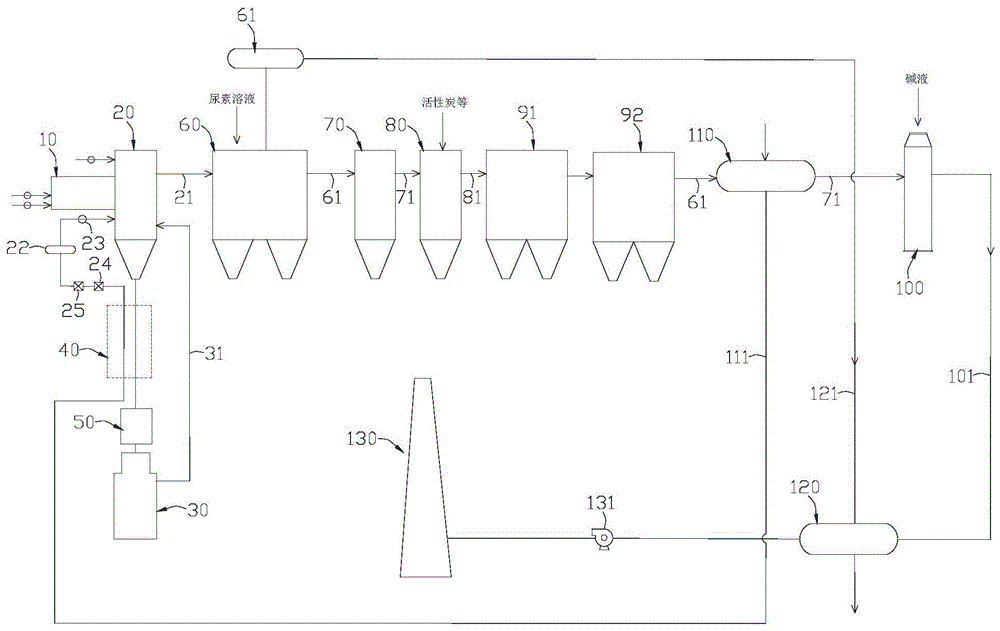
本发明涉及危险废物处理技术领域,尤其涉及一种危险废物焚烧处理系统及方法。
背景技术:
根据2016年新修订《国家危险废物名录》的定义,危险废物为1)具有腐蚀性、毒性、易燃性、反应性或者感染性等一种或者几种危险特性的;2)不排除具有危险特性,可能对环境或者人体健康造成有害影响,需要按照危险废物进行管理的。危险废物处理方法主要有资源化、无害化两类,而无害化以焚烧为主,目前国内外用于危险废物焚烧的主要炉型有回转窑焚烧炉(简称回转窑)、炉排炉、液体注射式焚烧炉、流化床焚烧炉、多层床焚烧炉和热解焚烧炉等,危险废物的焚烧过程较复杂,回转窑炉因结构简单、对危险废物的适应能力强、控制稳定、操作容易、技术成熟、运行历史悠久等优点被广泛采用。
但是,回转窑焚烧后会产生20%~25%的灰渣,这部分灰渣按国家规定仍属于危险废物,需进行固化处理后进入填埋场,填埋费用比较高,会占用宝贵的土地资源,也存在环境隐患。部分地区的液体废物在进入回转窑焚烧前可能出现因冬季环境温度过低而堵塞的情况,存在运行安全隐患。随着对烟气氮氧化物排放要求越来越严格,对回转窑焚烧排出的烟气,常规的烟气处理方法无法满足监管要求。
技术实现要素:
本发明要解决的技术问题在于,提供一种实现危险废物的无害化、减量化和资源化的危险废物焚烧处理系统及危险废物焚烧处理方法。
本发明解决其技术问题所采用的技术方案是:提供一种危险废物焚烧处理系统,包括对危险废物进行焚烧处理的回转窑、对烟气进行再次燃烧处理的二燃室、对残渣进行熔融处理的等离子体熔融炉、灰渣传输单元、余热锅炉、急冷塔、干法脱酸塔、除尘单元以及湿法脱酸塔;
所述回转窑和二燃室紧邻相接且两者共用一个出渣口;所述灰渣传输单元连接在所述出渣口和等离子体熔融炉之间,所述回转窑和二燃室内产生的残渣从所述出渣口排出并通过所述灰渣传输单元输送至所述等离子体熔融炉内,通过所述等离子体熔融炉进行熔融处理形成玻璃体;所述回转窑和所述等离子体熔融炉内产生的烟气输送至所述二燃室内进行再次燃烧处理;
所述余热锅炉、急冷塔、干法脱酸塔、除尘单元以及湿法脱酸塔依次连接所述二燃室,对所述二燃室排出的高温烟气依次进行降温、吸附净化、除尘过滤及脱酸处理。
优选地,所述回转窑的出烟口与所述二燃室的进烟口对接,所述回转窑内焚烧产生的烟气通过所述出烟口和进烟口进入所述二燃室;
所述等离子体熔融炉的出烟口通过出烟管道连接所述二燃室,所述等离子体熔融炉内熔融处理产生的烟气通过所述出烟管道输送至所述二燃室内。
优选地,所述灰渣传输单元包括用于对残渣进行冷却的水封刮板出渣机、用于输送所述残渣的密闭的皮带输送机构;
所述水封刮板出渣机设置在所述出渣口处,所述皮带输送机构连接在所述水封刮板出渣机和所述等离子体熔融炉的进料口之间。
优选地,所述危险废物焚烧处理系统还包括对残渣进行破碎并与促熔剂混合的底渣混料装置;所述底渣混料装置设置在所述皮带输送机构和所述等离子体熔融炉的进料口之间。
优选地,所述底渣混料装置包括将残渣进行破碎的破碎机、用于破碎的残渣在其中与促熔剂混合形成混料的混料机、接收来自所述混料机的混料并制成残渣颗粒的对辊制粒机、接收来自所述对辊制粒机的残渣颗粒并送入所述等离子体熔融炉的振动料仓。
