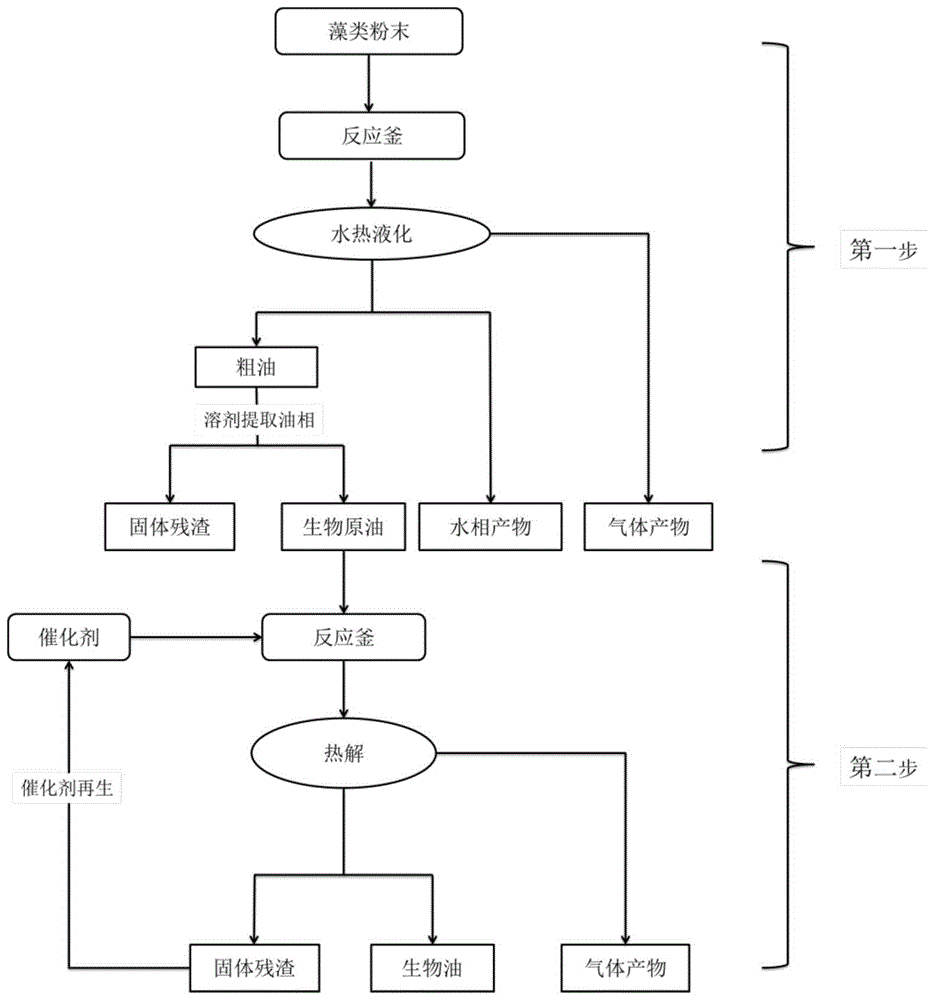
本发明涉及一种制备生物原油的方法,属于生物燃料制备技术领域。
背景技术:
工业废水、生活污水的超标排放以及化肥、农药的滥用,导致水体富营养化问题越来越严重,因此藻类植物大量繁殖。过度繁殖的藻类生物消耗水中大量氧气,不仅致使水中其他生物因缺氧而难以生存,而且使堆积在水下的有机物质和浮游生物在缺氧环境中分解产生有害气体和毒素,危害其他生物。
水热液化是一种有效处理藻类生物质的技术,是在以水为溶剂的条件下,将生物质转化为生物原油的热化学转化过程,反应温度为180-500℃,反应压强为5-25mpa。水热液化是适于水生生物质的炼制技术,该技术与热解技术相比,可以直接利用湿生物质进行转化,有效节约预处理成本。水热液化原油的高位热值高达30-38mj/kg,是石油热值的60-95%,因此生物原油是一种具有潜力的化石能源替代品。然而,传统的水热液化技术产生的生物原油在储存和利用过程中还存在一些问题亟待解决,比如:生物原油含氧量较高,从而导致储存过程中原油品质不稳定,另外,生物原油酸性强、黏度大,在储存和管道运输方面带来困难。因此,目前越来越多研究集中在水热液化-催化转化过程。
中国专利cn103059895a公开了一种条浒苔水热液化制备生物油的方法,利用k2co3作为催化剂,对藻类进行水热液化过程催化。
中国专利cn1102002381a公开了一种藻类生物质直接催化液化法制备生物油的方法,将藻类植物置于酸溶液或者碱溶液中浸泡,之后利用改性天然丝光沸石催化剂对水热液化过程催化。
中国专利cn106170534a公开了一种催化剂辅助水热转化生物质为生物原油的方法,利用离子液体作为催化剂制备水热液化生物原油,得到的生物原油产率在40-78%之间,生物原油含碳量在60-80%之间。
从现有的技术和工艺来看,催化水热液化的研究主要是集中对水热液化过程添加催化剂,调控水热反应路径,从而得到高品质生物原油。常用的催化剂有均相催化剂,如金属盐(na2co3、rb2co3)、强碱(ca(oh)2、koh)、强酸(hcl、h2so4)等,还有非均相催化剂,如pd/como、pt/ni、ru/ni/sio2或ni/hzsm-5等。最常用的催化剂为均相催化剂,但是水热液化反应后的液相废水污染严重,不利于排放,后续处理成本较高。负载型非均相催化剂表现出优于负载物或被负载物单独用于催化剂时的催化效果,在提升原油产量和改善原油品质方面起到一定的积极作用。但是常用的负载物为贵金属,成本较高,不利于工业化生产。除此之外,在对水热液化生物原油进行后续处理的研究中,一般是在氢气的气氛中,加入ni-mo等催化剂,实现原油的加氢脱氮反应。然而,目前几乎没有对水热液化产生的生物原油在非氢气氛中进行后续催化处理的研究。
技术实现要素:
本发明的目的在于提供一种催化转化法制备生物原油的方法,利用制备方法简单、回收再生率高、水热稳定性好的催化剂,获取高产量、高品质生物原油。
本发明的目的是通过以下技术方案实现的:
