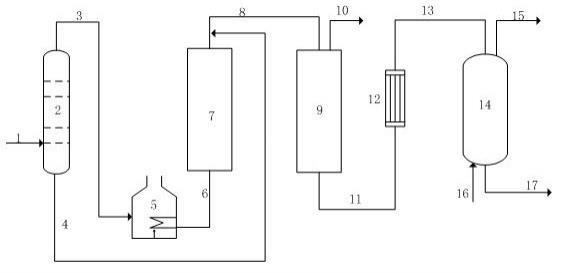
1.本发明属于中间相沥青制备技术领域,涉及一种生产中间相沥青的方法,具体地说涉及一种用于制备高端碳纤维的中间相沥青的生产方法。
背景技术:
2.中间相沥青是制备高性能沥青基炭纤维、针状焦及其他高级炭材料的原料,其本身也是一种独特的炭材料,一般要求沥青具有杂原子少、灰分含量低、芳香度高、缩合度低以及整齐的分子排列、高的碳收率、较好的流动性等特点。较好的中间相结构的形成还需要有较好的平面度,这是中间相结构的基础。
3.日本专利no.167788/81介绍了从石油催化裂化渣油制备中间相沥青的方法,首先用溶剂抽提去除渣油中的灰分杂质及催化剂颗粒,然后再经多级溶剂处理获得适宜作为中间相沥青前驱体的组份,再经热处理得到中间相沥青。上述方法制备工艺复杂,制备成本高,炭纤维的性能提高幅度却不大。
4.中国专利cn105238431a公开了一种催化油浆氢化还原-共炭化制备中间相沥青的方法,以环烷基或中间基原油的 fcc 油浆作为原料,在alcl3催化剂的作用下,得到高品质的中间相沥青。但alcl3与沥青的反应使其分离与回收变得困难,影响了最终中间相沥青的应用。
5.中国专利cn101525543a公开了一种中间相沥青的制备方法,由于采用的hf、bf3为催化剂,具有很强的腐蚀性和毒性,对设备的要求很高,而且带来操作防护的问题,使得这种沥青的产业化存在着成本高、风险大的缺点。中国专利cn103059893a公开了一种电化学催化制备中间相沥青的方法,在热缩聚的过程中通入直流电,操作过程复杂,装置设计苛刻,难以工业化生产。
技术实现要素:
6.针对现有技术的不足,本发明公开一种生产中间相沥青的方法,所述方法生产的中间相沥青可以作为高性能沥青基碳纤维的原料。
7.一种生产中间相沥青的方法,包括如下步骤:原料油经分馏后分离出轻、重馏分油;轻馏分油经热聚合反应后的产物同重馏分油混合进行二次热聚合反应获得中间相沥青。
8.上述方法中,所述原料可以为精制处理过的石油系原料,如乙烯焦油、热裂化渣油、石油重油或催化裂化油浆等,也可以是上述原料两种或两种以上的混合物,也可以是精制处理过的煤系原料,如煤焦油沥青等。
9.上述方法中,所述的精制处理过的石油系原料灰分含量质量分数≯0.1%,优选≯0.05%,更优选≯0.01%;硫含量质量分数≯0.5%,优选0.3%;沥青质含量质量≯5.0%,优选≯2.0%。
10.上述方法中,所述的轻馏分油10%馏出点温度为330℃-400℃,优选350℃-380℃,90%馏出点温度为440℃-500℃,优选460℃-480℃。
11.上述方法中,所述的重馏分油10%馏出点温度为450℃-520℃,优选460℃-490℃。
12.上述方法中,二次热聚合反应产物经过快速降温处理后获得中间相沥青。所述降温速率为20-150℃/min,优选30-100℃/min,快速降温至热聚合反应温度的60%-90%,优选65%-85%。
13.上述方法中,二次热聚合反应产物经过快速降温处理后进行三次热聚合反应后获得中间相沥青产品。
14.上述方法中,三次热聚合反应在负压下进行,反应压力为-0.1mpa~-0.01mpa。
15.一种生产中间相沥青的方法,具体包括如下步骤:(1)原料通过减压蒸馏装置分离出轻、重馏分油;(2)步骤(1)中轻馏分油经预热装置加热至特定温度后,进入热反应装置i;(3)热反应装置i生成的物料与步骤(1)中的重馏分油混合后进入热反应装置ii;(4)热反应装置ii生成的轻组份物料由反应器顶部出装置,重组分则由热反应装置ii底部排出进入急冷装置;(5)步骤(3)中急冷后的物料进入热反应装置iii,反应结束后获得中间相沥青产品。
16.本发明方法中,步骤(1)中所述原料可以为精制处理过的石油系原料,如乙烯焦油、热裂化渣油、石油重油或催化裂化油浆等,也可以是上述原料两种或两种以上的混合物,也可以是精制处理过的煤系原料,如煤焦油沥青等。
17.本发明方法中,步骤(1)中所述的精制原料灰分含量质量分数≯0.1%,优选≯0.05%,更优选≯0.01%;硫含量质量分数≯0.5%,优选0.3%;沥青质含量质量≯5.0%,优选≯2.0%。
18.本发明方法中,步骤(1)中所述的轻馏分油10%馏出点温度为330℃-400℃,优选350℃-380℃,90%馏出点温度为440℃-500℃,优选460℃-480℃。
