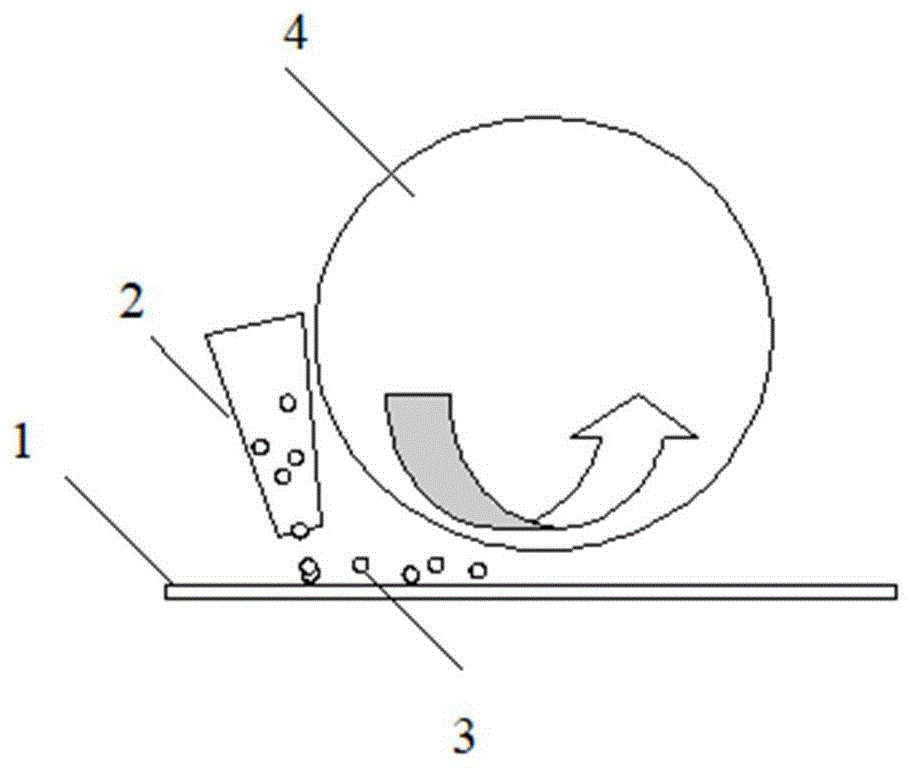
本发明属于轨道车辆技术领域,具体涉及一种轮轨增黏材料及其制备方法、使用方法。
背景技术:
轨道车辆无论牵引或制动都是通过在车轮和钢轨之间的黏着来实现的。但由于车轮和钢轨的接触界面处水膜、油膜等其它润滑膜的存在,常导致黏着力不足,车轮产生空转或滑行,从而使车轮踏面和轨道出现擦伤及剥离之类的损伤;而轮轨的擦伤将加剧车轮和钢轨的损伤,增加维护成本,引起噪声、振动,使车轴、轴承和钢轨等寿命降低,并使列车舒适度下降。
为了提高轮轨界面的黏着力,避免轮轨的擦伤,当车辆运行的黏着力不足时,就需要施加轮轨增黏材料。
传统的轮轨增黏材料为河沙或天然硅砂颗粒,粒径要求在0.5-2mm。但由于这类轮轨增黏材料形状不规则,硬度远高于轮轨材料,在提高黏着系数的同时会导致轮轨磨耗加剧、表面严重损伤等问题,反而增加铁路的维护成本。为此,现有技术提出对此轮轨增黏技术进行改进。
其中一种方法是,由压缩空气将粒径为0.3mm左右的二氧化硅、氧化铝等硬质陶瓷粒子直接喷洒到轮轨之间。通过坚硬的微粒子破坏接触面上的水膜等润滑膜,尤其是陶瓷微粒子被转动的车轮碾碎在轨道及车轮表面上,将轮轨表面挤压变形,增加了粗糙度,起到了提高黏着力的作用。
另一种方法是,制造一种含有硬质陶瓷粒子的研磨块,通过研磨块与车轮踏面摩擦,利用研磨块中的硬质粒子犁削车轮表面,增加轮面的粗糙度,从而起到增黏作用。
上述两种增黏方法虽一定程度降低对轮轨损伤,但依然是建立在增加轮轨表面粗糙度来提高黏着力的基础上的,同样是以轮轨表面发生犁削磨损为代价的,也会导致轮轨表面存在很多麻坑,促进疲劳裂纹的萌生,加剧了轨道和车轮的损伤和磨损程度,提高了车轮和轨道的维修成本。
为此,cn111153689a公开了一种用于轨道交通轮轨界面增黏的增黏颗粒及制备方法。其【0028】说明了通过喷雾造粒、烧结制备过程将微米级的二氧化硅粉末制备形状规则、粒径为0.5-1.5mm、具有较低硬度的团聚体颗粒,该团聚体颗粒单轴压缩破碎强度小于70mpa,可在增黏的同时显著降低对轮轨磨损和损伤程度。尽管该增黏方法中采取的团聚体颗粒硬度较低,但其原材料仍是sio2,仅仅是通过烧结制粒工艺将细小的sio2团聚成大尺寸颗粒,因此当这种团聚体颗粒在轮轨间运动并被碾压破碎时,与轮轨表面发生作用的实质仍是高硬度的sio2粒子,轨道和车轮的损伤和磨损程度并不会发生质的改变。
技术实现要素:
本发明的第一方面提供一种用于轮轨界面的增黏材料。该增黏材料不仅具有增黏作用,而且对轮轨的磨损和损伤更小,可延长轮轨使用寿命。
本发明所述的轮轨增黏材料为:
金属粉末,所述金属为铝、铜或铁中的一种或多种;或,
由金属粉末形成的研磨块;或,
由金属粉末与助剂形成的研磨块;
其中,所述金属粉末的粒径为0.05-2mm。
目前,本领域对于增黏材料的研究均是集中在陶瓷材料的改性方面,而本发明首次提出以特定的金属粉末或其制得的研磨块作为增黏材料,是从材料本质上进行改进。
