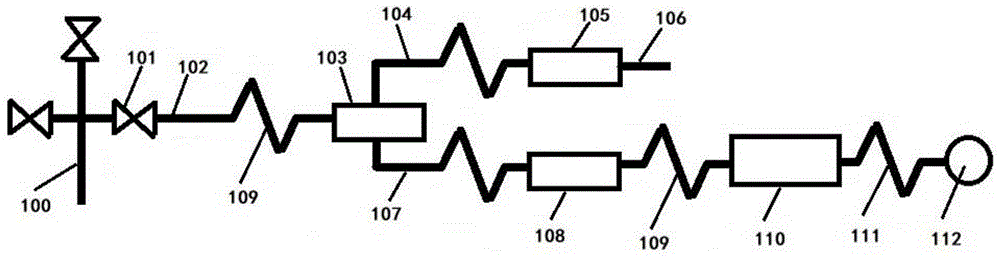
本发明涉及天然气生产领域,尤其是涉及一种分布式天然气脱硫方法。
背景技术:
国家标准《天然气gb17820-2018》规定天然气中的硫化氢浓度应≦20mg/m3,但是国内天然气井(简称气井)产出的天然气中硫化氢浓度往往高于20mg/m3。以普光气田为例,其气井所产天然气中的硫化氢浓度一般高达100g/m3(即100000mg/m3)以上,有的气井高达260g/m3。
由本领域公知知识可知:硫化氢是一种急性剧毒恶臭气体,溶于水形成氢硫酸;吸入少量高浓度硫化氢可于短时间内致命,低浓度硫化氢对眼、呼吸系统及中枢神经都有影响;普光气田曾因井喷失控导致200多人死亡。
因此,国内气井的天然气一般采用以下脱硫(又称除硫)方法进行处理、生产。
一、集中式脱硫法:该方法可进一步分为两种。其中一种如图1所示,可概述为:气井100产出的天然气(一般含一定量的水、油、化学剂等),经过阀门101、集气管线102进入集气站103分离为天然气、采出液;集气站103所分离出的天然气经过站间管线104进入天然气净化处理厂105进行脱硫、降露点等处理,达标后进入外输管线106;集气站103所分离出的采出液经过采出液管线107进入污水处理厂108进行油水分离、污水絮凝等处理,达标的污水再经过污水管线109进入回注站110增压,然后再经过注水管线110、注水井112回注地层中。
该方法的另一种如图2所示,可概述为:气井100产出的天然气,经过阀门101、集气管线102进入集气站103分离为天然气、采出液;集气站103所分离出的天然气经过站间管线104进入天然气净化处理厂105进行脱硫、降露点等净化处理,达标后进入外输管线106;集气站103所分离出的采出液先通过装车管线200装入汽车罐车201中、再用汽车罐车201运至污水处理厂108并通过卸车管线202进入污水处理厂108进行油水分离、污水絮凝等处理,达标的污水再经过污水管线109进入回注站110增压,然后再经过注水管线110、注水井112回注地层中。
由本领域公知知识可知:以延长气田为例,该气田建有多个集气站、1个污水处理厂,集气站至污水处理厂的运距一般为50~150公里,最远的运距甚至超过200公里;1个集气站一般汇集5~10口气井所产的天然气,平均1口井日产采出液不到0.方吨/日,1个集气站平均日产采出液量不到2方/日,因此用汽车罐车将采出液拉运至污水处理厂的方式显然比用采出液管线输送的方式更经济;目前,延长气田均采用汽车罐车拉运的方法,将集气站所产采出液拉运至污水处理厂集中处理。
该方法存在以下缺陷:
1、该方法使整个气田地面生产系统采用抗硫设计,会导致气田(或区块)地面生产系统的固定投资、运行费用与采气成本居高不下甚至成倍增加,进而导致气田(或区块)的开发效益大幅降低,甚至使国内众多储量丰富的低渗气田(或区块)、页岩气田失去工业开发价值。
由本领域公知知识可知:如图1、图2所示,采用集中式脱硫法时,天然气所含的硫化氢只能在天然气净化处理厂105进行脱除,而在阀门101、集气管线102、集气站103、站间管线104中的天然气则均含硫化氢,采出液管线107中的污水同样含硫化氢。
由本领域公知知识可知:根据《石油天然气工业-油气开采中用于含硫化氢环境的材料》gb/t20972、《天然气地面设施抗硫化物应力开裂和抗应力腐蚀开裂的金属材料要求》sy/t0599、《钢制化工容器材料选用规定》hg/t20581-2011等标准规定,国内各气田对其地面生产系统的基本设计要求为:当集气管线102内硫化氢含量>13ppm时,应采用抗硫设计;当站间管线104内硫化氢含量>55ppm时,应采用抗硫设计;当站场设备(包括但不限于集气站103、采出液管线107)内硫化氢含量>55ppm,应采用抗硫设计。
由本领域公知知识可知:采用抗硫设计后,管线设备的材质必须采用抗硫的特种钢或不锈钢,因此采用抗硫设计的地面生产系统造价、运行成本远高于常规设计,通常一个中型气田(或区块)抗硫地面生产系统采用抗硫设计后的固定投资高达几十亿元;如图1、图2所示,集气管线102最低设计压力6.4mpa,管径一般为dn50~dn150,长度可达十几公里,其采用抗硫设计的固定投资极其巨大;集气站103内设置多种最低设计压力6.4mpa的容器、设备,采用常规设计的固定投资一般1000万元左右,但采用抗硫设计后的固定投资则高达数千万元;站间管线104最低设计压力6.4mpa,管径一般为dn100~dn300,一般长达10~50公里,其采用抗硫设计后的固定投资极其高昂。
由本领域公知知识可知:特种钢、不锈钢的售价远高于普通钢。
2、该方法不能使含硫气藏区块、含硫气井利用现有已经建成运行的、常规设计的地面生产系统进行生产,不能提高含硫气藏、不含硫气藏分采的开发效益;因此,该方法不能用于同时拥有含硫气井(或含硫气层)、不含硫气井(或不含硫气层)的相同气田(或区块),不能用于对含硫气层、不含硫气层进行分采的气井,更不能降低含硫气藏的开采成本。
由本领域公知知识可知:国内气田(或区块)普遍同时拥有含硫气井、不含硫气井,为提高其开发效益、降低开采成本一般采用分采方法开发,并优先用常规设计的地面生产系统开发不含硫气层;国内开发不含硫气层用的地面生产系统均不采用抗硫设计,主要用普通钢材建成,可大幅降低不含硫气层的开采成本;开发含硫气层用的地面生产系统均采用抗硫设计,主要用抗硫的特种钢或不锈钢建成,将其用于不含硫气井生产将大幅增加不含硫气层的开采成本。
由本领域公知知识计算可知:含硫气井所产天然气进入现有已经建成运行的、常规设计的地面生产系统后,将导致该地面生产系统含硫超标,进而导致该地面生产系统出现硫化氢特有的腐蚀、氢脆等严重问题,严重时甚至导致该地面生产系统炸裂报废、出现重大人员伤亡事故。
以大牛地气田为例。
