的扩展图,显示了来自加氢处理器的产物是如何分离的。
62.图9描绘了用于生产合成的合成气的系统的示例,其中a描绘了水热液化单元;b描绘了超临界水气化单元;c描绘了重整单元;x
‑
x'表示a和b之间的进料流,z
‑
z'表示b和c之间的进料流。
具体实施方式
63.总体上,本公开内容提供了一种生产合成喷气燃料的方法,包括将原料转化为合成气;将合成气转化为包含液态烃的混合物;精炼包含液态烃的混合物以分离煤油产物;和加氢处理煤油产物以形成合成喷气燃料。
64.在本公开内容的一个实例中,提供了一种方法,其中将原料转化为合成气包括:在含水条件下热解原料以形成包含生物原油的混合物。
65.在另一个实例中,提供了一种方法,其中原料包含具有高含水量的生物质、有机材料、废物料流或它们的组合。
66.在另一个实例中,提供了一种方法,其中将原料转化为合成气包括:热解原料以形成包含生物原油的混合物。
67.在另一个实例中,提供了一种方法,其中原料包含具有低含水量的生物质、有机材料、废物料流或其组合。
68.在另一个实例中,提供了一种方法,其中将原料转化为合成气还包括:气化包含生物原油的混合物以形成合成气。
69.在另一个实例中,提供了一种方法,其中气化包含生物原油的混合物包括:将包含生物原油的混合物进行超临界水气化,以形成包含ch4、co、co2和h2的混合物;将包含ch4、co、co2和h2的混合物重整以形成合成气。
70.在另一个实例中,提供了一种方法,其中重整包括干式重整和蒸汽重整。
71.在另一个实例中,提供了一种方法,其中当原料转化为合成气时,该方法进一步包括:在气化之前将油原料、糖原料和/或醇原料添加到包含生物原油的混合物中。
72.在另一个实例中,提供了一种方法,其中合成气包含小于2:1的h2:co比率。
73.在另一个实例中,提供了一种方法,其中合成气包含小于2:1的(h2‑
co2)/(co co2)的化学计量比。
74.在另一个实例中,提供了一种方法,其中合成气包含小于1:1的(h2)/(2co 3co2)的ribblet比率。
75.在另一个实例中,提供了一种方法,其中将合成气转化为包含液态烃的混合物包括:进行费
‑
托合成以将合成气转化为包含液态烃的混合物。
76.在另一个实例中,提供了一种方法,其中使用铁基催化剂进行费
‑
托合成。
77.在另一个实例中,提供了一种方法,其中当进行费
‑
托合成以将合成气转化为包含液态烃的混合物时,该方法还包括:水煤气变换反应以提高h2的浓度。
78.在另一个实例中,提供了一种方法,其中在约2mpa的压力下;或在大于2mpa;或约2.5mpa;或约2.8mpa的压力下进行费
‑
托合成。
79.在另一个实例中,提供了一种方法,其中在约1.5mpa至5mpa范围内;或在约2mpa至约4mpa的范围内;或在约2mpa至约3mpa的范围内;或在约1.5至约2.5mpa的范围内;或在约
2mpa至约2.5mpa的范围内的压力下进行费
‑
托合成。
80.在另一个实例中,提供了一种方法,其中在大于2mpa的压力下进行费
‑
托合成。
81.在另一个实例中,提供了一种方法,其中包含液态烃的混合物包含大于1:1的烯烃与烷烃之比。
82.在另一个实例中,提供了一种方法,其中精炼包含液态烃的混合物以分离煤油产物包括:对包含液态烃的混合物进行气液平衡分离;和将混合物分离成煤油产物以及含水产物、石脑油和气体产物或瓦斯油和重质产物中的至少一种。
83.在另一个实例中,提供了一种方法,其中作为单级分离和/或多级分离进行气液平衡分离。
84.在另一个实例中,提供了一种方法,其中当分离含水产物时,精炼包含液态烃的混合物以分离煤油产物进一步包括:在原料转化为合成气时气化包含生物原油的混合物之前,将分离的含水产物添加到包含生物原油的混合物中。
85.在另一个实例中,提供了一种方法,其中当分离石脑油和气体产物时,精炼包含液态烃的混合物以分离煤油产物进一步包括:将石脑油和气体产物低聚以形成包含第一附加煤油产物的混合物。
86.在另一个实例中,提供了一种方法,其中石脑油和气体产物的低聚在约2.5mpa,或约2mpa的压力下进行。
87.在另一个实例中,提供了一种方法,其中石脑油和气体产物的低聚在约1.5mpa至3mpa范围内;或在约1.5mpa至约2.5mpa的范围内;或在约2mpa至约2.5mpa的范围内的压力下进行。
88.在另一个实例中,提供了一种方法,其中使用非硫化催化剂进行石脑油和气体产物的低聚。
89.在另一个实例中,提供了一种方法,其中使用酸性zsm
‑
5沸石催化剂进行石脑油和气体产物的低聚。
90.在另一个实例中,提供了一种方法,其中第一附加煤油产物包含烯烃和芳族化合物。
91.在另一个实例中,提供了一种方法,其中第一附加煤油产物包含约0%至约60%的芳族化合物;约1%至约60%的芳族化合物;或约1%至约50%的芳族化合物;或约1%至约40%的芳族化合物;或约1%至约30%的芳族化合物;或约0%至约1%的芳族化合物;或约1%至约7%的芳族化合物;或约8%至约25%的芳族化合物;或约8%的芳族化合物。
92.在另一个实例中,提供了一种方法,其中当分离瓦斯油和重质产物时,精炼包含液态烃的混合物以分离煤油产物进一步包括:将瓦斯油和重质产物加氢裂化以形成包含第二附加煤油产物的混合物。
93.在另一个实例中,提供了一种方法,其中瓦斯油和重质产物的加氢裂化在约2.5mpa,或约2mpa的压力下进行。
94.在另一个实例中,提供了一种方法,其中瓦斯油和重质产物的加氢裂化在约1.5mpa至3mpa范围内;或在约1.5mpa至约2.5mpa的范围内;或在约2mpa至约2.5mpa的范围内的压力下进行。
95.在另一个实例中,提供了一种方法,其中使用非硫化催化剂进行瓦斯油和重质产
物的加氢裂化。
96.在另一个实例中,提供了一种方法,其中用负载在无定形二氧化硅
‑
氧化铝上的贵金属催化剂进行加氢裂化。在另一个实例中,催化剂是pt/sio2‑
al2o3。
97.在另一个实例中,提供了一种方法,其中加氢处理煤油产物以形成合成喷气燃料包括:加氢处理煤油产物,并且当分离石脑油和气体产物时,加氢处理第一附加煤油产物,以形成包含链烷烃的混合物;和分馏包含链烷烃的混合物,并且当分离瓦斯油和重质产物时,分馏包含第二附加煤油产物的混合物,以分离合成喷气燃料。
98.在另一个实例中,提供了一种方法,其中当分馏包含链烷烃的混合物和分馏包含第二附加煤油产物的混合物时,该方法进一步包括:在分馏之前将包含第二附加煤油产物的混合物加入到包含链烷烃的混合物中.