优选地,所述除尘单元包括依次连接在所述干法脱酸塔和所述湿法脱酸塔之间的旋风除尘器和袋式除尘器。
优选地,所述危险废物焚烧处理系统还包括设置在所述袋式除尘器和所述湿法脱酸塔之间的空气预热器,用于烟气通过且回收烟气的热量,将回收的热量加热空气后作为所述二燃室的助燃风。
优选地,所述空气预热器内具有进行热交换的烟气通道和空气通道;所述烟气通道分别与所述袋式除尘器和湿法脱酸塔相连通,所述空气通道的出口通过通风管道连接所述二燃室,将与烟气热交换后的空气输送至所述二燃室内。
优选地,所述通风管道上设有对空气进行过滤的过滤器、对空气进行干燥的干燥器以及送风机。
优选地,所述皮带输送机构设置在所述通风管道上,利用所述通风管道输送的空气加热残渣。
优选地,所述危险废物焚烧处理系统还包括烟气加热器;所述烟气加热器连接在烟囱和所述湿法脱酸塔之间,将所述湿法脱酸塔排出的烟气进行加热后排至所述烟囱。
优选地,所述烟气加热器通过蒸汽管道和分汽缸连接所述余热锅炉,以所述余热锅炉产生的蒸汽作为热源。
本发明还提供一种危险废物焚烧处理方法,采用以上任一项所述的危险废物焚烧处理系统;所述危险废物焚烧处理方法包括以下步骤:
s1、将危险废物送入回转窑进行焚烧处理;
焚烧处理产生的烟气输送至二燃室内,焚烧处理产生的残渣与所述二燃室内产生的残渣通过出渣口进入灰渣传输单元;
s2、所述灰渣传输单元对残渣进行冷却及干燥处理后,送入等离子体熔融炉进行等离子体熔融处理,形成玻璃体;
s3、将所述等离子体熔融炉内熔融处理产生的烟气输送至二燃室,所述二燃室将来自所述回转窑和等离子体熔融炉的烟气进行再次燃烧处理,将烟气中的包括二噁英的有害成分分解,输出高温烟气;
s4、将高温烟气输送至余热锅炉内,高温烟气中的氮氧化物经与喷入所述余热锅炉内的尿素溶液进行反应脱除;
s5、将降温后的烟气从所述余热锅炉输送至急冷塔进行换热再降温,同时防止二噁英再合成;
s6、将换热再降温后的烟气输送至干法脱酸塔,去除烟气中的酸性气体;
s7、将净化后的烟气输送至除尘单元进行除尘过滤处理,去除烟气中的包括重金属和二噁英的污染物;
s8、将除尘过滤后的烟气输送至湿法脱酸塔内,通过碱液对烟气进行脱酸处理,脱除烟气中的hcl、hf和so2。
本发明的有益效果:以等离子体熔融炉结合回转窑,对焚烧后的残渣进行熔融处理形成玻璃体,通过二燃室及余热锅炉等进一步对焚烧和熔融处理产生的烟气进行处理,使得烟气满足排放标准,实现危险废物的无害化、减量化和资源化。
附图说明
下面将结合附图及实施例对本发明作进一步说明,附图中:
图1是本发明一实施例的危险废物焚烧处理系统的连接框图;
图2是本发明一实施例的危险废物焚烧处理系统中的臭氧制取装置的连接框图。
具体实施方式
为了对本发明的技术特征、目的和效果有更加清楚的理解,现对照附图详细说明本发明的具体实施方式。
本发明的危险废物焚烧处理系统,用于危险废物进行熔融处理以及对熔融处理产生的烟气进行处理,去除烟气中的有害物质等。
如图1所示,本发明一实施例的危险废物焚烧处理系统,包括回转窑10、二燃室20、等离子体熔融炉30、灰渣传输单元40、底渣混料装置50、余热锅炉60、急冷塔70、干法脱酸塔80、除尘单元以及湿法脱酸塔100。