该气田属于低渗气田,由地理位置相同的上部、下部两大气藏组成;其中,上部气藏为不含硫气层,所建气井产出的天然气中硫化氢含量<13ppm,一般视为不含硫气井;下部奥陶系气藏(又称下古气田)属于含硫气层,所建气井属于含硫气井,气井所产天然气中硫化氢含量一般为100~3000ppm,部分气井硫化氢含量甚至高达3000ppm以上。
为提高开发效益、降低开采成本,该气田对含硫气层、不含硫气层采用分别开采的方法开发,优先开采硫化氢含量<13ppm的上部气藏,并优先建成了只适用于硫化氢含量<13ppm的地面生产系统,包括70余座集气站(管辖3~50口气井不等)、1600余口不含硫气井以及相应的集气管线、站间管线等。
目前,该气田已建1600余口不含硫气井,其中大部分气井已经开采十余年,有的气井已开采15年以上,单井产气能力普遍较低;已建30余口含硫气井,仅有几口用于开展生产试验,其余气井均未生产,单井产气能力普遍很高。
由本领域公知知识可知:该气田的含硫气井利用现有已建地面生产系统进行生产时,含硫气井所产天然气先与不含硫气井所产天然气在集气站内混合,然后进入站间管线等;计算表明:按相同产气量计,1口硫化氢含量100ppm的含硫气井所产天然气与6口硫化氢含量0ppm的不含硫气井所产天然气混合均匀后,其硫化氢含量>13ppm,将导致该气田集气站、站间管线等现有优先建成的地面生产系统含硫超标;同样的计算表明:1口硫化氢含量700ppm的含硫气井所产天然气与52口硫化氢含量0ppm的不含硫气井所产天然气混合均匀后,其硫化氢含量>13ppm,将导致该气田集气站、站间管线等现有优先建成的地面生产系统含硫超标;进一步计算表明:7口硫化氢含量3000ppm的含硫气井所产天然气与52口硫化氢含量0ppm的不含硫气井所产天然气混合均匀后,其硫化氢含量>13ppm,将导致该气田全部现有优先建成的地面生产系统含硫超标;因此,大牛地气田的含硫气井不能利用现有已经建成运行的、常规设计的地面生产系统进行生产。
由本领域公知知识可知:集中式脱硫法虽然能够解决大牛地气田含硫气层、气井的开发生产问题,但却需要花费几十亿元另外建设一整套抗硫地面生产系统,使该气田在相同的区域同时拥有两套地面生产系统,从而使该气田的含硫气藏、不含硫气藏分层开采失去意义、开发成本大幅增加,甚至使该气田的含硫气藏失去工业开发价值。
由本领域公知知识可知:受地质条件制约,国内低渗气田的开发效益普遍很差;目前大牛地气田利用普通钢材建成的地面生产系统开发不含硫气藏区块的成本已经很高,经济效益低微;若该气田另行建设抗硫地面生产系统开发其含硫气藏区块,将导致含硫气藏区块的开发效益为负值,从而失去开发价值。
3、该方法需要将整个地面生产系统全部建成后才能开井生产天然气,导致气田开发进度缓慢、开发效益降低。
由本领域公知知识可知:不含硫气井能够单井生产,所产天然气可以不进入地面生产系统,可在井场直接制成cng、lng外运外销;含硫气井必须进入地面生产系统进行脱硫等处理;目前,国内没有含硫气井不进地面生产系统进行脱硫处理,或在井场直接制成cng、lng外运外销的成功先例。
4、该方法中如图2所示的用汽车罐车201将采出液运至污水处理厂108的方式,不能用于含硫气井。
由本领域公知知识可知:天然气生产要求和环保要求均明确规定采出液必须密闭输送、处理,禁止让采出液中的硫化氢进入大气环境;含硫气井的采出液极易挥发出大量硫化氢;用汽车罐车201装卸运输含硫化氢的采出液时,必然向空气中散发大量硫化氢,轻则危害人身健康,严重时甚至造成人员伤亡事故。
二、井口加注氧化型脱硫剂脱硫法:该方法是将常温常压下呈液态的氧化型除硫剂加入井筒或井口管线内,让氧化型除硫剂将天然气中的硫化氢氧化成单质硫,从而解决硫化氢特有的腐蚀、氢脆问题。该方法存在以下缺陷:
1、该方法会在天然气井筒或井口管线内生成固形硫磺微粒,进而形成硫垢,堵塞井筒、管线。
由本领域公知知识可知:单质硫即硫磺,不溶于水,在天然气管线内不与钢材产生化学反应,不产生氢脆问题。
以大牛地气田为例。
该气田开展的现场试验表明:所试验的氧化型除硫剂ph值<2,呈强酸性;所试验的含硫气井产出的天然气硫化氢含量>400ppm,产出的采出液呈酸性,油管出口加注该氧化型除硫剂前其集气管线不结垢;油管出口连续加注该氧化型除硫剂后,虽然可将天然气中的硫化氢含量降至13ppm以下,但其集气管线却出现快速结垢、堵塞问题;进一步的现场试验表明:油管出口连续加注该氧化型除硫剂时,其dn50的集气管线在30天内即被垢堵死,从而导致所试验含硫气井无法生产、集气管线全部报废;进一步的试验检测表明:堵塞集气管线的垢主要由硫磺、钙镁铁等成垢离子组成,其中硫磺的含量超过20%。
2、该方法所用的铁质氧化型除硫剂主要成分为铁离子,通过井筒或井口管线进入地面生产系统后,会进一步形成铁垢,堵塞地面生产系统的管线、设备。
以大牛地气田为例。
该气田开展的现场试验表明:所试验的铁质氧化型除硫剂为三价铁离子络合物水溶液,铁含量>30%;油管出口加注铁质氧化型除硫剂前,其地面生产系统的换热器结垢缓慢,且所结垢的铁含量低于2%;油管出口连续加注铁质氧化型除硫剂后,换热器出现快速结垢问题,且所结垢的铁含量超过20%。
由本领域公知知识可知:气田采出液中的铁含量一般不超过30mg/l,钙镁含量一般超过1000mg/l,铁含量不到钙镁含量的3%;因此由采出液中钙镁铁成垢离子所形成的垢中铁含量一般不会超过3%。
三、井口加注碱性脱硫剂脱硫法:该方法是将常温常压下呈液态的碱性除硫剂加入井筒或井口管线内,让碱性除硫剂吸收天然气中的硫化氢或与其反应成水溶性硫化物,从而解决硫化氢特有的腐蚀、氢脆问题。该方法存在以下缺陷:碱性脱硫剂均呈碱性,在采出液中稀释、水解后碱性增强,能够与采出液中的钙镁铁等成垢离子形成沉淀物质,在管线设备内结垢。
由本领域公知知识可知:硫化氢为酸性气体,溶于水形成氢硫酸,可与碱性液体产生化学反应。
以大牛地气田为例。