一种催化转化法制备生物原油的方法,包括:步骤1),将生物质原料进行水热液化,得到生物原油;步骤2),采用负载第ⅷ族金属的分子筛催化剂催化热解转化生物原油,得到提质的生物原油。
其中,步骤1)所述生物质水热液化可以按照常规方法进行,通常是将生物质原料加入适量水,加入反应釜中进行水热液化,反应完成后获得生物原油、固体残渣、气体和液相四种产物,并经过过滤、萃取、蒸馏、干燥等操作得到生物原油。
步骤1)所述水热液化初始压强通常为0mpa-8mpa,反应温度通常为200-500℃,反应保温时间通常为10min-200min,升温速率为5℃/min-50℃/min。优选反应温度为250-350℃,保温时间为60-120min。
所述生物质原料可以是藻类、纤维素、市政污泥、生活垃圾、餐厨垃圾、畜禽粪便、农作物秸秆和林业废弃物等,优选藻类,例如微拟球藻、栅藻、螺旋藻、蓝藻、念珠藻、硅藻和红藻等微藻类生物质中的一种或一种以上等等。
其中,步骤2)所述对生物原油催化热解转化步骤进一步包括:将所述生物原油进行干燥预处理除去水分后,与所述负载第ⅷ族金属的分子筛催化剂一同置于反应釜内进行高温催化热解,反应条件通常为反应温度为200℃-700℃,反应停留时间为10min-200min,优选反应温度280℃-350℃,反应停留时间60min-120min,反应结束后,利用有机溶剂萃取回收生物原油,将固体残渣高温煅烧,再生催化剂。
步骤2)中,所述分子筛选自hzsm-22、hzsm-5、h-beta、mcm-22、sapo-11等微孔沸石分子筛中的一种或几种。
步骤2)中,所述第ⅷ族金属优选铁,以催化剂总质量计,金属的负载量为1-20wt%,优选5-15wt%。催化剂加入量为生物原油质量的1-30wt%,优选5-10wt%。
步骤2)中,所述负载第ⅷ族金属的分子筛催化剂的制备方法包括:首先将酸性分子筛与第ⅷ族金属的盐溶液混合,混合液置于功率为500-900w,优选600-700w的微波下加热5-20min,然后洗涤固体残渣,烘干、焙烧。其中烘干条件为温度100℃-150℃,时间5-15h,最后置于马弗炉中焙烧,焙烧温度400℃-700℃,焙烧时间1h-6h,优选焙烧温度450-550℃,焙烧时间2h-4h。
步骤2)中,所述第ⅷ族金属的盐溶液为硝酸铁、硫酸铁、氯化铁中的一种。
步骤1)和步骤2)中,对得到的生物原油进行萃取分离,所述萃取溶剂为丙酮、乙醇、甲醇、二氯甲烷、乙醚、乙酸乙酯、正己烷、戊烷、二甲苯、三氯甲烷等有机溶剂中的一种。
步骤1)和步骤2)中,还通入惰性气体作为载气保证反应釜内绝氧,载气为n2或he中的一种,气体流量为150ml/min-300ml/min。
步骤1)和步骤2)中,反应器为间歇式或连续式高温高压反应釜。
本发明利用微波-浸渍法将第ⅷ族金属负载至分子筛上。与常规加热方法制备负载fe分子筛催化剂相比,微波法具有以下优势:(1)加热均匀、效率高、速度快,温度和功率可控,减少副反应。(2)金属分散性好。发明人发现,微波法得到的催化剂孔径和孔容均大于加热法,由此可以证明微波法有利于金属进入其孔道内部,增加其负载量和活性位点,从而有利于反应物和中间产物进出孔道内部,使其在分子筛内外表面与活性位点充分反应,可以抑制积碳的生成,提高催化剂的寿命和重复使用率。