相比其他金属,铝、铜或铁的延伸率更高(>10%),更易随着车轮运行而在轮轨表面被剪切挤压,进而发生塑性剪切流动。而通过其塑性剪切能耗和增加接触面积可增加轮轨接触面的摩擦力,从而更有效的增加轮轨接触面的黏着力。
本发明所述的增黏材料在增加黏着力的同时,还避免了如硬质粒子为了增黏而需要犁削轮轨表面的问题,因而减少了车轮和轨道表面由于犁削产生疲劳裂纹的风险,从而显著降低了车辆运行成本和维修时间。
而且,本发明所述增黏材料可依旧采用现有车辆增黏工装,不需要增加设备成本,节约了车辆的运行成本。
综上,本发明通过这一新的增黏材料及其增黏机制解决了现有增黏材料划伤车轮和轨道表面,进而降低车轮和轨道使用寿命的问题,实现了在不损伤轮轨表面的前提下,提高了轮轨间的黏着力的目的,保证了列车安全运行。而且,该增黏材料的实施基于现有车辆增黏工装,方法简单易行,有显著的经济和社会效益。
本发明所述的金属粉末的形状为等轴形。相比其他形状,等轴形的金属粉末在剪切挤压后更具有流动性。
所述增黏材料为单一金属粉末组成时,由于金属粉末的粒径较小,易被氧化,因此控制所述金属粉末中金属含量≥90%。例如,铜粉末中铜含量≥90%;铝粉末中铝含量≥90%;铁粉末中铁含量≥97%。
作为本发明的具体实施方式之一,对于两种金属粉末组成的增黏材料,其质量比优选为1:1时,可兼顾两种金属的优点,使用效果更好。如铝粉颗粒与铜粉颗粒按质量比1:1混合;铝粉颗粒与铁粉颗粒按质量比1:1混合;铜粉颗粒与铁粉颗粒按质量比1:1混合。
作为本发明的具体实施方式之一,对于三种金属粉末组成的增黏材料,须根据使用工况调整各金属含量比例,例如铜粉颗粒、铁粉颗粒和铝粉颗粒按质量比5:3:2混合,所得增黏材料的使用性能由于其他配比。
本发明所述的研磨块包括两种,具体选择可根据金属种类及使用工况条件而定。
本发明中,所述研磨块包括两种形成方式。一种是,仅由金属粉末形成的研磨块,其硬度应当满足hb≤80、抗压强度≥20mpa的要求方可满足使用要求。另一种是,由金属粉末与助剂形成的研磨块,该研磨块除了满足硬度、抗压强度的要求外,还对助剂的添加比例及种类有限制要求。
具体来讲,所述助剂为树脂和/或硬脂酸;所述助剂的添加比例为研磨块质量的5-20%,以保证研磨块具有合适的强度和硬度。
本发明的第二方面提供一种增黏材料的制备方法。
所述的增黏材料的制备方法须根据增黏材料的类型而确定。
具体而言,所述增黏材料为金属粉末,其可通过机械法或化学法获得;机械法为球磨法、研磨法、雾化法等。化学法为还原法、电解法、羟基法、化学置换法等。
所述增黏材料为研磨块,其可通过下述两种方式获得:
方法一:金属粉末通过粉末冶金工艺获得;所述粉末冶金工艺包括:压制成型、烧结成型;其中工艺条件为:压制压力10-30mpa,烧结温度500-1000℃。
