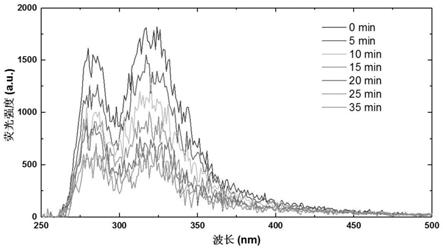
1.本发明涉及有机固体废弃物处理与应用技术领域,尤其涉及一种由有机固体废弃物热解形成的热解油电化学温和高效加氢方法。
背景技术:
2.固体有机物,例如煤和有机固体废弃物(农林废弃物、塑料、有机医疗废弃物等)热解得到的热解油是一种有前景的液体燃料,有望部分替代石油。相对于石油,热解油品质较低,主要表现为含氧量较高、含水量较高、导致热值低、热稳定性差,因而无法在现有的石油化工炼化设备中顺利处理,需进行进一步的高值化利用。
3.为了提升热解油的品质,使其适合在现有石油炼化设备中进行处理,热解油通常需要进行加氢提质。常规的热解油加氢提质工艺需要在高温高压下进行,且需要使用催化剂,而由于热解油组分受热易结焦,常规的热解油加氢提质工艺面临催化剂易积碳失活、反应器易结焦堵塞等技术难题。
4.针对上述问题,近年来,热解油电化学加氢提质的工艺被提出,电化学加氢工艺在常温常压下进行,极大的避免了热解油受热结焦及催化剂积碳失活问题,是一种十分有前景的热解油加氢提质技术。然而,目前热解油电化学加氢提质工艺在规模化应用时,仍存在如下问题亟待解决:1、提升电压/电流时,大量电能用于析氢反应,导致体系效率不高;2、提质后的热解油产品中仍存在大量水分,难以去除,不利于热解油的进一步利用;3、加氢过程主要在电极表面进行,热解油组分向电极表面转移过程存在传质阻力,限制了反应速率的提升。
5.鉴于上述情况,亟需研发一种可突破反应效率和速率限制的高效的生物油电化学加氢方法。
技术实现要素:
6.针对上述问题,现提供一种热解油电化学温和高效加氢方法,旨在通过耦合杂多酸和贵金属纳米颗粒的双重催化效应有效提升电化学加氢的反应速率及法拉第效率,从而实现在温和条件下对生物油进行高效、快速加氢,以显著降低热解油的氧含量和水分含量,提升热解油的热稳定性,并最终有利于热解油的高效、低成本规模化利用。
7.具体技术方案如下:
8.一种热解油电化学温和高效加氢方法,具有这样的特征,包括如下步骤:
9.1)向待加氢热解油中加入水溶性杂多酸及贵金属纳米颗粒催化剂,混合均匀,以使杂多酸溶解于热解油所含水分中、使贵金属纳米颗粒均匀分散在热解油中;
10.2)、将步骤1)中混合均匀的热解油注入由阳离子交换膜分隔形成的阴极室中,再向由阳离子交换膜分隔形成的阳极室中注入辅助溶液,在阳极室及阴极室中分别对应布置阳极电极、阴极电极;
11.3)、搅拌下通过电极对热解油施加高于热解油自身析氢电压的电压,使热解油发
生电化学反应;
12.4)、反应结束,对步骤3)中阴极室内热解油进行离心分离,过滤,滤渣即为杂多酸及贵金属纳米颗粒,滤液即为加氢提质后热解油。
13.上述的热解油电化学温和高效加氢方法,还具有这样的特征,步骤1)中以每升热解油计杂多酸加入量为0.01
‑
0.2mol。
14.上述的热解油电化学温和高效加氢方法,还具有这样的特征,步骤1)中以热解油质量计贵金属纳米颗粒催化剂的加入量为0.05
‑
0.2wt%。
15.上述的热解油电化学温和高效加氢方法,还具有这样的特征,步骤1)中贵金属纳米颗粒催化剂由贵金属负载于多孔活性载体上形成。
16.上述热解油电化学温和高效加氢方法,还具有这样的特征,贵金属为钌、铑、钯、锇、铱、铂中的一种。
17.上述热解油电化学温和高效加氢方法,还具有这样的特征,活性载体为活性炭、石墨烯、tio2中的一种。
18.上述的热解油电化学温和高效加氢方法,还具有这样的特征,步骤2)中辅助溶液为无机酸溶液。
19.上述热解油电化学温和高效加氢方法,还具有这样的特征,无机酸为硫酸、盐酸、高氯酸、磷酸溶液中的一种。
20.上述的热解油电化学温和高效加氢方法,还具有这样的特征,步骤3)中电化学反应时间为0.5
‑
4h,电化学反应中电流密度为100
‑
800ma cm
‑2,搅拌速度为300
‑
800rpm。