因此,本发明采用微波的方法制备催化剂,可以促进金属离子的交换及负载,增加金属离子的负载量,同时促进金属离子在分子筛孔道结构中的均匀分散,保证反应物与分子筛酸性位点及金属活性位点的充分接触,有利于催化反应的进行,对催化反应及产物质量提升作用明显。
附图说明
图1为本发明实施例的工艺流程图。
具体实施方式
下面结合流程图对本发明作进一步说明。本实施例是用于说明而不限于本申请的发明的范围。
实施例中,利用元素分析仪测定生物原油中的碳、氢、氮元素含量,利用差值法计算氧元素含量;通过dulong公式计算生物原油的热值;利用气相色谱质谱联用仪测定生物原油中烃类物质的含量。
实例1
(1)将hzsm-5分子筛与硝酸铁溶液混合,配置金属负载比为10wt%,在500w*10%微波炉低功率条件下加热10min,用去离子水清洗催化剂,然后经120℃烘干,并在500℃马弗炉中焙烧3h,催化剂制备完成。
(2)将250g干料螺旋藻粉加入反应釜中,密封好反应釜,通入氮气,使反应釜内压强达到初始压强,搅拌器转速为800rmp,压强在10min内稳定不变,则认为反应釜气密性良好。
(3)将反应釜温度加热至280℃,升温速率5℃/min,反应停留时间120min。
(4)待反应釜冷却至室温后,收集反应后的气体产物,水相产物用玻璃杯收集,剩余物用丙酮萃取,然后过滤,不溶于丙酮的部分为固体残渣,可溶于丙酮的部分为生物原油。
(5)将生物原油倒入分液漏斗中静置分层,最下层为水,上层液相倒入抽提瓶中进行蒸馏,回收丙酮后,生物原油再放入干燥箱中干燥12h,得到干燥后的生物原油。
(6)将步骤(5)得到的生物原油与5wt%的催化剂混合后,放入反应釜中,通入氮气10min,保证釜内绝氧,然后将反应釜升温至280℃,反应180min。
(7)待反应结束后,利用丙酮萃取反应剩余物,不溶于丙酮的固体残渣为焦炭和催化剂,可溶于丙酮的部分为高品质生物原油。
(8)将固体残渣置于575℃高温下煅烧8h,再生、回收催化剂。
(9)采用提质的生物原油与未提质的生物原油质量的比值计算生物原油产率;高品质生物原油的组成、热值等指标见表1。
(10)与未催化热解前的生物原油相比,制备的高品质生物原油氧含量降低了24.5%,热值增加了16.0%,烃类物质含量提高了1.29倍。
(11)与传统加热法制备的催化剂相比,微波制备法制备的催化剂催化生物原油产率提高了3.95%,碳含量提高了6.87%,氧含量降低了9.21%,热值提高了10.33%,烃类物质含量提高了1.42倍,说明微波法制备的催化剂有效提高生物原油产率和热值,并抑制积碳发生。
(12)回收、重生微波法制备的催化剂,重复使用5次,热值降低率4.18%,说明催化剂结构稳定,活性位点损失率低。
实例2
(1)将hzsm-5分子筛与硝酸铁溶液混合,配置金属负载比为10wt%,在700w*10%微波炉低功率条件下加热10min,用去离子水清洗催化剂,然后烘干后在500℃马弗炉中焙烧3h,催化剂制备完成。
