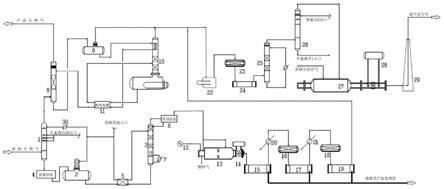
1.本公开涉及天然气净化领域,具体涉及一种处理高硫天然气的系统和方法。
背景技术:
2.天然气是一种优质、高效、清洁的低碳能源。2015年天然气占我国一次能源消费比例为5.9%,2020年将达8.3-10%。我国天然气资源匮乏,对外依存度不断增大。近年来四川地区探明的高酸天然气藏资源十分丰富,随着勘探开发一体化的快速推进,整个气田的数千亿方级储量规模将被逐步探明和评价,建设大型天然气生产基地的资源基础将进一步夯实。
3.天然气及油田伴生气中,均含有一定量的硫化物(h2s,cos,cs2,rsh,rsr)及co2。目前探明的高硫高酸气田,从气田采出的天然气在作为商品气输出之前,必须对其进行处理,将其中的硫含量、二氧化碳含量降低到一定值,以达到国家管输标准并符合商品气的要求。
4.高酸性高碳硫比气田天然气的净化难度高,原因在于该组成天然气不但为高含硫天然气,而且天然气组分中co2/h2s高,并且还含有cos、甲硫醇、乙硫醇等多种成分的有机硫,且由于co2/h2s高,溶剂再生部分酸性气体中h2s浓度远远低于炼厂硫磺回收装置中酸性气体浓度,这大大增加了硫磺回收装置的设计与操作难度。因此,亟需开发出一种针对高碳硫比、高有机硫含量的成套的天然气处理技术。
技术实现要素:
5.本公开的目的是提供一种系统和方法,该系统和方法能够针对高碳硫比、高有机硫含量的天然气进行连续成套的处理,使天然气产品满足国家天然气标准,并能提高低浓度的酸性气体中硫磺的回收率。
6.为了实现上述目的,本公开的第一方面提供一种处理高硫天然气的方法,该方法包括如下步骤:
7.s1,使高硫天然气原料进入复合溶剂法脱硫单元,在天然气脱硫塔内与贫溶剂接触进行吸收脱硫,从塔顶得到脱硫后天然气,从塔底得到富溶剂;使所述富溶剂经闪蒸并换热后进入溶剂再生塔进行再生,得到酸性气体和再生后贫溶剂;
8.s2,使步骤s1中得到的所述脱硫后天然气进入三甘醇法脱水单元,在天然气脱水塔中与脱水剂接触进行脱水,从所述天然气脱水塔的塔顶和塔底分别得到产品天然气和富脱水剂,使所述富脱水剂经过闪蒸后进入脱水剂再生塔进行溶剂再生;再生后的脱水剂经换热后循环回所述天然气脱水塔;所述闪蒸的闪蒸尾气与所述脱水剂再生塔的塔顶尾气作为天然气脱水单元尾气送入加氢还原吸收尾气处理单元;
9.s3,使步骤s1中得到的所述酸性气体进入克劳斯分流法硫磺回收单元,其中一部分所述酸性气体进入克劳斯反应炉的第一区与氧气接触反应,另一部分所述酸性气体进入所述克劳斯反应炉的第二区与从所述第一区来的反应混合气接触反应,从所述克劳斯反应炉得到的高温过程气经换热后进行克劳斯反应,得到液硫和硫磺回收尾气;
10.s4,使步骤s3中得到的所述硫磺回收尾气与所述天然气脱水单元尾气混合后进入所述加氢还原吸收尾气处理单元,依次进行燃烧反应、加氢反应、尾气急冷处理、尾气吸收反应和尾气焚烧,得到外排烟气;其中所述尾气吸收反应使用至少部分步骤s1得到的所述再生后贫溶剂,并使所述尾气吸收反应得到的富溶剂返回所述溶剂再生塔进行再生。
11.可选地,所述高硫天然气原料中co2与h2s的摩尔比co2/h2s为1.0-2.0,有机硫的含量为300-600mg/m3;所述酸性气体中h2s的含量为20-70mol%。
12.可选地,步骤s3还包括:使所述反应高温过程气经热量回收后依次进入一级硫冷凝器、一级克劳斯反应器、二级硫冷凝器、二级克劳斯反应器和末级硫冷凝器,从所述末级硫冷凝器得到所述硫磺回收尾气,并分别从一级硫冷凝器、二级硫冷凝器和末级硫冷凝器的出口得到所述液硫;并且/或者,