回转窑10用于对危险废物进行焚烧处理,二燃室20用于对烟气进行再次燃烧处理,去除其中的有害成分;回转窑10和二燃室20紧邻相接且两者共用一个出渣口。灰渣传输单元40连接在出渣口和等离子体熔融炉30之间,回转窑10和二燃室20内产生的残渣从出渣口排出并通过灰渣传输单元40输送至等离子体熔融炉30内,通过等离子体熔融炉30对残渣进行熔融处理形成玻璃体。底渣混料装置50设置在灰渣传输单元40和等离子体熔融炉30之间,对残渣进行破碎并与促熔剂混合形成混料再送至等离子体熔融炉30内。回转窑10和等离子体熔融炉30内产生的烟气输送至二燃室20内进行再次燃烧处理。
余热锅炉60、急冷塔70、干法脱酸塔80、除尘单元以及湿法脱酸塔100依次连接二燃室20,对二燃室20排出的高温烟气依次进行降温、吸附净化、除尘过滤及脱酸处理,最后获得符合排出标准的气体。
其中,回转窑10和二燃室20紧邻相接,回转窑10的出烟口和二燃室20的进烟口直接对接,回转窑10内的烟气在密闭空间内直接送入二燃室20,不外漏。
具体地,回转窑10包括窑头、本体、窑尾和传动机构等。窑头的主要作用是完成物料(如危险废物)的顺畅进料,内部布置有辅助燃料/液废组合燃烧器。窑头下部设置有废料收集器以收集废物漏料。回转窑10的本体是一个由钢板卷成的圆筒,内衬耐火材料。本体上设有两个带轮和一个大齿圈,传动机构通过小齿轮带动本体上的大齿圈,然后通过大齿圈带动回转窑10本体转动。窑尾是连接回转窑10本体以及二燃室20的过渡体,它的主要作用是保证窑尾的密封以及烟气和焚烧残渣的输送通道。
为保证危险废物向下的传输,回转窑10必须保持一定的倾斜度。回转窑10的窑尾插入二燃室,与二燃室20共用一个出渣口。出渣口设置在二燃室20的底部且优选设置为大开口出渣,便于大颗粒渣块落渣。同时在二燃室20底部设置多组分燃烧机,保证二燃室20的燃烧温度高于1100℃,同时提升回转窑10窑尾温度。
危险废物通常包括有液态废物和固态废物;固态废物通过液压推杆推入回转窑10内;液态废物通过输送泵经管道输送至回转窑10窑头,再送入回转窑10的本体内。回转窑10内焚烧产生的烟气输送至二燃室20进行再次燃烧处理,焚烧后的残渣则从出渣口排出。
二燃室20对烟气进行再次燃烧处理,以将烟气中的二噁英和其它有害成分分解。二燃室20的尺寸以能保证烟气在1100℃以上的温度下滞留时间大于2s进行设置;在此条件下,烟气中的二噁英和其它有害成分的99.99%能够被分解掉。二燃室20的下部设置有所需数量(如两个)的多功能燃烧器,保证二燃室20烟气温度达到要求,并使烟气有充分的扰动。二燃室20上可设置热电偶控制多功能燃烧器的火力大小,使二燃室20温度稳定在设定值。
在对烟气进行再次燃烧处理前,二燃室20内也需输入液态废物。液态废物通过输送泵经管道输送至二燃室20的多功能燃烧器,然后进入二燃室20内。回转窑10和二燃室20上均设有进风口以分别送入助燃风。
作为选择,二燃室20内壁为耐火层,外壁依次为隔热保温层和外防护板。二燃室20内部工作温度为1100℃以上,外表温度≤60℃。
等离子体熔融炉30用于对回转窑10和二燃室20排出的残渣进行熔融处理以形成稳定的玻璃体。等离子体熔融炉30以等离子体发生器作为加热热源,等离子体发生器在等离子体熔融炉30上采用侧向和顶部均布形式,具有加热效率高、加热均匀、换热量大、活化熔融效果好等特点。
