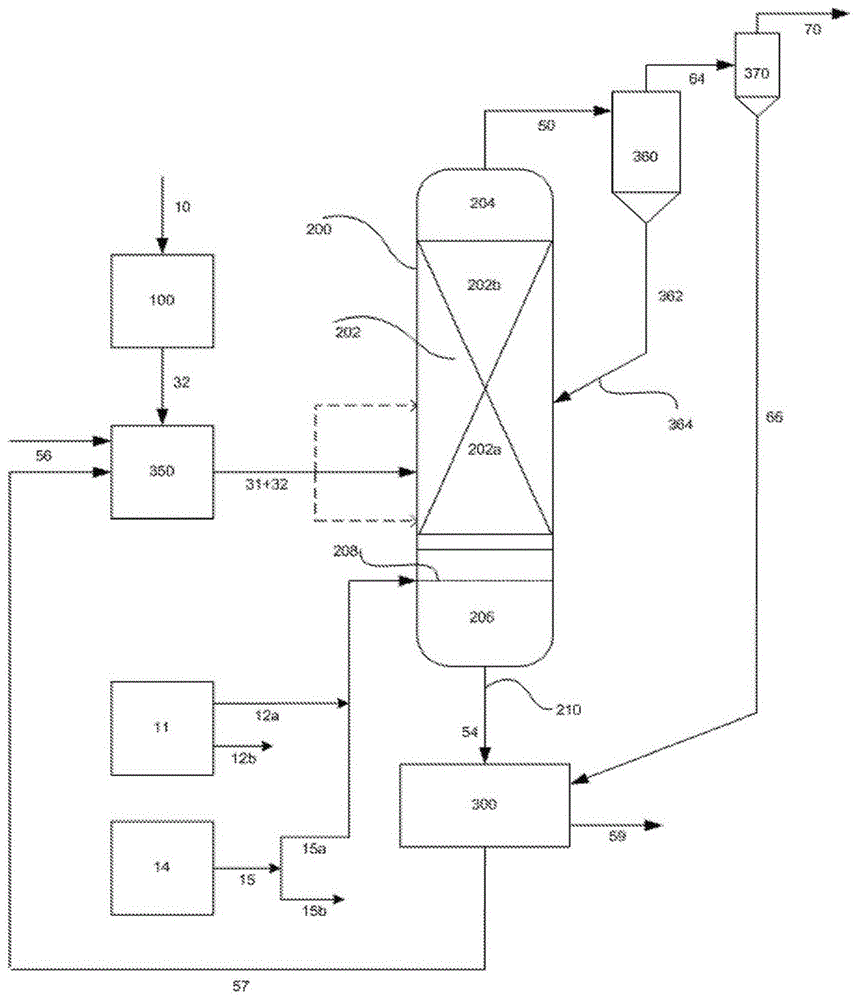
发明领域
本发明大体上提供了用于从碳质原料制备高价值产品的方法。
背景技术:
甲醇是重要的工业化学品,其具有包括以下的许多用途:(a)作为燃料或燃料添加剂,(b)作为用于生产如甲醛和乙酸的化学品的原材料化学品,和(c)作为工业溶剂(挡风玻璃清洗器液体、防冻液、水合物抑制剂)。
从甲醇合成气生产甲醇,该甲醇合成气主要包含氢、一氧化碳和二氧化碳,并且基本不含甲烷。通过以下催化反应进行甲醇合成:
副反应包括二甲醚和高级醇的形成。当下面定义的模数r处于1至2.1范围内的最佳值时,甲醇的生产最大化。
用于生产合成气的原料是天然气或例如煤或石油焦的固体烃类。在一些情况中,也可使用重质石油液体(例如沥青质)或者生物质。
常规地通过以下途径之一生成甲醇合成气:(1)天然气的蒸汽重整,(2)天然气的自热重整,和(3)固体烃类原料(例如煤或石油焦)与氧的非催化气化。
每一种合成气生成方法所产生的合成气的自然模数均不接近2至2.1的最佳值。天然气的蒸汽重整产生r=3-3.5的合成气。这会导致过量的氢,其必须作为副产品出售或者作为火焰加热器中的燃料燃烧。天然气与氧和蒸汽的自热重整产生r=1.7-1.8的合成气。由于自热重整技术和催化剂已有了长足发展,这种方法最接近于最佳可行选择。煤和石油焦的常规非催化气化产生r=0.4-0.6的合成气。高操作温度(2600-2900°f;约1427-1593℃)导致高耗氧量和小于1的低r值。必须通过使相当一部分合成气经历水煤气转化反应来满足氢的严重不足:
转化煤气以增加模数是不理想的,因为这会降低碳到甲醇的转化。因此,就氢转化或碳转化而言,合成气生产技术的天然模数是不理想的。
技术实现要素:
为克服天然气蒸汽重整中模数未达最佳的问题,已提出了组合重整途径作为最佳的替代方案。在该方法中,将一部分天然气进给到常规重整器中以产生r=3的富含氢的合成气。随后将重整器产品与其余天然气掺合以产生富含甲烷的气体,该气体随后被进给到自热重整器中。在这里,以受控速率添加蒸汽和氧,从而允许通过甲烷的部分氧化和重整得到具有最佳的r的最终产品。
由于煤或石油焦的非催化气化在出口气中几乎没有甲烷,因此不可能采用组合重整类型的概念。
本发明将催化气化与自热重整器(atr)单元组合以产生具有对甲醇合成进料气生产而言最佳的模数的甲醇合成进料气,并最终由该甲醇合成进料气生产例如甲醇和二甲醚的产品。与常规的吹氧气化技术相比,本发明减少了氧和副产品二氧化碳并且提高了每单位质量固体碳质原料的甲醇产率。对于其他基于合成气的生产过程来说也将产生类似的优点。
与煤或石油焦的非催化气化相比,煤或石油焦的催化气化在碱金属催化剂的存在下发生,这允许在低温(1300°f;约704℃)下工作。催化剂同时增强了三个反应的速率:蒸汽碳气化、水煤气转化和甲烷化。因此,通过放热的转化和甲烷化反应产生的热平衡了吸热的气化反应所需的热的大部分。需要相对少量的氧以进行固体碳和一些生成的合成气的部分氧化。催化气化能够在低温下将固体烃类原料中所含的碳有效地转化为富含甲烷的合成气。碳主要通过蒸汽-焦炭气化来转化,该反应生成碳和氢而不是燃烧产品。
催化气化的产品是富含甲烷的原料气,其具有至少1.5的h2:co摩尔比,并且在干燥、无co2的基础上,其甲烷含量为至少25mol%。催化气化产品气在冷却、脱水和酸性气体去除之后的高甲烷含量允许其在自热重整器中处理以产生具有最佳模数的甲烷合成进料气。这一概念类似于天然气的组合重整,即,煤的催化气化所产生的气体类似于进入组合重整过程的自热重整器的混合气体。
本发明涉及烃类原料经由中间的自热重整产生甲醇的催化气化。与将所有的氧都进给到气化器中从而以未达最优的模数转化碳的非催化气化不同,催化气化过程中的氧被分到在低温下运行以转化碳的催化气化器中和将富甲烷的气化器产品转化为甲醇合成进料气的自热重整器中。
本发明还将催化气化与低温分离单元结合,这也将以对于甲醇合成进料气生产而言最优的模数来产生甲醇合成进料气,并且最终从甲醇合成进料气产生例如甲醇和二甲醚的产品。催化气化与低温分离的结合也产生能直接用作替代天然气的甲烷产品。
碳质原料的加氢甲烷化的细节如下文所述。碳源的加氢甲烷化通常涉及四个反应:
蒸汽碳:c h2o→co h2(i)
水煤气转化:co h2o→h2 co2(ii)
co甲烷化:co 3h2→ch4 h2o(iii)
加氢气化:2h2 c→ch4(iv)
在加氢甲烷化反应中,前三个反应(l-lll)占优,从而得到以下总净反应:
2c 2h2o→ch4 co2(v)
总的加氢甲烷化反应基本上为热平衡的;然而,由于过程热损失和其他能量需要(如随原料进入反应器的水分蒸发所需),必须添加一些热以维持热平衡。
在加氢甲烷化过程的一个变体中,也可通过将氧进给到加氢甲烷化反应器中来至少部分原位生成所需的一氧化碳、氢和热能。参见,例如,先前并入的us2010/0076235a1、us2010/0287835a1和us2011/0062721a1,以及共同拥有的us2012/0046510a1、us2012/0060417a1、us2012/0102836a1、us2012/0102837a1、us2013/0046124a1、us2013/0042824a1、us2013/0172640a1和us2014/0094636a1。
其结果是还包含绝大多数的氢、一氧化碳和二氧化碳的“直接的”富含甲烷的粗产品气流,其可例如直接用作中等btu能源,或者可加工得到多种高价值产品流,如管道品质的替代天然气、高纯氢、甲醇、氨、高级烃、二氧化碳(用于强化采油和工业用途)和电能。
除了富含甲烷的粗产品气流之外,还产生了焦炭副产品流。固体焦炭副产品包含未反应的碳、夹带的加氢甲烷化催化剂和碳质原料的其他无机成分。根据原料组成和加氢甲烷化条件,副产品焦炭可包含20wt%或更多的碳。
周期性地或连续地从加氢甲烷化反应器去除这种副产品焦炭,并且通常将其送往催化剂回收和再循环操作,以改善整个过程的经济和商业可行性。在例如先前并入的如下文献中公开了与从加氢甲烷化反应器中提取的焦炭相关的催化剂成分的特质以及该催化剂成分的回收方法:us2007/0277437a1、us2009/0165383a1、us2009/0165382a1、us2009/0169449a1和us2009/0169448a1,以及共同拥有的us2011/0262323a1和us2012/0213680a1。可根据需要用补充催化剂来对催化剂再循环进行增补,如在先前并入的us2009/0165384a1中所公开的。
具体地,本发明提供了用于从非气体碳质材料和加氢甲烷化催化剂生成甲醇合成进料气的方法,该方法包括以下步骤:
a.从非气体碳质材料制备碳质原料;
b.将碳质原料、加氢甲烷化催化剂、高压过热蒸汽、氧引入加氢甲烷化反应器中;
c.将所述碳质原料在所述加氢甲烷化反应器中于约800°f(约427℃)到至多约1500°f(约816℃)的操作温度和至少约250psig(约1825kpa)的操作压力下反应以产生副产品焦炭和富含甲烷的粗产品气,所述富含甲烷的粗产品气包含甲烷、一氧化碳、氢、二氧化碳、硫化氢、蒸汽、热能和夹带细粒;
d.将所述副产品焦炭流从所述加氢甲烷化反应器中作为副产品焦炭流提取,其中所述副产品焦炭流包含碳含量和夹带的加氢甲烷化催化剂;
e.从所述富含甲烷的粗产品气去除绝大多数所述夹带细粒以形成清除细粒的富含甲烷的粗产品气;
f.冷却所述清除细粒的富含甲烷的粗产品气以生成蒸汽和冷却流;
g.从所述冷却流去除其他颗粒物以生成颗粒贫化的冷却气体;
h.通过以下生成甲醇合成进料气:
(i)通过以下步骤使用自热重整:
a.进一步冷却所述颗粒贫化的冷却气体以生成蒸汽,随后在氨回收系统中回收存在于冷却流出物中的氨以生成贫氨的流出物;
b.在酸性气体去除单元中从所述贫氨的流出物中去除绝大多数二氧化碳和绝大多数硫化氢以产生脱硫(sweetened)气体,其中所述脱硫气体包含氢、一氧化碳和甲烷,并且在干燥的、无co2的基础上,具有大于25%的甲烷;
c.将所述脱硫气体与高压过热蒸汽混合并加热混合物以产生产品流;
d.将所述产品流与氧混合并将混合物进给到自热重整器单元以形成流出物气体;和
e.冷却所述流出物气体以生成蒸汽和甲醇合成进料气,其中所述甲醇合成进料气包含氢、一氧化碳和二氧化碳;
或
(ii)通过以下步骤使用低温分离并联合产生替代天然气:
a.通过以下形成富含氢的粗产品气:
i.将一部分所述颗粒贫化的冷却气体引入水煤气转化反应器并使至少一部分所述一氧化碳进行蒸汽转化以生成流出物气体;和
ii.将剩余部分的所述颗粒贫化的冷却气体与通过蒸汽转化生成的流出物气体合并以形成富含氢的粗产品气;
条件是仅在e部分中所产生的甲醇合成进料气的模数小于1.75时执行a部分;
b.冷却所述颗粒贫化的冷却气体,或者如果存在的话冷却富含氢的粗产品气,以生成蒸汽和冷却的流出物;
c.在氨回收系统中回收存在于所述冷却的流出物中的氨以生成贫氨的流出物;
d.在酸性气体去除单元中从所述贫氨的流出物中去除绝大多数二氧化碳和绝大多数硫化氢以产生脱硫气体;和
e.将所述脱硫气体进给到低温分离器中并将所述气体分离为替代天然气流和甲醇合成进料气。
可从甲醇合成进料气生成甲醇。
该方法的蒸汽需求和功率需求通过内部能量整合来满足,因此该方法不需要净输入蒸汽或功率。
加氢甲烷化催化剂可包含碱金属,如钾。
该方法还可包括在催化剂回收单元中处理全部或部分副产品焦炭流,所述催化剂回收单元包括淬火槽和淬火介质,所述处理包括以下步骤:
a.将所述副产品焦炭流用所述淬火介质淬火以提取一部分夹带的催化剂,从而生成碳和催化剂贫化的焦炭以及解放的加氢甲烷化催化剂;
b.将所述碳和催化剂贫化的焦炭流从所述催化剂回收单元中作为碳和催化剂贫化的焦炭流提取;和
c.将所述解放的加氢甲烷化催化剂流从所述催化剂回收单元中作为回收的加氢甲烷化催化剂流提取。
该方法还可包括将回收的主细粒流、回收的辅助细粒流或二者的至少一部分进给到催化剂回收单元。此外,加氢甲烷化催化剂可包含至少一部分回收的加氢甲烷化催化剂流。
