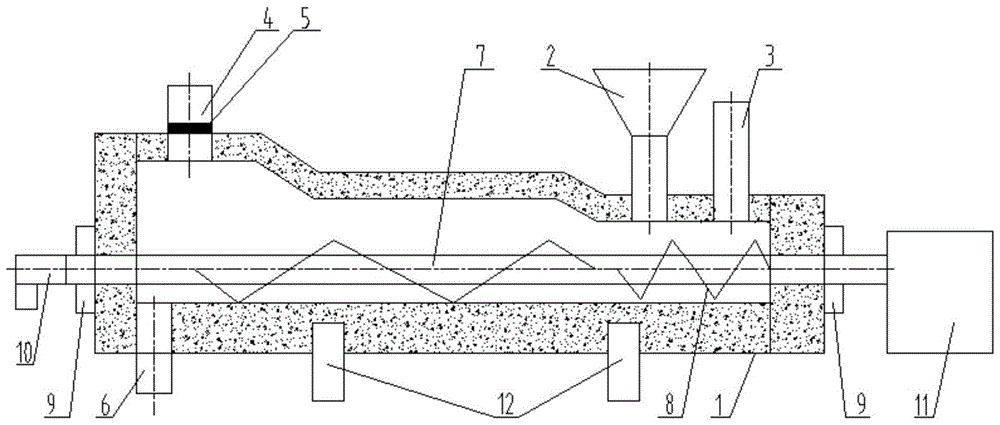
本发明属于固体废弃物热解技术领域,具体涉及一种用于固体热载体加热的热解反应器。
背景技术:
热解技术采用无氧热解原理,将固体物料由低能量密度的物质转化为高能量密度的油、气和热解炭,其以减量化、资源化、能源化的技术优势,成为极具发展潜力的一种新型固体废弃物处理技术,在垃圾、生物质等领域得到广泛应用。
热解反应器作为热解装置中核心设备,根据不同热解工艺,结构型式各有不同,主要有固定床反应器、流化床反应器、回转窑或绞龙等。目前,国内较多采用回转窑结构,其采用夹套结构,利用气体热载体方式对热解反应过程供热,能保证物料热解停留时间,但内部热解物料混合效果相对差,热解不均匀,易造成内壳内壁底部积碳。另外,回转窑高温密封问题一直无法很好解决。基于此,出现利用螺旋绞龙型式的热解反应器,此结构能满足热解停留时间要求,一定程度减弱热解不均匀性,降低局部物料滞留现象,利用螺旋推力使热解物料顺利排出。但国内已有技术中,多利用气体热载体供热方式,采用夹套结构,造成结构设计复杂,设备制造成本高;对组分复杂物料,在避免缠绕、搭桥问题上没有很好解决,且中心轴端高温密封问题也很难解决。
申请号cn104531227a中公开的一种生物质双轴螺旋热解装置,采用夹套结构,利用气体热载体供热方式,将烟气作为热解热源通入夹套,机壳中心设置两个螺旋绞龙用于物料混合与输送。气体热载体供热方式与固体热载体相比,传热效率相对低;结构采用双层夹套式,内、外层壳体与高温(700~1000℃)介质直接接触,造成高温选材难度大,设备造价高,性价比低;同时,设备壳体、中心轴等接触介质不同,温度不同,造成各部件线膨胀量不一致,结构设计复杂,且国内现有密封技术无法满足如此高温度下轴端密封要求。此外,采用的双轴结构主要用于物料混合与输送,间断式螺旋基于克服轴径向膨胀设计,不具备防止局部结焦、防缠绕、自清洁能力。
申请号cn107033932a中公开的一种用于处理城市废弃物的多功能连续双轴流化床裂解炉,此炉体利用热辐射原理,也采用夹套结构。炉内设置了双轴结构,但结构设计中主要发挥单轴输送功能,搅拌功能采用单轴螺旋叶片上开齿实现,不具备双轴间物料相互混合、破碎和搅拌功能。
基于上述,针对成分较为复杂的固体废弃物,例如生活垃圾,在热解过程中,易出现缠绕、搭桥、局部结焦引起的堵塞等问题,至今没有研发出一种传热效率高、结构简单、具有大规模处理量、绝氧密封性好、防堵塞、可靠性高的利于工程应用的热解反应器。
技术实现要素:
本发明的目的在于提供一种用于固体热载体加热的热解反应器,实现大规模处理固体物料。
本发明的技术方案如下:
一种用于固体热载体加热的热解反应器,包括反应器壳体、中心轴、助热解叶片、动密封装置、水冷装置、传动装置、支撑装置;
所述的反应器壳体的顶盖设置为“卧式阶梯”形式,前段低、后段高,使得反应器壳体的后段腔体容积根据热解气相产物体积量逐级增大,具备自除尘功能;
在所述反应器壳体的内部设有中心轴,所述的中心轴并排设置且互相平行,为中空结构;