99.在另一个实例中,提供了一种方法,其中煤油产物、第一附加煤油产物和第二附加煤油产物中的每一个都具有约140℃至约300℃的标准沸点温度范围。
100.在另一个实例中,提供了一种方法,其中在约2.5mpa,或约2mpa的压力下进行加氢处理。
101.在另一个实例中,提供了一种方法,其中在约1.5mpa至3mpa范围内;或在约1.5mpa至约2.5mpa的范围内;或在约2mpa至约2.5mpa的范围内的压力下进行加氢处理。
102.在另一个实例中,提供了一种方法,其中使用非硫化催化剂进行加氢处理。
103.在另一个实例中,提供了一种方法,其中用负载在氧化铝或二氧化硅上的还原贱金属催化剂进行加氢处理。在另一个实例中,催化剂是还原的ni/al2o3。
104.在另一个实例中,提供了一种方法,其中合成喷气燃料是半合成喷气燃料、全合成喷气燃料或它们的组合。
105.在详细解释本发明之前,应当理解,本发明不限于本申请中包含的示例性实施方案。本发明能够具有其它实施方案并且能够以各种方式实践或进行。应当理解,本文中使用的措辞和术语是为了描述的目的,而不是限制性的。
106.应当理解,为了图示的简洁和清楚,在认为合适的情况下,附图中可以重复附图标记以指示对应或类似的元件或步骤。此外,阐述了许多具体细节以提供对本文描述的示例性实施方案的透彻理解。然而,本领域普通技术人员将会理解,可以在没有这些具体细节的情况下实践本文描述的实施方案。在其他情况下,没有详细描述众所周知的方法、过程和组件,以免混淆这里描述的实施方案。此外,该描述不应被视为以任何方式限制在此描述的实施方案的范围,而是仅仅描述了在此描述的各种实施方案的示例性实施方式。
107.除非另有定义,本文使用的所有技术和科学术语具有与本发明所属领域的普通技术人员通常理解的相同的含义。
108.本说明书和权利要求书中使用的单数形式“一个/一种(a)”、“一个/一种(an)”和“所述”包括多数的引用,除非上下文中另外有明确说明。
109.如本文所用,术语“包括”将被理解为表示以下列表并非详尽无遗,并且可能包括或可能不包括任何其他合适的项目,适当情况下例如一个或多个其他特征、组件和/或成分。
110.如本文所用,术语“约”和“大致”与尺寸、浓度、温度或其他物理或化学性质和特性的范围结合使用。这些术语的使用旨在涵盖可能存在于性质和特性值或范围的上限和下限
中的轻微变化,例如
±
10%或
±
5%。
111.如本文所用,“航空涡轮燃料”或“喷气燃料”是指在添加所需的燃料添加剂以满足合成航空涡轮燃料的规格要求之前的煤油作为与石油衍生的煤油的喷气燃料混合组分(即半合成喷气燃料),或不含任何石油衍生煤油的喷气燃料(即全合成喷气燃料)。例如,这些规格要求在适当的标准文件中进行了描述,例如the united kingdom ministry of defense.defense standard 91
‑
91,issue 7.turbine fuel,kerosine type,jet a
‑
1,nato code:f
‑
35,joint service designation:avtur;ministry of defence:london,18february 2011,and astm d 7566
–
15b updated to astm d7566
–
19(例如,参见annex a1,synthesized paraffinic kerosene(spk)with aromatics).standard specification for aviation turbine fuel containing synthesized hydrocarbons;american society for testing and materials:west conshohocken,pa,2015。本领域技术人员将认识到,通过加入添加剂可能仅满足少数规格要求;许多规格要求可以通过精炼方法来满足(例如参见下面的实施例4,其中仅添加静电耗散剂就可以满足要求)。
112.如本文所用,“原料”是指生物质、有机材料、废物料流或它们的组合。原料的实例包括但不限于来自谷物乙醇工厂的废物料流(甘蔗渣、酒糟、废水和甘油)、纤维素生物质(木材、能源作物、草)、有机废物(绿色垃圾收集废物产物;污水污泥)、农业废物(农业植物废物或残留物、粪便)、纸浆和造纸厂废物料流(木材废物、预水解物)、市政分类的有机废物、生物柴油(甘油)及其任何组合。生物质的实例包括但不限于作为森林采伐、产品制造、建筑和拆除残骸收割或管理等活动的副产品的材料;和木质纤维素生物质,例如木基残留物,其分为三类:森林残留物、城市残留物和工厂残留物。有机材料的实例包括但不限于以下的任何一种:纤维素材料、木质纤维素材料、废物(例如木材加工废物、农业残余物、市政绿色垃圾箱收集物、肥料、来自纤维素材料加工厂的流出物、来自造纸厂的流出物、来自由生物质生产乙醇过程的流出物、酒糟废液或全酒糟、干酒糟和可生物降解的废水;分子结构中含有碳和氢的物质,例如醇、酮、醛、脂肪酸、酯、羧酸、醚、碳水化合物、蛋白质、脂类、多糖、单糖、纤维素、核酸等;并且可以存在于例如废物(例如农业或工业废物料流;污水污泥)、有机流体料流、新鲜生物质、预处理生物质、部分消化的生物质等中。在一些实例中,如本文所定义的“原料”包括具有高含水量的原料和/或具有低能量密度的原料。在一些实例中,如本文所定义的“原料”包括具有低含水量的原料。
113.在一些实例中,高含水量是指在环境条件下水作为单独相存在的材料。在一个实例中,高含水量是指材料的含水量超过有机物含量。在其他实例中,高含水量是指例如>40重量%,或介于约50重量%至约95重量%之间;或介于约60重量%至约90重量%之间;或介于约70重量%至约90重量%之间;或介于约80重量%至约90重量%之间的含水量;或者,约50wt%和约70wt%之间的任何值至约75重量%和约95重量%之间的任何值。在一些实例中,低含水量是指在环境条件下水不作为单独相存在的材料。在其他实例中,低含水量是指例如≤40重量%,或介于约5重量%至约40重量%之间;或介于约10重量%至约40重量%之间;或介于约20重量%至约40重量%之间;或介于约30重量%至约40重量%之间的含水量;或者,约5wt%和约20wt%之间的任何值至约25重量%和约40重量%之间的任何值。
114.如本文所用,“油原料”是指植物油或动物脂肪油。在一些实例中,“油原料”是指废弃的植物油或动物脂肪油。“糖原料”是指糖的溶液。在一些实例中,糖可以是废糖。“醇原
料”是指液体醇,如甘油。在一些实例中,液体醇可以是废物醇。
115.如本文所用,“在含水条件下热解原料”是指在环境条件下作为单独相存在的水存在下对原料进行热解或热处理;例如但不限于,水热液化。如本文所用,“热解原料”是指原料的热解或热处理,其中水在环境条件下不作为单独相存在;本领域技术人员将认识到,“含水条件”是指水以足以充当例如试剂、催化剂、溶剂或它们的组合的量存在。技术人员也将认识到,“热解条件”可以指不存在水;或以不足以充当例如试剂、催化剂、溶剂或它们的组合的量存在的水。
116.如本文所用,“液态烃”是指直链、支链和/或环状烷烃和烯烃(烯烃),或可以未被取代或被含氧官能团取代的芳族化合物,例如但不限于醇、醛、羧酸、酮、醚等。
117.如本文所用,“生物原油”是包括但不限于芳族化合物、多芳族化合物、脂肪酸、烷烃、烯烃和/或含氧化合物的混合物。
118.如本文所用,“链烷烃”是指直链或支链烷烃,并且可以包括环烷烃。
119.本文描述的是将原料如生物质、废物原料、油原料、糖原料和/或醇原料转化为适合混合或适合直接用作半合成或全合成喷气燃料的合成喷气燃料的方法。
