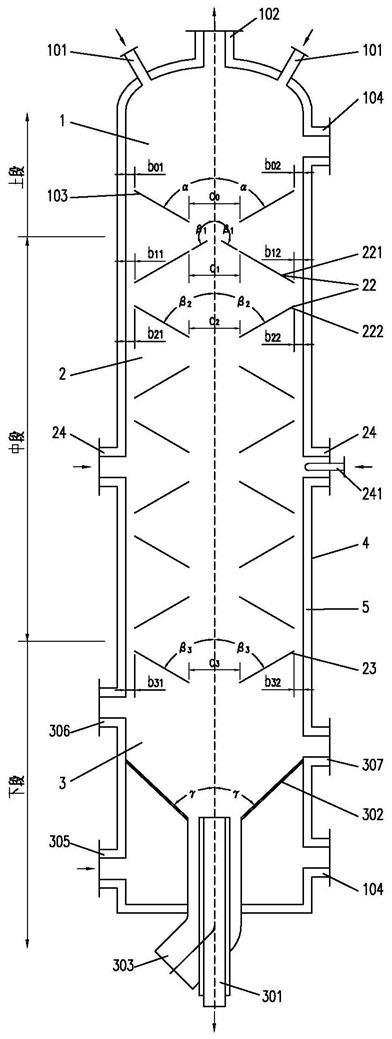
1.本申请涉及固废处理设备的领域,尤其是涉及一种燃烧火焰炉内直接给热式多级串联湍动床热解提馏炉。
背景技术:
2.随着我国经济发展与城镇化进程加快,资源消耗日益扩大,各类废弃物产量增加、废弃物形式多样化、土壤和地下水污染等问题日趋严峻。国家环保法规规定对含有机质的固体废弃物质(即:有机固废,大部分还属于危险废弃物)需进行减量化、无害化治理以达到环保排放要求,采用适当技术可实现资源化回收利用,被污染的土壤需要修复治理以达到农用或城镇化商用土质要求。
3.这些含有机质的固体废弃物质(有机固废)主要有三大类,一是工业生产过程生产的有机固废,如石油天然气开采和集输等过程产生的油田含油污泥和含油固体废弃物、石油化工生产过程产生的石化含油污泥和含有机质固体废弃物、市政公用工程如水处理厂生产的生化污泥以及造纸、纺织、印染等轻工业行业生产过程产生的含有机质固体废弃物;二是农业和林业产生的有机质固体废弃物,如农作物秸秆、稻(谷)壳、果壳、枝桠柴、树叶、木屑等;三是城镇生活垃圾有机固废,如纸类、织物、塑料橡胶、木竹等有毒有害垃圾和混合垃圾。
4.目前,含有机质的固体废弃物质(有机固废)的减量化、无害化环保治理技术主要有填埋法、焚烧法、生物法、机械脱水、干化法、化学热洗法、萃取法和热解法等单一处理方法或几种方法的组合。其中填埋法已明令禁止采用,其他方法存在或能耗高、或处理流程长、或处理成本高、或存在二次污染、或处理不彻底、或处理规模小、或处理效率低、或有机质转化回收率不高造成资源浪费等问题。
5.热解法能够将含有机质的固体废弃物质(有机固废)中的全部有机物进行无害化处理,还能回收油气或转化有机质实现资源化利用,是目前最具有发展潜力的技术。
6.热解提馏反应器是整个热解工艺的核心,热解过程在其中发生,其类型决定了热解反应方式及热解产物的成分。目前热解提馏反应器根据结构的不同分为固定床反应器、流化床、旋转炉(窑)和双塔循环式热解反应器。固定流化床为逆流式物流方向,停留时间长,保证了废物最大程度地转换成燃料;因气体流速较低,产生气体中夹带的颗粒物质也比较少,减少了对空气污染的潜在影响。流化床反应器中气体流速高到可以使得颗粒悬浮,使得有机固废颗粒分散,反应性能更好,但是热损失大,气体中带走大量得热量和较多地未反应得固体燃料粉末。旋转炉(窑)是一种间接加热的高温分解反应器,传热效率不高。双塔循环式热解反应器将热解与燃烧反应分开在两个塔中进行,设备投入大,占地面积大。
7.热解法随热解反应器(热解炉)技术的不同处理效果差别较大,“间歇式”热解炉,一次加料,一次排渣,不能连续生产,且热解炉处理规模小;“连续式”热解炉,处理规模不大,受各种因素影响连续操作性不高,目前,无论“间歇式”或“连续式”的热解炉均采用有机固废在炉膛内、热载体(外给热量)在炉膛外,夹套内的有机固废与热量非直接接触的“间接
式”给热热解方法,存在传热效率不高、吸热效率低导致热量利用效率低、热解反应速度慢、反应时间较长、能耗高、热解固态残渣不能满足超洁净排放环保指标要求等问题。
技术实现要素:
8.为了提高热解效率,本申请提供一种燃烧火焰炉内直接给热式多级串联湍动床热解提馏炉。
9.本申请提供的一种燃烧火焰炉内直接给热式多级串联湍动床热解提馏炉,采用如下的技术方案:一种燃烧火焰炉内直接给热式多级串联湍动床热解提馏炉,包括炉壳体,所述炉壳体包括相互连通的上段炉、中段炉、下段炉;所述上段炉具有有机固废物料进口以及气态混合物出口;所述中段炉具有若干组串联的湍动微反应床;所述下段炉具有燃料燃烧器、压温气体进口以及残渣出口;燃料经燃料燃烧器燃烧产生高温烟气自下而上流动与有机固废直接接触提供热量;所述湍动微反应床内具有主反应区,相邻所述湍动微反应床之间形成有副反应区。
10.通过采用上述技术方案,一方面将燃料燃烧器与热解提馏炉这两种不同功能的设备有机集成在同一设备内,有效降低了设备投资且减少了这两种不同功能的设备之间的高温连接管道系统,也降低了工程造价费用,减小了占地面积;另一方面,有机固废物料在每一组微反应床中呈现气固两相以湍动悬浮的充分混合状态与燃料燃烧产生高温烟气携带的热量直接接触高效换热,大大提高了有机固废热解提馏过程的给热效率与吸热效率,提高了热量利用效率、有效降低了能耗;同时,多级串联的湍动微反应床有效延长了有机固废物料的停留时间,充分的气固两相湍动悬浮混合状态大大提高了有机固废物料去除有毒有害物质和转化为低分子量的气态烃类物质及/或气相油品的热解反应和提馏反应速度、缩短了热解提馏反应时间、提高了有机固废中的有机质转化回收产率,达到有机固废热解固态残渣满足超洁净排放环保指标要求、避免了二次污染,实现有机固废彻底无害化治理和有机质资源化转化回收的环境友好和资源节约的有益效果。
