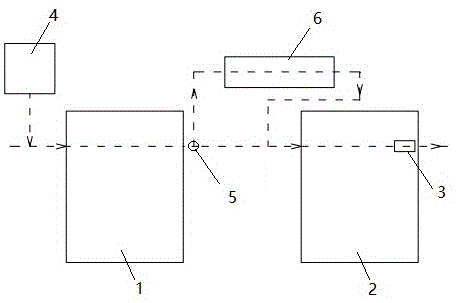
本发明涉及一种降低热流发生器排放的方法,特别是一种降低热振试验用热流发生器氮氧化物排放的方法。
背景技术:
热振动试验是汽车用排气后处理器研发和制造过程中,确保后处理器机械性能可靠性的必要试验环节。中国环境保护产业协会提出了针对柴油机排气后处理装置机械性能的相关标准,明确规定了热振动的试验要求。在热振动试验过程中,热流发生器主要用于提供高温热流,模拟发动机排气温度和流量。
热流发生器主要有电加热、燃气加热、柴油加热三种形式,其中,电加热主要用于提供恒定温度的试验要求,燃气加热与柴油加热可以实现温度的快速变化,除了用于恒定温度试验,还可以满足温度循环的试验要求,但是,燃气加热存在一定的安全隐患,当出现点火失败的情况时,再次点火时容易出现爆震,严重时有发生爆炸的风险。柴油加热在安全性上有明显的优势,但是,柴油在高温富氧的燃烧过程中,会产生大量的氮氧化物排放,造成环境污染,危害人体健康。
目前,针对热流发生器的氮氧化物排放问题,主要采用降低热流发生器燃烧温度的方法,降低氮氧化物排放,但是,这种方式普遍存在热流发生器提供的最终热流温度下降的问题,影响热振试验的热流环境稳定性。
技术实现要素:
针对上述现有技术缺陷,本发明的任务在于提供一种降低热振试验用热流发生器氮氧化物排放的方法,在保证热流环境温度稳定的同时,降低氮氧化物排放,从而降低对环境和人体的伤害。
本发明技术方案如下:一种降低热振试验用热流发生器氮氧化物排放的方法,所述热流发生器包括依次串联设置的第一燃烧器和第二燃烧器,所述第一燃烧器的排气通过控制阀选择直接或者经过排气旁路通入所述第二燃烧器,所述排气旁路设有用于冷却排气的水冷却器,所述第二燃烧器设有电加热器,经过所述电加热器加热后的排气作为最终排气热流,所述方法包括以下步骤:
步骤一、预设第一设定温度阈值、第二设定温度阈值和第三设定温度阈值,当需求热流温度小于第一设定温度阈值时,以柴油为单一燃料,由所述第一燃烧器燃烧形成热流至热流温度达到所述需求热流温度;当需求热流温度小于第二设定温度阈值且大于等于第一设定温度阈值时进入步骤二;当需求热流温度小于第三设定温度阈值且大于等于第二设定温度阈值时进入步骤三;当需求热流温度大于等于第三设定温度阈值时进入步骤四;所述第一设定温度阈值为350~360℃,所述第二设定温度阈值为500~520℃,所述第三设定温度阈值为700~750℃;
步骤二、以柴油为单一燃料,由所述第一燃烧器燃烧形成热流至第一切换温度后,以柴油与醇类燃料的混合燃料由所述第一燃烧器燃烧形成热流并控制通入所述第一燃烧器的co2流量使所述第一燃烧器形成的热流温度升温速率不大于第一控制速率直至热流温度达到需求热流温度,所述第一切换温度为190~200℃;
步骤三、以柴油为单一燃料,由所述第一燃烧器燃烧形成热流至第二切换温度后,以柴油与醇类燃料的混合燃料由所述第一燃烧器燃烧形成热流并控制通入所述第一燃烧器的co2流量使所述第一燃烧器形成的热流温度升温速率不大于第二控制速率直至热流温度达到第三切换温度后,启动所述第二燃烧器的电加热器对热流加热至需求热流温度,所述第二切换温度为230~250℃,所述第三切换温度为380~400℃;