120.参考图1,该方法的实例分五个步骤进行描述,如虚线框所示。这五个步骤包括(1)将原料热解,或在含水条件下将原料热解(例如水热液化)以产生包含生物原油的混合物,(2)将包含生物原油的混合物气化以形成合成气,以及任选地在气化之前向包含生物原油的混合物添加油原料、糖原料和/或醇原料,(3)进行费
‑
托合成以将合成气转化为包含液态烃的混合物,(4)精炼包含液态烃的混合物以分离煤油产物和至少三种其他馏分,以及(5)对煤油产物进行加氢处理以生产作为主要产物的喷气燃料。在一些实例中,图1的步骤1在分布式位置执行并且图1的步骤2至5在中央位置执行。
121.图1的步骤1旨在将原料(例如体积大的低能量密度原料)转化为易于处理和运输的密度更高的液体。在步骤1的实例中,含水条件下的热解涉及水热液化,如图1中的方框1所示。如图所示,水热液化单元是小规模的分布式单元,可以靠近原料源部署,例如生物质或废料源。水热液化单元由图1中的方框1.1到1.n表示,其中n是正整数值。通过以分布式方式部署直接液化单元,可以缩短原料到中央工厂的距离;并且,由于在步骤1中生产的产物(即包含生物原油的混合物)具有比原料更低的含水量和更高的物理密度和能量密度,因此这种转化可以使运输到大型集中式最终产品工厂成为可能。通过生产包含作为液体产物的生物原油的混合物,与致密的固体产物相比,均质化相对容易。任选地,水热液化单元之一可以位于中央处理设施处。在未示出的步骤1的另一个实例中,可以适当地为每个分布式原料选择其他液化技术,例如热解以从干燥/类固体原料生产油。在所述实例中,步骤1的方框1.n是热解单元。当只有一个局部进料源可用时,图1中的n=1,并且只使用一个水热液化单元。
122.水热液化是将原料在含水条件下加热一段足以基本上水解原料并产生平均分子量低于进料的液化产物的方法。水热液化是直接液化方法的一个实例。水热液化方法可以在亚临界或超临界水条件下作为间歇、半间歇或连续工艺实施。操作条件,无论是超临界或亚临界,也决定了液化产物中炭形成和氧含量的最小化。在此方法中产生的一些不可凝气体可用作燃料气体以提供所需的能量。水热液化不需要干燥原料。根据原料被加热到的温度,压力会自动产生以限制水的蒸发。在水热液化之后,可以采用液
‑
液相分离来分离水和
液化产物。水热液化方法可以小规模实施,以至于甚至可以在移动单元上实施。
123.在如本文所述的方法的实例中,水热液化(htl)在约350℃的温度下进行40分钟。或者,它在约410℃的超临界水中仅进行几分钟(例如,约5分钟或更短)。技术人员会认识到,不同的水热液化条件可以产生略有不同的生物原油,主要区别在于生物原油中的氧含量:超临界水htl可以生产含约8%至约10%氧的生物原油,而htl热解可以生产氧含量低于40%的生物原油。本文所述的方法可以接受所有不同类型的生物原油/生物油。
124.在一个实例中,装有移动液化单元(例如,水热液化单元或热解单元等)的拖车可以停在农场上,以将农场废物和生物质加工成液化产物(例如,包含生物原油的混合物),该液化产物被收集在用于间歇收集的移动罐中。这种移动单元通常设计用于简单和无人监督的操作。在另一个实例中,较大的固定式液化单元可以位于设施处,例如城市废物处理设施和锯或造纸厂,在这些设施中,生物质和废物原料的收集网络已经到位。由于规模较大,这些固定式液化单元通常设计为具有更复杂的热集成,以提高操作效率。该方法的其余部分在中央设施处进行,在那里从分布式液化单元收集液化产物(例如,包含生物原油的混合物)并进行处理。
125.图1的步骤2旨在将来自步骤1的液化产物(即,包含生物原油的混合物)(见图1中的2a)和可能的来自除步骤1之外的其他来源的油原料、糖原料和/或醇原料,例如废弃的植物油或动物脂肪油(见图1中的2b)组合和均化(见图1中的单元2.1),然后将这些进料气化为粗合成气(见图1中的单元2.2)。如图1所示,用于生产粗合成气(在单元2.2中)的进料可能另外包括费
‑
托含水产物(料流4a)和来自精炼的材料(料流5b)。然后对粗合成气进行净化(见图1中的单元2.3)以生产清洁合成气。
126.术语粗合成气是指包含氢气(h2)和一氧化碳(co)以及其他化合物的混合物的气体。其他化合物通常包括但不限于二氧化碳(co2)、水蒸气(h2o)和甲烷(ch4)。术语清洁合成气是指除去存在于粗合成气中的潜在有害化合物之后的粗合成气。必须去除的最常见的一类污染物是含硫化合物,例如硫化氢(h2s)和羰基硫(cos)。此外,还可以在清洁过程中去除其他化合物,以提高下游工艺的效率。
127.使用包含生物原油的混合物作为粗合成气生产的进料,以及其他液体进料,如油原料、糖原料和/或醇原料,可以通过在气化之前在原料罐中混合(见图1中的单元2.1)来减少进料异质性的影响。由于进料主要是液体,因此更容易将来自不同来源的进料均质化。此外,液体进料可以使粗合成气生产相对简单和高效,因为它避免了固体处理;可以泵送液体进料以对其加压;液体进料可能具有优异的气化传热性能;清洗后,不含可能污染合成气的矿物质。粗合成气生产步骤的操作压力影响下游操作。在高压下进行粗合成气生产是有益的。在一个实例中,在约2mpa或更高,或在约2mpa至5mpa范围内;或在约2mpa至约4mpa的范围内;或在约2mpa至约3mpa的范围内的压力下生产粗合成气。
128.在如本文所述的方法的实例中,粗合成气通过超临界水气化(scwg)生产。使用scwg和相对于碳/氢/氧含量的适量水,一旦通过外部热源(例如启动炉)开始气化,就会通过scwg放热反应在反应器内产生气化所需的热量。因此,scwg不需要恒定的外部热源,而多余的水需要一些外部热量。此外,scwg反应器在较低温度下运行,且无需使用外部供应的氧化剂。scwg反应器中的水通常通过水煤气变换反应放出一些氢,以将粗合成气中的氢碳比增加到高于通常单独通过液体进料气化所预期的水平。所有进料都在高压下以液相形式引
入scwg工艺,通常高于用于费托合成的合成气进料的压力要求,这既节能又比生产后压缩粗合成气更简单。从scwg反应器出来的热气体与进入的原料进行热交换,气体中的水蒸气与其他水溶性有机化合物一起被冷却/冷凝,并在加压的液/气分离器中分离。分离的富水产物一部分被循环回scwg工艺。此时,粗合成气可能仍含有除氢气和一氧化碳以外的化合物。其中的一些化合物可以通过冷凝去除,但可能需要进行一些气体净化(见图1中的单元2.3)以去除可能影响下游方法的气态污染物。清洁后的合成气可能仍含有除氢气和一氧化碳以外的化合物,例如水蒸气和二氧化碳,但基本上不含含硫化合物。清洁粗合成气以获得清洁合成气的方法是本领域技术人员已知的。
129.在本文所述方法的一个实例中,在570℃至590℃范围内的温度下、约30%至约60%的水含量下和在约20mpa至约30mpa或约22.5mpa至约25mpa范围内的压力下进行超临界水气化(scwg)。在另一个实例中,在约>550℃的温度下进行超临界水气化(scwg),其中压力取决于反应器设计和压力控制手段。
130.在步骤2的一些实例中,重整与清洁合成气生产结合使用以将清洁合成气中存在的烃转化为氢气和一氧化碳。在粗合成气中存在足够的甲烷与二氧化碳一起,允许使用蒸汽重整和干式重整对这些气体进行重整。这也允许从粗合成气中回收额外的co2,以最大限度地将甲烷转化为一氧化碳和氢气。在形成过程中也会产生一些二氧化碳和水。可以通过冷却气体来分离水,并且可以在合成气净化单元中减少二氧化碳。
131.在其最简单的形式中,蒸汽重整和干式甲烷重整的反应与步骤2中的水煤气变换和逆水煤气变换反应一起如下:
132.1.
133.2.
134.3.
135.4.