19.本发明方法中,步骤(1)中所述的重馏分油10%馏出点温度为450℃-520℃,优选460℃-490℃。
20.本发明方法中,步骤(1)中所述的重馏分油出塔底后的温度为300℃-380℃,优选340℃-360℃。
21.本发明方法中,步骤(2)中所述的原料预热装置加热物料温度为350℃-450℃,优选400℃-450℃。
22.本发明方法中,步骤(2)中所述的热反应装置i的反应温度为450℃-500℃,优选450℃-480℃。
23.本发明方法中,步骤(2)中所述的热反应装置i的反应压力为1.0-10.0mpa,优选1.0-5.0mpa,更优选2.0-4.0mpa。
24.本发明方法中,步骤(2)中所述的热反应装置i内的物料停留时间为5min-120min,优选10min-60min。
25.本发明方法中,步骤(3)中所述的热反应装置ii的反应温度为380℃-440℃,优选390℃-420℃。
26.本发明方法中,步骤(3)中所述的热反应装置ii的反应压力为0.1-4.0mpa,优选0.5-2.0mpa。
27.本发明方法中,步骤(3)中所述的热反应装置ii内的物料停留时间为20min-240min,优选30min-60min。
28.本发明方法中,步骤(3)中所述的热反应装置i生成的物料与重馏分混合后的物料温度为350℃-420℃,优选380℃-400℃。
29.本发明方法中,步骤(4)中所述的经过急冷装置后的物料温度为250℃-380℃,优选300℃-350℃。
30.本发明方法中,步骤(4)中所述的急冷装置,通过的物料降温速率为20-150℃/min,优选30-100℃/min。
31.本发明方法中,步骤(5)中所述的热反应装置iii的物料温度为200℃-400℃,优选,330℃-380℃。
32.本发明方法中,步骤(5)中所述的热反应装置iii采用负压操作,压力为-0.1mpa~-0.01mpa。
33.本发明方法中,步骤(5)中所述的热反应装置iii,从反应装置底部通入水蒸气或惰性气体,其体积空速为3-30h-1
,优选5-20h-1
。
34.本发明方法中,步骤(5)中所述的热反应装置iii反应时间为1-10h,优选3-5h。
35.同现有技术相比,本发明提供的一种生产中间相的方法,具有如下有益效果:(1)本发明提供的生产中间相沥青的方法,全程不采用任何固体催化剂,,不会引入其它固体杂质,灰分含量较低;也不引入腐蚀性较强的液体或气体催化剂,工艺产业化较为容易,中间相沥青纺丝性能好;(2)本发明将原料分为轻馏分油、重馏分油,热稳定较好的轻馏分油进入高温热反应装置,而热稳定性较差的重馏分油作为急冷油与高温热反应装置的产物混合一起进入热低温反应装置,有效抑制了过聚合反应,降低喹啉不溶物含量,提升了中间相沥青的应用性能。
36.(3)本发明提供的生产中间相沥青的方法,在非临氢条件下对原料进行热处理,抑制了芳烃的迫位缩合向渺位缩合发展,提升了中间相沥青的纺丝性能,同时获得较高的中间相沥青的收率。
37.(4)本发明提供的生产中间相沥青的方法,通过独立设置减压热反应装置,提高了中间相沥青收率,提升中间相沥青的应用性能。
38.(5)本发明生产的中间相沥青,可以生产高强度、高模量碳纤维产品。
附图说明
39.图1为本发明实施例一种中间相沥青的制备方法流程图。
40.其中:1为原料,2为减压蒸馏装置,3为轻馏分油,4为重馏分油,5预热装置,6为预热后轻馏分管线,7为高温热反应装置,8为高温反应后的物料管线,9为低温热反应装置,10为生成轻馏分油,11为生成的重馏分油管线,12为急冷装置,13为急冷后物料,14为减压热反应装置,15为轻馏分产品,16为高温水蒸气或惰性气体,17为中间相沥青产品。
具体实施方式
41.下面对本发明的具体实施方式进行详细说明,但是需要指出的是,本发明的保护范围并不受这些具体实施方式的限制,本发明中所涉及到的压力均为表压。
42.原料1进入减压蒸馏装置2分离出轻馏分油3和重馏分油4,轻馏分油3经预热装置5预热后经管线6进入热反应装置7进行热聚合反应,生成的物料在反应器顶部与重馏分油4快速混合后进入低温热反应装置9,生成的轻馏分油10由反应器顶部出装置,重馏分油经管线11进入急冷装置12,急冷后的物料13进入减压热反应装置14,高温水蒸气或惰性气体16从热反应装置14底部进入,产生轻馏分油15从热反应装置顶部出装置,中间相沥青产品17从热反应装置底部出装置。