(2)将250g干料螺旋藻粉加入反应釜中,密封好反应釜,通入氮气,使反应釜内压强达到初始压强,搅拌器转速为800rmp,压强在10min内稳定不变,则认为反应釜气密性良好。
(3)将反应釜温度加热至280℃,升温速率5℃/min,反应停留时间120min。
(4)待反应釜冷却至室温后,收集反应后的气体产物,水相产物用玻璃杯收集,剩余物用丙酮萃取,然后过滤,不溶于丙酮的部分为固体残渣,可溶于丙酮的部分为生物原油。
(5)将生物原油倒入分液漏斗中静置分层,最下层为水,上层液相倒入抽提瓶中进行蒸馏,回收丙酮后,生物原油再放入干燥箱中干燥12h,得到干燥后的生物原油。
(6)将步骤(5)得到的生物原油与8wt%的催化剂混合后,放入反应釜中,通入氮气10min,保证釜内绝氧,然后将反应釜升温至320℃,反应180min。
(7)待反应结束后,利用丙酮萃取反应剩余物,不溶于丙酮的固体残渣为焦炭和催化剂,可溶于丙酮的部分为高品质生物原油。
(8)将固体残渣置于575℃高温下煅烧8h,再生、回收催化剂。
(9)采用提质的生物原油与未提质的生物原油质量的比值计算生物原油产率;高品质生物原油的组成、热值等指标见表1。
(10)与未催化热解前的生物原油相比,制备的高品质生物原油氧含量降低了75.2%,热值增加了30%,烃类物质含量提高了3.5倍。
(11)与传统加热法制备的催化剂相比,微波制备法制备的催化剂催化生物原油产率提高了9.71%,碳含量提高了12.83%,氧含量降低了11.05%,热值提高了15.97%,烃类物质含量提高了1.75倍,说明微波法制备的催化剂有效提高生物原油产率和热值,并抑制积碳发生。
(12)回收、重生微波法制备的催化剂,重复使用5次后,热值降低率为3.66%,说明催化剂结构稳定,活性位点损失率低。
实例3
(1)将hzsm-5分子筛与硝酸铁溶液混合,配置金属负载比为10wt%,在900w*10%微波炉低功率条件下加热10min,用去离子水清洗催化剂,然后烘干后在500℃马弗炉中焙烧3h,催化剂制备完成。
(2)将250g干料螺旋藻粉加入反应釜中,密封好反应釜,通入氮气,使反应釜内压强达到初始压强,搅拌器转速为800rmp,压强在10min内稳定不变,则认为反应釜气密性良好。
(3)将反应釜温度加热至280℃,升温速率5℃/min,反应停留时间120min。
(4)待反应釜冷却至室温后,收集反应后的气体产物,水相产物用玻璃杯收集,剩余物用丙酮萃取,然后过滤,不溶于丙酮的部分为固体残渣,可溶于丙酮的部分为生物原油。
(5)将生物原油倒入分液漏斗中静置分层,最下层为水,上层液相倒入抽提瓶中进行蒸馏,回收丙酮后,生物原油再放入干燥箱中干燥12h,得到干燥后的生物原油。
(6)将步骤(5)得到的生物原油与10wt%的催化剂混合后,放入反应釜中,通入氮气10min,保证釜内绝氧,然后将反应釜升温至280℃,反应120min。
(7)待反应结束后,利用丙酮萃取反应剩余物,不溶于丙酮的固体残渣为焦炭和催化剂,可溶于丙酮的部分为高品质生物原油。