136.任选地,可以考虑使用水煤气变换器来改变清洁合成气中氢气与一氧化碳的摩尔比。至少可以为步骤3选择的一些潜在技术可能受益于接近2:1的氢与一氧化碳摩尔比。任选地,清洁合成气生产之后是从清洁合成气中去除一些co2。可以回收利用部分co2。
137.图9描绘了可用于如本文所述的方法的用于生产合成气的系统的实例,其中a描绘了水热液化单元;b描绘了超临界水气化单元;和c描绘了重整单元。
138.更具体地说,图9a描绘了水热液化(htl)单元的实例,它包括:
139.·
所有类型的原料,例如所有类型的有机废物、粪便、污水污泥、农业和森林残留物以及所有生物质类型;
140.·
调整原料比例以适应20%的干物质,以及调整水量;
141.·
原料(20%干物质)通过高压进料泵泵送到热回收单元,然后泵送到加热器单元;
142.·
进料可能包括来自费
‑
托单元的有机相/水相,然后通过hp泵从加热器单元泵送到htl反应器,然后返回到加热器单元;
143.·
从htl反应器后面的加热器单元,进料被移至冷却器,然后移至产物分离器;
144.·
产物分离器输出不可凝气体和生物原油(然后被泵送到图9b的超临界水气化单元);和
145.·
产物分离器还输出到htl水收集器,该水收集器输出盐净化,和盐分离后回收的水进入高压进料泵。
146.图9b描绘了超临界水(scw)生物原油气化单元的实例,它包括:
147.·
从图9a的htl单元接收生物原油,将其移至热回收单元,然后是加热器;
148.·
进料从加热器移至scwg反应器(其输出到能量汇“e”);
149.·
从反应器输出的进料被移回热回收单元,然后移至减压涡轮机(也输出到能量汇“e”);
150.·
进料从涡轮机被移至另一个热回收单元,然后移至冷却器;
151.·
进料从冷却器移至高压气/液分离器(hp闪蒸器),其输出水相和生物气体(然后移至图9c的重整单元);和
152.·
水相成为水循环的一部分,它接受补充水,然后被送回第二个热回收单元(其将热量输送到加热器)。
153.图9c描绘了重整单元的实例,它包括:
154.·
从图9b的scwg单元接收生物气体,将其移至热回收单元,然后移至hrsg;
155.ο热回收蒸汽发生器(hrsg)输入还包括补充水(通过hrsg给水泵泵送到hrsg);
156.οhrsg输出包括通到能量汇
‘
e’的剩余料流;
157.ο热回收装置和hrsg也都供给蒸汽甲烷/干式甲烷重整单元(smr/dmr),其输出返回到热回收单元;
158.·
进料从hrsg移至冷却器,然后移至hp闪蒸器;
159.·
另一个hp闪蒸器输入包括从补充水中回收水;和
160.·
进料从hp闪蒸器移至co2净化单元,该单元输出合成气,这些合成气可被引导至费
‑
托单元,以及co2(包括返回到热回收单元的循环co2和过量的co2)。
161.图1的步骤3旨在通过费
‑
托合成将合成气转化为包含液态烃的混合物(参见图1中的单元3.1)。甲醇合成是可用于该步骤的替代方法,但已知将甲醇转化为烃会产生1,2,4,5
‑
四甲基苯,这是生产喷气燃料时非常不受欢迎的煤油系列产物。
162.在其最简单的形式中,对于费
‑
托合成的步骤3中的主要反应可以用以下反应式1
‑
6表示,其中反应式6仅与铁催化的费
‑
托合成相关:
163.烯烃:n co 2n h2→
(ch2)
n
n h2o
ꢀꢀ
(1)
164.烷烃:n co (2n 1)h2→
h(ch2)
n
h n h2o
ꢀꢀ
(2)
165.醇:n co 2n h2→
h(ch2)
n
oh (n
–
1)h2o
ꢀꢀ
(3)
166.羰基:n co (2n
–
1)h2→
(ch2)
n
o (n
–
1)h2o
ꢀꢀ
(4)
167.羧酸:n co (2n
–
2)h2→
(ch2)
n
o2 (n
–
2)h2o
ꢀꢀ
(5)
168.水煤气变换:
169.反应式1到6中的n值取决于链增长的概率。链增长的概率或α值取决于费
‑
托催化剂的性质和操作。产物分布由anderson
‑
schulz
‑
flory分布合理地表示。对于本文所述方法的费
‑
托合成,来自费
‑
托合成的产物通常具有在n=1至100范围内的碳数,尽管可能形成一些n>100的产物。
170.在步骤3的实例中,铁催化的费
‑
托合成用于将合成气转化为包含液态烃的产物混合物。铁催化的费
‑
托合成不需要调整合成气组成以满足大约2:1的氢与一氧化碳使用比,
因为铁基费
‑
托催化剂能够执行水煤气变换反应。在一个实例中,铁催化的费
‑
托合成在240℃和更高的温度下进行,或者在240至280℃范围内的温度下进行。在较高温度下操作费
‑
托合成允许通过高压蒸汽生产去除反应放热,通常在4mpa或更高的压力下产生蒸汽。
171.在步骤3的另一个实例中,铁基费
‑
托合成是使用氢与一氧化碳之比小于2:1的合成气进行的。在另一个实例中,铁基费
‑
托合成是使用化学计量比(h2‑
co2)/(co co2)小于2:1的合成气进行的。在另一个实例中,铁基费
‑
托合成是使用ribblet比率(h2)/(2co 3co2)小于2:1的合成气进行的。在另一个实例中,费
‑
托合成的设计使得来自费
‑
托合成的包含液态烃的混合物的烯烃与烷烃之比大于1:1。大于1:1的所述烯烃/烷烃比对于本文所述的方法通常是期望的,因为随着烯烃/烷烃比的降低,低聚反应会受到影响(例如低聚反应的产率会降低),这会降低生产全合成喷气燃料的能力。
172.在另一个实例中,费
‑
托合成的设计使得在费
‑
托合成过程中合成气的单程一氧化碳转化率很高,通常高于80%,更优选高于90%。在另一个实例中,费
‑
托合成的设计是根据需要将蒸汽供入费
‑
托合成,以便反应进行而不会形成过多的碳。
173.以下是图1步骤3的实例的更详细说明(参见图2)。在步骤3中,图2中由料流299表示的合成气通过由方框300表示的费
‑
托合成转化为由料流301和302表示的包含液态烃的混合物。在这样的温度和压力条件下进行步骤3,在该条件下,费
‑
托反应器可能具有气相和液相,催化剂呈固相。费
‑
托合成的反应产物(即包含液态烃的混合物)可以作为两个单独相离开反应器,其中反应器本身既用作反应器又用作相分离器。在图2中,料流301是离开费
‑
托反应器(方框300)的气相产物,料流302是离开费
‑
托反应器(方框300)的液相产物。离开反应器的气相产物和液相产物的确切性质和位置取决于所选择的具体反应器技术,例如多管固定床反应器或淤浆相泡罩塔式反应器。任何需要在方框300中保留催化剂的装置都被视为该方框中技术的一部分。取决于费
‑
托合成的操作,料流301和302中产物的相对量可能会有所不同。在一个实例中,没有材料作为料流302离开方框300。由于图2中方框300中反应的放热性质,水作为料流303供应并蒸发以产生作为料流304的蒸汽。在料流303中供应的水不与工艺过程混合,并且料流303和304两者都可以被认为是与工艺过程分离的公用料流,但它们是从方框300中去除热量的组成部分。
174.图1的步骤4旨在通过将混合物分离为至少四个产物馏分(参见图1中的单元4.1)来分离来自费
‑
托合成的产物(即包含液态烃的混合物):(4a)含水产物,(4b)石脑油和气体产物,(4c)煤油产物,和(4d)瓦斯油和重质产物。含水产物包含水和在产物分离期间冷凝的水溶性分子。石脑油和气体产物包括在标准沸点温度低于煤油的含水产物中不存在的所有物质。煤油产物包含沸点范围与喷气燃料蒸馏要求相容的烃;广义上讲,煤油产物的标准沸点温度范围为140
‑
300℃。瓦斯油和重质产物包括标准沸点温度高于煤油的材料。在一些实例中,这四种产物没有被分离为精确的馏分。在一些实例中,气液平衡自然会导致费
‑
托合成反应器中的一些分离。部分或全部瓦斯油和重质产物(参见图1中的料流4d)可以作为单独的液体产物从费
‑
托合成中获得(参见图1中的单元3.1),并且不需要在第四步中进行分离。为了分离费
‑
