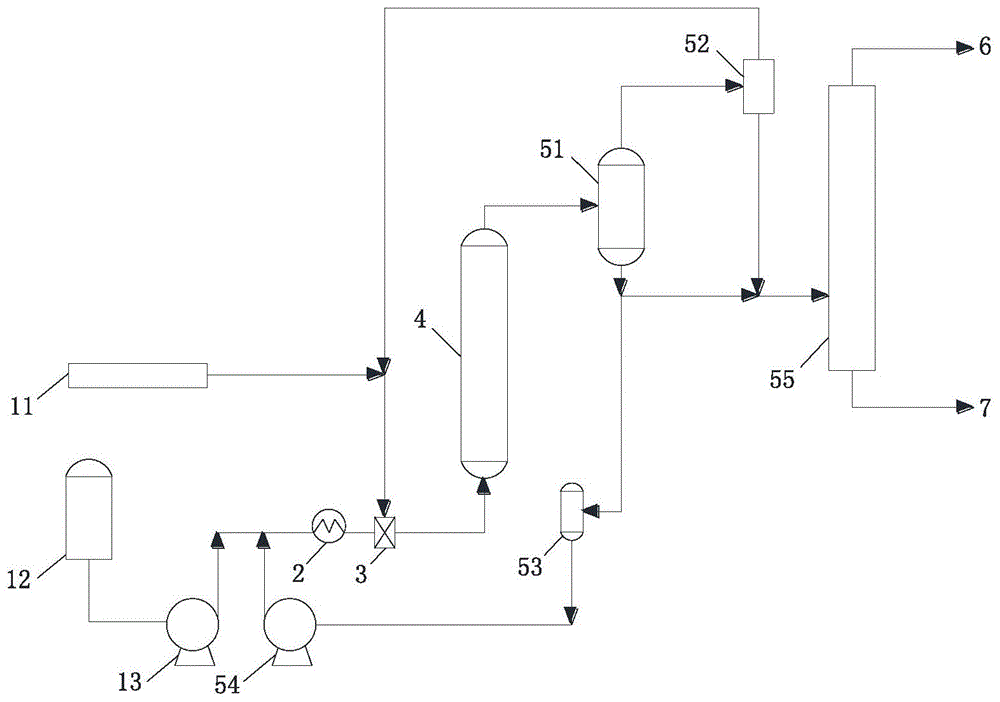
本实用新型涉及煤直接液化
技术领域:
,具体而言,涉及一种煤直接液化循环溶剂的制备系统。
背景技术:
:煤直接液化是煤在高温、高压、临氢、溶剂和催化剂存在下,热解加氢生成液态产品的工艺过程。在煤直接液化过程中,溶剂起了十分重要的作用:溶剂与煤配成煤浆,便于煤的输送和加压;能够溶解煤、防止煤热解产生的自由基碎片缩聚,从而提高煤液化油收率;能够溶解气相氢,使氢分子向煤或催化剂表面扩散;能够向自由基碎片直接供氢或传递氢。因此煤直接液化溶剂既要对煤热解的自由基碎片有较强的溶解能力,同时也具备良好的供氢能力。溶剂直接向自由基碎片的供氢是煤液化过程中溶剂的特殊功能,研究发现部分氢化的多环芳烃(如四氢萘、二氢菲、二氢蒽、四氢蒽等)具有很强的供氢性能。在目前实现长周期连续运转的煤直接液化工艺中,溶剂来自煤直接液化工艺本身,即煤直接液化油经过加氢稳定制得,并在煤直接液化过程中循环使用,也称作循环溶剂。根据煤加氢液化反应机理中的自由基理论,在煤加氢液化过程中,氢不能直接与煤分子反应使煤裂解,而是与煤分子本身受热分解生成不稳定的自由基“碎片”发生反应,若有足够的氢存在,自由基就能得到饱和而稳定下来,如果供氢不足,则自由基之间会相互结合转变为不溶性的焦。因此提高煤直接液化过程中系统的供氢性能,能够促进煤的转化,增加煤液化油收率,同时还有利于煤浆制备、输送和在进料预热器中的流动等。技术实现要素:鉴于此,本实用新型提出了一种煤直接液化循环溶剂的制备系统,旨在达到提高煤直接液化过程中系统供氢性能的效果。本实用新型提出了一种煤直接液化循环溶剂的制备系统包括:进料单元、反应器、微界面发生器:所述微界面发生器,一端与进料单元连接,另一端与反应器连接,用于在煤直接液化油加氢反应之前,将氢气的压力能和/或反应过程中的液体的动能转化为氢气气泡的表面能,使氢气破碎成微米级气泡,以增大加氢反应过程中所述氢气与所述煤直接液化油之间的相界传质面积,并使所述微米级气泡与所述的液体混合形成气液乳化物,将气液乳化物输送至反应器内进行后续反应;所述进料单元,用于存储和输送煤直接液化油和氢气,并对两者进行预热处理;所述反应器,用于作为煤直接液化油加氢反应过程的反应腔室。进一步地,上述煤直接液化循环溶剂的制备系统中,所述微界面发生器为气动式微界面发生器、液动式微界面发生器和气液联动式微界面发生器中的一种。进一步地,上述煤直接液化循环溶剂的制备系统中,所述进料单元包括:液相进料单元,用以存储和运输煤直接液化油;气体进料管道,用以运输氢气进料预热器,其分别与液相进料单元和微界面发生器连接用以对煤直接液化油进行预热。进一步地,上述煤直接液化循环溶剂的制备系统中,所述液相进料单元包括:液体原料罐,用以存储煤直接液化油;进料泵,其与所述液体原料罐、进料预热器相连,用以将煤直接液化油运输至进料预热器内部。进一步地,上述煤直接液化循环溶剂的制备系统中,还包括气液分离循环单元,其与反应器相连,用于接收反应器输出的混合物并对混合物进行气液分离和循环利用。