步骤四、以柴油为单一燃料,由所述第一燃烧器燃烧形成热流至第四切换温度后,以柴油与醇类燃料的混合燃料由所述第一燃烧器燃烧形成热流并控制通入所述第一燃烧器的co2流量使所述第一燃烧器形成的热流温度升温速率不大于第三控制速率直至热流温度达到第五切换温度后,以柴油与醇类燃料的混合燃料由所述第二燃烧器燃烧加热热流、启动所述电加热器对热流加热并将热流引导至水冷却器使热流回流至第二燃烧器直至所述电加热器加热后热流温度达到需求热流温度;所述第四切换温度为230~250℃,所述第五切换温度为480~520℃。
进一步地,所述步骤二包括以下步骤:步骤201、以柴油为单一燃料,由所述第一燃烧器燃烧形成热流至第一切换温度后进入步骤202;步骤202、以柴油与醇类燃料的混合燃料由所述第一燃烧器燃烧,所述醇类燃料按混合燃料总质量的12~15%添加进入步骤203;步骤203、判断第一燃烧器形成的热流温度升温速率,当热流温度升温速率大于第一限制速率时进入步骤204,当热流温度升温速率不大于第一限制速率时进入步骤205;步骤204、将混合燃料中醇类燃料的添加量在前一次添加量基础上增加40~50%,回到步骤203;步骤205、按目标热流流量的10~12%向所述第一燃烧器通入co2,进入步骤206;步骤206、判断第一燃烧器形成的热流温度升温速率,当热流温度升温速率大于第一控制速率时进入步骤207,当热流温度升温速率不大于第一控制速率时保持各参数使最终热流达到需求热流温度;步骤207、co2流量提高40~50%并回到步骤206。
进一步地,所述第一限制速率为40~45℃/s,所述第一控制速率为30~35℃/s。
进一步地,所述步骤三包括以下步骤:步骤301、以柴油为单一燃料,由所述第一燃烧器燃烧形成热流至第二切换温度后进入步骤302;步骤302、以柴油与醇类燃料的混合燃料由所述第一燃烧器燃烧,所述醇类燃料按混合燃料总质量的10~12%添加进入步骤303;步骤303、判断第一燃烧器形成的热流温度升温速率,当热流温度升温速率大于第二限制速率时进入步骤304,当热流温度升温速率不大于第二限制速率时进入步骤305;步骤304、将混合燃料中醇类燃料的添加量在前一次添加量基础上增加40~50%,回到步骤303;步骤305、按目标热流流量的5~8%向所述第一燃烧器通入co2,进入步骤306;步骤306、判断第一燃烧器形成的热流温度升温速率,当热流温度升温速率大于第二控制速率时进入步骤207,当热流温度升温速率不大于第一控制速率时保持各参数使第一燃烧器产生热流达到所述第三切换温度后进入步骤308;步骤307、co2流量提高40~50%并回到步骤306;步骤308、第一燃烧器的热流直接进入第二燃烧器,启动所述第二燃烧器的电加热器对热流加热至需求热流温度。
进一步地,所述第二限制速率为45~48℃/s,所述第二控制速率为35~38℃/s。
进一步地,所述步骤四包括以下步骤:步骤401、以柴油为单一燃料,由所述第一燃烧器燃烧形成热流至第四切换温度后进入步骤402;步骤402、以柴油与醇类燃料的混合燃料由所述第一燃烧器燃烧并按目标热流流量的5~8%向所述第一燃烧器通入co2,所述醇类燃料按混合燃料总质量的10~12%添加,进入步骤403;步骤403、判断第一燃烧器形成的热流温度升温速率,当热流温度升温速率大于第三控制速率时进入步骤404,当热流温度升温速率不大于第三控制速率时保持各参数使第一燃烧器产生热流达到第五切换温度进入步骤405;步骤404、将混合燃料中醇类燃料的添加量在前一次添加量基础上增加40~50%,co2流量提高40~50%,回到步骤403;步骤405、以柴油与醇类燃料的混合燃料由所述第二燃烧器燃烧,所述醇类燃料按混合燃料总质量的15~20%添加,第一燃烧器的热流经过排气旁路后进