托合成的重质和轻质产物,以便方便地升级为喷气燃料,使用了不同压力和温度下气液平衡分离技术的组合,并且可以与选定的分离馏分的蒸馏相结合。这避免了在该部分工艺过程中需要常压蒸馏单元,这可以使步骤4的能源效率相对更高且资本密集度更低。
175.以下是图1步骤4的实例的更详细说明(参见图2)。在方框400中降低图2中的料流301中气相产物的温度。可以通过本领域已知的装置实现这种温度变化。在一个实例中,料流301的温度通过在由方框400表示的进料
‑
产物热交换器中与料流299热交换而降低。方框400中的温度变化也可以通过其他方式实现,例如使用公用料流或通过空气冷却。在另一个实例中,料流401的温度使得料流301中存在的水冷凝并且料流401中的水处于其泡点或低于其泡点。料流401中水的泡点温度与压力之间的关系由气液平衡决定。在另一个实例中,401的温度是通过方法控制来控制和保持恒定的。此外,该温度是通过优化通到步骤5的产物路线来选择的,而不是像通常的工业实践那样用于冷凝更多材料。因此,该温度被控制为处于或接近料流401中水的泡点。料流401进入相分离器,由图2中的方框410表示。在该实例中,相分离器是三相相分离器。相分离器的目的是使存在于料流401中的相能够分离以产生气相料流411、有机液相料流412和含水液相料流413。在一个实例中,方框400和410组合在一个设备中,该设备能够在同一设备中实现温度变化和相分离两者。在另一个实例中,方框400和410以这样一种方式组合,即该装置具有一个以上的平衡级以实现分离成料流411、412和413。
176.图1和图2中所示的料流之间的关系如图2所示。气相料流411主要包含气态和石脑油馏分产物,料流(4b)。有机液相料流412主要包含煤油产物,料流(4c)。含水产物料流413主要包含水和溶解的有机化合物,所述有机化合物主要是含氧化合物,料流(4a)。来自费
‑
托反应器的液体产物是料流302并主要包括瓦斯油和重质有机化合物,料流(4d)。此处描述的分离的设计和控制能够以这样的方式进行产物路线,即不必在步骤5中的任何单元之前使用单独的常压蒸馏单元。这利用了来自单元300的热产物中已经可用的能量,而不会破坏炼油厂的运行。
177.图1的步骤5旨在精炼从费
‑
托液化产物(即包含液态烃的混合物)中分离出来的四种产物馏分。精炼采用三种工艺,即低聚(见图1中单元5.1)、加氢裂化(见图1中单元5.2)和加氢处理(见图1中单元5.3)。含水产物(见图1中的4a)被循环用作合成气生产的进料(见图1中的单元2.2)。含水产物与水热液化产物一样,本质上是酸性的。水热液化产物和费
‑
托含水产物的结合利用了对耐酸建筑材料的普遍需求。将含水产物与水热液化产物(即包含生物原油的混合物)共同进料能够使酸基本上转化为合成气,而不是依赖于化学计量。它消除了将含水产物作为具有高化学需氧量的酸性废水单独处理的情况,这是工业费
‑
托型煤制油和气制油设施中经常遇到的昂贵必需品。
178.直馏气体和石脑油产物(图1中的4b)没有进一步分离,这是费
‑
托合成后分离的常见做法。气体和石脑油产物也含有未反应的合成气,直接用作低聚过程的进料。低聚过程是指涉及两个或多个不饱和分子的加成反应的转化过程。该过程有利于将轻质烯烃(即链烯基)产物转化为重质烯烃产物,后者更容易通过冷凝回收。此外,进料更稀的性质有助于放热低聚方法中的热量管理,并且气体中氢气的存在可以抑制焦化反应。此外,含氧有机分子(含氧化合物)会转化为烃,即使这种转化可能不完全。在一个实例中,低聚过程使用非硫化催化剂,例如酸性zsm
‑
5沸石(mfi骨架型)作为催化剂。
179.在最简单的形式中,低聚过程操作期间的主要反应可以由以下反应式7
‑
9表示:
180.低聚/裂化:
181.芳构化:烯烃
→
芳烃 烷烃(8)
182.芳烃烷基化/脱烷基化:
183.除了反应式7
‑
9中的反应外,还可能发生各种涉及含氧化合物的反应,例如脱水和酮化。所描述的反应并非旨在详尽无遗,而是出于说明目的而提供。这些反应的相对普遍性取决于低聚过程的温度和压力条件。通过操纵低聚过程中的操作条件,可以生产煤油材料,该煤油材料能够混合来自本文所述方法的全合成喷气燃料。通过在有利于芳构化的温度和压力下操作至少部分低聚催化剂(反应式8),可以控制芳烃的总量以增加或减少与通过本文所述的方法生产的半合成喷气燃料相关的全合成喷气燃料的量。在一个实例中,使用非硫化催化剂,例如未促进的zsm
‑
5催化剂。
184.在如本文所述的低聚过程的实例中,在约200℃至约320℃范围内的操作温度通常会产生可用作生产半合成喷气燃料的共混材料的产物,因为它是加氢处理后的异链烷烃煤油(例如,参见实施例1和4)。约>320℃(通常为约320℃至约400℃)的操作温度通常用于生产具有更多芳烃的产物,该产物适合在加氢处理以饱和烯烃后将全合成喷气燃料共混(例如,参见实施例2和5)。在一些实例中,在两种情况下,压力都可以在很宽的范围内变化,例如约0.1mpa至约20mpa。
185.通常,本文所述的方法可在与本文所述的费
‑
托合成相当或略低的压力下操作,例如大约2mpa,尽管由于烯烃的分压较高,在较高压力下操作通常更容易。在与本文所述的费
‑
托合成相当或低于所述费
‑
托合成的压力下操作,无需事先分离以除去未转化的合成气,避免了本文所述方法中的分离和再压缩。
186.在另一个实例中,低聚过程使用气态产物料流411(图2),其包括来自费
‑
托方法的未转化合成气。未转化的合成气包括但不限于h2、co、co2和h2o。通常的做法是从包含h2、co和co2的未转化合成气中分离轻质烯烃,从而消除通常存在的分离步骤。此外,通过采用低聚反应,包括乙烯在内的烯烃转化为重质产物,其在低聚反应后比低聚反应前更容易回收。
187.来自低聚过程的产物(例如,包含第一附加煤油产物的混合物)包含未转化的材料和新产物。未转化的材料包括氢气、一氧化碳和链烷烃。新产物具有的沸点范围分布涵盖气体、石脑油和馏出液,材料范围从通常的气态化合物到标准沸点温度高达360℃的化合物。新产物包括第一附加煤油产物。第一附加煤油产物包含烯烃和芳族化合物。烯烃与芳族化合物的比例取决于低聚过程的操作条件。这种调节烯烃与芳族化合物比例的灵活性促进了半合成喷气燃料的生产和全合成喷气燃料的生产。该附加煤油产物(见图1中的5a)被送到加氢处理器(图1中的单元5.3)。煤油系列之外的液体产物(参见图1中的5b)可以通过以下一种或多种组合进行处理:(i)作为最终产物回收(如图1所示),(ii)送到加氢处理器(图1中未显示),(iii)再循环到低聚过程(图1中未显示),和/或再循环到合成气生产(见图1中的单元2.2)。
188.在一个实例中,煤油沸点范围之外的烯烃和芳族化合物作为产物被回收。在另一个实例中,煤油沸点范围之外的一些或全部烯烃和芳族化合物被再循环到低聚过程。在另一个实例中,煤油沸点范围之外的一些或全部烯烃和芳族产物被送至加氢处理器。
189.来自低聚过程的未转化材料至少可以用作加氢裂化器和加氢处理器的氢源。低聚反应下游的气体处理的性质涉及气体处理领域技术人员已知的方法,例如热碳酸盐吸收以去除二氧化碳,和变压吸附以回收氢气。
190.煤油产物(见图1中的4c)被送到加氢处理器。也可以选择将部分或全部产物送至
加氢裂化器单元(图1中未显示路线)。决定是否将任何该产物送至加氢裂化器的因素是目标喷气燃料的冰点规格。例如,直馏费
‑
托煤油通常具有高直链烃含量。然而,如果煤油中直链烃的浓度太高,则开始冻结的温度将太高而无法满足航空涡轮燃料规格。
191.以下是图1的步骤5中的低聚反应单元的实例的更详细说明。图3更详细地描述了步骤5中的低聚反应单元。包含烃、含氧有机化合物和未转化的合成气的料流411(即石脑油和气体产物)的转化发生在低聚反应单元510中。来自510的产物是料流511(即,包含第一附加煤油产物的混合物),其包含平均比料流411中的烃重的烃、显著更少含氧的有机化合物和未转化的合成气的混合物。如前所述,511中烃的组成取决于510中的操作条件。