进一步地,上述煤直接液化循环溶剂的制备系统中,所述气液分离循环单元包括:热高压分离器,其与反应器相连,用于将反应器输出的混合物分离成热高分气和热高分油;冷高压分离器,其与热高压分离器相连,用于将热高压分离器分离出来的热高分气体分离成冷高分气和冷高分油;循环油收集罐,其与热高压分离器相连,用于收集热高压分离器内未能分离的混合物;循环油泵,其一端与循环油收集罐相连,另一端与进料预热器相连,用于将循环油收集罐内的混合物运输至进料预热器内部与煤直接液化油混合,随煤直接液化油在系统中流动,从而进行二次加氢反应;分馏塔,其分别与热高压分离器、冷高压分离器连接,用于将热高分油和冷高分油进行分馏,从而得到煤直接液化循环溶剂。进一步地,上述煤直接液化循环溶剂的制备系统中,所述微米级气泡为直径大于等于1μm、小于1mm的微米级气泡。进一步地,上述煤直接液化循环溶剂的制备系统中,所述加氢反应在反应器中进行,所述反应器为沸腾床反应器、浆态床反应器、膨胀床反应器,或者沸腾床反应器、浆态床反应器、膨胀床反应器中的一种与固定床反应器组成的串联反应系统。本实用新型的有益效果在于,本实用新型提供的煤直接液化循环溶剂的制备系统,通过在进料单元与反应器之间设置微界面发生器,在所述加氢反应中的氢气与煤直接液化油在进入所述反应器之前将所述氢气在所述微界面发生器中破碎成直径为大于等于1μm、小于1mm的微米级气泡,以增大反应过程中所述氢气与所述煤直接液化油之间的相界传质面积,减小了液膜厚度,降低了传质阻力,从而提高反应相之间的传质效率,进而实现提高煤直接液化过程中系统供氢性能的效果。此外,可以根据不同原料组成、不同的产品要求或不同的催化剂,而对预设操作条件的范围进行灵活调整,进一步确保了反应的充分有效进行,进而保证了反应速率,达到了强化反应的目的。尤其,所述液相进料单元中设有进料泵,在所述系统运行时,进料泵能够为煤直接液化油的运输提供动力,使煤直接液化油能够以指定的速率输送至指定装置,提高了所述系统的运行效率。尤其,所述系统中设置有气液分离循环单元,此单元可使得加氢反应过程中,为充分反应的氢气和煤直接液化油,可以进行二次循环反应,从而挺高反应效率,节约能源,降低成本。附图说明通过阅读下文优选实施方式的详细描述,各种其它的优点和益处对于本领域普通技术人员将变得清楚明了。附图仅用于示出优选实施方式的目的,而并不认为是对本实用新型的限制。而且在整个附图中,用相同的参考符号表示相同的部件。在附图中:图1为本实用新型实施例提供的煤直接液化循环溶剂的制备系统的结构示意图。具体实施方式为了使本实用新型的目的和优点更加清楚明白,下面结合实施例对本实用新型作进一步描述;应当理解,此处所描述的具体实施例仅仅用于解释本实用新型,并不用于限定本实用新型。下面参照附图来描述本实用新型的优选实施方式。本领域技术人员应当理解的是,这些实施方式仅仅用于解释本实用新型的技术原理,并非在限制本实用新型的保护范围。需要说明的是,在本实用新型的描述中,术语“上”、“下”、“左”、“右”、“内”、“外”等指示的方向或位置关系的术语是基于附图所示的方向或位置关系,这仅仅是为了便于描述,而不是指示或暗示所述装置或元件必须具有特定的方位、以特定的方位构造和操作,因此不能理解为对本实用新型的限制。