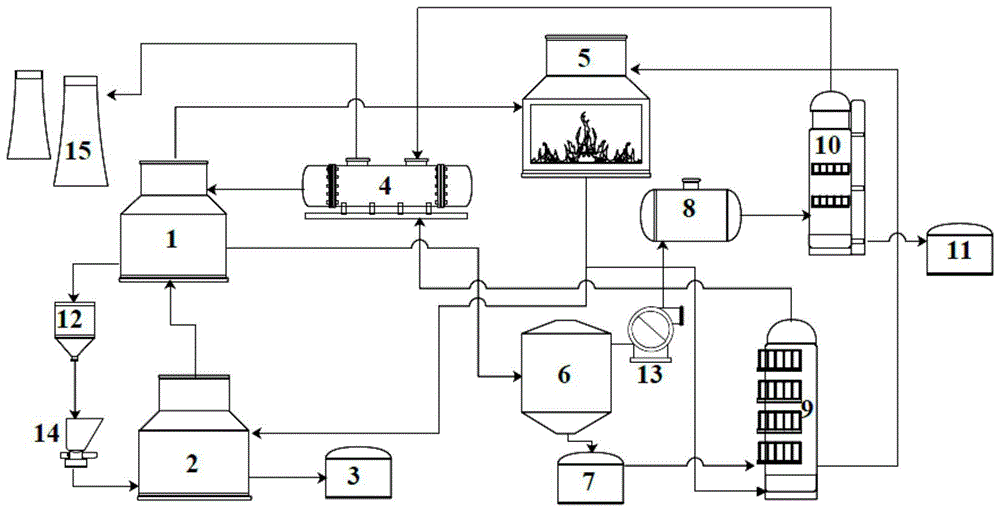
本发明属生物质废弃物回收利用技术领域,涉及一种棉花秸杆碳化多联产综合利用系统及工艺。
背景技术:
自上世纪90年代起,我国棉花种植布局重心逐渐向西北地区转移,目前新疆以成为我国棉花最主要的产区。在生产棉花的过程中,副产品棉花秸秆作为一般农业废弃物,处理不当往往会造成环境污染与资源浪费,这与我国的健康、绿色、可持续发展理念不符。目前棉花秸秆的处理方式以就地焚烧为主,在造成资源浪费的同时也会引起大气环境污染。因此,结合新疆目前自身生态环境的脆弱性,寻求合适的棉花秸秆资源化利用手段,促使生态、经济有机结合,通过合理的技术与工艺赋予棉花秸秆更多的资源属性变得十分迫切与重要。
目前关于棉花秸秆的资源化利用手段主要包含发酵制沼气、秸秆还田、用作饲料、充当生物质燃料等方面,专利cn201510059510提出利用微生物菌类降解棉花秸秆制取土壤高碳基添加物,为将秸秆发酵和还田有机结合,但此方法需要特定的微生物菌种,提取成本较高,且秸秆发酵后的剩余物难以处理,使得棉花秸秆整体资源利用效率较低。专利cn201710060404提出一种将棉叶、棉壳与棉花杆分离,前者进行发酵制肥,后者通过干馏制取生物碳的综合利用方式,该方法很好地将生物质燃料与秸秆还田相结合,并且实现了生物质废弃物的多样化利用,但此方式在前期分离处理过程较为复杂,提升了综合利用成本;此外,在棉花秸秆碳化过程的气相和液相产物并没有得到有效的回收利用,从而容易产生一定程度的环境污染。专利110403074a提出一种棉花秸秆饲料化利用的加工方法,将棉花秸秆经40-100℃低温干燥粉碎,为反刍类动物提供了良好的饲料来源,但棉花秸秆中存在棉酚等有毒物质,在生产过程中难以去除,会导致雌性家畜不孕不育、致盲等病变。因此,饲料化利用手段尚需进一步完善。
综上所述,对于棉花秸秆而言,丰富其多样化利用的手段、妥善处理对应副产品带来的环境污染已成为目前需要解决两大难题。
技术实现要素:
本发明旨在解决现有技术不能充分利用棉花秸秆且不造成环境污染的技术问题,提供一种棉花秸杆碳化多联产综合利用系统及工艺。
本发明的目的之一是提供一种棉花秸杆碳化多联产综合利用工艺,全流程循环控制,各环节的资源(产物与能源)完全被利用,实现了生物质废弃物的多极化综合利用。棉花秸秆较小麦、水稻、玉米等秸秆而言,木质素含量较高,若制成饲料对于普通单胃家畜而言无法消化。此外,棉籽中含有的棉酚具有较强的杀精作用,不利于家畜的繁殖,因此无法像其他类秸秆一样做饲料化处理。
本发明的另一个目的是提供一种棉花秸杆碳化多联产综合利用系统,是一整套的系统解决方案,将生物质一级干馏炉、生物质半焦二级碳化炉、焦炭存储罐、换热器、瓦斯燃烧炉、沉降分离器、精馏塔和蒸馏塔等有机地连接成一体,以满足棉花秸杆碳化多联产综合利用工艺要求。
本发明的棉花秸杆碳化多联产综合利用系统,包括生物质一级干馏炉、生物质半焦二级碳化炉、焦炭存储罐、换热器、瓦斯燃烧炉、沉降分离器、重油存储罐、木醋液存储罐、精馏塔、蒸馏塔、浓缩木醋液存储罐、半焦收集罐、离心泵和给料机;其中,
所述生物质一级干馏炉具有固体产物出口、液体产物出口、气体产物出口、进气口和过热蒸汽入口;
所述固体产物出口连接半焦收集罐,所述半焦收集罐与给料机相连,所述给料机连通所述生物质半焦二级碳化炉的进料口,所生物质半焦二级碳化炉的出料口接焦炭储存罐,所生物质半焦二级碳化炉的排放口和生物质一级干馏炉的过热蒸汽入口相接;