192.料流511在520中分离。在一个实例中,料流511被分离以产生气态产物521、有机液体产物522和富水液体产物523。这种类型的分离可以通过降低温度来冷凝511的一部分来实现,它们然后可以在三相汽
‑
液
‑
液分离器中进行分离。实现这种类型分离的另一种方法是使用具有一个以上平衡级的装置。实现这种类型分离的另一种方法是使用采用液体吸收的装置。料流521可以以各种方式应用。料流521的一种潜在用途是作为燃料气体。料流521的另一个潜在用途是将部分或全部的521再循环到费
‑
托合成或合成气生产。在一个实例中,料流521如图4所示进行处理。料流521在单元610中被处理以除去部分或几乎所有的二氧化碳以产生富含co2的料流611和贫co2的料流612。这种类型的分离可以通过本领域已知的工艺技术进行,例如热碳酸盐吸收或胺吸收。富含co2的料流611是流出物,但由于其高co2浓度,料流611可能适合作为co2封存或直接排放的进料。贫co2的料流612可以与进入料流613的部分或全部的料流612分开。未进入料流613的料流612的其余部分可以进入料流614。由于料流613中的co2含量降低,它可用于与521相同的目的,但与直接使用521相比具有更高的效率。
193.料流614在单元620中被进一步分离。使用单元620来回收存在于614中的部分氢气作为料流621,剩余的材料在料流622中。通常用于在620中分离的技术之一是变压吸附,它会在料流621中产生h2作为高纯度氢气料流。料流621中的氢气将用于图1所示的单元5.2和5.3中。料流522被送到加氢处理器,图1中的单元5.3。
194.任选地,可以进一步分离有机液体产物522。该选项在图5中描述,其显示了在单元530中将522分离成由料流531表示的轻质馏分和由料流532表示的重质馏分。531中的轻质馏分通常是标准沸点低于140℃的材料,而532中的重质馏分通常是标准沸点为140℃或更高的材料。料流532被送到加氢处理器,图1中的单元5.3。轻质馏分料流531可以与进入料流533的部分或全部的料流531分开。未进入料流533的料流531的其余部分可以进入料流534。料流534再循环至低聚反应单元510以将部分轻质馏分转化为在转化后将形成由532表示的部分重质馏分的产物。因此,料流534的再循环能够将部分轻质馏分转化为重质馏分,从而增加532与531的比率,这增加了适用于喷气燃料生产的材料量。料流533通常是具有可接受的混合到发动机汽油中的特性的石脑油,且可以原样出售。料流523与料流413组合并用作图1中的料流4a。任选地,料流523被认为是废水流并作为废水流进行处理。
195.瓦斯油和重质产物(参见图1中的4d)被送到加氢裂化器,其将瓦斯油和重质产物转化为沸点较轻的产物(即包含第二附加煤油产物的混合物)。产物中的分子也比瓦斯油和重质产物中的分子更多地支化。来自加氢裂化器的第二附加煤油产物可直接用于混合成航空涡轮燃料。产物的其余部分也可用作最终产物。任选地,轻质产物可以用作低聚反应单元
的共同进料。在一个实例中,产物中沸点高于煤油的部分或全部材料被回收。在另一个实例中,使用非硫化催化剂,例如负载在无定形二氧化硅
‑
氧化铝催化剂上的还原贵金属,在固定床反应器中进行加氢裂化。负载在无定形二氧化硅
‑
氧化铝催化剂上的还原贵金属的一个实例是pt/sio2‑
al2o3。此类催化剂将具有高的金属与酸活性比以促进加氢异构化。
196.在本文所述方法的另一个实例中,加氢裂化器在比费
‑
托合成更低的压力下操作,以能够直接使用从低聚过程后未转化的产物中回收的氢气(例如参见实施例3)。通常,加氢裂化在约350℃至约400℃和>3mpa的压力下进行(例如,典型的轻度加氢裂化在约5
‑
8mpa的压力下和典型的重度加氢裂化在约10
‑
20mpa的压力下)。然而,如实施例3(见下文)中所证明的,如本文所述的加氢裂化使用<3mpa(例如,约2mpa)的压力,在约320℃的温度下进行。在一些实例中,可以在约320℃至约400℃,或约320℃至约380℃,或约320℃至约350℃的温度下操作本文所述的加氢裂化。在其他实例中,在约1mpa至约20mpa、或约1mpa至约15mpa、或约1mpa至约10mpa、约1mpa至约5mpa,或约1mpa至约3mpa,或约1mpa至约2mpa的压力下操作本文所述的加氢裂化。
197.以下是图1的步骤5中的加氢裂化的实例的更详细说明。图6更详细地描述了步骤5中的加氢裂化单元。加氢裂化器单元540的主要进料(例如,瓦斯油和重质产物)是料流302。任选地,有机液体料流412可以与进入料流414的部分或全部的料流412分开。未进入料流414的料流412的其余部分可以进入料流415。料流415也是加氢裂化器单元540的进料。通常仅当合成喷气燃料中的凝固点开始高于
‑
47℃的规格限制时才需要将料流415进料到加氢裂化器。在加氢裂化器单元540中,进料被加氢裂化和加氢异构化。在一个实例中,料流415没有暴露于加氢裂化器中的所有催化剂,而是作为中间床进料在中途引入。通过这样做,作为比料流302更轻沸点进料的料流415不太可能被加氢裂化并且更可能被加氢异构化。通过这样做,合成喷气燃料的收率比使用到加氢裂化器的单个液体进料点的常规操作提高。540中加氢裂化和加氢异构化的产物是料流541。
198.加氢裂化器单元540的氢气进料和氢气循环系统没有明确显示。加氢裂化技术的氢气回路是本领域已知的(例如,scherzer,j.;gruia,a.j.hydrocracking science and technology;crc press:boca raton,fl,1996)。加氢裂化器的氢气进料可从图4中的料流621或以本领域描述的其他方式获得,例如从本发明的步骤2中产生的合成气中分离。
199.产物料流541在分离器单元550中被分离成不同的馏分。任选地,来自加氢处理器即图1中的单元5.3的产物可以与料流541分离以减少分离步骤的数量。在通常通过蒸馏进行的分离器单元550中,材料被分离成轻质烃料流551、适用于合成喷气燃料共混的煤油系列烃料流552、瓦斯油料流553和常压渣油料流554。可以以料流553为零的方式选择分离。进行单元550中的分离主要是为了确保料流552适用于合成喷气燃料。任选地,重质产物料流554可以与进入料流555的部分或全部的料流554分开。未进入料流555的料流554的其余部分可以进入料流556。料流556再循环到加氢裂化器单元540。在一个实例中,料流556没有暴露于加氢裂化器中的所有催化剂,而是作为中间床进料在中途引入。
200.料流551可以进一步分离成产物馏分并作为丙烷、丁烷和石脑油出售。这种材料也可用于从油砂矿床中亚表面回收沥青。石脑油可用作发动机汽油的共混材料,或用作炼油厂进料或石化进料。石脑油可用作油砂衍生沥青的稀释剂,或用于诸如石蜡泡沫处理以回收沥青的工艺中。料流552用于半合成喷气燃料。料流553可以作为柴油燃料共混组分出售
并且通常具有等于或优于51的十六烷值、不含硫并且具有可接受的冷流特性。料流554可以作为润滑剂基础油共混组分、零硫燃料油或合成油出售。
201.送到加氢处理器的进料(例如煤油产物)被氢化以将烯烃和含氧分子基本上转化为链烷烃分子。将加氢处理后的产物分馏得到最终产物。煤油馏分被分馏以适合作为航空涡轮燃料。在一个实例中,使用非硫化的、负载在氧化铝或二氧化硅上的还原贱金属催化剂被用于在固定床反应器中进行加氢处理。负载在氧化铝上的还原贱金属催化剂的一个实例是还原的ni/al2o3催化剂。使用还原金属(例如,加氢处理)催化剂代替硫化贱金属(例如,加氢处理)催化剂可以避免向进料中添加硫,并且可以在比使用硫化贱金属(例如加氢处理)催化剂时更温和的条件下进行诸如加氢处理的反应。在一些实例中,加氢处理器在约80℃至约200℃,或约80℃至约180℃,或约80℃至约150℃的温度下操作。在其他实例中,加氢处理器在约180℃至约420℃,或约180℃至约380℃,或约260℃至约380℃的温度下操作。在一个实例中,加氢处理器在比费