此外,还需要说明的是,在本实用新型的描述中,除非另有明确的规定和限定,术语“安装”、“相连”、“连接”应做广义理解,例如,可以是固定连接,也可以是可拆卸连接,或一体地连接;可以是机械连接,也可以是电连接;可以是直接相连,也可以通过中间媒介间接相连,可以是两个元件内部的连通。对于本领域技术人员而言,可根据具体情况理解上述术语在本实用新型中的具体含义。参阅图1所示,为本实用新型实施例提供的煤直接液化循环溶剂的制备系统,其包括:进料单元、进料预热器2、微界面发生器3(microinterfacialgenerator,简称mig)、反应器4、气液分离循环单元;其中,进料单元,用以存储和输送煤直接液化油和氢气;所述进料预热器2与进料单元相连,用以对煤直接液化油和氢气进行预热;所述微界面发生器3位于所述进料预热器2和所述反应器4之间,入口端与进料预热器2和进料单元相连,出口端与反应器4相连,用以接收预热后的煤直接液化油和氢气并将氢气破碎为微米级气泡;所述反应器4,出口端与气液分离循环单元相连,用于作为煤直接液化油加氢反应过程的反应腔室,并将加氢反应生成的混合物输送至分离循环单元进行气液分离和循环利用。当所述系统运行时,所述进料单元启动,将煤直接液化油输送至进料预热器2中进行预热,预热完毕后将,将煤直接液化油输送至所述微界面发生器3,同时进料单元将氢气输送至所述微界面发生器3内部,微界面发生器3会对氢气进行打碎,使氢气破碎至微米尺度,形成直径大于等于1μm、小于1mm的微米级气泡,在破碎完成后,微界面发生器3将微米级气泡与煤直接液化油混合形成气液乳化物,微界面发生器3在气液乳化物混合完成后将气液乳化物输出至反应器4,通过控制反应器4内部的温度、气压以及气液乳化物的空速以使气液乳化物在反应器内进行高效反应,反应完成后反应器4将生成的混合物输出至分离循环单元进行气液分离和循环利用。继续参阅图1所示,所述进料单元包括:气体进料管道11、液体原料罐12和进料泵13;其中,所述气体进料管道11一端外接氢气源另一端与微界面发生器3连接,用以运输氢气至微界面发生器3内部;所述进料泵13一端与所述液体原料罐12相连另一端与进料预热器2连接,用以将液体原料罐12内的煤直接液化油抽出运输至进料预热器2内部;当所述进料单元运行时,所述进料泵13会抽取所述液体原料罐12中储存的煤直接液化油并将其输送至进料预热器2,进料预热器2对煤直接液化油预热至指定温度后,将其输送至所述微界面发生器3,同时气体进料管道11将氢气输送至所述微界面发生器3。具体而言,所述液体原料罐12为一罐体,用以储存煤直接液化油,液体原料罐12与所述进料泵13相连,用以在系统运行时,通过进料泵13将煤直接液化油输送至指定位置。可以理解的是,所述液体原料罐12可以为金属油罐,也可以为非金属油罐,只要满足所述液体原料罐12能够装载指定量的煤直接液化油即可。具体而言,进料预热器2为加热炉,其进口端与进料泵13连通,出口端与微界面发生器3入口端连通,用以对煤直接液化油预热,当加热到指定温度时其输送至微界面发生器3内部。