13.步骤s4还包括:使所述硫磺回收尾气与所述天然气脱水单元尾气混合后进入加氢进料燃烧炉进行燃烧反应,所得混合气体进入加氢反应器进行所述加氢反应,得到加氢尾气;使所述加氢尾气依次经过加氢反应出口冷却器和急冷塔进行所述尾气急冷处理后进入尾气吸收塔与所述贫溶剂接触进行所述尾气吸收反应,从所述尾气吸收塔的塔底得到所述富溶剂,从所述尾气吸收塔的塔顶得到的塔顶气经尾气焚烧炉得到所述烟气;使所述烟气经焚烧炉余热锅炉和烟囱后排放至大气。
14.可选地,步骤s1中,所述天然气脱硫塔的操作压力为2.0-10.0mpa(g),所述溶剂再生塔的操作压力为0.1-0.2mpa(g);所述贫为物理吸收剂和化学吸收剂中的至少一种;
15.步骤s1中还包括使所述再生后贫溶剂分别经贫富溶剂换热器和溶剂冷却器冷却后进入所述天然气脱硫塔,其中,所述高硫天然气原料中cos与硫醇的体积含量之比为1.0-3.0时,使所述溶剂冷却器出口温度为42-48℃;所述高硫天然气原料中cos与硫醇的体积含量之比为0.2-1.0时,使所述溶剂冷却器出口温度为35-42℃。
16.可选地,步骤s2中,使所述闪蒸后的富脱水剂进入所述脱水剂再生塔10上部与含有水和轻烃的混合气体进行换热。
17.可选地,步骤s3中,以所述酸性气体的总体积为基准,进入所述第一区的酸性气体的体积比例为35%-100%;所述第一区的反应温度为950-1500℃,所述克劳斯反应的热反应总转化率为60%以上。
18.为了实现上述目的,本公开的第二方面提供一种采用本公开的第一方面的方法处理高硫天然气的系统,该系统包括原料天然气入口、复合溶剂法脱硫单元、三甘醇法脱水单元、克劳斯分流法硫磺回收单元、加氢还原吸收尾气处理单元、产品天然气出口、尾气出口和液硫出口;其中,
19.所述复合溶剂法脱硫单元包括天然气脱硫塔、富溶剂闪蒸装置和溶剂再生塔;所述原料天然气入口与所述天然气脱硫塔的气体入口连通,所述溶剂再生塔的再生溶剂出口分别与所述天然气脱硫塔的脱硫溶剂入口和所述加氢还原吸收尾气处理单元的液体入口连通;
20.所述三甘醇法脱水单元包括依次连接的天然气脱水塔、脱水剂闪蒸罐、脱水剂换热装置和脱水剂再生塔;所述天然气脱水塔的气体入口与所述天然气脱硫塔的塔顶气出口连通,所述天然气脱水塔的塔顶气出口与所述产品天然气出口连通,所述脱水剂再生塔的顶部气体出口与所述加氢还原吸收尾气处理单元的气体入口连通;
21.所述克劳斯分流法硫磺回收单元包括克劳斯反应炉、反应炉余热锅炉、多级加热器、多级克劳斯反应器和多级硫冷凝器;所述克劳斯反应炉包括气体连通的第一区和第二区,所述加氢还原吸收尾气处理单元的气体入口分别与所述第一区和所述第二区连通,所述克劳斯反应炉还包括与所述第一区连通的燃料气入口,所述第二区的出口依次与所述反应炉余热锅炉和一级硫冷凝器的入口连通,末级硫冷凝器的气体出口与所述天然气脱水单元尾气出口连通;所述多级硫冷凝器的液体出口分别与所述液硫出口连通;
22.所述加氢还原吸收尾气处理单元包括尾气焚烧炉和依次连接的加氢进料燃烧炉、加氢反应器、加氢反应出口冷却器、急冷塔、尾气吸收塔,所述尾气吸收塔的气体出口与所述尾气焚烧炉的入口连通,所述尾气吸收塔的液体出口与所述天然气脱硫塔的富溶剂入口连通。
23.可选地,所述克劳斯分流法硫磺回收单元包括依次连通的所述一级硫冷凝器、二级硫冷凝器和所述末级硫冷凝器,所述一级硫冷凝器与所述二级硫冷凝器之间依次设有一级加热器和一级克劳斯反应器,所述二级硫冷凝器与所述末级硫冷凝器之间依次设有二级加热器和二级克劳斯反应器;所述一级硫冷凝器、二级硫冷凝器和所述末级硫冷凝器的液体出口分别与所述液硫出口连通;并且/或者,