‑
托合成更低的压力下运行,以能够直接使用从低聚过程后未转化的产物中回收的氢气。在其他实例中,加氢处理器在约0.5mpa至约20mpa、或约1mpa至约15mpa、或约1mpa至约10mpa、约1mpa至约5mpa,或约1mpa至约3mpa,或约1mpa至约2mpa的压力下操作。在如本文所述的加氢处理的另一个实例中,已发现使用模型进料(10%1
‑
己烯、5%甲苯、85%正辛烷)有可能在约80℃和约1mpa下使用还原ni/al2o3几乎完全转化烯烃。
202.来自本文所述方法的主要产物是满足合成航空涡轮燃料的规格要求的煤油系列材料,作为半合成喷气燃料共混组分或全合成喷气燃料。
203.以下是步骤5中的加氢处理单元的实例的更详细说明。图7更详细地描述了步骤5中的加氢处理单元。加氢处理器接收两种有机进料,一种来自低聚反应单元(即第一附加煤油产物),另一种来自费
‑
托合成后的分离(即煤油产物)。来自低聚反应单元的材料是料流522或料流532,这取决于料流522是否被进一步分离。来自费
‑
托合成后分离的材料是料流412或料流414,这取决于任何或所有这种材料是否在料流415中被送到加氢裂化单元。因此,加氢处理器可能仅接收来自低聚反应单元的进料。加氢处理器单元560的氢气进料和氢气循环系统没有明确显示。加氢处理器的氢气进料可从图4中的料流621或以本领域已知的其他方式获得,例如从本发明的步骤2中产生的合成气中分离。
204.加氢处理的产物是料流561。料流561中的产物基本上不含烯烃和含氧有机化合物。料流561中的产物主要由烷烃、环烷烃和芳烃组成,每种化合物类别的相对丰度取决于加氢处理器单元560的操作和加氢处理器的进料组成。当加氢处理器单元560的进料仅包含料流532时,可能所有料流561都适合用作全合成喷气燃料或半合成喷气燃料。当料流561的芳烃含量为8至25体积%时,料流561适合作为全合成喷气燃料,并且根据喷气燃料规格适当选择料流561的蒸馏范围。这里描述的方法提供了一种精炼方法,以从费
‑
托产物(即,包含液态烃的混合物)生产全合成喷气燃料,该方法仅使用两个转化步骤,低聚反应单元510和加氢处理器单元560。
205.当芳烃含量较低时,料流561适合作为半合成喷气燃料,并且根据喷气燃料规格适当选择料流532的蒸馏范围。本文描述的方法提供了一种精炼方法,以从费
‑
托产物(即,包含液态烃的混合物)生产半合成喷气燃料,该方法仅使用两个转化步骤,低聚反应单元510和加氢处理器单元560。
206.任选地,并且不管进入加氢处理器单元560的进料组成,料流561可以在单元550中分离,如图6所示。任选地,并且不管进入加氢处理器单元560的进料组成,料流561可以在单元570中进一步分离,如图8所示。单元570中料流561的分离便于根据其蒸馏范围生产对不同应用有用的产物。单元570中料流561的分离产生石脑油料流571、煤油料流572和瓦斯油料流573。料流571是石脑油系列产物。石脑油可用作发动机汽油的共混材料,或用作炼油厂进料或石化进料。石脑油可用作油砂衍生沥青的稀释剂,或用于诸如石蜡泡沫处理以回收沥青的工艺中。料流572用于半合成喷气燃料或用于全合成喷气燃料。料流573可以作为柴油燃料共混组分出售并且通常具有等于或优于51的十六烷值、不含硫并且具有可接受的冷流特性。
207.在一些实例中,可以以产生很少或不产生芳烃的方式操作低聚过程。这种类型的操作可用于增加半合成喷气燃料的产量(并延长催化剂循环寿命)。在一个具体实例中,芳烃含量为8%或更多,例如高达约60%,该料流可用于全合成喷气燃料生产,无论是其本身,还是作为与不含芳烃的其他煤油料流之一的共混物。优选地,全合成喷气燃料将具有8至25%的芳烃。在一些实例中,芳烃含量少于8%。在其他实例中,芳烃含量为约0
‑
1%。在该实例中,该料流可用作半合成喷气燃料的共混组分,其中一些预先批准的合成喷气燃料类别(异链烷烃煤油)具有<1%的芳烃。
208.在如本文所述的方法的实例中,整个方法产生足够量的h2以进行需要h2作为反应物/输入的每个方法步骤(例如,如图1至8中的任一个所示),而不必使用来自方法外部的来源(例如,甲烷重整器/甲烷重整等)的h2。在实例中,如本文所述的方法不需要来自外部来源的h2输入。
209.在如本文所述的方法的其他实例中,以高收率生产该方法的最终输出
‑
具有高沸点(例如,在140
°
至260
°
之间)和低凝固点(例如,<
‑
60℃)的喷气燃料。在一些实例中,与其他现有技术或标准技术相比,本文所述的方法产生更多的具有高沸点(例如,在140
°
至260
°
之间)和低凝固点(例如,<
‑
60℃)的喷气燃料。
210.在如本文所述的方法的其他实例中,不需要在费
‑
托单元(例如,图1中的单元3.1)和精炼单元(低聚反应(例如,图1中的单元5.1)、加氢裂化(例如,图1中的单元5.2)和加氢处理(例如图1中的单元5.3))之间使用气体压缩机以增加操作精炼单元的压力。在一些实例中,本文所述的方法使用来自费
‑
托单元(例如,图1中的单元3.1)的压力,以实施精炼单元(低聚反应(例如,图1中的单元5.1)、加氢裂化(例如,图1中的单元5.2)和加氢处理(例如图1中的单元5.3))中的方法。在一些实例中,本文所述的最终精炼步骤(低聚反应(例如,图1中的单元5.1)、加氢裂化(例如,图1中的单元5.2)和加氢处理(例如图1中的单元5.3))在与本文所述的费
‑
托合成相当的压力下进行:例如,在约2mpa或约2.5mpa的压力下;或在约1.5mpa至3mpa的范围内;或在约1.5mpa至约2.5mpa的范围内;或在约2mpa至约2.5mpa的范围内。这与例如标准加氢处理条件形成对比,标准加氢处理条件需要约8至10mpa的最小压力。
211.以下是对如本文所述的方法的最终精炼步骤的其他实例的更详细描述;特别是低聚反应(例如图1中的单元5.1)、加氢裂化(例如图1中的单元5.2)和加氢处理(例如图1中的单元5.3)。
212.实施例1
‑
半合成喷气燃料,50%共混物。根据例如图1中的低聚反应单元5.1,使用
固定床连续流动反应器来生产烯烃煤油系列产物。使用市售的非硫化h
‑
zsm
‑
5催化剂,在240
‑
280℃和2mpa的条件下,将碳数范围为c1‑
c8的轻链烷烃、烯烃和含氧化合物的混合物在催化剂上转化为包含煤油系列材料的产物。进料的碳数范围比现有技术描述的更宽。压力低于通常用于低聚反应的压力,并且是费
‑
托合成后的典型出口压力(例如,图1中的步骤3和4)。进料代表例如图1中的料流4b和进入图3中的单元510的料流411。进料中的烯烃浓度为24重量%。
213.在该实例中,反应器以单程方式运行。以丙烯为例,轻质烯烃的转化率>95%。对>140℃材料的质量选择性为29%,该材料可能适合包含在喷气燃料共混物中。如前所述(garwood,w.e.acs symp.ser.1983,218,383
‑
396),在h
‑
zsm
‑
5上的碳数分布由温度和压力的组合决定。可用于提高>140℃馏分的总收率的工程方法是将石脑油(c5‑
140℃)内部循环至低聚反应器。在本实例中没有这样做,因为它是已知的。
214.来自低聚反应的烯烃产物在还原的、非硫化的ni/al2o3催化剂上加氢处理至烯烃含量<1%。例如,加氢处理器是图1中的单元5.3。加氢处理过的产物被蒸馏成不同的沸点馏分,每个沸点馏分根据密度和凝固点起始进行表征(见表1)。制备的馏分数量是为了说明不同馏分对于可能包含在喷气燃料共混物中的适用性,并不旨在代表建议的分离策略。
215.表1.在240
‑
280℃和2mpa下对来自低聚转化的加氢处理产物的不同蒸馏馏分进行表征。
[0216][0217]
值得注意的是,在140
‑
260℃沸点范围内的所有蒸馏馏分都满足了jet a
‑
1的最大起始凝固点规格,即
‑
47℃。通常难以获得(例如,使用现有或标准技术)具有高沸点(例如,在140
°
至260
°
之间)和低凝固点(例如,<
‑