所述液体产物出口与所述沉降分离器相连,所述沉降分离器分别与所述离心泵的进口和所述重油存储罐相连,所述离心泵的出口连接所述木醋液存储罐,所述木醋液存储罐接入所述蒸馏塔,所述蒸馏塔的水分排出口接通所述换热器,所述蒸馏塔还连接所述浓缩木醋液存储罐;所述重油存储罐与所述精馏塔相连,所述精馏塔的烟气出口接入所述换热器,所述精馏塔的底油出口接入所述瓦斯燃烧炉;
所述气体产物出口与所述瓦斯燃烧炉相连,所述瓦斯燃烧炉的高温烟气出口分别与所述生物质半焦二级碳化炉的加热气体入口和所述精馏塔的的加热气体入口相连。
所述进气口接通所述换热器的出口。
作为优选的技术方案:
如上所述的棉花秸杆碳化多联产综合利用系统,所述沉降分离器整体呈圆柱状,高度和直径比h/d为1.2,直径大小根据干馏炉规格确定。所属沉降分离器包含一个入口与两个出口,入口管道从顶部沿壁垂直延伸至木醋液与重油交界面,防止中间进油引发的产物倒流现象。利用木醋液与重油密度不同,在该容器内静置分层,木醋液出口管道自顶部引入接上层木醋液,利用所述离心泵将木醋液抽出,重油出口管道一端沿外壁垂直延伸至所属沉降分离器下端,与底部链接,另一端出口高度与木醋液重油交界面平齐,利用重油自身重力流出。各自在管道内流速比等于所得木醋液与重油组分比。
如上所述的棉花秸杆碳化多联产综合利用系统,所述精馏塔还连接生物质柴油储存罐、汽油储存罐和润滑油储存罐。
如上所述的棉花秸杆碳化多联产综合利用系统,所述生物质一级干馏炉还连接棉花秸杆输送装置。
如上所述的棉花秸杆碳化多联产综合利用系统,所述棉花秸杆输送装置为封闭式输送装置,以通过所述换热器产生的过热蒸汽作为载气,全程隔绝空气防止燃烧,经传送带输送至进料口,所述进料口位于所述生物质一级干馏炉上端,根据生物质自身重力自上而下落入炉膛,并在下降过程中与热载气充分换热。
如上所述的棉花秸杆碳化多联产综合利用系统,所述棉花秸杆粒径范围在40-100mm,经自然干燥后进行简单破碎即可送入所述生物质一级干馏炉中,无需进行刻意干燥、粉碎与筛选,节约生产成本。
本发明还提供了一种棉花秸杆碳化多联产综合利用工艺,包括以下步骤:
(1)将干燥且破碎后的棉花秸秆进行干馏,产生瓦斯气、挥发分和半焦;
(2)分步处理:
a)半焦经碳化生产焦炭;
所述碳化用的高温烟气作为热载体排出后,继续作为热源对棉花秸秆进行加热;
b)冷凝收集挥发分,经沉降后分层,上层为木醋液,下层为重油;
c)瓦斯气燃烧产生高温烟气,部分作为所述碳化的热源,部分用于所述重油的分馏加热;
(3)所述木醋液经蒸馏分离出多余的水分后,收集木醋液;所述重油进行精馏;
(4)所述多余的水分进一步加热后,以水蒸气的形式给所述干馏提供热量;所述精馏积余的底油送与瓦斯气混合一起燃烧。
如上所述的棉花秸杆碳化多联产综合利用工艺,经自然干燥后破碎的棉花秸秆的粒径为40~100mm。
如上所述的棉花秸杆碳化多联产综合利用工艺,干馏温度为280~350℃,碳化温度为400~500℃。
如上所述的棉花秸杆碳化多联产综合利用工艺,重油精馏产物为生物质柴油、汽油和润滑油。
本发明中,包括了二级制备焦炭的方法,即将棉花秸秆干馏后分离出半焦,然后将半焦被送入半焦收集罐,随后经给料机送入生物质半焦二级碳化炉,经高温烟气加热后生成焦炭,并存储于焦炭存储罐中。引入二级碳化炉目的在于降低干馏炉的干馏温度,从而抑制二次裂解反应,保证瓦斯气、木醋液与重油的产量。不仅降低能耗,更保证了产品的品质。
有益效果
相较于现有技术,本发明的优点在于:
1、将生物质废弃物的干馏、碳化与热解气体燃烧有机结合,燃烧产生的高温烟气为干馏、精馏和碳化提供热量,实现能量的内部热耦合,使得气、液、固三种热解产物均得到有效利用;