21.上述的热解油电化学温和高效加氢方法,还具有这样的特征,热解油由含碳固体有机物于惰性气氛下在200
‑
800℃发生热裂解反应后得到的挥发份迅速冷凝形成。
22.本发明中以高于热解油自身析氢电压的电压对热解油进行电化学加氢,虽然电化学电压超过析氢电压会促使部分电能用于电解热解油所含的水产生氢气和氧气,但是均匀溶解于热解油中的杂多酸可迅速与气相氢气结合并将气相h2转化为“液相”活性氢,由此使得液相电解反应体系中活性氢浓度得到显著提升,并进而显著降低热解油中有机组分在贵金属纳米颗粒催化剂上加氢所需的活化能;同时,不同于传统方式中仅在电极上发生加氢反应,本发明中将贵金属纳米颗粒催化剂均匀分散在热解油中,不仅有效的利用了贵金属催化加氢反应的能力,还有效突破了传统方式下热解油有机组分向电极迁移过程中的传质限制,更是将加氢反应扩展到了整个液相体系中,从而进一步加强了加氢反应速率。因此,本发明中杂多酸和贵金属纳米颗粒催化剂的双重催化体系可以显著促进氢通过贵金属纳米颗粒催化剂向热解油组分转移,从而实现热解油快速加氢,因此本发明中适当析氢并不降低法拉第效率,相反,适当的电解水过程一方面有助于提升液相反应体系中的活性h浓度,有助于提升加氢反应速率;另一方面,电解消耗了热解油中的水,降低了目标产物油中水分含量,进一步提升产品的品质。
23.本发明中电化学反应结束后由于水分消耗完毕,杂多酸会析出结晶,而加氢提质后的热解油由于粘度显著降低,故可对热解油进行离心分离。
24.上述方案的有益效果是:
25.1)、本发明中加氢反应的电压及电流密度比常规热解油电化学加氢反应高,因而加氢速率更快,且加大电压还消耗了热解油中的水,大大降低了提质后油的水分含量;
26.2)、本发明中电化学加氢时电解水产生的氢气迅速与杂多酸结合形成活性氢,因此提高反应电压导致析氢产生的氢气仍会通过本发明的方法对热解油有机组分进行加氢,最终在可实现提升电化学参数的同时还不降低法拉第效率;
27.3)、上述活性氢在加氢反应过程中所需活化能低,更有助于在贵金属纳米颗粒催化剂上发生加氢反应。本发明的液相加氢体系中存在均分分布的贵金属纳米颗粒催化剂,可近似以“液相形式”实现热解油原位均相加氢,突破了传统热解油电化学加氢中需在电极进行反应的限制,大大提升了传质速率和反应效率。
附图说明
28.图1为本发明实施例1中热解油的恒能量差紫外荧光光谱图;
29.图2为本发明实施例1中加氢前后热解油中特征组分含量图;
30.图3为本发明实施例1及对比例1中法拉第效率与电流密度测试图。
具体实施方式
31.下面将结合本发明实施例中的附图,对本发明实施例中的技术方案进行清楚、完整地描述,显然,所描述的实施例仅仅是本发明一部分实施例,而不是全部的实施例。基于本发明中的实施例,本领域普通技术人员在没有做出创造性劳动的前提下所获得的所有其他实施例,都属于本发明保护的范围。
32.需要说明的是,在不冲突的情况下,本发明中的实施例及实施例中的特征可以相互组合。
33.下面结合附图和具体实施例对本发明作进一步说明,但不作为本发明的限定。
34.实施例1
35.一种热解油电化学温和高效加氢方法,包括如下步骤:
36.1)、向待加氢热解油中加入水溶性杂多酸(本实施例中杂多酸选用siw
12
,以每升热解油计杂多酸加入量为0.01mol)及贵金属纳米颗粒催化剂(本发明中为pt纳米颗粒,且以热解油质量计pt纳米颗粒的加入量为0.05wt%),混合均匀,以使杂多酸溶解于热解油所含水分中、使贵金属纳米颗粒均匀分散在热解油中;
37.2)、将步骤1)中混合均匀的热解油注入由阳离子交换膜分隔形成的阴极室中,再向由阳离子交换膜分隔形成的阳极室中注入辅助溶液(本实施例中为硫酸),在阳极室及阴极室中分别对应布置阳极电极、阴极电极;
38.3)、搅拌下通过电极对热解油施加高于热解油自身析氢电压的电压,使热解油发生电化学反应;
39.4)、反应结束,对步骤3)中阴极室内热解油进行离心分离,过滤,滤渣即为杂多酸及pt纳米颗粒(回用),滤液即为加氢提质后热解油;