等离子体熔融炉30内最高温度在1400℃以上,残渣在炉内有足够的停留时间,确保残渣熔化并经等离子体活化反应确保重金属的固化后从等离子体熔融炉30的出料口流出。等离子体熔融炉30的炉膛内设有高温熔池,可以最大限度的加快入炉残渣的熔融,提高热利用率和处理能力。同时,熔池熔液对重金属具有较好的均匀包裹,所形成的固化体物化性能更加稳定。
残渣在等离子体高温加热熔化作用下,逐步熔融并形成熔池,成为均匀的固化体熔液。熔液在炉膛内停留一定时间,使之在高温等离子体活化作用下进行类玻璃化反应,最终从出料口流出并经自然冷却或水淬冷却后形成玻璃固化体(简称玻璃体),有效抑制避免了亚稳态、非平衡组合复杂成分的生成。残渣中的铜等不易挥发的金属元素及其化合物大部分进入玻璃固化体中。
等离子体熔融炉30产生的玻璃体浸出毒性浓度低于国家标准,可以当做一般废弃物处理。同时,部分残渣熔融处理后的玻璃固化体可回收利用,作为水泥配料、建筑材料、保温材料或工艺制品材料等,实现了部分危险废物的循环再利用。
等离子体熔融炉30一般为微负压设计,炉体密封效果好,无有害气体外泄,可大大减少有用组分的挥发,只有极少量的废气、烟气排出,操作环境好,环保条件优良。
灰渣传输单元40和底渣混料装置50依序设置在出渣口和等离子体熔融炉30之间,对进入等离子体熔融炉30的残渣进行预处理。
其中,灰渣传输单元40包括用于对残渣进行冷却的水封刮板出渣机、用于输送残渣的密闭的皮带输送机构。
水封刮板出渣机设置在回转窑10和二燃室20的出渣口处,皮带输送机构连接在水封刮板出渣机和底渣混料装置50之间。水封刮板出渣机的槽内灌满冷却水,从出渣口处排出的残渣进入槽内冷却,这使得焚烧产生的烟气和残渣都不直接和外部接触,达到密封的效果。焚烧后的残渣进入水中后迅速冷却,由水封刮板出渣机连续的输出到密闭的皮带输送机构,自动输送到底渣混料装置50,实现自动出渣和自动输送。
另设有料斗接口插入水封刮板出渣机的槽内水中150mm,通过自动补水保持水位恒定。
底渣混料装置50设置在皮带输送机构和等离子体熔融炉30的进料口之间,对皮带输送机构输送的残渣进行破碎并与促熔剂混合制成混料;促熔剂起到促进残渣熔融的作用以形成稳定玻璃体,其可包括硅酸盐混合物。
如图2所示,底渣混料装置50可包括将残渣进行破碎的破碎机51、用于破碎的残渣在其中与促熔剂混合形成混料的混料机52、接收来自混料机52的混料并制成残渣颗粒的对辊制粒机53、接收来自对辊制粒机53的残渣颗粒并送入等离子体熔融炉30的振动料仓54。
具体地,皮带输送机构将残渣先倾倒入破碎机51的料斗内进行破碎。破碎机51的投料口处可设置除尘装置,降低空气含尘量。破碎后的残渣通过第一斗式提升机输送到储料仓55,储料仓55底部装有配料绞龙,配料绞龙将料仓内残渣输送入配料称。电脑配料系统按促熔剂组成经配料称进行称重后,通过卸料阀进入缓冲仓,再通过螺旋输送机进入第二斗式提升机,然后通过第二斗式提升机进入待混合仓56。
同时,在第三斗式提升机入口处设一套起吊装置57,用起吊装57置将促熔剂料包吊起转运至第三斗式提升机入口,通过第三斗式提升机进入配方仓58。配方仓58底部装有配料绞龙,配料绞龙将配方仓内促熔剂料包输送入配料称。电脑配料系统按促熔剂组成经配料称进行称重后,通过卸料阀进入缓冲仓,再通过螺旋输送机进入第二斗式提升机,然后通过第二斗式提升机进入待混合仓56。