入第二燃烧器,开启所述电加热器,进入步骤406;步骤406、判断经过电加热器加热后热流温度,当加热后热流温度大于第六切换温度后进入步骤407;步骤407、判断电加热器加热后热流温度的升温速度,当加热后热流温度的升温速度大于第四控制速率时进入步骤408,当热流温度升温速率不大于第四控制速率时保持各参数使电加热器加热后热流达到需求热流温度;步骤408、将第二燃烧器的混合燃料中醇类燃料的添加量在前一次添加量基础上增加30~35%,水冷却器流量提高30~35%,回到步骤407。
进一步地,所述第三控制速率为40~42℃/s,所述第四控制速率为30~32℃/s,所述第六切换温度为600~650℃。
进一步地,所述醇类燃料为甲醇或乙醇。
本发明根据需要达到热流温度的不同进行不同的控制,其基本原理是
1、需要达到的热流温度小于第一设定温度阈值时,生成的氮氧化物较少,不进行处理。
2、需要达到的热流温度处于第一设定温度阈值与第二设定温度阈值之间时,一方面,通过增加多组分燃料中醇类燃料的比例,由于醇类燃料的汽化潜热高,燃烧过程中能够吸收更多的热流,从而降低热流温度;另一方面,通过在热流中通入比热容较高的co2,也能起到降低热流温度的作用,从而控制氮氧化物的生成量。
3、需要达到的热流温度处于第二设定温度阈值与第三设定温度阈值时,第一燃烧器主要负责将热流温度升高到第三切换温度左右(380~400℃),这个过程中,通过多组分燃料中醇类燃料的比例和co2的流量控制第一燃烧器的温度,从而降低氮氧化物的生成量。第二燃烧器采用电加热策略,过程中不产生氮氧化物,实现对热流温度的进一步提升。
4、需要达到的热流温度高于第三设定温度阈值时,与“3、需要达到的热流温度处于第二设定温度阈值与第三设定温度阈值时”相比,第一燃烧器发挥的作用一样。由于热流温度要求的提高,电加热策略已经不能很好地满足热流升温要求,所以第二燃烧器采用“喷射多组分燃料与电加热”相结合的加热策略。此时,通过水冷却器,降低多组分燃料的燃烧温度,从而降低氮氧化物的生成。
本发明与现有技术相比的优点在于:能够显著降低热振试验用热流发生器的氮氧化物排放,降低氮氧化物排放对环境和人体的危害。
附图说明
图1为实施例的热流发生器组合结构示意图。
图2为实施例的降低热振试验用热流发生器氮氧化物排放的方法示意图。
图3为步骤二的流程示意图。
图4为步骤三的流程示意图。
图5为步骤四的流程示意图。
图6为不同需求热流温度时氮氧化物排放对比图。
图7为不同需求热流温度时最终得到的热流温度对比图。
具体实施方式
下面结合实施例对本发明作进一步说明,但不作为对本发明的限定。
本发明实施例涉及的热流发生器组合结构如图1所示,包括两个燃烧器分别为第一燃烧器1和第二燃烧器2,第一燃烧器1的排气和第二燃烧器2的排气为串联设置,另外在第一燃烧器1与第二燃烧器2之间设置一个排气旁路,排气旁路上设置水冷却器6对第一燃烧器1的排气进行降温处理。通过控制阀5控制第一燃烧器1的排气直接进入第二燃烧器2或者通过排气旁路后再进入第二燃烧器2,在第二燃烧器2内设置电加热器3以对第二燃烧器2的排气进一步加热。在第一燃烧器1的进气端连接co2发生器4以便需要时向第一燃烧器1内通入co2。
请结合图2至图5所示,具体的降低热振试验用热流发生器氮氧化物排放的方法是这样的:
步骤一:热流发生器设定温度判断(即判断热流发生器期望达到的热流出口温度)
具体步骤:
101.判断热流发生器设定温度t0(即需求热流温度)是否小于第一设定温度阈值(本实施例为350℃):