24.所述加氢还原吸收尾气处理单元还包括余热锅炉和烟囱;所述尾气焚烧炉的气体出口与所述余热锅炉、所述烟囱依次连通,所述烟囱的出口与外界大气连通。
25.可选地,所述天然气脱硫塔的再生后贫溶剂入口处还设有贫富溶剂换热器和溶剂冷却器;
26.所述脱水剂再生塔上部设有换热设备,所述换热设备的入口与所述脱水剂闪蒸罐的液体出口连通,所述换热设备的出口与所述脱水剂换热装置的低温介质入口连通;
27.可选地,所述复合溶剂法脱硫单元还包括能量回收装置和贫富溶剂换热器;所述能量回收装置设置于所述天然气脱硫塔的富溶剂出口与所述富溶剂闪蒸装置的液体入口之间,所述贫富溶剂换热器设置于所述富溶剂闪蒸装置与所述溶剂再生塔之间。
28.本公开通过复合溶剂法脱硫、三甘醇法脱水、克劳斯分流法硫磺回收、加氢还原吸收尾气处理,实现了对高碳硫比、高含硫的天然气的连续处理以及对低酸性气浓度尾气的硫磺回收,使得产品天然气达到国际一类气标准,总硫回收率达到99.9%以上;将天然气脱水单元尾气引入加氢进料燃烧炉进行加氢还原反应,充分利用了尾气中的还原性气体,同时减少了加氢进料燃烧炉还原蒸汽的注入量;而且,所用克劳斯分流反应器能够通过控制分流条件提高炉膛温度保证稳定燃烧,提升热反应转化率,减少杂质对下游催化转化的影响,提高下游硫磺回收装置对不同酸性气浓度的适应性;同时,复合溶剂法脱硫单元与加氢还原吸收尾气处理单元采用同一溶剂循环使用,在保证天然气净化效果和尾气达标排放的基础上,充分利用了溶剂的吸收能力,降低了装置脱硫溶剂的用量及再生能耗。
29.本公开的其他特征和优点将在随后的具体实施方式部分予以详细说明。
附图说明
30.附图是用来提供对本公开的进一步理解,并且构成说明书的一部分,与下面的具体实施方式一起用于解释本公开,但并不构成对本公开的限制。在附图中:
31.图1是本公开的处理高硫天然气的方法的一种具体实施方式的工艺流程图。
32.附图标记说明
33.1.天然气脱硫塔2.富溶剂闪蒸装置3.溶剂再生塔
34.4.能量回收装置5.贫富溶剂换热器6.再生塔顶回流装置
35.7.重沸器8.天然气脱水塔9.脱水剂闪蒸罐
36.10.脱水剂再生塔11.换热装置12.克劳斯风机
37.13.克劳斯反应炉14.反应炉余热锅炉15.一级硫冷凝器
38.16.克劳斯一级反应器17.二级硫冷凝器18.克劳斯二级反应器
39.19.末级硫冷凝器20.一级加热器21.二级加热器
40.22.加氢进料燃烧炉23.加氢反应器24.加氢反应出口冷却器
41.25.急冷塔26.尾气吸收塔27.尾气焚烧炉
42.28.焚烧炉余热锅炉29.烟囱30.溶剂冷却器
具体实施方式
43.以下结合附图对本公开的具体实施方式进行详细说明。应当理解的是,此处所描述的具体实施方式仅用于说明和解释本公开,并不用于限制本公开。
44.在本公开中,在未作相反说明的情况下,使用的方位词如“上、下”通常是指装置在正常使用状态下的上和下,具体可参考图1的图面方向。“内、外”是指针对装置本身的轮廓而言的。
45.如图1所示,本公开第一方面提供一种处理高硫天然气的方法,该方法包括如下步骤:
46.s1,使高硫天然气原料进入复合溶剂法脱硫单元,在天然气脱硫塔1内与贫溶剂接触进行吸收脱硫,从塔顶得到脱硫后天然气,从塔底得到富溶剂;使富溶剂经闪蒸并换热后进入溶剂再生塔3进行再生,得到酸性气体和再生后贫溶剂;