当通过自热重整过程生成甲醇合成进料气时,在步骤h,部分(i).c中产生的产品流的温度可为至少1000°f(538℃)。此外,在步骤h,部分(i).e中产生的甲醇合成进料气的模数可在1.75至2范围内。
最后,本发明还提供了用于从甲醇合成进料气或从由甲醇合成进料气生成的甲醇制备二甲醚的方法,其中使用自热重整或低温分离制备所述甲醇合成进料气并联合产生替代天然气。
附图说明
图1是加氢甲烷化反应器的示意图,该加氢甲烷化反应器包括含烃进料系统、催化剂应用系统、催化剂回收和再循环系统、用于将夹带固体再循环到反应器的主外部旋风分离器和用于从富含甲烷的粗气流去除细粒的辅助外部旋风分离器。
图2是在将细粒贫化的富含甲烷的粗气流转化为甲醇中所涉及的气体处理步骤的示意图。这些步骤包括将气体冷却至环境条件,同时回收作为过热高压蒸汽和饱和中压蒸汽的废热,去除酸性气体(主要是二氧化碳和硫化氢),氨回收,自热重整器和带有甲醇纯化的甲醇合成回路。
图3是本发明中允许通过低温液化联合生产甲醇和替代天然气或液化天然气的特殊情况的示意图。
图4是自热重整器和甲醇合成回路的细节的示意图。
具体实施方式
本发明涉及用于将非气体碳质材料以最佳模数r最终转化为合成气随后用于生产甲醇、二甲醚、液体燃料和其他合成气衍生化学品或产品的方法。在本说明书的上下文中,如果没有另外说明,则本文中提到的所有公开出版物、专利申请、专利和其他参考文件均通过引用以其整体明确并入本文用于所有目的,如同完全阐述一样。
除非另有定义,本文中所用的所有技术和科学术语均具有与本公开所属领域普通技术人员通常理解的相同含义。在冲突的情况下,以本说明书(包括定义)为准。
除非另有明确说明,商标以大写字母显示。
除非另有说明,所有百分数、分数、比率等均基于重量。
除非另有说明,以psi单位表示的压力为表压,以kpa单位表示的压力为绝对压力。
当量、浓度或者其它值或参数作为范围或一列上下限值给出时,这将被理解为具体地公开由任何上下限范围的任何配对所形成的所有范围,而不管是否单独公开了范围。当在本文中述及数值范围时,除非另有说明,否则该范围旨在包括其端点以及该范围内的所有整数和分数。并非旨在将本公开的范围限制于限定范围时所述的特定值。
当使用术语“约”来描述值或范围端点时,本公开应当理解为包括所提及的特定值或端点。
如本文所用的,术语“包括”、“包含”、“含有”、“包含有”、“具有”、“带有”或其任何其他变体旨在涵盖非排他性的包含。例如,包含一系列要素的过程、方法、物品或装置不一定仅限于那些要素,而是可包含未明确列出的或对于此类过程、方法、物品或装置来说固有的那些要素。
此外,除非明确说明相反,“或”和“和/或”表示包含性而非排他性的。例如,以下任何一项均满足条件a或b或者a和/或b:a为真(或存在)且b为伪(或不存在),a为伪(或不存在)且b为真(或存在),和a和b均为真(或存在)。
在本文中使用“一个”或“一种”来描述各个要素和组分时仅为方便起见,并且给出本公开的一般意义。该描述应被理解为包括一个/种或至少一个/种,并且单数也包括复数,除非其明显另有含义。
除非在本文中另有定义,否则本文所用的术语“绝大多数”表示大于约90%的所指材料,优选大于约95%的所指材料,更优选大于约97%的所指材料。如果没有规定,当提及分子(如甲烷、二氧化碳、一氧化碳和硫化氢)时,百分比以摩尔为基础,其他情况以重量为基础(如对于夹带细粒)。
除非在本文中另有定义,否则本文所用的术语“大部分”表示大于50%的所指材料。如果没有规定,当提及分子(如氢、甲烷、二氧化碳、一氧化碳和硫化氢)时,百分比以摩尔为基础,其他情况以重量为基础(如对于夹带细粒)。
术语“贫化(depleted)”是相对于初始存在减少的同义词。例如,从流去除绝大多数材料将产生该材料基本贫化的材料贫化的流。相反,术语“富含”是多于初始存在的同义词。
本文所用的术语“碳质”是烃类(hydrocarbon)的同义词。
本文所用的术语"碳质材料”是包含有机烃含量的材料。如本文定义,碳质材料可分为生物质和非生物质材料。
本文所用的术语"生物质”是指来源于近期(例如,在过去一百年内)活着的生物体的碳质材料,包括植物基生物质和动物基生物质。为清楚起见,生物质不包含化石基碳质材料,如煤。例如,参见先前并入的us2009/0217575a1、us2009/0229182a1和us2009/0217587a1。
本文所用的术语“植物基生物质”表示来源于绿色植物、作物、藻类和树的材料,例如但不限于甜高粱、甘蔗渣、甘蔗、竹子、杂交杨树、杂交柳树、合欢树、桉树、紫花苜蓿、三叶草、油棕、柳枝稷、苏丹草、谷子、麻风树和异芒草(例如,异源三倍体芒草奇岗)。生物质还包括来自农业种植、加工和/或降解的废物,例如玉米芯和谷壳、玉米秸秆、稻草、坚果壳、植物油、芥花油、菜籽油、生物柴油、树皮、木屑、锯末和庭院废物。
本文所用的“动物基生物质”是指在动物养殖和/或利用过程中产生的废物。例如,生物质包括但不限于来自家畜养殖和加工产生的废物,包括动物粪便、鸟粪、家禽垃圾、动物脂肪和城市固体废物(例如污水)。
如本文所用的术语“非生物质”是指不被本文所定义的术语“生物质”所涵盖的那些碳质材料。例如,非生物质包括但不限于无烟煤、烟煤、亚烟煤、褐煤、石油焦、沥青质、液态石油残余物或其混合物。例如,参见us2009/0166588a1、us2009/0165379a1、us2009/0165380a1、us2009/0165361a1、us2009/0217590a1和us2009/0217586a1。
“液态重烃材料”是指在环境条件下可流动或在高温条件下可成为可流动的粘性液体或半固体材料。这些材料通常为来自烃类材料(如原油)加工的残余物。例如,原油精炼的第一个步骤通常是蒸馏以将烃类的复杂混合物分离为不同挥发性的级分。典型的第一步蒸馏需要在大气压下加热以尽可能多地蒸发掉烃类含量而实际温度不超过约650°f(约343℃),这是因为较高的温度可能会导致热分解。在大气压下不会被蒸发掉的级分通常被称为“大气压石油渣油"。该级分可在真空下进一步蒸馏,从而使在至多约650°f(约343℃)的实际温度下可蒸发掉甚至更多的材料。剩余的不能蒸馏的液体被称为“真空石油渣油”。大气压石油渣油和真空石油渣油都被认为是可用于本发明目的的液体重质烃材料。
液态重质烃材料的非限制性示例包括真空渣油;大气压渣油;重质和还原石油原油;热解沥青(pitch)、石油沥青(asphalt)和天然沥青(bitumen)(天然的以及石油精炼过程产生的);焦油砂油;页岩油;催化裂化过程的底部沉积油;煤液化的底部沉积物;以及包含大量重或粘稠材料(如石油蜡级分)的其他碳氢化合物进料流。
如本文所用的术语“沥青烯”是室温下的芳族碳质固体,并且可以来源于例如原油和原油焦油砂的加工。沥青烯也可被认为是液体重质烃原料。
液体重质烃材料可固有地包含少量固体碳质材料,如石油焦和/或固体沥青烯,其通常分散在液体重质烃基质中,并且在用作本过程进料条件的高温条件下保持固体。
本文所用的术语“石油焦”和“石油焦油”包括:(i)在石油加工过程中获得的高沸点烃类级分(重质残余物-“渣油石油焦”)的固体热分解产品;和(ii)加工焦油砂(沥青砂或油砂-“焦油砂石油焦”)的固体热分解产品。这种碳化产品包括,例如,绿色石油焦、煅烧石油焦、针状石油焦和流化床石油焦。
渣油石油焦也可来源于原油,例如,通过用于提质高api度残余原油(例如液态石油渣油)的焦化过程,该石油焦含有灰分作为微量组分,基于焦的重量,其通常为约1.0wt%或更少,更通常为约0.5wt%或更少。通常,此类低灰分焦中的灰分主要包含金属如镍和钒。
焦油砂石油焦可以来源于油砂,例如,通过用于提质油砂的焦化过程。焦油砂石油焦包含灰分作为微量组分,基于焦油砂石油焦的总重,其通常在约2wt%至约12wt%的范围内,更通常在约4wt%至约12wt%的范围内。通常,此类高灰分焦中的灰分主要包含如二氧化硅和/或氧化铝的材料。
基于石油焦的总重,石油焦可包含至少约70wt%的碳,至少约80wt%的碳,或至少约90wt%的碳。通常,基于石油焦的总重,石油焦包含少于约20wt%的无机化合物。
本文所用的术语“煤”是指泥炭、褐煤、亚烟煤、烟煤、无烟煤或其混合物。在某些实施方式中,基于总煤重,煤的碳含量为少于约85wt%,或少于约80wt%,或少于约75wt%,或少于约70wt%,或少于约65wt%,或少于约60wt%,或少于约55wt%,或少于约50wt%。在其他实施方式中,基于总煤重,煤的碳含量为至多约85wt%,或至多约80wt%,或至多约75wt%。可用的煤的示例包括但不限于illinois#6、pittsburgh#8、beulah(nd)、utahblindcanyon和powderriverbasin(prb)煤。以干燥基础上的煤的总重计,无烟煤、烟煤、亚烟煤和褐煤可分别含有约10wt%、约5wt%至约7wt%、约4wt%至约8wt%和约9wt%至约11wt%的灰分。然而,任何具体煤源的灰分含量将取决于煤的等级和来源,如同本领域技术人员所熟悉的那样。参见,例如,“coaldata:areference",energyinformationadministration,officeofcoal,nuclear,electricandalternatefuels,u.s.departmentofenergy,doe/eia-0064(93),february1995。
由煤的燃烧产生的灰分通常包含飞灰和底灰,如同本领域技术人员所熟悉的那样。基于飞灰的总重,来自烟煤的飞灰可包含约20wt%到约60wt%的二氧化硅和约5wt%到约35wt%的氧化铝。基于飞灰的总重,来自亚烟煤的飞灰可包括约40%至60%的二氧化硅和约20%至30%的氧化铝。基于飞灰的总重,来自褐煤的飞灰可包含约15wt%到约45wt%的二氧化硅和约20wt%到约25wt%的氧化铝。参见,例如,meyers,etal."flyash.ahighwayconstructionmaterial,"federalhighwayadministration,reportno.fhwa-ip-76-16,washington,dc,1976.
