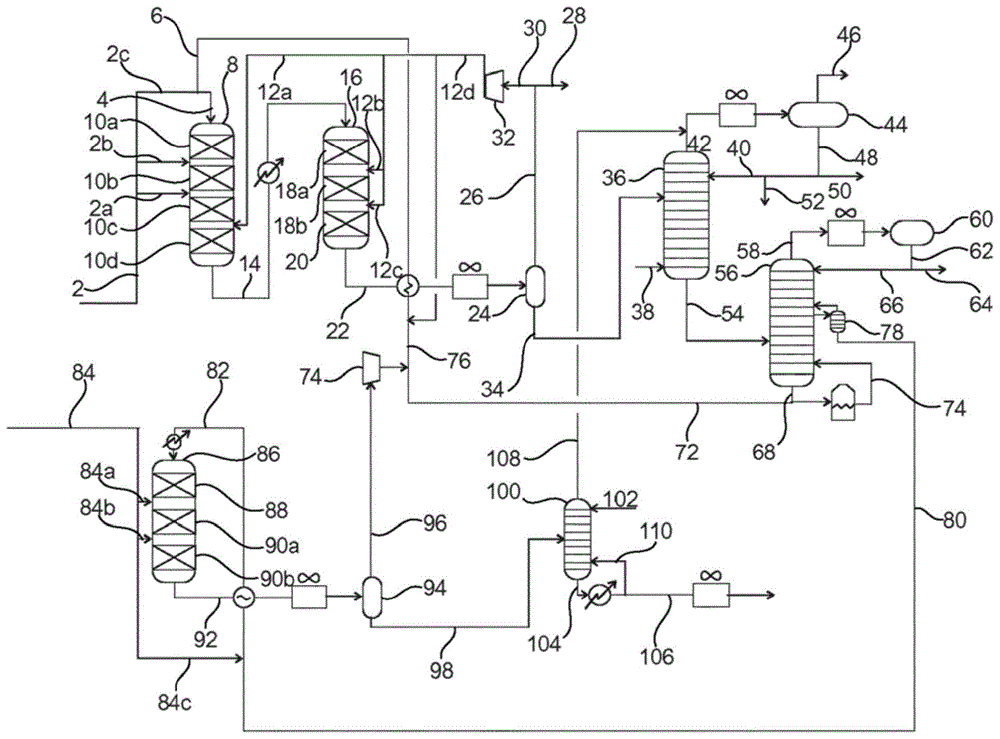
迄今为止,加氢处理中可再生物的转化一直集中在制造柴油上,因为石蜡对应于生物材料的典型脂肪酸,例如植物油和动物脂肪(c14、c16和c18)的典型沸点为250℃至320℃,很好地对应于沸点为150℃至380℃的典型的柴油产品。喷气燃料产品要求的沸点范围为120℃至300℃或310℃,这意味着来自可再生原料的石蜡的重质部分需要被转化为较轻质的材料,才能仅生产喷气燃料。由可再生物生产喷气燃料的另一个挑战是,在可再生原料的加氢处理过程中发现了令人惊讶的高产量的芳族化合物。本发明涉及一种具有高产率的可再生喷气燃料的方法,其通过将重质材料转化为较轻质材料并限制产物中芳族化合物的量来满足典型的产物要求。已知通过在设计用于制造柴油的单元中共同生产一些喷气燃料来从可再生原料生产喷气燃料。但是,有兴趣将主要在柴油沸程内的可再生原料完全转换为喷气燃料产品,这需要显著的转换。控制源自加氢处理的含氧化合物(如酯和脂肪酸)的喷气燃料的质量的标准是astmd7566,a2.1,其中特别规定了沸点曲线和组成。通过加氢处理和分馏可以很容易地满足这些性质中的大多数。但是,需要特别注意以满足最高-40℃的凝固点(fp)要求和最高0.5wt%的芳族化合物总含量。此外,该标准通过要求t10(即根据astmd86已蒸馏10%的温度)为205℃以下而要求一定量的低沸点产物。根据astmd86,最终沸点(fbp)被指定为300℃,这意味着根据astmd86在300℃以上蒸馏的所有物质都必须被转化为更轻质的成分,才能落入喷气燃料范围。现在根据本发明,提出以两阶段构造进行喷气燃料生产,其中在第一阶段中对进料进行加氢处理、加氢裂化和任选的异构化,并且在去除酸性气体之后,在第二阶段中进行加氢脱芳构化和任选的异构化。在这两个阶段之间,可以使用全分馏工段以分离出用于第二阶段的煤油原料,并产生比煤油重的流,该流在第一阶段中再循环至不复存在。提高喷气燃料的凝固点的异构化可以在第一阶段、第二阶段或这两个阶段中完成。在下文中,术语阶段应当用于过程的不执行任何分离的工段。在下文中,缩写ppm摩尔应当用于表示每百万份的原子份数。在下文中,缩写ppmw应当用于表示每百万份重量的份数,即mg/kg。在下文中,缩写wt/wt%应当用于表示重量百分比。在下文中,缩写vol/vol%应当用于表示气体的体积百分比。在下文中,以“atlasofzeoliteframeworktypes”,第六修订版,elsevier,2007中描述的意义使用术语分子筛的拓扑结构,并据此使用三个字母的骨架类型代码。在下文中,术语可再生原料或烃应当用于表示源自生物来源或废物回收的原料或烃。化石来源的再循环废物,例如塑料,也应当被视为可再生的。在下文中,术语加氢脱氧用于表示通过在氢的存在下形成水而从含氧化合物中除去氧,以及通过在氢的存在下形成碳氧化物而从含氧化合物中除去氧。本技术实现要素:的广义方面涉及一种用于从含氧化合物原料生产适合用作喷气燃料的烃馏分的方法,所述含氧化合物原料可以是作为可再生原料的原料,该方法包括以下步骤:a.将原料与稀释烃流(diluenthydrocarbonstream)合并以形成加氢处理进料流,与在加氢处理条件下在加氢处理中具有催化活性的材料接触,以提供经加氢处理的中间产物;b.引导至少一定量的所述经加氢处理的中间产物与在加氢裂化条件下在加氢裂化中具有催化活性的材料接触,以提供经加氢裂化的中间产物;c.将经加氢裂化的中间产物分离为经加氢裂化的中间液态馏分和气态馏分;d.引导至少一定量的所述经加氢裂化的中间液态馏分与在加氢脱芳构化条件下在加氢脱芳构化中具有催化活性的材料接触,以提供包含适合用作喷气燃料的烃馏分的经处理的产物,其相关的益处是,以高产率从含氧化合物原料中产生适合用作喷气燃料的烃馏分。在另一个实施方案中,引导一定量的所述经加氢裂化的中间液态馏分作为所述稀释烃流,其相关的益处是,提供稀释烃流作为散热剂(heatsink),并通过稀释来缓和聚合反应,同时避免或减少所需的外部流的量,潜在地充分避免在操作中使用化石原料。