11.主反应区和副反应区可提供多层次的反应区域,使有机固废更充分地在中段炉进行热反应,进一步提高热解效率。
12.可选的,所述湍动微反应床包括至少一块上导流板和至少一块下导流板,所述上导流板和所述下导流板之间形成有主反应区,所述上导流板和壳体内壁之间、所述下导流板和壳体内壁之间均形成有副反应区。
13.通过采用上述技术方案,通过上导流板和下导流板的组合即可形成主反应区和副反应区,一方面可根据实际产品需要调整上导流板和下导流板的组合搭配,从而适应提馏不同的有机固废原料;另一方面设备生产简单,且配件较少便于后期维护。
14.可选的,所述上段炉设置有物料进口分配板。
15.通过采用上述技术方案,分配板可将有机固废物收集后均匀下落至中段炉的湍动微反应床内,提升有机固废与高温烟气的接触体积,从而进一步提升反应效率。
16.可选的,所述中段炉具有与所述炉壳体内连通的二次给热口,所述二次给热口位于相邻湍动微反应床之间。
17.通过采用上述技术方案,可随时补充高温烟气,使高温烟气与湍动微反应床内的有机固废原料充分接触,从而提升有机固废原料的分解提馏效率。
18.可选的,所述下段炉设置有用于将渣料导入燃料燃烧器的出口导流板。
19.通过采用上述技术方案,出口导流板可将渣料导入燃料燃烧器,参与燃烧反应,并同时与高温烟气直接接触换热继续进行高温热解反应,这样可以使流出下段炉的固态残渣中有机质的含量降低到远低于环保超洁净排放指标要求。
20.可选的,所述下段炉设置有气体分布板。
21.通过采用上述技术方案,气体分布板主要起到通过通入压温气体来调节燃料燃烧产生高温烟气进入中段炉温度的作用,同时也起到防止热解固态残渣下行流动不畅而附着架桥使其流入残渣出口的作用。
22.可选的,所述上段炉和下段炉均设置有人孔。
23.通过采用上述技术方案,可供工作人员进入进行检修。
24.可选的,所述炉壳体内压力为
‑
0.1
‑
10mpag、温度为300
‑
1000℃。
25.通过采用上述技术方案,上述参数具有较好的热提馏效果。
26.综上所述,本申请包括以下至少一种有益技术效果:1.本申请采用有机固废贫氧或无氧环境的中高温热解提馏工艺,通过有机固废与高温热载体直接接触的“直接式”给热方法,大大提高了有机固废热解提馏过程的给热效率与吸热效率,提高了热量利用效率、有效降低了能耗。
27.2.本申请构建多级串联的湍动微反应床,使有机固废物料在每一组微反应床中呈现气固两相以湍动悬浮的充分混合状态与高温热载体携带的热量直接接触高效换热。多级串联的湍动悬浮微反应床有效延长了有机固废物料的停留时间,充分的气固两相湍动悬浮混合状态大大提高了有机固废物料去除有毒有害物质和转化为低分子量的气态烃类物质及/或气相油品的热解反应和提馏反应速度、缩短了热解提馏反应时间、提高了有机固废中的有机质转化回收产率,达到有机固废热解固态残渣满足超洁净排放环保指标要求、避免了二次污染,实现有机固废彻底无害化治理和有机质资源化转化回收的环境友好和资源节约的有益效果;3.采用多级串联湍动床兼具固定床停留时间长和流化床的反应性能更好优点;采用直接给热式加热方式克服了旋转炉(窑)传热效率不高的缺点;采用燃烧火焰炉和热解提馏炉合并在一个炉子内进行,克服了设备投入大和占地面积大的缺点。
附图说明
28.图1是本申请实施例1的内部结构示意图。
29.图2是本申请实施例2的内部结构示意图。
30.图3是本申请实施例3湍动微反应床的结构示意图。
31.图4是本申请实施例4湍动微反应床的结构示意图。
32.附图标记说明: 1、上段炉;2、中段炉;3、下段炉;4、炉壳体;5、耐火隔热衬里;101、有机固废物料进口;102、气态混合物出口;103、物料进口分配板;104、人孔;22、湍动微反应床;23、出口导流板;24、二次给热口;221、上导流板;222、下导流板;241、二次燃料燃烧器;301、燃料燃烧器;302、气体分布板;303、残渣出口;305、压温气体进口;306、二次给热高温