60℃)的产物。这支持了本文所述的方法能够使喷气燃料产率最大化。
[0218]
实施例2
‑
半合成喷气燃料,100%共混物。该方法有可能生产出能够配制全合成喷气燃料的材料,而不含石油源材料。对全合成喷气燃料的要求之一是它必须包含8
‑
25体积%的芳烃。在该实施例中,根据例如图1中的低聚反应单元5.1,使用固定床连续流动反应器来生产烯烃和芳族煤油系列产物。反应器、催化剂和进料与实施例1中的相似。进料是碳数范围为c1‑
c8的轻链烷烃、烯烃和含氧化合物的混合物,并且它含有25重量%的烯烃。进料在350
‑
380℃和2mpa下在催化剂上转化以生产包括煤油系列材料的产物。
[0219]
来自低聚反应器的烯烃和芳烃产物在还原的、非硫化的ni/al2o3催化剂上加氢处理至烯烃含量<1%,但在基本上不会将芳烃氢化成环烷烃的条件下。例如,加氢处理器是图1中的单元5.3。由于实施例1中解释的相同原因,加氢处理过的产物被蒸馏成不同的沸点馏分,每个沸点馏分根据密度和凝固点起始进行表征(表2)。
[0220]
表2.在350
‑
380℃和2mpa下对来自低聚转化的加氢处理产物的不同蒸馏馏分进行表征。
[0221][0222]
在140
‑
260℃沸点范围内的所有蒸馏馏分都满足了jet a
‑
1的最大起始凝固点规格,即
‑
47℃。表2中较高密度的蒸馏馏分(与表1相比)表明加氢处理产物中含有芳烃和环烷烃。通常,合成喷气燃料的芳烃含量来自化石燃料来源。相比之下,在较高温度下运行(例如,图1中的单元5.1)使该方法能够生成用于合成喷气燃料共混的煤油系列共混材料中通常不存在的化合物类别(即芳烃)。它还说明了例如图1中的单元5.1在不同操作模式下使用的灵活性。
[0223]
实施例3.本实施例说明了加氢裂化单元(例如图1中的单元5.2)在与费
‑
托合成相似的压力(即2mpa)下操作时的性能。使用pt/sio2‑
al2o3加氢裂化催化剂在320℃、2mpa、600m3/m3的h2/进料比和2h
‑1的液时空速下操作固定床连续流反应器。选择这些条件是为了证明在比加氢裂化常规遇到的条件更温和的条件下操作,并说明其在如本文所述的方法中应用的益处。
[0224]
加氢裂化器的进料是蜡,代表例如图1中的料流4d。当用沸点来描述时,蜡是一种常压渣油,初始沸点温度约为360℃,并且它含有碳数为c
24
及更重的正烷烃(石蜡)。反应器以单程方式运行。例如,通过将重质产物馏分循环到加氢裂化器来完全转化蜡的工程设计如图6所示。对制造合成喷气燃料感兴趣的是煤油与石脑油的选择性比。在本文采用的操作条件下,140
‑
260℃沸点范围内的烃与沸点<140℃的烃的质量比为1:1。
[0225]
加氢裂化产物分离不反映该方法的任何分离策略,并且出于与实施例1中所述相同的原因制备窄馏分。测定加氢裂化产物中每种窄沸点馏分的密度和凝固点起始(表3)。
[0226]
表3.对来自在320℃和2mpa下生产的加氢裂化产物的不同蒸馏馏分进行表征。
[0227][0228][0229]
在140
‑
250℃沸点范围内的窄蒸馏馏分具有满足了jet a
‑
1的最大起始凝固点规格的起始凝固点,即
‑
47℃。
[0230]
实施例4.使用实施例1和3中描述的产物与来自石油精炼厂的煤油系列产物共混半合成喷气燃料。来自炼油厂的煤油系列产物被重新蒸馏以去除低于150℃的沸点物质。剩余的石油衍生煤油进行了表征,密度为817.5kg/m3,起始凝固点为
‑
51℃。
[0231]
制备了半合成喷气燃料。该共混物由25体积%的表1中所示的加氢处理低聚反应产物的160
‑
260℃馏分、25体积%的表3中所示的加氢裂化产物的160
‑
240℃馏分和50体积%的石油衍生的煤油组成。考虑到前面列出的特性,可以使用更宽的沸点范围,但目的是证明可行的半合成喷气燃料可以通过如本文所述的方法生产。共混物没有被优化以最大化喷气燃料的收率。
[0232]
对以这种方式制备的半合成喷气燃料进行了表征,并与jet a
‑
1规范要求进行了比较(表4)。燃料实验室进行了表征,并在表征前向半合成喷气燃料中添加了1mg/lstadis 450。这是添加的用于喷气燃料使用规定的唯一常用添加剂。表4所列标准试验方法和规格为jet a
‑
1航空涡轮燃料评价所规定的方法和规格。
[0233]
除了表4中列出的那些规格外,还测量了半合成喷气燃料的冷流密度和粘度。在
‑
20℃时,密度为816kg/m3,粘度为3.75mpa.s(cp),动态粘度为4.58mm2/s(cst)。在
‑
20℃时的最大允许动态粘度为8mm2/s(cst)。所有测试参数均通过了astm d7566
‑
18a标准规范中描述的用于包含合成烃的航空涡轮燃料的半合成jet a
‑
1的详细要求。
[0234]
50.0℃的闪点温度(要求最低38℃)和790.7kg/m3的密度(要求最低775kg/m3)表明可以在半合成喷气燃料共混物中加入附加的低沸点材料。起始凝固点
‑
56.3℃(要求最高
‑
47℃),密度790.7kg/m3(要求最高840kg/m3),烟点23.0mm(要求最低18mm),最终沸点温度261.0℃(要求最高300℃),表明半合成喷气燃料共混物中可以容纳附加的更高沸点材料。
[0235]
表4.半合成喷气燃料表征和与jet a
‑
1规格的对比。
[0236][0237]
实施例5.本文所述的方法还能够生产全合成喷气燃料共混物。与半合成喷气燃料不同,全合成喷气燃料在喷气燃料共混物中没有石油源的共混物组分。
[0238]
使用实施例2和3中描述的产物共混全合成喷气燃料。该共混物由40重量%的表2中所示的加氢处理低聚反应产物的160
‑
260℃馏分和60重量%的表3所示的加氢裂化产物的160
‑
240℃馏分组成。对这种全合成喷气燃料进行了表征,并与jet a
‑
1规范要求进行了比较(表5)。燃料实验室进行了表征,并在表征前向全合成喷气燃料中添加了1mg/l stadis 450。
[0239]
除了表5中列出的那些规格外,还测量了全合成喷气燃料的冷流密度和粘度。在
‑
20℃时,密度为812kg/m3,粘度为3.27mpa.s(cp),动态粘度为4.02mm2/s(cst)。在
‑
20℃时的最大允许动态粘度为8mm2/s(cst)。对于所进行的那些分析,全合成喷气燃料通过了astm d7566
‑
18a标准规范中描述的用于包含合成烃的航空涡轮燃料的合成jet a
‑
1的要求。
[0240]
t
50
‑
t
10
=(197.8
‑
181.7)=16.1℃,其大于对全合成喷气燃料所要求的最小差异15℃。t
90
‑
t
10
=41.1℃,其大于对全合成喷气燃料所要求的最小差异40℃。47.0℃的闪点温度(要求最低38℃)和786.1kg/m3的密度(要求最低775kg/m3)表明可以在全合成喷气燃料共混物中容纳附加的低沸点材料。起始凝固点
‑
72.2℃(要求最高
‑
47℃),密度786.1kg/m3(要求最高840kg/m3),烟点24.0mm(要求最低18mm),最终沸点温度242.9℃(要求最高300℃),表明全合成喷气燃料共混物中可以容纳附加的更高沸点材料。
[0241]
表5.全合成喷气燃料表征和与jet a
‑
1规格的对比。
[0242][0243][0244]
本文描述的实施方案仅旨在作为示例。本领域技术人员可以对具体实施方案进行改变、修改和变化。权利要求的范围不应受本文阐述的具体实施方案的限制,而应以与整个
说明书一致的方式进行解释。
[0245]
本说明书中提及的所有出版物、专利和专利申请均表明本发明所属领域的技术人员的技术水平,并以好似每个单独的出版物、专利或专利申请被具体和单独地表明而参考引入的相同的程度通过引用并入本文。
[0246]
如此描述的本发明,显然可以以多种方式改变本发明。这些变型不应被视为脱离本发明的精神和范围,并且对于本领域技术人员来说将很明显的所有这些修改旨在包括在所附权利要求的范围内。
再多了解一些
本文用于企业家、创业者技术爱好者查询,结果仅供参考。