在另一个实施方案中,步骤c包括将液态的经加氢裂化的中间产物分离为根据astmd86低于310℃,其相关的益处是,提取(withdrawing)比适用于喷气燃料的烃馏分更重质的产物馏分。在另一个实施方案中,步骤c包括根据沸点分离液态的经加氢裂化的中间产物,以提供根据astmd86具有120℃以上的t5和310℃以下的最终沸点的经加氢裂化的中间喷气燃料产物(jetproduct),其构成步骤d的经加氢裂化的中间液态馏分,其相关的益处是,使得能够在包含元素贵金属的具有催化活性的材料上进行加氢脱芳构化,且尽管在异构化中具有催化活性的材料上发生加氢裂化副反应,仍能实现最大的喷气燃料产率(jetyield)。在另一个实施方案中,步骤b或d进一步包括引导用于异构化的流(其是所述经加氢处理的中间产物、所述经加氢裂化的中间产物或者所述经处理的产物)与在异构化中具有催化活性的材料接触,以提供在步骤b或d中分别用作所述经加氢处理的中间产物、所述经加氢裂化的中间产物或者所述经处理的产物的经异构化的流,其相关的益处是,提供具有符合喷气燃料规范astmd7566的凝固点的产品。在另一个实施方案中,将一定量的任选地根据沸点分离后且至少包含沸点为310℃以上的烃馏分的经加氢裂化的中间产物引导与所述原料或所述经加氢处理的中间产物组合,其相关的益处是,将经加氢裂化的中间产物进一步加氢裂化,以确保高度转化为在喷气燃料沸程内的产物,以及任选地,如果引导至在加氢处理中具有催化活性的材料,则提供可以控制在加氢处理中具有催化活性的材料的温度的稀释剂。在另一个实施方案中,步骤b包括将经加氢处理的中间产物分离成液态的经加氢处理的中间产物和气态馏分以及任选地进一步根据沸点分离液态的经加氢处理的中间产物的步骤,提供根据astmd86,t10为120℃以上且最终沸点为310℃以下的经加氢处理的中间喷气燃料产物,其相关的益处是,去除加氢裂化上游的酸性气体,以允许在包含元素贵金属的催化活性材料的存在下进行加氢裂化,并且如果包括进一步的分离步骤,则使加氢脱芳构化所需的体积以及例如石脑油的潜在产率损失最小化。在另一个实施方案中,任选地通过添加包含一种或多种硫化合物(例如二甲基二硫化物或化石燃料)的流,硫化氢的总体积相对于被引导与在加氢处理中具有催化活性的材料接触的总流的气相中的分子氢的体积为至少50ppmv,100ppmv或200ppmv,其相关的益处是,如果原料中硫含量不足,确保了包含硫化的基础金属(basemetal)的在加氢处理中具有催化活性材料的稳定运行。在另一个实施方案中,所述原料包含至少50wt%的甘油三酸酯或脂肪酸,其相关的益处是,提供产生高链烷烃性的经加氢处理的中间产物的原料。在另一个实施方案中,选择工艺条件,使得转化率为20%、50%或80%以上,所述转化率被定义为所述经加氢裂化的中间产物中沸点为310℃以上的物质的量与所述第二馏分中沸点为310℃以上的物质的量之间的差相对于所述第二馏分中沸点为310℃以上的物质的量,其相关的益处是,提供具有完全或基本完全的整体转化率的工艺,同时避免过度的条件和过度的产量损失。在另一个实施方案中,根据芳族分子的总质量相对于流中所有的烃计算,所述经处理的产物包含小于1wt/wt%、0.5wt/wt%或0.1wt/wt%,其相关的益处是,提供符合喷气燃料规范astmd7566的喷气燃料。在另一个实施方案中,引导包含至少90vol/vol%氢的富氢流(84)与在加氢脱芳构化中具有催化活性的材料接触,并且其中如果将经加氢裂化的中间产物分离成液态馏分和气态馏分,则任选地纯化一定量的所述气态馏分,并引导其与在加氢处理中具有催化活性的材料接触,其相关的益处是,在工艺中有效利用氢气,因为来自加氢脱芳构化的气流在不引导至加氢处理和加氢裂化之前不需要进一步纯化。在另一个实施方案中,将经处理的产物引导至气/液分离器,以提供第二阶段气态馏分和经处理的中间喷气燃料产物,将该经处理的中间喷气燃料产物引导至另一个分离装置,例如汽提器,以提供所述适于用作喷气燃料的烃馏分和经处理的产物尾气,其相关的益处是,提供稳定的喷气燃料产品,同时需要最少的分离设备。