残渣和促熔剂一起通过待混合仓56底部的卸料阀进入混料机52。混料机52按设定的混料时间进行混料,混合好后,混料机52底部的卸料阀打开,卸料到第四斗式提升机,通过第四斗式提升机把混合好的物料输送到对辊制粒机53的料斗内,开始制粒,粒度为6-10mm,可优选8mm。制好的颗粒落到接驳台上的金属桶内。转运小车转运接料后的金属桶到振动料仓54进行下一步处理。振动料仓54下料时,先打开其底部的第一个气动闸板阀,再打开耐高温的第二个气动闸板阀,下料,颗粒落入等离子体熔融炉20中。其中,通过调节振动电机的振幅来控制振动料仓54下料的速度。
等离子体熔融炉30的出烟口通过出烟管道31连接二燃室20,等离子体熔融炉30内熔融处理产生的烟气通过出烟管道31输送至二燃室20内,与回转窑10产生的烟气一起在二燃室20内进行再次燃烧处理。
二燃室20通过第一烟道21连接余热锅炉60的进气口,将再次燃烧后形成的高温烟气输送至余热锅炉60,进行选择性非催化还原反应(sncr)。在余热锅炉60内,尿素溶液等还原剂与高温烟气中的氮氧化物进行反应,从而达到脱除烟气中氮氧化物的目的。通过sncr,高温烟气的热量被余热锅炉60回收,可产生大量蒸汽,产生的蒸汽可供生产线内部及厂区其他用户使用,避免烟气热量损失。
具体地,在余热锅炉60内烟气温度900℃-1050℃区间的水冷壁上均匀喷入尿素溶液,尿素溶液与高温烟气中的氮氧化物进行反应,从而达到脱除烟气中氮氧化物的目的。高温烟气经过余热锅炉60的处理后,温度可降至550℃或以下。余热锅炉60的出气口通过第二烟道61连接急冷塔70,烟气从余热锅炉60的出气口输出并通过第二烟道61输送至急冷塔70。余热锅炉60内产生的飞灰从其底部排出进行收集处理。
烟气主要从急冷塔70的上方进入其内。急冷塔70内设有双流体喷头,喷出雾化液滴与进入急冷塔70内的烟气进行换热,带走烟气的热量。其中,在压缩空气的作用下,在喷头的内部,压缩空气与naoh溶液经过若干次的打击,naoh溶液被雾化成0.08mm左右的雾化液滴,雾化液滴与高温烟气充分换热,在短时间内迅速蒸发(蒸发时间短,确保100%蒸发,保证不湿底),带走热量,使得烟气温度在瞬间被降至200℃以下,且含水率(质量比)小于3%。通过控制烟气流速,使烟气在200℃-500℃之间停留时间小于1s,防止二噁英的再合成。另外,由于雾化液滴由naoh溶液形成,naoh溶液与烟气中的so2等酸性气体发生中和反应,达到初步脱酸的目的。
急冷塔70内从烟气中脱除的一部分飞灰从急冷塔70底部排出,以便于收集处理。
经过急冷后的烟气从急冷塔70通过第三烟道71输送至干法脱酸塔80以进行吸附净化处理。为了满足废物烟气排放标准,确保重金属(尤其是hg)、二噁英、呋喃的排放标准,除严格控制焚烧工艺和技术参数外,干法脱酸塔80常采用活性炭喷射吸附的辅助净化措施。由于活性炭具有极大的比表面积,因此,即使是少量的活性炭,只要与烟气混合均匀且接触时间足够长,就可以达到高吸附净化效率。
烟气进入干法脱酸塔80与喷入塔中的熟石灰、活性炭和飞灰的混合粉充分接触,反应形成粉尘状钙盐,达到去除烟气中二氧化硫和氯化氢等酸性气体的目的。