47.s2,使步骤s1中得到的脱硫后天然气进入三甘醇法脱水单元,在天然气脱水塔8中与脱水剂接触进行脱水,从天然气脱水塔8的塔顶和塔底分别得到产品天然气和富脱水剂,使富脱水剂经过闪蒸后进入脱水剂再生塔10进行溶剂再生;再生后的脱水剂经换热后循环回天然气脱水塔8;闪蒸的闪蒸尾气与脱水剂再生塔10的塔顶尾气作为天然气脱水单元尾气送入加氢还原吸收尾气处理单元;
48.s3,使步骤s1中得到的酸性气体进入克劳斯分流法硫磺回收单元,其中一部分酸性气体进入克劳斯反应炉13的第一区与氧气接触反应,另一部分酸性气体进入克劳斯反应炉13的第二区与从第一区来的反应混合气接触反应,从克劳斯反应炉13得到的高温过程气经换热后进行克劳斯反应和冷凝分离,得到液硫和硫磺回收尾气;
49.s4,使步骤s3中得到的硫磺回收尾气与天然气脱水单元尾气混合后进入加氢还原吸收尾气处理单元,依次进行燃烧反应、加氢反应、尾气急冷处理、尾气吸收反应和尾气焚烧,得到外排烟气;其中尾气吸收反应使用至少部分步骤s1得到的再生后贫溶剂,并使尾气吸收反应得到的富溶剂返回溶剂再生塔3进行再生。
50.本公开通过复合溶剂法脱硫、三甘醇法脱水、克劳斯分流法硫磺回收、加氢还原吸收尾气处理,实现了对高碳硫比、高含硫的天然气的连续处理以及对低酸性气浓度尾气的硫磺回收,使得产品天然气达到国际一类气标准,总硫回收率达到99.9%以上;将天然气脱
水单元尾气引入加氢进料燃烧炉进行加氢还原反应,充分利用了尾气中的还原性气体,同时减少了加氢进料燃烧炉还原蒸汽的注入量;而且,所用克劳斯分流反应器能够通过控制分流条件提高炉膛温度保证稳定燃烧,提升热反应转化率,减少杂质对下游催化转化的影响,提高下游硫磺回收装置对不同酸性气浓度的适应性;同时,复合溶剂法脱硫单元与加氢还原吸收尾气处理单元采用同一溶剂循环使用,在保证天然气净化效果和尾气达标排放的基础上,充分利用了溶剂的吸收能力,降低了装置脱硫溶剂的用量及再生能耗。
51.根据本公开,对所处理的原料天然气的硫含量没有限制,为了能够处理硫含量较高的天然气原料,以达到天然气国际一类气标准同时提高总硫回收率。在本公开的一种具体实施方式中,高硫天然气原料中co2与h2s的摩尔比co2/h2s可以为1.0-2.0,优选地可以为1.0-1.7;有机硫的含量可以为300-600mg/m3,优选地可以为350-550;酸性气体中h2s的含量可以为20-70mol%,优选地可以为30-50mol%。
52.根据本公开,为了使硫磺回收单元反应更加充分,提高硫磺回收率并得到液硫产品,可以采用多级冷凝、多级反应的方法,例如采用三级硫冷凝和两级克劳斯反应的方法。在本公开的一种具体实施方式中,步骤s3还可以包括:使反应高温过程气经热量回收后依次进入一级硫冷凝器15、一级克劳斯反应器16、二级硫冷凝器17、二级克劳斯反应器18和末级硫冷凝器19,从末级硫冷凝器19得到硫磺回收尾气,并分别从一级硫冷凝器15、二级硫冷凝器17和末级硫冷凝器19的出口得到液硫。
53.为了进一步回收三甘醇法脱水单元和克劳斯分流法硫磺回收单元尾气中的含硫气体,达到国家尾气排放标准。在本公开的一种具体实施方式中,步骤s4还包括:使硫磺回收单元得到的硫磺回收尾气与三甘醇法脱水单元得到的天然气脱水单元尾气混合后进入加氢还原吸收尾气处理单元的加氢进料燃烧炉22进行燃烧反应,所得混合气体进入加氢反应器23进行加氢反应,得到加氢尾气;使加氢尾气依次经过加氢反应出口冷却器24和急冷塔25进行尾气急冷处理后进入尾气吸收塔26,与贫溶剂接触进行尾气吸收反应,从尾气吸收塔26的塔底得到富溶剂,从尾气吸收塔26的塔顶得到的塔顶气进入尾气焚烧炉27进行焚烧得到烟气;使烟气经焚烧炉余热锅炉28和烟囱29后排放至大气。其中,尾气吸收塔26使用的贫溶剂来自复合溶剂法脱硫单元的溶剂再生塔3。