该气田开展的现场试验表明:所试验的碱性除硫剂ph值>8,将其用蒸馏水稀释至浓度10%后的ph值>9.5;将10%碱性除硫剂加入氯化钙、氯化镁水溶液中可产生沉淀,将0%碱性除硫剂加入该气田采出液中同样产生沉淀。
四、干法脱硫法:该方法是利用固体脱硫剂与硫化氢的氧化还原反应脱除天然气中的硫化氢,或者利用固体脱硫剂的催化作用使氧气与硫化氢进行氧化还原反应脱除天然气中的硫化氢,或者利用固体脱硫剂吸附天然气中的硫化氢;从而解决硫化氢特有的腐蚀、氢脆问题。该方法存在以下缺陷:
1、该方法所用固体脱硫剂需要制成特定的形状码放或堆放在密闭容器中静态使用,不能以流化床形态使用,需要定期更换,更换固体脱硫剂的过程劳动强度大、危险性强。
由本领域公知知识可知:活性炭型脱硫剂、分子筛型脱硫剂、氧化铁型脱硫剂、氧化锌型脱硫剂、氧化锰型脱硫剂均为目前常用的固体脱硫剂;以氧化铁型脱硫剂为例,其脱硫机理为:氧化铁与硫化氢反应后生成硫化铁、硫化亚铁、硫磺;因此,当氧化铁型脱硫剂中的氧化铁反应完毕后,必须更换新的氧化铁型脱硫剂;更换氧化铁型脱硫剂时,先打开密闭容器,用人工或特定机械将氧化铁型脱硫剂从密闭容器中取出来,然后将新的氧化铁型脱硫剂放入容器中并按特定方式进行堆放或码放,然后再封闭密闭容器;吸收硫化氢后的氧化铁型脱硫剂置于空气中极易与氧气反应、自燃。
2、更换下来的固体脱硫剂不能在井场、集气站等天然气生产场所再生,必须送至特定危废处理站点进行再生或其他无害化特别处理,从而导致天然气的脱硫成本巨大。
由本领域公知知识可知:吸收硫化氢后的氧化铁型脱硫剂属于危险固废,置于空气中极易自燃,在天然气生产场所进行再生易导致易燃易爆事故发生,燃烧时产生二氧化硫等污染物。
总之,上述方法均有缺陷,均不满足天然气生产要求。
技术实现要素:
本发明中的“分布式”:又称分散式、局域式、区域式、非集中式。
本发明中的“脱硫”:又称除硫;可以是指去除(或除去)硫化氢,也可以是指去除(或除去)硫化氢、硫醇、硫醚等,也可以是指去除gb14554-1993《恶臭污染物排放标准》规定的恶臭污染物。
本发明中的“含硫气井”:有时简称气井,一般指所产天然气含硫化氢或硫醇、硫醚等的气井。
本发明中“恶臭气体”:是指《恶臭污染物排放标准》规定的恶臭污染物的挥发物,也可以是指有毒或有臭味、令人不愉快的气体。
本发明中“天然气”是指:从储气层流入气井的天然气,或从地层采出的可燃气体,包括由地下天然气水合物(如可燃冰)分解形成的天然气体;天然气的称谓众多,如一般从气田产出的天然气叫气田气,从油田产出的天然气叫油田气(也称伴生气),从煤层产出的天然气叫煤层气、煤成气,从页岩采出的叫页岩气;是指天然蕴藏于地下地层中的烃类和非烃类气体的混合物;一般含水、油、采气助剂、压裂液等液态物质以及水蒸气、硫化氢、二氧化碳、硫醇、硫醚等气态物质,有的不含水。
本发明中的“储气层”是指:简称气层或储层,是指天然蕴藏有天然气的地层。
本发明中的“集气管线”:又称采气管线或矿场集输管线,是指气井至集气站之间的天然气管线;有的集气管线只输送1口气井的天然气,有的集气管线汇集并输送2口以上气井的天然气;集气管线一般长达300~20000米。
本发明中的“集气站”:又称集气计量站或计量站,俗称小站,一般管辖2~50口气井,即在集气站内对2~50口气井所产的天然气进行汇集、混合、处理、输送、管理;具体生产功能(或工序环节)因不同气田(或区块)而异,一般具有气液分离(俗称分液)、产气量计量、产水量计量的功能;有的还具有油水分离、储运功能;有的还具有加热(即提高天然气温度)、节流降压(即通过节流方式降低天然气压力)、脱水(即脱除天然气中的水分)、降露点(即降低天然气露点,俗称干燥)功能;有的还具有增压(即增加天然气压力)功能。
本发明中的“站间管线”是指:又称集输管线,是指集气站至天然气净化处理厂之间的天然气管线;一般长达2-50公里。
本发明中的“地面生产系统”:简称地面系统,又称地面工程或地面生产系统、地面生产工艺。
本发明中的“外输管线”:又称长输管线,是指天然气离开气田至用户的储运管线,通常管径较大、输气量较大,一般长5~3000公里。
本发明中的“天然气净化处理厂”:又称天然气净化处理场,规模小的又称天然气净化处理站,简称净化厂(场)或处理厂(场),俗称集中处理站或大站;通常负责1个气田或1个气田区块所产天然气的集中净化处理;有的还处理从集气站用车辆运输或管线输送来的采出液。
本发明中的“净化”是指:对气井所产天然气进行脱硫、脱碳、脱水、脱烃、降露点等的处理过程。
本发明中的“采出液”:又称污水或生产污水,是指从气井产出的液态物质(包括从天然气中冷凝析出的各种液体),主要成分为水,一般含油类物质、压裂液、采气助剂等;通常矿化度很高,含大量矿钙离子、镁离子、铁离子。
本发明中的“采气助剂”:是指用于天然气开采生产过程的功能性化学剂。
本发明中的“硫垢”是指:由硫磺与钙镁铁等离子混合形成的垢,极易沉积在管壁。
本发明中的“铁垢”是指:含铁量较高的垢。
本发明中的“分采”是指:分层开采或分别开采的简称。
本发明中的“抗硫设计”是指:气田所用管线设备的材质必须满足《石油天然气工业-油气开采中用于含硫化氢环境的材料》gb/t20972、《天然气地面设施抗硫化物应力开裂和抗应力腐蚀开裂的金属材料要求》sy/t0599、《钢制化工容器材料选用规定》hg/t20581-2011等标准的规定;又指气田所用管线设备材质为抗硫化氢腐蚀的特种钢或不锈钢。
本发明中的“常规设计”是指:气田所用管线设备材质可以采用普通钢材。
本发明中的“气藏区块”:简称区块,又称气田区块。
本发明中的“硫磺”:又称单质硫,简称硫。
本发明中的“填料式静态混合器”:是指内部装有填料且用填料增强混合效果的静态混合器。
本发明中的“迷宫式静态混合器”:是指内部具有折返、蜂窝状迷宫结构且用该迷宫结构增强混合效果的静态混合器。