所述中心轴的两端均伸出反应器壳体,分别连接两侧动密封装置后,一端与水冷装置相连,另一端承接传动装置;
所述的动密封装置采用机械密封和通隔离气的组合密封结构,分别与反应器壳体的两侧端面相连,并分别与中心轴的两端位置对应;
所述的水冷装置能够通过向中心轴内部通入冷却水使中心轴降温,避免中心轴长期在高温工况下工作;
所述的传动装置通过调整中心轴的转速和转向,根据热解效果实时控制固体废弃物与固体热载体进入反应器壳体内的流动速度、停留时间;
在所述中心轴位于反应器壳体内部的部分上、沿轴向分为输送区和混合搅拌区,输送区与混合搅拌区设置助热解叶片;助热解叶片根据各区功能要求,采用连续螺旋或单片桨叶结构;
所述的助热解叶片沿轴向重叠、交错布置,用于输送、混合、破碎、搅拌,并具备自清洁功能;
在所述反应器壳体的顶盖低段设有相邻的固体热载体进料口和固体废弃物进料口,且固体热载体进料口在固体废弃物进料口之前,起缩短固体热载体和固体废弃物下料路程及防止固体废弃物在反应器初始段堵料的作用;
在所述反应器壳体的顶盖高段设有热解气出口;在所述反应器壳体的底板尾端设置残碳出口,用于排出热解产物;
在所述反应器壳体的外部设有支撑装置,支撑装置采用鞍式支座或钢结构支撑形式,设置固定端和滑动端,可吸收反应器壳体整体热膨胀量。
所述的助热解叶片螺距小于3d,d为助热解叶片的旋转直径,安装倾角小于90°,安装倾角控制物料停留时间,保证热解要求。
所述助热解叶片的重叠宽度<0.5d。
所述的中心轴能够同时相向或相对转动。
所述的中心轴上自带可插件或焊接凸台,凸台上焊接助热解叶片,以保证助热解叶片在线更换或维修时,中心轴同轴度不变。
还包括除尘装置,所述的除尘装置设于反应器壳体的末级,用于降低热解气出口的含尘量。
所述的传动装置采用链轮结构,实现多轴同时传动。
在所述助热解叶片的顶端设有防磨结构,以增强助热解叶片的耐磨性。
在所述反应器壳体的内壁涂有蓄热耐磨耐高温涂料,以保持热解区稳定的温度场。
在所述中心轴的外表面涂设有耐磨耐高温涂料,防止中心轴局部低温,导致固体废弃物在热解环境中产生大量焦油引起堵塞。
本发明的显著效果在于:
(1)本发明热解反应器采用固体热载体供热方式,卧式单壳体 中心轴结构,相较于夹套式气体热载体热解反应器,结构简单、可靠性高、可实现大规模固体物料热解能力,生活垃圾处理量≥350吨/天。
(2)本发明热解反应器采用连续螺旋和单片桨叶式作为助热解叶片,叶片重叠、交错布置,实现了固体热载体与热解物料的均匀混合,保证同时段热解程度均匀性;同时,具备输送、混合、破碎,防缠绕和堵塞的自清洁功能。
(3)本发明热解反应器中心轴两端采用机械密封 通隔离气的组合密封型式,解决了长轴(≥9m)、大轴径(≥500mm),高温(≥850℃)、中心轴径向大摆动(径向跳动≥2mm)所引起的设备密封失效问题。此结构已通过中试试验验证,实现设备内含氧量<0.1%。
(4)本发明热解反应器传动装置利用链轮结构,突破现有双轴局限,实现多轴同时运转,并实现根据热解效果实时控制热解停留时间的目的。