43.实施例1以某炼厂经过精制处理的催化油浆为原料,其性质分析见表1,该原料进入减压蒸馏装置分离出轻馏分油和重馏分油,轻馏分油10%馏出点温度为350℃,90%馏出点温度为450℃,重馏分油10%馏出点温度为458℃,重馏分油出塔底的温度为350℃,轻馏分油经预热装置2加热至350℃后进入热反应装置7,热反应装置2反应的温度为480℃,反应压力为3.0mpa,物料停留时间为10min,反应生产的物料与上述重馏分油混合后进入热反应装置9,混合后的物料温度为360℃,热反应装置9的反应温度为420℃,反应压力为1.5mpa,物料停留时间为40min,中间相沥青由反应器底部排出,该中间相沥青的收率及性质及见表2,采用该中间相沥青用纺丝设备在290℃下纺丝,并经碳化制成碳纤维,其性质见表2。
44.实施例2采用与实施例1相同的原料及工艺过程,只是热反应装置9反应后的物料经过急冷装置12,急冷装置12的降温速率为50℃/min,降温后的物料温度为350℃,获得中间相沥青产品的收率及性质及见表2,采用该中间相沥青用纺丝设备在275℃下纺丝,并经碳化制成碳纤维,其性质见表2。
45.实施例3采用与实施例2相同的原料及工艺过程,只是急冷装置12降温后的物料进入热反应装置14,热反应装置14的反应温度为360℃,反应压力为0.2mpa,热反应装置底部通入水蒸气,其体积空速为4h-1
,反应时间为4h。其它条件完成同实施例2相同,获得中间相沥青产品的收率及性质及见表2,采用该中间相沥青用纺丝设备在276℃下纺丝,并经碳化制成碳纤维,其性质见表2。
46.实施例4采用与实施例3相同的原料及工艺过程,只是热反应装置14的反应压力为-0.05mpa,其它条件完成同实施例3相同,获得中间相沥青产品的收率及性质及见表2,采用该中间相沥青用纺丝设备在281℃下纺丝,并经碳化制成碳纤维,其性质见表2。
47.实施例5以某炼厂经过精制处理的催化油浆为原料,其性质分析见表1,该原料进入减压蒸馏装置分离出轻馏分油和重馏分油,轻馏分油10%馏出点温度为370℃,90%馏出点温度为470℃,重馏分油10%馏出点温度为475℃,重馏分油出塔底的温度为320℃,轻馏分油经预热装置2加热至400℃后进入热反应装置7,热反应装置2反应的温度为470℃,反应压力为5.0mpa,物料停留时间为20min,反应生产的物料与上述重馏分油混合后进入热反应装置9,混合后的
物料温度为400℃,热反应装置9的反应温度为400℃,反应压力为0.3mpa,物料停留时间为70min,生产的物料进入急冷装置12降温至375℃,降温速率为120℃/min,降温后的物料进入热反应装置14,热反应装置14的反应温度为380℃,压力为-0.09mpa,热反应装置底部通入水蒸气,其体积空速为5h-1
,反应时间为3h。 该中间相沥青的收率及性质及见表2,采用该中间相沥青用纺丝设备在284℃下纺丝,并经碳化制成碳纤维,其性质见表3。
48.实施例6以某炼厂经过精制处理的催化油浆为原料,其性质分析见表1,该原料进入减压蒸馏装置分离出轻馏分油和重馏分油,轻馏分油10%馏出点温度为340℃,90%馏出点温度为450℃,重馏分油10%馏出点温度为475℃,重馏分油出塔底的温度为350℃,轻馏分油经预热装置2加热至430℃后进入热反应装置7,热反应装置2反应的温度为490℃,反应压力为3.0mpa,物料停留时间为5min,反应生产的物料与上述重馏分油混合后进入热反应装置9,混合后的物料温度为390℃,热反应装置9的反应温度为430℃,反应压力为3.0mpa,物料停留时间为40min,生产的物料进入急冷装置12降温至345℃,降温速率为60℃/min,降温后的物料进入热反应装置14,热反应装置14的反应温度为330℃,压力为-0.03mpa,热反应装置底部通入水蒸气,其体积空速为10h-1
,反应时间为8h。 该中间相沥青的收率及性质及见表2,采用该中间相沥青用纺丝设备在276℃下纺丝,并经碳化制成碳纤维,其性质见表3。
49.表1 原料性质分析表2 中间相沥青性能分析
ꢀ
表3 中间相沥青性能分析
再多了解一些
本文用于企业家、创业者技术爱好者查询,结果仅供参考。