本发明中的“起泡剂”:又称发泡剂、泡沫剂,是指能够让水或水溶液产生泡沫的粘性物质或/和表面活性剂。
本发明要解决的技术问题是提供一种分布式天然气脱硫方法;该方法克服了现有天然气脱硫方法的缺陷,能够使含硫气井利用现有已建常规设计的地面生产系统进行生产,能够缩短气田开发建设周期,能够大幅降低气田固定投资,能够大幅提高气田开发效益,适用于含硫气井的天然气生产,尤其适用于含硫气井和不含硫井共存的气田或区块;具有实施容易,安全可靠,应用广泛,推广容易等优特点。
为解决上述技术问题,本发明所采用的第一种技术方案是:
本发明一种分布式天然气脱硫方法,包括如下步骤:
1)先将气井产出的气液混合物分离为天然气和采出液,然后让采出液通过采出液管线进入污水处理厂进一步处理;
2)再将含量大于0.001%的氧化剂液体加入分离出的天然气中,使天然气中的硫化氢和/或臭味物质氧化,形成含硫磺的固液混合物;
3)然后将固液混合物从天然气中分离出来,再让分离固液混合物后的天然气进入集气管线内,以便进入集气站。
由本领域公知知识可知:不含硫化氢的气井采出液一般呈酸性,具有腐蚀性,且采出液管线的防腐技术属于成熟技术;同样的,含硫化氢的气井采出液一般呈酸性,具有腐蚀性,且含硫化氢的采出液管线防腐技术属于成熟技术;管线内的液体膨胀性极小,压力状态下的采出液管线破裂后,采出液不会产生显著快速膨胀而导致爆炸事故,因此用管线输送含硫化氢的采出液符合气田生产要求。
进一步的,为了将天然气中的硫化氢和/或臭味物质更充分的除去,步骤2)中,将含量大于0.001%的氧化剂液体加入填料塔的上部并使氧化剂液体自上而下在填料中流动,同时让天然气进入填料塔的下部并使天然气由下而上在填料中流动,从而使天然气中的硫化氢和/或臭味物质与氧化剂液体充分接触、混合而被氧化,形成含硫磺的固液混合物;步骤3)中,让固液混合物进入填料塔下部或底部,再从填料塔下部或底部离开填料塔进一步处理。
进一步的,为了将天然气中的硫化氢和/或臭味物质更充分的除去,并减缓填料结垢堵塞速度,步骤2)中,将含量大于0.001%的氧化剂液体加入板式塔上部并使氧化剂液体自上而下流动,同时让天然气进入板式塔下部并使天然气由下而上流动,从而使天然气中的硫化氢和/或臭味物质与氧化剂液体充分接触、混合而被氧化,形成含硫磺的固液混合物;步骤3)中,让固液混合物进入板式塔下部或底部,再从板式塔下部或底部离开板式塔进一步处理。
进一步的,为了将天然气中的硫化氢和/或臭味物质更充分的除去,并解决填料、塔板的堵塞问题,步骤2)中,将含量大于0.001%的氧化剂液体加入喷淋塔上部并使氧化剂液体自上而下流动或滴落,同时让天然气进入喷淋塔下部并使天然气由下而上流动,从而使天然气中的硫化氢和/或臭味物质与氧化剂液体充分接触、混合而被氧化,形成含硫磺的固液混合物;步骤3)中,让固液混合物进入喷淋塔下部或底部,再从喷淋塔下部或底部离开喷淋塔进一步处理。
进一步的,为使天然气与氧化剂接触混合充分并降低制造成本,步骤2)中,将含量大于0.001%的氧化剂液体加入密闭容器中并使氧化剂液体的液位高度大于5cm且低于密闭容器顶部以上,再让天然气进入氧化剂液体下部并使天然气以气泡的形式由下而上流动,从而使天然气中的硫化氢和/或臭味物质与氧化剂液体充分接触、混合而被氧化,形成含硫磺的固液混合物;步骤3)中,让固液混合物从密闭容器底部或下部离开密闭容器进一步处理。
进一步的,为使天然气与氧化剂接触混合充分并降低制造成本,步骤2)中,将含量大于0.001%的氧化剂液体加入天然气中,进而伴随天然气进入静态混合器中并与天然气不断接触、混合,从而使天然气中的硫化氢和/或臭味物质与氧化剂液体充分接触、混合而被氧化,形成含硫磺的固液混合物;更进一步的,所述的静态混合器是指填料式静态混合器、迷宫式静态混合器、立式静态混合器、卧式静态混合器中的任意一种或其任意两种以上的任意联合;步骤3)中,先让固液混合物伴随天然气进入气液分离器或塔式密闭容器内,然后用气液分离器或塔式密闭容器将固液混合物从天然气中分离出来进一步处理。
进一步的,为进一步强化天然气与氧化剂液体在静态混合器内的接触、混合,步骤2)中,让含量大于0.001%的氧化剂液体和天然气进入装有填料的静态混合器底部,利用填料不断接触、混合;步骤3)中,让固液混合物和天然气从静态混合器顶部进入气液分离器或塔式密闭容器内。
进一步的,为进一步强化天然气与氧化剂液体的接触、混合,步骤2中,使含量大于0.001%的氧化剂液体进入雾化器内雾化成微小液滴并与天然气接触、混合,从而使天然气中的硫化氢和/或臭味物质与氧化剂液体充分接触、混合而被氧化,形成含硫磺的固液混合物;更进一步的,所述的雾化器是指能够让液体成为微小雾滴(或液滴)的装置,可以是机械雾化器、超声雾化器、电喷雾化器的任意一种或其任意两种以上的任意联合;步骤3)中,先让固液混合物伴随天然气进入气液分离器或塔式密闭容器内,然后用气液分离器或塔式密闭容器将固液混合物从天然气中分离出来进一步处理。
进一步的,为了使氧化剂循环使用,或为了回收硫磺,步骤3)中,将固液混合物送入再生系统再生为氧化剂含量大于0.001%的悬浊液;然后将氧化剂悬浊液送入固液分离系统分离为硫磺膏(或硫磺固形物)和含量大于0.001%的氧化剂液体,将硫磺膏(或硫磺固形物)进一步回收利用或无害化处理,将含量大于0.001%的氧化剂液体送入药剂罐内;然后将含量大于0.001%的氧化剂液体加入天然气中,以便氧化剂液体循环使用。