40.其中,步骤3)中电化学反应时间为0.5h,电化学反应中电流密度为100ma cm
‑2,搅拌速度为300rpm。
41.如图1所示,使用本发明提供的加氢方法进行加氢后热解油中芳香组分的含量均下降;进一步的,如图2所示,使用上述加氢方法进行加氢后热解油中苯酚、环己酮等不饱和组分比例下降,而环己醇、环己醇等组分比例上升,这说明使用本发明提供的加氢方法可有
效对热解油进行加氢反应。
42.如图3所示,使用siw
12
和pt纳米颗粒时即使电流密度增加到600ma cm
‑2,体系中法拉第效率仍较高,这表明siw
12
和pt纳米颗粒双重催化体系可通过提升电化学参数显著提升反应速率,且不降低法拉第效率。
43.本发明中利用卡尔费休滴定法检测电化学加氢前、后热解油水分含量,发现热解油中水分由电解前的26.00wt%下降为电解后的5.23wt%,说明利用本发明提供的加氢方法进行加氢后产物油中水分含量得到显著降低。
44.实施例2
45.一种热解油电化学温和高效加氢方法,包括如下步骤:
46.1)、向待加氢热解油中加入水溶性杂多酸(本实施例中杂多酸选用siw
12
,以每升热解油计杂多酸加入量为0.1mol)及贵金属纳米颗粒催化剂(本发明中为pt纳米颗粒,且以热解油质量计pt纳米颗粒的加入量为0.12wt%),混合均匀,以使杂多酸溶解于热解油所含水分中、使贵金属纳米颗粒均匀分散在热解油中;
47.2)、将步骤1)中混合均匀的热解油注入由阳离子交换膜分隔形成的阴极室中,再向由阳离子交换膜分隔形成的阳极室中注入辅助溶液(本实施例中为硫酸),在阳极室及阴极室中分别对应布置阳极电极、阴极电极;
48.3)、搅拌下通过电极对热解油施加高于热解油自身析氢电压的电压,使热解油发生电化学反应;
49.4)、反应结束,对步骤3)中阴极室内热解油进行离心分离,过滤,滤渣即为杂多酸及pt纳米颗粒(回用),滤液即为加氢提质后热解油
50.其中,步骤3)中电化学反应时间为2.4h,电化学反应中电流密度为510ma cm
‑2,搅拌速度为560rpm。
51.实施例3
52.一种热解油电化学温和高效加氢方法,包括如下步骤:
53.1)、向待加氢热解油中加入水溶性杂多酸(本实施例中杂多酸选用siw
12
,以每升热解油计杂多酸加入量为0.2mol)及贵金属纳米颗粒催化剂(本发明中为pt纳米颗粒,且以热解油质量计pt纳米颗粒的加入量为0.2wt%),混合均匀,以使杂多酸溶解于热解油所含水分中、使贵金属纳米颗粒均匀分散在热解油中;
54.2)、将步骤1)中混合均匀的热解油注入由阳离子交换膜分隔形成的阴极室中,再向由阳离子交换膜分隔形成的阳极室中注入辅助溶液(本实施例中为高氯酸),在阳极室及阴极室中分别对应布置阳极电极、阴极电极;
55.3)、搅拌下通过电极对热解油施加高于热解油自身析氢电压的电压,使热解油发生电化学反应;
56.4)、反应结束,对步骤3)中阴极室内热解油进行离心分离,过滤,滤渣即为杂多酸及pt纳米颗粒(回用),滤液即为加氢提质后热解油;
57.其中,步骤3)中电化学反应时间为4h,电化学反应中电流密度为800ma cm
‑2,搅拌速度为800rpm。
58.对比例1
59.本对比例中加氢方法与实施例1中基本相同,区别在于本对比例步骤1)中未向待
加氢热解油中加入水溶性杂多酸及pt纳米颗粒。
60.由图3可知,在提升电化学加氢过程的电流密度时未使用siw
12
和pt纳米颗粒情况下体系法拉第效率显著下降,由此可知本对比例中加氢反应速率将明显低于本发明实施例1中加氢速率。
61.以上所述仅为本发明较佳的实施例,并非因此限制本发明的实施方式及保护范围,对于本领域技术人员而言,应当能够意识到凡运用本发明说明书及图示内容所做出的等同替换和显而易见的变化所得到的方案,均应当包含在本发明的保护范围内。
再多了解一些
本文用于企业家、创业者技术爱好者查询,结果仅供参考。