1)如果是,则进行“步骤102”。
2)如果否,则进行“步骤103”。
102.以柴油为单一燃料,由第一燃烧器燃烧形成热流,然后执行“步骤104”。
103.判断热流发生器设定温度t0是否小于第二设定温度阈值(本实施例为500℃):
1)如果是,则进行“步骤105”。
2)如果否,则进行“步骤106”。
104.检测热流出口处的温度tt,判断tt是否达到热流发生器设定温度t0(±5%):
1)如果是,则已达到设定温度,程序结束。
2)如果否,则进行“步骤102”。
105.执行“步骤二:多组分燃料喷射结合co2发生器策略”。
106.判断热流发生器设定温度t0是否小于第三设定温度阈值(本实施例为700℃)
1)如果是,则进行“步骤107”。
2)如果否,则进行“步骤108”。
107.执行“步骤三:多组分燃料喷射、co2发生器结合电加热策略”。
108.执行“步骤四:多组分燃料喷射、co2发生器、水冷却器结合电加热策略”。
步骤二:多组分燃料喷射结合co2发生器策略(设定温度t0为350~500℃)
具体步骤:
201.以柴油为单一燃料,由第一燃烧器燃烧形成热流,采用温度传感器,检测“第一燃烧器”形成的热流温度t1,判断t1是否大于第一切换温度(本实施例为200℃):
1)如果是,则进行“步骤202”。
2)如果否,则持续等待升温。
202.第一燃烧器喷入柴油与醇类燃料(甲醇或乙醇)的混合燃料,设置醇类燃料(甲醇或乙醇)的初始添加比例为15%(质量比),进行“步骤203”。
203.检测第一燃烧器形成的热流温度升温速率dt1/dt,判断dt1/dt是否大于第一限制速率(本实施例为40℃/s):
1)如果是,则进行“步骤204”。
2)如果否,则进行“步骤205”。
204.醇类燃料(甲醇或乙醇)的添加比例,在之前的基础上,增加50%(初始15%、22.5%、33.75%......),然后执行“步骤203”。
205.启动“co2发生器”,设置初始流量为10%*f0向第一燃烧器通入co2,f0为目标热流流量,进入步骤206。
206.检测第一燃烧器形成的热流温度升温速率dt1/dt,判断dt1/dt是否大于第一控制速率(本实施例为30℃/s):
1)如果是,则提高co2流量,在之前的基础上,增加50%,并进行“步骤206”。
2)如果否,则保持第一燃烧器的燃烧及co2流量使最终热流出口处的温度tt达到热流发生器设定温度t0(±5%)。
步骤三:多组分燃料喷射、co2发生器结合电加热策略(设定温度t0为500~700℃)
301.以柴油为单一燃料,由第一燃烧器燃烧形成热流,采用温度传感器,检测“第一燃烧器”形成的热流温度t1,判断t1是否大于第二切换温度(本实施例为250℃):
1)如果是,则进行“步骤302”。
2)如果否,则持续等待升温。
302.第一燃烧器喷入柴油与醇类燃料(甲醇或乙醇)的混合燃料,设置醇类燃料(甲醇或乙醇)的初始添加比例为10%(质量比),进行“步骤303”。
303.检测第一燃烧器形成的热流温度升温速率dt1/dt,判断dt1/dt是否大于第二限制速率(本实施例为45℃/s):
1)如果是,则进行“步骤304”。
2)如果否,则进行“步骤305”。
304.醇类燃料(甲醇或乙醇)的添加比例,在之前的基础上,增加50%(初始10%、15%、22.5%......),然后执行“步骤303”。
305.启动“co2发生器”,设置初始流量为5%*f0向第一燃烧器通入co2,f0为目标热流流量,进入步骤306。