方法二:以金属粉末、助剂为原料,通过固化工艺制得;所述固化工艺包括粉料混合、压制成型、固化成型;其工艺条件为:压制压力5-20mpa,固化温度100-300℃;所述金属粉末与助剂的质量比为8~9.5:2~0.5。
本发明所述的研磨块可由单一块组成,也可以是2-4块成分不同的多个块组合而成。
本发明第三方面提供了上述增黏材料的使用方法。本发明所述的增黏材料的使用方法根据增黏材料的类型分为两种:
对于增黏材料为金属粉末,可通过压缩空气或震动的方式将所述金属粉末洒落在轮轨界面。
对于增黏材料为研磨块,可利用车体的研磨块气缸的压力使研磨块与车轮发生摩擦磨损,进而使增黏材料黏附到车轮表面。
本发明针对增黏材料类型分别采用不同的实施方式,最终利用附着在轮轨表面的增黏材料在车轮转动过程中发生塑性变形流动而形成摩擦力,从而起到增加黏着力的作用,解决了现有的轮轨增黏技术难以平衡增黏效果好及降低轮轨表面损伤和磨损程度的问题。
本发明的有益效果如下:
本发明利用高纯度金属粉末作为增黏材料,基于金属粉末易变形、黏附力强、充填性好的优点,实现了在不损伤轮轨表面的前提下提高轮轨间的黏着力的目的,解决了现有的采用硬质粒子划伤车轮和轨道表面而降低车轮和轨道使用寿命的问题,可在轨道车辆运输等领域推广应用。
附图说明
图1为本发明实施例1-7中所述增黏材料通过压缩空气或震动方式撒落到轮轨表面上的示意图。
图2为在钢摩擦副上添加铜、铝、铁三种粉末所测试的摩擦系数情况。
图3为本发明实施例8-9中所述研磨块通过与车轮摩擦方式,将软金属粉末黏附到车轮表面上的示意图。
图中:1、轨道;2、粉末容器;3、粉末;4、车轮;5、研磨块。
具体实施方式
以下实施例用于说明本发明,但不用来限制本发明的范围。
本发明目的在于针对现有技术的不足,提供一种增黏效果好、减少轮轨磨损、提高轮轨使用寿命的增黏材料。
为了降低车轮和轨道由于硬质粒子犁削形成的微裂纹,本发明采用铝、铜、铁等软金属粉末颗粒作为增黏材料,由于软金属粉末颗粒硬度低于轮轨材料,在与轮轨的相互作用中,软金属粉末颗粒发生变形流动,在轮轨接触面上充填和挤压,并增加了接触面积,降低了局部应力集中,在形成黏着力的同时,减少了轮轨表面的损伤。
本发明这种利用金属粉末颗粒增黏方式,不必改变现有车辆增黏工装,没有增加设备成本,改善了车轮和轨道由于疲劳产生裂纹而失效的问题,降低了车辆的运行成本。该方法简单易行,有显著的经济和社会效益。
金属粉末作为增黏材料
实施例1
本实施例提供一种增黏材料及其使用方法。
所述增黏材料为铝粉颗粒,其为干状态,具有流动性。
所述铝粉颗粒中铝含量≥90%,颗粒尺寸为0.05-2mm。
所述增黏材料的使用方法如下:
如图1所示,所述增黏材料置于容器中,在容器的出口,增黏材料可以借助压缩空气或震动流动出来,散落到轮轨表面。
所述增黏材料散落到轮轨表面,随着车轮的转动,增黏材料被碾压附着到车轮表面和轨道表面,发生剪切变形,起到增加接触面黏着力的效果。