具体而言,微界面发生器3与反应器4连通,用以接收进料预热器2预热完成的煤直接液化油和气体进料管道11输送的氢气,并将氢气破碎成直径为微米级气泡,且破碎完成后将二者同时输送至反应器4内进行加氢反应。微界面发生器根据能量输入方式或气液比分为气动式微界面发生器、液动式微界面发生器和气液联动式微界面发生器,其中气动式微界面发生器采用气体驱动,输入气量远大于液体量;液动式微界面发生器采用液体驱动,输入气量一般小于液体量;气液联动式微界面发生器采用气液同时驱动,输入气量接近于液体量。所述微界面发生器3为气动式微界面发生器、液动式微界面发生器和气液联动式微界面发生器中的一种或几种。具体而言,反应器4为沸腾床反应器、浆态床反应器、膨胀床反应器,或者沸腾床反应器、浆态床反应器、膨胀床反应器中的一种与固定床反应器组成的串联反应系统。继续参阅图1所示,气液分离循环单元包括:热高压分离器51、冷高压分离器52、循环油收集罐53、循环油泵54、分馏塔55:其中热高压分离器51入口端与反应器4顶部连通,出口端与分别与冷高压分离器52、循环油收集罐53、分馏塔55的入口端连通;冷高压分离器52出口端分别与进料预热器2和分馏塔55连通;循环油收集罐53出口端通过循环油泵54和进料预热器2入口端连通。系统工作时,液体原料罐12中的煤直接液化油经进料泵13进入进料预热器2,加热后的物料进入微界面发生器3中,同时气体进料管道11输送的氢气至微界面发生器3,微界面发生器3将氢气破碎成直径为大于等于1μm、小于1mm的微米级气泡,完成破碎后的物料进入反应器4中进行加氢稳定反应,反应器4顶端出来的物料经热高压分离器51分离成热高分气和热高分油,热高分气进入冷高压分离器52后分离出冷高分气和冷高分油,冷高分气循环至进料预热器2内,冷高分油进入分馏塔55,热高压分离器51底部分离出的流出物分两路,一路进入循环油收集罐53,经循环油泵54与原料油混合进入反应器4进行循环;另一路与冷高分油一同进入分馏塔55,经分馏塔55分离出的轻质馏分油与部分中质馏分油混合一同进入下游装置用于加工燃料产品(如车用汽柴油),经分馏塔55分离出的部分中质馏分油和重质馏分油混合即为煤直接液化循环溶剂。本实用新型提供的煤直接液化循环溶剂的制备系统,通过在反应器4上连接微界面发生器3,在所述加氢反应过程中的氢气与煤直接液化油混合物料进入所述反应器4之前将所述氢气在所述微界面发生器3中破碎成微米级气泡,有效地增大了反应过程中所述氢气与煤直接液化油之间的相界传质面积,极大地提高了反应相之间的传质效率,进而实现提高煤直接液化过程中系统供氢性能的效果。下面结合图1进一步说明本实用新型所述系统的具体方法与效果。