306.检测第一燃烧器形成的热流温度升温速率dt1/dt,判断dt1/dt是否大于第二控制速率(本实施例为35℃/s):
1)如果是,则提高co2流量,在之前的基础上,增加50%,并进行“步骤306”。
2)如果否,则保持第一燃烧器的燃烧及co2流量使第一燃烧器形成的热流温度t1达到第三切换温度(本实施例为400℃)进入步骤307。
307.第一燃烧器的热流直接进入第二燃烧器,启动第二燃烧器的电加热器,调整功率范围为60~80kw对第一燃烧器形成的热流加热使第二燃烧器排出的热流温度达到热流发生器设定温度t0(±5%)。
步骤四:多组分燃料喷射、co2发生器、水冷却器结合电加热策略(设定温度t0大于700℃)
401.以柴油为单一燃料,由第一燃烧器燃烧形成热流,采用温度传感器,检测“第一燃烧器”形成的热流温度t1,判断t1是否大于第四切换温度(本实施例为250℃):
1)如果是,则进行“步骤402”。
2)如果否,则持续等待升温。
402.第一燃烧器喷入柴油与醇类燃料(甲醇或乙醇)的混合燃料,设置醇类燃料(甲醇或乙醇)的初始添加比例为10%(质量比),同时启动“co2发生器”,设置初始流量为5%*f0向第一燃烧器通入co2,f0为目标热流流量,进入“步骤403”。
403.检测第一燃烧器形成的热流温度升温速率dt1/dt,判断dt1/dt是否大于第三控制速率(本实施例为40℃/s):
1)如果是,则进行“步骤404”。
2)如果否,则保持第一燃烧器的燃烧及co2流量使第一燃烧器形成的热流温度t1达到第三切换温度(本实施例为500℃)进入步骤405。
404.醇类燃料(甲醇或乙醇)的添加比例,在之前的基础上,增加50%(初始10%、15%、22.5%......),提高co2流量,在之前的基础上,增加50%,并进行“步骤403”.
405.柴油与醇类燃料(甲醇或乙醇)的混合燃料,由第二燃烧器燃烧,设置醇类燃料(甲醇或乙醇)的初始添加比例为15%(质量比),开启电加热器,功率范围为60~80kw并将电加热器加热,第一燃烧器的热流经过排气旁路后进入第二燃烧器,水冷却器中冷却水初始流量为1800kg/h,进入步骤406;
406.判断经过电加热器加热后热流温度,当加热后热流温度大于第六切换温度(本实施例为600℃)后进入步骤407;
407.检测电加热器加热后热流温度的升温速度dt2/dt,判断dt2/dt是否大于第四控制速率(本实施例为30℃/s):
1)如果是,则进行“步骤408”。
2)如果否,则保持第二燃烧器的燃烧、电加热器功率及水冷却器冷却水使电加热器加热后热流温度达到热流发生器设定温度t0(±5%)。
408.将第二燃烧器的混合燃料中醇类燃料的添加量在前一次添加量基础上增加30~35%,水冷却器流量提高30~35%,回到步骤407。
以三种不同热流温度要求为例(350℃、600℃、750℃),分别测量未使用任何降低氮氧化物技术措施(方案一)、采用循环水冷却法降低氮氧化物(方案二)、以及采用本发明设计的降低氮氧化物方法(方案三),排出的氮氧化物含量对比结果如图6所示,热流发生器出口处热流温度对比结果如图7所示。
可以看出,采用循环水冷却法对于降低氮氧化物有一定的作用,而采用本发明设计的降低氮氧化物的方案后,氮氧化物排放有明显的下降,而且热流发生器出口处热流温度基本没有下降,维持了试验热流温度的稳定性。本发明的方案对于降低氮氧化物,具有明显的作用。
本文用于企业家、创业者技术爱好者查询,结果仅供参考。