本发明充分利用上述增黏材料塑性变形流动强、容易黏附在轮轨表面的优点,通过增加表面微凸体间的接触面积和剪切变形而提高了摩擦力,达到增加轮轨黏着力的目的。
与采用二氧化硅、氧化铝等硬质陶瓷粒子增黏材料相比,这种以铝金属粉末颗粒作为增黏材料在使用过程中不存在硬质粒子划伤轮轨表面的问题,具有增黏效果好、减少轮轨磨损、提高轮轨使用寿命等优点。
实施例2
本实施例提供一种增黏材料及其使用方法,与实施例1的区别仅在于:所述增黏材料为纯铜粉末,颗粒尺寸为0.01-2mm。
实施例3
本实施例提供一种增黏材料及其使用方法,与实施例1的区别仅在于:所述增黏材料为铁粉颗粒;
所述铁粉颗粒为纯铁或微碳铁粉末,颗粒尺寸为0.02-2mm。
实施例4
本实施例提供一种增黏材料及其使用方法,与实施例1的区别仅在于:所述增黏材料为铝粉颗粒与铜粉颗粒按质量比1:1混合得到增黏材料。
实施例5
本实施例提供一种增黏材料及其使用方法,与实施例1的区别仅在于:所述增黏材料为铝粉颗粒与铁粉颗粒按质量比1:1混合得到增黏材料。
实施例6
本实施例提供一种增黏材料及其使用方法,与实施例1的区别仅在于:所述增黏材料为铜粉颗粒与铁粉颗粒按质量比1:1混合得到增黏材料。
实施例7
本实施例提供一种增黏材料及其使用方法,与实施例1的区别仅在于:所述增黏材料为铜粉颗粒、铁粉颗粒和铝粉颗粒按质量比5:3:2混合得到增黏材料。
图2为在钢摩擦副上添加铜、铝、铁三种粉末所测试的摩擦系数情况。由图可见,三种粉末的添加都起到增加摩擦系数的作用。
研磨块增黏材料
实施例8
本实施例提供一种增黏材料及其制备方法、使用方法。
所述增黏材料为以铝粉颗粒为原料,采用粉末冶金工艺方法制成研磨块。
所述粉末冶金工艺方法包括压制成型、烧结成型。
其中具体操作条件为:混合10min,压制10mpa,保压1min,烧结500℃,保温1h。
所述增黏材料的使用方法,如图3所示:
所述的研磨块可以固定在轨道车辆已有的研磨子支架上,利用气缸的作用力,推动研磨块与转动的车轮表面接触摩擦,研磨块容易发生磨损而使软金属黏附到车轮表面。
实施例9
本实施例提供一种增黏材料及其制备方法、使用方法。
所述增黏材料为以铝粉颗粒、树脂类粘合剂为原料,采用固化工艺方法制成研磨块。
所述固化工艺包括粉料混合、压制成型、固化成型。
其具体操作条件为:混合10min,压制5mpa,保压1min,固化200℃,固化时间10h。
所述增黏材料的使用方法,如图3所示:
所述的研磨块可以固定在轨道车辆已有的研磨子支架上,利用气缸的作用力,推动研磨块与转动的车轮表面接触摩擦,研磨块容易发生磨损而使软金属黏附到车轮表面。
虽然,上文中已经用一般性说明及具体实施方案对本发明作了详尽的描述,但在本发明基础上,可以对之作一些修改或改进,这对本领域技术人员而言是显而易见的。因此,在不偏离本发明精神的基础上所做的这些修改或改进,均属于本发明要求保护的范围。
本文用于企业家、创业者技术爱好者查询,结果仅供参考。