54.根据本公开,对天然气脱硫塔1和溶剂再生塔3的操作条件没有限制,天然气脱硫塔1的操作压力可以为2.0-10.0mpa(g),优选地可以为5.0-6.0mpa(g),溶剂再生塔3的操作压力可以为0.1-0.2mpa(g),优选地可以为0.12-0.14mpa(g);贫溶剂可以包含物理吸收剂和化学吸收剂中的至少一种,优选地可以为胺类、环胺类物理吸收剂或化学吸收剂中的至少一种。
55.高硫天然气原料中的有机硫主要为cos和硫醇,为了进一步提高高硫天然气原料中的有机硫脱除率,在根据本公开的一种具体实施方式中,步骤s1中还可以包括使溶剂再生塔3中的再生后贫溶剂与来自富溶剂闪蒸装置2中的富溶剂在贫富溶剂换热器5中进行换热后,经溶剂冷却器30冷却后进入天然气脱硫塔1,高硫天然气原料中cos与硫醇的体积含量之比为1.0-3.0,优选地可以为1.5-3.0时,使溶剂冷却器30出口温度为42-48℃,优选地可以为45℃,以提高cos脱除率;高硫天然气原料中cos与硫醇的体积含量之比为0.2-1.0,优选地可以为0.3-0.8时,使溶剂冷却器30出口温度为35-42℃,优选地可以为36-38℃,以提高硫醇脱除率。
56.在根据本公开的一种具体实施方式中,如图1所示,闪蒸后的富脱水剂可以进入脱水剂再生塔10上部与含有水和轻烃的混合气体进行换热,然后再与来自脱水剂再生塔10的再生后贫溶剂进行换热,换热后的富脱水剂进入脱水剂再生塔10进行再生反应。这一实施方式中,能够将富脱水剂中解吸出来的温度较高的气体中的热量进一步回收利用,从而降低了脱水剂再生过程中的热量损失和装置能耗。
57.在根据本公开的一种具体实施方式中,步骤s3中,为了进一步提高对不同酸性气浓度的适应性、提高克劳斯反应炉炉膛温度及热反应转化率,以酸性气体的总体积为基准,进入第一区酸性气体的体积比例为35-100%;第一区的反应温度可以为950-1400℃。优选地,进入第一区酸性气体的体积比例可以为45-90%;第一区的反应温度可以为1100-1300℃。
58.根据本公开,克劳斯反应的热反应总转化率可以为60%以上,其中,热反应总转化率是指进入反应炉的酸性气中h2s转化为单质硫的比例,其值为反应炉出口过程气中单质硫含量与反应炉入口酸性气中h2s含量的摩尔百分比。以上范围内的克劳斯反应能够更好的保证稳定燃烧,提升热反应转化率,减少杂质对下游催化转化的影响,提高下游硫磺回收装置对不同酸性气浓度的适应性。
59.如图1所示,本公开第二方面提供一种采用本公开的第一方面的方法处理高硫天然气的系统,该系统包括原料天然气入口、复合溶剂法脱硫单元、三甘醇法脱水单元、克劳斯分流法硫磺回收单元、加氢还原吸收尾气处理单元、产品天然气出口、尾气出口和液硫出口;其中,
60.复合溶剂法脱硫单元包括天然气脱硫塔1、富溶剂闪蒸装置2和溶剂再生塔3;原料天然气入口与天然气脱硫塔1的气体入口连通,溶剂再生塔3的再生溶剂出口分别与天然气脱硫塔1的脱硫溶剂入口和加氢还原吸收尾气处理单元的溶剂入口连通;三甘醇法脱水单元包括依次连接的天然气脱水塔8、脱水剂闪蒸罐9、脱水剂换热装置11和脱水剂再生塔10;天然气脱水塔8的气体入口与天然气脱硫塔1的塔顶气出口连通,天然气脱水塔8的塔顶气出口与产品天然气出口连通,脱水剂再生塔10的顶部气体出口与加氢还原吸收尾气处理单元的气体入口连通;