在另一个实施方案中,加氢处理条件涉及在250-400℃之间的温度、在30-150巴之间的压力以及在0.1-2之间的液时空速(lhsv),且其中在加氢处理中具有催化活性的材料包含一种或多种选自镍、钴、钼或钨的金属,其负载在包含一种或多种耐热(refractory)氧化物的载体上,所述耐热氧化物例如是氧化铝、二氧化硅或二氧化钛,其相关的益处是,这样的工艺条件非常适合成本有效地从可再生原料中去除杂原子,尤其是氧。在另一个实施方案中,加氢裂化条件涉及在250-400℃之间的温度、在30-150巴之间的压力以及在0.5-8之间的液时空速(lhsv),以及任选地通过用冷的氢、进料或产物骤冷而进行中间冷却,并且其中在加氢裂化中具有催化活性的材料包含(a)一种或多种活性金属,其选自铂、钯、镍、钴、钨和钼;(b)酸性载体,其选自显示高裂化活性且具有诸如mfi、bea和fau的拓扑结构的分子筛,以及无定形酸性氧化物,例如二氧化硅-氧化铝;以及(c)耐热载体,例如氧化铝、二氧化硅或二氧化钛,或其组合,其相关的益处是,这种工艺条件非常适合于调节产品的沸点以符合煤油沸点范围。在另一个实施方案中,引导至少一定量的所述第一馏分或所述经加氢脱芳构化的产物与在异构化条件下在异构化(isom)中具有催化活性的材料接触,其相关的益处是,这样的工艺提供了符合喷气燃料冷流特性要求的产品。在另一个实施方案中,异构化条件涉及在250-350℃之间的温度、在30-150巴之间的压力以及在0.5-8之间的液时空速(lhsv),并且其中在异构化中具有催化活性的材料包含:活性金属,其选自铂、钯、镍、钴、钨和钼,优选一种或多种元素贵金属,例如铂或钯;酸性载体,优选为分子筛,更优选具有选自mor、fer、mre、mww、ael、ton和mtt的拓扑结构;和无定形耐热载体,其包含一种或多种选自氧化铝、二氧化硅和二氧化钛的氧化物,其相关的益处是,这些条件和材料是用于调节产物的冷流特性的具有成本效益和选择性的方法。在另一个实施方案中,加氢脱芳构化条件涉及在200-350℃之间的温度、在30-150巴之间的压力以及在0.5-8之间的液时空速(lhsv),并且其中所述在加氢脱芳构化中具有催化活性的材料包含:活性金属,其选自铂、钯、镍、钴、钨和钼,优选一种或多种元素贵金属,例如铂或钯;以及耐热载体,优选无定形二氧化硅-氧化铝、氧化铝、二氧化硅或二氧化钛,或其组合,其相关的益处是,这样的工艺条件适合于芳香烃的氢化。所述在加氢脱芳构化条件下在脱芳构化中具有催化活性的材料可以是在加氢裂化中有催化活性的材料或在有利于加氢脱芳构化的中等温度下操作的异构化中具有催化活性的材料。加氢脱芳构化条件优选涉及至少50%或80%的芳族化合物的转化率。本发明的另一方面涉及一种用于从作为可再生原料或含氧化合物原料的原料生产适合用作喷气燃料的烃的工艺设备,包括加氢处理工段、加氢裂化工段和加氢脱芳构化工段,所述工艺设备被配置用于:将原料引导至加氢处理工段,以提供经加氢处理的中间产物;将至少一定量的经加氢处理的中间产物引导至加氢裂化工段,以提供经加氢裂化的中间产物;将至少一定量的所述经加氢裂化的中间产物引导至加氢脱芳构化工段,以提供包含适合用作喷气燃料的烃馏分的经处理的产物,其相关的益处是,这种工艺设备能够生产具有符合喷气燃料规范astmd7566,a2.1的沸点和芳族化合物含量的喷气燃料。本发明中描述的方法接收可再生原料和/或含氧化合物原料,其包含一种或多种选自以下的含氧化合物:甘油三酸酯、脂肪酸、树脂酸、酮、醛、醇、酚和芳族羧酸,其中所述含氧化合物源自生物来源、气化工艺、热解工艺、费-托合成、基于甲醇的合成或其他合成工艺中的一种或多种,尤其是得自可再生来源的原材料,例如源自植物、藻类、动物、鱼、植物油精炼、生活垃圾、废弃食用油(usedcookingoil)、塑料废物、橡胶废物或工业有机废物,例如妥尔油或黑液。这些原料中的一些可能含有芳族化合物;特别是通过热解或其他工艺从例如木质素和木材得到的产品或来自例如煎炸油的废品。取决于来源,含氧化合物原料可以包含1wt/wt%至40wt/wt%。生物来源通常将包含约10wt/wt%,并且衍生产物包含1wt/wt%至20wt/wt%或甚至40wt/wt%。