干法脱酸塔80输出的含尘的烟气通过进气管81输送至除尘单元进行除尘过滤处理。除尘单元包括依次连接在干法脱酸塔80和湿法脱酸塔100之间的旋风除尘器91和袋式除尘器92。
烟气由进风管81进入旋风除尘器91,通过旋风除尘器91去除大颗粒灰尘,提高除尘效率。旋风除尘器91采用双进口除尘器,降低设备阻力。旋风除尘器91的出口连接袋式除尘器92,将经一次除尘过滤后的烟气输送至袋式除尘器92进行二次除尘和过滤。袋式除尘器92中的滤袋与缓慢通过滤袋的烟气充分接触,达到对烟气中重金属(尤其是hg)、二噁英、呋喃等污染物的吸附净化,吸附重金属、二噁英等污染物的活性炭落入袋式除尘器92底部的灰斗内,净化后的烟气经滤袋口进入袋式除尘器60的清洁室,由袋式除尘器92的出口排出。
旋风除尘器91出口设置温度计和红外加热设备,当检测到烟气温度低于设计值,启动红外加热设备,将烟气温度加热至设计值,可降低袋式除尘器92堵塞几率。袋式除尘器92采用高效聚四氟乙烯覆膜滤料,滤出烟气中的烟尘确保达到设计烟尘排放标准,所收集的飞灰外送进行安全填埋。
湿法脱酸塔100连接袋式除尘器92,对除尘过滤后的烟气进行脱酸处理。
湿法脱酸塔100内上部设置喷淋装置,通过喷淋装置喷出naoh溶液。烟气进入湿法脱酸塔100内在上升过程中,与喷出的naoh溶液混合接触反应,去除烟气中的hcl、hf以及so2。湿法脱酸塔100的内壁做玻璃鳞片防腐,提高设备的安全可靠性,延长运行周期。
本发明中,湿法脱酸塔100和袋式除尘器92之间还设有空气预热器110,用于烟气通过且回收烟气的热量,将回收的热量加热空气后作为回转窑10的助燃风。空气预热器110内具有进行热交换的烟气通道和空气通道;烟气通道分别与袋式除尘器92和湿法脱酸塔100相连通;空气通道的进口用于接入外部的冷空气,出口通过通风管道111连接二燃室20。袋式除尘器92排出的烟气进入空气预热器110的烟气通道,与进入空气通道内的冷空气进行热交换,经换热降温后的烟气从烟气通道输出进入湿法脱酸塔100;空气通道内的冷空气经热交换后升温形成热空气,通过通风管道111输送至二燃室20内,作为二燃室20的助燃风,提高二燃室20的燃烧效率。
为进一步利用热量,通风管道111接入皮带输送机构,使得通风管道111输送的热空气通过皮带输送机构,利用通风管道111输送的热空气加热残渣皮带输送机构输送的残渣,降低残渣含水率,有效提高后续等离子体熔融炉30的处理效果。
进一步地,通风管道111上设有对空气进行过滤的过滤器、对空气进行干燥的干燥器22以及送风机23。过滤器、干燥器22以及送风机23均设置在通风管道111位于二燃室20和皮带输送机构之间的管道段上,对经过皮带输送机构的热空气进行过滤、干燥等处理后再进入二燃室20。
其中,送风机23提供动力,将热空气送入二燃室20内。过滤器可包括过滤精度不同的粗过滤器24和精过滤器25,分别滤去空气中不同粒度的颗粒杂质。干燥器22位于过滤器的后端,对过滤后的烟气进行干燥处理,最后再进入二燃室20。
湿法脱酸塔100输出的烟气温度为60℃左右,输出的烟气可通过第四烟道101输送至烟囱130进行外排。为避免烟囱130出口出现“白烟”现象,本发明的危险废物焚烧处理系统还包括烟气加热器120;烟气加热器120连接在湿法脱酸塔100和烟囱130之间,接收来自湿法脱酸塔100的烟气并对烟气进行加热。经加热后的净烟在风机131的驱动下从烟囱130排出。