2、利用气体作为干馏炉、碳化炉的热载体,克服了固体热载体容易吸附挥发分从而导致生物质液相产物减少的问题,且可有效降低干馏温度,杜绝二次裂解和碳化反应,降低了污染;
3、液相产物经沉降分离,实现多样化利用,上层木醋液可作为肥料改善新疆盐碱地土壤结构,下层生物质重油经精馏形成生物质柴油、汽油、润滑油等商品用油,经精馏过后的底油可混合瓦斯气燃烧提供热量,木醋液分馏形成的水蒸气通入干馏炉中可提升气化效率;
4、本发明的系统及方法对原料的适应性广,且综合利用程度较高,对于新疆棉花秸秆各个部分均适用,反应物不需要进行过多的预处理,无需过多粉碎,对粒径要求不高,从而降低生产成本;
5、本发明的系统及方法能够实现将新疆棉花秸秆还田、充当热源和碳化材料有机结合,实现生物质废弃物的多极化综合利用,同时避免了固体废弃物和热解气等伴随产物对环境的污染问题,最终实现新疆棉花秸秆洁净、高效的资源化利用。
附图说明
图1为本发明棉花秸杆碳化多联产综合利用系统示意图
具体实施方式
下面结合具体实施方式,进一步阐述本发明。应理解,这些实施例仅用于说明本发明而不用于限制本发明的范围。此外应理解,在阅读了本发明讲授的内容之后,本领域技术人员可以对本发明作各种改动或修改,这些等价形式同样落于本申请所附权利要求书所限定的范围。
本发明的棉花秸杆碳化多联产综合利用系统,如图1所示,包括生物质一级干馏炉1、生物质半焦二级碳化炉2、焦炭存储罐3、换热器4、瓦斯燃烧炉5、沉降分离器6、重油存储罐7、木醋液存储罐8、精馏塔9、蒸馏塔10、浓缩木醋液存储罐11、半焦收集罐12、离心泵13和给料机14;其中,
所述生物质一级干馏炉1具有固体产物出口、液体产物出口、气体产物出口、进气口和过热蒸气入口;
所述固体产物出口连接半焦收集罐12,所述半焦收集罐12与给料机14相连,所述给料机14连通所述生物质半焦二级碳化炉2的进料口,所生物质半焦二级碳化炉2的出料口接焦炭储存罐3,所生物质半焦二级碳化炉2的排放口和生物质一级干馏炉1的过热蒸气入口相接;
所述液体产物出口与所述沉降分离器6相连,所述沉降分离器6分别与所述离心泵13的进口和所述重油存储罐7相连,所述离心泵13的出口连接所述木醋液存储罐8,所述木醋液存储罐8接入所述蒸馏塔10,所述蒸馏塔10的水分排出口接通所述换热器4,所述蒸馏塔10还连接所述浓缩木醋液存储罐11;所述重油存储罐7与所述精馏塔9相连,所述精馏塔9的烟气出口接入所述换热器4,所述精馏塔9的底油出口接入所述瓦斯燃烧炉5;
所述气体产物出口与所述瓦斯燃烧炉5相连,所述瓦斯燃烧炉5的高温烟气出口分别与所述生物质半焦二级碳化炉2的热载体入口和所述精馏塔9的的热载体入口相连。
所述进气口接通所述换热器4的出口。
如上所述的棉花秸杆碳化多联产综合利用系统,所述沉降分离器6整体呈圆柱状,高度和直径比h/d为1.2,直径大小根据干馏炉规格确定。所属沉降分离器包含一个入口与两个出口,入口管道从顶部沿壁垂直延伸至木醋液与重油交界面,防止中间进油引发的产物倒流现象。利用木醋液与重油密度不同,在该容器内静置分层,木醋液出口管道自顶部引入接上层木醋液,利用所述离心泵将木醋液抽出,重油出口管道一端沿外壁垂直延伸至所属沉降分离器下端,与底部链接,另一端出口高度与木醋液重油交界面平齐,利用重油自身重力流出。各自在管道内流速比等于所得木醋液与重油组分比。
如上所述的棉花秸杆碳化多联产综合利用系统,所述精馏塔9还连接生物质柴油储存罐、汽油储存罐和润滑油储存罐。
如上所述的棉花秸杆碳化多联产综合利用系统,所述生物质一级干馏炉1还连接棉花秸杆输送装置。