进一步的,为了更好的使氧化剂循环使用、回收硫磺,步骤3)中,将固液混合物送入包括壳体、出药管线、硫磺泡沫出口流道、空气出气管、空气进气管的再生系统,使固液混合物中的液体再生为氧化剂含量大于0.001%的氧化剂液体,并使固液混合物中的固形物、硫磺被空气气泡浮选至液面,形成硫磺泡沫物和含量大于0.001%的氧化剂液体,将含量大于0.001%的氧化剂液体送入药剂罐内;然后让硫磺泡沫物进入固液分离系统并分离为硫磺膏(或硫磺固形物)和含量大于0.001%的氧化剂液体,将硫磺膏(或硫磺固形物)进一步回收利用或无害化处理,将含量大于0.001%的氧化剂液体送入药剂罐内;然后再将药剂罐内的含量大于0.001%的氧化剂液体加入天然气中,以便氧化剂液体循环使用。更进一步的,为强化气泡浮选硫磺固形物的效果,步骤3)中,向固液混合物或再生系统中加入起泡剂、絮凝剂。更进一步的,为强化气泡浮选硫磺固形物的效果,步骤3)中,所述空气进气管位于固液混合物底部且有布气装置。
进一步的,为了使氧化剂循环使用,或为了回收硫磺,步骤3)中,将固液混合物送入固液分离系统分离为硫磺膏(或硫磺固形物)和液体,将硫磺膏(或硫磺固形物)进一步回收利用或无害化处理,将液体送入再生系统再生为氧化剂含量大于0.001%的氧化剂液体;然后将含量大于0.001%的氧化剂液体加入天然气中,以便氧化剂液体循环使用。
进一步的,为了降低采出液管线的腐蚀速度,步骤1)中,先将氧化剂或含量大于0.001%的氧化剂液体或/和碱加入采出液中,使采出液中的硫化氢和/或臭味物质氧化,形成含硫磺的采出液混合物;然后将采出液混合物中的硫磺、固形物分离出来进一步处理;然后再让分离出硫磺、固形物的采出液通过采出液管线进入污水处理厂进一步处理。
进一步的,为了减少还原性固形物消耗氧化剂的用量,降低加药成本,步骤1)中,先将采出液中的固形物分离出来进一步处理;然后将氧化剂或含量大于0.001%的氧化剂液体或/和碱加入分离固形物后的采出液中,使采出液中的硫化氢和/或臭味物质氧化,形成含硫磺的采出液混合物;然后将采出液混合物中的硫磺、固形物分离出来进一步处理;然后再让分离出硫磺、固形物的采出液通过采出液管线进入污水处理厂进一步处理。
进一步的,为了使硫化氢和/或臭味物质充分氧化,降低加药成本,步骤1)中,先将氧化剂或含量大于0.001%的氧化剂水溶液或/和碱加入采出液中并进入密闭反应容器,使采出液中的硫化氢和/或臭味物质充分氧化,形成含硫磺的采出液混合物;然后将采出液混合物中的硫磺、固形物分离出来进一步处理;然后再让分离出硫磺、固形物的采出液通过采出液管线进入污水处理厂进一步处理。
进一步的,所述氧化剂是氯酸盐、高氯酸盐、高锰酸盐、过氧化物、过氧化氢、双氧水、氟、氯、溴、碘、三价铁盐、二价铜盐、三价铜盐、四价铜盐、络合铁、螯合铁中的任意一种或其任意两种以上任意比例混合后不产生化学反应的混合物。
进一步的,所述氧化剂液体是氧化剂的甲醇与水任意比例混合的混合溶液。
进一步的,所述氧化剂液体是氧化剂的甲醇溶液。
进一步的,所述氧化剂液体是ph值大于7.5的三价铁络合物水溶液或/和醇溶液。
进一步的,为了防止冬季结冰,所述氧化剂液体中含5~60%的有机酸盐。
本发明的有益效果如下:本发明克服了现有天然气脱硫方法的缺陷,能够使含硫气井利用现有已建常规设计的地面生产系统进行生产,能够大幅降低气田固定投资,能够大幅提高气田开发效益,尤其适用于含硫气井和不含硫井共存的气田或区块;具有实施容易,安全可靠,应用广泛,推广容易等优特点。
附图说明
下面结合附图对本发明的具体实施方式作进一步详细的说明
图1为现有集气站采出液管输-集中式脱硫法的地面生产系统示意图;
图2为现有集气站采出液罐车拉运-集中式脱硫法的地面生产系统示意图;
图3为实施例1中的分布式天然气脱硫方法示意图;
图4为实施例1中的室内试验装置示意图;
图5为实施例2中的分布式天然气脱硫方法示意图;
图6为实施例3中的分布式天然气脱硫方法示意图;
图7为实施例4中的分布式天然气脱硫方法示意图;
图8为实施例5中的分布式天然气脱硫方法示意图;
图9为实施例6中的分布式天然气脱硫方法示意图;
图10为实施例7中的分布式天然气脱硫方法示意图;
图11为实施例8中的分布式天然气脱硫方法示意图;
图12为实施例9中的分布式天然气脱硫方法示意图;
图13为实施例10中的分布式天然气脱硫方法示意图;
图14为实施例11中的分布式天然气脱硫方法示意图;
图15为实施例12中的分布式天然气脱硫方法示意图;
图16为实施例13中的分布式天然气脱硫方法示意图;
图17为实施例14中的分布式天然气脱硫方法示意图。
具体实施方式
实施例1
参见图3所示,一种分布式天然气脱硫方法,包括如下步骤:
1)先让气井100产出的气液混合物通过阀门101、进气管301进入气液分离器300中分离为天然气和采出液,然后让采出液通过出液管线302进入采出液管线107中,以便进入污水处理厂108进一步处理;
2)再用加药管线304将含量大于0.001%的氧化剂水溶液加入从气液分离器300分离出来进入管线303的天然气中,使天然气中的硫化氢和/或臭味物质氧化,形成含硫磺的固液混合物;
3)然后用气液分离器(或塔式密闭容器)305将固液混合物从天然气中分离出来进入固液出口管线307进一步处理,再让分离固液混合物后的天然气通过天然气出口管线306进入集气管线102内,以便进入集气站103。
由本领域公知知识可知:气液分离器简称分离器,用气液分离器、塔式密闭容器分离气液混合物属于成熟方法;用气液分离器、塔式密闭容器,分离气体与悬浊液、浆状液属于成熟方法;塔式密闭容器一般是指高度大于内径的圆桶形密闭容器,有时也指高度大于宽度的长方体型密闭容器。