61.克劳斯分流法硫磺回收单元包括克劳斯反应炉12、反应炉余热锅炉14、多级加热器、多级克劳斯反应器和多级硫冷凝器;克劳斯反应炉包括气体连通的第一区和第二区,加氢还原吸收尾气处理单元的气体入口分别与第一区和第二区连通,克劳斯反应炉12还包括与第一区连通的燃料气入口,第二区的出口依次与反应炉余热锅炉14和一级硫冷凝器15的入口连通,末级硫冷凝器19的气体出口与天然气脱水单元尾气出口连通;多级硫冷凝器的液体出口分别与液硫出口连通;
62.加氢还原吸收尾气处理单元包括尾气焚烧炉和依次连接的加氢进料燃烧炉22、加氢反应器23、加氢反应出口冷却器24、急冷塔25、尾气吸收塔26,尾气吸收塔26的气体出口与尾气焚烧炉27的入口连通,尾气吸收塔26的液体出口与天然气脱硫塔1的富溶剂入口连通。
63.本公开的系统实现了对高碳硫比、高含硫的天然气的连续处理以及对低酸性气浓度尾气的硫磺回收,使得产品天然气达到国际一类气标准,总硫回收率达到99.9%以上;将天然气脱水单元尾气引入加氢进料燃烧炉进行加氢还原反应,充分利用了尾气中的还原性
气体,同时减少了加氢进料燃烧炉还原蒸汽的注入量;并且,所用克劳斯分流反应器通过控制分流条件提高了炉膛温度及热反应转化率,减少了杂质对下游催化转化的影响,提高了下游硫磺回收装置对不同酸性气浓度的适应性;同时,天然气脱硫塔与尾气吸收塔采用同一溶剂循环使用,在保证天然气净化效果和尾气达标排放的基础上,充分利用了溶剂的吸收能力,降低了装置脱硫溶剂的用量及再生能耗。
64.根据本公开,克劳斯分流法硫磺回收单元可以包括多级硫冷凝器和多级加热器、多级克劳斯反应器,以进一步充分去除和回收尾气中的硫,在得到液硫产品的同时提高硫磺回收率。在本公开的一种具体实施方式中,克劳斯分流法硫磺回收单元还可以包括依次连通的一级硫冷凝器15、二级硫冷凝器17和末级硫冷凝器19;进一步地,一级硫冷凝器15与二级硫冷凝器17之间可以依次设有一级加热器20和一级克劳斯反应器16,二级硫冷凝器17与末级硫冷凝器19之间可以依次设有二级加热器21和二级克劳斯反应器18;一级硫冷凝器15、二级硫冷凝器17和末级硫冷凝器19的液体出口可以分别与液硫出口连通,以回收液硫。
65.为了进一步使得系统最终排放的尾气达到国家尾气排放标准,在根据本公开的一种具体实施方式中,加氢还原吸收尾气处理单元还可以包括余热锅炉28和烟囱29,余热锅炉28和烟囱29可以依次连接在尾气焚烧炉27的气体出口,烟囱29的出口可以与外界大气连通。
66.根据本公开,天然气脱硫塔1的再生后贫溶剂入口处还可以设有贫富溶剂换热器5和溶剂冷却器30,溶剂再生塔3中的再生后贫溶剂与来自富溶剂闪蒸装置2中的富溶剂在贫富溶剂换热器5中进行换热后,在溶剂冷却器30中进一步冷却,以充分利用再生后贫溶剂的热量,降低装置能耗,同时通过调节进入天然气脱硫塔1的贫溶剂的温度,使得天然气脱硫塔1能够针对不同有机硫分布的天然气原料,在不同的贫溶剂温度下脱除cos和硫醇,满足天然气净化要求,扩大了装置的处理范围。
67.为了进一步回收利用脱水剂再生塔10上部的含有水和轻烃的混合气体中的热量,可以在塔的上部设置间壁式换热设备,如列管式、u型管式或蛇形管式,或者其他热量回收装置,如冷却盘管。在根据本公开的一种具体实施方式中,脱水剂再生塔10上部可以设有换热设备,换热设备的入口可以与脱水剂闪蒸罐9的液体出口连通,换热设备的出口可以与脱水剂换热装置11的低温介质入口连通;以使闪蒸后的富脱水剂进入脱水剂再生塔10上部与含有水和轻烃的混合气体进行换热,然后再与来自脱水剂再生塔10的再生后贫溶剂进行换热,换热后的富脱水剂进入脱水剂再生塔10进行再生反应。这一实施方式中,能够将富脱水剂中解吸出来的温度较高的气体中的热量进一步回收利用,从而降低了脱水剂再生过程中的热量损失和装置能耗。