为了将可再生原料和/或含氧化合物原料转化为烃类运输燃料,引导原料与氢一起与在加氢处理(尤其是加氢脱氧)中具有催化活性的材料接触。尤其是在升高的温度下,催化加氢脱氧过程可能会发生副反应,例如从原料中的烯烃分子形成重质产物。为了缓和热量的释放,可以添加液态烃,例如,液态再循环流或外部稀释进料。如果该方法被设计用于化石原料和可再生原料的共处理,则方便的是将化石原料用作稀释剂,因为在化石原料的加工过程中释放的热量更少,因为释放更少的杂原子且使更少的烯烃饱和。除了使温度缓和之外,再循环或稀释剂还具有降低烯烃物质聚合(这将在产物中形成不希望的重质馏分)的可能性的作用。所得产物流将是经加氢处理的中间产物流,其包含烃,通常为正构石蜡,以及酸性气体如co、co2、h2o、h2s、nh3以及轻质烃,尤其是c3和甲烷。特别是在升高的温度下,催化加氢脱氧过程可能导致副反应形成芳族化合物。如果原料包含氮,则可能形成氨,其具有使催化活性材料失活的作用,因此需要这种升高的温度,进而形成芳族化合物,其量超过定义喷气燃料规格的astmd7566的限值。在加氢处理中具有催化活性的材料通常包含活性金属(一种或多种硫化的基础金属(例如镍、钴、钨或钼),但也可能包含元素贵金属(例如铂和/或钯))和耐热载体(例如氧化铝、二氧化硅或二氧化钛,或其组合)。典型的加氢处理涉及引导原料与催化活性材料接触,所述催化活性材料通常包含负载在载体上的一种或多种硫化的基础金属(例如镍、钴、钨或钼),但也可以是元素贵金属(例如铂和/或钯),所述载体包含一种或多种耐热氧化物,所述耐热氧化物通常是氧化铝,但也可以是二氧化硅或二氧化钛。载体通常是无定形的。催化活性材料可以包含其他组分,例如硼或磷。条件通常是在250-400℃之间的温度、在30-150巴之间的压力以及在0.1-2之间的液时空速(lhsv)。加氢处理通常是放热的,并且在存在大量氧气的情况下,该过程可能涉及中间冷却,例如通过用冷的氢、进料或产品骤冷(quenching)。原料可以优选地包含一定量的硫以确保金属的硫化,以保持金属的活性。如果气相包含少于10、50或100ppmv的硫,则可以将硫化物供体(例如二甲基二硫化物(dmds))添加到进料中。经加氢处理的中间产物将主要具有与原料含氧化合物的碳骨架相同的结构,或者如果原料包含甘油三酸酯,则经加氢处理的中间产物将主要具有与正构石蜡的碳骨架相同的结构,但长度可能短于脂肪酸。通常,经加氢处理的中间产物将主要包含具有不适合用作喷气燃料的沸点范围(250℃至320℃)和凝固点(0℃至30℃)的直链烷烃。如果不饱和脂肪酸聚合并形成芳族结构,则在加氢处理步骤中也可能形成一些重质组分和芳族化合物。为了在实践中将经加氢处理的中间产物用作燃料,必须调节凝固点。通过引导经加氢处理的中间产物与在异构化中具有催化活性的材料接触,可以通过将正构石蜡异构化为异构石蜡来调节凝固点。在异构化中具有催化活性的材料通常包含活性金属(元素贵金属,例如铂和/或钯,或者硫化的诸如镍、钴、钨和/或钼的基础金属)、酸性载体(通常为显示高形状选择性并具有诸如mor、fer、mre、mww、ael、ton和mtt的拓扑结构的分子筛)和典型的无定形耐热载体(例如氧化铝、二氧化硅或二氧化钛,或其组合)。催化活性材料可以包含其他组分,例如硼或磷。优选的异构化催化剂包含分子筛,例如eu-2、zsm-48、β沸石以及β沸石和沸石y的组合。通常,异构化涉及引导中间经加氢处理的原料与在异构化中具有催化活性的材料接触。条件通常是在250-350℃之间的温度、在30-150巴之间的压力以及在0.5-8之间的液时空速(lhsv)。异构化基本上是热中性的,并且在加氢裂化副反应中仅消耗氢,因此在异构化工段中仅添加中等量的氢。当在异构化中具有催化活性的材料上的活性金属是贵金属时,通常通过气/液分离来纯化经加氢处理的原料,以将潜在的催化剂毒物含量降低至低水平,例如硫、氮和碳氧化物的水平为1-10ppm摩尔以下。当活性金属是基础金属时,中间经加氢处理的原料优选地含有至少50ppmv的硫。