室内实验表明:以三价铁离子fe 3络合物水溶液为例。参见图4所示,玻璃容器400下部盛装含量2%的三价铁离子fe 3络合物水溶液401,上部形成空腔405,顶部用密封件404密封,天然气进气管402穿过密封件404插入玻璃容器400下部的三价铁离子fe 3络合物水溶液401中至玻璃容器400底部,天然气出气管403穿过密封件404插入玻璃容器400上部的空腔405中;让硫化氢含量200mg/m3的天然气以0.1升/秒的流量通过天然气进气管402进入液位高度500毫米的三价铁离子fe 3络合物水溶液401中,然后再上升至三价铁离子fe 3络合物水溶液401液面并进入玻璃容器400上部的空腔405中,然后再通过天然气出气管403离开玻璃容器400后,其硫化氢含量降至120mg/m3,由此计算可知该天然气的脱硫率为40%;进一步的实验表明:不断降低该硫化氢含量200mg/m3的天然气通过天然气进气管402的流量(或者让从天然气出气管403出来的硫化氢含量120mg/m3天然气多次循环进入天然气进气管402),可将其离开玻璃容器400后的硫化氢含量降至15mg/m3,满足《天然气gb17820-2018》的规定;进一步的实验表明:随着该硫化氢含量200mg/m3的天然气不断进入三价铁离子fe 3络合物水溶液401中,目测有淡黄色或灰白色微粒物形成,进一步试验检测可知该淡黄色或灰白色微粒物的主要成分为硫磺;进一步试验表明:停止天然气进入三价铁离子fe 3络合物水溶液401中,将生成淡黄色或灰白色微粒物的三价铁离子fe 3络合物水溶液401静置2小时,其中的淡黄色或灰白色微粒物不沉淀至玻璃容器400底部,即三价铁离子fe 3络合物水溶液401与其所生成的硫磺能够形成流动性良好的悬浊液或固液混合物;进一步试验表明:将生成淡黄色或灰白色微粒物的三价铁离子fe 3络合物水溶液401静置7天后,淡黄色或灰白色微粒物沉淀在三价铁离子fe 3络合物水溶液401的底部。
由此可知:氧化剂水溶液加入管线303天然气中所形成的固液混合物能够顺利进入气液分离器305;在气液分离器305中能够将固液混合物从天然气中分离出来,并进入固液出口管线307中。
实施例2
参见图5所示,重复实施例1,其不同之处在于:为了将天然气中的硫化氢和/或臭味物质更充分的除去,步骤2)中,用加药管线304将含量大于0.001%的氧化剂水溶液加入填料塔500中填料501的上部并使氧化剂水溶液自上而下在填料501中流动,同时让从气液分离器300分离出来的天然气通过管线303进入填料塔500中填料501的下部并使天然气由下而上在填料501中流动,从而使天然气中的硫化氢和/或臭味物质与氧化剂水溶液充分接触、混合而被氧化,形成含硫磺的固液混合物;
步骤3)中,让固液混合物进入填料塔500的下部或底部,再从填料塔500下部或底部的固液出口管线307离开填料塔500进一步处理;并让天然气从填料塔500顶部或上部进入天然气出口管线306,然后再通过天然气出口管线306进入集气管线102内,以便进入集气站103。
由本领域公知知识可知:填料塔、填料属于成熟技术,拉西环、鲍尔环、瓷环、陶土烧结物、金属粉末烧结物、金属纤维、塑料纤维、化纤、植物纤维、网状物、纤维物质、多孔性物质均可用作填料。
实施例3
参见图6所示,重复实施例1,其不同之处在于:为了将天然气中的硫化氢和/或臭味物质更充分的除去,并为了减缓填料结垢堵塞速度,步骤2)中,用加药管线304将含量大于0.001%的氧化剂水溶液加入板式塔600上部并使氧化剂水溶液自上而下流动,同时让从气液分离器300分离出来的天然气通过管线303进入板式塔600下部并使天然气由下而上流动,从而使天然气中的硫化氢和/或臭味物质与氧化剂水溶液充分接触、混合而被氧化,形成含硫磺的固液混合物;
步骤3)中,让固液混合物进入板式塔600的下部或底部,再从板式塔600下部或底部的固液出口管线307离开板式塔600进一步处理;并让天然气从板式塔600顶部或上部进入天然气出口管线306,然后再通过天然气出口管线306进入集气管线102内,以便进入集气站103。
实施例4
参见图7所示,重复实施例1,其不同之处在于:为了将天然气中的硫化氢和/或臭味物质更充分的除去,并为了解决填料、塔板的堵塞问题,步骤2)中,用加药管线304将含量大于0.001%的氧化剂水溶液通过喷淋装置701加入喷淋塔700上部并使氧化剂水溶液自上而下流动或滴落,同时让从气液分离器300分离出来的天然气通过管线303进入喷淋塔700下部并使天然气由下而上流动,从而使天然气中的硫化氢和/或臭味物质与氧化剂水溶液充分接触、混合而被氧化,形成含硫磺的固液混合物;所述喷淋装置701是指能使液体滴落或淋落的装置,可以是喷淋头、喷淋管、喷淋雾化器、机械雾化器、超声雾化器的任意一种或其两种以上的任意联合;
步骤3)中,让固液混合物进入喷淋塔700的下部或底部,再从喷淋塔700下部或底部的固液出口管线307离开喷淋塔700进一步处理;并让天然气从喷淋塔700顶部或上部进入天然气出口管线306,然后再通过天然气出口管线306进入集气管线102内,以便进入集气站103。
实施例5
参见图8所示,重复实施例1,其不同之处在于:为使天然气与氧化剂接触混合充分并降低制造成本,步骤2)中,用加药管线304将含量大于0.001%的氧化剂水溶液802加入密闭容器800中并使氧化剂水溶液802的液位高度大于5cm且低于密闭容器800顶部5cm以上,再让从气液分离器300分离出来的天然气依次通过管线303、插入管线801进入氧化剂水溶液下部并使天然气以气泡803的形式由下而上流动,从而使天然气中的硫化氢和/或臭味物质与氧化剂水溶液充分接触、混合而被氧化,形成含硫磺的固液混合物;
步骤3)中,让固液混合物从密闭容器800底部或下部的固液出口管线307离开密闭容器800进一步处理;并让天然气从密闭容器800顶部或上部进入天然气出口管线306,然后再通过天然气出口管线306进入集气管线102内,以便进入集气站103。
室内实验表明:参见图4所示,三价铁离子fe 3络合物水溶液与天然气所形成的固液混合物静置2小时不分层、不沉淀;因此固液混合物能够从密闭容器800底部或下部的固液出口管线307离开密闭容器800。
实施例6