烟气加热器120还通过蒸汽管道121连接余热锅炉60,以余热锅炉60产生的蒸汽作为热源,不需要使用外供蒸汽,节省能源。余热锅炉60的蒸汽出口设有分汽缸61,通过分汽缸61连接蒸汽管道121。
蒸汽在烟气加热器120与通过烟气加热器120的烟气进行热交换,使烟气温度升高,蒸汽热交换后冷凝排出至除盐水箱进行后续处理。
此外,为解决烟气加热器120的腐蚀问题,烟气加热器120的换热管采用氟塑钢制成,区别常规的不锈钢换热管,不易腐蚀,使命寿命长。
本发明的危险废物焚烧处理系统用于对危险废物进行焚烧处理处理,参考图1,危险废物焚烧处理方法可包括以下步骤:
s1、将危险废物送入回转窑10进行焚烧处理。
焚烧处理产生的烟气输送至二燃室20内,焚烧处理产生的残渣与二燃室20内产生的残渣通过共用的出渣口进入灰渣传输单元40。
s2、灰渣传输单元40对残渣进行冷却及干燥处理后,再通过底渣混料装置50破碎并与促熔剂混合制成混料后,送入等离子体熔融炉30进行等离子体熔融处理,形成玻璃体。
s3、将等离子体熔融炉30内熔融处理产生的烟气输送至二燃室20,二燃室20将来自回转窑10和等离子体熔融炉30的烟气进行再次燃烧处理,将烟气中的包括二噁英的有害成分分解,输出高温烟气。
s4、将高温烟气输送至余热锅炉60内,高温烟气中的氮氧化物经与喷入余热锅炉60内的尿素溶液进行反应脱除。
s5、将降温后的烟气从余热锅炉60输送至急冷塔70进行换热再降温,同时防止二噁英再合成。
高温烟气经过余热锅炉60的处理后,温度可降至550℃或以下。在急冷塔70内,通过双流体喷头喷出0.08mm左右的液滴,液滴与烟气充分换热,在短时间内迅速蒸发,带走热量,使得烟气温度在瞬间被降至200℃以下,且含水率(质量比)小于3%。由于烟气在200℃-500℃之间停留时间小于1s,因此防止了二噁英的再合成。
s6、将换热再降温后的烟气输送至干法脱酸塔80,去除烟气中的酸性气体。
烟气进入干法脱酸塔80与喷入塔中的熟石灰、活性炭和飞灰的混合粉充分接触,反应形成粉尘状钙盐,达到去除烟气中二氧化硫和氯化氢等酸性气体的目的。烟气中含有的水分在ca(oh)2颗粒表面与酸性气体间发生液相离子反应,显著提高脱酸效率和吸收剂利用率。
s7、将净化后的烟气输送至除尘单元进行除尘过滤处理,去除烟气中的包括重金属和二噁英的污染物。
除尘单元通过旋风除尘器91和袋式除尘器92对烟气进行两级除尘过滤处理。
s8、将除尘过滤后的烟气输送至湿法脱酸塔100内,通过碱液对烟气进行脱酸处理,脱除烟气中的hcl、hf和so2。
s9、将脱酸处理后的烟气输送至烟气加热器120,烟气加热器120利用余热锅炉60排出的蒸汽与烟气进行热交换,将烟气加热后再通过烟囱130排放。
由于烟气加热器110的热源由余热锅炉60产生的蒸汽提供,不需要使用外供蒸汽,节省能源。
本发明的危险废物焚烧烟气处理方法,各处理过程的具体操作可参考上述系统相关所述。
以上所述仅为本发明的实施例,并非因此限制本发明的专利范围,凡是利用本发明说明书及附图内容所作的等效结构或等效流程变换,或直接或间接运用在其他相关的技术领域,均同理包括在本发明的专利保护范围内。
本文用于企业家、创业者技术爱好者查询,结果仅供参考。