如上所述的棉花秸杆碳化多联产综合利用系统,所述棉花秸杆输送装置为封闭式输送装置,以通过所述换热器产生的过热蒸汽作为载气,全程隔绝空气防止燃烧,经传送带输送至进料口,所述进料口位于所述生物质一级干馏炉上端,根据生物质自身重力自上而下落入炉膛,并在下降过程中与热载气充分换热。
如上所述的棉花秸杆碳化多联产综合利用系统,所述棉花秸杆粒径范围在40-100mm,经自然干燥后进行简单破碎即可送入所述生物质一级干馏炉中,无需进行刻意干燥、粉碎与筛选,节约生产成本。
本发明的一种棉花秸杆碳化多联产综合利用工艺,包括以下步骤:
(1)将干燥且破碎后的棉花秸秆进行干馏,产生瓦斯气、挥发分和半焦;
(2)分步处理:
a)半焦经碳化生产焦炭;
所述碳化用的高温烟气作为热载体排出后,继续作为热源对棉花秸秆进行加热;
b)冷凝收集挥发分,经沉降后分层,上层为木醋液,下层为重油;
c)瓦斯气燃烧产生高温烟气,部分作为所述碳化的热源,部分用于所述重油的分馏加热;
(3)所述木醋液经蒸馏分离出多余的水分后,收集木醋液;所述重油进行精馏;
(4)所述多余的水分进一步加热后,以水蒸气的形式给所述干馏提供热量;所述精馏积余的底油送与瓦斯气混合一起燃烧。
如上所述的棉花秸杆碳化多联产综合利用工艺,经自然干燥后破碎的棉花秸秆的粒径为40~100mm。
如上所述的棉花秸杆碳化多联产综合利用工艺,干馏温度为280~350℃,碳化温度为400~500℃。如上所述的棉花秸杆碳化多联产综合利用工艺,重油精馏产物为生物质柴油、汽油和润滑油。
本发明的棉花秸杆碳化多联产综合利用系统的具体过程为:
a)将干燥、破碎后的棉花秸秆送入生物质一级干馏炉-1中进行干馏,产生瓦斯气、挥发分和半焦;
b)半焦被送入半焦收集罐-12,随后经给料机送入生物质半焦二级碳化炉-2,经高温烟气加热后生成焦炭存储于焦炭存储罐-3中;
c)挥发分经冷凝收集至沉降分离器-6中沉降、分层,上层为木醋液,经离心泵输送至木醋液存储罐-8中,下层为重油,收集至重油存储罐-7;
d)产生的瓦斯气通入瓦斯燃烧炉中进行燃烧,产生的高温烟气部分通入生物质半焦二级碳化炉-2中作为热源加热步骤b)中产生的焦炭,部分通入精馏塔-9中对步骤c)中产生的重油进行分馏加热。
e)步骤c)中产生的木醋液经蒸馏塔分离出多余的水分后,收集于浓缩木醋液存储罐-11中,多余的水分经换热器-4加热后,以水蒸气的形式通入生物质一级干馏炉-1中以增加生物质热解瓦斯气产量;
f)步骤d)中通入生物质半焦二级气化炉-2中的高温烟气作为热载体排出后,继续进入生物质半焦一级干馏炉-1中作为热载体与热源对生物质进行加热;
作为一种实施方案,步骤c)中,所述木醋液与重油利用物理沉降分层方式分离。
作为一种实施方案,步骤c)中,分离出的木醋液先被送入木醋液储存罐-8中,然后被送入蒸馏塔中进行蒸馏,获得浓缩木醋液;重油被送入精馏塔-9中进行精馏。
作为一种实施方案步骤d)中,精馏塔-9底油被输送至瓦斯燃烧室-5中,混合瓦斯气共同燃烧。
如上所述的棉花秸杆碳化多联产综合利用系统及工艺,经前期调研计算,可初步可对其经济效益进行如下预估:由于干馏及碳化所需热量完全来自棉花秸秆热解气本身,因此本系统无需额外能量消耗,1t棉花秸秆可获得生物质商品油共计约90kg,重油沥青10kg左右,获得生物质碳约3000kg,排出二氧化碳1.5t左右,远小于就地燃烧所排放的3.5t上下。在获得生物质碳、商品油等资源的同时,降低了二氧化碳和其他有害气体的排放。
本文用于企业家、创业者技术爱好者查询,结果仅供参考。