烟气出口。
具体实施方式
33.以下结合附图1
‑
4对本申请作进一步详细说明。
34.实施例1一种燃烧火焰炉内直接给热式多级串联湍动床热解提馏炉,参见图1,包括炉壳体4,炉壳体4包括由上至下依次相互连通的上段炉1、中段炉2、下段炉3,炉壳体4设置有耐火隔热衬里5。
35.上段炉1的顶部或侧面上部设置 n(n≥1)个有机固废物料进口101、n(n≥1)个气态有机质热解提馏产物和高温烟气的气态混合物出口102、物料进口分配板103及人孔104。
36.物料进口分配板103的上表面与炉壳体4中心线的夹角α为0
‑
180
°
之间的任一角度,并在其中心区域的底部(0
°
< α≤ 90
°
时)或顶部(90
°
< α < 180
°
时)开设宽度或直径为a0( a0≥0)的缺口,对应地,在其底部(0
°
< β1 < 90
°
时)或顶部(90
°
< β2 ≤ 180
°
时)与耐火隔热衬里5内壁面之间开有宽度为b01和b02( b01≥0、b02≥0)的缺口或环隙,均为有机固废物料下行和气态物料上行的通道,且a0和b01及b02不同时为0。
37.物料进口分配板103在0
°
< α < 90
°
设置时,其顶部可以不开设缺口或环隙(b01和b02均为0),但其底部需开设缺口作为固态物料下行和气态物料上行的通道,且a0>0。
38.物料进口分配板103在90
°
< α < 180
°
设置时,在其顶部可以不开设缺口(即a0为0),但其两侧底部需开设宽度或环隙为b01和b02 的缺口(b01和b02均>0)作为固态物料下行和气态物料上行的通道。
39.物料进口分配板103的上表面形状是以有利于物料流动的结构,可以是平直的,也可以是波纹状,也可以是开设导流槽结构,也可以是这几种结构的不同组合。
40.中段炉2作为有机固废物料热解提馏段,设置有n(n≥1)组串联的湍动微反应床22、残渣出口303导流板23和n(n≥0)个二次给热口24。
41.每一组湍动微反应床22包括一块上导流板221和一块下导流板222,且以炉壳体4中心线为中心轴双向对称布置或双向非对称布置;每一组湍动微反应床22内具有主反应区,具体为上导流板221与下导流板222之间构成的空间区域;相邻两组湍动微反应床22之间具有副反应区,具体为上一组微反应床的下导流板222与下一组微反应床的上导流板221之间构成的两侧两个空间区域或环隙区域;上导流板221的上表面与炉壳体4中心线的夹角β1为0
‑
180
°
之间的任一角度;下导流板222的上表面与炉壳体4中心线的夹角β2为0
‑
180
°
之间的任一角度,且当90
°
≤β1 < 180
°
时0
°
< β2 ≤ 90
°
,相应地当0
°
< β1 ≤ 90
°
时90
°
≤β1 < 180
°
。每相邻两组湍动微反应床22的上导流板221和下导流板222与炉壳体4中心线的夹角β1与β2可以是相同数值,也可以是相互不同数值。
42.每一组湍动微反应床22的上导流板221中心区域顶部(90
°
≤β1 < 180
°
时)或底部(0
°
< β1 < 90
°
时)开有宽度或直径为a1( a1≥0)的缺口,对应地,在其底部(90
°
≤β1 < 180
°
时)或顶部(0
°
< β1 ≤ 90
°
时)与耐火隔热衬里5内壁面之间开有宽度为b11和b12( b11≥0、b12≥0)的缺口或环隙,均为固态物料下行和气态物料上行的通道,且a1和b11及b12不同时为0,且每相邻两组湍动微反应床22上导流板221的 a1和b11及b12可以是相同数
值,也可以是相互不同数值。
43.每一组湍动微反应床22的下导流板222中心区域底部(0
°
< β2 ≤ 90
°
时)或顶部(90
°
< β2 < 180
°
时)开设宽度或直径为a2( a2≥0mm)的缺口,对应地,在其顶部(0
°
< β2 ≤ 90
°
时)或底部(90
°
< β2 < 180
°
时)与耐火隔热衬里5内壁面之间开有宽度为b21和b22( b21≥0、b22≥0)的缺口或环隙,均为固态物料下行和气态物料上行的通道,且a2和b21及b22不同时为0,且每相邻两组湍动微反应床22下导流板222的 a2和b21及b22可以是相同数值,也可以是相互不同数值。