为了将经加氢处理的中间产物流用作煤油馏分,必须调节沸点范围。通过引导经加氢处理的中间产物与在加氢裂化中具有催化活性的材料接触,通过将长的石蜡加氢裂化为较短的石蜡来调节沸点。在加氢裂化中具有催化活性的材料的性质与在异构化中具有催化活性的材料的性质相似,并且其通常包含活性金属(元素贵金属(例如铂和/或钯)或硫化的基础金属(例如镍、钴、钨和/或钼))、酸性载体(通常是显示高裂化活性并具有诸如mfi、bea和fau的拓扑结构的分子筛,但也可以使用无定形酸性氧化物,例如二氧化硅-氧化铝)和耐热载体(例如氧化铝、二氧化硅或二氧化钛,或其组合)。与在异构化中具有催化活性的材料的区别通常是酸性载体的性质,该酸性载体可以具有不同的结构(甚至是无定形二氧化硅-氧化铝),或者例如由于二氧化硅:氧化铝的比例而具有不同的酸度。催化活性材料可以包含其他组分,例如硼或磷。优选的加氢裂化催化剂包含分子筛,例如zsm-5、沸石y或β沸石。通常,加氢裂化涉及引导中间经加氢处理的原料与在加氢裂化中具有催化活性的材料接触。条件通常是在250-400℃之间的温度、在30-150巴之间的压力以及在0.5-4之间的液时空速(lhsv)。由于加氢裂化是放热的,因此该过程可能涉及中间冷却,例如通过用冷的氢、进料或产品骤冷。当在异构化中具有催化活性的材料上的活性金属是贵金属时,通常通过气/液分离来纯化经加氢处理的原料,以将潜在的催化剂毒物含量降低至低水平,例如硫、氮和碳氧化物的水平1-10ppm摩尔以下。当活性金属是基础金属时,中间经加氢处理的原料优选地含有至少50ppmv的硫。不饱和脂肪酸的加氢脱氧和加氢裂化也可能产生芳族化合物作为副反应,尤其是在温度和/或转化率较高的情况下。因此,通常期望在加氢裂化期间的低转化率,这阻碍了向煤油馏分的完全转化。增加转化率的一个考虑因素是使经加氢裂化的中间产物再循环,使其与在加氢裂化中具有催化活性的材料进行额外的接触,但即使如此,也可能产生大量的芳族化合物。因此,甚至对于包含少于1%芳族化合物的含氧化合物原料,也可能进一步有必要引导经加氢裂化的中间产物与在加氢脱芳构化中具有催化活性的材料接触,这令人惊讶,因为可再生原料不含或少量含有芳族化合物。在一些情况下,加氢脱芳构化可以在加氢异构化中具有催化活性的材料存在下令人满意地进行,但也可能需要单独的反应器或反应器床,其具有在加氢脱芳构化中具有催化活性的材料。在加氢脱芳构化中具有催化活性的材料通常包含活性金属(通常是元素贵金属(例如铂和/或钯),但也可以是硫化的基础金属(例如镍、钴、钨和/或钼))和耐热载体(例如无定形二氧化硅-氧化铝、氧化铝、二氧化硅或二氧化钛或其组合)。加氢脱芳构化是平衡控制的,高温有利于芳族化合物,优选贵金属作为活性金属,因为与基础金属相比,它们在较低的温度下具有活性。通常,加氢脱芳构化涉及引导中间产物与在加氢脱芳构化中具有催化活性的材料接触。由于芳族化合物和饱和分子之间的平衡在升高的温度下向芳族化合物移动,因此优选温度为中等。条件通常是在200-350℃之间的温度、在30-150巴之间的压力以及在0.5-8之间的液时空速(lhsv)。由于在加氢脱芳构化中具有催化活性的材料上的优选活性金属是贵金属,因此通常通过气/液分离来纯化经加氢裂化的中间产物,以将硫含量降低至1-10ppm以下。这种必须组合3或4种催化活性材料以将可再生原料转化为喷气燃料自然使工艺布局复杂化,并且必须仔细考虑材料的顺序。另外,再循环可以用于三个不同的目的;气体再循环以有效利用氢气、液体围绕着在加氢裂化中具有催化活性的材料再循环以使煤油馏分的产率最大化、液体围绕着在加氢脱氧中具有催化活性的材料再循环以限制由于放热的加氢脱氧反应引起的温度升高。在本公开的一个方面,通过在与加氢脱氧相同的阶段中通过加氢裂化来调节沸点,二者均在酸性条件下操作,并且使用包含硫化的基础金属的催化活性材料。由于催化剂通常包含在较低温度下运行的贵金属,因此加氢脱芳构化通常需要温和的(sweet)条件,因此利用加氢脱芳构化反应的平衡在低温下远离芳族化合物这一事实。因此,可以在加氢脱芳构化之前并且任选地还在根据沸点进行中间经加氢裂化的产物的分离之前进行气体分离,使得只有在煤油沸程内的中间经加氢裂化的产物与在加氢脱芳构化中具有催化活性的材料接触。