68.在根据本公开的一种具体实施方式中,复合溶剂法脱硫单元还可以包括能量回收装置4和贫富溶剂换热器5;能量回收装置4可以设置于天然气脱硫塔的富溶剂出口与富溶剂闪蒸装置2的液体入口之间,例如设置于天然气脱硫塔的底部,以进一步回收从天然气脱硫塔1内流出的富溶剂中的热量;贫富溶剂换热器5可以设置于富溶剂闪蒸装置2与溶剂再生塔3之间,能量回收装置可以为本领域常规种类,如液力透平及热量回收设施,以充分利用装置的热量节省能耗。
69.下面通过实施例来进一步说明本公开,但是本公开并不因此而受到任何限制。
70.实施例1
71.本实施例用于说明本公开的天然气净化成套系统及工艺。
72.如图1所示,本实施例中,天然气净化成套系统包括了复合溶剂法脱硫单元、三甘醇法脱水单元、克劳斯灵活分流硫磺回收单元和加氢还原吸收尾气处理单元。
73.表1
[0074][0075]
天然气原料组成如上表1所示:其中,天然气原料中co2与h2s的摩尔比co2/h2s为1.34,有机硫中cos与硫醇的体积含量之比为0.38,此时溶剂冷却器30出口温度为36℃。
[0076]
具体地,天然气净化成套工艺包括如下步骤:
[0077]
1)使原料天然气进入复合溶剂法脱硫单元,在天然气脱硫塔1内与贫溶剂接触,脱除h2s、部分co2及其余硫化物,得到脱硫后天然气(h2s含量小于等于6mg/m3,co2摩尔分数小于等于3%);脱硫后富溶剂经塔底能量回收装置4(液力透平)回收热量后送至富溶剂闪蒸装置2进行闪蒸,使闪蒸后富溶剂经贫富溶剂换热器5(富溶剂100℃,0.4mpa(g))进入溶剂再生塔3(塔底操作温度120-130℃,操作压力0.15mpa(g))进行再生,其中,塔底所得再生后的脱硫溶剂(贫胺液,总流量为380t/h)分别送至天然气脱硫塔1和加氢还原吸收尾气单元尾气吸收塔26,塔顶所得酸性气(h2s的含量为40.6mol%)送至克劳斯分流法硫磺回收单元。
[0078]
2)使步骤1)中所得到的脱硫天然气进入三甘醇法脱水单元天然气脱水塔8中进行脱水后,作为合格产品天然气送出界区;塔底富脱水剂送入脱水剂闪蒸罐9闪蒸,再生塔内的上部设有冷却盘管(热量回收装置)),闪蒸后的富脱水剂进入脱水剂再生塔10上部的冷却盘管与含有水和轻烃的混合气体进行换热,然后进入脱水剂换热装置11再与来自脱水剂再生塔10的再生后贫溶剂进行换热,换热后的富脱水剂进入脱水剂再生塔10进行再生反应,再生后贫溶剂由脱水剂换热装置11冷却至45℃后返回天然气脱水塔8循环利用。
[0079]
3)步骤1)中所得酸性气送至克劳斯分流法硫磺回收单元,酸性气在控制系统作用下分两路分别进入克劳斯反应炉13的第一区与第二区,根据本实例实际工况,以酸性气体的总体积为基准,进入第一区与进入第二区的酸性气的体积比分别为67.6%:32.4%,由克劳斯风机12提供反应所需空气,此时第一区的燃烧温度为1050-1070℃,反应稳定燃烧,克劳斯反应的热反应总转化率为63.7%;反应完成后,使高温过程气进入与反应炉直接相连的反应炉余热锅炉14进行热量回收并产生蒸汽,然后将余热锅炉产生的过程气依次送入一级硫冷凝器15、克劳斯一级反应器16、二级硫冷凝器17、克劳斯二级反应器18和末级硫冷凝
器19,从末级硫冷凝器19所得硫磺回收尾气送入加氢还原尾气处理单元,各级硫冷凝器出口所得液体送至液硫产品区进行后续处理。