44.另外,上导流板221和下导流板222的上表面形状是以有利于物料流动的结构,可以是平直的,也可以是波纹状,也可以是开设导流槽结构,也可以是这几种结构的不同组合。
45.中段炉2的n(n≥0)个二次给热口24设置在任何相邻两组湍动微反应床22之间位置,根据有机固废物料组成、处理规模、气态混合物出口102和残渣出口303组成确定其数量为0个或n个。
46.中段炉2的n(n≠0)个二次给热口24可以设置二次燃料燃烧器241,该燃烧器为气体燃料或液体燃料燃烧器301或气液联合燃烧器;也可以从设置在下段炉3侧面位置的n(n≠0)个二次给热高温烟气出口306直接引入高温烟气进入对应的n(n≠0)个二次给热口24。
47.每一组湍动微反应床22由 m1(m1≥1,且m1≤n/2且取整数)块上导流板221(221)和 m2(m2≥1,且m2≤n/2且取整数)块下导流板222(222)构成,其每相邻两组或若干组湍动微反应床22以炉壳体4中心线为中心轴分别以双向导流板和单向导流板两种形状交错布置。
48.残渣出口303导流板23的上表面形状是以有利于物料流动的结构,可以是平直的,也可以是波纹状,也可以是开设导流槽结构,也可以是这几种结构的不同组合。
49.残渣出口303导流板23的上表面与炉壳体4中心线的夹角β3为0
‑
180
°
之间的任一角度,其中心区域底部(0
°
< β3 ≤ 90
°
时)或顶部(90
°
< β3 < 180
°
时)开设宽度或直径为a3( a3≥0)的缺口,对应地,在其顶部(0
°
< β1 < 90
°
时)或底部(90
°
< β2 ≤ 180
°
时)与耐火隔热衬里5内壁面之间开设宽度为b31和b32( b31≥0、b32≥0)的缺口或环隙,均为残渣出口303和高温烟气上行的通道,且a3和b31及b32不同时为0。
50.残渣出口303导流板23的形状与炉壳体4及其耐火隔热衬里5的截面形状相匹配。残渣出口303导流板23的形状也可以与上导流板221或下导流板222的设置方法相同或类似。
51.物料进口分配板103、上导流板221、下导流板222、残渣出口303导流板23上可以开设 n(n≥0)个通气孔,总开孔数量和总开孔面积根据有机固废物料粒径分布、处理规模和多级串联的湍动微反应床22的气相流速和压降确定,也可以不开设通气孔(n=0)。
52.下段炉3设置有燃料燃烧器301、气体分布板302、残渣出口303、人孔104、 n(n≥0)个上部压温气体进口305、 n(n≥0)个二次给热高温烟气出口306和 n(n≥0)个下部压温气体进口305。
53.燃料燃烧器301、残渣出口303和人孔104设置在下段炉3的底部或侧面,数量可以分别是n(n≥1)个设置在不同位置;在下段炉3的底部或侧面气体分布器下部位置设置数量为n(n≥1)个压温气体进口305;可以在下段炉3侧面气体分布器上方设置n(n≥0)个二次给
热高温烟气出口306或不设置(n=0);可以在下段炉3侧面且位于气体分布器上方设置数量为n(n≥0)个压温气体进口305 或不设置(n=0)。
54.燃料燃烧器301为气体燃料或液体燃料燃烧器301或气液联合燃烧器用于燃料在下段炉3内燃烧产生高温烟气作为热量载体为有机固废热解提馏反应提供热量。
55.气体分布板302主要起到通过通入压温气体来调节燃料燃烧产生高温烟气进入中段炉2温度的作用,同时也起到防止热解固态残渣下行流动不畅而附着架桥使其流入残渣出口303的作用,该压温温气体为具有易经济获得性、安全性、且不对热解反应及其热解产物产生不良影响的单一组分气体(氧气除外)或贫氧或无氧的多组分气体混合物。如n2、氩气等惰性气体、co2气体、蒸汽或燃料燃烧后的低温排放烟气、热解尾气、炼厂干气或石化废气或弛放尾气等单一组分气体或此类气体的多组分气体混合物。
56.气体分布板302的形状与下段炉3的炉壳体4及其耐火隔热衬里5的截面形状相匹配。气体分布板302上表面与下段炉3的炉壳体4中心线的夹角γ为0
‑
90
°
之间的任一角度,并开设有n(n≥1)个通气孔。
57.下段炉3的燃料燃烧器301可以附加设置外通道通入压温气体来调节燃料燃烧产生高温烟气进入中段炉2温度。