可以与加氢裂化组合或与加氢脱芳构化组合进行异构化。在这两种情况下,可以将在异构化中具有催化活性的材料分别置于在加氢裂化或加氢脱芳构化中具有催化活性的材料的上游或下游。在另一方面,在与加氢脱芳构化相同的阶段中,通过加氢裂化调节沸点,两者均在温和的条件下操作,并使用包含元素贵金属的催化活性材料。因此,可以在加氢裂化之前并且任选地还在根据沸点进行中间经加氢处理的产物的分离之前进行气体分离,使得只有在喷气燃料沸程内及以上的中间经加氢处理的产物与在加氢裂化和加氢脱芳构化中具有催化活性的材料接触。异构化可以通过在加氢裂化中具有催化活性的材料的上游、在加氢脱芳构化中具有催化活性的材料的下游或在两者之间与包含元素贵金属的在异构化中具有催化活性的材料接触来进行。也可以通过在分离气体之前使中间经加氢处理的产物与包含硫化的基础金属的在异构化中具有催化活性的材料接触来进行异构化。在再循环的条件下对在加氢裂化中具有催化活性的材料进行操作,可以在中等温度下实现完全转化,从而保持高的煤油产率,并使过度裂化成石脑油和轻质油最小化。使用异构化催化剂改善喷气燃料的凝固点,允许增加喷气燃料的蒸馏终点,同时仍然满足对凝固点的要求。最后,由于第二阶段会使芳族化合物饱和,因此第一阶段不需要满足任何芳族化合物的要求,从而允许第一阶段处理较重质和/或更多的芳族、环烷(naphthenic)或不饱和原料以及已知在典型的加氢处理条件下会少量产生芳族化合物的诸如废弃食用油、热解产物或妥尔油沥青等原料,因为这些芳族化合物将在第二阶段被饱和。根据本公开的一个实施方案对应于以下方法,其中将包含含氧化合物和稀释烃且包含一定量硫的流引导到含有催化活性材料的加氢脱氧反应器中,该催化活性材料包含一种或多种基础金属和低酸度的耐热载体。这种材料在加氢脱氧和除去杂原子和双键的其他加氢处理反应中具有活性。再循环的烃起到散热剂的作用,吸收从加氢脱氧释放的反应热,从而在加氢脱氧反应器中保持中等的温度。该步骤提供了包含大量饱和直链烷烃以及一定量的水、硫化氢和氨的流。将经加氢处理的流引导至加氢裂化反应器,该反应器含有催化活性材料,该材料包含一种或多种基础金属和高酸度的耐热载体。这种材料在加氢裂化中具有活性,并且该步骤提供了一种流,其中较高沸点的烃被转化为较低沸点的烃。由于在加氢裂化中具有催化活性的材料包含基础金属,因此不必除去硫化氢,此外,氨的存在可能有助于调节加氢裂化活性。与贵金属相比,基础金属的较低成本也是有利的。将经加氢裂化的流引导至包括分离装置(例如汽提器或分馏器)的分离工段,并且至少抽出气体馏分、中间馏分和底部馏分。从分馏器出来的所有流中硫化氢和氨的含量都非常低。经加氢裂化的流的底部馏分太重而不能用作喷气燃料产物,并被再循环到加氢脱氧反应器中。中间馏分的沸点范围通常适合用作喷气燃料,但是芳族化合物的含量和凝固点可能不在规格范围内。因此,将中间馏分引导至异构化反应器,该异构化反应器含有在异构化中具有催化活性的材料和在加氢脱芳构化中具有催化活性的材料。这两种材料均基于贵金属催化剂(例如铂、钯或其组合)与酸性载体的组合。为了进行异构化,酸性载体优选是形状选择性的,例如沸石,以提供选择性的异构化,将直链烷烃重排成支链烷烃,具有最小化的较轻烃的产生。对于加氢脱芳构化,酸性载体也有助于该反应,此外,由于贵金属的活性高于基础金属的活性,因此反应将在较低的温度下进行。由于芳族化合物和非芳族化合物之间的平衡在低温下远离芳族化合物,因此贵金属提供了较低温度与平衡相匹配的好处。加氢脱芳构化甚至可以在在异构化中具有催化活性的材料上发生,该材料通常具有一定的加氢脱芳构化活性。一定量的加氢裂化反应可能在异构化反应器中发生,因此,可以优选经加氢裂化的流可能比喷气燃料规格略重质一些。因此,由于所有重质产品都被再循环并加氢裂化,该布局提供了原料向喷气燃料范围或更轻质产品的完全转化。而且,凝固点的调节是通过在贵金属催化剂上进行异构化而选择性地进行的,不受加氢裂化条件的影响,且最终,加氢脱芳构化可以在相同的反应器中,甚至可能在与异构化相同的催化活性材料中,在中等温度下有效地进行。