基于底灰的总重,来自烟煤的底灰可包含约40至约60wt%的二氧化硅和约20至约30wt%的氧化铝。基于底灰的总重,来自亚烟煤的底灰可包含约40wt%到约50wt%的二氧化硅和约15wt%到约25wt%的氧化铝。基于底灰的总重,来自褐煤的底灰可包含约30wt%到约80wt%的二氧化硅和约10wt%到约20wt%的氧化铝。参见,例如,moulton,lylek."bottomashandboilerslag",proceedingsofthethirdinternationalashutilizationsymposium,u.s.bureauofmines,informationcircularno.8640,washington,dc,1973。
根据上述定义,取决于其来源,如甲烷之类的材料可以是生物质或非生物质。
"非气体"材料基本在环境条件下为液体、半固体、固体或混合物。例如,煤、石油焦、沥青烯和液体石油残余物是非气体材料,而甲烷和天然气是气体材料。
术语"单元”是指单元操作。当描述了存在多个“单元”时,除非另有说明,否则这些单元以并行方式操作。然而,根据上下文,单个“单元”可包含串联或并联的多个单元中的多于一个。例如,酸性气体去除单元可包含硫化氢去除单元,随后是串联的二氧化碳去除单元。作为另一个示例,污染物去除单元可包含用于第一污染物的第一去除单元,随后是串联的用于第二污染物的第二去除单元。又一个示例,压缩机也包含将流压缩至第一压力的第一压缩机,随后是串联的将流进一步压缩至第二(更高)压力的第二压缩机。
术语“一部分碳质原料”是指未反应的原料以及部分反应的原料的碳含量,以及可完全或部分来源于碳质原料的其他组分(如一氧化碳、氢和甲烷)。例如,“一部分碳质原料"包括可能存在于副产品焦炭和再循环细粒中的碳含量,该焦炭最终来源于原始的碳质原料。
在本发明上下文中,术语“过热蒸汽”是指在所使用的条件下不冷凝的蒸汽流,正如相关领域的普通技术人员通常理解的。
术语"蒸汽需求”是指必须通过气体进料流添加到本发明的各个过程的蒸汽量。例如,在加氢甲烷化反应器中,在加氢甲烷化反应中消耗蒸汽,并且必须将一些蒸汽添加到加氢甲烷化反应器中。蒸汽的理论消耗量是进料中每两摩尔的碳消耗两摩尔蒸汽,以产生一摩尔的甲烷和一摩尔的二氧化碳(参见等式(v))。在实际应用中,蒸汽消耗不是完全有效的,并且蒸汽与产品气体一起排出;因此,需要向加氢甲烷化反应器中添加大于理论量的蒸汽,该添加量就是“蒸汽需求”。例如,可以通过蒸汽流和氧气流添加蒸汽,二者通常在引入加氢甲烷化反应器之前合并(如图1所示和下文所述)。在下文中进一步详细讨论所添加的蒸汽量(和来源)。由碳质原料原位生成的蒸汽(例如,来自碳质原料的任何水分含量的蒸发,或者来自氢、甲烷和/或者存在于碳质原料中或由碳质原料生成的其他烃类的氧化反应)可有助于提供蒸汽;然而,应注意到在低于加氢甲烷化反应器内的操作温度(即加氢甲烷化反应温度)的温度下在加氢甲烷化反应器中原位生成或进给到加氢甲烷化反应器中的任何蒸汽将会影响加氢甲烷化反应的“热需求”。
术语“热需求”是指必须添加到加氢甲烷化反应器的热能的量,该热能原位产生(例如,通过供应氧的燃烧/氧化反应,如下文所讨论)以使步骤(c)的反应保持基本热平衡,如下文所讨论。
术语"功率需求"是指必须使用以操作本发明的过程的功率的量。
尽管在本公开的实践或检测中可使用类似或等同于本文所述那些的方法和材料,在本文中描述了合适的方法和材料。因此,本文的材料、方法和示例仅为说明性的,并且除非明确说明,否则并不旨在限制。
一般过程信息
在本发明的一个实施方式中,由非气体碳质材料(10)和加氢甲烷化催化剂(31)最终生成清除细粒的富含甲烷的产品气流(70)以及碳-和催化剂-贫化的焦炭流(59),如图1中所示。
参考图1,根据本发明的一个实施方式,在原料准备单元(100)中加工非气体碳质材料(10)以生成碳质原料(32),该碳质原料(32)被进给到催化剂应用单元(350),在这里施加加氢甲烷化催化剂(31)以生成催化的碳质原料(31 32)。施加方法可包括将催化剂溶液分散在固体进料颗粒上的机械混合器件和实现对于催化的碳质原料(31 32)优选的水分含量的热干燥器。
原料准备单元(100)包括煤或焦粉碎机以实现预先确定的最佳尺寸分布,这在很大程度上取决于碳质的机械和化学性质。在某些情况下,包括粒化和/或压块机以强化细粒,从而使所有固体原料材料的利用最大化。
加氢甲烷化催化剂流(31)通常将包含从副产品焦炭(54)和回收的辅助细粒(66)回收的回收加氢甲烷化催化剂流(57)和来自补充的催化剂流(56)的补充催化剂。
将催化的碳质原料(31 32)与蒸汽流(12a)和氧流(15a)一起进给到加氢甲烷化反应器(200)。
由蒸汽源如蒸汽分配系统(11)提供蒸汽流(12a)和(12b),该蒸汽源理想地利用过程热回收(例如,从热的粗产品气和其它过程来源回收热能),使得过程是蒸汽集成并且蒸汽充足的。
蒸汽流(12a)和氧流(15a)(来自已被分为氧流(15a)和(15b)的氧流(15))可以是单个进料流或多个进料流,所述单个进料流或多个进料流与热能和合成气的原位生成相结合地包含至少基本满足或至少满足加氢甲烷化反应器(200)中发生的加氢甲烷化反应的蒸汽和热量需求所需要的蒸汽、热能。
在加氢甲烷化反应器(200)中,(i)一部分碳质原料、蒸汽、氢和一氧化碳在加氢甲烷化催化剂存在下反应以生成富含甲烷的粗产品气(加氢甲烷化反应),和(ii)一部分碳质原料在蒸汽和氧存在下反应以生成热能并且通常生成一氧化碳、氢和二氧化碳。将生成的富含甲烷的粗产品气从加氢甲烷化反应器(200)中作为富含甲烷的粗产品气流(50)提取。提取的富含甲烷的粗产品气(50)通常至少包含甲烷、一氧化碳、二氧化碳、氢、硫化氢、蒸汽、夹带固体细粒和热能。
加氢甲烷化反应器(200)包括具有位于下部部分(202a)上方的上部部分(202b)的流化床(202)和位于流化床上方的分离区(204)。加氢甲烷化反应器(200)还通常包含位于流化床(202)下方的气体混合区(206),其具有通常通过栅板(208)或类似分隔物(例如喷淋管阵列)隔开的两个区段。将氧(15a)与高压过热蒸汽(12a)混合,并将混合物引入气体混合区(206)中,经由该气体混合区(206)进入流化床(202)的下部部分(202a)中,在其他位置处进入流化床(202)中,或者进入其组合中。理想地,将氧进给到流化床的下部部分。不受限于任何特定理论,加氢甲烷化反应在上部部分(202b)中占主导,与来自氧流(15a)的氧的氧化反应在下部部分(202a)中占主导。据信,在两个部分之间没有具体的限定边界,而是随着氧在下部部分(202a)中的消耗(以及热能和合成气的生成)而过渡。还据信,在存在于加氢甲烷化反应器(200)中的条件下,氧消耗迅速。
流化床(202)的下部部分(202a)中的至少一部分碳质原料将与来自氧流(15a)的氧反应以生成热能以及氢和一氧化碳(合成气)。这包括来自未反应(新鲜)原料、部分反应原料(如焦炭和再循环细粒)的固体碳以及可能由下部部分(202a)中的原料和再循环细粒生成或携带的气体(一氧化碳、氢、甲烷和高级烃)的反应。通常,根据燃烧/氧化和水煤气转化反应的程度,可能会产生一些水(蒸汽)以及其他副产品如二氧化碳。如上所述,在加氢甲烷化反应器(200)(主要在流化床(202)的上部部分(202b))中,碳质原料、蒸汽、氢和一氧化碳在加氢甲烷化催化剂存在下反应生成富含甲烷的粗产品,该粗产品最终作为富含甲烷的粗产品流(50)从加氢甲烷化反应器(200)中提取。
碳质原料在流化床(202)中的反应还产生副产品焦炭,该副产品焦炭包含未反应的碳以及来自碳质原料的非碳含量(包括加氢甲烷化催化剂)。为防止残余物在加氢甲烷化反应器(200)中积聚,通常通过焦炭提取管线(210)来(周期性地或连续地)提取副产品焦炭(54)的固体净化物(purge)。副产品焦炭(54)包含碳含量和夹带的加氢甲烷化催化剂。
在先前并入的us2012/0102836a1的一个实施方式中,将碳质原料(32)(或催化的碳质原料(31 32))进给到流化床(202)的下部部分(202a)中。因为将催化的碳质原料(31 32)引入流化床(202)的下部部分(202a)中,所以至少一个焦炭提取管线(210)通常位于如下的点处:该点使得在催化的碳质原料(31 32)的进料位置上方的一个或多个点处从流化床(202)提取副产品焦炭,通常来自流化床(202)的上部部分(202b)。
过大以至于不能在在流化床区段(202)中流化的颗粒,例如,大颗粒副产品焦炭和不可流化的聚集物,通常被收集在流化床(202)的下部部分(202a)以及气体混合区(206)中。此类颗粒通常包括碳含量(以及灰分和催化剂含量),并且可以通过焦炭提取管线(210)从加氢甲烷化反应器(200)周期性去除,以进行催化剂回收和进一步处理。
全部或部分副产品焦炭流(54)(通常为全部此类流)在催化剂回收单元(300)中处理以回收夹带的加氢甲烷化催化剂,以及任选地其他有附加值的副产品如钒和镍(取决于非气体碳质材料(10)的含量),以生成碳-和催化剂-贫化的焦炭流(59)和回收的加氢甲烷化催化剂流(57)。
可在锅炉中处理催化剂贫化的焦炭流(59)以生成蒸汽和功率。
在加氢甲烷化反应器(200)中,富含甲烷的粗产品气通常通过位于流化床区段(202)上方的分离区(204),随后从加氢甲烷化反应器(200)提取。分离区(204)可任选地包含,例如,一个或多个内部旋风分离器和/或其他夹带颗粒分离机构(未示出)。“提取的“(参见下文讨论)富含甲烷的粗产品气流(50)通常至少包含甲烷、一氧化碳、二氧化碳、氢、硫化氢、蒸汽、热能和夹带细粒.