58.下段炉3也可以通过将n(n≥1)个燃料燃烧器301设置在下段炉3的底部,气体分布器作为布风板,并与炉壳体4及其耐火隔热衬里5的截面形状相匹配构建流化床,此时,气体分布板302需调整设置为流化床的常规布风板结构,n(n≥1)个压温气体进口305需设置在下段炉3所构建的流化床区域的侧面上部位置。
59.下段炉3构建成流化床时,可以将部分有机固废物料从下段炉3加入炉内,与热解固态残渣共同在此流化床进行燃烧反应或高温热解反应。
60.另外,上段炉1、中段炉2和下段炉3的炉壳体4及其耐火隔热衬里5的截面形状可以是圆筒形或椭圆形,也可以是矩形(正方形或长方形)或多边形,上段炉1、中段炉2和下段炉3的炉壳体4及其耐火隔热衬里5的截面形状可以是同一种截面结构,也可以是不同截面形状及其不同结构的组合;上段炉1、中段炉2和下段炉3的炉壳体4及其耐火隔热衬里5的截面面积可以相等,也可以不同。耐火隔热衬里5可以是n(n≥1)层耐火隔热浇注料结构,也可以是n(n≥1)层的耐火隔热砖结构,也可以是耐火隔热浇注料与耐火隔热砖的组合结构,也可以是列管式或盘管式的膜式水冷壁结构,也可以是冷却夹套结构,也可以是这几种结构形式的不同组合。
61.上段炉1、中段炉2、下段炉3及其炉壳体4和耐火隔热衬里5可以是整体结构,也可以是分段连接结构。
62.更具体地说,热解提馏炉壳体4为立式圆筒形结构,由上段炉1、中段炉2和下段炉3组成并同轴且相互连通,上段炉1的炉壳体4内直径为3000mm,耐火隔热衬里5内直径2700mm,直筒段高度3000mm;中段炉2的炉壳体4内直径为2400mm,耐火隔热衬里5内直径1800mm,直筒段高度30000mm;下段炉3的炉壳体4内直径为3000mm,耐火隔热衬里5内直径2200mm,直筒段高度3000mm。热解提馏反应压力为1.0mpag,反应温度区间为350
‑
900℃。
63.上段炉1的顶部距离壳体中心线450mm均匀对称设置4个有机固废物料进口101,顶部中心位置设置1个气态有机质热解提馏产物和高温烟气的气态混合物出口102,侧面位置设置1个人孔104;物料进口分配板103底部开口a0为600mm,α为 30
°
。
64.中段炉2有机固废物料热解提馏段设置12组串联的湍动微反应床22,上导流板221、下导流板222和残渣出口303导流板23均为圆锥形结构。上导流板221β1为120
°
,a1为200mm,b11和b12均为400mm;下导流板222β2为45
°
,a2为800mm,b21和b22均为0mm;残渣出口303导流板23β3为30
°
,a3为600mm,b31和b32均为0mm。上导流板221上和下导流板222、残渣出口303导流板23上均开设760个直径为5mm的通气孔;设置两个二次给热口24,其位置在从上往下的第四组和第五组湍动微反应床22之间、第八组和第九组湍动微反应床22之间,两个二次给热口24各设置一个二次燃料燃烧器241。
65.下段炉3的底部中心位置设置一个燃料燃烧器301,气体分布板302采用常规布风板结构,与炉壳体4及其耐火隔热衬里5相匹配构成流化床;燃料燃烧器301采用油气联合烧嘴,并在其外通道附加热解尾气加入通道;在下段炉3的侧面上部位置对称设置四个压温气体进口305;不设置二次给热高温烟气出口306;设置1个残渣出口303,位于中心位置的燃料燃烧器301外侧;气体分布板302为圆锥形结构,与炉壳体4中心线的夹角γ为30
°
,并开设800个直径为5mm的通气孔;在侧面下部位置设置1个人孔104。
66.耐火隔热衬里5在上段炉1为一层耐火隔热浇注料,厚度150mm;在中段炉2和下段炉3均为耐火隔热浇注料和耐火隔热砖两层组合构成,中段炉2总厚度300mm,下段炉3总厚度400mm;耐火隔热浇注料采用高致密隔热浇注料。耐火隔热砖耐火隔热砖采用高铬砖(cr2o3含量大于86.0%,厚度均为76mm。
67.本申请实施例一种燃烧火焰炉内直接给热式多级串联湍动床热解提馏炉的实施原理为:燃料和空气或富氧空气或氧气进入下段炉3的燃料燃烧器301在炉壳体内1进行燃烧反应产生高温烟气,并与进入下段炉3下部压温气体进口305并经气体分布器分配后的压温气体及/或燃料燃烧器301外通道通入的压温气体及/或下段炉3设置的上部压温气体进口305进入的压温气体共同混合调整到热解反应所需的温度后上行进入中段炉2底部,自下而上流动为n级串联的湍动微反应床22进行的热解提馏反应提供热量。