如果希望只生产柴油而不生产任何喷气燃料,那么就不需要加氢裂化。在这种情况下,可能优选绕过加氢裂化反应器或在该反应器之前冷却产物,以使其不活泼。工艺设备可以被配置为允许在短时间内进行这样的配置,例如,在控制室中设置适当的设备并进行控制。附图图1示出了根据本公开的方法。图2示出了根据本公开的方法的简化图示。图3示出了根据现有技术的方法的简化图示。图1显示了用于由逐步(2a、2b和2c)添加到加氢处理工段(8)中的可再生原料(2)生产适于用作喷气燃料的烃(106)的工艺布局。将第一量的可再生原料(2c)与稀释剂(6)混合,并将其引导至加氢处理工段(8),在该处与在加氢处理中具有催化活性的材料(10a)接触。引导另外量的可再生原料(2b、2c)和一定量的富氢气体(12a)与在加氢处理条件下具有催化活性的材料的各个床(10b、10c、10d)接触。这提供了经加氢处理的中间产物(14)。将经加氢处理的中间产物(14)引导至加氢裂化工段(16),与包含基础金属的在加氢裂化条件下在加氢裂化中具有催化活性的材料(18a、18b)以及包含基础金属的在异构化中具有催化活性的材料(20)接触,以提供经加氢裂化的中间产物(22)。在气/液分离器(24)中,经加氢裂化的中间产物(22)被分离成气态馏分(26)和液态馏分(34)。将气态馏分(26)分流为可选的吹扫气体(28)和再循环气体(30),将该再循环气体(30)加压(32),并作为加氢处理工段(12a)的骤冷氢气供应源引导至反应床之间的一个或多个位置以及加氢裂化工段(12b、12c)。将液态的经加氢裂化的中间产物(34)引导至汽提器(36),汽提器(36)还接收汽提介质(38)和任选的汽提器塔顶再循环物(40)。将气态汽提器产物(42)从汽提器引导至气/液分离器(44),从该气/液分离器(44)中抽出废气(46)和轻质石脑油馏分(48)。抽出一定量的轻质石脑油作为产品(50),一定量(52)可以作为进料(102)引导至煤油稳定器(100),一定量作为塔顶再循环物(40)引导至汽提器(36)。将液态汽提器产物(54)引导至分馏器(56),将轻质塔顶馏出物流(58)从该分馏器(56)引导至塔顶容器(60),从该塔顶容器(60)抽出重质石脑油(62)。抽出一定量的重质石脑油(64)作为产品,将另外一部分(66)引导作为分馏器再循环物(66)。将底部馏分(68)分流为再循环流(72)和再沸流(74)。从侧塔(78)将经加氢裂化的中间喷气燃料产物(80)与富氢流(84c)合并,并作为进料(82)引导至加氢脱芳构化和加氢脱蜡工段(86),在此与在异构化中具有催化活性的材料(88)以及在加氢脱芳构化条件下在加氢脱芳构化中具有催化活性的材料(90a、90b)接触,接收另外的富氢流(84a、84b),提供经处理的产物(92),将其引导至产物气/液分离器(94),从该产物气/液分离器(94)中抽出第二气态馏分(96)并将其与再循环流(72)合并,并作为稀释剂中的补充氢(76)提供给加氢处理工段(8)。从产物分离器中取出中间喷气燃料产物(98),并将其引导至另一个分离装置(100),例如煤油稳定器,该另一个分离装置(100)还任选地接收一定量的轻质石脑油(102),从该另一个分离装置(100)中抽出液态产物(104),并将其分流为适于用作喷气燃料的烃馏分(106)和再沸液体(110)。将来自煤油稳定器(108)的气态塔顶馏出物与气态汽提器产物(42)合并,并引导至气/液分离器(44)。在另一实施方案(未示出)中,不将第二气态馏分(96)引导作为加氢处理工段的补充气,而是将其引导至加氢脱芳构化和加氢脱蜡工段(86),这可能需要额外的压缩机,但也增加了简便性。在这种情况下,然后将补充氢单独添加到加氢处理工段中。在另一个实施方案中,来自煤油稳定器(92)的气态塔顶馏出物可以在单独的塔顶回路中进行处理,这具有简便性和独立性的优点,但以用于冷却、分离和回流泵的额外设备的成本为代价。在另一个实施方案中,分离器、分馏和轻烃回收工段可以以本领域技术人员已知的多种方式构造。