[0080]
4)将步骤3)中所得硫磺回收尾气与步骤2)中所得天然气脱水单元尾气混合后依次送入加氢还原吸收尾气处理单元的加氢进料燃烧炉22、加氢反应器23,使混合气中的二氧化硫及其他含硫物质发生加氢反应被还原为硫化氢,羰基硫和二硫化物则发生水解反应生成硫化氢;使加氢反应器23中的气体经急冷塔25降温后(温度为35-40℃)进入尾气吸收塔26,脱除尾气中的硫化氢,其中,尾气吸收塔26塔顶的贫溶剂(贫胺液)来自复合溶剂法脱硫单元的再生后贫溶剂,塔底生成的富溶剂返回复合溶剂法脱硫单元的溶剂再生塔3进行再生;
[0081]
5)使步骤4)中尾气吸收塔26塔顶产生的塔顶气进入尾气焚烧炉27,将尾气中未被吸收的硫化氢和其它硫化物氧化为二氧化硫,最终经余热锅炉28回收热量后由烟囱29排入大气。
[0082]
实施例2
[0083]
采用实施例1的方法处理高硫天然气,不同之处仅在于,高硫原料气的有机硫中cos与硫醇的体积含量之比为1.06,此时溶剂冷却器30出口温度为45-48℃。
[0084]
实施例3
[0085]
采用实施例1的方法处理高硫天然气,不同之处仅在于,步骤s1中未使用溶剂冷却器30。
[0086]
实施例4
[0087]
采用实施例1的方法处理高硫天然气,不同之处仅在于,步骤3)中,以酸性气体的总体积为基准,进入第一区与进入第二区的酸性气的体积比为36%:64%,此时第一区的燃烧温度为1420-1500℃,克劳斯反应的热反应总转化率为60%。
[0088]
实施例5
[0089]
采用实施例1的方法处理高硫天然气,不同之处仅在于,天然气原料中co2含量6.57mol%,h2s含量5.55mol%,co2与h2s的摩尔比co2/h2s为1.18,有机硫的含量为362mg/m3;有机硫中cos与硫醇的体积含量之比为0.71,溶剂冷却器出口温度为39℃,复合溶剂法脱硫单元中所得酸性气体的h2s含量为44.6mol%,以酸性气体的总体积为基准,进入第一区与进入第二区的酸性气的体积比分别为67.6%:32.4%,反应炉一区操作温度1090-1150℃,热转化率64.1%。
[0090]
对比例1
[0091]
步骤1)中采用常规天然气脱硫方法处理高硫天然气,步骤3)中克劳斯反应炉13采用传统分流流程进行反应,一部分酸性气进入反应炉13,反应炉出口的过程气经过余热锅炉14冷却后与另一部分酸性气混合进入克劳斯反应器16,以酸性气体的总体积为基准,进入反应炉与进入克劳斯反应器的酸性气的体积比分别为67.6%:32.4%,热转化率为37.5%,反应器存在积碳问题,催化剂寿命较本公开缩短10%以上。
[0092]
测定上述实施例1-5和对比例1中脱硫后天然气(产品天然气)、酸性气组成、cos脱除率、硫醇脱除率、反应炉温度及热转化率等进行对比,结果如表2所示。
[0093]
表2
[0094][0095]
以上结合附图详细描述了本公开的优选实施方式,但是,本公开并不限于上述实施方式中的具体细节,在本公开的技术构思范围内,可以对本公开的技术方案进行多种简单变型,这些简单变型均属于本公开的保护范围。
[0096]
另外需要说明的是,在上述具体实施方式中所描述的各个具体技术特征,在不矛盾的情况下,可以通过任何合适的方式进行组合,为了避免不必要的重复,本公开对各种可能的组合方式不再另行说明。
[0097]
此外,本公开的各种不同的实施方式之间也可以进行任意组合,只要其不违背本公开的思想,其同样应当视为本公开所公开的内容。
再多了解一些
本文用于企业家、创业者技术爱好者查询,结果仅供参考。