68.含有机质的固体废弃物质(有机固废)自上段炉1的有机固废物料进口101进入上段炉1内靠重力下行,与上行的高温烟气与热解提馏气态产物的混合物直接接触换热,并经过吸热预热下行进入中段炉2的顶部。
69.经上段炉1预热的有机固废从中段炉2顶部自上而下流动依次进入n级串联的湍动微反应床22与自下而上流动的高温烟气与热解提馏气态产物两者的混合物直接接触进行热解提馏反应。
70.每一组湍动微反应床22内部作为主反应区,相邻两组湍动微反应床22(22)之间作为副反应区,下行的有机固废与上行的高温烟气和热解提馏气态产物两者的混合物在主反应区和副反应区内部呈现气固两相湍动悬浮的充分混合状态直接接触换热,有机固废吸收高温烟气携带的热量发生有机质的裂解反应和提馏反应而产生低分子量的气态烃类物质及/或气相油品,并与梯级放热降温的高温烟气组成混合物自下而上流动。
71.在中段炉2完成热解提馏反应的有机固废残渣物料下行经残渣出口303导流板23汇集后流进下段炉3。流进下段炉3的部分有机固废固体残渣物料下行参与燃料燃烧器301的燃烧反应,并同时与高温烟气直接接触换热继续进行高温热解反应,这样可以使流出下段炉3的固态残渣中有机质的含量降低到远低于环保超洁净排放指标要求或降低为零;
如将部分有机固废物料加入下段炉3内,则该部分有机固废物料与热解固态残渣共同进行燃烧反应或高温热解反应。产生的气态反应产物随高温烟气一起上行,最终热解固态残留物(热解残渣)经气体分布器汇集后自残渣出口303流出热解提馏炉,进入后续残渣冷却与余热回收工序。
72.根据热解提馏气态有机质产物出口温度和残渣出口303组成分析,如发现热解固态残渣中残余有机质含量超标则说明高温烟气所携带的热量不足而导致有机固废热解反应进行不完全,或气态有机质热解提馏产物出口温度偏低时,可以从设置在中段炉2的二次给热口24的二次燃料燃烧器241向炉内输入高温烟气为热解反应提供附加热量;也可以从下段炉3的燃料燃烧器301加大燃料的流量(当没有设置二次给热口24时)多产高温烟气及/或从设置在下段炉3侧面位置的二次给热高温烟气出口306直接引出高温烟气进入二次给热口24(不设置二次燃料燃烧器241时)向炉内输入高温烟气为热解反应提供附加热量。
73.气态烃类和气相油品与梯级放热降温的高温烟气组成的气态混合物最后经上段炉1的气态有机质热解提馏产物和高温烟气的气态混合物出口102流出热解提馏炉,进入后续热解提馏产物余热回收利用与有机质分离回收工序。
74.实施例2参见图2,一种燃烧火焰炉内直接给热式多级串联湍动床热解提馏炉,包括立式方形结构的炉壳体4,炉壳体4包括相互连通的上段炉1、中段炉2和下段炉3,其截面形状为长方形但不等截面积,上段炉1的炉壳体4截面长x宽为4000x2500mm,直段高度3000mm,其耐火隔热衬里5厚度为150mm;中段炉2的炉壳体4内径长x宽为4000x2000mm,直段高度24000mm,其耐火隔热衬里5厚度为250mm;下段炉3的炉壳体4截面长x宽为4000x2500mm,直段高度2000mm,其耐火隔热衬里5厚度为400mm。
75.上段炉1顶部距离宽度方向中心线400mm两侧且距离长度方向中心线600mm两侧各对称设置两个有机固废物料进口101,顶部中心位置设置1个气态有机质热解提馏产物和高温烟气的气态混合物出口102,长度方向两侧中心线位置各设置1个人孔104;不设置物料进口分配板103。
76.中段炉2有机固废物料热解提馏段设置八组串联的湍动微反应床22,上导流板221、下导流板222和残渣出口303导流板23均为宽度方向对称于中段炉2中心线的两个长方形结构。上导流板221上表面与宽度方向中段炉2中心线的夹角β1为120
°
,a1为100mm,b11和b12均为300mm;下导流板222与炉壳体4中心线的夹角β2为40
°
,a2为600mm,b21和b22均为50mm;残渣出口303导流板23与炉壳体4中心线的夹角β3为30
°
,a3为700mm,b31和b32均为0mm;上导流板221上和下导流板222上、残渣出口303导流板23上均开设1180个直径为5mm的通气孔;设置两个二次给热口24但不设置二次燃料燃烧器241,位于中段炉2宽度方向的两侧中心线位置各1个,其高度方向位置在从上往下的第四组和第五组湍动微反应床22之间。