通常通过旋风分离器组件(例如,一个或多个内部和/或外部旋风分离器)对富含甲烷的粗产品气流(50)进行初始处理以去除绝大多数夹带的细粒,如有必要,随后可进行可选的附加处理,例如文丘里洗涤器,如下文所述。在图1所示的实施方式中,旋风分离器组件包括外部主旋风分离器(360),随后是外部辅助旋风分离器(370),但其他设置也将是合适的。例如,旋风分离器组件可包括内部主旋风分离器,然后是外部辅助旋风分离器。
因此,“提取的”富含甲烷的粗产品气流(50)被认为是进行细粒分离之前的粗产品,无论在加氢甲烷化反应器(200)内部和/或外部是否发生了细粒分离。
如图1中详细描绘的,将富含甲烷的粗产品流(50)从加氢甲烷化反应器(200)通往外部主旋风分离器(360)以分离大部分夹带细粒颗粒。尽管为简单起见在图1中示出了作为单个外部旋风分离器的主旋风分离器(360),如上所述旋风分离器组件(360)可为内部和/或外部旋风分离器,并且可以为一系列多个内部和/或外部旋风分离器。
如图1所示,在主旋风分离器(360)中处理富含甲烷的粗产品气流(50)以生成细粒贫化的富含甲烷的粗产品气流(64)和回收的主细粒流(362)。
将回收的主细粒流(362)进给回到加氢甲烷化反应器(200)中,例如,经由细粒再循环管线(364)进给到流化床(202)的一个或多个部分。例如,如先前并入的us2012/0060417a1中所公开的,将回收的细粒经由细粒再循环管线(364)进给到流化床(202)的下部部分(202a)。
细粒贫化的富含甲烷的粗产品气流(64)通常至少包含甲烷、一氧化碳、二氧化碳、氢、硫化氢、蒸汽、氨和热能以及少量污染物,如剩余的残余夹带细粒,和可能存在于碳质原料中的其他蒸发和/或携带材料。在细粒贫化的富含甲烷的粗产品气流(64)中通常基本不存在(总含量通常小于约50ppm)(在环境条件下)可冷凝的碳氢化合物。
通常,如图1中所示,细粒贫化的富含甲烷的粗产品气流(64)将被进给到辅助旋风分离器(370)以去除绝大多数的任何剩余细粒,生成清除细粒的富含甲烷的粗产品气流(70)和回收的辅助细粒流(66)。回收的辅助细粒流(66)通常将被再循环到催化剂回收单元(300)。
在一个实施方式中,全部或部分回收的辅助细粒流(66)可与催化剂回收单元(300)中的提取的副产品焦炭(54)或其一些组合共同处理。
催化剂回收单元(300)通过常规固体浸出或洗涤技术回收水溶性催化剂。单元(300)可包括逆流混合沉降器或带洗涤区的压滤机或类似的固体洗涤/浸出和脱水装置的任何组合。具体地,催化剂回收单元(300)可包含淬火槽和淬火介质,处理包括以下步骤:将副产品焦炭流(54)用淬火介质淬火以提取一部分夹带的催化剂,从而生成碳-和催化剂-贫化的焦炭和解放的加氢甲烷化催化剂;将碳-和催化剂-贫化的焦炭流作为碳-和催化剂-贫化的焦炭流(59)从催化剂回收单元(300)中提取;和将解放的加氢甲烷化催化剂作为回收的加氢甲烷化催化剂流(57)从催化剂回收单元(300)提取。将回收的辅助细粒流(66)进给到催化剂回收单元(300)。
加氢甲烷化催化剂(31)通常将包含至少一部分回收的加氢甲烷化催化剂流(57)和来自补充的催化剂流(56)的补充催化剂。
可在一个或多个下游处理步骤中处理清除细粒的富含甲烷的粗产品气流(70),以回收热能,去污染,并转化为一种或多种增值产品,例如,替代天然气(管道质量)、氢、一氧化碳、合成气、氨、甲醇和其他合成气衍生产品、电力和蒸汽。
在下文中提供了其他细节和实施方式。
加氢甲烷化(hydromethanation)
在图1所示的根据本发明的一个实施方式中,将催化的碳质原料(31 32)、蒸汽流(12a)和氧流(15a)引入到加氢甲烷化反应器(200)中。
从加氢甲烷化反应器(200)去除焦炭副产品可在任何理想的位置或多个位置处进行,例如,在流化床(202)顶部,在流化床(202)的上部部分(202b)和/或下部部分(202a)内的任何位置,和/或在栅板(208)处或其紧邻下方。如上所示,催化的碳质原料(31 32)的引入位置将影响焦炭提取点的位置。
通常,在栅板(208)处或下方将有至少一个焦炭提取点以提取包含较大或聚集的颗粒的焦炭,如上面所讨论的。
加氢甲烷化反应器(200)通常在中高压力和温度下操作,需要将固体流(例如,催化的碳质原料(31 32)和如果存在的再循环细粒)引入反应器的反应室内同时保持所需的温度、压力和流的流速。本领域技术人员熟悉向具有高压和/或温度环境的反应室供应固体的进料口,包括星形进料器、螺旋进料器、旋转活塞和闭锁式料斗。应该理解的是,进料口可以包括交替使用的两个或多个压力平衡元件,例如闭锁式料斗。在一些情况中,可在高于反应器的操作压力的压力条件下准备碳质原料,因此,可将颗粒组合物直接通入反应器中而无需进一步加压。用于加压的气体可以是惰性气体(例如氮气)、反应气体(例如蒸汽)或更典型的二氧化碳流,该二氧化碳流可以例如从由酸性气体去除单元产生的二氧化碳流中再循环。
加氢甲烷化反应器(200)理想地在中等温度(与“常规的”基于氧化的气化过程相比)下操作,操作温度为从约800°f(约427℃),或从约1000°f(约538℃),或从约1100°f(约593℃),或从约1200°f(约649℃),至1500°f(约816℃),或至约1400°f(约760℃),或至约1375°f(约746℃);且压力为至少约250psig(约1825kpa,绝对压力),或至少约400psig(约2860kpa),或至少约450psig(约3204kpa)。通常,压力可在最高达机械可行性水平的范围内,例如,高达约1200psig(约8375kpa),高达约1000psig(约6996kpa),或高达约800psig(约5617kpa),或高达约700psig(约4928kpa),或高达约600psig(约4238kpa),或高达约500psig(约3549kpa)。在一个实施方式中,加氢甲烷化反应器(200)在如下压力(第一操作压力)下操作:至多约600psig(约4238kpa),或至多约550psig(约3894kpa)。在这种情况中,优选的压力范围可低于550psig(3894kpa)但将高于100psig(约708kpa)。
加氢甲烷化反应器(200)中的典型气流速度为约0.5ft/sec(约0.15m/sec),或约1ft/sec(约0.3m/sec),到约2.0ft/sec(约0.6m/sec),或约1.5ft/sec(约0.45m/sec)。
当将氧流(15a)进给到加氢甲烷化反应器(200)中时,一部分碳质原料(理想地为来自部分反应的原料、副产品焦炭和再循环细粒的碳)将在部分氧化/燃烧反应中消耗,生成热能以及通常一些量的一氧化碳和氢(和通常其他气体如二氧化碳和蒸汽)。供应到加氢甲烷化反应器(200)的氧量的变化提供了有利的过程控制,从而最终维持了合成气和热平衡。增加氧量将增加部分氧化/燃烧,因此增加了原位热生成。减少氧量将相反地减少原位热生成。
供应到加氢甲烷化反应器(200)的氧量必须足以燃烧/氧化足够的碳质原料以生成足够的热能和合成气从而满足稳态加氢甲烷化反应的热和合成气需求。
在一个实施方式中,提供到加氢甲烷化反应器(200)的分子氧的总量可在如下范围内:对于每重量单位(例如,磅或kg)的干燥的、无催化剂的碳质原料(32),提供从约0.10或约0.20或约0.25到约0.6或约0.5或约0.4或约0.35重量单位(例如,磅或kg)的o2。
加氢甲烷化反应器(200)内的加氢甲烷化和氧化/燃烧反应将同时发生。取决于加氢甲烷化反应器(200)的配置,这两个步骤通常在不同的区中占主导地位——流化床(202)的上部部分(202b)中的加氢甲烷化和流化床(202)的下部部分(202a)中的氧化/燃烧。
氧气流(15a)通常与蒸汽流(12a)混合,并且将混合物引入流化床(202)、气体混合区(206)、经由气体混合区(206)引入下部部分(202a)、在其它位置引入流化床(202)或其组合。在加氢甲烷化反应器(200)中的这些位置处引入这些流以避免在反应器中形成热斑,和避免(最小化)在加氢甲烷化反应器(200)内生成的理想气体产品的燃烧。进给具有高水分含量的催化的碳质原料(31 32),特别是进给到流化床(202)的下部部分(202a),也有助于热耗散和避免在反应器(200)中形成热斑,如在先前并入的us2012/0102837a1中所公开的。
可通过任何合适的方式将氧流(15a)进给到加氢甲烷化反应器(200)中,如将纯氧、氧-空气混合物、氧-蒸汽混合物、氧-二氧化碳混合物或氧-惰性气体混合物直接注入反应器中。参见,例如,us4315753和chiaramonteetal.,hydrocarbonprocessing,sept.1982,pp.255-257。如图1中所示,通过空气分离单元(14)供应氧流(15a)。
通常经由标准空气分离技术生成氧流(15a),并将其与蒸汽混合进给,以至少略高于加氢甲烷化反应器(200)中存在的压力引入。
如上所述,加氢甲烷化反应具有蒸汽需求、热需求和合成气需求。这些条件结合起来是确定加氢甲烷化反应以及过程的其余部分的操作条件的重要因素。
例如,加氢甲烷化反应需要蒸汽与(原料中的)碳的理论摩尔比为至少约1。然而,摩尔比通常大于约1,或为从约1.5(或更高),到约6(或更低),或到约5(或更低),或到约4(或更低),或到约3(或更低),或到约2(或更低)。催化的碳质原料(31 32)的水分含量、从加氢甲烷化反应器(200)中的碳质原料生成的水分、以及蒸汽流(12a)、氧流(15a)和再循环细粒流中所含的蒸汽全都为加氢甲烷化反应贡献了蒸汽。蒸汽流(12a)、氧流(15a)和氧化气流(52)中的蒸汽应足以至少基本满足(或至少满足)加氢甲烷化反应的"蒸汽需求"。供应到反应器的蒸汽的最佳量取决于许多因素,例如,原料的元素组成(c、h、n、0、s)、原料的无机物或灰分含量、理想的碳转化率、进料的水分含量、蒸汽与干进料的比率、反应容器的内部温度和压力和理想的合成气组成。
同样如上所述,加氢甲烷化反应是主要热平衡的,但是由于过程热损失和其他能量需求(例如,原料上的水分蒸发),必须(在加氢甲烷化反应器(200)中)原位生成一些热以维持热平衡(热需求)。在从氧流(15a)引入到加氢甲烷化反应器(200)中的氧的存在下的碳的部分燃烧/氧化应当足以至少基本满足(或至少满足)加氢甲烷化反应的热和合成气需求。