(5)本发明热解反应器中心轴结构满足高温低材料选型,采用外表面敷设耐磨耐高温涂料,内部通冷却水结构,实现在与高温物料直接接触的同时,可避免轴上局部低温引起的结焦,进而避免结焦引起的堵塞、磨损;并降低中心轴选材等级,提高设备性价比。
(6)本发明热解反应器采用“卧式阶梯”结构,遵循热解进程中热解产物气、油和碳产量配比设计;并具备自除尘功能,简化后续热解气除尘配置,实现反应器多功能目的。
附图说明
图1为本发明热解反应器示意图;
图2为中心轴布置及转向示意图。
图3为中心轴上凸台示意图。
图中:1.反应器壳体;2.固体废弃物进料口;3.固体热载体进料口;4.热解气出口;5.除尘装置;6.残碳出口;7.中心轴;8.助热解叶片;9.动密封装置;10.水冷装置;11.传动装置;12.支撑装置。
具体实施方式
下面结合附图及具体实施例对本发明作进一步详细说明。
如图1-2所示的一种用于固体热载体加热的热解反应器,包括反应器壳体1、固体废弃物进料口2、固体热载体进料口3、热解气出口4、除尘装置5、残碳出口6、中心轴7、助热解叶片8、动密封装置9、水冷装置10、传动装置11、支撑装置12。
所述反应器壳体1采用单壳体“卧式阶梯”结构,顶盖设置为阶梯形式,阶梯采用两级及以上结构,前段低、后段高,使得反应器壳体1的后段腔体容积相对前段腔体增大,可根据热解气量的增多有效降低热解气速,从而降低气体对粉尘的夹带;同时根据重力沉降原理,热解气在行进过程中,大颗粒粉尘逐渐沉降至釜底,具备自除尘功能。
在所述反应器壳体1的内壁涂有蓄热耐磨耐高温涂料,以保持热解区稳定的温度场,确保热解反应的稳定性。
在所述反应器壳体1的内部设有中心轴7,所述的中心轴7并排设置且互相平行,为中空结构,轴数量采用两个及以上结构。
在所述中心轴7的外表面涂设有耐磨耐高温涂料,防止中心轴7局部低温,导致固体废弃物在热解环境中产生大量焦油引起堵塞。
如图3所示,所述的中心轴7上自带可插件或焊接凸台,凸台上焊接助热解叶片8。此结构既实现助热解叶片连接可靠,保证运行中叶片不发生脱落现象;又可解决在线更换叶片时,引起中心轴7同轴度改变,造成设备运行不稳定的问题。
所述中心轴7的两端均伸出反应器壳体1,分别连接两侧动密封装置9后,一端与水冷装置10相连,另一端承接传动装置11。
所述的动密封装置9分别与反应器壳体1的两侧端面相连,并分别与中心轴7的两端位置对应。
所述动密封装置9采用机械密封 通隔离气的组合密封结构,解决了长轴(≥9m)、大轴径(≥500mm),高温(≥850℃)、中心轴径向大摆动(径向跳动≥2mm)所引起的设备密封失效问题。
所述的动密封装置9能够隔离反应器壳体1内部易燃易爆气体外泄,造成安全事故;也能防止外部空气进入反应器壳体1内部,生成二噁英。目前,此密封已通过设备中试试验验证,实现设备内部含氧量<0.1%。
所述的水冷装置10能够通过向中心轴7内部通入冷却水使中心轴7降温,避免中心轴7长期在高温工况下工作,有效降低中心轴7的选材等级,提高使用寿命的同时,降低设备选材、制造成本。