77.下段炉3的底部宽度方向中心线位置以长度方向中心线对称设置两个燃料燃烧器301,两个燃料燃烧器301中心线间距为1750mm,燃料燃烧器301采用油气联合烧嘴,并在其外通道附加热解尾气加入通道;气体分布器为长方形结构,与下段炉3宽度方向中心线的夹角γ为30
°
,并开设1200个直径为10mm的气体分配孔;在下段炉3的底部的宽度方向的中心线位置设置1个残渣出口303;设置四个压温气体进口305,位于下段炉3宽度方向的两侧各两个,并沿下段炉3长度方向中心线两侧对称设置;设置两个二次给热高温烟气出口306,位
于下段炉3宽度方向的两侧各一个的沿长度方向的中心线位置;在下段炉3长度方向的两侧面中心线位置各设置一个人孔104,不设置上部压温气体进口305。
78.耐火隔热衬里5在上段炉1为一层耐火隔热浇注料,厚度150mm;在中段炉2和段炉均为耐火隔热浇注料和耐火隔热砖两层组合构成,中段炉2总厚度250mm,下段炉3总厚度400mm;耐火隔热浇注料采用高致密隔热浇注料,耐火隔热砖耐火隔热砖采用高铬砖,cr2o3含量大于86.0%,设置在炉壳体4内侧,厚度均为76mm。
79.实施例3与实施例1的区别在于,湍动微反应床22的结构不同。参见图3,每一组湍动微反应床22也可以由m1(m1≥2,且m1≤n/2且取整数)块上导流板221和 m2(m2≥2,且m2≤n/2且取整数)块下导流板222构成,其均以炉壳体4中心线为中心轴双向形状对称布置或非对称布置呈阶梯状,每一组及相邻两组湍动微反应床22的m1和m2可以是相同数量,也可以是不同数量;每一组的第一块上导流板221和第一块下导流板222之间区域构成主反应区,每一组的m1块上导流板221与耐火隔热衬里5内壁面之间区域或环隙可以通过上导流板221上不同的开缺口方式形成若干个副反应区,每一组的m1块上导流板221之间的中心区域以及每一组的m2块下导流板222与耐火隔热衬里5内壁面之间区域或环隙均可以通过在导流板上不同的开缺口方式匹配导流板之间的板间距h1
‑
h1m1
‑
1、h2
‑
h2m2
‑
1的不同设置形成若干个微小的副反应区;每一组湍动微反应床22的m1块上导流板221的β1
‑
β1m1、a1
‑
a1m1和b11
‑
b11m1及b12
‑
b12m1的定义与上导流板221等同位置的定义相同,可以是同位置取相同数值,也可以是同位置取相互不同数值,m1块上导流板221之间的间距h1
‑
h1m1
‑
1可以是等间距,也可以是不等间距;同理,每一组湍动微反应床22的下导流板222的β2
‑
β2m2、a2
‑
a2m2和b21
‑
b21m2及b22
‑
b22m2的定义与下导流板222等同位置的定义相同,可以是相同数值,也可以是相互不同数值,m2块下导流板222之间的间距h2
‑
h2m2
‑
1可以是等间距,也可以是不等间距。
80.更具体地说,中段炉2设置八组串联的湍动微反应床22。每一组湍动微反应床22由三块上导流板221和三块下导流板222构成,且均以热解炉壳体4中心线为中心轴双向对称布置呈阶梯状布置;每一组湍动微反应床22的第一块上导流板221的β1=β12=β13=120
°
,a1=100mm、b11=b12=250mm,a12=200mm、b112=b122=500mm,a13=50mm、b113=b123=700mm,三块上导流板221之间不等间距设置,h1=500mm,h12=300mm;每一组湍动微反应床22的下导流板222的β2 =β22 =β23 =45
°
,a2=600mm、b21=b22=0mm;a22=900mm、b212=b222=200mm,a23=1200mm、b213=b223=50mm,三块下导流板222之间不等间距设置,h2=300mm,h22=500mm。
81.每一组的第一块上导流板221和第一块下导流板222之间的中心区域构成该组湍动微反应床22的主反应区,三块上导流板221与耐火隔热衬里5内壁面之间的环隙区域形成三个副反应区,三块上导流板221的中心区域形成三个微小的副反应区,第二块和第三块下导流板222与耐火隔热衬里5内壁面之间的环隙区域形成两个微小的副反应区。