如果轻质材料(如lpg或丙烷)有价值,则可以通过使用海绵吸油系统(例如,使用分馏塔顶重质石脑油作为贫油并将富油返回至汽提器)来改善这些物质的回收率。图2是简化的图,示出了类似于图1的布局,为简单起见,省略了气态流的供应和分离的细节。将可再生原料(202)与稀释剂(226)组合,并作为加氢处理进料流(204)与一定量的富氢流(未显示)一起引导至加氢处理工段(hdo),在此处与在加氢处理条件下在加氢中具有催化活性的材料接触。这提供了经加氢处理的中间产物(206)。将经加氢处理的中间产物(206)引导至在加氢裂化条件下操作的加氢裂化工段(hdc),提供经加氢裂化的中间产物(212),该经加氢裂化的中间产物被引导至分馏工段(frac)(为了简化起见,将其显示为单一单元),将经加氢裂化的中间产物分离成轻质的塔顶馏出物流(220)、石脑油流(222)、经加氢处理的中间喷气燃料产物(224)和底部馏分(226)。底部馏分(226)作为再循环流被引导,如上所述,将该再循环流与可再生原料(202)合并在一起。经加氢处理的中间喷气燃料产物(224)作为进料被引导至后处理工段(pt),在该后处理工段(pt)处与在异构化(isom)中具有催化活性的材料以及在加氢脱芳构化条件下在加氢脱芳构化(hda)中具有催化活性的材料接触,提供经处理的喷气燃料产品(218)。图3以类似于图2的详细程度示出了现有技术的示例,为简单起见,省略了气态流的供应和分离的细节。将可再生原料(302)与再循环的稀释剂流(310)合并,作为加氢处理进料流(304)与一定量的富氢流(未显示)一起引导至加氢处理工段(hdo),在此处与在加氢处理条件下在加氢中具有催化活性的材料接触。这提供了经加氢处理的中间产物(306),在例如汽提器(sep)中从该经加氢处理的中间产物(306)中分离出气体,从而提供了经温和加氢处理的中间产物(308),将其分流为所述再循环稀释剂流(310)和异构化进料(312),该异构化进料(312)被引导至加氢异构化工段(isom),在该处与在异构化条件下在异构化中具有催化活性的材料接触,从而提供经脱蜡的中间产物(314)。将经脱蜡的中间产物(314)引导至加氢裂化工段(hdc),在该处与在加氢裂化条件下在加氢裂化中具有催化活性的材料接触,从而提供经加氢裂化的产物(316)。将经加氢裂化的产物(316)引导至分馏工段(frac)(为简单起见,将其显示为单一单元),将经加氢裂化的产物分离为轻质塔顶馏出物流(320)、石脑油流(322)、喷气燃料产物(324)和底部柴油馏分(326)。实施例基于两种相似的原料和针对最大喷气燃料产量而优化的工艺条件,对图2和图3所示工艺布局的性能进行了比较。表1显示了可再生原料的特性,该可再生原料是50%的废弃食用油和50%的动物脂肪的混合物。原料包含6%的芳族化合物和80%的沸点在500℃以上的物质;这主要是由于高沸点甘油三酸酯的存在。将原料a用图2和图3所示的方法处理,并将该处理的结果示于表2中。在加氢处理中,由于甘油三酸酯被转化为烷烃,沸点得到了明显的转化。另外,在加氢裂化反应器和异构化反应器中观察到一定量的转化。但是,由于循环量很高,因此每遍的实际转化率非常低。两个实施例的结果均显示出具有优异性能、低凝固点(-40℃)和低芳族化合物含量(<0.5wt/wt%)的喷气燃料的生产。根据本发明的实施例(图2)具有63wt/wt%的喷气燃料产率,而根据现有技术的实施例(图3)具有58w/wt%的喷气燃料产率。此外,在两种情况下均生产石脑油。在为生产喷气燃料而设计的方法中,5%的产率差异当然很有价值。图2的配置,即,将加氢脱氧和加氢裂化的产物分流为轻质馏分和重质馏分,然后将重质馏分再循环,从而将重质原料完全转化为喷气燃料产物,从而得到与图3的配置相比更高的喷气燃料产物产率。表1sg0.9209进料中的芳族化合物,wt/wt%6蒸馏:simdist,wt/wt%ibp3405%36510%39820%53330%58240%59750%60160%60270%60880%61090%61195%612fbp695表2当前第1页12
再多了解一些
本文用于企业家、创业者技术爱好者查询,结果仅供参考。