在加氢甲烷化反应器(200)中用于对催化的碳质原料(31 32)加压和与其反应的气体包括蒸汽流(12a)、氧流(15a)和二氧化碳输送气体,它们可根据本领域技术人员已知的方法供应到加氢甲烷化反应器(200)。因此,蒸汽流(12a)和氧流(15a)必须在允许它们进入加氢甲烷化反应器(200)的较高压力下提供。
蒸汽流(12a)的温度可低至进料压力下的饱和点,但理想的是在高于该温度的温度下进料,以避免发生任何冷凝的可能性。过热蒸汽流(12a)的典型进料温度是约500°f(约260℃)或约600°f(约316℃)或约700°f(约371℃)至950°f(约510℃)或至约900°f(约482℃)。蒸汽流(12a)的典型进料压力是约25psi(约172kpa)或高于加氢甲烷化反应器(200)内的压力。
蒸汽流(12a)的实际温度和压力将最终取决于从过程回收的热的水平以及加氢甲烷化反应器(200)内的操作压力,如下文所讨论的。在任何情况下,在过程的稳态操作中,理想的是不要在蒸汽流(12a)的过热中使用燃料燃烧型过热器。
当将蒸汽流(12a)和氧流(15a)组合以进给到流化床(202)的下部部分(202a)时,组合流的温度将通过蒸汽流(12a)的温度来控制,并且将通常在以下范围内:从约400°f(约204℃),或从约450°f(约232℃),到约650°f(约343℃),或到约600°f(约316℃)。
可例如通过控制供应到加氢甲烷化反应器(200)的蒸汽流(12a)的量和温度来控制反应器(200)中的温度。
在稳态操作中,用于加氢甲烷化反应器(200)的蒸汽理想地仅由其它过程操作通过过程热捕获生成(如在废热锅炉中生成,通常称为“过程蒸汽”或“过程生成的蒸汽”,并且在图1中称为蒸汽分配系统(11)),特别是由在热交换器单元中冷却粗产品气生成。可生成额外的蒸汽以用于整个过程的其他部分,如例如在先前并入的us2010/0287835a1和us2012/0046510a1中公开的,并且如下面讨论的图2和图3所示。
本文所描述的整个过程理想地是蒸汽正性的,使得可以通过热交换和在不同阶段的过程热回收来满足加氢甲烷化反应器(200)的蒸汽需求(压力和量),从而允许产生可用于功率生成和其他目的的多余蒸汽。理想地,过程生成的蒸汽占加氢甲烷化反应蒸汽需求量的100wt%或更大。
加氢甲烷化反应的结果是从加氢甲烷化反应器(200)中作为富含甲烷的粗产品流(50)提取的富含甲烷的粗产品,其通常包括ch4、co2、h2、co、h2s、未反应的蒸汽、热能和任选的其他污染物(如夹带细粒、nh3、cos和hcn,取决于用于加氢甲烷化的碳质材料的特质)。
可用于这些过程的非气体碳质材料(10)包括,例如,多种生物质和非生物质材料。碳质原料(32)来源于一种或多种非气体碳质材料(10),其可在原料准备单元(100)处理,如下文所讨论。
加氢甲烷化催化剂(31)可包括一种或多种催化剂物种,如碱金属或碱金属化合物。合适的碱金属是锂、钠、钾、铷、铯及其混合物。特别有用的是钾源。合适的碱金属化合物包括碱金属碳酸盐、碳酸氢盐、甲酸盐、草酸盐、胺化物、氢氧化物、醋酸盐或类似化合物。例如,催化剂可包含碳酸钠、碳酸钾、碳酸铷、碳酸锂、碳酸铯、氢氧化钠、氢氧化钾、氢氧化铷或氢氧化铯中的一种或多种,尤其是碳酸钾和/或氢氧化钾。
碳质原料(32)和加氢甲烷化催化剂(31)通常在紧密混合之后提供给加氢甲烷化反应器(200)(即,提供催化的碳质原料(31 32)),但是它们也可以单独进给。
离开加氢甲烷化反应器(200)的反应室的热气体流出物可通过作为分离区的并入加氢甲烷化反应器(200)的和/或加氢甲烷化反应器(200)外部的细粒去除单元(例如旋风分离器组件(360))。过重以至于不能被离开加氢甲烷化反应器(200)的气体夹带的颗粒(即细粒)被返回到加氢甲烷化反应器(200),例如,返回到反应室(例如,流化床(202))。
剩余的夹带细粒可通过如下方式基本去除:通过任何合适的装置(如内部和/或外部旋风分离器或机械过滤器),任选地随后通过洗涤器。如上文所讨论的,至少一部分这些细粒可经由再循环管线(364)返回到流化床(202)。任何剩余的回收细粒可进行处理以回收碱金属催化剂,和/或在某个阶段与碳质原料(32)结合,和/或直接再循环回到原料准备,如先前并入的us2009/0217589a1所述。
去除“绝大多数”细粒表示从所得气流中去除一定量的细粒,以使得下游处理不受不利影响;因此,应去除至少绝大多数细粒。一些少量的超细材料可能会残留在所得气流中,其程度不会使下游处理受到明显的不利影响。通常,去除了粒径大于约20μm或大于约10μm或大于约5μm的细粒的至少约90wt%或至少约95wt%或至少约98wt%。
可通过任何合适的装置(例如内部和/或外部旋风分离器(例如外部辅助旋风分离器(370)),任选地随后通过洗涤器从细粒贫化的富含甲烷的粗产品气流(64)中去除额外的残余夹带细粒。所得的清除细粒的富含甲烷的粗产品流(70)可进一步处理以根据需要进行热回收和/或纯化/转化,从而实现理想的产品,如先前并入的公开中所公开的。进一步的细节参考那些公开内容。
催化的碳质原料准备(100)
(a)碳质材料处理
碳质材料,如生物质和非生物质,可根据本领域已知的任何方法(如冲击粉碎以及干法或湿法研磨)经由单独地或共同地粉碎和/或研磨来准备以得到一种或多种碳质颗粒。取决于用于粉碎和/或研磨碳质材料源的方法,所得的碳质颗粒可分尺寸(即,根据尺寸分离)以提供用于催化剂加载过程的处理原料,从而形成催化的碳质原料。
本领域技术人员已知的任何方法可用于将颗粒分尺寸。例如,可通过筛分颗粒或将颗粒通过筛网或一系列筛网来进行分尺寸。筛分设备可包括格栅、条筛和丝网筛网。筛分可以是静态的或者包含摇动或震动筛网的机构。可替代地,可使用分级来分离开碳质颗粒。分级设备可包括矿石分选机、气体旋风分离器、水力旋流器、耙式分级机、旋转滚筒或流化分级机。碳质材料还可分尺寸或分类之后再进行研磨和/或粉碎。
碳质颗粒可作为平均粒径为约25微米或约45微米到至多约2500微米或至多约500微米的细粒颗粒供应。本领域技术人员可容易地确定用于碳质颗粒的合适粒径。例如,当使用流化床催化气化器时,此类碳质颗粒的平均粒径可使得能够以流化床催化气化器中所用的气体速度使碳质材料开始流化。
此外,某些碳质材料,例如玉米秸秆和柳枝稷,以及工业废物,例如锯末,可能不适于粉碎或研磨操作,或者可能不适合在催化气化器中使用,例如由于超细粒径。这些材料可以形成适合用于粉碎或直接用于例如流化床催化气化器中的尺寸的团粒或块。通常,可以通过压实一种或多种碳质材料来制备团粒,例如,参见先前并入的us2009/0218424a1。在其他示例中,可将生物质材料和煤形成为块,如us4249471、us4152119和us4225457中所述。在以下讨论中,此类团粒或块可与前面的碳质颗粒互换使用。
取决于碳质材料源的品质,其他原料处理步骤可能是必要的。生物质可能包含高水分含量,如绿色植物和草,并且可能需要在粉碎之前进行干燥。城市垃圾和污水也可能含有高水分含量,其可通过使用压机或辊磨机降低水分含量(例如us4436028)。类似地,非生物质如高水分的煤可能需要在粉碎之前进行干燥。一些结块的煤可能需要部分氧化以简化催化气化器操作。缺乏离子交换位点的非生物质原料如无烟煤或石油焦可进行预处理以产生额外的离子交换位点,从而有利于催化剂加载和/或缔合。此类预处理可通过本领域已知的产生离子交换可能位点和/或增强原料孔隙率的任何方法实施(参见,例如,先前并入的us4468231和gb1599932)。氧化性预处理可使用本领域已知的任何氧化剂进行。
碳质颗粒中碳质材料的比率可根据技术考虑、加工经济性、可用性以及非生物质和生物质来源的接近程度来选择。碳质材料来源的可用性和接近程度可影响进料的价格,从而影响催化气化过程的总生产成本。例如,基于湿重或干重,生物质和非生物质材料可以如下比率掺合:约5:95,约10:90,约15:85,约20:80,约25:75,约30:70,约35:65,约40:60,约45:55,约50:50,约55:45,约60:40,约65:35,约70:20,约75:25,约80:20,约85:15,约90:10,或约95:5,取决于处理条件。
很明显,碳质材料来源以及碳质颗粒的单个组分(例如,生物质颗粒和非生物质颗粒)的比率可用于控制碳质颗粒的其他材料特性。非生物质材料(如煤)和某些生物质材料(如稻壳)通常包含大量无机物,包括钙、氧化铝和二氧化硅,它们在催化气化器中形成无机氧化物(即,灰分)。在约500℃至约600℃的温度,钾和其他碱金属可与灰分中的氧化铝和二氧化硅反应形成不溶性碱金属铝硅酸盐。在这种形式中,碱金属基本上不溶于水并且作为催化剂无活性。为了防止残余物在催化气化器中积聚,可以常规地提取包含灰分、未反应碳质材料和各种碱金属化合物(水溶性和非水溶性)的焦炭的固体净化物。
在制备碳质颗粒中,各种碳质材料的灰分含量可选择为,例如,约20wt%或更低,或约15wt%或更低,或约10wt%或更低,或约5wt%或更低,这取决于例如各种碳质材料的比率和/或各种碳质材料的起始灰分。在其他实施方式中,基于碳质颗粒的重量,所得的碳质颗粒可包含如下范围内的灰分含量:约5wt%或约10wt%到约20wt%或到约15wt%。在其他实施方式中,基于灰分的重量,碳质颗粒的灰分含量可包含少于约20wt%,或少于约15wt%,或少于约10wt%,或少于约8wt%,或少于约6wt%的氧化铝。在某些实施方式中,基于处理原料的重量,碳质颗粒可包含小于约20wt%的灰分,其中基于灰分的重量,碳质颗粒的灰分含量包含少于约20wt%的氧化铝或少于约15wt%的氧化铝。
碳质颗粒中的这种较低的氧化铝值最终允许减少过程的催化气化部分中碱催化剂的损失。如上所述,氧化铝可与碱金属源反应得到不溶性的焦炭,其包括例如碱金属铝酸盐或铝硅酸盐。此类不溶性焦炭可导致催化剂回收减少(即,催化剂损失增加),因此在整个气化过程中需要额外的补充催化剂成本。
另外地,所得的碳质颗粒可具有显著更高%的碳,因此每单位重量的碳质颗粒具有更高的btu/lb值和甲烷产物。在某些实施方式中,基于非生物质和生物质的合计重量,所得的碳质颗粒的碳含量可在约75wt%或约80wt%或约85wt%或约90wt%到至多约95wt%范围内。