82.实施例4与实施例1的区别在于,湍动微反应床22的结构不同。参见图4,每一组湍动微反应床22也可以由一块上导流板221和一块下导流板222构成,其均与耐火隔热衬里5内壁面呈单向形状布置。同理,也可以由m1(m1≥1,且m1≤n/2且取整数)块上导流板221和 m2(m2≥1,且m2≤n/2且取整数)块下导流板222构成,且与耐火隔热衬里5内壁面呈单向布置,每一
组及相邻两组湍动微反应床22的m1和m2可以是相同数量,也可以是不同数量;每一组的第一块上导流板221和第m2块下导流板222与耐火隔热衬里5内壁面之间区域构成主反应区,同理,每一组的第m1块上导流板221和相邻上一组的第一块下导流板222与耐火隔热衬里5内壁面之间区域也构成主反应区,每一组的m1块上导流板221以及每一组的m2块下导流板222与耐火隔热衬里5内壁面之间的各自顶部区域均可以通过在导流板上不同的开缺口方式匹配导流板之间的板间距h1
‑
h1m1
‑
1、h2
‑
h2m2
‑
1的不同设置形成若干个微小的副反应区;每一组湍动微反应床22的m1块上导流板221的β1
‑
β1m1、b11
‑
b11m1及b12
‑
b12m1可以是同位置取相同数值,也可以是同位置取相互不同数值,m1块上导流板221之间的间距h1
‑
h1m1
‑
1可以是等间距,也可以是不等间距;同理,每一组湍动微反应床22的m2块下导流板222的β2
‑
β2m2、b21
‑
b21m2及b22
‑
b22m2可以是相同数值,也可以是相互不同数值, m2块下导流板222之间的间距h2
‑
h2m2
‑
1可以是等间距,也可以是不等间距。
83.更具体地说,中段炉2中设置有六组串联的湍动微反应床22。最上部第一组湍动微反应床22由一块上导流板221和一块下导流板222构成,其与耐火隔热衬里5内壁面呈单向布置,上导流板221和下导流板222与耐火隔热衬里5内壁面之间区域构成主反应区,上导流板221β1=120
°
、b11=50mm、b12=600mm,下导流板222β2=40
°
、b21=600mm、b22=50mm;第二组湍动微反应床22由两块上导流板221和两块下导流板222构成,其与耐火隔热衬里5内壁面呈单向布置,第一块上导流板221和第二块下导流板222与耐火隔热衬里5内壁面之间区域构成主反应区,同理,第2块上导流板221和第一组的下导流板222与耐火隔热衬里5内壁面之间区域也构成主反应区,同时,第一块上导流板221和第2块下导流板222分别与耐火隔热衬里5内壁面之间的各自顶部区域构成两个微小副反应区;上导流板221β1=β12=120
°
、b11=150mm、b112=50mm、 b12=500mm、b122=1000mm、h1=300mm,下导流板222β2=β22=45
°
、 b21=600mm、b212=1000mm、 b22=150mm、b222=50mm、h2=300mm;第三组
‑
第六组湍动微反应床22均由三块上导流板221和三块下导流板222构成,其与耐火隔热衬里5内壁面呈单向布置,每一组的第一块上导流板221和第三块下导流板222与耐火隔热衬里5内壁面之间区域构成主反应区,同理,每一组的第三块上导流板221和相邻上一组的第一块下导流板222与耐火隔热衬里5内壁面之间区域也构成主反应区,同时,每一组的第一块和第二块上导流板221以及每一组的第一块和第二块下导流板222分别与耐火隔热衬里5内壁面之间的各自顶部区域构成四个微小副反应区;每一组上导流板221β1 =β12=β13=120
°
、 b11=150mm、b112=400mm、b113=50mm、b12=500mm、b122=900mm、 b123=1200mm、h1=h12=300mm,下导流板222β2=β22=β23=45
°
、b21=600mm、b212=900mm、 b213=1200mm 、b22=150mm、b222=400mm、b223=50mm、h2= h22=300mm;上导流板221、下导流板222、残渣出口303导流板23均开设1180个直径为5mm的通气孔。
84.以上均为本申请的较佳实施例,并非依此限制本申请的保护范围,故:凡依本申请的结构、形状、原理所做的等效变化,均应涵盖于本申请的保护范围之内。
再多了解一些
本文用于企业家、创业者技术爱好者查询,结果仅供参考。