所述的传动装置11采用链轮结构,通过传动装置11使多轴同时相向或相对转动,并调整中心轴7的转速和转向,根据热解效果实时控制固体废弃物与固体热载体进入反应器壳体1内的流动速度、停留时间,更进一步控制热解反应时间。
在所述中心轴7位于反应器壳体1内部的部分上、沿轴向分为输送区和混合搅拌区,输送区与混合搅拌区设置助热解叶片8。
所述的助热解叶片8根据功能要求,可以采用连续螺旋或单片浆叶式,螺距可以相同,也可以不同螺距交叉布置,安装倾角可相同也可不同进行布置。
所述的助热解叶片8沿轴向重叠、交错布置,螺距小于3d,d为助热解叶片8的旋转直径,安装倾角小于90°,用于输送、混合、破碎、搅拌,并具备自清洁功能,实现物料均匀热解功能,从而保证物料颗粒在反应器运行时运动轨迹的流畅性,避免局部滞留,引起堵料。
所述助热解叶片8的重叠宽度<0.5d,以形成剪切面,使反应器运转时能有效破除固体废弃物引起的缠绕、结块、搭桥、堵塞现象,并将大颗粒固体废弃物破碎至小粒径。
所述的助热解叶片8具有搅拌功能,使固体热载体与固体废弃物均匀混合,固体废弃物均匀受热,更利于高温固体热载体对固体废弃物的传热及发生热解反应,并保持同时段热解程度均匀性。
所述助热解叶片8的顶端设有防磨结构,防磨结构采用堆焊硬质合金或加可拆卸防磨套的方式,以增强助热解叶片8的耐磨性、检修便利性,避免助热解叶片8频繁损坏更换。
在所述反应器壳体1的顶盖低段设有相邻的固体热载体进料口3和固体废弃物进料口2,以缩短固体废弃物和固体热载体下料路程,减小物料对反应器中心轴7和助热解叶片8的冲蚀度,延长中心轴7和助热解叶片8的使用寿命。同时,固体热载体进料口3在固体废弃物进料口2之前,使固体热载体通过固体热载体进料口3进入反应器壳体1内部,并向后推进,推进过程中与低温固体废弃物接触并加热,减少低温固体废弃物原料在反应器初始段堵料机率。
在所述反应器壳体1的顶盖高段设置热解气出口4,在热解气出口4的内部设有除尘装置5,结合反应器壳体1顶盖自除尘功能结构,进一步降低热解气出口4的含尘量,减少后续系统除尘压力,实现反应器多功能目的。
在所述反应器壳体1的底板尾端设置残碳出口6,用于排出热解反应产物。
在所述反应器壳体1的外部设置支撑装置12,支撑装置可采用鞍式支座或钢结构支撑形式,设置固定端和滑动端,以吸收反应器壳体1的整体热膨胀量,并以简单结构设计方式,解决在大规模处理量、设备操作重量≥300吨时的支撑强度难题。
本发明一种用于固体热载体加热的热解反应器,工作过程如下:
固体热载体与固体废弃物同时分别进入热解反应器输送区,固体热载体位于固体废弃物前端,通过传动装置11控制中心轴7的转速和转向,使高温固体热载体推动固体废弃物进入混合搅拌区,并对助热解叶片8进行合理的布置,使固体热载体与固体废弃物在反应器壳体1内充分混合、搅拌均匀、剪切破碎、均匀热解,并根据热解产物要求控制热解停留时间,最终完成热解反应。热解产生的气相产物经过壳体1及除尘装置5,完成热解气自除尘,通过热解气出口4排出;产生的热解残碳和固体热载体混合物通过残碳出口6排出,最终实现固体热载体热解反应器的连续运行。
本文用于企业家、创业者技术爱好者查询,结果仅供参考。