在一个示例中,对非生物质和/或生物质进行湿法研磨和分尺寸(例如,得到约25至约2500μm的粒径分布),随后抽干其游离水(即,脱水)为湿滤饼稠度(wetcakeconsistency)。用于湿法研磨、分尺寸和脱水的合适方法的示例是本领域技术人员已知的;例如,参见先前并入的us2009/0048476a1。根据本公开的一个实施方式的湿法研磨形成的非生物质和/或生物质颗粒的滤饼的水分含量可在约40%至约60%,或约40%至约55%,或50%以下的范围内。本领域技术人员将会意识到脱水的湿法研磨碳质材料的水分含量取决于碳质材料的颗粒类型、粒径分布和所用的特定脱水设备。此类滤饼可如本文所述地进行热处理以产生一种或多种水分减少的碳质颗粒,将其通往原料准备单元(100)。
一种或多种碳质颗粒中的每一种可具有独特的组成,如上文所述。例如,可使用两种碳质颗粒,其中第一种碳质颗粒包含一种或多种生物质材料,第二种碳质颗粒包含一种或多种非生物质材料。可替代地,采用包含一种或多种碳质材料的单一的碳质颗粒。
(b)催化剂加载
可对一种或多种碳质颗粒进行进一步处理以缔合至少一种通常包含至少一种碱金属来源的气化催化剂,以生成催化的碳质原料(31 32)。
提供用于催化剂加载的碳质颗粒可经处理以形成催化的碳质原料(31 32),并将后者送往加氢甲烷化反应器(200),或可分为一个或多个处理流,其中至少一个处理流与气化催化剂缔合以形成至少一个催化剂处理的原料流。其余的处理流可例如进行处理以缔合第二组分。另外地,催化剂处理的原料流可进行第二次处理以缔合第二组分。第二组分可为,例如,第二种气化催化剂、助催化剂或其他添加剂。
在一个示例中,可将主气化催化剂提供到单一的碳质颗粒(例如,钾和/或钠源),随后进行单独处理以向相同的单一碳质颗粒提供一种或多种助催化剂和添加剂(例如,钙源),从而得到催化的碳质原料(31 32)。例如,参见先前并入的us2009/0217590a1和us2009/0217586a1。气化催化剂和第二种组分也可作为混合物在单一处理中提供到单一碳质颗粒以得到催化的碳质原料(31 32)。
当一种或多种碳质颗粒提供用于催化剂加载时,则至少一个碳质颗粒与气化催化剂缔合以形成至少一个催化剂处理的原料流。此外,任何碳质颗粒可被分成一个或多个处理流,如上所述,以与第二或更多组分缔合。所得的流可以任何组合掺合以提供催化的碳质原料(31 32),条件是利用至少一个催化剂处理的原料流来形成催化的原料流。
在一个实施方式中,将至少一个碳质颗粒与气化催化剂和任选的第二组分缔合。在另一实施方式中,将每个碳质颗粒与气化催化剂和任选的第二组分缔合。
可使用本领域技术人员已知的任何方法将一种或多种气化催化剂与任何碳质颗粒和/或处理流缔合。这些方法包括但不限于,与固体催化剂源混合并将催化剂浸渍到处理的碳质材料上。本领域技术人员已知的几种浸渍方法可用于加入气化催化剂。这些方法包括但不限于:初始湿浸渍、蒸发浸渍、真空浸渍、浸泡浸渍、离子交换以及这些方法的组合。
在一个实施方式中,可通过在加载罐中用催化剂溶液(例如,水溶液)浆化来将碱金属气化催化剂浸渍到一个或多个碳质颗粒和/或处理流中。当用催化剂和/或助催化剂的溶液浆化时,可对所得浆液进行脱水以提供催化剂处理的原料流,同样典型地,作为湿滤饼。催化剂溶液可由本过程中的任何催化剂源制备,包括新鲜或补充的催化剂和再循环催化剂或催化剂溶液。使浆液脱水以提供催化剂处理的原料流的湿滤饼的方法包括过滤(重力或真空)、离心和流体压制。
如先前并入的us2009/0048476a1中所述,一种适合用于将煤颗粒和/或包含煤的处理流与气化催化剂组合以提供催化剂处理的原料流的特定方法是通过离子交换。通过离子交换机制进行的催化剂加载可根据专门针对煤开发的吸附等温线最大化,如所并入的参考文献中所述的。此类加载提供了作为湿滤饼的催化剂处理的原料流。可以控制保留在离子交换颗粒湿滤饼上(包括孔内)的额外催化剂,以便以受控的方式获得总催化剂目标值。加载催化剂并脱水的湿滤饼可含有例如约50wt%的水分。可通过控制溶液中催化剂组分的浓度以及接触时间、温度和方法来控制加载的催化剂总量,这可由相关领域的普通技术人员基于起始煤的特性容易地确定。
在另一示例中,碳质颗粒和/或处理流之一可用气化催化剂处理,第二处理流可用第二组分处理(参见先前并入的us2007/0000177a1)。
由上述方法得到的碳质颗粒、处理流和/或催化剂处理的原料流可以以任何组合掺合以提供催化的碳质原料,条件是使用至少一个催化剂处理的原料流来形成催化的碳质原料(31 32)。最终,催化的碳质原料(31 32)被通入加氢甲烷化反应器(200)中。
通常,每个原料准备单元(100)包括至少一个加载罐以使一个或多个碳质颗粒和/或处理流与包含至少一种气化催化剂的溶液相接触,从而形成一个或多个催化剂处理的原料流。可替代地,催化组分可作为固体颗粒掺入一个或多个碳质颗粒和/或处理流中以形成一个或多个催化剂处理的原料流。
通常,气化催化剂在催化的碳质原料中的存在量足以在颗粒组合物中提供在如下范围内的碱金属原子与碳原子之比:从约0.01,或从约0.02,或从约0.03,或从约0.04,至约0.10,或至约0.08,或至约0.07,或至约0.06。
对于一些原料,也可在催化的碳质原料中提供碱金属组分以实现如下的碱金属含量:基于质量,该碱金属含量比催化的碳质原料中的碳质材料的合计灰分含量高约3到约10倍。
合适的碱金属为锂、钠、钾、铷、铯及其混合物。特别有用的是钾源。合适的碱金属化合物包括碱金属碳酸盐、碳酸氢盐、甲酸盐、草酸盐、胺化物、氢氧化物、乙酸盐或类似化合物。例如,催化剂可包含碳酸钠、碳酸钾、碳酸铷、碳酸锂、碳酸铯、氢氧化钠、氢氧化钾、氢氧化铷或氢氧化铯中的一种或多种,尤其是碳酸钾和/或氢氧化钾。
可以使用任选的助催化剂或其他催化剂添加剂,例如在先前并入的参考文献中公开的那些。
组合形成催化的碳质原料(31 32)的一个或多个催化剂处理的原料流通常包含大于约50%、大于约70%或大于约85%或大于约90%的与催化的碳质原料(31 32)缔合的加载催化剂总量。可根据本领域技术人员已知的方法来确定与各个催化剂处理的原料流缔合的总加载催化剂的百分比。
如前所述,分离的碳质颗粒、催化剂处理的原料流和处理流可适当地掺合以控制例如催化的碳质原料(31 32)的总催化剂加载或其他品质。组合的各个流的合适比率将取决于包含每一个的碳质材料的质量以及所催化的碳质原料(31 32)的理想性质。例如,如前所述,生物质颗粒流和催化的非生物质颗粒流可按此比率组合以产生具有预定灰分含量的催化的碳质原料(31 32)。
任何前述催化剂处理的原料流、处理流和处理的原料流,如一个或多个干颗粒和/或一个或多个湿滤饼,可通过本领域技术人员已知的任何方法组合,包括但不限于捏合以及垂直或水平混合器,例如单螺杆或双螺杆、螺带式或鼓式混合器。所得的催化的碳质原料(31 32)可存储以供将来使用,或转移至一个或多个进料操作以引入催化气化器。催化的碳质原料可根据本领域技术人员已知的任何方法(例如,螺旋输送机或气力输送)输送至存储或进料操作。
此外,可以从催化的碳质原料(31 32)中去除多余的水分。例如,催化的碳质原料(31 32)可用流化床浆液干燥器干燥(即用过热蒸汽处理以蒸发液体),或在真空或惰性气流下热蒸发或去除溶液,以提供具有例如如下残余水分含量的催化的碳质原料:约10wt%或更少,或约8wt%或更少,或约6wt%或更少,或约5wt%或更少,或约4wt%或更少。
经由自热重整器生产甲醇
气体处理-热交换器系统(400)和高压蒸汽流(40)
在通过高效旋风分离器系统(360 370)处理之后,离开加氢甲烷化反应器(200)的细粒清除的富含甲烷的粗产品气流(70)含有极少量的细粒。流(70)的温度和压力由所选择的操作条件决定。压力在250至1000psig(1825至6996kpa)范围内,优选在500至650psig(3549至4583kpa)之间。温度在1100至1500°f(593至816℃)范围内,优选在1250至1350°f(677至732℃)之间。
参考图2,细粒清除的富含甲烷的粗产品气流(70)被输送到任选地包含过热器区段(未示出)的热交换器或锅炉系统(400),从而通过锅炉给水(39a)的蒸发而以高压蒸汽流(40)的形式回收热能。蒸汽压力至少比加氢甲烷化反应器(200)的压力高25至50psig(172至345kpa)。蒸汽流(40)优选过热至750至950°f(399至510℃),以使加氢甲烷化反应器(200)的热效率最大化。在没有热交换器系统(400)的过热器区段的情况下,可以在热交换器系统(400)的压力下产生饱和蒸汽。高压蒸汽流(40)被送往蒸汽分配系统(11)。
冷却流(71)是已冷却至约550°f(288℃)的离开热交换器系统(400)的富含甲烷的粗产品。其在中压热交换器或锅炉(410)中在锅炉给水(39b)的作用下进一步冷却至370-400°f(188-204℃),以产生150psig(1136kpa)的冷却蒸汽(72)和中压饱和蒸汽(41),这接近这些条件下的冷却蒸汽(72)的露点。中压饱和蒸汽流(41)被送至蒸汽分配系统(11)。
离开中压锅炉(410)的冷却流(72)在热气体洗涤器(420)中用从低温气体冷却系统(450)和氨回收系统(600)(如下所述)获得的再循环过程冷凝液(未示出)进行洗涤,以去除从旋风分离器中逸出的任何细颗粒物质痕迹。来自热气体洗涤器(420)的含有细颗粒物质的流出物流(未示出)被输送到催化剂回收系统(300)(见图1)。颗粒贫化的冷却气体(73)从热气体洗涤器(420)排出。
气体转化/净化
用于进一步转化颗粒贫化的冷却气体(73)的处理步骤将取决于所需的最终产品,即甲醇或甲醇和替代天然气的双重生产。参考图2,生产甲醇所需的过程步骤包括低温气体冷却(450)、氨回收(600)、酸性气体去除(700)、自热重整(800)和甲醇合成(900)。
(a)低温气体冷却(450)
从热气体洗涤器(420)排出的颗粒贫化的冷却气流(73)直接进入低温气体冷却系统(450),并在低温气体冷却系统(450)内的一系列热交换器中冷却,以进一步将温度降低到120°f(49℃),从而产生干燥的粗气体,即冷却的流出物流(74)。低温气体冷却系统(450)通常包括第一和第二分液罐(knock-outdrums)、空气冷却器和调温冷却器(trimcooler)。