(8)将固体残渣置于575℃高温下煅烧8h,再生、回收催化剂。
(9)采用提质的生物原油与未提质的生物原油质量的比值计算生物原油产率;高品质生物原油的组成、热值等指标见表1。
(10)与未催化热解前的生物原油相比,制备的高品质生物原油氧含量降低了41.2%,热值增加了24.3%,烃类物质含量提高了1.52倍。
(11)与传统加热法制备的催化剂相比,微波制备法制备的催化剂催化生物原油产率提高了5.55%,碳含量提高了9.23%,氧含量降低了8.90%,热值提高了13.09%,烃类物质含量提高了1.46倍,说明微波法制备的催化剂有效提高生物原油产率和热值,并抑制积碳发生。
(12)回收、重生微波法制备的催化剂,重复使用5次,热值降低率为5.37%,说明催化剂结构稳定,活性位点损失率低。
实例4
(1)将hzsm-5分子筛与溶液混合,配置金属负载比为10wt%,在900w*10%微波炉低功率条件下加热10min,用去离子水清洗催化剂,然后烘干后在500℃马弗炉中焙烧3h,催化剂制备完成。
(2)将250g干料螺旋藻粉加入反应釜中,密封好反应釜,通入氮气,使反应釜内压强达到初始压强,搅拌器转速为800rmp,压强在10min内稳定不变,则认为反应釜气密性良好。
(3)将反应釜温度加热至280℃,升温速率5℃/min,反应停留时间120min。
(4)待反应釜冷却至室温后,收集反应后的气体产物,水相产物用玻璃杯收集,剩余物用丙酮萃取,然后过滤,不溶于丙酮的部分为固体残渣,可溶于丙酮的部分为生物原油。
(5)将生物原油倒入分液漏斗中静置分层,最下层为水,上层液相倒入抽提瓶中进行蒸馏,回收丙酮后,生物原油再放入干燥箱中干燥12h,得到干燥后的生物原油。
(6)将步骤(5)得到的生物原油与8wt%的催化剂混合后,放入反应釜中,通入氮气10min,保证釜内绝氧,然后将反应釜升温至320℃,反应120min。
(7)待反应结束后,利用丙酮萃取反应剩余物,不溶于丙酮的固体残渣为焦炭和催化剂,可溶于丙酮的部分为高品质生物原油。
(8)将固体残渣置于575℃高温下煅烧8h,再生、回收催化剂。
(9)采用提质的生物原油与未提质的生物原油质量的比值计算生物原油产率;高品质生物原油的组成、热值等指标见表1。
(10)与未催化热解前的生物原油相比,制备的高品质生物原油氧含量降低了28.5%,热值增加了大约22.0%,烃类物质含量提高了2.5倍。
(11)与传统加热法制备的催化剂相比,微波制备法制备的催化剂催化生物原油产率提高了16.23%,碳含量提高了21.90%,氧含量降低了17.67,热值提高了22.78%,烃类物质含量提高了2.45倍,说明微波法制备的催化剂有效提高生物原油产率和热值,并抑制积碳发生。
(12)回收、重生微波法制备的催化剂,重复使用5次,热值降低率为2.54%,说明催化剂结构稳定,活性位点损失率低。
表1.高品质生物原油理化特性
上述实例仅为说明本发明的操作流程,但是本申请的保护范围并不局限于此。任何在本发明的技术上所做的改动、变化,都应涵盖在本发明的保护范围之内。
本文用于企业家、创业者技术爱好者查询,结果仅供参考。