参见图9所示,重复实施例1,其不同之处在于:为使天然气与氧化剂接触混合充分并降低制造成本,步骤2)中,用加药管线304将含量大于0.001%的氧化剂水溶液加入从气液分离器300分离出来进入管线303的天然气中,进而伴随天然气进入静态混合器900中并与天然气不断接触、混合,从而使天然气中的硫化氢和/或臭味物质与氧化剂水溶液充分接触、混合而被氧化,形成含硫磺的固液混合物;所述的静态混合器900是指填料式静态混合器、迷宫式静态混合器、立式静态混合器、卧式静态混合器中的任意一种或其任意两种以上的任意联合;
步骤3)中,先让固液混合物伴随天然气通过连接管线901进入气液分离器(或塔式密闭容器)305内,然后用气液分离器(或塔式密闭容器)305将固液混合物从天然气中分离出来进入固液出口管线307进一步处理,再让分离固液混合物后的天然气通过天然气出口管线306进入集气管线102内,以便进入集气站103。
由本领域公知知识可知:用静态混合器进行气液混合属于成熟技术。
实施例7
参见图10所示,重复实施例1、6,其不同之处在于:为进一步强化天然气与氧化剂水溶液在静态混合器内的接触、混合,步骤2)中,让含量大于0.001%的氧化剂水溶液和天然气进入装有填料1001的静态混合器1000底部,利用填料1001不断接触、混合;
步骤3)中,让固液混合物和天然气从静态混合器1000顶部通过连接管线901进入气液分离器(或塔式密闭容器)305内。
实施例8
参见图11所示,重复实施例1,其不同之处在于:为进一步强化天然气与氧化剂水溶液的接触、混合,步骤2中,用加药管线304使含量大于0.001%的氧化剂水溶液进入雾化器1100内雾化成微小液滴并与从气液分离器300分离出来进入管线303的天然气接触、混合,从而使天然气中的硫化氢和/或臭味物质与氧化剂水溶液充分接触、混合而被氧化,形成含硫磺的固液混合物;所述的雾化器1100是指能够让液体成为微小雾滴(或液滴)的装置,可以是机械雾化器、超声雾化器、电喷雾化器的任意一种或其任意两种以上的任意联合;
步骤3)中,先让固液混合物伴随天然气通过连接管线901进入气液分离器(或塔式密闭容器)305内,然后用气液分离器(或塔式密闭容器)305将固液混合物从天然气中分离出来进入固液出口管线307进一步处理,再让分离固液混合物后的天然气通过天然气出口管线306进入集气管线102内,以便进入集气站103。
由本领域公知知识可知:气流预混雾化器、气流引射雾化器、高压射流(喷射)雾化器、喷嘴雾化器、气流雾化器、旋杯式雾化器均为机械雾化器。
实施例9
参见图12所示,重复实施例1,其不同之处在于:为了使氧化剂循环使用,或为了回收硫磺,步骤3)中,将固液混合物通过固液出口管线307送入再生系统1200再生为氧化剂含量大于0.001%的悬浊液;然后通过悬浊液管线1201将氧化剂悬浊液送入固液分离系统1202分离为硫磺膏(或硫磺固形物)和含量大于0.001%的氧化剂水溶液,将硫磺膏(或硫磺固形物)进一步回收利用或无害化处理,将含量大于0.001%的氧化剂水溶液用进罐管线1203送入药剂罐1204内;然后通过进泵管线1205、泵1206、加药管线304将含量大于0.001%的氧化剂水溶液加入从气液分离器300分离出来进入管线303的天然气中,以便氧化剂水溶液循环使用。
由本领域公知知识可知:药剂罐可以是圆形容器,也可以是方形或其他形状的容器;用硫磺膏(或硫磺固形物)制成硫磺属于成熟技术。
室内试验表明:参见图4所示,以三价铁离子fe 3含量为2%的络合物水溶液为例;当硫化氢含量200mg/m3的天然气以0.5升/秒的流量进入三价铁离子fe 3含量为2%的络合物水溶液401中3小时后,则目测可知该络合物水溶液401中已悬浮大量微粒,检测可知天然气出气管403的天然气硫化氢含量达到195mg/m3以上,由此证明该络合物水溶液401已经不能再有效降低天然气中的硫化氢含量;进一步检测可知该络合物水溶液401中悬浮微粒的主要成分为硫磺;进一步检测可知该络合物水溶液401中已形成大量二价铁离子fe 2,证明该络合物水溶液401中的三价铁离子fe 3已被还原为二价铁离子fe 2。
进一步试验表明:向上述悬浮大量微粒的络合物水溶液401中以0.5升/秒的流量通入空气3小时,目测该络合物水溶液401中的悬浮微粒漂浮至液面并形成泡沫固形物;用滤纸将该络合物水溶液401中的微粒及液面漂浮物过滤出来,使该络合物水溶液401变得清澈,然后再将硫化氢含量200mg/m3的天然气以0.5升/秒的流量通入该清澈的络合物水溶液401中,则目测可知该络合物水溶液401中再次不断生成悬浮微粒,同时通过检测可知天然气出气管403中的天然气硫化氢含量已经低于130mg/m3,由此计算可知该天然气的脱硫率为35%。
进一步的对比试验表明:先用滤纸将上述络合物水溶液401中的悬浮微粒过滤出来,使该络合物水溶液401变得清澈;再向该清澈的络合物水溶液401中以0.5升/秒的流量通入空气3小时,目测可知该络合物水溶液401外观清澈、没有固形微粒生成;然后再向该清澈的络合物水溶液401中以0.5升/秒的流量通入硫化氢含量200mg/m3的天然气,则目测可知该络合物水溶液401中再次不断生成悬浮微粒,同时通过检测可知天然气出气管403中的天然气硫化氢含量已经低于150mg/m3,由此计算可知该天然气的脱硫率为25%。
由此证明:空气能够将吸收硫化氢后不能再有效降低天然气中硫化氢含量的三价铁离子fe 3络合物水溶液401再生,使其再次具备有效降低天然气中硫化氢含量的能力。
实施例10