一种煤直接液化循环溶剂的制备方法,包括以下步骤:步骤1:在运行系统前向所述液体原料罐12中添加指定量的煤直接液化油;步骤2:添加完成后启动系统,进料泵从液体原料罐中抽取煤直接液化油至进料预热器内部,使得煤直接液化油加热至指定温度;步骤3:将预热后的煤直接液化油和气体进料管道的氢气运输至对应的微界面发生器内部,微界面发生器将氢气打碎成微米级气泡,打碎完成后,将微米级气泡和煤直接液化油进行混合形成气液乳化物;步骤4:所述微界面发生器3在微米级气泡和煤直接液化油混合完成后将其输送至反应器4,控制反应器4内的压力和温度进行煤直接液化油的加氢反应,并使气液乳化物按指定方向流动;步骤5:得到的加氢产物经热高压分离器51分离出热高分气和热高分油;步骤6:得到的所述热高分油一部分与煤直接液化油混合后循环加氢,另一部分所述热高分气冷却得到的冷高分油混合进入分馏塔55;步骤7:所述分馏塔55分馏得到轻质馏分油、中质馏分油和重质馏分油;步骤8:将所述重质馏分油与部分所述中质馏分油混合得到所述煤直接液化循环溶剂。其中,在上述步骤4中所述加氢反应的温度为300-400℃,优选330-360℃;所述反应压力为1.0-12.0mpa,优选2.0-8.0mpa。可以理解的是,可以根据不同原料组成、不同的产品要求或不同的催化剂,而灵活地进行预设操作条件的范围调整,以确保反应的充分有效进行,进而保证反应速率,达到了强化反应的目的。同时,本实施例中不具体限定催化剂的种类,其可以为铁系催化剂、钼系催化剂、镍系催化剂、钴系催化剂以及钨系催化剂中的一种或几种组合,只要能够确保强化反应顺利进行即可。为了进一步验证本实用新型所提供的加工方法,以煤直接液化油为原料,在反应器内采用加氢精制催化剂进行试验,结合实施例和对比例进一步说明本实用新型的有益效果。在本实用新型中,pdqi为供氢指数,表示溶剂的供氢能力,是指位于环烷基芳烃上环烷基β位氢原子的质量与溶剂质量之比,即每克供氢溶剂中位于环烷基芳烃上环烷基β位氢原子的毫克数。实施例1-3按照图1所示工艺流程制备循环溶剂,表1示出了煤直接液化油性质,表2示出了实施例1-3以及对比例1-3所用的加氢催化剂及加氢催化剂性能,表3给出了实施例1-3及对比例1-3的加氢工艺条件,表4示出了实施例1-3及对比例1-3的循环溶剂性质。对比例是以表1所列煤直接液化油为原料,采用与实施例相同的试验装置、催化剂、试验条件进行的加氢试验。表1原料油性质表2加氢精制催化剂性质表3加氢实验工艺条件工艺参数对比例1实施例1对比例2实施例2对比例3实施例3反应温度,℃330330345345360360反应压力,mpa225588氢油体积比3003001000100015001500主剂总体积空速,h-111223.53.5表4循环溶剂性质通过表4中实施例1与对比例1、实施例2与对比例2、实施例3与对比例3的对比可以看出,本实用新型循环溶剂的单环和双环芳烃含量增加,供氢指数均有提高,说明煤直接液化油与氢反应前,用微界面发生器对氢进行破碎处理,使得其中重质芳烃活性氢数量增加,从而达到提高煤直接液化过程中系统供氢性能的效果。显然,本领域的技术人员可以对本实用新型进行各种改动和变型而不脱离本实用新型的精神和范围。这样,倘若本实用新型的这些修改和变型属于本实用新型权利要求及其等同技术的范围之内,则本实用新型也意图包含这些改动和变型在内。当前第1页12
再多了解一些
本文用于企业家、创业者技术爱好者查询,结果仅供参考。