初始约为475°f(246℃)的颗粒贫化的冷却气流(73)首先用锅炉给水(39c)冷却以产生50psig(446kpa)的中压蒸汽(42)和两种水平的低压蒸汽(未示出):30psig(308kpa)和15psig(205kpa)。低品位热的回收允许与过程中需要这些压力水平的蒸汽的其他部分热集成。中压蒸汽流(42)被送至蒸汽分配系统(11)。当气体(73)冷却到200°f(93℃)时,它开始接近水露点,冷凝水在第一个分液罐(未示出)中回收。冷却的流出物流(74)用使用环境空气作为冷却介质的空气冷却器(未示出)进一步冷却,最后用使用冷却水的调温冷却器(未示出)达到120°f(49℃)的最终温度。低温气体冷却系统(450)位置的环境条件将决定可以实现的空气冷却和调温冷却的量。离开调温冷却器的流被送至第二个分液罐(未示出),以从流(74)中分离剩余的水。来自分液罐(未示出)的合并冷凝液被送至氨回收系统(600)。流(74)离开低温气体冷却系统(450)。
(b)氨回收系统(600)
相对于其他气化技术而言,加氢甲烷化反应器(200)在高还原条件下的低温操作允许在脱挥发过程中以氨形式释放的所有氮,从而保持分子形式而不会转化为其他氮氧化物或分解为气态氮。可根据本领域技术人员已知的方法回收氨。接下来描述氨回收过程的具体实施方式。
继续参考图2,在冷却的流出物流(74)离开低温气体冷却系统(450)之后,其在氨回收系统(600)中进行处理以形成氨贫化的流出物(76)。通过在50°f(10℃)下用冷冻水从第一洗涤流(74)来从流(74)回收氨以去除大部分氨。由此产生的氨洗涤器底部液体与分离罐中的冷凝液相结合,并被进给到一系列酸性水汽提塔(未示出),该酸性水汽提塔将氨作为主要产品流和含有痕量的氨、氰化氢、硫化氢和硫化羰的尾气与液相分离。尾气流被送至claus单元(未示出)进行进一步处理。
离开酸性水汽提塔的清洁水没有溶解气体。该水的一部分用作热气体洗涤器(420)的液体进料。余量的水送至催化剂回收系统(300),作为溶剂用于焦炭洗涤步骤(未示出)。
氨回收率大于富含甲烷的粗气流中所含氨的95%。氨通常作为浓度为20-30wt%的水溶液(75)回收。任何回收的氨都可以原样使用,或者,例如,可以与该过程的其他副产品一起转化。例如,它可以与硫酸反应生成产品硫酸铵。
(c)酸性气体去除系统(700)
继续参考图2,离开氨回收系统(600)的流出物(76)随后被送入酸性气体去除(agr)单元(700),以去除绝大多数co2(77)和绝大多数h2s(78),并产生脱硫气流(79)。
酸性气体去除过程通常涉及将气流与选择性吸收酸性气体的溶剂接触。几种酸性气体去除过程可通过商业途径获得,并适用于处理氨贫化的流出物(76)。选择agr的主要标准是使甲烷损失最小化,使得脱硫气流(79)至少包括来自进给到酸性气体去除单元(700)的流出物流(76)的绝大多数(和基本全部)甲烷。通常,此类损失应相应为agr的甲烷进料的约2mol%或更少,或约1.5mol%或更少,或约1mol%或更少。
符合上述标准的溶剂是冷冻甲醇。采用甲醇作为溶剂的可商业获得的过程称为rectisol,由lindeagandlurgioelgaschemiegmbh提供。可考虑的另一可商购过程是selexol(uopllc,desplaines,ilusa),其使用专有溶剂(聚乙二醇二甲醚)。类似地,也可使用由甲基二乙醇胺(mdea)与诸如哌嗪等其他添加剂组成的化学溶剂。mdea可从basf和dow等工艺许可方处获得。
先前并入的us2009/0220406a1中描述了一种去除酸性气体的方法。
应通过酸性气体去除过程去除至少绝大多数(例如,基本全部)co2和/或h2s(以及其他残留的痕量污染物)。在酸性气体去除的上下文下,“基本”去除意味着去除足够高百分比的组分,由此可生成理想的产品。因此,实际去除量可能因组分而异。只能存在(最多)痕量的h2s,尽管可以容忍较高(但仍然很小)的co2。
生成的脱硫气流(79)通常将包含氢、一氧化碳和甲烷(用于下游甲烷化),以及通常痕量的h2o。脱硫气体(79)通常具有至少1.5的氢与一氧化碳的摩尔比,并且在干燥、无co2的基础上具有大于25%的甲烷。
从酸性气体去除(和其他过程,例如酸性水汽提)中回收的任何h2s(78)可通过本领域技术人员已知的任何方法(包括claus工艺)转化为元素硫。硫可以作为熔融液体回收。
从酸性气体去除中回收的任何co2(77)可被压缩以用于在co2管道中运输、用于工业用途和/或封存以用于存储或其他过程(如强化采油),也可用于其他过程操作(如在某些方面中用于催化剂回收和进料准备)。
(d)自热重整(800)和甲醇合成(900)处理
所得的脱硫气流(79)可通过自热重整器(800)处理(利用锅炉给水(39f)、(39g)和(39i))进一步处理,生成甲醇合成进料气(83)和过程蒸汽流(45)、(46)和(48)。然后,甲醇合成进料气(83)可经历甲醇合成(900)(利用锅炉给水(39h))以生成纯化的甲醇产品流(96)和过程蒸汽流(47)。
图4提供了如以上讨论和如图2中描述的自热重整(800)和甲醇合成反应器系统(900)处理的更多细节。
(e)蒸汽生成和分配系统
加氢甲烷化过程需要几种不同压力的蒸汽。首先,在加氢甲烷化反应器(200)中需要蒸汽作为反应物。将蒸汽以比反应器压力至少高50psig(446kpa)的压力进给到加氢甲烷化反应器(200)。尽管反应器可使用饱和蒸汽来工作,但必然会发生氧使用量增加、甲烷生成量降低和二氧化碳生成量增加所致的能量损失。因此,为了使整个过程热效率最大化,优选在510℃(950°f)下在所需压力下的过热蒸汽。其次,需要蒸汽作为执行各种加热任务如催化剂溶液的蒸发/结晶、用于agr和氨回收系统的再沸器等的多用途设施。
参考图2,蒸汽分配系统(11)接收由各种来源生成的蒸汽,并将其分配给过程中的消耗者。具体而言,如上所述,过程蒸汽流(45)、(46)和(48)由自热重整器(800)生成,过程蒸汽流(47)由甲醇合成反应器系统(900)生成。过程蒸汽流(40)、(41)、(42)、(45)、(46)、(47)和(48)被送入蒸汽分配系统(11)。
在加氢甲烷化反应器(200)之后的主过程热交换器或锅炉(400)以及自热重整系统(800)和甲醇合成回路(900)内的热交换器单元产生用于加氢甲烷化反应器(200)和自热重整系统(800)所需品质的高压蒸汽。如前所述,通常使蒸汽温度最大化以提高效率。将过量的高压、饱和或过热蒸汽的压力降至50psig(446kpa)的水平。来自中压锅炉(410)的150psig(1136kpa)的饱和蒸汽也被减压到50psig(446kpa)的水平。低温气体冷却系统(450)还通过回收低品位热产生50psig的蒸汽。50psig蒸汽的所有来源可作为过程内各个消耗者的传热介质。将过量的50psig(446kpa)蒸汽降压至30psig(304kpa),并与低温气体冷却中的30psig(304kpa)蒸汽源合并,以分配给过程中的各个消耗者。各个蒸汽源产生足够的所需水平的蒸汽以满足各个消耗者的需要。因此,整个过程是蒸汽平衡的。任何超出过程需求的高压蒸汽均可转换为功率。过程的蒸汽需求和功率需求由内部能量集成满足,因此该过程不需要净输入蒸汽或功率。
甲醇与替代天然气的联合生产
参考图3,用于联合生产甲醇和替代天然气的气体处理步骤包括首先在热交换器系统(400)中利用锅炉给水(39a)冷却细粒清除的富含甲烷的粗产品气流(70)以形成高压蒸汽流(40)和冷却气流(71),在中压热交换器或锅炉(410)中用锅炉给水(39b)进一步冷却流(71)以产生中压饱和蒸汽(41)和冷却流(72),在热气体洗涤器(420)中洗涤冷却流(72)以形成颗粒贫化的冷却气体(73)。高压蒸汽流(40)和中压饱和蒸汽流(41)被送至蒸汽分配系统(11)。上面的图2更详细地描述了这些冷却和洗涤过程。
然后,使用水煤气转化系统(500)、低温气体冷却(450)、氨回收(600)、酸性气体去除(700)、从甲烷中低温分离氢和一氧化碳(850)以及甲醇合成(900)来继续进行甲醇和替代天然气的联合生产。
(a)水煤气转化(500)
继续参考图3,对于甲醇和替代天然气的联合生产,可能需要使用水煤气转化系统(500)将颗粒贫化的冷却气流(73)的模数调整为甲醇合成回路(900)所需的最佳水平。由于加氢甲烷化催化剂(31)(参见以上图1的描述)促进了水煤气转化反应,因此颗粒贫化的冷却气流(73)具有高的氢与一氧化碳的摩尔比(至少1.5)。因此,与需要多个转化反应器的非催化气化技术相比,只需要一个转化反应器。
当使用联合生产方法制备(即离开低温分离器(850)(见下文))的甲醇合成进料气(83)的模数小于1.75时,离开热气体洗涤器(420)的颗粒贫化的冷却气流(73)将被分为两部分,转化入口流(73a)和转化旁路流(73b)。转化入口流(73a)被送至水煤气转化系统(500),在这里被重新加热至450至550°f(232至288℃),然后通过固定床反应器中的酸转化催化剂(通常是钴-钼),将部分一氧化碳和蒸汽转化为氢和二氧化碳,形成排出气体,即转化出口流(73c)。由于转化反应是放热的,因此来自水煤气转化系统(500)的转化出口流(73c)与转化入口流(73a)进行热交换以回收能量。转化旁路流(73b)绕过水煤气转化系统(500),并与转化出口流(73c)合并以形成富含氢的粗产品气流(73d)。颗粒贫化的冷却气体(73)中被转化的部分,即转化入口流(73a),被控制为在富含氢的粗产品气流(73d)中保持1.75到2的模数。也就是说,只有当在部分e中产生的甲醇合成进料气的模数小于1.75时,才进行转化反应。在某些情况下,可以调节和控制引入水煤气转化反应器(500)中要进行转化的颗粒贫化的冷却气体(73)(即转化入口流(73a))的比例以保持甲醇合成进料气(83)中的模数为1.75到2。
本领域技术人员公知用于在含co气流上执行水煤气转化反应的方法和反应器。在先前并入的us7074373中示出了合适的转化反应器的示例,尽管本领域技术人员已知的其他设计也是有效的。
(b)低温气体冷却(450)
继续参考图3,颗粒贫化的冷却气体(73)或富含氢的粗产品气流(73d)(如果存在)接下来进入低温气体冷却系统(450),并在低温气体冷却系统(450)内的一系列热交换器中冷却,以进一步将温度降低至120°f(49℃),从而产生干燥的粗气体,冷却的流出物流(74)。低温气体冷却系统(450)通常包括第一和第二分液罐、空气冷却器和调温冷却器。