参见图13所示,重复实施例1、9,其不同之处在于:为了更好的使氧化剂循环使用、回收硫磺,步骤3)中,将固液混合物通过固液出口管线307送入包括壳体1301、出药管线1302、硫磺泡沫出口流道1303、空气出气管1304、空气进气管1305的再生系统1300,使固液混合物1306中的液体再生为氧化剂含量大于0.001%的氧化剂水溶液,并使固液混合物1306中的固形物、硫磺被空气气泡1307浮选至液面,形成硫磺泡沫物和含量大于0.001%的氧化剂水溶液,将含量大于0.001%的氧化剂水溶液用出药管线1302送入药剂罐1204内;然后让硫磺泡沫物通过硫磺泡沫出口流道1303进入固液分离系统1202并分离为硫磺膏(或硫磺固形物)和含量大于0.001%的氧化剂水溶液,将硫磺膏(或硫磺固形物)进一步回收利用或无害化处理,将含量大于0.001%的氧化剂水溶液用进罐管线1203送入药剂罐1204内;然后再通过进泵管线1205、泵1206、加药管线304将药剂罐1204内的含量大于0.001%的氧化剂水溶液加入从气液分离器300分离出来进入管线303的天然气中,以便氧化剂水溶液循环使用。
进一步的,为强化气泡浮选硫磺固形物的效果,步骤3)中,向固液混合物1306或固液出口管线307、再生系统1300中加入起泡剂、絮凝剂。
进一步的,为强化气泡浮选硫磺固形物的效果,步骤3)中,所述空气进气管1305位于固液混合物1306的底部且有布气装置。
由本领域公知知识可知:向悬浊液中通入空气可产生泡沫浮选(简称气浮)作用,将固形物气浮到液面;流道可以供液体、气体流动,也可以供浆状物、固液混合物、泡沫固形物流动或滑动,可以是密闭的管状物,也可以是半敞口的滑道物;用管线上的孔洞与割缝、织物管状物、多孔物质均可使空气在液体中均布,是本领域常用的布气装置。
实施例11
参见图14所示,重复实施例1、9,其不同之处在于:为了使氧化剂循环使用,或为了回收硫磺,步骤3)中,将固液混合物通过固液出口管线307送入固液分离系统1202分离为硫磺膏(或硫磺固形物)和液体,将硫磺膏(或硫磺固形物)进一步回收利用或无害化处理,将液体用液体管线1400送入再生系统1200再生为氧化剂含量大于0.001%的氧化剂水溶液;然后通过进药管线1401、泵1206、加药管线304将含量大于0.001%的氧化剂水溶液加入从气液分离器300分离出来进入管线303的天然气中,以便氧化剂水溶液循环使用。
实施例12
参见图15所示,重复实施例1、9,其不同之处在于:为了降低采出液管线的腐蚀速度,步骤1)中,先将氧化剂或含量大于0.001%的氧化剂液体或/和碱用加药管线1500加入出液管线302的采出液中,使采出液中的硫化氢和/或臭味物质氧化,形成含硫磺的采出液混合物;然后用固液分离设备1501将采出液混合物中的硫磺、固形物分离出来进一步处理;然后再让分离出硫磺、固形物的采出液通过管线1502进入采出液管线107中,以便进入污水处理厂108进一步处理。
实施例13
参见图16所示,重复实施例1、9,其不同之处在于:为了减少还原性固形物消耗氧化剂的用量,降低加药成本,步骤1)中,先用固液分离装置1600将采出液中的固形物分离出来进一步处理;然后将氧化剂或含量大于0.001%的氧化剂液体或/和碱用加药管线1500加入管线1601内分离固形物后的采出液中,使采出液中的硫化氢和/或臭味物质氧化,形成含硫磺的采出液混合物;然后用固液分离设备1501将采出液混合物中的硫磺、固形物分离出来进一步处理;然后再让分离出硫磺、固形物的采出液通过管线1502进入采出液管线107中,以便进入污水处理厂108进一步处理。
实施例14
参见图17所示,重复实施例1、12,其不同之处在于:为了使硫化氢和/或臭味物质充分氧化,降低加药成本,步骤1)中,先将氧化剂或含量大于0.001%的氧化剂水溶液或/和碱用加药管线1500加入出液管线302的采出液中并进入密闭反应容器1700,使采出液中的硫化氢和/或臭味物质充分氧化,形成含硫磺的采出液混合物;然后用固液分离设备1501将采出液混合物中的硫磺、固形物分离出来进一步处理;然后再让分离出硫磺、固形物的采出液通过管线1502进入采出液管线107中,以便进入污水处理厂108进一步处理。
实施例15
重复实施例1-14,其不同之处在于:所述氧化剂是五价钒化合物、氯酸盐、高氯酸盐、高锰酸盐、过氧化物、过氧化氢、双氧水、氟、氯、溴、碘、三价铁盐、二价铜盐、三价铜盐、四价铜盐、五价钒盐、络合铁、螯合铁中的任意一种或其任意两种以上任意比例混合后不产生化学反应的混合物。
由本领域公知知识可知:络合铁又称三价铁络合物、三价铁配位化合物;螯合铁又称三价铁獒合物;三氯化铁为常用的三价铁盐,溶于水。
实施例16
重复实施例1-14,其不同之处在于:所述的氧化剂液体是氧化剂的甲醇与水任意比例混合的混合溶液。
由本领域公知知识可知:水与甲醇互溶,目前气田大规模应用甲醇抑制天然气水合物、防冻堵。
室内试验表明:双氧水、三氯化铁水溶液、次氯酸钠水溶液、三价铁络合物均溶于甲醇或乙醇。
实施例17
重复实施例1-14,其不同之处在于:所述的氧化剂液体是氧化剂的甲醇溶液。
实施例18
重复实施例1-14,其不同之处在于:所述氧化剂液体是ph值大于7.5的三价铁络合物水溶液或/和醇溶液。
室内试验表明:ph为10的三价铁络合物水溶液在室内静置48小时不分层、不沉淀,稳定性良好;进一步对比试验可知:双氧水在ph值为10时分解加速、产生气泡、稳定性差,将三氯化铁水溶液ph值用纯碱或氢氧化钠调整至8时产生沉淀。
实施例19
重复实施例1-14,其不同之处在于:为了防止冬季结冰,所述氧化剂水溶液中含5~60%的有机酸盐。
由本领域公知知识可知:气井在冬季正常生产;甲酸钾属于有机酸盐。
室内试验表明:10%次氯酸钠水溶液、20%双氧水、15%三价铁络合物水溶液中,含60%甲酸钾的冰点低于-50℃,含40%甲酸钾的冰点低于-30℃,,5%甲酸钾的冰点低于-4℃。
显然,本发明的上述实施例仅仅是为清楚地说明本发明所作的举例,而并非是对本发明的实施方式的限定。对于所属领域的普通技术人员来说,在上述说明的基础上还可以做出其它不同形式的变化或变动。这里无法对所有的实施方式予以穷举。凡是属于本发明的技术方案所引伸出的显而易见的变化或变动仍处于本发明的保护范围之列。
本文用于企业家、创业者技术爱好者查询,结果仅供参考。