首先,在大约475°f(246℃)的初始温度下,使用锅炉给水(39c)冷却颗粒贫化的冷却气体(73)或富含氢的粗产品气流(73d)(如果存在)以产生50psig(446kpa)的中压蒸汽(42)和两种水平的低压蒸汽(未示出):30psig(308kpa)和15psig(205kpa)。低品位热的回收允许与过程中需要这些压力水平的蒸汽的其他部分热集成。中压蒸汽流(42)被送至蒸汽分配系统(11)。当气体(73)或气体(73d)(如果存在)冷却至200°f(93℃)时,它开始接近水露点,冷凝水在第一个分液罐(未示出)中回收。冷却后的流出物(74)在使用环境空气作为冷却介质的空气冷却器(未示出)上进一步冷却,最后在使用冷却水的调温冷却器(未示出)中冷却以达到120°f(49℃)的最终温度。低温气体冷却系统(450)位置的环境条件将决定可以实现的空气冷却和调温冷却的量。离开调温冷却器的流被送至第二个分液罐(未示出),以将剩余的水从富含氢的粗产品气流(74)中分离出来。来自分离罐(未示出)的合并冷凝液被送至氨回收系统(600),如上图2所示。冷却后的流出物(74)离开低温气体冷却系统(450)。
(c)氨回收系统(600)和酸性气体去除系统(700)
关于甲醇和替代天然气的联合生产,继续参考图3,冷却后的流出物(74)在氨回收系统(600)中进行处理以形成氨贫化的流出物(76),其随后被进给到酸性气体去除(agr)单元(700),以去除绝大多数co2(77)和绝大多数h2s(78),并产生脱硫气流(79),如上文图2所述。
(d)低温分离单元(850)
然后使用低温分离单元(850)从脱硫气流(79)中的甲烷中分离氢和一氧化碳。包含氢和一氧化碳的合成气产品是甲醇合成进料气(83),其模数已通过使用水煤气转化系统(500)而针对甲醇合成回路(900)进行优化。甲烷产品(98)可直接用作替代天然气,并可进一步液化生产液化天然气。
来自酸性气体去除单元(700)的脱硫气流(79)首先在多通道热交换器中相对于排出的产品流进行冷却。将接近其露点的冷却气体投入低温蒸馏,该低温蒸馏将氢和一氧化碳与甲烷分离以形成甲醇合成进料气(83)和甲烷产品(98)。低温分离过程的一个重要特点是能够在内部产生所需的所有制冷。因此,不需要外部制冷循环来完成分离。
(e)甲醇合成(900)处理
然后,甲醇合成进料气(83)可经历甲醇合成(900)(利用锅炉给水(39h))以生成产品纯化甲醇流(96)和过程蒸汽流(47)。
关于上面所讨论和如图3所示的甲醇合成反应器系统(900)处理的更多细节,请参见图4。
(f)蒸汽发生和分配系统
加氢甲烷化过程需要在几种不同的压力下的蒸汽。首先,在加氢甲烷化反应器(200)中需要蒸汽作为反应物。将蒸汽以比反应器压力至少高50psig(446kpa)的压力进给到加氢甲烷化反应器(200)。尽管反应器可以使用饱和蒸汽工作,但必然会产生氧使用量增加、甲烷生成量减少和二氧化碳生成量增加方面的能量损失。因此,为了使整个过程热效率最大化,优选510℃(950°f)和所需压力下的过热蒸汽。其次,需要蒸汽作为执行各种加热任务如催化剂溶液的蒸发/结晶、用于agr的再沸器和氨回收系统等的多用途设施。
参考图3,蒸汽分配系统(11)接收通过各种来源生成的蒸汽,并将其分配给过程中的消耗者。具体地,过程蒸汽流(40)、(41)和(42)分别由热交换器系统(400)、中压热交换器(410)和低温气体冷却单元(450)产生,过程蒸汽流(47)由甲醇合成反应器系统(900)产生。过程蒸汽流(40)、(41)、(42)和(47)被进给到蒸汽分配系统(11)。
在加氢甲烷化反应器(200)之后的主过程热交换器或锅炉(400)和在甲醇合成回路(900)内的热交换器单元产生加氢甲烷化反应器(200)所需质量的高压蒸汽。如前所述,蒸汽温度通常最大化以提高效率。将过量的高压、饱和或过热蒸汽的压力降至50psig(446kpa)的水平。来自中压锅炉(410)的150psig(1136kpa)的饱和蒸汽也被减压到50psig(446kpa)的水平。低温气体冷却系统(450)还通过回收低品位热产生50psig的蒸汽。所有来源的50psig蒸汽可作为过程中各个消耗者的传热介质。过量的50psig(446kpa)蒸汽被降压至30psig(304kpa),并与低温气体冷却中的30psig(304kpa)蒸汽源合并,以分配给过程中的各个消耗者。各种蒸汽源在所需水平产生足够的蒸汽,以满足各种消耗者的需求。因此,整个过程是蒸汽平衡的。任何超出过程需求的高压蒸汽均可转化为功率。该过程的蒸汽需求和功率需求由内部能量集成来满足,因此该过程不需要净输入的蒸汽或功率。
水处理与回收
对于本文所述的任何过程,由一种或多种痕量污染物去除、酸转化、氨去除、酸性气体去除和/或催化剂回收过程所致的废水中的残余污染物可在废水处理单元中去除,以允许根据本领域技术人员已知的任何方法在装置内在循环回收水和/或处理来自装置过程的水。取决于原料和反应条件,此类残余污染物可包括例如芳烃、co、co2、h2s、cos、hcn、nh3和hg。例如,h2s和hcn可通过以下方法去除:将废水酸化至ph值约为3,在汽提塔中用惰性气体处理酸性废水,并将ph值增加至约10,然后用惰性气体第二次处理废水以去除氨(见us5236557)。h2s可通过如下方式去除:在残留焦颗粒存在的情况下用氧化剂处理废水,将h2s转化为不溶性硫酸盐,后者可通过浮选或过滤去除(见us4478425)。芳族化合物可通过如下方式去除:将废水与任选含有一价和二价碱性无机化合物的碳质焦炭(例如,固体焦炭产品或在催化剂回收后的贫化焦炭,见上文)接触并调节ph值(见us4113615)。痕量芳族化合物(c6h6、c7h8、c10h8)也可通过用有机溶剂萃取然后在汽提塔中处理废水来去除(见us3972693、us4025423和us4162902)。
自热重整系统(800)
参考图4,脱硫气流(79)具有35-40mol%h2、19-23mol%co和31-36mol%ch4的典型组成,这是greatpointenergy开发的加氢甲烷化反应器(200)中进行的烃类原料的催化气化所特有的。流(79)与过热蒸汽(12b)(由蒸汽源如蒸汽分配系统(11)提供;见图1)混合以产生混合的粗气体-蒸汽流(79a)。流(79a)在燃烧加热器(810)中利用燃料源(即氢贫化的变压吸收尾气流(86b))在空气中燃烧产生的热来预热至538℃(1000℉),以产生烟道气(88)和产品流(79b)。在满足流(79a)的预热需求后,余热用于在与使用锅炉给水流(391)的热交换器系统(400)相同的条件下产生高压过热蒸汽(48)。已经预热到204℃(400℉)的氧流(15b)和从燃烧加热器(810)产生的产物流(79b)合并以形成混合气体蒸汽流(80),并且进给到自热重整单元(820)。调节氧(15b)和蒸汽(12b)的流速,以确保单元(820)内不发生积碳。自热重整器单元产品,流出物气流(81)具有小于2%的干甲烷含量和在1.7-1.8范围内的模数r。离开自热重整器的蒸汽(81)的温度为954℃(1750℉)。流(81)在自热重整器高温气体冷却系统(830)中冷却至204℃(400℉)。进给到冷却系统(830)的锅炉给水(39f)在510℃(950°f)和5171kpa(750psig)下转化为高压过热蒸汽(45)。冷却系统(830)包括蒸汽生成系统和用于将气体最终冷却至204℃(400℉)的洗涤器。在自热重整器低温气体冷却系统(840)中,将离开冷却系统(830)的冷却的流出物流(82)用锅炉给水流(39g)和环境空气进一步冷却,以生成中压蒸汽(46)和温度为约49℃(120°f)的干燥的、无硫的、甲烷贫化的气体产品,甲醇合成进料气(83)。甲烷合成进料气(83)包含氢、一氧化碳和二氧化碳,其模数可以在1.75-2范围内,并且满足在甲醇合成回路(900)中处理的规格。
甲醇合成回路(900)
继续参考图4,通常在2068至4826kpa(300至700psig)压力下的甲醇合成进料气流(83)在两级压缩系统(910 920)中被压缩至甲醇合成回路的压力,至少5000kpa(1000至1150psig),优选7000至8000kpa(1000至1150psig)。来自第一压缩阶段(910)的产品气体(91)与富含氢的再循环合成气(87)混合以形成气体混合物(92),然后在第二压缩阶段(920)中进一步压缩至所需的最终压力以产生产品气体(93)。产品气体(91)的压力将大于5000kpa(1015psig),优选为7000kpa(1146psig)。将产品气体(93)进给到在近等温条件下操作的甲醇合成反应器(930)。反应的放热以4238kpa(600psig)的高压饱和蒸汽(47)形式从锅炉给水流(39h)回收。来自甲醇合成反应器(930)的产品气体(94)通过如下方式在气体冷却单元(940)中进一步冷却:首先将产品气流(94)预热到所需的入口条件,随后在空气冷却器和冷却水交换器的组合中进行热交换。来自冷却单元(940)的液体冷凝液流(95)在甲醇净化单元(960)中进一步处理,以将产品甲醇流(97)与在反应器(930)中形成的水、高级醇和其他副产品分离,从而产生纯甲醇(96)。来自冷却单元(940)的气体产品是再循环合成气(84),其将包含至少50%的氢。将一部分流(84)作为吹扫气流(85b),以避免惰性物(例如甲烷)在合成回路中积聚到高水平。由于吹扫气流(85b)处于高压并且具有高浓度的氢,因此将其进给到变压吸附单元(950),在这里在与吹扫气流(85b)几乎相同的压力下回收氢流(86a)。在将氢流(86a)与再循环合成气流(84)的剩余部分(85a)合并以形成富含氢的再循环合成气(87)之后,将其循环至甲醇合成回路。来自单元(950)的氢贫化的变压吸收尾气流(86b)用作燃烧加热器单元(810)的燃料源,以预热混合的粗气体-蒸汽流(79a)(如上文中在自热重整单元(800)的描述中所述)。
替代产品
使用自热重整器系统(800)或低温分离系统(850)生产的甲醇合成进料气(83)的氢与一氧化碳的摩尔比在1.75到2.0之间。结果,流(83)适于生产需要在该范围内的氢与一氧化碳的比率的替代产品。一种这样的替代产品是二甲醚。
二甲醚合成的一个途径涉及一氧化碳与氢催化反应生成二甲醚:
另一种生产二甲醚的方法是通过甲醇催化脱水:
应用于替代过程的催化气化的益处将与甲醇的益处相似,因为它们依赖于氢/一氧化碳比约为2的甲醇合成进料气。
虽然已经提供了许多示例性实施方式,但是本文所公开的各个方面和实施方式是为了说明的目的而不是旨在限制。在不脱离本文所呈现的主题的精神和范围的情况下,可以使用其他实施方式,并且可以进行其他改变。将容易理解,如本文一般描述并在附图中示出的,本发明的各个方面可以以各种不同的配置来布置、替换、组合、分离和设计,所有这些配置都在本文中被明确地考虑。
本文用于企业家、创业者技术爱好者查询,结果仅供参考。